Figures & data
Figure 1. Magnet coordination system xyz and ultrasound applicator coordinate system x′ y′ z′. The direction of the main static magnetic field is in parallel with the z axis. The origin of the ultrasound applicator coordinate system is (a, b, c) in the magnet coordinate system. Relations between the applicator coordination system and the magnet coordination system are: (A) translation, (B) translation and rotation along z direction.
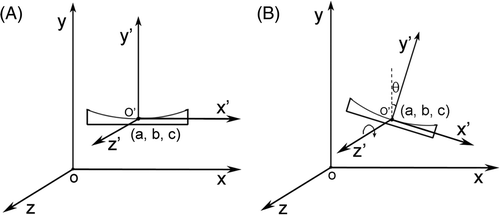
Figure 2. Diagram of tumour treatment by MRgHIFU. After finishing the treatment at position 1, the ultrasound applicator is moved to position 2. The ideal workflow is: a reference image is acquired at position 1 for temperature imaging, when the applicator is shifted to position 2, the reference image can still be used for calculating a temperature map.
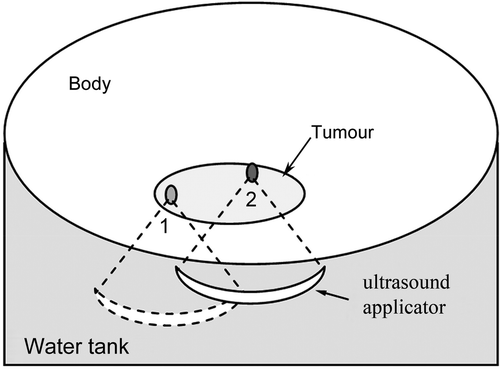
Figure 3. A simplified ultrasound applicator model was used for calculating the delta magnetic field. The model was divided into 2 mm × 2 mm × 2 mm-sized volume elements. For each volume element we assumed that only one kind of material was contained.
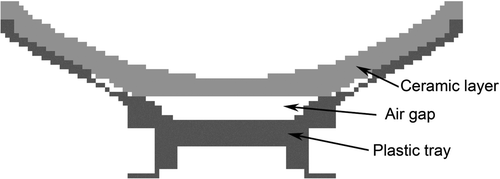
Figure 4. Diagram for measuring the delta magnetic field induced by the ultrasound applicator. A water tank was positioned in the magnet centre. MR phase images were acquired with and without ultrasound applicator in the water tank while keeping the water level constant for both measurements.
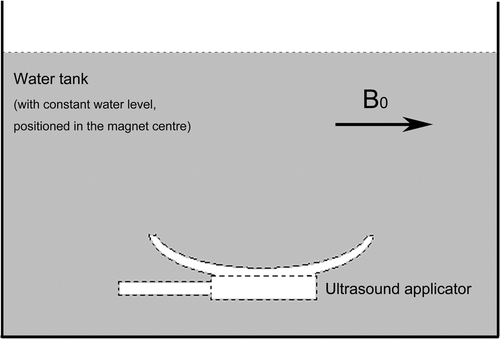
Figure 5. Experimental set-up. (A) Phantom: a 240-mm diameter spherical water phantom was put on the water tank. (B) Ex vivo: a block of porcine muscle was put inside a container with a plastic film beneath it through which ultrasound energy can penetrate freely.
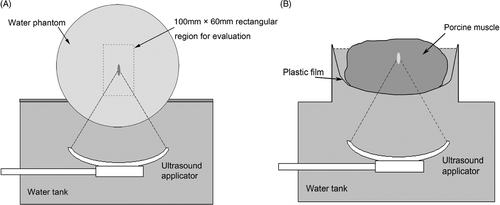
Figure 6. Ultrasound applicator-induced delta magnetic fields. The direction of the static main magnetic field B0 is indicated by the arrow. The fields are shown (A) from a measurement, (B) by calculation. The magnetic field varies between −0.01 ppm to 0.4 ppm from the focal region to the applicator surface. Phase wraparound can be observed around the applicator due to large magnetic field variations in A; however, it can be neglected during the temperature error compensation as those areas are far away from the ultrasound focal region.
