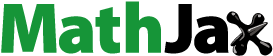
Abstract
To quantify carbon fiber-reinforced plastic (CFRP) fatigue, herein, we investigate the relationship between fatigue and an epoxy resin used in CFRPs. Generally, fatigue is related to the entropy, which comprises the mechanical entropy, calculated from the dissipated energy and temperature, and thermal entropy, calculated from the relationship between specific heat capacity and temperature. According to previous studies, mechanical entropy generation and thermal entropy generation are equal. Herein, 100 cyclic loading tests are conducted on epoxy resin specimens consisting of 4,4’-DDS and bisphenol a diglycidyl ether. The dissipated energy is determined based on stress – strain curves, and mechanical entropy generation is quantified. An equation for the relationship between the specific heat capacity and temperature is developed based on the Debye model, and the increase in specific heat capacity is calculated for equal mechanical and thermal entropy generations. Generally, differential scanning calorimetry is used for specific heat capacity measurements; however, because these measurements are performed by cutting the specimen, a nondestructive measurement method is required. In this study, the specific heat capacity is measured using lock-in thermography (LIT), and the measured and estimated values are comparable. Thus, fatigue can be estimated by quantifying the thermophysical properties, and the lock-in thermography method is a suitable thermophysical property measurement method for this application.
1 Introduction
Carbon fiber-reinforced plastics (CFRPs) are widely used in the aerospace industry and other applications [Citation1,Citation2]. However, the durability of CFRPs is a key issue [Citation3–9]. Generally, CFRP durability depends on the durability of the resin used [Citation9–14]. The most common CFRP resin is the epoxy resin. Generally, transverse cracking occurs in CFRPs owing to fatigue [Citation15–18], which is caused by resin degradation [Citation19–21]. However, the onset of transverse cracking in CFRPs with unknown load histories is difficult to determine.
Some studies have demonstrated that resin damage is associated with the entropy [Citation22–33]. Notably, the entropy can be calculated by either dividing the dissipated energy with temperature, or by integrating heat capacity with temperature. Sato et al. [Citation21] predicted the time-dependent fracture of thermoset CFRPs. This prediction was based on the entropy; however, no actual entropy measurements were involved. Several previous studies have proposed numerous entropy-based fracture models [Citation7,Citation12,Citation21,Citation33–39]. However, only a few actual entropy measurements have been performed [Citation40–42].
Herein, we aim to predict the remaining life and residual strength of CFRPs subjected to prolonged use and with unknown loading histories. This prediction would be revolutionary if it were made using entropy measurements, which is why we make this prediction using nondestructive measurements [Citation43]. Sakai et al. [Citation42] compared the entropy generation between experiments and molecular dynamics (MD) simulations for the tensile loading of PA6. However, the study had several limitations. Because differential scanning calorimetry (DSC) requires samples to be broken down for testing, the measurements render the samples unusable. When DSC tests destroy the specimens, the heat capacity increases. Entropy generation was quantified by a linear and quadratic extrapolation of the relationship between heat capacity and temperature. Monotonic tensile load tests were conducted; however, cyclic loading tests were not involved. Furthermore, a thermoplastic resin was used, but the thermosetting resin used was not mentioned. Indeed, for commercial use, a study on thermoset resins is required.
In this study, entropy generation is quantified by performing cyclic loading tests on epoxy resins and by measuring the dissipated energy. We determine the relationship between the specific heat capacity and temperature using an equation based on the Debye model. From this equation, we construct a relationship between entropy generation and specific heat capacity increase. Based on the results, an increase in the specific heat capacity of the epoxy specimen after cyclic loading tests is predicted.
