Abstract
A long-lasting generator of continuous silica nanoparticle aerosols based in a fluidized bed of glass beads coated with nanosized silica has been developed. The attrition resulting from the bubbling fluidized bed regime progressively detaches the silica coating from the glass beads, giving rise to a steady production of silica nanosized aerosols with median diameters from 100 to 250 nm depending on the initial size of the coating nanoparticles. Continuous aerosol production could be maintained for more than 12 h, and the nanoparticle concentration can be easily tuned in the range of 2000 to 14,000 #/cm3 by adjusting the fluidization and/or dilution flow rates.
Copyright 2013 American Association for Aerosol Research
1. INTRODUCTION
The generation of long-lasting nanoparticle aerosols with stable particle number concentration is a key requirement for many applications. For instance, the development of high-efficiency filtering systems for airborne nanoparticles and the tuning of aerosol spectrometers need constant and monodisperse aerosols to assess nanoparticle penetration under different conditions (Denny et al. Citation2010; Savolainen et al. Citation2010). Other applications include the validation of models of nanoparticle behavior in the atmosphere, where the production of well-characterized aerosols is essential to study particle aggregation and agglomeration (Cho et al. Citation2011; Wang et al. Citation2011). Nanoparticle aerosol generators are also widely used in investigations of the effect of nanoparticle aerosols on human health (Grassian et al. Citation2007), their biological and environmental impacts (Schmoll et al. Citation2009; Chen et al. Citation2010; Kreyling et al. Citation2011), and the role of particles as vectors for the transport of airborne pathogens (Liu et al. Citation2012).
Standard aerosol generators often use wet processes involving atomizing solutions of a given composition to form droplets that give rise to solid nanoparticles when the solvent is evaporated, or of suspensions already containing the nanoparticles at the desired concentrations (Liu and Lee Citation1975; Kruis et al. Citation1998). Often, drop formation and evaporation is facilitated by means of ultrasound, vibrating orifice systems, pneumatic or electro hydrodynamic atomization, spray pyrolysis, and condensation devices (John Citation1993; Biskos et al. Citation2008). While wet generation methods have the advantage of a high flexibility regarding the nature of the particles that can be produced, they also present important problems, including the presence of impurities in the solvent, the production of aerosols with a low nanoparticle concentration, and the difficulties in achieving a sufficiently low droplet size (Biskos et al. Citation2008), in addition to the obvious problem of having to evaporate a large amount of solvent that is then entrained in the produced aerosol. This has prompted numerous studies to aim to achieve stable aerosol generation by dry processes. Spark generation and electrospray can be used to produce highly stable aerosols containing engineered nanomaterials, including carbon nanotubes and nanosized metal oxides (Biskos et al. Citation2008; Bau et al. Citation2010; Jennerjohn et al. Citation2010; MacMillan et al. Citation2012). These systems produce stable nanoparticle aerosols with controllable sizes up to several hours of operation.
Fluidized beds are widely used in the chemical industry in a variety of reactive and non-reactive processes. Aerosol generation is a less common application but nevertheless fluidized beds have also been used for decades to generate aerosols of relatively coarse particles (Guichard Citation1976), and more recently for nanoparticles (Wang et al. Citation1998; Yao et al. Citation2002). Myojo et al. (Citation2009) reported the use of a fluidized bed to homogenize the supply of multi-walled carbon nanotubes from a rotating brush aerosol generator, giving concentrated carbon nanotube aerosols for limited experimental times (under 1 h of operation). Lind et al. (Citation2010) reported on the use of a glass-bead-fluidized bed for producing silica ultrafine particles (1 and 2.6 μm). However, this produced a decreasing particle concentration, unless the operating flow rate was continuously adjusted to compensate for the diminishing particle supply. Denny et al. (Citation2010) designed a TiO2 nanoparticle aerosol generator by continuously feeding TiO2 particles to a fluidized bed composed of 300 μm bronze beads. The device was able to generate a flow of TiO2 nanoparticles that was used to coat a photo catalytic filter. Indeed, the continuous addition of bed material leads to longer periods of stable aerosol generation and it was originally proposed by Prenni et al. (Citation2000) for generating submicrometer soot aerosols from a bronze-bead fluidized bed. It should be realized that fluidizing nanomaterials is a challenging task, as shown in a recent review (Van Ommen et al. Citation2012), and this is the reason why most of the fluidized bed aerosol generators (FBAGs) use a second, coarse solid as a co-adjuvant. Nanoparticles from fluidized bed devices form agglomerates with a particle size distribution that depends on the material properties, primary particle size, characteristics of the generator device, and operating conditions (Van Ommen et al. Citation2012).
