ABSTRACT
The aim of this study is to investigate the effect nanosilica and nanoalumina has on nanoparticle release from industrial nanocomposites due to drilling for hazard reduction whilst simultaneously obtaining the necessary mechanical performance. This study is therefore specifically designed such that all background noise is eliminated in the measurements range of 0.01 particles/cm3 and ±10% at 106 particles/cm3. The impact nano-sized SiO2 and Al2O3 reinforced polyester has on nanoparticle aerosols generated due to drilling is investigated. Real-time measurement was conducted within a specially designed controlled test chamber using a condensation particle counter (CPC) and a scanning mobility particle sizer spectrometer (SMPS). The results show that the polyester nanocomposite samples displayed statistically significant differences and an increase in nanoparticle number concentration by up to 228% compared to virgin polyester. It is shown that the nanofillers adhered to the polyester matrix showing a higher concentration of larger particles released (between 20 – 100 nm). The increase in nanoparticle reinforcement weight concentration and resulting nanoparticle release vary considerably between the nanosilica and nanoalumina samples due to the nanofillers presence. This study indicates a future opportunity to safer by design strategy that reduces number of particles released concentration and sizes without compromising desired mechanical properties for engineered polymers and composites.
© 2017 American Association for Aerosol Research
EDITOR:
1. Introduction
The use of nanofillers in polymer nanocomposites has allowed for extensive improvement in targeting material properties with great control and precision. Polyester based nanocomposites are utilized in lightweight applications where nanofillers are used to improve mechanical (Shokrieh et al. Citation2013; Baskaran et al. Citation2011), thermal (Chen et al. Citation2003; Leszczyńska et al. Citation2007), electrical (Paszkiewicz et al. Citation2012) and optical (Zhao et al. Citation2007; Zhou et al. Citation2003) properties. A study carried out by Piccino et al. (Citation2012), surveyed companies' estimates on production of various nanomaterials and found that most companies estimated a median of 5500 tons/year of nanosilica and 550 tonnes/year of nanoalumina were produced within Europe. The introduction of these materials into the workplace institutes conceivable health risks and toxicity when human exposure is concerned (Ding et al. Citation2016; Njuguna et al. Citation2009).
Through various toxicity mechanisms relating to nanoparticle exposure, nanosilica has reported to increase oxidative stress (Lin et al. Citation2006; Eom and Choi Citation2009) and pro-inflammatory responses (Park and Park Citation2009; Kaewamatawong et al. Citation2006). An extensive review focused on inhalation exposure to nano-sized silica by Rabolli et al. (Citation2010) encapsulates the hazard and physico-chemical properties of nanosilica that can affect cytotoxicity with studies linking nanosilica to causing silicosis, chronic obstructive pulmonary disease (COPD) and pulmonary tuberculosis (Calvert et al. Citation2003). Equally, aluminum oxide nanoparticles (alumina) are increasingly being investigated for toxicity. Studies have shown nanoalumina to cause cellular toxicity and increase in oxidative stress (Alshatwi et al. Citation2013), and a study in mice has shown nanoalumina to increase the lactate dehydrogenase level in the blood and induced the development of a pathological lesion in the liver and kidneys (Park et al. Citation2015). Studies by Zhang et al. (Citation2013) and Zhang et al. (Citation2011) have shown nanoalumina to have neurotoxicity effects inducing cell necrosis and apoptosis. Hence, it is generally agreed upon throughout literature that nanosilica and nanoalumina particles have shown toxic effects. Studies into the human occupational exposure possibilities to the particles are, however, rare in literature.
Various studies have looked into nanoparticle aerosol release due to various mechanical processes such as cutting (Methner et al. Citation2012), abrasion (Schlagenhauf et al. Citation2012), sanding (Saber et al. Citation2012), sawing (Gomez et al. Citation2014), drilling (Sachse et al. Citation2012a,Citationb), production (Spinazze et al. Citation2016) and direct handling (Ding et al. Citation2015) just to name a few. Froggett et al. (Citation2014) summarized the existing release studies from mechanical scenarios, highlighting the current gap in knowledge with 54 publications covering the release from solid non-food nanocomposites. From the experimental studies, 96% demonstrated release of nanomaterial from the nanocomposites (Froggett et al. Citation2014). Both review articles agreed on a lack of systematic harmonized methods to compare the results and identified the need of a standardized method to test or characterize the release and exposure of nanoparticles from nanomaterials during a lifecycle scenario. Drilling is a fundamental and significant machining process used during assembly operations. In a review on the effects of drilling on nanocomposites (Starost and Njuguna Citation2014; Starost et al. Citation2015), five studies were identified to have investigated the release of nanoparticles from nanocomposite materials (Bello et al. Citation2010; Sachse et al. Citation2012a,Citationb; Irfan et al. Citation2013; Starost et al. Citation2017). All five studies demonstrated nano-sized aerosols to be released due to the drilling. In one of the studies by Sachse et al. (Citation2012a), nanosilica filled nanocomposites demonstrated 56 times the nano-emissions than the non nano-filled reinforcement. In a study by Bello et al. (Citation2010), CNTs were revealed in the emissions after drilling on CNT-alumina and CNT-carbon nanocomposites. With a similar study using cutting, drilling demonstrated significant differences and an increase in overall nanoparticle release (Bello et al. Citation2009). In the study by Irfan et al. (2013), polyamide-silica nanocomposites displayed up to ten times more nanoparticles generated than from polypropylene materials.
