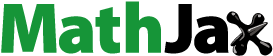
ABSTRACT
Magnesium (Mg) alloys are difficult to cold/warm-process due to their hexagonal close-packed (HCP) lattice, which has restricted slip systems and makes plastic deformation at low temperatures a challenging task. Multi-axial forging (MAF) and annealing of as-cast alloys were combined to create a texture-free ultrafine-grained (UFG) structure with a high strength-high ductility combination to address this challenge. The study showed a clear and fundamental change from basal and pyramidal dislocation slip to twinning in the strong and ductile UFG Mg alloy compared to the low strength coarse-grained (CG) Mg alloy counterpart. This implied that the dislocation activity, grain orientation, and particular grain boundary states played an important role in controlling the deformation mechanisms. The potential impact of processing Mg alloys by MAF opens-up a new frontier of strong and ductile low-density materials for light and efficient solutions including energy absorption and formability and provides a perspective in terms of process-structure-property relationship.
1. Introduction and challenge in processing high strength-high ductility Mg-alloys
The element magnesium (Mg) is available in plenty in nature, and its alloys display a variety of desirable characteristics, such as high specific strength and stiffness, excellent damping and shock absorption, high thermal conductivity, and great electromagnetic shielding ability [Citation1] [Citation2–5]. Despite the fact that these characteristics support the use of magnesium alloys in the automotive, aerospace, biomedical, and packaging industries, there are three factors that prevent their broad application. The first is that magnesium alloys are weaker than their aluminium counterparts. Second, it is difficult to plastically deform magnesium alloys at low temperatures due to the hexagonal close-packed (HCP) lattice and limited slip systems that characterize magnesium. Finally, due to the HCP crystal structure, Mg-alloys have poor formability (ductility), and subsequent processing creates crystallographic asymmetry (texture effects).
In regard to the strength, Mg-rare earth (RE) alloys, either binary or with additional alloying elements, are currently of significant interest because of high yield strength that can be achieved through precipitation hardening. In recent years, a wide range of RE elements (La, Ce, Nd, Gd, Y) are being explored to increase the strength of Mg-alloys. Their addition has been promising in increasing the strength through precipitation hardening-induced by phases such as Mg12RE, Mg3RE or Mg2RE phases [Citation6].
One significant strategy for boosting engineering material ductility without sacrificing strength is grain refinement. Ultrafine-grained alloys have exceptional cyclic stability during fatigue and a combination of high strength and homogeneous elongation [Citation7,Citation8]. These characteristics have sparked new attention and suggested fresh approaches to alloy processing. When compared to materials that have relatively fewer grain boundaries and interfaces, UFG materials exhibit significantly different structure and properties [Citation9]. This is because UFG materials have a high density of grain boundaries and interphase barriers.
There are some restrictions on both current severe plastic deformation methods and thermomechanical processing (TMP). One of the main techniques for obtaining grain refinement in metals is TMP, which involves strain-induced transformation or dynamic recrystallization. Recent TMP research conducted in the author’s lab [Citation10,Citation11] and at other institutions has shown that extreme plastic deformation processes that result in UFG structure can overcome the grain refinement restrictions imposed by traditional TMP [Citation12]. Equal channel angular pressing (ECAP) [Citation13], accumulative roll bonding (ARB)Citation14,Citation15], high pressure torsion (HPT) [Citation16–19,, repeated compression [Citation20], and upsetting extrusion [Citation21] are the primary SPD techniques. However, as these are laboratory-scale procedures, they cannot be used to produce alloys with uniform and texture-free structures. A bi-modal grain size distribution is typically attained. As a result, it is still difficult to process strong, ductile, texture-free UFG Mg-alloys. We overcame this difficulty by combining the multi-axial forging (MAF) process with the annealing of as-cast magnesium alloy.
The objective here is to provide a perspective and overview of the promise of texture-free Mg-rare earth alloys with high strength-high ductility combination processed by multiaxial forging (MAF). The current understanding in terms of process-structure-property relationships that govern the manufacturing of texture-free ultra-fine grained (UFG) strong and ductile magnesium alloys processed by multi-axial forging with the ability to sustain large plastic deformation, as recently obtained by the author’s group is presented [Citation1–3].