We have developed a thermal diffusivity, thermal conductivity, and volumetric heat capacity measurement method based on a periodic laser heating method using lock-in thermography (LIT) [Citation42–45]. Using the LIT method, the fatigue damage evaluation through thermal diffusivity has been conducted for a CFRP laminate [Citation46,Citation47]. The LIT method has the advantage of obtaining a high accuracy 2-D image of thermophysical properties. It can provide the information about the location dependence of fatigue damage on composite material such as CFRP. The sensitivity of conventional pulse thermography [Citation48], which uses pulse excitation to heat a sample and can measure 2-D thermal diffusivity, is restricted by nominal sensitivity of the infrared camera. Typical nominal sensitivity of cooled quantum detector infrared camera is 20 mK [Citation49]. The LIT method can achieve a high signal-to-noise ratio and is suitable for very weak temperature signals due to its averaging nature of periodic signal [Citation49]. The nominal sensitivity of LIT can reach less than 1 mK [Citation49]. The LIT method is appropriate for thermal properties measurement, which needs high accurate measurement. In this study, we applied the LIT method to the fatigue sample to obtain volumetric heat capacity without cutting process compared to DSC analysis. We also conducted an Archimedes method to measure the density. Finally, we obtained the specific heat capacity to quantify the entropy generation due to fatigue damage.
2. Cyclic loading test
Fifty grams of bisphenol a diglycidyl ether (DGEBA) and 16.3 g of 4,4’-DDS were stirred at 100 ºC for 10 min and defoamed at 80 ºC. The mixture was both defoamed and stirred four times and to make the sample 3 mm thick, the mixture was poured between glass plates kept at 3 mm. It was baked at 180 °C for 2 h and cut with a diamond cutter to create four specimens with dimensions of 100 mm x 15 mm. A net was attached 30 mm from the top and bottom edges of each specimen, as shown in . The net is attached to prevent destruction in the pinched area. A universal testing machine (AG-X plus, Shimadzu Co., Ltd., Kyoto, Japan) was used for cyclic loading testing, as shown in . A strain gauge was mounted in the center of the specimen to measure strain. The specimen was maintained at 50 °C for 30 min in a thermostatic chamber. The stress – strain diagram corresponding to the cyclic loading tests is shown in . The maximum stress in the cyclic loading test was 60 MPa, and the minimum stress was 10 MPa. Two of the four specimens were subjected to repeated loading tests, whereas the other two were not loaded. These two no-loaded specimens were used as undamaged reference samples.
3. Estimation of the specific heat capacity based on mechanical and thermal entropies
Next, the specific heat capacity of the specimen after cyclic loading is evaluated by combining two types of entropies: mechanical entropy and thermal entropy. In the estimations of these entropies, energy dissipation due to mechanical loading is determined using the stress – strain diagram and specific heat capacity, respectively. Thus, the two entropies are distinguished according to the method of energy dissipation measurement, but they present identical values, as supported by previous studies [Citation42]. The specific heat capacity of the specimen after fatigue loading is estimated based on the entropies determined using these methods.
The mechanical entropy generation is expressed by following equation as [Citation33]
where t is the time, T is the temperature, and is the dissipated energy, which is the total work (
minus the internal energy (
) based on energy balance. These energies are obtained using the stress – strain diagram shown in . The total work is obtained by integrating the product of the strain increment and stress with time. The internal energy, that is, the elastic strain energy, can be estimated from the elastic modulus and stress after cyclic loading, where the elastic modulus is determined by the slope of the stress around 0.01%–0.2% strain in the first cycle.
As a result, the dissipated energy is calculated to be 1.81 × 104 J/m3K. Furthermore, given that the density of the epoxy resin is 1233 kg/m3, the entropy generated per unit mass is 1.468 × 10−2 J/gK.
Next, thermal entropy generation is represented by [Citation42]
where is the heat capacity of the epoxy resin. The temperature dependence of specific heat capacity over a wide temperature range is necessary to determine thermal entropy generation. It is well known that the Debye model can represent the temperature dependence of solid materials; that is, the specific heat capacity is proportional to the cube of the temperature in the low-temperature region and is constant in the high-temperature region [Citation50]. However, previous experiments have demonstrated that thermoplastic polymers, such as PA6, have a specific heat capacity that increases with temperature at approximately room temperature [Citation42]. One of the primary factors causing the difference in the temperature dependence of specific heat capacity is the arrangement of atoms constituting a molecule. The Debye model assumes that the atoms are arranged in a regular lattice. By contrast, the thermosetting polymer used in this study has an amorphous structure in which atoms are arranged randomly in a system similar to that of a thermoplastic polymer. To capture the temperature dependence resulting from the irregular arrangement of atoms, we propose the following equation:
where are fitting parameters.
