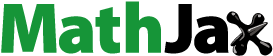
ABSTRACT
Strain ageing embrittlement behaviour of X80 self-shielded flux-cored arc welding (FCAW) girth weld metal at different strain ageing conditions (1% prestrain, and aged at 150°C/100°C for 1 –6 h, and 80°C for 1–30 days) was studied. Microstructure of FCAW girth weld generally consisted of coarse granular bainite and lath bainite. After strain ageing, toughness notably decreased, and higher ageing temperature or longer ageing induced lower toughness, until ageing is fully yielded. At initial stage of strain ageing, more dimples were found accompanying with cleavage facet. With the progress of strain ageing, the embrittlement was more obvious, while larger cleavage facet and less dimples were found. Meanwhile, the critical size for cleavage fracture initiation site became smaller. Martensite–austenite constituent (1–2 μm) was found to initiate cleavage fracture when partially strain aged, while submicron inclusions could initiate cleavage facet when fully strain aged.
Introduction
Pipelines are the most efficient way for long distance oil and gas transportation, and natural gas pipelines were widely constructed in the past decades. Most of these pipelines are designed for more than 50 years [Citation1–6]. During service, they may sustain geological subsidence, landslide, earthquake, etc., which may cause the displacement of the pipeline, and hence the girth weld metal may bear strain concentration, especially for the under matched weld joint [Citation7,Citation8]. During the following long period service, the strained weld may suffer from loss of toughness caused by strain ageing.
Strain ageing is induced by the interaction between the interstitial atoms (i.e. carbon and/or nitrogen) and the dislocations, namely Cottrell atmosphere pining. The strain-aged material usually showed elevated strength and deteriorated toughness [Citation9–15]. Particularly, for the weld metal which contains more dissolved nitrogen due to poor protection of welding metallurgy, the strain ageing embrittlement is more obvious as well as harmful for the service safety of welded high-strength structures [Citation16–19]. Achar et al. [Citation20] investigated the influence of dissolved nitrogen on the strain ageing behaviour of manual shielded metal arc welding C-Mn steel weld metals, and the results showed that with the increasing of nitrogen content, the Charpy V-notch (CVN) energy and crack tip opening displacement (CTOD) values of the strain-aged weld metal notably decreased and the brittle-ductile transition temperature increased by 50°C. Moreover, post-weld stress relieving heat treatment could not retrieve the toughness for the high nitrogen content (210 ppm) weld metal, within which the nitrogen atoms in solution state could not be erased by precipitation. Research on submerged arc welding weld metal of MnMoNi steel from Patrocínio et al. [Citation21] showed that the as-cast microstructure of cap layer, which was consisted of coarse proeutectoid ferrite and side-plate ferrite, was more sensitive to the strain ageing than that of the reheated filler metal with the microstructure of fine polygonal ferrite (PF) and acicular ferrite (AF). After strain ageing, the transition temperature of cap layer increased by 78°C and the CVN upper shelf energy decreased by 44 J. Increment of the flow stress induced by strain ageing enables cleavage fracture initiation from smaller inclusions or defects was considered to be the main reason for the embrittlement of the strain-aged metals [Citation22].
Considering the complexity of welding, the strain-ageing behaviour of the weld metal using different welding methods is distinctive, due to varied microstructure, chemical composition and level of dissolved nitrogen. Self-shielded flux-cored arc welding (FCAW) was widely used in the last 20 years during the construction of pipelines in China. The nitrogen content of FCAW weld metal was proved to be as high as 250– 300 ppm and is much higher than that of the gas metal arc weld (GMAW) metal which is the major welding method for automatic girth welding of pipelines [Citation23]. The strain ageing embrittlement of high-strength pipeline girth weld attracted more attention in recent years. Previous research showed that CTOD value of GMAW girth weld decreased by 2–3 times after strain ageing [Citation24], and the strength of FCAW weld metal increased by 90 MPa. However, the strain ageing embrittlement of FCAW weld metal was rarely reported yet, which is of significance for the safety evaluation of in-service pipelines. For example, West-East Gas Pipeline Project No. 2, which is X80 grade and used FCAW as main weld method during construction, has been in service for more than 10 years, and some failure cases were found to be associated with strain ageing embrittlement. In this paper, strain ageing embrittlement behaviour of X80 FCAW girth weld metal under different strain ageing temperatures and periods was studied, and the embrittlement mechanism was analysed.