2. Key features and sketch of the multi-axial manufacturing route for Mg-alloys
We processed the as-cast Mg-RE alloy via a combination of annealing and multiaxial forging to obtain ultrafine-grained (UFG) structure with high strength-high ductility combination. In this regard, we considered a relatively dilute and model ternary alloy system, with minimum targeted strength of ~200 MPa and elongation exceeding ~20% in the multiaxial forged alloy. A schematic illustration of the multiaxial forging process is presented in [Citation1–3].
Figure 1. Schematic of multiaxial forging (MAF) process used to process Mg alloy [Citation1–3]. .
![Figure 1. Schematic of multiaxial forging (MAF) process used to process Mg alloy [Citation1–3]. .](/cms/asset/8c357fd9-2625-47e4-b1d3-ff58d3fee6f5/ymte_a_2189769_f0001_oc.jpg)
In designing the lean and model Mg-RE alloy, the following aspects were considered after a critical review of the phase diagrams of Mg-RE alloys and fundamental knowledge available in the literature. (a) Gadolinium (Gd) has high solubility of 23.49 wt% at eutectic temperature in Mg [Citation22] and significantly contributes to solid solution strengthening [Citation23]. (b) Alloying Mg with 2 wt% Gd exhibits maximum tensile strength as compared to any other rare earth element for similar percentage of alloying elements. Beyond 2 wt% Gd, there is no significant effect on strength and may reduce the strength because of solute segregation. (c) Gd and Zn together form FCC w-phase with Mg (Mg3Zn3Gd) that is suitable for grain refinement. Based on the aforementioned aspects, a lean model alloy system with nominal chemical composition in wt% of Mg-2Zn-2Gd was considered, ensuring the formation of precipitation strengthening w-phase and simultaneously obtaining solid solution strengthening. The combination of annealing and MAF processing route is generic in nature and can be successfully extended to other Mg-alloys based on Nb-, Mo- or Ce-alloy design, in lieu of Gd, and to other grades of non-RE Mg-alloys.
3. Preparation and processing of Mg-2Zn-2Gd alloy
The alloy was melted in a resistance furnace under a protective atmosphere of Ar + 2% SF6. Pure Mg, Zn, and Gd were used to prepare the designed alloy. First, Mg and Zn were melted in a boron nitride (BN)-coated mild steel crucible, and Gd was added to the liquid melt at ~770°C. This was followed by mechanical stirring to completely dissolve Gd and obtain uniform composition in the melt. Lastly, the liquid melt was poured into a preheated metallic round mould to obtain the as-cast alloy [Citation1–3].
Prior to multiaxial forging (MAF), the as-cast alloy was annealed at 500°C for 2 h to relieve the internal residual stresses. Multiaxial forging (MAF) of as-cast Mg-2Zn-2Gd alloy was carried out at a using a forging press of. Rectangular samples were subjected to MAF, as schematically illustrated in [Citation1–3]. The sample was placed in preheated die and MAF. During MAF, the dimensional ratio of the sample was maintained constant through the MAF process, while the loading direction was changed 90° from pass to pass [Citation1,Citation3].
The MAF device consisted of a punch for external loading and a die, and the punch moved vertically inside the chamber comprising of punch and die. The dimensional ratio of samples was maintained constant throughout the MAF processing, while the loading direction was changed 90° from pass to pass. The samples were MAF processed (two passes), and in each pass the true strain induced was 2.1, such that the total strain after the second pass was 4.2. We can produce different grain structures, from ultra-fine grained (UFG) to sub-micron (SMG) and fine-grained (FG) structure, by controlling the strain in each pass, a key parameter in the MAF process. As a result, we can adjust the structure to have appropriate mechanical properties.
After the first pass, the microstructure was heterogeneous, consisting of coarse deformed grains and fine dynamic recrystallized grains. Some grains were oriented parallel to their (0001) plane, implying the presence of some texture. However, after the second pass, a near homogeneous structure with recrystallized grains was present with randomization of texture (see below).