It seems evident that a fluidized bed generator capable to deliver a stable flow of nanoparticles without the need to supply additional solid feed would be extremely interesting for a number of nanotechnology applications. This can only be achieved by (1) loading a sufficiently high amount of nanomaterials in the fluidized bed, and (2) implementing a mechanism that allows a progressive release of these nanomaterials, in such a way that a stable aerosol results. In this work we have achieved this by coating glass beads of a suitable size for fluidization (80–150 μm) with a layer of silica nanoparticles, and loading the coated beads in a FBAG. The bubbling fluidization regime produces attrition of the nanoparticle coating, leading to a steady release of nanoparticles into the gas phase. As a consequence, the FBAG produces a concentration-tunable aerosol of nanoparticles with a size of 100 to 300 nm. This is a range usually employed in health-related studies, as well as in nanoparticle penetration tests, since it is considered as the most penetrating particle size range (Wang Citation2005).
In the present work, a FBAG that allows the production of nanoparticle aerosols for up to 12 h of continuous operation, without the need for continuous feeding of nanoparticles, is developed. The FBAG is tested with two types of particles, namely 15 nm SiO2 nanoparticles and 100 nm nanoparticles prepared by the Stöber method. The particle size distributions of the resulting aerosols are centered on 200 and 100 nm, respectively.
2. MATERIALS AND METHODS
2.1. Bed Preparation
Glass beads with a bulk density of 2.5 g/cm3 are provided by Abrasivos y Maquinaria, SA (Barcelona, Spain) with nominal composition of SiO2 (70–73%), Na2O (13–15%), CaO (7–11%), MgO (3–5%), Al2O3 (0.5–2%), and K2O (0.2–0.6%), and with a hardness of 6 in the Mohs scale. As-received beads are subjected to two cycles of washing with ethanol (Sigma-Aldrich) followed by drying at 25°C for 8 h. The dry glass beads are sieved to a size between 80 and 150 μm using stainless steel sieves. A mass of 66 g of the sieved glass beads was then immersed in a colloidal suspension of 0.225 g of dense 5–15 nm silica nanoparticles (Sigma-Aldrich) in 25 mL of 96% ethanol. Alternatively, Stöber silica nanoparticles are prepared using tetraethyl orthosilicate (TEOS, Sigma-Aldrich 98%), ammonium hydroxide (NH4OH, Sigma-Aldrich), and Milli-Q water using the synthesis procedure that was published elsewhere (Gutierrez et al. Citation2011). Suspensions are stirred at 25°C for solvent evaporation. The mass of deposited silica nanoparticles is estimated as 0.34 wt% of the total mass of the glass beads. The overall process for the bed preparation is schematically plotted in .
2.2. Design and Operation
A scheme of the system used is presented in . The FBAG is built in a 30 mm-i.d., 200 mm-long polypropylene tube equipped with a 50 μm stainless steel grid. Two independent dry and HEPA-filtered (Whatman HEPA-Cap 150) air supplies are used to supply fluidizing air to the FBAG and to incorporate additional carrier flow to dilute the concentration of the generated aerosol as needed. All airflows are mass-flow controlled (Bronkhorst), and the generated particulate aerosol is driven using stainless steel pipes first into a large-particle collector (LPC) chamber that eliminates aerosol particles over 5 μm in size and then into the aerosol particle counters (see below) located downstream. This LPC is an inertia-driven device that directs the aerosol through a 10 mm glass pipe into the bottom of a 350 cm3 glass chamber with 56 mm internal diameter. Inside the LPC, larger particles impact the bottom wall where they are deposited while the aerosol, now with a lower velocity, is able to entrain the smaller particles that constitute the aerosol. The excess aerosol is driven out of the system through a HEPA-filter unit located in a three-way valve to avoid overpressure in the line that could damage the detection units. The range of operating conditions was as follows: feed flow rate, 1–2.5 L/min; diluting airflow rate, 0.5–8.5 L/min; the silica-coated glass beads, 80–150 μm, had a minimum fluidization velocity (u mf) of 0.58 cm/s, as determined in separate experiments with dry and HEPA-filtered air at 25°C, and the relative gas velocity (u r = u/u mf) was 1.8–4.5 cm/s; height of the bed (HB) in the absence of fluidization gas, 5 cm; and temperature, 25°C. Before each experiment, the fluidized bed system was purged with HEPA-filtered air in order to eliminate the ambient particle aerosol out of the pipes and other conductions of the sampling system and to remove loose material in the fluidized bed.
