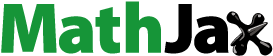
ABSTRACT
This study focuses on evaluating the response of concrete block pavement (CBP) reinforced with rubberised oil palm shell (ROPS) layers when subjected to vehicular loads using laboratory experiments and finite element (FE) simulations. The key parameters considered in this study are the sand bed thickness, oil palm content in ROPS layers, embedment depth of ROPS layers, and vehicle velocity. The dynamic loads due to the vehicular movement were generated using a real-time road unevenness signal. Outcomes from the lab-scale 1g experiments and FE simulations were expressed as displacement and acceleration responses in the frequency domain. CBP sections with sand bed thicknesses of 10mm and 70mm were found to yield high surface deflection and acceleration values, both with and without ROPS reinforcements. CBPs reinforced with the ROPS layer having 20% OPS content demonstrate the best performance compared to ROPS layers made with 5% and 10% OPS contents. Further simulations show that the ROPS layers at an optimum embedment depth of 180mm from the surface in the CBP profile can significantly reduce the unacceptable levels of vibration. To this end, this preliminary research attempts the possible reengineering of oil palm shells and ascertains the suitability of ROPS reinforcements in stabilising CBP−soil systems.
1. Introduction and research background
Countries across the globe have experienced accelerated urbanisation over the past 50 years, typically leading to big cities and metropolitan areas. An estimate from the United Nations Population Division shows that more than half of the world’s population currently lives in urban areas – 53% as of 2015, while projections show the estimate to reach a staggering 60% of the world’s population to live in urban areas by 2030 (Population Reference Bureau Citation2007). Increasing urbanisation is associated with growing demand for basic facilities and infrastructure, including the transportation sector. For example, from a local perspective, more than half of Malaysia’s population live in urban areas, and increasing usage causes severe demand on the transportation sector, the road networks in particular (Hasan and Nair Citation2014). The road pavements are increasingly overloaded with heavy vehicles alongside a surge in privately owned vehicles, resulting in increased load and traffic (repetition in load application). Both the load and traffic can induce vibrations to the road surface, which eventually travels to the sub-surface. Such vibrations are well known to cause discomfort to the vehicle users and vibrations propagating to the sub-surface impact the integrity of pavement structure, which are both serious concerns dictating the serviceability of roads. Ideally, the vibration induced by vehicles can be either airborne vibration caused by engines and exhaust or ground-borne vibrations caused by road surface irregularities and cracks (Sacramento Citation2002). The airborne vibrations generally lie in the low-frequency range and are less felt, while the ground-borne ones can cause stress waves that travel to the nearby buildings. With the urbanisation and rapid growth of cities, an increasing spike in building’s density across the roads is typical (Selcuk and Cubukcu Citation2015), thereby making traffic-induced ground-borne vibrations a major issue. Literature highlights the fact that the amplitude levels of such vibrations exceed the desirable levels, which can be further amplified influenced by the uneven road surfaces (Lombaert et al. Citation2000, Jakubczyk-Galczynskaa and Jankowskib Citation2014). Unevenness in the road surface can be the characteristic of a few newly constructed pavements as well, such as the ones paved using pavement blocks, of which concrete block pavers are the most common in urban areas.
Concrete block pavement (CBP) is well regarded for its various advantages, including ease in installation/maintenance and aesthetic values. Nonetheless, the riding comfort is not equivalent to that of the conventional pavements. Unlike traditional asphalt pavement, CBPs comprise multiple paving units – typically known as pavers, interconnected by sand joints leading to recurring surface discontinuities at very short spans. This marks higher values of unevenness index for CBPs in comparison to asphalt and rigid concrete pavements (Lak et al. Citation2011). These uneven finishes in CBP’s surface can lead to load amplification under moving vehicles resulting in dynamic excitation. So caused excitation or vibrations are borne by the vehicle’s suspension system, while the majority are transmitted onto the CBPs surface and the underlying soil layers eventually (Di Mascio et al. Citation2019). Such repeated application of loads due to vehicular movement leads to increasing strains at the CBPs surface and imparts strength degradation in the supporting soil layers. Improvements attempted until date ideally refer to the physical modification of the blocks. For example, rubberised concrete paving blocks with tire waste are used to increase the flexural hardening and reduce stress at the joints of the paving layer (Ling et al. Citation2010, Murugan et al. Citation2016). Nevertheless, the compressive strength of such rubberised blocks was less than that of conventional ones. Apart from the physical modification of blocks, other improvement methods include altering the pattern of laying the concrete blocks (Panda and Ghosh Citation2002b, Lin et al. Citation2016); changing the size and shape of the blocks (Lin et al. Citation2016, Gunatilake and Mampearachchi Citation2019); varying the interlocking mechanism (Soutsos et al. Citation2011, Füssl et al. Citation2016); adopting joint-sand width with increased frictional resistance (Panda and Ghosh Citation2002a, Ah et al. Citation2014); and modifying the edge restraint properties of the paving layer (Mampearachchi and Gunarathna Citation2010, Füssl et al. Citation2018). While these studies proved helpful, literature from as early as the 1980s to date highlights that the strength of the base and subgrade layers play a crucial role in dictating the stability and performance of CBPs, irrespective of the properties of the surface paving layer (Shackel Citation1988, Shackel Citation1991, Rada et al. Citation1992; Huurman Citation1994; Huurman Citation1996, Panda and Ghosh Citation2002a, Huurman et al. Citation2003, Hassani and Jamshidi Citation2006, Füssl et al. Citation2018). This is because the failure mechanism of CBP mainly depends on the strength and stiffness of the sand bed and subgrade. Deterioration in the sand bed and subgrade strength criteria can lead to the separation and sinking of blocks, respectively (Lilley and Dowson Citation1988, Rada et al. Citation1992, Hassani and Jamshidi Citation2006).
Literature also presents research attempts in support of introducing elastic material/layers into the soil mass to improve the vibration attenuation properties while the stiffness is maintained. Some examples include tire crumbles, rubber waste, and geo-cell as soil reinforcement, which likely improve the elastic response and the natural frequency of stabilised soil substructure (Yadav and Tiwari Citation2017, Priyadarshee et al. Citation2018, Hegde and Venkateswarlu Citation2019). Using rubber sheets in several soil-based applications and machine foundations for a similar purpose is also documented (Kelly and Konstantinidis Citation2011, Zakeri et al. Citation2021). The introduction of rubber may be used in constructing pavements to avoid resonance, but rubber is relatively compressible and can bulge laterally, leading to large surface settlements. The provision of steel reinforcements can increase the stiffness and reduce displacement but make the method more expensive and resource intense, making the approach less environmental and sustainable.
Using sustainable and low-cost materials can promote vast applications without concern about high expenses and environmental impacts. Though natural fibres have proved to improve the strength of the soil layer in geotechnical applications (Sivakumar Babu and Vasudevan Citation2008, Al-Oqla and Sapuan Citation2014), usage of natural shells that can improve both the strength and damping properties of the soil layer can be an ideal substitute. Oil palm shell (OPS) is one such natural shell – a biomass byproduct from the oil palm production process (Alengaram et al. Citation2013, Hanipah et al. Citation2016). Studies focusing on OPS to date hint that the dome-shaped structure and the associated strength-flexibility ratio of OPS can result in higher load carrying and shock absorption capacities (Basri et al. Citation1999, Teo et al. Citation2006). Hypothetically, incorporating OPS as reinforcement is likely to improve the damping behaviour of soil layers without significantly compromising their load-carrying capacity. Recent literature shows such utilisation of OPS for various applications, such as reinforcing kaolin soil samples (Loi et al. Citation2020), preparing rubberised oil palm shell composites (Anandan et al. Citation2020), and improving the tensile strength of the polyester matrix (Sahari and Maleque Citation2016). The outcome from these literatures commends the potential of OPS for soil applications, which mostly show good results and encourage sustainable development. Though using OPS likely improves the damping response without reducing the load-carrying capacity, agro-based biomass such as OPS readily undergoes degradation when exposed to atmospheric moisture. Coating rubber on the surface of OPS or embedding OPS in rubber will undoubtedly improve the performance of OPS (Loi et al. Citation2020). Since rubber is a well-known damping material (Kelly and Konstantinidis Citation2011) as well, using rubber-OPS layers is hypothetically a more feasible solution towards reducing, controlling, or isolating vibrations in CBP systems subjected to vehicular movement. However, no literature addressing this possibility was encountered during the literature review of this study, which is the fundamental motivation.