is the reference temperature used to switch the magnitudes of the contributions of the first and second terms to the total specific heat capacity. This equation appropriately interpolates the behavior of the specific heat capacity between the low- and high-temperature regions. The validity of this equation is not discussed in the present study. For this study, we need an equation such as EquationEquation (4)
(4)
(4) to estimate the increase in specific heat capacity due to entropy increase. For this purpose, EquationEquation (4)
(4)
(4) is not strictly valid. The validity of this equation will be discussed in a subsequent study, but we will adopt it in the meantime.
shows the specific heat capacities obtained using EquationEquation (4)(4)
(4) and the DSC experiments using a small piece cut from the specimen after cyclic loading. EquationEquation (4)
(4)
(4) adequately expresses the experimentally obtained specific heat capacity: Although DSC measurements of the cut specimens are used to demonstrate the validity of this equation, the specific heat capacity generally increases before and after cutting. To avoid this artificial influence on the heat capacity, this study derives the heat capacity after fatigue loading without cutting, as described in the next section.
Figure 4. Specific heat capacity change of the specimen after cyclic loading obtained by the DSC measurement and relationship between temperature and specific heat capacity fitted with experimental values based on EquationEquation (4)(4)
(4) . Note that the DSC measurement is destructive; hence, the specific heat capacity is inherently greater than the actual. The results are only used to prove the temperature dependence of specific heat capacity.

As described above, the generated mechanical entropy is 1.468 × 10−2 J/gK, which is consistent with the thermal entropy obtained using EquationEquations (3)(3)
(3) and (Equation4
(4)
(4) ). Furthermore, as will be detailed in the next section, the experimentally measured heat capacity before fatigue loading is 1.06 J/gK. The measurement method is nondestructive and is an original contribution of the present study. These two conditions yield the fitting parameters in EquationEquation (4)
(4)
(4) , resulting in the temperature dependence of the specific heat capacity shown in . Consequently, the specific heat capacity after fatigue loading at 24 °C increases by 2.49% compared to that before the loading.
4. Measurement of the specific heat capacity using LIT-based laser periodic heating method
4.1 Measurement principles and procedures
The specific heat capacity can be calculated using the thermal conductivity, thermal diffusivity, and density as follows:
These three values were measured separately to determine the specific heat capacity. Alasli et. al [Citation45] have developed the mapping measurement method of the volumetric heat capacity using the LIT-based laser periodic heating method. First, a one-dimensional heat conduction model is introduced to obtain the thermal diffusivity in the out-of-plane direction. The rear surface of the sample is uniformly heated using a laser beam, which is modulated by a square-shaped signal. The other boundary conditions along the perimeter of the sample and camera-side surface are defined as adiabatic. By applying these boundary conditions, the quasi-steady-state temperature solution is expressed as follows [Citation45]:
where is the DC temperature and
is the periodic temperature at angular frequency
, which is expressed by complex function as follows:
where d(m) is the sample thickness, (W/m2) is the input heat flux,
(W/mK) is the thermal conductivity, and
(Hz) is the frequency of laser modulation. The complex number
is expressed as follows:
where (m2/s) is the thermal diffusivity. The amplitude of the temperature oscillation
and the phase delay
(rad) at
are as follows:
shows the analysis procedure based on the principle. At first, the infrared camera captured the periodic temperature response of the sample surface. At the same time, lock-in analysis was conducted to calculate the amplitude and phase delay. This process was applied to all pixels of the photodetector. Amplitude and phase were measured at multiple frequencies to obtain the frequency dependence. Experiment data was fitted to the theoretical curve of EquationEquations (9)(9)
(9) and (Equation10
(10)
(10) ) to calculate the thermal diffusivity,
. Thermal conductivity
can be calculated using the following equation by measuring the input heat flux dependence of the temperature amplitude
.
Figure 6. (a) Schematic diagram of lock-in analysis to obtain amplitude and phase delay. (b) Analysis procedure to measure thermal diffusivity, thermal conductivity, and volumetric heat capacity.

