Figures & data
Table 1. Dynamic variables and parameters for the slider-crank mechanism.
Table 2. Geometric parameters for the eccentric cam mechanism.
Table 3. Dynamic variables and parameters for the eccentric cam mechanism.
Table 4. Required parameters for the numerical examples.
Figure 5. (a) Transmission efficiency of motion; (b) Linear acceleration of the slider and the follower.
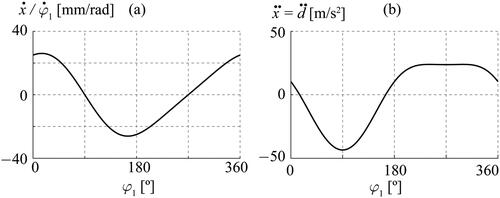
Figure 7. Internal reactions for each pair: (a) Slider-crank; (b) Eccentric cam with small roller radius; (c) Eccentric cam with big roller radius; (d) Transmission efficiency of force.
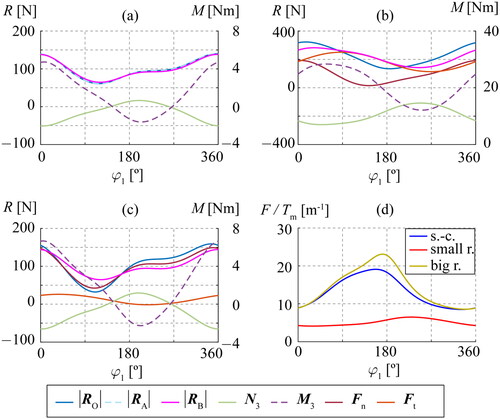
Table 5. Required parameters for traction coefficient (Masjedi and Khonsari Citation2015).
Table 6. Test stand specifications of the shared components.
Figure 12. (a) Slider-crank; (b) Eccentric cam with small roller radius; (c) Eccentric cam with big roller radius.
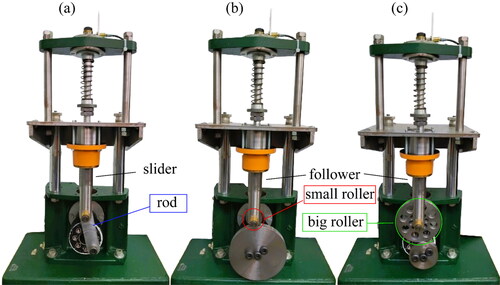
Figure 13. Test results: (a) Eccentric cam with small roller radius; (b) Eccentric cam with big roller radius; (c) Slider-crank.