2. Research objective and approach
The main objective of this paper is to ascertain the response of CBP systems reinforced with the rubber-oil palm shell (ROPS) layers subjected to dynamic loads (to simulate vehicular movement) using laboratory experimentation and finite element (FE) simulations. This objective is systematically approached in this paper under the following two phases.
Phase 1 focuses mainly on understanding the mechanism associated with settlement in an ideal CBP system under moving vehicles. It should be noted that the ROPS layers are not adopted in this phase yet. Surface deflections in CBPs are predominantly linked with the thickness of the sand bed (Lilley and Dowson Citation1988, Panda and Ghosh Citation2002a, Citation2002b, Soutsos et al. Citation2011). Therefore, the sand bed layer is one of the critical components in the CBP system – owing to its ability to improve the interlocking efficiency and load dispersing potential of the concrete block surface layer (Hassani and Jamshidi Citation2006). Standards followed for the design of sand bed thickness typically use only static loading without considering the dynamic response of CBPs (Rada et al. Citation1992, Panda and Ghosh Citation2002a, Citation2002b). This phase, therefore, studies the influence of sand bed thickness under the varying velocity of the vehicle considering the non-linearity associated with the supporting soil layers. The objectives in this phase are addressed using a combination of 1g laboratory scaled experimental model studies and FE simulations. The experimental findings are used to validate the FE model first. The thus validated model with modification as required (scaling and soil profiles) was used to study the effect of varying sand bed thickness and vehicle velocity on the response of the CBP system.
Phase 2 focuses on evaluating the dynamic response of the CBP-soil system reinforced with ROPS layer under varying sand bed thickness and vehicular velocities. The ROPS samples fabricated in the laboratory were subjected to a cyclic compression test to determine their behaviour and were simulated using the Hyperelastic material model in FE simulations. These results, including the suitability of the Hyperelastic modelling technique for ROPS, are discussed in Anandan et al. (Citation2020). The physical and dynamic properties of ROPS samples are comparable to that of complex synthesised rubber components in the laboratory, while the percentage of OPS content predominantly governs the strength of ROPS layers (Anandan et al. Citation2020). Therefore, in the current work, the effect of OPS content on the frequency response of the whole CBP system is also investigated. Further, the depth of embedment of the ROPS layer is another factor considered while executing the parametric investigations. This optimised embedment depth was then used in the FE simulations. The dynamic behaviour of the CBP system is determined in terms of the acceleration and displacement responses of CBP systems with and without ROPS reinforcement in the frequency domain. Parametric variations in this phase focused on the effect of varying sand bed thickness, vehicular velocity, and OPS content in ROPS layers.
3. Experimental validation
An experimental model of an idealised CBP system was constructed in the laboratory. The focus of the experiments was to measure the response of concrete blocks and the underlying soil layers when subjected to dynamic loading. The acceleration, vertical stresses, and displacements were the key responses measured in the experiments at varying depths and loading. shows images explaining the key construction features and the experimental setup used in this study. The test tank was fabricated using 5mm thick mild-steel walls with an internal cubical volume of 1500mm x 1500mm x 1000mm (see a and f). The test CBP section was prepared in the tank to a plan area of 1500mm x 1500mm and 730mm deep. The CBP test section was prepared to resemble an ideal CBP section in the field – with an 80mm thick paving block layer, followed by a 50mm thick sand bed layer, 350mm thick subgrade layer, and 250mm thick base sand layer. The locally sampled sandy silt soil was compacted to prepare the subgrade layer. The sand and subgrade layers were compacted to dry unit weights of 16.1 and 15.6kN/m3, respectively. The samples were compacted using a handheld rotary compactor (see b) in layers, with soil lifts of 50mm. Utmost care was exercised in preparing the soil bed to ensure minimum moisture loss – the variation in the measured moisture content was within 2%. Thus, ensuring the homogeneity of the test section. The paving block layer was prepared using square pavers arranged with 5mm wide sand joints between adjacent pavers. The paving blocks were laid as per the standard procedure specified in IRC: SP:63 (Citation2004) (see d).
Figure 1. Experimental setup used in this study; (a) steel tank with compacted and finished sand layer; (b) handheld compactor used for uniform compaction; (c) load cell embedded within the soil; (d) Finished paving block layer showing the joint sand; (e) loading assembly including motovibrator; (f) overview of the complete experimental setup, highlighting logger, hydraulic actuator and test tank.

The acceleration, vertical stress, and displacement in this study were measured using one-dimension accelerometers, load cells (see c), and displacement transducers (see d and e), respectively. Instrumentation and their positioning were carefully planned to capture the response of the model to the best possible accuracy and extent. shows the schematics demonstrating a cut-section made along the central cross-section of the test tank, including the locations of all the sensors. The sensors were calibrated and carefully checked before installing them in the test section. Due care was exercised to ensure the soil layers were levelled before and after placing the sensors (see a and c). An MVE-type electric motovibrator was used in this study to apply the dynamic loads. The motovibrator was placed at the centre of the test section on the surface (see e), which was in line with the hydraulic actuator (see f) used to apply the surcharge loads. (a) shows the acceleration-time response data obtained at the surface of loading area during 5s of vibration. The dynamic loads using the motovibrator was applied by maintaining the rotation frequency of the oscillator at 10Hz – which is in close comparison with the typical operating frequency observed during the car, bus, and truck movements (Lombaert et al. Citation2000, Lak et al. Citation2011, Hegde and Venkateswarlu Citation2019). This motovibrator was fixed inside an I- beam setup fabricated with a loading area of 500 × 500mm so as to create a pressure equivalent to tyre pressure which was 1.06 MPa. In the current study, the actuator was operated under a load-controlled scenario, and the surcharge load applied was maintained constant – as ensured by the device’s software. However, the vibration was applied using a motor vibrator. During each trial, the load applied was considered to remain constant which was not varied by the user during vibrations. While it is true that the dynamic stress is being divided, the actuator was also observed to move in order to maintain a constant load. Based on these observations, it is assumed that the variation in dynamic stress is minimal. The surcharge loads were applied in increments of 10kN, starting from 10kN up to 30kN – each load increment counted as one trial. The loading sequence included seating loads that were applied in increments of 2.5kN until a load of 10kN was reached. The seating load was crucial to ensure proper interlock in the CBP layer and prevent excess surface deflections in the first few cycles of dynamic load application. IMC data loggers were used to record the acceleration and load measurements simultaneously at 1/100th of a second for every loading and unloading operation. It is expected to have minimal effect on the reflection and refraction of waves from the test tank side walls, since the plan dimensions of the tank were 3 times the width of the loaded area. Literature on full-scale dynamic studies on vibrating machine foundation systems warrants choosing the plan dimensions of the test tank at least 3–4 times that of the loaded area width, helps in reducing any boundary effects and ensures proper dissipation of wave energy (Baidya and Krishna Citation2001, Baidya and Mandal Citation2006). Nonetheless, to check for any possible reflection and refraction of waves from the test tank boundaries, in this study, vertical acceleration responses near the side walls and bottom were measured and analysed. (b), shows a typical model response measured near the bottom wall of the test tank from a test with 10Hz frequency. The values of acceleration recorded were as low as 0.02, signifying minimal disturbance in soil, thus confirming the reduced effects of reflection and refraction. Also, owing to the smaller thickness of the test tank side wall, its stiffness is unlikely to induce a compelling amount of reflection or refraction. The primary purpose of the experimental findings was to validate the finite element (FE) model. A 3-dimensional FE model with similar dimensions and material used in the test tank was considered for this purpose. For validation purposes, the dynamic response of the numerical CBP model was obtained under loading cases similar to that adopted in the experiments. The elastic modulus assigned to the sand and subgrade in the model were 350MPa and 306MPa, respectively. These values were obtained based on laboratory experiments conducted on representative samples. The Poisson’s ratio values used were 0.3 and 0.4. The detailed procedure for modelling the interactions in pavement systems is discussed next. The nominal mesh sizes chosen were 160mm, 120mm, 75mm, and 40mm. For every case, the aspect ratio equal to one was maintained as far as possible. Mesh convergence is obtained when an increase in mesh density has negligible effects on the results produced. As can be observed from a, the convergence study implies that the discretisation with a mesh size of 40mm in the loaded area and 75mm in the rest of the areas produced results that are in close agreement with the experimental results. Further, the 75mm-40mm mesh converges to an overall mesh size of 40mm, thus indicating the attainment of convergence. Mesh size of 120 and 160mm appears to have unstable behaviour and doesn’t correlate well with the experimental results. Therefore, the combination of 75mm and 40mm mesh size were used for the rest of the analysis. b and c show the comparison of findings from the experimental and FE simulations. As observed, the experimental and FE simulation are in good comparison. The results, therefore, validate the FE simulations, which will be further used for the parametric study to address the objectives of this paper.
