Abstract
Grid-based machining simulation methods have become very popular due to their advantages in computational efficiency. However, these methods are prone to generating machined workpiece models with chamfer edges, which reduce model accuracy and visual quality. An effective method is presented in this paper targeting the restoration of machined edges from these chamfer edges for triangle mesh models derived from grid-based machining simulation. The method starts by detecting the chamfer edge triangles via utilizing both edge-based mesh segmentation and feature-based mesh segmentation. The outcomes of the two segmentation methods are then compared and combined to achieve improved detection accuracy. To restore the machined edges, the detected chamfer edge triangles are split by adding new points based on the neighbors of the chamfer edge triangles. Triangle quality checks are imposed during the point addition process in order to ensure that the restored edges do not negatively impact the triangle mesh quality. Once all the applicable new points are added for all the chamfer edge triangles, the edge restoration task is complete. The presented method has been implemented and executed on sample triangle mesh models derived from grid-based machining simulation. Improved edge restoration compared to that of existing edge restoration methods has been observed. Sub-second computational performance is attained for the majority of the test cases.
GRAPHICAL ABSTRACT
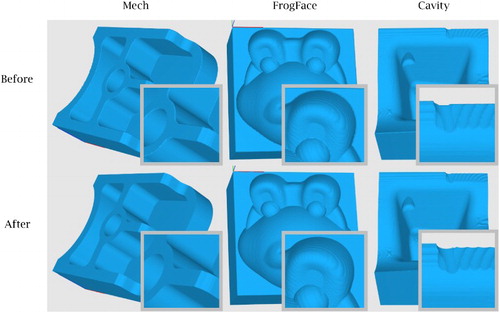
Acknowledgements
The machining simulation research work being conducted in our group has been supported by the Natural Sciences and Engineering Research Council of Canada (NSERC). The Mitacs Globalink Research Internship awarded to the first author of this paper is also gratefully acknowledged. The FrogFace model was created by the paper’s third author along with his teammates Ted Angus, Alicia Figueira and Josh Harrington as part of a graduate course project at UBC Mechanical Engineering. The Cavity model and the Impeller model were retrieved from the Siemens NX CAST Library of part models.
ORCID
Ziqi Wang http://orcid.org/0000-0002-3817-3922
Jack Szu-Shen Chen http://orcid.org/0000-0002-1225-6340
Jimin Joy http://orcid.org/0000-0003-4499-2366
Hsi-Yung Feng http://orcid.org/0000-0001-6189-6910