Experimental methods
A X80 grade pipe of Φ1219 mm × 18.4 mm was used to fabricate the girth weld. The same welding parameters with West-East Gas Pipeline Project No. 2 were used. Surface tension transfer welding was applied for root weld, using BOHLER SG3-P as welding consumable. For the hot pass, filling passes and cap pass, FCAW semi-auto welding was used, with welding wire of HOBERT 81N1.
Prestrain was conducted by through-thickness plate tensile. The tensile specimen was milled according to GBT228.1-2010, and its schematic is presented in . The specimen was tensiled at material testing machine (WDW-600), with a 30-mm extensometer attached across the weld joint. During tensile, the strain of the weld joint was monitored. When the online strain reached 1.5%, the tensile was stopped. Since in the industry, Rt0.5 is usually used as the yield strength, 1.5% online strain means that the weld joint has engendered 1% plastic deformation. The prestrained specimen was machined into 10 mm × 10 mm × 55 mm Charpy impact specimen, as indicated in . Before Charpy impact test, the specimen was aged at 150°C and 100°C for 1–6 h, and at 80°C for 1–30 days. The impact toughness of as-welded and strain-aged weld metal was tested at −10°C. The specimen which was only prestrained or only aged was also tested for comparison.
Figure 1. Schematic of through thickness plate tensile specimen for prestrain and CVN sample position.

The microstructure of the as-welded and strain-aged weld metal was polished and etched, and then observed using optical microscope (OM, Leica DM2500M) and scanning electron microscope (SEM, JEOL-7200 F). The fracture surface of CVN samples was characterized by stereo microscope (ZEISS SteREO Discovery) and SEM to reveal the embrittlement mechanism.
The stain-ageing sensitivity (CV) was calculated based on the method of GB/T 4160-2004, and the equation was listed as follows:
where is the Charpy absorbed energy before strain-ageing and
is that after strain-ageing.
Results and discussions
Microstructure
The microstructure of X80 FCAW weld metal is presented in . Either cap pass or filling passes were generally consisted of coarse granular bainite (GB) and lath bainite (LB), with small fraction of martensite–austenite (M-A) constituent and AF. As the as-welded metal, more GB was found in the cap pass than that in the filling passes. As previously reported, the toughness of FCAW weld has large scatter due to heterogeneous microstructure and high nitrogen and oxygen content. The nitrogen content of FCAW weld metal could be up to 250–300 ppm [Citation23], which could also stimulate strain ageing. Meanwhile, coarse GB and LB were reported more sensitive to strain ageing than fine AF and PF. Therefore, the FCAW weld is supposed to have high strain ageing sensitivity.
The microstructure of filling passes of X80 FCAW girth weld metal at different strain ageing conditions is presented in . Since all the ageing temperatures are not higher than 150°C, no phase transformation would occur. However, with higher ageing temperature or longer ageing period, some very fine precipitates were found in the ferrite matrix, as indicated in . These precipitates may have some positive effect on the toughness.
Strain ageing embrittlement behaviour
The CVN absorbed energy and strain-ageing sensitivity (CV) of X80 FCAW weld metal before and after strain ageing treatment are presented in and . The data of only 1% prestrained or only aged are also included for comparison. The as-welded FCAW weld metal has good toughness of 158.8 J. After prestrain or ageing, the toughness decreased to a certain extent, to around 105–115 J. However, after strain ageing, the toughness notably decreased. Since strain ageing is a diffusion controlled process, higher ageing temperature or longer ageing period could induce more significant loss of toughness as well as higher CV, until ageing is fully yielded. The results showed that 1% prestrain and 150°C ageing for 1 and 3 h both induced low toughness of ~60 J and high CV of around 60, which means at higher temperature of 150°C, 1 h is enough for complete ageing. Also, 1% prestrain and 100°C ageing for 6 h and 80°C ageing for 30 days both yielded toughness of ~60 J. At the initial stage of ageing, the toughness showed larger scatter, i.e. 100°C ageing for 1 h and 80°C ageing for 1 day, which means they are in the transition region.