Polyester is one of the most widely used composite materials in polymer engineering especially in the energy industry. With a better understanding of the aerosol emissions and exposure introduced from nanocomposites, materials can be manufactured to be safer by design. The knowledge on aerosol release can be used towards developing materials which will reduce the release of the toxic nanoparticles and hence, safer for workers and consumers. It is now recognized that safer by design allows bridging the gap between the rapid developments in nanotechnology and nanosafety concerns (Njuguna et al. Citation2014). At present, however, there is a lack of knowledge on aerosol nanorelease and its mechanism from polyester nanocomposites undergoing industrial machining such as mechanical drilling process.
The aim of this study is therefore to investigate the effect nanosilica and nanoalumina has on nanoparticle release from industrial nanocomposites due to drilling for exposure reduction whilst simultaneously obtaining the necessary mechanical performance. The work stems from the fact that it is difficult to compare particle number concentrations in the literature due to the inability to conceal background influence and noise in nanoparticles aerosols measurements. This is mainly because there is currently no common methodology used in the past that works effectively and reported studies have used various machining techniques, dissimilar composite materials and influencing background particle number concentrations. The studies on drilling on nanocomposites thus far have revealed that nanoparticle fillers do have an effect on nanoparticle aerosol emissions. The sampling and methodology undertaken were developed as a part of a controlled drilling protocol within the European Commission Life+ project named Simulation of the release of nanomaterials from consumer products for environmental exposure assessment (SIRENA, Pr. No. LIFE 11 ENV/ES/596) with the sole intention of testing these nanocomposites for nanoparticle release.
2. Materials and methods
2.1. Materials and samples preparation
A commercially available unsaturated orthophthalic polyester from Gazechim Composites (RESICHIM-Resina Poliéster) was chosen as the matrix polymer due to its common use within industries such as the energy industry. The polyester was reinforced with unmodified nano silicon dioxide (SiO2 61Va11 Type 1 from TORRECID S.A.) and nano aluminum oxide (Al2O3 30VA12 Type 1 from TORRECID S.A.). Two weight concentrations of 2 wt. % and 5 wt. % of SiO2, and 2 wt.% and 5 wt.% of Al2O3 were chosen based on material performance (Liu and Kontopoulou Citation2006; Allahverdi et al. Citation2012). The SiO2 and Al2O3 nanofillers were added to the liquid polyester resin (Cobalt salt pre-accelerated resin combined with a tyxotropic agent) and the samples were prepared using a dispermat high speed mixer to create a homogeneous concentration within the polyester resin, followed by casting processes. The materials were cured at room temperature in a mould. A common sample size of 70 × 45 × 5 mm were prepared for the drilling tests. The corresponding standard of 100 × 80 × 4 mm sample size was fabricated for the flexural testing ISO 178 (ISO B. 2010) and Shore D hardness test (ASTM D2240–15, 2015).
2.2. Automated drilling process: Drilling setup, instrumentation, and measurement procedure
Building on previous studies (Sachse et al. Citation2012a,Citationb), the drilling studies were carried out by drilling across the width of the sample resulting in eight holes and bearing a time duration of 3 min. In a typical procedure the particle number concentration was gathered using a TSI Environmental Particle Counter (CPC) model 3783 at a flow rate of 0.6 LPM, particle range of 7–3000 nm and concentration range of 0–106 particles/cm3 with false background counts <0.01 particles/cm3 and ±10% at 106 particles/cm3. The particle size distribution was measured using a scanning mobility particle sizer spectrometer (SMPS). The SMPS used for the study is a TSI 3080 Electrostatic Classifier utilizing a nano differential mobility analyser (DMA) with 99 distinct particle diameters within a particle range of 4.61 – 156.8 nm and a flow rate of 0.31 LPM. The SMPS is the commonly used aerosol nanoparticle sizer in literature although it has limitations for fast changes in the particle size distributions due to its time resolution (Kuhlbusch et al. Citation2011). The data collected from the SMPS produces a representation of the particle size distribution over a 45 s period followed by 10 s for the classifier to regenerate to its initial voltage and 5 s to start the size distribution again. This gives a 1 minute sampling period and therefore three particle size distributions across the 3 minute drilling. The eight holes drilled per sample were repeated three times to get a statistical average of the aerosols released.
The chamber designed for this study was capable of achieving a completely clean environment with concentration of particle stability of limit of detection (LOD) 0.01 particles/cm3 monitored using the CPC, removing any background noise or interference on the number concentration and particle size distribution readings. The data collected therefore is a true representation of the particles released solely from the material. A closed stainless steel chamber with dimensions of 740 mm x 550 mm x 590 mm, and therefore a total inner volume of 0.240 m3, was used to assure a closed environment to simulate an appropriate volume around the drill and minimizing electrostatic attraction to the surfaces. To obtain the clean environment, the chamber was initially cleared of particles before each test through an inflow of clean air with the use of TSI 99.97% retention HEPA Capsule Filters. A separate capsule, as shown in , was constructed around the drill with separate air flow to avoid any interference of the drilling fumes on the particle number concentration within the capsule. The chamber inlet and outlet were used when flushing the chamber with clean air to obtain the clean environment.
Figure 1. Design of drilling setup within enclosed test chamber with cycled airflow to allow for a clean environment removing any background interference.