Figure 2. Schematic diagram of experimental set-up along the central cross-section of the test tank.

4. FE models of CBP systems
Three-dimensional FE modelling is used in this study, considering its accuracy and computational efficiencies in simulating the CBP models. Models were prepared to work around composite dynamic material properties with multiple variables and realistic boundary conditions instead of employing vast repeating experimental studies. To acquire the dynamic response of the CBP system under vehicular movement, separate models are used: (a) vehicle model using quarter car including mass, spring and damper system, (b) CBP-soil substructure, and (c) ROPS layers.
4.1. Modelling of dynamic loads
The dynamic response of the vehicle model primarily depends on the road unevenness; in the case of CBPs, it is due to the short distant irregularities (Lak et al. Citation2011). Typically, the power spectral density (PSD) function is used in most studies to calculate road roughness. However, usage of the PSD function will not be suitable for road conditions when the irregularities are periodic (La Agostinacchio et al., Citation2008). Hence, the real-time road unevenness signal of CBP obtained by Lak et al. (Citation2011) is used to simulate the dynamic load from the vehicle model. A typical road surface signal of CBP consists of a substantial number of periodic bumps with different amplitudes (Huurman, Citation1994). Since trucks with overweight goods and buses can produce discernible vibrations, a class six medium-duty truck (Yang et al. Citation2016) is considered in this study. The vehicle parameters used in the model are referred from Park et al. (Citation2020). The dynamic load signal obtained from the quarter car model in MATLAB Simulink comprises the static vehicular load and dynamic loads – induced by oscillations of the vehicle’s interaction with CBP’s surface joints. Next to road unevenness, the moving velocity of vehicles affects the frequency levels of vibration considerably. Therefore, the load signals are acquired for three different commonly observed velocity values of vehicles, which are 40, 50, and 70km/h. shows the variation of loads with time at these three vehicular velocities. The loads typically vary between 20 and 70kN, fluctuating around 41kN with a minor increase observed at higher speeds.
4.2. Finite element modelling of CBP
(a) shows a section view of the 3D FE model of the CBP-soil system used in this study. Components of the model include the concrete paving block surface, sand bed, base course, and subgrade layers. ROPS layer of thickness 10mm was included in the later stages of the analysis. Practical evaluation of the soil strata is essential to account for effectively predicting the dynamic response of the CBP system under vehicular loading. The amount of shear strain transferred into the soil layers under repeated vehicular load warrants the consideration of non-linear material behaviours. For example, results presented by Ye et al. (Citation2018) on asphalt type pavement show the typical shear strain values reaching 0.15% for the vehicular loads. This strain value perhaps falls in a range requiring non-linear modelling – soil mass typically shows non-linear behaviour at shear strains >0.08% (Asheghabadi and Cheng Citation2020). A simple case considering a linear model will likely underestimate the permanent deformations in the soil system. More advanced non-linear models like the kinematic hardening and cap plasticity models and simple models like Mohr-Coulomb (MC) model are increasingly used for various geotechnical applications. Though the MC model requires only a few basic parameters – cohesion (c) and friction angle (ϕ), they are used under monotonic loading conditions. Still, the hardening or softening behaviour identified is not sufficiently accurate. Hence, a modified Drucker-Prager or cap plasticity model is used for the current scenario of dynamic vehicular load. In this constitutive model, Hooke’s law is used to simulate the elastic material behaviour, and a combination of cap yield surface and Drucker Prager failure surface defines the plastic zone. The equation of the yield surface (Robert et al. Citation2015) is as shown in EquationEquation (1)(1)
(1) .
(1)
(1) Where, d and
are the values of cohesion and angle of friction,
is the evolution parameter accounting for hardening/softening depending on the volumetric plastic strains, R is the value of cap eccentricity signifying the cap shape, and
is the transition surface radius that promotes a smooth transition between the Drucker Prager failure and cap yield surfaces. The yield surface of the cap plasticity function is a cylindrical cone and hence can overcome the sharp corner problems arising in the MC model. shows the material parameters of the cap plasticity model used in this paper. Experimental data presented by Chiroux et al. (Citation2005) is used to calculate the parameters for the cap plasticity model in this study.
Figure 6. (a). Section of FE model of CBP-soil system showing soil layers along with ROPS layer (b). Schematic showing the location of measuring points through the depth of CBP- soil model

Table 1. Material Properties used in the FE modeling of this study.
Having described the material model, the boundary conditions were then assigned to the CBP model. The bottom boundary of the subgrade layer was assigned as rigid with a fixed boundary condition to prevent any movement. Interaction between soil layers was modelled using tie constraints to reduce the number of elements and subsequently the computation time. The loading area was determined based on the tire’s contact area for the vehicle class used – as per the AASHTO HL-93 specifications for the design truck with two rear axles and one front axle. The contact area for a single tire was approximated as a single rectangle of size 510mm x 250mm (HL-Citation2014 AASHTO Citation2014). The depth and width of the model were chosen to be three to four times larger than the loading area so as to reduce boundary reflections. This is based on dynamic full-scale experimental studies which reported negligible values of displacement and acceleration near the boundaries. (Baidya and Krishna Citation2001, Baidya and Mandal Citation2006). Moreover, variation in mass and inertia of the foundation soil system can significantly influence the resonance frequency of the whole system (Gazetas Citation1981), thus justifying the use of a full-scale model similar to field scenarios to improve the accuracy of results. Therefore, the modelled CBP section had dimensions of 3.0m x 3.0m x 2.5m. This dimension was also found sufficient to achieve convergence for the dynamic loads considered in this study. As the oscillatory vibrations from vehicles are analysed, care was exercised in choosing proper time discretisation to obtain stable solutions. During mesh discretisation, element size was reduced in the loaded area, and coarse elements were used for the remaining sections and base course layers. The C3D8R elements of reduced integration type were chosen for the soil model in the ABAQUS package. During the analysis, the model didn’t face severe hourglass issues. But hourglass control was enabled since coarse elements of reduced integration type may have a chance to face reduced stiffness issues (refer to ABAQUS User Manual). Near model boundaries, infinite elements of type CIN3D8 were used to prevent the reflection of waves back into the model. Since these elements are linear, they are placed at a sufficient distance from the nonlinear loading region. This was to ensure proper prediction of the results by improving the calculation efficiency. Mesh sensitivity analysis was carried out before analysing the model.