Figure 4. Strain ageing embrittlement behaviour of FCAW girth weld metal. Charpy absorbed energy; (b) strain ageing sensitivity (CV).

Table 1. CVN absorbed energy and strain-ageing sensitivity (CV) of X80 FCAW weld metal before and after strain ageing treatment.
The allowable Charpy absorbed energy values in the criterion of West-East Pipeline Project No. 2 and No. 3, which are 80 J for minimum average and 60 J for minimum single value, are presented in ). The results showed that strain ageing has damaging effect for the service safety of high-strength pipeline girth weld. Once strain ageing occurs, it is easy that the toughness drops below the allowable value in the criterion, even the original toughness of FCAW girth weld metal is as high as 158.8 J. Strain of pipe body or girth weld metal, especially for the under matched girth weld, probably happens during the long time service when the landslide or geological movement occurs. Therefore, it is necessary and significant to take strain ageing into consider during the safety assessment of in-service pipelines. The property prediction of girth weld at in-service ageing condition is also meaningful.
Characterizationof fracture surfaces
Fracture surfaces of the CVN samples at different strain ageing conditions are presented in . The results showed that strain ageing induced obvious embrittlement of the FCAW girth weld metal, namely smaller ductile area and larger brittle area with the progress of strain ageing. SEM characterizations of the brittle regions of the CVN samples in are presented in . All the samples showed quasi-cleavage fracture. However, there were more ductile traces in the original sample or the initial ageing stage samples as shown in , and more dimples were found in these samples. Meanwhile, with the progress of strain ageing, the cleavage facet size became larger, and dimples were rarely found, which is the evidence for strain ageing embrittlement.
Figure 5. (a–h) Fracture surfaces of the CVN samples at different strain ageing conditions characterized by stereo microscope.

Figure 6. (a–h) Fracture surfaces of the CVN samples at different strain ageing conditions characterized by SEM.

Some in-depth characterizations of the fracture surfaces strain aged at 80°C for different periods are presented in . When strain aged at 80°C for 1 day, the characteristic of the fracture surface showed small cleavage facet accompanied with some small dimples. With the progress of strain ageing, M-A constituent with size of 1–2 μm was found to initiate the cleavage fracture when strain aged 80°C for 15 days. With further strain ageing, small inclusions (submicron in size) were found to be the initiation of cleavage facet. The results showed that with the progress of strain ageing, the strain ageing embrittlement was more obvious. This is in accordance with previously reported research [Citation22], strain ageing could induce the increment of the flow stress of the metals, which enables cleavage fracture initiation from smaller inclusions or defects, and it was considered to be the main reason for the embrittlement of the strain-aged metals.
Conclusions
In this paper, strain ageing embrittlement behaviour of X80 FCAW girth weld metal, with microstructure of GB and LB, at different strain ageing conditions was studied. The embrittlement effect with the progress of strain ageing was mainly represented as follows:
1. Notable toughness loss. Higher ageing temperature or longer ageing period induced more significant loss of toughness. Around 60% toughness loss was recorded when the strain ageing was fully yielded.
2. Larger cleavage facet and less dimples. More dimples were found accompanying with cleavage facet at initial stage of strain ageing. With the progress of strain ageing, the size of cleavage facet became larger and less dimples were found at the fracture surface.
3. Smaller critical cleavage fracture initiation size. M-A constituent with size of 1–2 μm was found to initiate the cleavage fracture when partially strain aged, while submicron inclusions could initiate the cleavage facet when fully strain aged.
Contribution of the present paper is that the damaging effect of strain ageing on high-strength FCAW girth weld was indicated. Therefore, it is necessary and significant to take strain ageing into consideration during the safety assessment of in-service pipelines. The property prediction of girth weld at in-service ageing condition is also meaningful.
Acknowledgments
The authors wish to acknowledge the financial support from the project of ‘Research on failure mechanism for girth weld of high steel pipeline’ (No. WZXGL202105).
Disclosure statement
No potential conflict of interest was reported by the authors.
References
- Cui TC, Zheng L, Wu HF. Effect of strain aging on mechanical properties of high strength pipeline steel with different composition[J]. Mater Mech Eng. 2010;34(5):30–32+55.