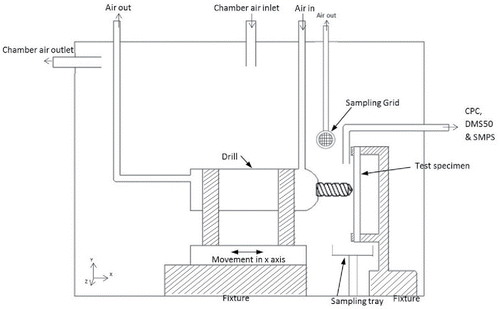
A Dremel 4000 drilling tool with an industrial standard stainless steel 3.5 mm twist drill bit was used at 10000 rpm with a feed rate of 78 mm/min. These drilling setup and parameters were selected based on industrial specifications, literature available and previous studies carried out on the drilling damage on the polyester samples (Sachse et al. Citation2012a,b; Bello et al. Citation2010; Starost et al. Citation2015). In order to have a repeatable and controlled setup, the drill is placed on an automated assembly operated via an external computer that controlled the feed rate in the x axis, and the sample was moved in the z axis to allow for multiple holes to be drilled. An outlet channel is placed adjacent to the test specimen for the nanoparticle release equipment readings. A sampling grid for post-test analysis and characterization of the airborne particles was placed next the test specimen with a slight suction to attract and prevent particles from detaching away from the grid. An additional sampling tray was positioned below the test specimen for collection of the deposited particles for further post-test analysis. The setup is designed to meet the recommendations for measurement and data analysis introduced in a paper attempting to harmonize measurement strategies for exposure to manufactured nano-objects (Brouwer et al. Citation2012). Beneficial as verification, studies have evaluated and as documented by Hornsby and Pryor (Citation2014) the limitations and deficiencies of current nano-sized aerosol measurement techniques, and how they may differ to actual lung-deposited particles (Leavey et al., Citation2013).
2.3. Mechanical testing
As to validate the improved properties and to support the link between mechanical performance and the nanoparticle release of the materials, the samples underwent a flexural 3-point bend test and hardness test in accordance to ISO 178 at 2 mm/min and Shore D reference standards, respectively (ISO B. 2010; ASTM D2240–15, 2015). The introduction of the nanofillers demonstrated an increased flexural performance of the nano-filled samples without having any effect on the hardness with a constant shore C value of 75 for the three samples.
3. Results and discussion
3.1. Filler effect on particle number concentration
The polyester nanocomposite samples underwent the replicated drilling setup as described. In comparison to the neat polyester sample, the introduction of the SiO2 and Al2O3 nanofillers were noted to have an effect on the nanoparticle aerosol release from drilling operation. An image of the number of visible particles generated is displayed in .
The averages of the particle number concentration released from the three samples are shown in . The peaks in exemplified across the three minutes clearly highlight the 8 holes being drilled. Visible on most of the peaks, the movement of the drill entering and withdrawing the sample can also be seen from peaks being faintly divided into two parts each. The drilling can be seen to release a substantial quantity of nanoparticles for all three samples. When the drill bit is out of the sample, the particle concentration is seen to drop between each hole being drilled. The mechanical drilling can therefore be seen to generate a substantial quantity of nanoparticles into the environment, which then quickly disperse inside the chamber. The particle number concentration was perceived to relatively stabilize during the 1 minute of recorded data after the drilling was completed, but remained at considerably higher particle number concentration than before drilling had started. Thus, the nanoparticles released from the drilling remained airborne and dispersed throughout the chamber.
Figure 3. Particle number concentration averages of polyester-based nanocomposites recorded using the CPC.
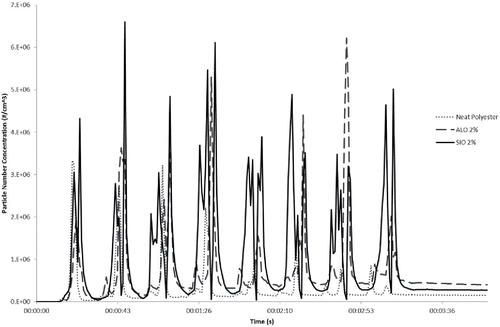
Over the eight holes, the two nanofilled polyester sample averages demonstrated higher nanoparticle peaks (PE/SiO2 nanocomposites 6.6 × 106 #/cm3, PE/Al2O3 nanocomposites 6.2 × 106 #/cm3) than the neat polyester sample (3.3 × 106 #/cm3). Few studies have produced data of the actual release of particles at the time of the machining. These results clearly demonstrate the immediate release of nanoparticles from the sample due to drilling. Over the 4th minute once drilling was concluded, these results traits are in accordance with Sachse et al. (Citation2012b) in which PE/SiO2 nanocomposites demonstrated 56 times the nano-emissions than the pristine polyester samples. However, in Sachse et al., the background noise was not accounted for, and repeated that so far it is difficult to compare particle number concentrations as no common methodology has been used in the past that works effectively mainly due to the inability to conceal background influence and noise. Previous studies have also used various machining techniques, dissimilar composite materials and the influencing background particle number concentrations. Hence this current study eliminates all the background noise in the measurements allowing for comparable data between studies.
The nanofillers demonstrated an increase in particle number concentration. Between the PE/SiO2 and PE/Al2O3, the PE/SiO2 nanocomposites recorded a higher average concentration during the three minutes of drilling. However, the PE/Al2O3 nanocomposites demonstrated a slightly higher particle number concentration during the 1 minute following the drilling conclusion. Although a higher concentration of particles was emitted from the PE/SiO2 nanocomposites during the drilling, the particles from the aluminum oxide PE/Al2O3 nanocomposites remained airborne for longer and displayed a 22% higher particle number concentration following the conclusion of the drilling (PE/Al2O3 = 4.3 × 105 #/cm3, PE/SiO2 = 3.52 × 105 #/cm3). Across the entire 4 min, the aluminum oxide produced a 136% increase in particle number concentration compared to the neat polyester, as shown in . The silicon dioxide sample produced a further 228% increase compared to the neat polyester, also shown in . The nanofillers can therefore be seen to have a substantial escalation in the particle number concentration throughout the entire 4 min for particles ranged 7–3000 nm.