4.3. Modelling of ROPS layer
ROPS layers in this study were modelled to a thickness of 10mm, while the depth of embedment was one of the parameters investigated. A complex hyperelastic model, aided by Yeoh’s function, is used to simulate the material behaviour of ROPS layers instead of a simple elastic model. shows a flow chart highlighting key steps followed to confirm the usage of the hyperelastic model and Yeoh’s function to model ROPS layers in this study. More details can be found in Anandan et al. (Citation2020). tabulates the material coefficients and properties for the ROPS layer used in the hyperelastic modelling of this study.
Figure 7. Flow chart demonstrating the methodology used to simulate the Hyperelastic model of ROPS. Note: Refer to Anandan et al. (Citation2020) for a detailed procedure.

Table 2. Material Coefficients of ROPS Layer used by the Yeoh Function.
4.4. Summary of the FE modelling in this study
Four different sand bed thicknesses – 10mm, 20mm, 40mm, and 70mm, are adopted in modelling the CBP system for the parametric study. The effect of ROPS embedment and its position within the soil profile, OPS content of ROPS, and vehicular velocity are among other parameters considered. Twelve scenarios are simulated in total for every CBP profile with and without the ROPS layer. Another 84 models are generated to optimise the embedment depth of the ROPS layer at a critical velocity equivalent to 70km/h (the highest velocity considered in this study). The effect of OPS content in the ROPS layer on the dynamic response of the CBP-soil system was then studied. tabulated all relevant details and parameters varied for this purpose, which account for 112 models. Changes in the resonant frequency of the system, along with the peak surface deflection and acceleration values, were studied in the frequency domain with sufficient detail. Variation of acceleration amplitudes as they propagate through the CBP-soil system was also studied under the scenarios (see for more information) with and without the ROPS layers.
Table 3. Details of the numerical simulations and model schedule.
5. Results and discussion
(b) shows the points within the FE model at which the acceleration and displacement amplitudes were recorded. The dynamic response of the CBP systems with and without the ROPS layer is studied in terms of their acceleration–frequency and displacement–frequency response at the loading surface – point #1. While points #2 till #7 were used to monitor changes in acceleration values across the depth of the CBP-soil model. Variation in the damping behaviour of the whole system was also monitored simultaneously.
5.1. Influence of sand bed thickness
Series 1 simulations, as described in , were carried out on the validated CBP-soil models to ascertain the response of the CBP system with varying sand bed thickness under different vehicular velocities. shows the variation of the deflection amplitude at the loading surface in the frequency domain at various vehicular velocities observed for all four CBP-soil profiles under study. Measuring the pavement deflection is important because the structural competency of the sand bedding layer is indirectly reflected by the magnitude of pavement surface deflection, and they play a key role in amplifying the levels of traffic-induced vibrations throughout the service life of the pavement. The overall analysis of revealed that the deflection amplitudes observed correlated well with those identified in the literature (Panda and Ghosh Citation2002a, Shafabakhsh et al. Citation2014) at vehicular velocities of 40km/h, thus verifying the reliability of the model and hence further analysis of the results was carried out. From (b) and (c), it is evident that the profiles with sand bed thicknesses of 20mm and 40mm recorded lower values of surface deflection irrespective of the vehicular velocity under consideration. The maximum displacement values were observed for the CBP-soil profiles with a 70mm thick sand bed, as shown in (d). The mechanism behind this phenomenon can be explained through the changes in resonance frequency of the CBP- soil system induced due to the varying soil profiles – that is, the varying sand bed thickness. Resonance frequency values are those corresponding peak displacement amplitude in the graphs. The values of the first and second modes of natural frequency values of the soil profiles under study are listed in .
Figure 8. Variation of displacement amplitudes observed at the loading surface in the frequency domain with varying vehicular velocities for the CBP section with sand bed thickness of, (a) 10mm, (b) 20mm, (c) 40mm, and (d) 70mm.

Table 4. Natural frequency values and Damping constants of CBP-soil profiles.
Generally, the resonance condition was observed for the second mode of natural frequency in every case of the CBP-soil profile. Decreasing the sand bed thickness from 20mm to 10mm, resulted in a decrease in the system’s resonant frequency, while the surface deflection values showed a noticeable increase. This can be attributed to the reduction in the dampening behaviour of the soil profile induced by the degradation in the stiffness matrix of the whole CBP system owing to the thin section (10 mm) of the bedding sand layer. This concept is well evident from the reduced values of the equivalent damping ratio listed in . Similar behaviour of increasing surface deflection is observed in the experimental studies on CBP sections when the thickness of sand bed was reduced to values less than 20mm (Panda and Ghosh Citation2002a, Shafabakhsh et al. Citation2014). The increase in surface deflection may seem small, but after the innumerable vehicle passes, the surface sinking also is amplified, leading to vertical rotation of paving blocks. Nonetheless, laying a thin sand bedding layer may fail to provide the uniform surface required for laying the paving blocks, causing surface unevenness and reducing the interlocking efficiency. Moving towards the analysis of CBP sections with thicker sand beds, there was a substantial decrease in the natural frequency of the CBP-soil system with increasing sand bed thickness to 70mm. This is evident from , where the CBP-soil model with a 70mm sand bed recorded the lowest values of natural frequency. The corresponding low values of equivalent damping ratio can signify degradation in the stiffness matrix higher than that observed in CBP profiles with a 10mm thick sand bed. Overall, the reduced dampening and the associated spike in the peak displacement amplitude observed with the cases of 10mm and 70mm thick bedding sand can be reasoned as follows.
In the case of CBP systems with 20mm and 40mm thick sand beds, the natural frequency is higher than the loading frequency, thereby resulting to lower surface deflections, unlike in CBP systems with 10mm and 70mm thick sand beds. This trend theoretically relates to the interaction between the vehicle’s operating frequency and CBP surface roughness. In general, the operating frequency of vehicles in the case of CBP systems is proportional to the wavelength of road roughness and directly proportional to the vehicle speeds (Al-Qadi et al. Citation2008), as typically explained by equation (4).
(4)
(4) where v is the velocity (in m/s) and
. is the wavelength number. The value of
in real-time, is recorded in the range of 0.5–1 (Lak et al. Citation2011). Therefore, at a wavelength number of 1, the frequency range of vehicular loads at velocities of 40, 50, and 70km/h will be in the range of 11.11Hz to 19.1Hz. Lower values of natural frequency obtained for CBP systems with 70mm and 10mm thick sand bed were found in this range of operating frequency of vehicles, thus causing amplification of acceleration and, thereby, higher displacement. Especially in the case of the CBP section with a 70mm sand bed, the operating frequency of vehicles moving at 70km/h (18.85Hz) is almost equivalent to that of the natural frequency of the CBP soil section, thereby causing resonance, resulting in increased surface deflection. This overall trend of higher displacement amplitudes for CBP systems in the case of 10mm and 70mm sand beds was observed to amplify further at higher vehicular speeds, as evident from (d).