Because the input heat flux and temperature amplitude depend on the emissivity and absorptivity of the sample, the front and rear surfaces of the sample should be coated with a black-body spray. In the experiment, input heat flux dependence of amplitude was fitted to the theoretical solution to calculate the . Volumetric heat capacity
was calculated based on EquationEquation (5)
(5)
(5) on each pixel. Finally, the spatial distribution of
was obtained. The density
(g/cm3) of the sample was measured using the Archimedes method, which was then used to calculate the average specific heat capacity of the sample.
4.2 Measurement apparatus
The measurement set-up is illustrated in . The quasi-steady-state temperature response was recorded using a LIT system (ELITE System, Thermo Fisher Scientific). The detailed specification of the infrared camera is shown in . The acquired data were processed using digital lock-in processing with commercial software to extract the temperature amplitude and phase delay. Here, a square wave signal was required as the reference signal for the lock-in analysis. The diode laser beam intensity was directly modulated by the reference signal. The laser beam periodically heated the rear side of the sample through a square-core multimode fiber, a mode mixer, and an adjustable collimator. A square iris was used to shape the beam and match the sample geometry, thereby preventing laser incidence in the infrared camera. The intensity distribution of the laser beam output from this configuration was sufficiently uniform [Citation47]. The resin sample was placed in a sample holder, and its rear surface was uniformly heated. The sample density was determined using the Archimedes method with a semi-micro analytical balance (GH-200, A&D) and a density determination kit (AD1653, A&D).
Table 1. Specifications of the infrared camera.
4.3 Measurement sample
The specifications of each sample are listed in . The increase in specific heat capacity was evaluated for two sets of samples to verify the reproducibility: N01 and N02, N1001 and N1002. The center of each fatigue sample was cut to dimensions of 40 mm × 15 mm. This process is necessary for the density measurement. In principle, there is no limitation on the size in the in-plane direction. shows the surface preparation of the sample. To prevent laser penetration into the resin, platinum (Pt) thin films were deposited on the bare surfaces using the magnetron sputtering system (MSP-1S, Vacuum device). Additionally, a black-body paint (JSC 3, Japan Sensor Corp.) was applied on the Pt coating to enhance laser absorptivity and emissivity. If the black-body paint can effectively absorb the laser beam, the presence of Pt becomes unnecessary. Nevertheless, we observed laser transmission when Pt coating was absent.
Figure 8. Surface preparation of the sample for each step before the measurement. Pt layer was coated on the bare surface of the epoxy resin. Pt layer was applied only on the laser heating side to reduce the laser transmission. Black-body paint was applied on Pt layer to improve the absorptivity and emissivity. For camera-side sample surface, black-body paint directly on the bare surface.

Table 2. Specifications of the measurement samples.
4.4 Measurement conditions
The measurement conditions are presented in . The heating frequency for the thermal diffusivity measurements ranged from 0.02 Hz to 0.05 Hz, and four points were measured in 0.01 Hz increments. Once quasi-steady state temperature was achieved, the lock-in analysis was conducted for 30 periods. In the thermal conductivity measurement, the heating frequency was 0.02 Hz, and the laser intensity was measured every five points from 200 mW to 1000 mW. The density was measured after measuring these two properties. Because the sample position was fixed between both measurements, the volumetric heat capacity of each pixel was calculated from the thermal diffusivity and thermal conductivity distributions. Finally, the average specific heat capacity was calculated from the density using EquationEquation (5)(5)
(5) .
Table 3. Measurement conditions.