The use of nanosilica and nanoalumina is established to improve the mechanical properties of the polyester. Nevertheless, a small addition of the nanofillers provided significant influence on the release material composition. Although, the aluminum oxide reinforced sample presented the greatest flexural strength over the nanosilica and neat polyester samples, the sample released the medium peak nanoparticle concentration number. The aluminum oxide reinforced sample exposed a different release composition to the two other samples, as it had the highest quantity of remaining airborne particles after the drilling had finished (PE = 2.1 × 105 #/cm3, PE/Al2O3 = 4.3 × 105 #/cm3, PE/SiO2 = 3.52 × 105 #/cm3). Therefore, along with the quantity of nanoparticles released, the data represented from the CPC, as shown in , also allude to the particle characteristics due to the disparate rapidity of dispersion and particle deposition.
Two distinct concentrations of the reinforced samples were fabricated in order to investigate the effect of the nano-filler weight percentage on nanorelease. illustrates the effect for the aluminum oxide reinforced polyester sample. The data in displays the increase of alumina nano-filler demonstrated a miniature difference in the particle number concentration. The increased concentration of the 5 wt. % exhibited a 33% increase in particle number concentration during the peaks (2 wt. % Al2O3 at 3.6 × 106 #/cm3 and 5 wt. % Al2O3 at 4.7 × 106 #/cm3) and at the conclusion of the drilling during the 1-minute post drilling (2 wt. % Al2O3 at 4.0 × 105 #/cm3 and 5 wt. % Al2O3 at 4.7 × 105 #/cm3). The concentration at the end of the 4 minutes of the 5 wt. % alumina sample represented a 19% increase in particle number concentration from the 2 wt. % alumina sample.
Figure 4. Average particle number concentration of 2 wt. % Al2O3 and 5 wt. % Al2O3 reinforced polyester nanocomposites recorded on CPC.
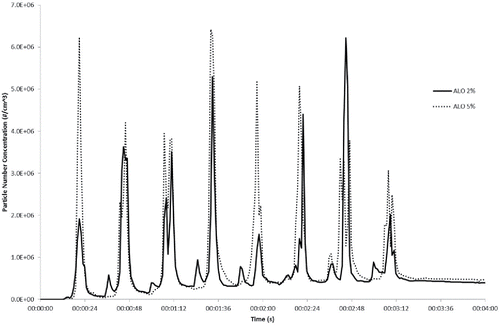
The effect of the filler on mechanical properties can be directly related to the effect on nanoparticle release. The 2 wt. % alumina sample has an inconsequential reduction of flexural strength of around 20 MPa from the 5% alumina sample (a reduction of around 1%), but an improved impact resistance of 6.9 KJ/m2 in comparison to 3.5 KJ/m2 for the 5 wt. % alumina sample. A 1% reduction in flexural strength of the 2 wt. % alumina sample, exhibited a 33% decrease in particle number concentration from the 5 wt. % alumina sample. This correlation between the material's mechanical performance and nanoparticle release is essential when considering materials safer by design.
The comparison of two concentrations of the PE/SiO2 nanocomposites was also carried out. The particle number concentration release from the silica samples, shown on , can be seen to have an inverse correlation on the nanoparticle release compared to the alumina nanofiller, shown in . The increase to 5 wt. % of the nanosilica filler displayed an average decrease of 70% of nanoparticles introduced across the eight peaks of particles released. Furthermore, an average 94% decrease of particle number concentration was observed at the end of the 4-min sampling period for the 5 wt. % nanosilica sample. In spite of this, the increase in nanoparticle reinforcement displayed no evident influence on the flexural strength which remained the same at 3200 MPa, and the impact energy decreased from 7.2 KJ/m2 to 6.2 KJ/m2 for the 2 wt. % and 5 wt. %, respectively. Therefore, the marginal influence in mechanical properties can be seen to have a reduction on the nanoparticle release.
Figure 5. Average particle number concentration of 2 wt. % SiO2 and 5 wt. % SiO2 reinforced polyester nanocomposites as recorded on CPC.
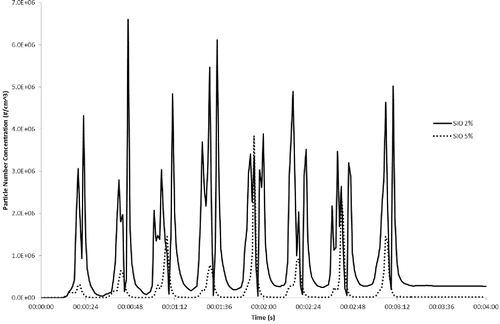
With an increase in nanoparticles embedded within the material, one would expect a resulting increase in nanoparticle release. However, the increase in nanosilica may have further molecular effects to the structure of the material, such as reforming the embedding and bonding of the nanoparticles to the nanocomposite or bonding/agglomeration variations which may cause the release of larger micro-sized particles. This may be the cause for the contrasting influences in results between the nanosilica and nanoalumina reinforced samples. Based on this study, a rise in nanoparticle filler wt. % content in the matrix may either augment or reduce the quantity of nanoparticles released. The corresponding result on particle number concentration released is therefore more dependent on the matrix-filler bonding and consequent material structure, instead of solely the quantity of nanofiller weight percentage embedded within.
displays the statistical analysis carried out on the peak particle number concentrations of the samples. The data represents the statistical differences between the peak concentrations introduced due to drilling. The calculated lower tail of 5% and upper tail of 95% give a representation of the data for a 90% confidence interval of a t-distribution. This highlights the disparities between the peak particle number concentrations and therefore, a statistically significant difference with the introduction of nanofillers on release in comparison to the neat polyester. A two sample t-test of significance of each sample mean and deviation to the neat polyester sample returned statistically significant differences for all samples except for the PE/SiO2 5% which demonstrated to be within a 95% confidence interval of the PE sample (statistically insignificant). Equally, the increase in nanofiller weight concentration demonstrated a statistically significant difference in comparison to the lower weight concentration for both SiO2 and Al2O3. ANOVA single factor analysis was performed to assess the variability between the sample peak means introduced due to the filler. The analysis returned statistically significant differences within the 5 samples (F value = 9.68 F critical value = 2.64) and a 0.22% chance that the observation could have been observed due to random error alone and therefore rejecting a hypothesis that the samples displayed no difference.