The multiaxial forging (MAF) was carried out in the temperature range of 350–500°C and working ratio of 0.3–0.4/condition. The preliminary data reported here is for the optimized MAF conditions (temperature of 450°C, working ratio of 0.3/direction) which provided a uniform structure.
4. Microstructure
As-cast and forged samples were mechanically polished using a series of SiC papers. Final polishing was carried out using 0.2 μm alumina. The samples were etched for ~2 minutes in a solution containing 8 g picric acid, 5 ml acetic acid, 10 ml distilled water, and 100 ml ethanol. The microstructure of polished samples was examined by X-ray diffraction (Bruker D8 model) and field emission scanning electron microscopy (Hitachi S4800). To analyse different phases, EVA software available with the XRD equipment was used. Transmission electron microscopy was carried out using 3 mm disks that were electropolished in a solution containing 3% perchloric acid in ethanol (A-C). summarizes the X-ray diffraction data of as-cast and as-cast + annealed + MAF alloy indicating the presence of α-Mg and w-phase (Mg3Zn3Gd).
Figure 2. X-ray diffraction data of as-cast, and as-cast + annealed + MAF alloy indicating the presence of α-Mg (matrix) and w-phase (Mg3Zn3Gd) [Citation1,Citation2].
![Figure 2. X-ray diffraction data of as-cast, and as-cast + annealed + MAF alloy indicating the presence of α-Mg (matrix) and w-phase (Mg3Zn3Gd) [Citation1,Citation2].](/cms/asset/fc74ce97-e4bd-4a1a-8ed3-46b6f97b0331/ymte_a_2189769_f0002_b.gif)
Figure 3. Microstructure of as-cast + annealed alloy referred as coarse-grained (CG) and as-cast + annealed + multiaxial forged referred as ultrafine-grained (UFG) Mg-2zn-2gd alloy. (c) Transmission electron micrograph illustrating size range of the Mg3Zn3Gd precipitates in α–Mg matrix, as confirmed by (d) electron diffraction pattern [Citation1,Citation2].
![Figure 3. Microstructure of as-cast + annealed alloy referred as coarse-grained (CG) and as-cast + annealed + multiaxial forged referred as ultrafine-grained (UFG) Mg-2zn-2gd alloy. (c) Transmission electron micrograph illustrating size range of the Mg3Zn3Gd precipitates in α–Mg matrix, as confirmed by (d) electron diffraction pattern [Citation1,Citation2].](/cms/asset/a4e369d0-1426-4435-b3eb-06b250986294/ymte_a_2189769_f0003_oc.jpg)
From the pole figures of CG (as-cast + annealed) Mg alloy () [Citation1], it may be seen that before MAF, in the CG alloy there was a strong texture on all easy slip planes with the maximal value of 52.59 (), implying strong anisotropy in the Mg alloy before MAF. In summary, before forging almost all the planes had maximal texture. However, after MAF, the majority of grains had no obvious texture on the slip planes including prismatic plane <a> , pyramidal plane <a>
, pyramidal plane <a+c>
, extension twin plane
and compression twin plane
. Even on basal plane <a>
, the maximal value of texture was only 8.29 (). This clearly implied that the MAF significantly suppressed texture. There was some texture at {0001}. The significant change in texture is attributed to the combined effect of MAF and Mg3Zn3Gd particle-simulated nucleation of new grains. Dynamic precipitation of Mg3Zn3Gd impacts nucleation of new grains and also hinders grain growth. It may also be noted that FCC precipitates inherited from the as-cast alloy have high deformability during MAF and fragmented during forging. It is also likely that besides dynamic recrystallization, grain fragmentation via kinking mechanism occurred during MAF [Citation1–3].