4.5 Results
shows the spatial distribution of the amplitude and phase delay of the N1001 sample. shows the frequency dependence of the amplitude and phase at the position indicated in . In addition, the laser power dependence of the amplitude can be seen in . The experimental plot was sufficiently fitted to the theoretical curve. shows the distribution of the thermophysical properties measured by the LIT method for the N1001 sample. The broken lines in the distribution indicate areas sufficiently far from the sample boundary. One-dimensional heat conduction in the out-of-plane direction was ensured in this area. In addition, the effect of the cutting process was also negligible. The average thermophysical values within this region and the densities measured using the Archimedes method are listed in . The change in density before and after fatigue loading was sufficiently small. The average specific heat capacity of the unloaded sample was compared with the literature value [Citation51] for DGEBA-4,4’-DDM was used to verify the validity of the measurement, which contains a different curing agent from that used in the experiment. was up to 19% lower than the literature value of 1.304
0.023 J/gK. Furthermore, the literature values of density and thermal diffusivity were 1.160
0.004 g/cm3 and 0.136
0.001 mm2/s, respectively, which agreed with the experimental results within 6%. By contrast, the thermal conductivity was 0.21 W/mK, which was approximately 20% lower than the results. Molecular dynamics simulation for DGEBA-4,4’-DDS revealed that the thermal conductivity varies from 0.14 to 0.22 W/mK [Citation52]. This difference was attributed to the crosslinking portion of the epoxy resin. Because the thermal conductivity obtained in this study was within this range, the specific heat capacity is also consistent because of the validity of the density and thermal diffusivity results. presents a histogram of the volumetric heat capacity. The peak of the histogram increased in both sets. As the density difference was less than 0.24%, this increase directly leads to an increase in the specific heat capacity. This also suggests that a cutting process for density measurements is not necessary for fatigue quantification. As listed in , the specific heat capacity increased by 4.9% on average. This value is comparable to an increase of 2.49% in the specific heat capacity predicted from the entropy-based
estimation, which was specified in Section 3. These results suggest the possibility of estimating fatigue damage based on specific heat capacity measurements. In addition, the LIT method is suitable for this measurement because it can measure the volumetric heat capacity without requiring the cutting of the sample into tiny pieces, which is a mandatory process for the DSC method.
Figure 9. (a) Spatial distribution of the amplitude and phase delay of N1001 sample at =0.02Hz. (b) the first two plot shows the frequency dependence of the amplitude and phase delay. The third plot shows the laser power dependence of the amplitude. Each plot was obtained at the position indicated by the plus sign in . The fitted curve and experimental result are shown in each plot.

Figure 10. Distribution of each thermophysical property of the N1001 sample. Each broken line specifies the area for calculating the average thermal diffusivity, thermal conductivity, and volumetric heat capacity.

Figure 11. Histogram of the volumetric heat capacity of the samples. Upper histogram compares the results of N01 and N1001. Lower histogram compares the results of N02 and N1002.

Table 4. Results of each thermophysical property, which denotes the average value for the samples with the same loading cycles.
5 Conclusion
Epoxy resins consisting of DGEBA and 4,4’-DDS were tested over 100 loading cycles. The specific heat capacity after the cyclic loading test was estimated using entropy generation. Based on previous studies, mechanical entropy generation was assumed to have the same value as thermal entropy generation. The mechanical entropy was calculated from the stress-strain diagram. To determine the temperature dependence of the specific heat capacity, the equation was devised with reference to the Debye model. The specific heat capacity after the cyclic loading test was estimated from the thermal entropy generation, that is, the mechanical entropy generation. The specific heat capacities of the specimens before and after the cyclic loading tests were measured nondestructively. The density was measured using the Archimedes method, and the thermal diffusivity, thermal conductivity, and volumetric heat capacity were measured via thermophysical property mapping using LIT. The values obtained from the thermophysical property measurements and those predicted from the entropy generation were comparable. The results suggest that sample fatigue can be estimated based on thermophysical property analysis, and the lock-in thermography method is a suitable method for this application.
Disclosure statement
No potential conflict of interest was reported by the authors.