Table 1. Inferential statistical representation of the particle number concentrations introduced at the peaks due to the drilling. Lower and upper limits represent the values of a 90% confidence interval on a sampling t-distribution.
This data set and correlation between the nanofiller concentration, nanoparticle release and mechanical properties may be used when improving materials safer by design. It follows that the means for hazard reduction whilst simultaneously obtaining the necessary mechanical performance is a growing challenge and an opportunity likewise in nanocomposite materials manufacturing. The reduction in nanoparticle number concentration can be used towards developing less hazardous silica reinforced composites. The study correlates with the literature, e.g., in a study by Reijnders (Citation2009) that considered various options at hazard reduction for nanosilica reinforced nanocomposites. A minor increase or decrease in nanofiller may end up reducing the nanoparticle release hazard, without having a significant effect on mechanical properties if Safer by Design principles are followed during material development.
3.2. Filler effect on particle size distribution
With a sampling period of 1 min, an average of the 4 data sets from the SMPS across the 4 min for each sample is displayed in . The particle size distribution data illustrates little contrast between the three samples in the sizes of the nanoparticles released. However, the data accentuates the large particle number concentration disparity between the samples as shown in the CPC data in . The larger particle number concentration released from the silicon dioxide sample is clearly visible over the aluminum oxide and neat polyester samples. Nonetheless, two of the peak size distributions are indicated to be around the same particle diameters.
All three samples displayed particle number concentration peaks at 10 nm and 30 nm. The nano-filled samples revealed a third peak between 60–70 nm. The nanofillers can therefore be apparent to introduce a concentration of larger sized nanoparticles. The average particle diameter weighed against the concentration released from the neat polyester sample, 27 nm, is 23% smaller than the PE/Al2O3, 34 nm, and 50% smaller than the PE/SiO2, 53 nm. In one previous study (Sachse et al. Citation2012b), that investigated the effect of nanosilica on nanoparticle release reported that a principal peak release at 30 nm particle diameter at the highest concentration of release within a particle size range of 5.6–1083 nm. The further two diameter peaks seen in the size distributions in were not reported. The third peak at 60–70 nm may therefore be as a result of polymer matrix-filler embedment since a different matrix has been used in the present study. A comparison between the two studies suggests that the matrix has a meaningful influence on the size of the nanoparticles released. It is noteworthy that the polyester matrix released identifiable nanoparticles (although not nano sized in origin) as shown in the particle size distribution in Sachse et al. (Citation2012a,Citationb), and as shown in the CPC data in .
Figure 7. Average particle size distributions collected on SMPS of 2 wt. % Al2O3 and 5 wt. % Al2O3 reinforced polyester nanocomposite samples.
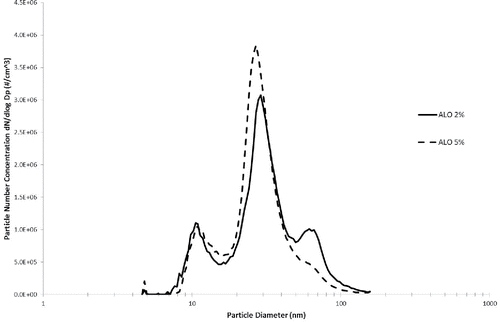
The effect of weight percentage of nanofiller on nanoparticle release was also investigated. The two concentrations of alumina demonstrated that an increase to 5 wt. % from 2 wt. % displayed an increase in particle number concentration. A comparison of the two particle size distributions is shown in .
The two samples demonstrated similar particle size distributions. Both samples presented peaks at 10 nm and 30 nm. A third peak at 60 nm is more visible for the 2 wt. % sample than a diminished peak for 5 wt. % sample. The largest quantity of particles for both samples was witnessed to be around 27 nm. The average particle diameter weighed against the concentration released from the 2 wt. % PE/Al2O3 sample is a minor increase to 35 nm from the 30 nm for the 5 wt. % PE/Al2O3. However, PE/Al2O3 (5 wt. %) nanocomposites released a 25% greater average of particle number concentration at 27 nm compared to the 2 wt. % sample as shown in . When linking to the SMPS data, the increase in particle number concentration observed in the CPC data, shown in , can be understood to be due to the increase of particles around 30 nm. Given that the average particle size of the nanoalumina is less than 50 nm, the peak observed may be the release of the independent nanofillers. The increase in weight percentage concentration of the nanofiller could potentially be increasing the release of liberated nanofiller, although this was not confirmed in the microscopy analysis.
The concentration of the alumina nanofiller has an effect on the particle number concentration and corresponding particle size distributions. The improved mechanical properties of the 2 wt. % from the 5 wt. % silica reinforcement also demonstrated a decrease in particle number concentration of the potentially hazardous 30 nm. When considering the fabrication of alumina reinforced materials safer by design, the particle number concentration release and corresponding size distributions are two parameters to consider minimalizing nanotoxicological risks. The comparison of the two nanosilica weight percentage concentrations is illustrated in .
Figure 8. Average particle size distributions collected on SMPS of 2 wt. % SiO2 and 5 wt. % SiO2 reinforced polyester nanocomposite samples.