To determine the fraction of aerosol particles with sizes between 300 nm and 20 μm, an eight-channel optical particle counter (OPC, Model #1.108; Grimm Aerosol Technik) is used. The fraction of smaller aerosol particles is determined using a stepping mobility particle spectrometer (SMPS+C, Model #5.403; Grimm Aerosol Technik) that comprises a differential mobility analyzer (DMA, Model 33–900; Grimm Aerosol Technik) and a condensation particle counter (CPC). This SMPS+C system allows the measurement of unit density spherical particles from 10 to 1110 nm with a normal scan time of 7 min. The inlet aerosol in the SMPS system is electrically neutralized using a 241Am alpha-emission source to provide an equalized distribution of charges on the surface of nanoparticles. The ambient aerosol in the laboratory conditions is usually composed of 5 to 50 nm particles at concentrations between 3000 and 5000 #/cm3, as measured by the SMPS+C apparatus. A dry and HEPA-filtered airflow of 2 L/min is used to purge the whole system before operation, and within 5 min after purging, values below 5 #/cm3 are measured by the condensation particle counter unit (CPC) of the SMPS+C system, confirming the successful purge of the system.
2.3. Material Characterization
The morphology of glass beads and the particles collected in the aerosol phase is observed using SEM with a FEI Inspect Field Emission Gun microscope. Silica nanoparticles were characterized using TEM in a FEI Tecnai T20 microscope using copper grids as sample holder. The effective sizes of the SiO2 nanoparticle suspensions used for the coating are measured in liquid suspensions using dynamic light scattering (DLS) in a Brookhaven 90Plus analyzer (Brookhaven Instruments Co., NY, USA). The data (not shown) indicated that the mean effective particle size in the suspensions used to coat the glass beads is centered on 230 and 120 nm for 5–15 nm silica and Stöber nanoparticles, respectively.
3. RESULTS AND DISCUSSION
3.1. Glass Bead and Nanoparticle Characterization
The morphology of the primary silica nanoparticles used to coat the glass beads used in the FBAG is displayed in the TEM images of together with their size histograms. Images show isolated particles with a mean particle size of 6.7 nm and a standard deviation of 2.7 nm. An overall view of uncoated and silica-coated glass beads is given in the SEM images of . The naked beads present a clean, particle-free surface () and the cross-section of the beads () shows the smooth surface of the glass particles. After coating with 5–15 nm silica nanoparticles (), most of the surface appears coated with a relatively homogeneous layer of nanoparticle agglomerates of a small size, although some larger agglomerates are also visible. The close-up cross-sectional view of reveals that most of the nanoparticle coating presents a thickness of 100 to 400 nm, which is of the order expected taking into account the weight load of the silica (see online supplemental information). Coating with 100 nm Stöber nanoparticles produces a layer of silica nanoparticles on the surface of glass beads, as it can be seen in and . This coating with a thickness of a few hundred nm is formed by nanoparticles about 100 nm in size.
3.2. Generation of Nanoparticle Aerosols
Stable and monodisperse nanoparticle aerosols are generated using the FBAG with silica-coated glass beads. The collisions among glass beads in the bubbling fluidization regime of the FBAG lead to the progressive release of the nanoparticle agglomerates attached to their surface, giving rise to a continuous aerosol, as will be shown later. In order to demonstrate that the aerosol is produced from the coatings on the glass beads and not from the beads themselves, a blank experiment was performed in which a bed of uncoated glass beads was fluidized in the FBAG. From Figure S1 (see the online supplemental information), it can be observed that the measured number concentration of the aerosol generated using a non-coated bed reaches a maximum immediately after the start of fluidization due to the presence of unbound material and then rapidly decreases below 5 #/cm3after a few minutes of operation. Consequently, debris from the glass beads will only have limited contribution to the aerosol produced by the fluid bed generator.
All of the experiments in this work are conducted in a semi-continuous mode: a batch of nanoparticle-coated glass beads is loaded on to the FBAG and the system is operated without additional feed of nanoparticles to the bed. In spite of this, a stable aerosol is generated for up to 12 h of operation, as shown in , where the time evolution of the aerosol is followed by measuring the number concentration of particles with particle sizes between 5 and 1110 nm using the SMPS+C device in the counting mode. For this purpose, the generated dry aerosols are driven through the CPC without previous electrostatic classification. The data in this figure correspond to the particle counts obtained with two different batches of 5–15 nm silica-coated beds, prepared independently. It can be seen that in both cases there is an initial transient period of a few minutes during which the particle counts rapidly decrease to a nearly stable level that is maintained, with small variations for the duration of the experiment (12 h in this case). In addition, there is an excellent reproducibility of the aerosol counts (values of 9584 ± 343 #/cm3 for Bed-A and 9857 ± 318 #/cm3 for Bed-B were obtained after fluidization for 10 h in both experiments). Similar results (not shown) are obtained for Stöber-silica-coated glass beads, which indicate a good repeatability of the coating protocol together with a high stability of the generated aerosols.
