Figures & data
Table 1. Summary of epoxy resin systems used in the investigation.
Figure 3. SEM micrographs of plastically deformed (a,b) and successfully debonded (c,d) microbond droplets.
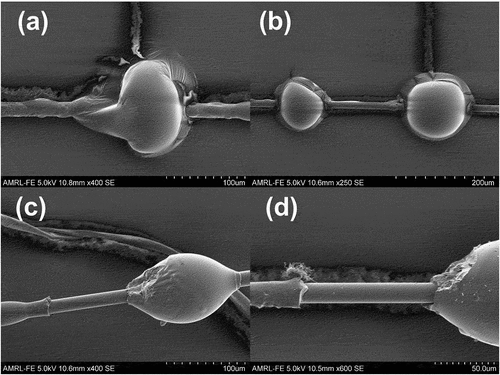
Table 2. Epoxy/amine curing FTIR band assignments.
Figure 7. Spectral comparison of Epotec droplet and bulk matrix specimens cured according to the recommended macroscale schedule.
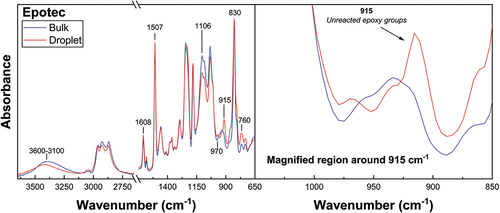
Figure 8. Spectral comparison of Olin droplet and bulk matrix specimens cured according to the recommended macroscale schedule.
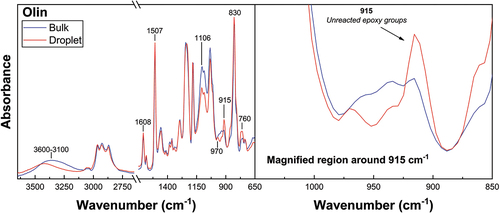
Figure 9. Spectral comparison of 332-TETA droplet and bulk matrix specimens cured according to identical schedules.

Figure 10. Load–extension curves generated during microbond testing showing (a) semi-plastic behaviour and (b) good debonding.

Figure 12. FTIR spectra of microbond droplet specimens and bulk cured matrices after standard cure cycle and with 0–48 h pre-cure.
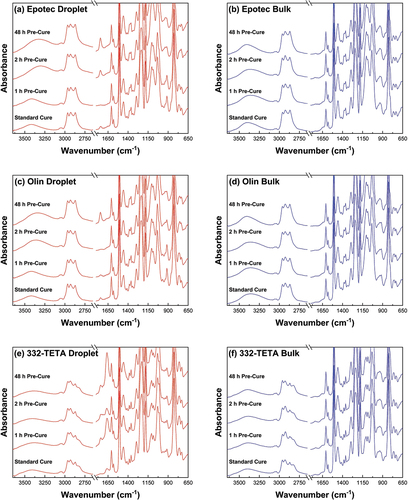
Figure 13. Comparison of apparent IFSS for the Epotec epoxy system and the degree of epoxy conversion in a microdroplet versus a bulk polymer sample with different pre-cure standing times.
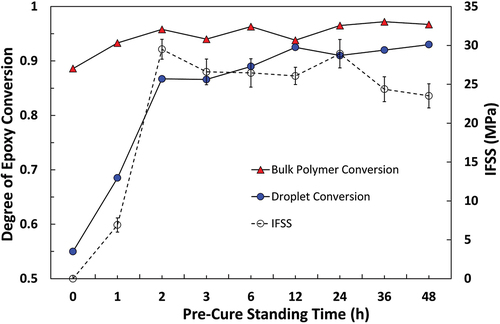