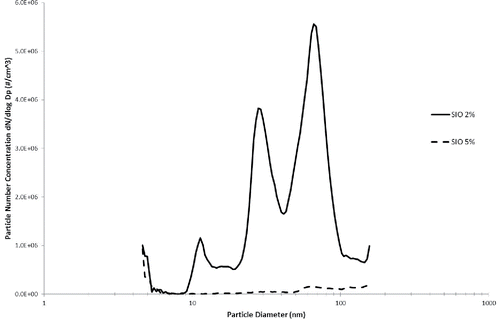
The average decrease of 70% of nanoparticle concentration introduced with the increase to 5 wt. % of the nanosilica filler witness in , is even more evident in the particle size distribution shown in . Although the 2 wt. % PE/SiO2 has a similar average particle diameter weighed against the concentration released of 53 nm compared to 58 nm of the 5 wt. % PE/SiO2 sample, the particle number concentration difference is clearly apparent. If taking into consideration particle number concentration alone as a nanotoxicology factor, the nanosilica demonstrated that the increased weight percentage displays a reduced risk to nano-sized particles in contrast to the alumina nanofiller results shown in . A reduced particle number concentration can be presupposed to have a direct reduction in exposure to the nanoparticles. However, the sample still exhibited a high concentration of nanoparticles at the lower end of the spectrum, at 5 nm. With a slightly improved performance in release energy, the 2 wt % sample presented an intensified release of nanoparticles. These factors are therefore vital and should be considered when fabricating materials safer by design.
4. Conclusion
Three polyester based nanocomposites were fabricated with two different nanofillers. The mechanical properties were improved from the neat polyester with the reinforced 2 wt. % and 5 wt. % aluminum oxide, and 2 wt. % and 5 wt. % silicon dioxide. All samples tested, including the neat polyester, revealed that nanoparticle emissions were generated and released from the sample during the drilling process. Across the entire 4 minutes of simultaneous drilling and particles measurement, the reinforced aluminum oxide and the silicon dioxide samples produced an increase of 136% and 228% respectively in particle number concentration compared to the neat polyester. The different concentrations of nanofiller displayed inverse results with the alumina releasing an increase in nanoparticles with the 5 wt. % reinforced sample, whereas the silica revealed a decreasing effect in nanoparticles released.
The particle emissions for the materials studied demonstrated that the nanofilled polyester nanocomposites produced a substantial escalation in particle number concentration and therefore have a detrimental effect on nanoparticle release. The significant difference between the three materials must be considered when implementing materials safer by design. As no smaller particle diameter peaks are seen in the release in the two nano-filled samples, there is no evidence that the nanofillers are released from the matrix and it is apparent that the nanofillers are adhering to and embedded within the polyester matrix. The correlation between increase in nanoparticle reinforcement weight percentage and nanoparticle release can be seen between the PE/SiO2 and PE/Al2O3 nanocomposite samples. The two nanofillers displayed almost an inverse correlation with the higher weight percentage of nanofiller.
Acknowledgments
The authors would like to acknowledge K. Tirez and R. Persoons at Vito for their XRF and SEM support.
Funding
The work is funded by and part of the European Commission Life+ project named “Simulation of the release of nanomaterials from consumer products for environmental exposure assessment” (SIRENA, Pr. No. LIFE 11 ENV/ES/596). J. Njuguna is thankful to the funding by QualityNano Project through Transnational Access (TA Application VITO-TAF-382 and VITO-TAF-500) under the European Commission, Grant Agreement No: INFRA-2010-262163 for the access and use of the facilities at the Flemish Institute for Technological Research (VITO). K. Starost is also thankful for partial funding by the School of Engineering for his studentship.
References
- Allahverdi, A., Ehsani, M., Janpour, H., and Ahmadi, S. (2012). The Effect of Nanosilica on Mechanical, Thermal and Morphological Properties of Epoxy Coating. Prog. Org. Coat., 75(4):543–548.
- Alshatwi, A. A., Subbarayan, P. V., Ramesh, E., Al-Hazzani, A. A., Alsaif, M. A., and Alwarthan, A. A. (2013). Aluminium Oxide Nanoparticles Induce Mitochondrial-Mediated Oxidative Stress and Alter the Expression of Antioxidant Enzymes in Human Mesenchymal Stem Cells. Food Addit. Contam.: Part A, 30(1):1–10.
- Baskaran, R., Sarojadevi, M., and Vijayakumar, C. (2011). Unsaturated Polyester Nanocomposites Filled with Nano Alumina. J. Mater. Sci., 46(14):4864–4871.
- Bello, D., Wardle, B. L., Yamamoto, N., deVilloria, R. G., and Hallock, M. (2009). Exposures to Nanoscale Particles and Fibers During Handling, Processing, and Machining of Nanocomposites and Nanoengineered Composites Reinforced with Aligned Carbon Nanotubes. 17th International conference on composite materials (ICCM) proceedings, Edinburgh, Scotland.
- Bello, D., Wardle, B. L., Zhang, J., Yamamoto, N., Santeufemio, C., Hallock, M., and Virji, M. A. (2010). Characterization of Exposures to Nanoscale Particles and Fibers During Solid Core Drilling of Hybrid Carbon Nanotube Advanced Composites. Int. J. Occup. Environ. Health, 16(4):434–450.
- Brouwer, D., Berges, M., Virji, M. A., Fransman, W., Bello, D., Hodson, L., Gabriel, S., and Tielemans, E. (2012). Harmonization of Measurement Strategies for Exposure to Manufactured Nano-Objects; Report of a Workshop. Ann. Occup. Hyg., 56(1):1–9.