FIG. 4 Reproducibility of nanoparticle aerosol generation: number concentration of particles (5–1000 nm) for two independent beds (A and B) prepared using the same procedure with 5–15 nm silica-coated glass beads (Q FEED = 1.5 L/min; Q DILUTION = 0.5 L/min; and H B = 5 cm). (Color figure available online.)
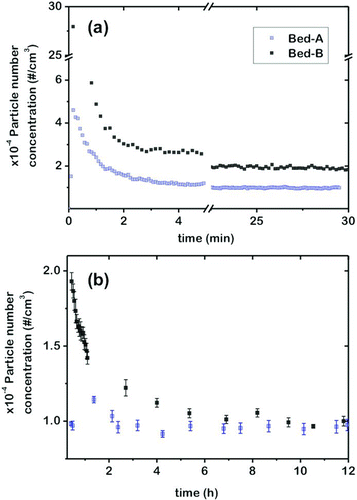
From the data of , the generation of nanoparticle aerosols using the FBAG can be described as a three-stage process:
1. | In the first stage fluidization starts, and the initial collisions among the nanoparticle-coated glass spheres rapidly remove the weakly bound material, resulting in a burst release of particles, leading to concentrations up to 30,000 #/cm3 for the first seconds of operation. | ||||
2. | A stabilization stage follows, during which the initial burst decreased abruptly for the next 15–60 min until stable levels are reached. This stabilization period might be related to the removal of large agglomerates on the surface of the beads, which are likely to be more affected by particle collisions. This effect has been also reported in the dustiness tests performed with nanoparticles (Jensen et al. Citation2009; Tsai et al. Citation2012). | ||||
3. | The third stage corresponds to the generation of a stabilized nanoparticle aerosol. Once the weakly bound material and the large agglomerates in the surface of the beads have been eliminated, the remaining nanoparticle coating on the beads presents similar characteristics and stable generation is achieved by attrition in the bubbling fluidized bed regime. |
As shown in , the number concentration of aerosols produced upon fluidization of 5 to 15 nm silica-coated glass beads is stabilized about 10,000 #/cm3. Similar results are obtained when fluidizing glass beads coated with 100 nm Stöber nanoparticles. As can be seen in , the aerosol number concentration is stabilized at values close to 10,000 #/cm3 for periods up to 12 h of continuous operation. In both cases, these numbers are well above those of previously reported aerosol generators based on fluidized bed technology (Prenni et al. Citation2000; Myojo et al. Citation2009; Denny et al. Citation2010; Lind et al. Citation2010). By using a continuous feeding system, generation of highly concentrated aerosols can be achieved over a period of several hours but the average particle size is usually larger than 1 μm (Vincent Citation2007), a value too large for studies of nanoparticle aerosols.
FIG. 5 Stability of nanoparticle aerosol generation using glass beads coated with Stöber silica (Q FEED = 1.5 L/min; Q DILUTION = 0.5 L/min; and H B = 5 cm). (Color figure available online.)
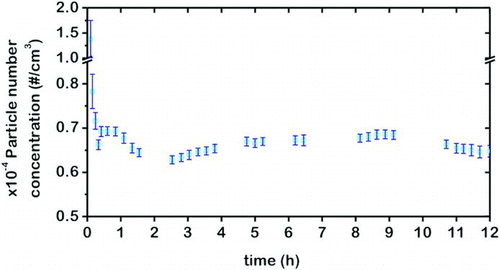
The count particle size distributions are fitted using a log-normal probability density function (Vincent Citation2007). The values of count median diameter (CMD) for aerosols obtained from Beds A and B are 201.9 and 202.1 nm respectively, whereas geometric standard deviation (GSD) for the same count distributions are 1.31 and 1.32, respectively. The statistical testing of the resulting aerosols gives that both CMD and GSD are similar with p > 0.005. For log-normal distributed aerosols, the polydispersity index (W) of the obtained size distributions is estimated after the values of GSD as (Pratsinis Citation1988). In these conditions, the values for W are about 0.28 in both cases. Although W is a quantitative measure of the spread of the size distributions, the threshold values for mono- and polydisperse aerosols are arbitrarily selected depending on the end use of the aerosol (Pratsinis et al. Citation1986). In general, aerosols are usually accepted to be truly monodisperse aerosols if W < 0.3. In terms of GSD, monodispersity is conventionally considered for values between 1 and 1.4 (Hinds Citation1999; Rosati et al. Citation2003).