In general, observations from show that an increase in vehicle velocity from 40km/h to 50km/h results in decreasing displacement values irrespective of the sand bedding thickness used. However, this trend does not hold good for velocity increasing from 50km/h to 70km/h – only CBP systems with sand bed thicknesses of 20mm and 40mm show this trend. Contrary to the law of mechanics, higher deflection values were observed at higher speed for CBP systems with 10mm and 70mm thick sand beds, with a substantial increase observed for the latter case, as evident from (d). By theory, the stress values and associated deflection tend to diminish at higher speeds due to the reduction in loading time. Nevertheless, this seems to be not the case from the results of this study. The deflection values reported for every case from the FE modelling have good agreement with the experimental results, thereby bringing more confidence to this statement. Thus, it can be concluded with confidence that the sand bed thickness also significantly influences the dynamic response of the CBP system subjected to vehicle loads at different velocities.
shows the acceleration response of the CBP system in the frequency domain, measured at the centre of the loading surface for all the three-vehicle velocities under consideration. Higher acceleration values are observed for the CBP system with a 70mm thick sand bed ((d)), followed by CBP systems with a 10mm and 20mm thick sand bed. The least value of acceleration is observed in (c), where a 40mm thick sand bed is used. The peak vertical acceleration is observed mainly in the frequency range of 11 to 19Hz, as this is the operating frequency range of vehicles on CBP test sections – refer to Equation (4) discussion. The drastic increase in accelerations for 70mm case, is due to the occurrence of resonance conditions at frequencies of dynamic excitation equivalent to the natural frequency of that CBP system. Unlike the observations with displacement amplitudes, increasing the velocity from 40 to 70km/h did not show a considerable increase in acceleration amplitude for cases with 20mm and 40mm sand bed thickness. Results show a 2% to 5% decrease in acceleration amplitude recorded at 50km/h compared to 40km/h for all four cases of CBP systems. Generally, increasing vehicular speed will result in increasing peak acceleration, owing to a reduction in time between consecutive excitation (by the pavement surface irregularities). However, upon repeated excitations of the moving wheel, acceleration values move out of phase and do not follow this trend anymore. This may have accounted for minor discrepancies observed at the speed level of 50km/h. Overall, the displacement and acceleration amplitudes double up owing to the increase in sand bed thickness to 70mm, with the next highest values observed for the 10mm case. In both cases, the natural frequency of the CBP system is reduced to the range of dynamic excitations, resulting in higher deflection and acceleration amplitudes.
5.2. Influence of ROPS−layer embedment depth
The sand bed thickness in CBP systems is subjected to variations depending on several conditions, and no single design value is followed globally. Measures to curtail the dynamic response of the CBP system due to varying sand bed thickness are crucial. Material damping plays a key role in reducing the unacceptable levels of deflection amplitude and acceleration, especially when the operating frequency range is near resonance. Therefore, increasing the dampening nature by the inclusion of an elastic material in the underlying soil layers can effectively attenuate excess vehicular vibrations. Rubberised oil palm shell (ROPS) layer in one such attempt studied in this paper. ROPS is not only elastic but also stiff, which would be beneficial in reducing the high levels of vertical acceleration and displacement amplitudes – discussed in Section 5.1. For this purpose, optimising the depth of placement is pivotal. Based on outcomes from Section 5.1, the critical CBP–soil profile is with 70mm sand bed thickness, having higher values of acceleration and displacement. This profile, therefore, is used in the FE simulations with ROPS layers placed at different embedment depths – refer to under Series 2. In this series of trials, the ROPS layer with different OPS content – 0%, 5%, 10%, and 20% are used (denoted as R0, R5, R10, and R20, respectively). Twenty-one graphs of displacement amplitude vs frequency response are generated for every case, which is difficult to delineate in a single figure. Therefore, the results from representative CBP soil profiles incorporated with the R20 ROPS layer alone are presented. While the results obtained from all 21 graphs were used to analyse the optimum percentage of OPS content in ROPS layers – discussed in Section 5.3. shows the variation of displacement and acceleration amplitudes, respectively. As anticipated, both the displacement and acceleration amplitudes decrease with the inclusion of the ROPS layer in the CBP system. It should be noted that at the embedment depth of 80mm, adhesive contact elements are used to model the interaction between concrete block and ROPS layers – so that they behave as a single unit, and this avoids any relative movements. A smaller decrease observed in the amplitudes up to an embedment depth of 80mm is likely related to the increasing stiffness emerging from the concrete block−ROPS tie. With the embedment depth increased beyond 80mm, a considerable reduction in deflection and acceleration values emerged. An embedment depth of around 180mm shows the least possible values of displacement. Even in the case of acceleration amplitudes, this trend was right at velocities of 40 and 50kmph, whereas, at the higher velocity of 70kmph, a reduction in acceleration amplitude was observed in the depth range of 150 to 180mm. This minor discrepancy arising in the acceleration amplitude values is due to the repeated excitation from the moving wheel (refer to section 5.1). This was considered negligible since the difference is in the range of 10−2. Henceforth an embedment depth of around 180mm will be considered as the optimum value of embedment depth. Further increases in the embedment depths show an increase in displacement and acceleration amplitudes. No effect of placing the ROPS layer was evident with embedment depth greater than 1000mm, and amplitudes were similar to cases of CBP systems without ROPS layers.
5.3. Influence of OPS content in the ROPS layer
The percentage of OPS content in the ROPS layer is highly likely to influence the dampening nature of the whole CBP system due to its physical and structural properties as described in section 1. Henceforth efforts were made to study its effect on the dynamic response of CBP soil system. shows the variation of resonant frequency, displacement, and peak vertical acceleration amplitudes of the CBP soil system reinforced with ROPS layers with varying OPS contents (R0, R5, R10, and R20). This analysis used the optimum embedment depth of 180mm – from Section 5.2. The CBP soil system with 70mm sand bed thickness, which posed higher values of acceleration and displacement amplitudes (refer to under Series 3), is chosen to show the influence of OPS content in the ROPS layer. As explained in Section 4.2, the cap plasticity model is used to simulate the soil layers. As observed from the figures decreasing the ROPS content from 20% to 5% shows an increase in the displacement and acceleration amplitudes, whereas a decrease in the resonance frequency. The percentage increase in the displacement and acceleration amplitudes are as high as 33% and 25% for changes of OPS content in ROPS layers from 20% to 10%, respectively. Moreover, the deflection amplitudes higher than that of the CBP sections with no ROPS layer were observed when pure rubber with no OPS was used. The mechanism behind this phenomenon can be explained as follows. With increasing OPS content from 0 to 20%, the compressive strength of the rubberised oil palm shell composite increases by 2.5 folds. Young’s modulus, vertical stiffness, and lateral stiffness values subsequently increase as well. Increasing stiffness values with the addition of OPS ensures no lateral bulging to have occurred, which otherwise would result in increased acceleration and large surface deflections – as encountered in the case of using rubber without OPS. When a stiffer rubber composite layer is used in combination with the soil system, the dampening effect of the entire system is most likely improvised owing to the increased shear modulus. This attributes to the reducing dynamic acceleration values obtained when ROPS layers with 20% OPS are used. Nevertheless, this does not mean or assume that the increasing OPS beyond 20% will yield a stiffer layer. As evident from previous studies on ROPS, 20% OPS has been proven the optimum value based on results from cyclic compression tests (Anandan et al. Citation2020). However, using higher OPS contents may lead to cracking of the layers under repeated cyclic loads. Despite that, the ROPS layers with 5% and 10% OPS can also attenuate the vibrations; their flexibility is a little high, and magnification observed in displacement and acceleration amplitudes can be larger at higher vehicular velocities. Therefore, the ROPS layer with 20% OPS content is the most suitable option for the CBP systems studies, based on the results from this study.