5. Mechanical properties of MAF Mg-alloy
shows stress-strain plots of as-cast and multiaxial-forged alloy. The as-cast alloy had a low yield strength of 53 MPa and significant precipitation was observed along the grain boundaries which may introduce stress concentration, resulting in early fracture [Citation3–5]. On annealing, the yield strength was decreased from 53 to 46 MPa because of grain growth. But, when the as-cast alloy was annealed and multiaxial forged, the yield strength was increased to 227 MPa, with tensile strength of 272 MPa, and high elongation of 30%. Direct multiaxial forging of as-cast alloy gave inferior properties, yield strength of 170 MPa, tensile strength of 220 MPa, and elongation of 16%. In summary, the MAF process involving forging along the three-dimensions and controlling strain/pass enabled texture-free and UFG structure with random orientation of grains to be obtained. The combination of UFG structure and mechanical properties was excellent for the ‘lean’ Mg-alloy after MAF []. Texture-free and homogenous structure is difficult to obtain in other severe plastic deformation processes described in Section 2.
Figure 5. Stress-strain plots ofas-cast and as-cast + annealed + MAF Mg-2zn-2gd alloy [Citation1,Citation2]. .
![Figure 5. Stress-strain plots ofas-cast and as-cast + annealed + MAF Mg-2zn-2gd alloy [Citation1,Citation2]. .](/cms/asset/a44af76a-91c5-4937-9edb-f29ca53f00ec/ymte_a_2189769_f0005_b.gif)
6. Nanoscale deformation experiments (UFG versus CG alloy)
The following justifications led to the execution of nanoscale deformation experiments. In UFG structures where indentation is contained within ‘a single grain’, nanoindentation can first provide insights into tiny deformation mechanisms [Citation24–26]. Second, the tested volume is scalable with respect to the microstructure, allowing us to examine the fundamental processes behind discrete deformation in a tiny amount of the material with a very low risk of encountering pre-existing dislocations prior to the start of plastic deformation. Third, single specimen geometry and loading configuration are used in nanoindentation. When paired with an applied force of the order of millinewtons (mN), a typical nanoindentation experiment’s contact area of nearly 100 nm2 results in an applied stress in the GPa range [Citation27–29].
The maximum load for the load-controlled mode of the nanoindentation tests was set at 25 mN, and the loading rate was 1 mN/s. The Berkovich three-sided pyramidal diamond indenter, with a nominal angle of 65.3° and an indenter tip diameter of 20 nm, constituted the nanoscale deformation experiment [Citation3].
Based on TEM studies, the following slip systems in multi-axial forged (MAF) UFG Mg-alloy were found. show, respectively, post-mortem TEM analyses of the plastic zone surrounding the depression for UFG and CG Mg-alloy [Citation1–3]. The TEM studies on the UFG alloy revealed substantial activity in around 60% of the grains and dislocation interaction. Complete Burgers vector analysis in more than 25 grains served as the foundation for the analysis. The UFG alloy indicated high density of dislocations characteristic of 1/3 < 113> pyramidal slip systems, that were observed in the two-beam condition of g = [0002], while 1/3 < 11
0> basal slip systems cannot be seen in this condition. The occurrence of <c+a> dislocation slip changes the active deformation mode on the pyramidal planes in the Mg alloy.
Figure 6. Representative bright field (a) and dark field transmission electron micrographs illustrating high density of dislocations in the plastic zone surrounding the indentation (top-right corner) in the ultrafine-grained (UFG: as-cast + annealed + multiaxial forged) Mg-2zn-2gd alloy. Zones 1 and 2 have high density of dislocations and zones 3A and 3B illustrate dislocations emitted by the grain boundary. (c) Selected area diffraction (SAED) pattern for grain in (a) and (b) showing [0002] operating reflection [Citation3].
![Figure 6. Representative bright field (a) and dark field transmission electron micrographs illustrating high density of dislocations in the plastic zone surrounding the indentation (top-right corner) in the ultrafine-grained (UFG: as-cast + annealed + multiaxial forged) Mg-2zn-2gd alloy. Zones 1 and 2 have high density of dislocations and zones 3A and 3B illustrate dislocations emitted by the grain boundary. (c) Selected area diffraction (SAED) pattern for grain in (a) and (b) showing [0002] operating reflection [Citation3].](/cms/asset/372daa80-00fb-4a5d-9450-1555a9f98a3a/ymte_a_2189769_f0006_b.gif)
Figure 7. (a,b) Transmission electron micrograph of plastic deformation zone surrounding the indentation showing the occurrence of twinning in the CG Mg-2zn-2gd alloy and the diffraction pattern. (b) Another illustration of twinning in the CG alloy. Diffraction pattern was similar to a (ii). From the diffraction pattern, the twin {11 ̅01} <01 ̅12> belongs to the family of {101 ̅1} <101 ̅2> compression twin. a(i) and a(ii) show original and enlarged (and indexed) SAED pattern for (a) [Citation3]. .