- Calvert, G. M., Rice, F. L., Boiano, J. M., Sheehy, J. W., and Sanderson, W. T. (2003). Occupational Silica Exposure and Risk of Various Diseases: An Analysis Using Death Certificates from 27 States of the United States. Occup. Environ. Med., 60(2):122–129.
- Chen, X., Wu, L., Zhou, S., and You, B. (2003). In Situ Polymerization and Characterization of Polyester‐Based Polyurethane/Nano‐Silica Composites. Polym. Int., 52(6):993–998.
- Ding, Y., Stahlmecke, B., Jiménez, A. S., Tuinman, I. L., Kaminski, H., Kuhlbusch, T. A., van Tongeren, M., and Riediker, M. (2015). Dustiness and Deagglomeration Testing: Interlaboratory Comparison of Systems for Nanoparticle Powders. Aerosol Sci. Technol., 49(12):1222–1231.
- Ding, Y., Stahlmecke, B., Kaminski, H., Jiang, Y., Kuhlbusch, T. A., and Riediker, M. (2016). Deagglomeration Testing of Airborne Nanoparticle Agglomerates: Stability Analysis Under Varied Aerodynamic Shear and Relative Humidity Conditions. Aerosol Sci. Technol., 50(11):1253–1263.
- Eom, H., and Choi, J. (2009). Oxidative Stress of Silica Nanoparticles in Human Bronchial Epithelial Cell, Beas-2B. Toxicol. Vitr., 23(7):1326–1332.
- Froggett, S. J., Clancy, S. F., Boverhof, D. R., and Canady, R. A. (2014). A Review and Perspective of Existing Research on the Release of Nanomaterials from Solid Nanocomposites. Part. Fibre Toxicol., 11(1):1.
- Gomez, V., Levin, M., Saber, A. T., Irusta, S., Dal Maso, M., Hanoi, R., Santamaria, J., Jensen, K. A., Wallin, H., and Koponen, I. K. (2014). Comparison of Dust Release from Epoxy and Paint Nanocomposites and Conventional Products During Sanding and Sawing. Ann. Occup. Hyg., 58(8):983–994.
- Hornsby, K., and Pryor, S. (2014). A Laboratory Comparison of Real-Time Measurement Methods for 10–100-nm Particle Size Distributions. Aerosol Sci. Technol., 48(5):571–582.
- Irfan, A., Sachse, S., Njuguna, J., Pielichowski, K., Silva, F., and Zhu, H. (2013). Assessment of nanoparticle release from polyamide 6-and polypropylene-silicon composites and cytotoxicity in human lung A549 cells. Journal of Inorganic and Organometallic Polymers and Materials, 23(4):861–870.
- ISO, B. 178: 2010. Plastics–Determination of Flexural Properties. International Standard Organization, Switzerland.
- Kaewamatawong, T., Shimada, A., Okajima, M., Inoue, H., Morita, T., Inoue, K., and Takano, H. (2006). Acute and Subacute Pulmonary Toxicity of Low Dose of Ultrafine Colloidal Silica Particles in Mice After Intratracheal Instillation. Toxicol. Pathol., 34(7):958–965.
- Kuhlbusch, T. A., Asbach, C., Fissan, H., Göhler, D., and Stintz, M. (2011). Nanoparticle Exposure at Nanotechnology Workplaces: A Review. Part. Fibre Toxicol., 8(1):1.
- Leavey, A., Fang, J., Sahu, M., and Biswas, P. (2013). Comparison of Measured Particle Lung-Deposited Surface Area Concentrations by an Aerotrak 9000 Using Size Distribution Measurements for a Range of Combustion Aerosols. Aerosol Sci. Technol., 47(9):966–978.
- Leszczyńska, A., Njuguna, J., Pielichowski, K., and Banerjee, J. (2007). Polymer/Montmorillonite Nanocomposites with Improved Thermal Properties: Part II. Thermal Stability of Montmorillonite Nanocomposites Based on Different Polymeric Matrixes. Thermochim. Acta, 454(1):1–22.
- Lin, W., Huang, Y., Zhou, X., and Ma, Y. (2006). In Vitro Toxicity of Silica Nanoparticles in Human Lung Cancer Cells. Toxicol. Appl. Pharmacol., 217(3):252–259.
- Liu, Y., and Kontopoulou, M. (2006). The Structure and Physical Properties of Polypropylene and Thermoplastic Olefin Nanocomposites Containing Nanosilica. Polymer, 47(22):7731–7739.
- Methner, M., Crawford, C., and Geraci, C. (2012). Evaluation of the potential airborne release of carbon nanofibers during the preparation, grinding, and cutting of epoxy-based nanocomposite material. J. Occup. Environ. Hyg., 9(5):308–318.
- Njuguna, J., Pena, I., Zhu, H., Rocks, S., Blazquez, M., and Desai, S. (2009). Opportunities and Environmental Health Challenges Facing Integration of Polymer Nanocomposites: Technologies for Automotive Applications. Int. J. Appl. Polym. Technol., 12–3.
- Njuguna, J., and Sachse, S. (2014). Measurement and Sampling Techniques for Characterization of Airborne Nanoparticles Released from Nano-Enhanced Products. Health Environ. Saf. Nanomaterials. Polym. Nancomposites Other Mater. Containing Nanoparticles, 78–111.
- Njuguna, J., Pielichowski, K., and Zhu, H. (2014). Health and Environmental Safety of Nanomaterials: Polymer Nancomposites and Other Materials Containing Nanoparticles. Elsevier.
- Park, E., and Park, K. (2009). Oxidative Stress and Pro-Inflammatory Responses Induced by Silica Nanoparticles in Vivo and in Vitro. Toxicol. Lett., 184(1):18–25.