Additional information
Funding
References
- Geier N, Davim JP, Szalay T. Advanced cutting tools and technologies for drilling carbon fibre reinforced polymer (CFRP) composites: a review. Compos Part A Appl Sci Manuf. 2019;125:105552. doi: 10.1016/j.compositesa.2019.105552
- Dransfield K, Baillie C, Mai Y-W. Improving the delamination resistance of CFRP by stitching—a review. Compos Sci Technol. 1994;50(3):305–317. doi: 10.1016/0266-3538(94)90019-1
- Koyanagi J, Kiyota G, Kamiya T, et al. Prediction of creep rupture in unidirectional composite: creep rupture model with interfacial debonding and its propagation. Adv Compos Mater: J Soc Compos Mater. 2004;13(3–4):199–213. doi: 10.1163/1568551042580190
- Koyanagi J, Hatta H, Ogawa F, et al. Time-dependent reduction of tensile strength caused by interfacial degradation under constant strain duration in UD-CFRP. J Compos Mater. 2007;41(25):3007–3026. doi: 10.1177/0021998307082175
- Koyanagi J, Nakada M, Miyano Y. Tensile strength at elevated temperature and its applicability as an accelerated testing methodology for unidirectional composites. Mech Time-Dependent Mater. 2012;16(1):19–30. doi: 10.1007/s11043-011-9160-y
- Guedes RM. Cumulative creep damage for unidirectional composites under step loading. Mech Time-Dependent Mater. 2012;16(4):381–396. doi: 10.1007/s11043-012-9168-y
- Deng H, Mochizuki A, Fikry M, et al. Numerical and experimental studies for fatigue damage accumulation of CFRP cross-ply laminates based on entropy failure criterion. Materials. 2023;16(1):388. doi: 10.3390/ma16010388
- Alam P, Mamalis D, Robert C, et al. The fatigue of carbon fibre reinforced plastics - a review. Com Part B Eng. 2019;166:555–579. doi: 10.1016/j.compositesb.2019.02.016
- Kotelnikova-Weiler N, Baverel O, Ducoulombier N, et al. Progressive damage of a unidirectional composite with a viscoelastic matrix, observations and modelling. Compos Struct. 2018;188:297–312. doi: 10.1016/j.compstruct.2017.12.067
- Sato M, Koyanagi J, Lu X, et al. Temperature dependence of interfacial strength of carbon-fiber-reinforced temperature-resistant polymer composites. Compos Struct. 2018;202:283–289. doi: 10.1016/j.compstruct.2018.01.079
- Koyanagi J, Yoneyama S, Nemoto A, et al. Time and temperature dependence of carbon/epoxy interface strength. Compos Sci Technol. 2010;70(9):1395–1400. doi: 10.1016/j.compscitech.2010.04.019
- Koyanagi J, Mochizuki A, Higuchi R, et al. Finite element model for simulating entropy-based strength-degradation of carbon-fiber-reinforced plastics subjected to cyclic loadings. Int J Fatigue. 2022;165:107204. doi: 10.1016/j.ijfatigue.2022.107204
- Qi W, Yao W, Shen H. A bi-directional damage model for matrix cracking evolution in composite laminates under fatigue loadings. Int J Fatigue. 2020;134:105417. doi: 10.1016/j.ijfatigue.2019.105417
- Koyanagi J, Ogihara S, Nakatani H, et al. Mechanical properties of fiber/matrix interface in polymer matrix composites. Adv Compos Mater. 2014;23(5–6):551–570. doi: 10.1080/09243046.2014.915125
- Ogihara S, Takeda N, Kobayashi S, et al. Effects of stacking sequence on microscopic fatigue damage development in quasi-isotropic CFRP laminates with interlaminar-toughened layers. Compos Sci Technol. 1999;59(9):1387–1398. doi: 10.1016/S0266-3538(98)00180-8
- Kitagawa Y, Arai M, Yoshimura A, et al. Prediction of transverse crack multiplication of CFRP cross-ply laminates under tension-tension fatigue load. Adv Compos Mater. 2022;32(3):419–436. doi: 10.1080/09243046.2022.2113700
- Yokozeki T, Aoki T, Ishikawa T. Fatigue growth of matrix cracks in the transverse direction of CFRP laminates. Compos Sci Technol. 2002;62(9):1223–1229. doi: 10.1016/S0266-3538(02)00068-4