5.4. Effect of ROPS reinforcement on CBP system
The simulations under Series 4 (refer to ) focused on all four CBP−soil profiles with the ROPS layer at an optimum depth of 180mm. The vehicle velocities varied from 40km/h to 70km/h in every case. and show the response of ROPS embedded CBP systems expressed as displacement and acceleration amplitudes, respectively. As compared to and , it is evident that the displacement and acceleration amplitudes have considerably decreased. Even for the critical case of CBP soil profile with R20 ROPS layer and 70mm thick sand bed at 70km/h, substantial percentage decrease was observed for displacement amplitudes which is around 58% - see (d). The inclusion of ROPS layers mainly reduces the vibration levels to acceptable levels in the cases of 10mm and 70mm sand bed thickness but is not comparable to the levels as observed with 20mm and 40mm thick sand beds. This is because, with 20mm and 40mm thick sand beds, the stiffness of the whole model increased further after the inclusion of ROPS. Nevertheless, with 10mm and 70mm thick sand beds, the ROPS layers had to first negate the effect of excessive vibrations caused by the loose and less stiff sand bed. Following this, the peak acceleration and deflection amplitudes most likely were reduced by the increase in equivalent stiffness of the soil substratum. Another important observation from is that the peak displacement amplitudes were obtained in the frequency range of 23–26Hz, which is reasonably away from the typical frequency range of the operating vehicles on the CBP system (11 to 18Hz). The provision of ROPS increased the resonant frequency values which indirectly indicates improved dampening in the CBP soil system. Similarly, the amplification in the acceleration amplitude was also reduced by a significant amount of 47% after introducing ROPS layers, as evident from The trend of higher values recorded for 70mm and 10mm thick sand bed cases remained the same. Nonetheless, these peaks are observed in the frequency range of 23–80Hz, which is again outside the operating frequency range, thus suggesting no resonance condition. Regarding the effect of vehicle velocity on the dynamic response of ROPS embedded CBP systems, the increasing trend of deflection and acceleration amplitudes with increasing velocity from 50km/h to 70km/h remains similar. This is attributed to the frequency of dynamic loading at a higher velocity (18.85Hz), which is the nearest value to the modified natural frequency of the four CBP systems considered in this study (23–26Hz). Moreover, even in the current case of the ROPS reinforced soil system, the effect of velocity is overcast by the variation in the soil profile as indicated by the rate of increase in deflection. This value is only 17% as velocity shifts from 40km/h to 70km/h as against the rate of increase of 51% observed for changing the sand bed thickness from 40mm to 70mm – refer to (c) and (d). Overall, it is evident that the inclusion of ROPS likely leads to an increase in the dampening effect, thereby reducing the vibration levels in the CBP system.
5.5. Comparison of displacement contours with and without ROPS layer
(a to d) shows the vertical deflection in CBP systems with and without the ROPS layer, simulated under a dynamic vehicular load moving at a velocity of 40km/h. For comparison purposes, CBP-soil models with minimum vertical deflection (CBP with 20mm sand bed thickness) and maximum vertical deflection (CBP with 70mm sand bed thickness) were chosen for the contour representation of vertical deformation. All four figures represent the deformation contours of the longitudinal section (a half-section along the middle of the loaded area) in order to better understand the deformation behaviour of the substructure layers. It is well observed from the figures, that the maximum vertical deflection is encountered in the vicinity of the loaded area on the CBP surface. Especially before the provision of the ROPS layer (b), maximum deformation is highlighted in the joints between paving blocks due to the hinge formation phenomenon under loading. Whereas in the case of CBP systems with a 20mm thick sand bed (a), maximum deformation is seen in the sand bed, owing to its ability to take the load impact and deform while simultaneously reducing the rotation of blocks. These observations are in close agreement with the findings of Gunatilake and Mampearachchi (Citation2019); Panda and Ghosh (Citation2002a, Citation2002b) and Huurman (Citation1996). The magnitude of vertical deformation substantially decreased along the depth of the substructure layers after the provision of ROPS layers, as can be seen in (c) and (d). Moreover, after the provision of ROPS, the vertical deformation contours were concentrated well within one-third to one-half depth from the loading surface as against one-half to two-thirds depth observed for no ROPS conditions. These results further confirm the ability of ROPS layers to reduce the vertical deformations occurring in the substructure of the CBP system under vehicular loading.
5.6. Comparison of displacement contours under varying OPS contents
(a) to (d) shows the vertical deformation contours in CBP systems embedded with ROPS layers of varying OPS contents. To showcase the maximum efficiency of the ROPS layer, the CBP system with a 70mm thick sand bed was chosen for comparison purposes. All four figures represent the deformation contours of the longitudinal section (a half-section along the middle of the loaded area) in order to better understand the deformation behaviour of the substructure layers. (d) shows the conventional CBP system without any ROPS layer. The vertical deformation is maximum at the surface, especially at the joints, due to rotation and sinking in of blocks. Reinforcing the substructure with a pure rubber layer without any OPS content affected the dynamic behaviour of the CBP system negatively. This is evident from the deformation contours in (c), showing deflection values higher than that of the conventional CBP system. The provision of a ROPS layer with 5% OPS content (a) still resulted in the sinking in of blocks, but the magnitude is considerably less than that of the CBP system with no ROPS layer. A substantial decrease in surface deflection was observed for CBP systems, with the ROPS layer having 20% OPS content. As can be seen from (b), the faulting of the paving block layer is barely seen, and most of the deformations were concentrated within one-third depth from the surface.
5.7. Comparison of cases with and without ROPS layer
The influence of ROPS embedment on the DAR, resonance frequency and peak acceleration amplitude of the CBP soil profiles were numerically analysed and depicted in the following (a to c). (a) shows the variation of displacement amplitude reduction ratio (DAR) for CBP systems with different sand bed thicknesses obtained at the three loading velocities used in this study. DAR is defined as the ratio of displacement amplitude of CBP with the ROPS layer to that of CBP without the ROPS layer. Lower values of DAR symbolise higher efficiency of the ROPS layer in effectively reducing the traffic-induced vibrations. Observations from the figures show low DAR values for the CBP systems with 20mm and 40mm thick sand beds subjected to vehicle velocities of 40km/h and 50km/h. This indicates that higher efficiency of the ROPS layer can be expected for CBP systems with 20mm and 40mm thick sand beds. The DAR values obtained for 70km/h were relatively high irrespective of the sand bed thickness. At the same time, the DAR values for CBP systems with 10mm and 70mm thick sand beds are relatively higher. Nonetheless, about 60% reduction in the peak displacement amplitudes is observed after providing the ROPS layer, as shown by a DAR value of 0.42. This further strengthens the suitability of utilising ROPS layers as potential reinforcement in the CBP−soil systems to reduce vibration levels and associated deflections. Similar conclusions can be drawn to compare resonance frequency for CBP systems before and after ROPS reinforcement. (b) shows the variation in resonance frequency for all four CBP profiles with and without ROPS layers under the vehicle velocity of 70km/h. As anticipated, the resonance frequency of CBP systems increased by at least 4.5Hz after the inclusion of the ROPS layer, moving away from the expected operating frequency, thus avoiding resonance.
Figure 16. Variation of (a) displacement amplitude ratio (DAR) at different velocities, (b) resonance frequency at V = 70km/h with and without ROPS layers, and (c) peak acceleration at V = 70km/h (V70) of CBP-soil system reinforced with ROPS (with 20% OPS content) layers (R20) subjected to different sand bed thickness (10, 20 and 70mm).

(c) shows the variation of peak acceleration amplitudes observed at various depths in the CBP system with and without ROPS layers. Mass scaling of the peak accelerations amplitudes was carried out to avoid errors caused by obtaining acceleration values at nodes that do not have mass. As shown in (c), for all cases of CBP−soil profiles, a sharp dip in acceleration values occurs at 80mm depth. Within the depth of 140mm, a significant portion of the vibration energy emerging from the dynamic oscillations was attenuated. After the depth of 140mm, the rate of reduction of acceleration values was reduced and remained stable after that. This indicates that the dynamic effects of the paving block layer and bedding sand layer are likely to disperse traffic loads effectively as compared to the subgrade and base course layers. In addition, the acceleration values of the vibration did not approach zero even at higher depths and were found within a small range of 0.06–0.00088. This can be attributed to the numerical problem arising from the bedrock simulation (fixed boundary constraint), where minimal damping ratio values are assumed in the ABAQUS FE package, thus resulting in small values of acceleration amplitudes. Such behaviour is also reported in the literature (Karatzetzou et al. Citation2014). For CBP systems with a 10mm thick sand bed, the peak acceleration amplitude at the surface was similar to that of a 20mm thick sand bed case. This is because of the calibration effect of Rayleigh damping, which leads to acceleration values being underestimated at the ground surface. The acceleration values reduced drastically after including the ROPS layer at 180mm depth in the layers below. About 96% reduction in acceleration amplitudes was observed for CBP systems with 20mm and 40mm thick sand beds, even at shallow depths of 300mm. These observations thus suggest the suitability and possibility of ROPS reinforcement in CBP systems to avoid excessive displacement and resonance conditions.