The time evolution of the particle size distribution in the aerosol is investigated in successive SMPS+C scans at the FBAG outlet. The fluidization of 5 to 15 nm silica-nanoparticle-coated glass beads gives highly stable size distributions with a CMD of 210 nm and GSD of 1.4 nm, with values of W under 0.3 throughout the sampled period (). In the case of Stöber nanoparticle aerosols, the time stability is tested for periods as long as 10 h of continuous operation as it is shown in . The size distributions for the aerosols formed with those nanoparticles give a CMD of 112 nm and GSD of 1.25, with W under 0.3 during the tests, indicating a highly monodisperse aerosol. Moreover, it is interesting to mention that aerosol particles have median size very close to that observed in the SEM images (), which indicates that aerosol is mainly composed of non-agglomerated particles.
FIG. 6 (a) Evolution of particle size distributions using 5–15 nm silica-coated glass beads (conditions of ) obtained after periodic SMPS+C scans at the FBAG outlet. (b) Average particle size distribution obtained from SMPS+C (open black dots) and OPC data (closed blue dots). The data shown correspond to the average of the scans represented in . (Color figure available online.)
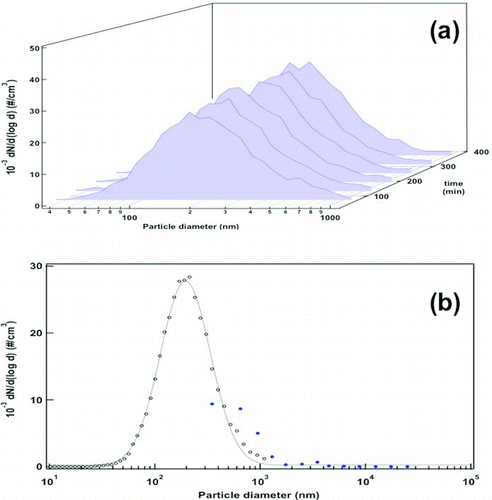
FIG. 7 (a) Evolution of particle size distributions using Stöber-silica-coated glass beads (conditions of ) obtained after periodic SMPS+C scans at the FBAG outlet. (b) Average particle size distribution obtained from SMPS+C (open black dots) and OPC data (closed blue dots). The data shown correspond to the average of the scans represented in . (Color figure available online.)

As an additional check of the particle size distribution for the larger fraction of particle sizes, the number of aerosol particles with sizes over 300 nm was also measured using the OPC in the above-described experiment. The overall size distribution of generated aerosol with data from the OPC and the SMPS+C for the aerosols generated upon fluidization of both 5–15 nm silica-coated and 100 nm Stöber-silica-coated beads are respectively plotted in and . In the area where the measurements from both instruments overlap (300–1000 nm) the CPC gives consistently higher counts (around 2500–3000 #/cm3), but the discrepancy can be considered acceptable because both instruments are based on different physical principles.
The design of the FBAG allows an effective tuning of the particle concentration in the generated aerosol by changing the fluidization or the diluting airflow. shows the effect of the fluidization gas flow rate upon the concentration of the aerosol particles generated for a constant dilution flow rate using the 5–15 nm silica-coated glass beads. As the fluidization flow rate increases, the bed expands and the bubbling becomes more vigorous, increasing the particle number concentration at the FBAG exit. Also, for a given fluidization flow rate, increasing the diluting airflow allows to tune down the concentration of nanoparticles in the generated aerosols, as can be seen in . The particle number concentration continuously decreased with increasing dilution rates down to 1400 #/cm3, for a diluting airflow of 8.5 L/min. Similar results (not shown) are also found for the 100 nm Stöber-silica-coated glass beads.
FIG. 8 Evolution of the aerosol number concentration of particles (5–1000 nm) using 15 nm silica-coated glass beads when the fluidization flow rate (Q F) was increased step-wise (a) and the dilution flow rate (Q D) was increased step-wise (b). (Color figure available online.)