- Hosoi A, Arao Y, Kawada H. Transverse crack growth behavior considering free-edge effect in quasi-isotropic CFRP laminates under high-cycle fatigue loading. Compos Sci Technol. 2009;69(9):1388–1393. doi: 10.1016/j.compscitech.2008.09.003
- Koyanagi J, Sato Y, Sasayama T, et al. Numerical simulation of strain-rate dependent transition of transverse tensile failure mode in fiber-reinforced composites. Com[pos Part A Appl Sci Manuf. 2014;56:136–142. doi: 10.1016/j.compositesa.2013.10.002
- Sato M, Shirai S, Koyanagi J, et al. Numerical simulation for strain rate and temperature dependence of transverse tensile failure of unidirectional carbon fiber-reinforced plastics. J Compos Mater. 2019;53(28–30):4305–4312. doi: 10.1177/0021998319857111
- Sato M, Hasegawa K, Koyanagi J, et al. Residual strength prediction for unidirectional CFRP using a nonlinear viscoelastic constitutive equation considering entropy damage. Compos Part A Appl Sci Manuf. 2021;141:106178. doi: 10.1016/j.compositesa.2020.106178
- Iwamoto S, Oya Y, Koyanagi J. Evaluation of microscopic damage of PEEK polymers under cyclic loadings using molecular dynamics simulations. Polymers. 2022;14(22):4955. doi: 10.3390/polym14224955
- Mahmoudi A, Mohammadi B. On the evaluation of damage-entropy model in cross-ply laminated composites. Eng Fract Mech. 2019;219:106626. doi: 10.1016/j.engfracmech.2019.106626
- Basaran C, Nie S. An irreversible thermodynamics theory for damage mechanics of solids. Int J Damage Mech. 2004;13(3):205–223. doi: 10.1177/1056789504041058
- Kecik K, Ciecielag K, Zaleski K. Damage detection by recurrence and entropy methods on the basis of time series measured during composite milling. Int J Adv Manuf Technol. 2020;111(1–2):549–563. doi: 10.1007/s00170-020-06036-9
- Naderi M, Khonsari MM. Thermodynamic analysis of fatigue failure in a composite laminate. Mech Mater. 2012;46:113–122. doi: 10.1016/j.mechmat.2011.12.003
- Gunel EM, Basaran C. Damage characterization in non-isothermal stretching of acrylics. Part I: theory. Mech Mater. 2011;43(12):979–991. doi: 10.1016/j.mechmat.2011.09.002
- Mahmoudi A, Khonsari MM. Entropic characterization of fatigue in composite materials. In: Hashmi MSJ, editor Encyclopedia of Materials: plastics and polymers. Oxford: Elsevier; 2022. pp. 147–162.
- Naderi M, Khonsari MM. On the role of damage energy in the fatigue degradation characterization of a composite laminate, Composites Part B. Eng. 2013;45(1):528–537. doi: 10.1016/j.compositesb.2012.07.028
- Takase N, Koyanagi J, Mori K, et al. Molecular dynamics simulation for evaluating fracture entropy of a polymer material under various combined stress states. Materials. 2021;14(8):1884. doi: 10.3390/ma14081884
- Brinson HF. Matrix dominated time dependent failure predictions in polymer matrix composites. Compos Struct. 1999;47(1):445–456. doi: 10.1016/S0263-8223(00)00075-1
- Huang J, Yang H, Liu W, et al. Confidence level and reliability analysis of the fatigue life of CFRP laminates predicted based on fracture fatigue entropy. Int J Fatigue. 2022;156:106659. doi: 10.1016/j.ijfatigue.2021.106659
- Naderi M, Amiri M, Khonsari MM. On the thermodynamic entropy of fatigue fracture. Proc R Soc A: Math Phys Eng Sci. 2010;466(2114):423–438. doi: 10.1098/rspa.2009.0348
- Kagawa H, Umezu Y, Sakaue K, et al. Numerical simulation for the tensile failure of randomly oriented short fiber reinforced plastics based on a viscoelastic entropy damage criterion. Compos Part C Open Access. 2023;10:100342. doi: 10.1016/j.jcomc.2022.100342
- Meneghetti G. Analysis of the fatigue strength of a stainless steel based on the energy dissipation. Int J Fatigue. 2007;29(1):81–94. doi: 10.1016/j.ijfatigue.2006.02.043