6. Conclusion
Traffic vibrations caused by dynamic excitations from wheel load due to road surface irregularities are a significant concern, especially in CBP systems having periodic joints. CBP-type pavements have been increasingly used in the recent decade due to their ease of installation and aesthetic value. The current study presents a preliminary investigation into the effect of ROPS reinforcement on the amplitude levels of vibration observed in CBP systems with varying sand bed thickness. Efforts have been made to capture the inhomogeneity in the soil substructure of CBP to a certain extent by including two different soil layers underlying paving blocks and bedding sand subjected to different vehicle velocities. The testing programme focused on parametric studies using FE models of CBP−soil systems. The simulation results revealed that CBP systems with very thin (10mm) or thick (70mm) sand bed thickness experienced higher surface displacements and acceleration. The scale of changes in the dynamic response of pavement induced due to varying velocity of vehicular loads was low compared to those induced by varying sand bed thickness. Thus, proving the significance of soil properties in controlling the response of CBPs. The CBP system embedded with a ROPS layer of 20% OPS content shows reduced surface deflection values compared to 5% and 10% OPS content, owing to reduced lateral bulging and increased vertical stiffness at 20% OPS content. After including ROPS layers at an optimised depth of 180mm from the surface, about 58% deamplification in peak acceleration and displacement values were observed. However, increasing the ROPS embedment depth beyond 180mm leads to dynamic responses similar to cases without ROPS, thus signifying the profile conditions where the ROPS layer can function at maximum efficiency. Therefore, adopting ROPS reinforcement would be an ideal approach to reduce the level of traffic vibrations arising from surface irregularities in CBP systems. The future studies should preferably include the gradation properties of sand beds and variation in laying patterns of paving blocks since they might influence the variation trend and amplitude levels. This study is an intrinsic attempt to ascertain the suitability of ROPS layers in CBPs using FE simulation. However, more experimental and field investigations considering different vehicle classes and FE simulations using real-time boundary conditions are certainly crucial to get a better insight and further develop this approach for field applications. To this end, this study provides an insight into the basic mechanism governing the response of CBP system subjected to varying sand bed thickness, vehicular velocity, and inclusion of ROPS.
Acknowledgements
Support for conducting the finite element simulations received from the High-Performance Computing (HPC) and the Unified Research Computing (URC) platforms at Monash University Malaysia is highly acknowledged. The authors acknowledge Ms. Shack Yee Hiew and Mr. Wai Hong Lim (former Bachelor of Civil Engineering students at Monash University Malaysia) for their support and assistance during the laboratory experiments of this study.
Disclosure statement
No potential conflict of interest was reported by the author(s).
References
- Ah, N. H., Nor, H. M., and Azman, M., 2014. Effect of jointing sand sizes and width on horizontal displacement of concrete block pavement. Jurnal Teknologi, 71 (3), doi:10.11113/jt.v71.3764.
- Al-Oqla, F. M., and Sapuan, S., 2014. Natural fiber reinforced polymer composites in industrial applications: feasibility of date palm fibers for sustainable automotive industry. Journal of Cleaner Production, 66, 347–354. doi:10.1016/j.jclepro.2013.10.050.
- Al-Qadi, I. L., Xie, W., and Elseifi, M. A, 2008. Frequency determination from vehicular loading time pulse to predict appropriate complex modulus in MEPDG. Asphalt Paving Technology-Proceedings, 77, 739.
- Alengaram, U. J., et al., 2013. A comparison of the thermal conductivity of oil palm shell foamed concrete with conventional materials. Materials & Design, 51, 522–529. doi:10.1016/j.matdes.2013.04.078.
- Anandan, S., et al., 2020. Numerical and experimental investigation of oil palm shell reinforced rubber composites. Polymers, 12 (2), 314. doi:10.3390/polym12020314.
- Asheghabadi, M. S., and Cheng, X., 2020. Analysis of undrained seismic behavior of shallow tunnels in soft clay using nonlinear kinematic hardening model. Applied Sciences, 10 (8), 2834. doi:10.3390/app10082834.
- Baidya, D., and Krishna, G.M., 2001. Investigation of resonant frequency and amplitude of vibrating footing resting on a layered soil system. Geotechnical Testing Journal, 24 (4), 409–417. doi:10.1520/GTJ11138J.
- Baidya, D., and Mandal, A., 2006. Dynamic response of footing resting on a layered soil system. West Indian Journal of Engineering, 28 (2), 65–79.
- Basri, H., Mannan, M., and Zain, M. F. M., 1999. Concrete using waste oil palm shells as aggregate. Cement and Concrete Research, 29 (4), 619–622. doi:10.1016/S0008-8846(98)00233-6.
- Chiroux, R., et al., 2005. Three-dimensional finite element analysis of soil interaction with a rigid wheel. Applied Mathematics and Computation, 162 (2), 707–722. doi:10.1016/j.amc.2004.01.013.
- Di Mascio, P., Moretti, L., and Capannolo, A., 2019. Concrete block pavements in urban and local roads: analysis of stress-strain condition and proposal for a catalogue. Journal of Traffic and Transportation Engineering (English Edition), 6 (6), 557–566. doi:10.1016/j.jtte.2018.06.003.
- Füssl, J., et al., 2018. Numerical simulation tool for paving block structures assessed by means of full-scale accelerated pavement tests. International Journal of Pavement Engineering, 19 (10), 917–929. doi:10.1080/10298436.2016.1224410.
- Füssl, J., Kluger-Eigl, W., and Blab, R., 2016. Experimental identification and mechanical interpretation of the interaction behaviour between concrete paving blocks. International Journal of Pavement Engineering, 17 (6), 478. doi:10.1080/10298436.2014.993205.
- Gazetas, G., 1981. Machine foundatios on deposits of soft clay overlain by a weathered crust. Géotechnique, 31 (3), 387–398.
- Gunatilake, D., and Mampearachchi, W., 2019. Finite element modelling approach to determine optimum dimensions for interlocking concrete blocks used for road paving. Road Materials and Pavement Design, 20 (2), 280–296. doi:10.1080/14680629.2017.1385512.
- Hanipah, S.H., Mohammed, M.A.P., and Baharuddin, A.S., 2016. Non-linear mechanical behaviour and bio-composite modelling of oil palm mesocarp fibres. Composite Interfaces, 23 (1), 37–49. doi:10.1080/09276440.2016.1091681.
- Hasan, A. R., and Nair, P. L., 2014. Urbanisation and growth of metropolitan centres in Malaysia. Malaysian Journal of Economic Studies, 51 (1), 87–101.
- Hassani, A., and Jamshidi, A., 2006. Modelling and structural design of a concrete block pavement system. 8th international conference on concrete block paving, November 2006, California USA.
- Hegde, A., and Venkateswarlu, H., 2019. Mitigation of traffic induced vibration using geocell inclusions. Frontiers in Built Environment, 5, 136. doi:10.3389/fbuil.2019.00136.
- HL-93 AASHTO Vehicular Live Loading, 2014. Online source. Available from: https://engineeringcivil.org/articles/bridge/hl-93-aashto-vehicular-live-loading-truck-tandem-design-lane-load/ [Accessed 25 January 2022]
- Huurman, M, 1994. Longitudinal unevenness and dynamic axle loading: on concrete block pavements. Available from: http://www.sept.org/techpapers/511.pdf [Accessed March 2023].