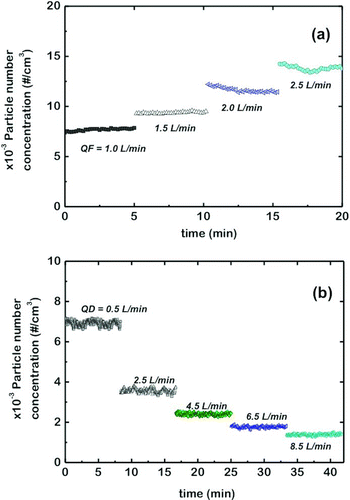
The particle morphology was examined offline on aerosol samples collected at the exit of the FBAG using two different devices that were placed perpendicular to the airflow. displays images of the particles sampled using a holey carbon-coated copper TEM grid at 300 mL/min for 15 s ( and ). Alternatively, a polycarbonate filter with a cut-off size of 50 nm was placed in a Whatman filter holder unit and the aerosol was sampled at 300 mL/min for 5 min, and then the filter was examined using SEM ( and ). The fluidization of 15 nm silica-coated glass beads produces agglomerates with a mean size of about 350 nm ( and ). On the other hand, single nanoparticles of about 100 nm are obtained upon fluidization of 100 nm Stöber-silica-coated glass beads ( and ). It is worth mentioning that offline collection procedures give similar size distributions for the aerosol agglomerates, which are slightly higher than the data obtained using the SMPS+C and OPC, probably due to additional agglomeration on the collection device. In any case, the size and morphology of the particles within the aerosol was completely different from the original 5–15 nm particles loaded onto the glass beads. Instead, most of the particles collected are in the 100–400 nm intervals, which is coincident with the thickness of the coating on beads. This suggests that the aerosol particles may originate from detachment of whole nanoparticle lumps on the surface. For Stöber silica nanoparticles, the size of initially attached nanoparticles roughly coincides with the sizes detected using SMPS+C and offline techniques, where mainly non-agglomerated nanoparticles can be observed. This strongly suggests that the formation of airborne silica nanoparticles during fluidization of Stöber-coated beads can be attributed to the detachment of individual nanoparticles from the glass surface. Although additional aggregation could be expected from the gas-phase agglomeration of the nanoparticles released, as Lushnikov (Citation2010), Eggersdorfer and Pratsinis (Citation2012), and Van Ommen et al. (Citation2012) reported, this is unnoticed at least for 100 nm Stöber-silica-coated glass beads.
FIG. 9 SEM images of filter-collected nanoparticles and size distributions for (a) 5–15 nm silica (N = 448; mean = 336 nm; σ = 2.05), and (b) Stöber nanoparticles (N = 99; mean = 101.1 nm; σ = 14.1 nm); TEM images and size distribution of the holey grid-collected (c) silica nanoparticles (N = 345; mean = 361 nm; σ = 2.01 nm) and (d) Stöber nanoparticles (N = 104; mean = 99 nm; σ = 10.0 nm). (Color figure available online.)
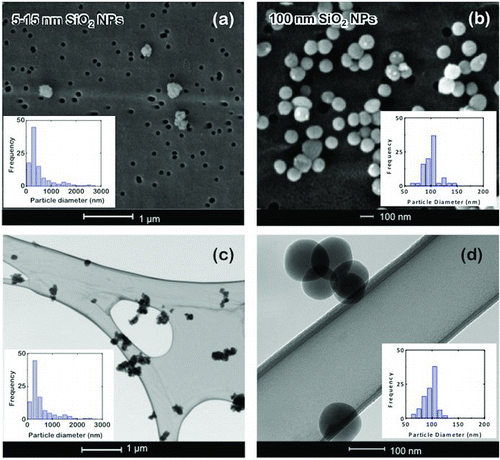
The nanoparticle-detaching process leading to aerosol generation has been analyzed using SEM images of the glass beads after fluidization for a certain period. The surface of as-coated glass beads with both 5–15 nm silica and 100 nm Stöber silica nanoparticles shows rather different features, as it can be seen in Figure S2. Agglomerated particles are observed for the small-sized silica while the originally larger Stöber nanoparticles are extended all over the surface and largely maintain their individuality. The fluidization provokes the detachment of nanoparticles with the sizes that are in the region of the clusters present on the glass surfaces. The surface coverage of glass beads is eventually reduced after fluidization, although it is worth mentioning that the aerosol number concentration is only reduced by 20% during the 100 h fluidization tests (results not shown). In addition, the sizes of the particles forming the aerosol are approximately constant during the period of operation, indicating that the size of the detached objects remains roughly constant.
4. CONCLUSIONS AND OUTLOOK
Stable silica aerosols are produced after fluidization of a bed composed of glass beads with a thick coat of agglomerated silica nanoparticles. The process of nanoparticle loading on the glass beads produces highly stable coatings, which are progressively detached during prolonged fluidization due to mechanical attrition. The bubbling fluidization of these composite beads allows the generation of stable nanoparticle aerosols for periods of more than 12 h of continuous operation, with aerosol particle size distributions centered between 100 and 200 nm, depending on the size of the original coating particles and without the need for continuous feeding of additional nanoparticles. The high stability of the aerosols generated, with the nanoparticle diameters in the most penetrating particle size range, makes the FBAG useful for a variety of studies ranging from the toxicological and occupational impact of dry nanoparticle aerosols to the efficiency of aerosol-filtering methods.