![Figure 7. (a,b) Transmission electron micrograph of plastic deformation zone surrounding the indentation showing the occurrence of twinning in the CG Mg-2zn-2gd alloy and the diffraction pattern. (b) Another illustration of twinning in the CG alloy. Diffraction pattern was similar to a (ii). From the diffraction pattern, the twin {11 ̅01} <01 ̅12> belongs to the family of {101 ̅1} <101 ̅2> compression twin. a(i) and a(ii) show original and enlarged (and indexed) SAED pattern for (a) [Citation3]. .](/cms/asset/ee2f5318-ed57-4575-8912-7a5687f95365/ymte_a_2189769_f0007_oc.jpg)
A typical illustration of the dislocation structure connected to nanoindentation is shown in [Citation3]. shows a dark grain with extremely strong dislocation activity, which is also visible in ’s dark-field image as a bright grain. It was analysed using the [0002] operating reflection in the SAED pattern of . In the bottom part of left grain in , dislocation profiles (zones 3A, 3B) are shown being emitted from the grain boundary, while the overall dislocation density in this grain is significantly lower than in the central (dark) grain in . Only two sources are activated by these profiles, which function as pile-ups against the opposing (lower) grain boundary and emit the dislocation profiles illustrated at 3A and 3B [Citation3].
highlights the frequency and type of dislocations discovered in the UFG alloy by post-mortem TEM investigation based on numerous TEM micrographs. Complete Burgers vector analysis of at least 25 randomly chosen grains from at least 5 separate samples, is the foundation of the analysis.
Table 2. Frequency of dislocations observed in the UFG Mg-alloy via post-mortem TEM analysis. The analysis is based on complete Burgers vector analysis in at least 25 random selected grains.
According to the g.b. criterion, where b is Burgers vector and g is diffraction vector, dislocations with different Burgers vectors are visible when g.b#0 and invisible when g.b = 0. TEM analysis revealed that <c+a> dislocations of different vectors were present (), namely, b = 1/3[113], b = 1/3[11
] and b = 1/3[
11
]. Additionally, the collinear dissociation of b = 1/3[11
3] dislocations according to 1/3[
3] → 1/6[
023]+1/6[
203] was observed. The observation of second order [
113] pyramidal slip and <c+a> dislocations suggest that screw <c+a> dislocations are stable, while edge <c+a> dislocations decompose <a> and <c> dislocations [Citation3,Citation30].
In contrast to the high dislocation activity in the UFG structure, {101} nanoscale twinning was an active deformation mechanism in the CG structure, however, the frequency of observation of twinning was ~15% considering all the grains. Typical twinning observations are shown in . They exhibited similar orientation with the matrix. From the SAED pattern ( a(i), (ii)), the type of the twin is {1
01}[0
12], which belongs to the family of {10
1}<10
2> compression twinning, consistent with the earlier studies on coarse-grained Mg alloys [Citation30, Citation31,Citation32]. The formation of twins early during the deformation process accommodates the applied strain [Citation3,Citation33].
The enhanced activity on non-basal planes in the UFG alloy is attributed to modified Peierls potential [Citation3,Citation34–39]. FE. Thus, the explanation of SFE varying with grain size is considered untenable.
As a result, under the same processing conditions, suggested a distinct distinction and fundamental transition in the deformation mechanism of CG and UFG alloy in a single material. The texture-free UFG Mg-RE alloy reduced twinning. Pyramidal non-basal <c+a> slip was activated in the UFG Mg alloy and twinned in the CG counterpart.