- Mahmoudi A, Khonsari MM. Investigation of metal fatigue using a coupled entropy-kinetic model. Int J Fatigue. 2022;161:106907. doi: 10.1016/j.ijfatigue.2022.106907
- Mohammadi B, Shokrieh MM, Jamali M, et al. Damage-entropy model for fatigue life evaluation of off-axis unidirectional composites. Compos Struct. 2021;270:114100. doi: 10.1016/j.compstruct.2021.114100
- Mohammadi B, Mahmoudi A. Developing a new model to predict the fatigue life of cross-ply laminates using coupled CDM-entropy generation approach. Theor Appl Fract Mech. 2018;95:18–27. doi: 10.1016/j.tafmec.2018.02.012
- Movahedi-Rad AV, Eslami G, Keller T. A novel fatigue life prediction methodology based on energy dissipation in viscoelastic materials. Int J Fatigue. 2021;152:106457. doi: 10.1016/j.ijfatigue.2021.106457
- Huang J, Li C, Liu W. Investigation of internal friction and fracture fatigue entropy of CFRP laminates with various stacking sequences subjected to fatigue loading. Thin Walled Struct. 2020;155:106978. doi: 10.1016/j.tws.2020.106978
- Mahmoudi A, Mohammadi B. Theoretical-experimental investigation of temperature evolution in laminated composites due to fatigue loading. Compos Struct. 2019;225:110972. doi: 10.1016/j.compstruct.2019.110972
- Sakai T, Takase N, Oya Y, et al. A possibility for quantitative detection of mechanically-induced invisible damage by thermal property measurement via entropy generation for a polymer material. Materials. 2022;15(3):737. doi: 10.3390/ma15030737
- Ishizaki T, Nagano H. Measurement of three-dimensional anisotropic thermal diffusivities for carbon fiber-reinforced plastics using lock-in thermography. Int J Thermophys. 2015;36(10–11):2577–2589. doi: 10.1007/s10765-014-1755-5
- Ishizaki T, Nagano H. Measurement of 3D thermal diffusivity distribution with lock-in thermography and application for high thermal conductivity CFRPs. Infrared Phys Technol. 2019;99:248–256. doi: 10.1016/j.infrared.2019.04.023
- Alasli A, Fujita R, Nagano H. Thermophysical properties mapping of composites by lock-in thermography: applications on carbon fiber reinforced plastics. Int J Thermophys. 2022;43(12). doi: 10.1007/s10765-022-03109-7
- Fujita R, Katsukura K, Nagano H. Early-stage fatigue evaluation of CFRP laminates using microscale lock-in thermography based on laser-spot-periodic-heating method. Infrared Phys Technol. 2022;126:104323. doi: 10.1016/j.infrared.2022.104323
- Fujita R, Alasli A, Yokozeki T, et al. Quantification of early-stage fatigue damage on cross-ply CFRP laminates by lock-in thermographic thermal diffusivity measurement, Proceedings of SPIE - The International Society for Optical Engineering, Orlando, Florida, 2022.
- Manta A, Gresil M, Soutis C. Infrared thermography for void mapping of a graphene/epoxy composite and its full‐field thermal simulation. Fatigue Fract Eng Mater Struct. 2019;42(7):1441–1453. doi: 10.1111/ffe.12980
- Breitenstein O, Warta W, Langenkamp M. Lock-in thermography: basics and use for evaluating electronic devices and materials. Springer Berlin Heidelberg; 2010.
- Landau LD, Lifshit︠s︡ EM, Sykes JB, et al. Statistical physics. 3rd ed. E.M. Lifshitz and L.P. Pitaevskii, editors. Oxford, United Kingdom: Butterworth-Heinemann; 1980.
- Harada M, Morioka D, Ochi M. Thermal and mechanical properties of tetra-functional mesogenic type epoxy resin cured with aromatic amine. J Appl Polym Sci. 2018;135(16):46181. doi: 10.1002/app.46181
- Zhao Y, Kikugawa G, Kawagoe Y, et al. Molecular-scale investigation on relationship between thermal conductivity and the structure of crosslinked epoxy resin. Int J Heat Mass Trans. 2022;198:123429. doi: 10.1016/j.ijheatmasstransfer.2022.123429