Supplemental Information_797952.zip
Download Zip (3.5 MB)Acknowledgments
Financial support through research project MAT2008-01319/NAN of the Spanish Ministry of Economy and Competitiveness, and EU FP7 NanoValid project #263147 is gratefully acknowledged. Francisco Balas also acknowledges support from the Ramón y Cajal program.
[Supplementary materials are available for this article. Go to the publisher's online edition of Aerosol Science and Technology to view the free supplementary files.]
REFERENCES
- Bau , S. , Witschger , O. , Gensdarmes , F. , Thomas , D. and Borra , J.-P. 2010 . Electrical Properties of Airborne Nanoparticles Produced by a Commercial Spark-Discharge Generator . J. Nanopart. Res , 12 : 1989 – 1995 .
- Biskos , G. , Vons , V. , Yurteri , C. U. and Schimidt-Ott , A. 2008 . Generation and Sizing of Particles for Aerosol-Based Nanotechnology . KONA Powder Part. J , 26 : 13 – 35 .
- Chen , B. T. , Afshari , A. , Stone , S. , Jackson , M. , Schwegler-Berry , D. Frazer , D. G. 2010 . Nanoparticles-Containing Spray Can Aerosol: Characterization, Exposure Assessment, and Generator Design . Inhal. Toxicol., , 22 : 1072 – 1082 .
- Cho , K. , Chung , K. S. and Biswas , P. 2011 . Coagulation Coefficient of Agglomerates with Different Fractal Dimensions . Aerosol Sci. Technol., , 45 : 740 – 743 .
- Denny , F. , Permana , E. , Scott , J. , Wang , J. , Pui , D. Y. H. and Amal , R. 2010 . Integrated Photocatalytic Filtration Array for Indoor Air Quality Control . Environ. Sci. Technol., , 44 : 5558 – 5563 .
- Eggersdorfer , M. L. and Pratsinis , S. E. 2012 . The Structure of Agglomerates Consisting of Polydisperse Particles . Aerosol Sci. Technol , 46 : 347 – 353 .
- Grassian , V. H. , Adamcakova-Dodd , A. , Pettibone , J. M. , O’Shaughnessy , P. T. and Thorne , P. S. 2007 . Inflammatory Response of Mice to Manufactured Titanium Dioxide Nanoparticles: Comparison of Size Effects Through Different Exposure Routes . Nanotoxicology , 1 : 211 – 226 .
- Guichard , J. C. 1976 . “ Aerosol Generation Using Fluidized Beds ” . In Fine Particles: Aerosol Generation, Measurement, Sampling, and Analysis , Edited by: Liu , B. Y. H. 173 – 194 . New York : Academic Press .
- Gutierrez , L. , Gomez , L. , Irusta , S. , Arruebo , M. and Santamaria , J. 2011 . Comparative Study of the Synthesis of Silica Nanoparticles in Micromixer-Microreactor and Batch Reactor Systems . Chem. Eng. J., , 171 : 674 – 683 .
- Hinds , W. C. 1999 . Aerosol Technology , New York : Wiley .
- Jennerjohn , N. , Eiguren-Fernandez , A. , Prikhodko , S. , Fung , D. C. , Hirakawa , K. S. Zavala-Mendez , J. D. 2010 . Design, Demonstration and Performance of a Versatile Electrospray Aerosol Generator for Nanomaterial Research and Applications . Nanotechnology, , 21 : 255603
- Jensen , K. A. , Koponen , I. K. , Clausen , P. A. and Schneider , T. 2009 . Dustiness Behavior of Loose and Compacted Bentonite and Organoclay Powders: What is the Difference in Exposure Risk? . J. Nanopart. Res., , 11 : 133 – 146 .
- John , W. 1993 . “ The Characteristics of Environmental and Laboratory-Generated Aerosols ” . In Aerosol Measurement: Principles, Techniques, and Applications , Edited by: Willeke , K. and Baron , P. A. 55 New York : Van Nostrand Reinhold .
- Kreyling , W. G. , Biswas , P. , Messing , M. E. , Gibson , N. , Geiser , M. Wenk , A. 2011 . Generation and Characterization of Stable, Highly Concentrated Titanium Dioxide Nanoparticle Aerosols for Rodent Inhalation Studies . J. Nanopart. Res., , 13 : 511 – 524 .