- Park HS, Kang JS, Yoo JY, et al. In situ TEM and APT analysis on the dislocations associated with solute carbons in strain-aged low carbon pipeline steels[J]. Mater Sci Forum. 2010;654:122–7.
- Zhao WG, Chen M, Chen SH, et al. Static strain aging behavior of an X100 pipeline steel[J]. Mater Sci Eng A. 2012;550:418–422.
- Cheng YF. Some technical considerations on ensuring the long term safe operation of China Russia east gas pipeline[J]. Oil Gas Storage Transp. 2020;39(1):1–8.
- Zhukov D, Konovalov S, Afanasyev A. Morphology and development dynamics of rolled steel products manufacturing defects during long-term operation in main gas pipelines[J]. Eng Fail Anal. 2020;109:104359.
- Lee S, Hwang B. Correlation of microstructure with tensile behavior and properties of API X70 pipeline steels subjected to strain aging[J]. J Iron Steel Res Int. 2020;27(3):319–324
- Zhang ZY. Key points of safety lifting design for girth weld of high grade and large diameter natural gas pipeline[J]. Oil Gas Storage Transp. 2020;39(7):740–748.
- Shuai J, Wang X, Zhang YH, et al. Main characteristics and safety evaluation of girth weld of high grade steel pipeline[J]. Oil Gas Storage Transp. 2020;39(6): 623–631
- Cottrell AH, Bilby BA. Dislocation theory of yielding and strain aging of iron[J]. Proc Phys Soc A. 1949;62:49–62.
- Baird JD. The effects of strain-ageing due to interstitial solutes on the mechanical properties of metals[J]. Metall Rev. 1971;16(1):1–18
- Rashid MS. Strain-aging of vanadium, niobium or titanium-strengthened high-strength low-alloy steels[J]. Metall Trans A. 1975;6(7):1265–1268.
- Narayanan BK, Brady N, Wang YY, et al. Effect of strain ageing on yield strength and post yield behavior of FCAW-G ferritic weld metal[J]. International Pipeline Conference. 2010;569–576
- Liang GC, Peng X, Juan ES, et al. Strain aging of X100 steel in service and the enhanced susceptibility of pipelines to stress corrosion cracking[J]. J Mater Eng Perform. 2013;22(12):3778–3782.
- Yan-hua L, Chi Q, Feng H, et al. Effect of strain aging on properties of X90 line pipe[J]. Eng Fail Anal. 2020;118:104844.
- Yang J, Bi ZY, Nan HH, et al. Strain aging behavior and sensitive temperature of X90 high strength pipeline steel[J]. Chin J Mater Res. 2021;35(10):769–777.
- Wang HK, Shang XX, Liu W, et al. Study on strain aging embrittlement of girth weld of high grade oil and gas pipeline[J]. Pressure Vessel Technol. 2021;38(5):8–13.
- Hoekstra S, Schmidt-van der Burg MA, Mandziej S, et al. Effect of artificial strain aging on microstructure and mechanical properties of a single-bead ferritic weld metal[J]. Mater Sci Technol. 1985;1(3):234–239.
- Kakovkin OS, Pen’kov VB Special features of absorption of nitrogen by metal in arc welding[J]. Weld Int. 1998;2(1):42–44.
- Shin JH, Jeong JS, Lee J, et al. Nitrogen-induced yield point phenomenon in an austenitic steel[J]. Mater Sci Eng A. 2020;774:138897.
- Achar DRG, Koçak M, Evans GM. Effect of nitrogen on toughness and strain age embrittlement of ferritic steel weld metal[J]. Sci Technol Weld. 1998;3(5):233–243
- Patrocínio AB, Novovic M, Bowen P. Effect of prestraining and strain-aging on toughness of MnMoNi steel weld metal[J]. J Mater Process Technol. 2004;155-116:1124–1131.
- McRobie DE, Knott JF. Effects of strain and strain aging on fracture toughness of C–Mn weld metal[J]. Mater Sci Technol. 1985;1(5):357–365.
- Yu P, Tian ZL, Pan C, et al. Gas in weld of self shielded flux cored wire[J]. Trans China Weld Inst. 2007;28(2):67–70.
- Gao SS, Di XJ, Li CN, et al. Effect of strain aging on fracture toughness of welded joints of high strain pipeline steel[J]. Trans China Weld. 2021;42(10):22–28.