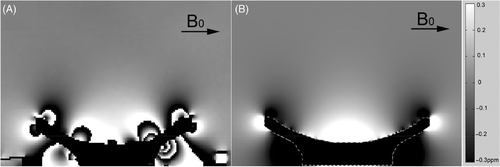
Figure 7. Temperature error map within a 100 mm × 60 mm rectangular evaluation region. The ultrasound focus was located at the centre of the rectangle. The ultrasound applicator was shifted along the y direction. (A) Conventional PRF shift-based method without the applicator delta field compensation. (B) Compensation with the pre-measured applicator delta field. (C) Compensation with the calculated applicator delta field.
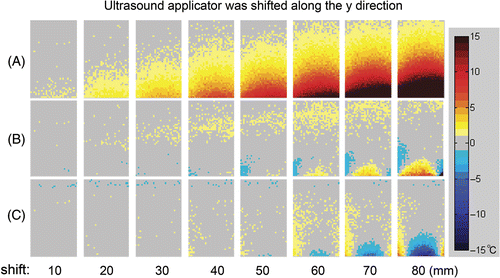
Figure 8. Temperature error map within a 100 mm × 60 mm rectangular evaluation region. The ultrasound focus was located at the centre of the rectangle. The ultrasound applicator was shifted along the z direction. (A) Conventional PRF shift-based method without the applicator delta field compensation. (B) Compensation with the pre-measured applicator delta field. (C) Compensation with the calculated applicator delta field.
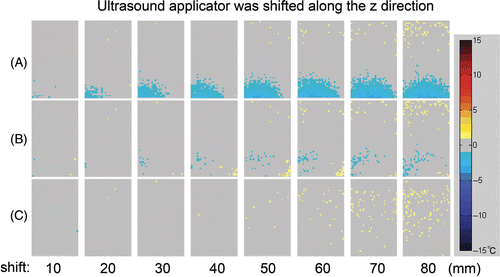
Figure 9. Temperature measurement error at the 95th percentile in the 100 mm × 60 mm evaluation region correlated to the distance of the ultrasound applicator from the position where the reference image was acquired. Ultrasound applicator was shifted in (A) y direction and (B) z direction.
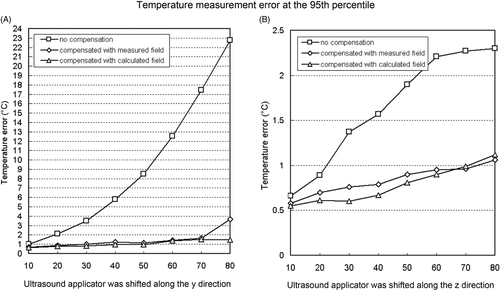
Table I. Quantitative temperature error measurement for applicator shifts in y direction.
Table II. Quantitative temperature error measurement for applicator shifts in z direction.
Figure 10. Ex vivo experiments with porcine muscle. Ten ablations were applied at different ultrasound applicator positions. The values of y and z indicate the shifts of the applicator from the position where the reference image was acquired. (A) Delta temperature map without ultrasound applicator delta magnetic field compensation. (B) With ultrasound applicator delta magnetic field compensation. Images were sorted in a time sequence of HIFU heating with labels 1∼10. The temperature measurement errors in group A, indicated by arrows, were significantly reduced by compensating the ultrasound applicator-induced delta field in B. The ultrasound foci and the heated region which did not fully cool down during the sequence can be shown clearly and accurately.
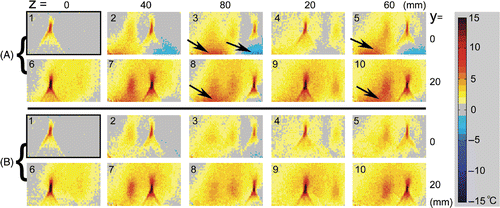