- Kruis , F. E. , Fissan , H. and Peled , A. 1998 . Synthesis of Nanoparticles in the Gas Phase for Electronic, Optical and Magnetic Applications: A Review . J. Aerosol Sci., , 29 : 511 – 535 .
- Lind , T. , Danner , S. and Guentay , S. 2010 . Monodisperse Fine Aerosol Generation Using Fluidized Bed . Powder Technol., , 199 : 232 – 237 .
- Liu , B. Y. H. and Lee , K. W. 1975 . An Aerosol Generator of High Stability . Am. Ind. Hyg. Assoc. J., , 36 : 861 – 865 .
- Liu , W. , Mazumdar , S. , Zhang , Z. , Poussou , S. B. , Liu , J. Lin , C. H. 2012 . State-of-the-Art Methods for Studying Air Distributions in Commercial Airliner Cabins . Build Environ., , 47 : 5 – 12 .
- Lushnikov , A. A. 2010 . “ Introduction to Aerosols ” . In Aerosols – Science and Technology , Edited by: Agranovski , I. 1 – 37 . Weinheim : Wiley-VCH .
- MacMillan , A. C. , Morrison , J. B. , Harmon , C. W. and Nizkorodov , S. A. 2012 . Enhancement of Surfactants in Nanoparticles Produced by an Electrospray Aerosol Generator . Aerosol Sci. Technol., , 46 : 1239 – 1245 .
- Myojo , T. , Oyabu , T. , Nishi , K. , Kadoya , C. , Tanaka , I. Ono-Ogasawara , M. 2009 . Aerosol Generation and Measurement of Multi-Wall Carbon Nanotubes . J. Nanopart. Res., , 11 : 91 – 99 .
- Pratsinis , S. E. 1988 . Simultaneous Nucleation, Condensation and Coagulation in Aerosol Reactors . J. Coll. Int. Sci., , 124 : 416 – 427 .
- Pratsinis , S. E. , Kodas , T. T. , Dudukovic , M. P. and Friedlander , S. K. 1986 . Aerosol Reactor Design: Effect of Reactor Type and Process Parameters on Product Aerosol Characteristics . Ind. Eng. Chem. Process Des. Dev., , 25 : 634 – 642 .
- Prenni , A. J. , Siefert , R. L. , Onasch , T. B. , Tolbert , M. A. and DeMott , P. J. 2000 . Design and Characterization of a Fluidized Bed Aerosol Generator: A Source for Dry, Submicrometer Aerosol . Aerosol Sci. Technol., , 32 : 465 – 481 .
- Rosati , J. A. , Leith , D. and Kim , C. S. 2003 . Monodisperse and Polydisperse Aerosol Deposition in a Packed Bed . Aerosol Sci. Technol., , 37 : 528 – 535 .
- Savolainen , K. , Alenius , H. , Norppa , H. , Pylkkänen , L. , Tuomi , T. and Kasper , G. 2010 . Risk Assessment of Engineered Nanomaterials and Nanotechnologies: A Review . Toxicology, , 269 : 92 – 104 .
- Schmoll , L. H. , Elzey , S. , Grassian , V. H. and O’Shaughnessy , P. T. 2009 . Nanoparticle Aerosol Generation Methods from Bulk Powders for Inhalation Exposure Studies . Nanotoxicology, , 3 : 265 – 275 .
- Tsai , C. , Lin , G. , Liu , C. , He , C. and Chen , C. 2012 . Characteristics of Nanoparticles Generated from Different Nano-Powders by Using Different Dispersion Methods . J. Nanopart. Res., , 14 : 777
- Van Ommen , J. R. , Valverde , J. M. and Pfeffer , R. 2012 . Fluidization of Nanoparticles: A Review . J. Nanopart. Res., , 14 : 737 – 766 .
- Vincent , J. H. 2007 . Aerosol Sampling: Science, Standards, Instrumentation and Applications , Chichester : Wiley .
- Wang , C. S. 2005 . Inhaled Particles , Amsterdam : Elsevier .
- Wang , J. , Liu , J. , Zhang , G. , Zhou , J. and Cen , K. 2011 . Orthogonal Design Process Optimization and Single Factor Analysis for Bimodal Acoustic Agglomeration . Powder Technol., , 210 : 315 – 322 .
- Wang , Z. , Kwauk , M. and Li , H. 1998 . Fluidization of Fine Particles . Chem. Eng. Sci., , 53 : 377 – 395 .
- Yao , W. , Guangsheng , G. , Fei , W. and Jun , W. 2002 . Fluidization and Agglomerate Structure of SiO2 Nanoparticles . Powder Technol., , 124 : 152 – 159 .