- Huurman, M., 1996. Development of traffic induced permanent strain in concrete block pavements, 41, 29-52. Available from: https://repository.tudelft.nl/islandora/object/uuid:1314a091-f6f3-422d-b2a8-4e14aeede69b/datastream/OBJ/download.
- Huurman, M., et al., 2003. The upgraded Dutch design method for concrete block road pavements. 7th International Conference on Concrete Block Paving, Africa.
- IRC: SP:63, 2004. Guidelines for the use of interlocking concrete block pavement. The Indian Roads Congress.
- Jakubczyk-Galczynskaa, A., and Jankowskib, R., 2014. Traffic-induced vibrations. The impact on buildings and people. 9th international conference in environmental engineering, May 22-23, Lithuania. doi:10.3846/enviro.2014.028.
- Karatzetzou, A., et al., 2014. A comparative study of elastic and nonlinear soil response analysis. 2nd European conference on earthquake engineering and seismology, Istanbul, Turkey.
- Kelly, J. M., and Konstantinidis, D., 2011. Mechanics of rubber bearings for seismic and vibration isolation. United Kingdom: John Wiley & Sons. doi:10.1002/9781119971870.
- La Agostinacchio, M., Ciampa, D., and Olita, S., 2008. The vibrations induced by surface irregularities in road pavements – a Matlab® approach. European Transport Research Review: Mechanisms, Modeling, Detection, Testing and Case Histories, 201), doi:10.1007/s12544-013-0127-8.
- Lak, M. A., Degrande, G., and Lombaert, G., 2011. The effect of road unevenness on the dynamic vehicle response and ground-borne vibrations due to road traffic. Soil Dynamics and Earthquake Engineering, 31, 1357–1377. doi:10.1016/j.soildyn.2011.04.009.
- Lilley, A. A., and Dowson, A. J., 1988. Laying course sand for concrete block paving. Available from: http://www.sept.org/techpapers/153.pdf.
- Lin, W., Cho, Y.-H., and Kim, I. T., 2016. Development of deflection prediction model for concrete block pavement considering the block shapes and construction patterns. Advances in Materials Science and Engineering, 2016), doi:10.1155/2016/5126436.
- Ling, T., et al., 2010. Long-term strength of rubberised concrete paving blocks. Proceedings of the Institution of Civil Engineers - Construction Materials, 163 (1), 19–26. doi:10.1680/coma.2010.163.1.19.
- Loi, S. J., et al., 2020. Compaction characteristics of kaolin reinforced with Raw and rubberized Oil palm shell. Minerals, 10 (10), 863. doi:10.3390/min10100863.
- Lombaert, G., Degrande, G., and Clouteau, D., 2000. Numerical modelling of free field traffic-induced vibrations. Soil Dynamics and Earthquake Engineering, 19 (7), 473–488. doi:10.1016/S0267-7261(00)00024-5.
- Mampearachchi, W., and Gunarathna, W., 2010. Finite-element model approach to determine support conditions and effective layout for concrete block paving. Journal of Materials in Civil Engineering, 22 (11), 1139–1147. doi:10.1061/(ASCE)MT.1943-5533.0000118.
- Murugan, R. B., Natarajan, C., and Chen, S.-E., 2016. Material development for a sustainable precast concrete block pavement. Journal of Traffic and Transportation Engineering (English Edition), 3 (5), 483–491. doi:10.1016/j.jtte.2016.09.001.
- Panda, B. C., and Ghosh, A. K., 2002a. Structural behavior of concrete block paving. I: Sand in bed and joints. Journal of Transportation Engineering, 128 (2), 123–129. doi:10.1061/(ASCE)0733-947X(2002)128:2(123).
- Panda, B. C., and Ghosh, A. K., 2002b. Structural behavior of concrete block paving. II: Concrete blocks. Journal of Transportation Engineering, 128 (2), 130–135. doi:10.1061/(ASCE)0733-947X(2002)128:2(130).
- Park, J., Choi, S., and Jung, H. M., 2020. Measurement and analysis of vibration levels for truck transport environment in Korea. Applied Sciences, 10 (19), 6754. doi:10.3390/app10196754.
- Population Reference Bureau, 2007. Online source. Available from: https://www.prb.org/resources/urban-population-to-become-the-new-majority-worldwide/ [Accessed 21 December 2022].
- Priyadarshee, A., et al., 2018. Compaction and strength behavior of tire crumbles–fly ash mixed with clay. Journal of Materials in Civil Engineering, 30 (4), doi:10.1061/(ASCE)MT.1943-5533.0002171.
- Rada, G. R., et al., 1992. Structural design of interlocking concrete pavements in North America. 4th Structural Design of Interlocking Concrete Pavement in North America, 1, 99-116. Available from: http://sept.org/techpapers/11.pdf.
- Robert, D., Soga, K., and Britto, A., 2015. Soil constitutive models to simulate pipeline-soil interaction behaviour. International conference on geotechnical engineering ICGE Colombo, Sri Lanka.
- Sacramento, C., 2002. Transportation-related earth borne vibrations. Technical Advisory. California Department of Transportation. Available from: http://www.vibrationdata.com/tutorials_alt/caltrans_earth.pdf.
- Sahari, J., and Maleque, M., 2016. Mechanical properties of oil palm shell composites. International Journal of Polymer Science, 2016), doi:10.1155/2016/7457506.
- Selcuk, I. A., and Cubukcu, K. M., 2015. Modelling traffic-induced, in-dwelling vibration using urban design and planning variables. Journal of Architectural and Planning Research, 307–323. Available from: https://www.jstor.org/stable/44113118.
- Shackel, B., 1988. The evolution and application of mechanistic design procedures for concrete block pavements. 3rd international conference on concrete block paving, Rome. Available from: http://www.sept.org/techpapers/108.pdf.
- Shackel, B., 1991. The performance of interlocking block pavements under accelerated trafficking. National Institute of Transport and Road Research, CSIR, South Africa. Available from: http://www.sept.org/techpapers/85.pdf.
- Shafabakhsh, G., Family, A., and Abad, B. P. H., 2014. Numerical analysis of concrete block pavements and comparison of its settlement with asphalt concrete pavements using finite element method. Engineering Journal, 18 (4), 39–51. doi:10.4186/ej.2014.18.4.39.
- Sivakumar Babu, G., and Vasudevan, A., 2008. Strength and stiffness response of coir fiber-reinforced tropical soil. Journal of Materials in Civil Engineering, 20 (9), 571–577. doi:10.1061/(ASCE)0899-1561(2008)20:9(571).
- Soutsos, M. N., et al., 2011. The effect of construction pattern and unit interlock on the structural behaviour of block pavements. Construction and Building Materials, 25 (10), 3832–3840. doi:10.1016/j.conbuildmat.2011.04.002.
- Teo, D.C., Mannan, M.A., and Kurian, J.V., 2006. Flexural behaviour of reinforced lightweight concrete beams made with oil palm shell (OPS). Journal of Advanced Concrete Technology, 4 (3), 459–468. doi:10.3151/jact.4.459.
- Yadav, J. S., and Tiwari, S. K., 2017. A study on the potential utilization of crumb rubber in cement treated soft clay. Journal of Building Engineering, 9, 177–191. doi:10.1016/j.jobe.2017.01.001.
- Yang, G., et al., 2016. Truck acceleration behavior study and acceleration lane length recommendations for metered on-ramps. International Journal of Transportation Science and Technology, 5 (2), 93–102. doi:10.1016/j.ijtst.2016.09.006.
- Ye, Z., Lu, Y., and Wang, L., 2018. Investigating the pavement vibration response for roadway service condition evaluation. Advances in Civil Engineering, 2018, doi:10.1155/2018/2714657.
- Zakeri, R., et al., 2021. Influence of rubber sheet on dynamic response of machine foundations. Construction and Building Materials, 274, 121788. doi:10.1016/j.conbuildmat.2020.121788.