Load–displacement plots also showed the distinct plastic deformation of MAF UFG and CG Mg-alloys. [Citation3] shows representative force-displacement plots for the alloys UFG and CG. Three distinct displacement bursts (pop-ins) were observed in the case of the UFG alloy, with the first one occurring at a displacement of about 70 nm and an applied load of about 0.12 mN. In contrast, in the CG alloy, there were no displacement bursts and deviation from Hertzian solution occurred at ~60 nm. The loading data prior to the first pop-in is described by a power law relationship (P~h1.5), consistent with Hertzian elastic contact solution [Citation40,Citation41]. The broken-line in depicts the theoretical Hertzian elastic behaviour, which is consistent with the experimental plot. Moreover, it suggests that the region is elastic before the first discontinuity or pop-in and plastic thereafter.
Figure 8. Representative load-displacement plots for UFG and CG Mg-2zn-2gd alloy acquired via nanoindentation experiments in the load-controlled mode with a Berkovich indenter of radius 20 nm (maximum load of 0.5 mN and loading rate of 2 μN/s). (It may be noted that similar plots were observed in a large number of grains of each material, irrespective of their orientation of grains and hence they truly reflect the behaviour of the alloy) [Citation3].
![Figure 8. Representative load-displacement plots for UFG and CG Mg-2zn-2gd alloy acquired via nanoindentation experiments in the load-controlled mode with a Berkovich indenter of radius 20 nm (maximum load of 0.5 mN and loading rate of 2 μN/s). (It may be noted that similar plots were observed in a large number of grains of each material, irrespective of their orientation of grains and hence they truly reflect the behaviour of the alloy) [Citation3].](/cms/asset/e6e2fabd-f56a-4bdd-aa25-18d91d1d728d/ymte_a_2189769_f0008_b.gif)
We are looking at a small portion of the material that is thought to have a low chance of coming across a pre-existing dislocation (essentially defect-free) [Citation3], with the indenter tip’s diameter (20 nm) and the maximum displacement of about 200 nm (). Thus, the pop-ins represent burst or nucleation of dislocations in the UFG alloy and are expected to occur when the maximum shear stress (τmax) approaches the theoretical value, τtheo. In nanoindentation, stresses can reach the theoretical strength of the material [Citation41,Citation42], as determined by EquationEquations (1)(1)
(1) to (Equation3
(3)
(3) ):
where P is the applied load, E* is the effective indentation modulus, R is the radius of the Berkovich indenter tip, and h is the corresponding indentation depth. The effective indentation modulus is related to the Young’s modulus, E, and Poisson’s ratios, υ, of the sample and the indenter via [Citation41]:
The subscripts i and s refer to the indenter and sample, respectively.
Using the isotropic elastic constant for Mg-Gd alloy (Es = 52.5 GPa and υs = 0.28 [Citation43]) and Ei = 1141 GPa and υi = 0.07 for the diamond indenter tip [Citation41], a value of effective indentation modulus of E* = 54 GPa was obtained. Hertzian analysis of the data from the elastic portion of CG and UFG in gave similar E* = 32 GPa and E* = 41 GPa, respectively [Citation3].
The maximum shear stress at the first pop-in was determined using τmax = 0.31p0, where [Citation9],
based on Hertzian analysis. τmax was determined to be ~3.6 GPa for UFG and ~2.7 GPa for CG using EquationEquation (3)(3)
(3) . The measured τmax is ~1/7th of theoretical shear modulus of Mg-Gd alloy at ~21 GPa [Citation10] and is within the range for the theoretical strength of polycrystalline metals (~G/30 to ~G/5) [Citation3,Citation44].
6.1. Conclusions
To produce UFG Mg alloys with high strength-high ductility combination that are nearly texture-free, multiaxial forging of magnesium alloys is a practical manufacturing technique. The improvement in grain structure, which includes grain division and fragmentation as well as uniform distribution of nanoscale precipitates, is associated with the increase in strength. While the finding of a texture-free alloy is thought to be the result of MF and particle-stimulated grain nucleation working together over time. A new route for processing magnesium-based alloys for use in aerospace, automotive, and biomedical applications is made possible by using MAF to create UFG Mg alloys.
Acknowledgments
The author is grateful to the National Science Foundation for financial support through grant # CMMI 2130586.
Disclosure statement
No potential conflict of interest was reported by the author.