- Park, E., Sim, J., Kim, Y., Han, B.S., Yoon, C., Lee, S., Cho, M., Lee, B., and Kim, J. (2015). A 13-Week Repeated-Dose Oral Toxicity and Bioaccumulation of Aluminum Oxide Nanoparticles in Mice. Arch. Toxicol., 89(3):371–379.
- Paszkiewicz, S., Szymczyk, A., Špitalský, Z., Soccio, M., Mosnáček, J., Ezquerra, T. A., and Rosłaniec, Z. (2012). Electrical Conductivity of Poly (Ethylene Terephthalate)/Expanded Graphite Nanocomposites Prepared by in Situ Polymerization. J. Polym. Sci. Part B: Polym. Phys., 50(23):1645–1652.
- Piccinno, F., Gottschalk, F., Seeger, S., and Nowack, B. (2012). Industrial Production Quantities and Uses of Ten Engineered Nanomaterials in Europe and the World. J. Nanopart. Res., 14(9):1–11.
- Rabolli, V., Thomassen, L. C., Princen, C., Napierska, D., Gonzalez, L., Kirsch-Volders, M., Hoet, P. H., Huaux, F., Kirschhock, C. E., and Martens, J. A. (2010). Influence of Size, Surface Area and Microporosity on the in Vitro Cytotoxic Activity of Amorphous Silica Nanoparticles in Different Cell Types. Nanotoxicology, 4(3):307–318.
- Reijnders, L. (2009). The Release of TiO 2 and SiO 2 Nanoparticles from Nanocomposites. Polym. Degrad. Stab., 94(5):873–876.
- Saber, A. T., Koponen, I. K., Jensen, K. A., Jacobsen, N. R., Mikkelsen, L., Møller, P., Loft, S., Vogel, U., and Wallin, H. (2012). Inflammatory and Genotoxic Effects of Sanding Dust Generated from Nanoparticle-Containing Paints and Lacquers. Nanotoxicology, 6(7):776–788.
- Sachse, S., Silva, F., Irfan, A., Zhu, H., Pielichowski, K., Leszczynska, A., Blazquez, M., Kazmina, O., Kuzmenko, O., and Njuguna, J. (2012a). Physical Characteristics of Nanoparticles Emitted During Drilling of Silica Based Polyamide 6 Nanocomposites. IOP Conference Series: Materials Science and Engineering, IOP Publishing, pp. 012012.
- Sachse, S., Silva, F., Zhu, H., Irfan, A., Leszczyńska, A., Pielichowski, K., Ermini, V., Blazquez, M., Kuzmenko, O., and Njuguna, J. (2012b). The Effect of Nanoclay on Dust Generation During Drilling of PA6 Nanocomposites. J. Nanomaterials, 2012:26.
- Schlagenhauf, L., Chu, B. T., Buha, J., Nüesch, F., and Wang, J. (2012). Release of Carbon Nanotubes from an Epoxy-Based Nanocomposite During an Abrasion Process. Environ. Sci. Technol., 46(13):7366–7372.
- Shokrieh, M. M., Saeedi, A., and Chitsazzadeh, M. (2013). Mechanical Properties of Multi-Walled Carbon Nanotube/Polyester Nanocomposites. J. Nanostruct. Chem., 3(1):1–5.
- Spinazze, A., Cattaneo, A., Campagnolo, D., Bollati, V., Bertazzi, P. A., and Cavallo, D. M. (2016). Engineered Nanomaterials Exposure in the Production of Graphene. Aerosol Sci. Technol., 50(8):812–821.
- Starost, K., Frijns, E., Van Laer, J., Faisal, N., Blazquez, M., and Njuguna, J. (2015). The Effect of Drilling on Nanoparticles Release from Silica and Alumina Reinforced Polyester Nanocomposites. 7th International Symposium on Nanotechnology, Occupational and Environmental Health, Limpopo, South Africa.
- Starost, K., and Njuguna, J. (2014). A Review on the Effect of Mechanical Drilling on Polymer Nanocomposites. IOP Conference Series: Materials Science and Engineering, IOP Publishing, pp. 012031.
- Starost, K., Frijns, E., van Laer, J., Faisal, N., Egizabal, A., Elizextea, A., Nelissen, I., Blazquez, M., and Njuguna, J. (2017). Environmental Particle Emissions due to Automated Drilling of Polypropylene Composites and Nanocomposites Reinforced with Talc, Montmorillonite and Wollastonite. In IOP Conference Series: Materials Science and Engineering (Vol. 195, No. 1, p. 012011). IOP Publishing.
- Zhang, Q., Xu, L., Wang, J., Sabbioni, E., Piao, L., Di Gioacchino, M., and Niu, Q. (2013). Lysosomes Involved in the Cellular Toxicity of Nano-Alumina: Combined Effects of Particle Size and Chemical Composition. J. Biol. Regul. Homeost. Agents, 27(2):365–375.
- Zhang, Q. L., Li, M. Q., Ji, J. W., Gao, F. P., Bai, R., Chen, C. Y., Wang, Z. W., Zhang, C., and Niu, Q. (2011). In Vivo Toxicity of Nano-Alumina on Mice Neurobehavioral Profiles and the Potential Mechanisms. Int. J. Immunopathol. Pharmacol., 24(1 Suppl):23S–29S.
- Zhao, Y., Wang, F., Fu, Q., and Shi, W. (2007). Synthesis and Characterization of ZnS/Hyperbranched Polyester Nanocomposite and Its Optical Properties. Polymer, 48(10):2853–2859.
- Zhou, S., Wu, L., Sun, J., and Shen, W. (2003). Effect of Nanosilica on the Properties of Polyester‐Based Polyurethane. J. Appl. Polym. Sci., 88(1):189–193.