Additional information
Funding
References
- Misra RDK. “Strong and ductile texture-free ultrafine-grained magnesium alloy via three-axial forging,”. Mater Lett. 2023;331:133443.
- Trivedi P, Nune KC, Misra RDK, et al. “Grain refinement submicron regime in magnesium alloy and relationship to mechanical properties. Materials Science & Engineering A. 2016;668:59–10.
- Li K, Injeti VSY, Trivedi P, et al. “Nanoscale deformation of ultrafine-grained magnesium alloy with high strength-high ductility combination,”. J Mater Sci Technol. 2018;34(2):311–316.
- Qiu D, Zhang MX, Taylor JA, et al. A new approach to designing a grain refiner for Mg casting alloys and its use in Mg–Y-based alloys. Acta Materialia. 2009;57(10):3052–3059.
- Yamasakia M, Hashimoto K, Hagihara K, et al. Effect of multimodal microstructure evolution on mechanical properties of Mg–Zn–Y extruded alloy. Acta Materialia. 2011;59(9):3646–3658.
- Moreno IP, Nandy TK, Jones JW, et al. “Microstructural characterization of a die-cast magnesium-rare earth alloy,”. Scr Mater. 2001;45(12):1423–1429.
- Tsuji N, Saito Y, Utsunomiya H, et al. “Ultra-fine grained bulk steel produced by accumulative roll-bonding (ARB) process,”. Scr Mater. 1999;40(7):795–800.
- Maier HJ, Gabor P, Gupta N, et al. Cyclic stress–strain response of ultrafine grained copper. Int J Fatigue. 2006;28(3):243–250.
- Gleiter H. “Materials with ultrafine microstructures: retrospectives and perspectives,”. NanoStruct Mater. 1992;1(1):1–19.
- Misra RDK, Weatherly GC, Hartmann JE, et al. Ultrahigh strength hot rolled microalloyed steels-Microstructural aspects of development,”. Mater Sci Technol. 2001;17(9):1119–1129.
- Misra RDK, Thomson SW, Hylton TA, et al. “Microstructures of hot rolled high strength steels with significant differences in edge formability,”. Metall Mater Trans A. 2001;35A(13):745.
- Song R, Ponge D, Raabe D, et al. Microstructure and crystallographic texture of an ultrafine grained C–Mn steel and their evolution during warm deformation and annealing. Acta Materialia. 2005;53(3):845–858.
- Humphreys FJ, Prangnell PB, Bowen JR, et al. Developing stable fine–grain microstructures by large strain deformation. Philos Trans R Soc of London A. 1999;357(1756):1663–1681.
- Saito Y, Utsunomiya H, Tsuji N, et al. Novel ultra-high straining process for bulk materials—development of the accumulative roll-bonding (ARB) process. Acta Materialia. 1999;47(2):579–583.
- Costa ALM, Reis ACC, Kestens L, et al. “Ultra grain refinement and hardening of IF-steel during accumulative roll-bonding,”. Mat Sci Eng A. 2005;406(1–2):279–285.
- Zhilyaev AP, Nurislamova GV, Kim BK, et al. “Experimental parameters influencing grain refinement and microstructural evolution during high-pressure torsion,”. Acta Materialia. 2003;51(3):753–765.
- Ivanisenko Y, Lojkowski W, Valiev RZ, et al. “The mechanism of formation of nanostructure and dissolution of cementite in a pearlitic steel during high pressure torsion,”. Acta Materialia. 2003;51(18):5555–5570.
- Beladi H, Kelly GL, Shokouhi A, et al. “Effect of thermomechanical parameters on the critical strain for ultrafine ferrite formation through hot torsion testing,”. Mat Sci Eng A. 2004;367(1–2):152–161.
- Sauvage X, Wetscher F, Pareige P. Mechanical alloying of Cu and Fe induced by severe plastic deformation of a Cu–Fe composite. Acta Materialia. 2005;53(7):2127–2135.
- Belyakov A, Sakai T, Miura H, et al. “Substructures and internal stresses developed under warm severe deformation of austenitic stainless steel,”. Scr Mater. 2000;42:319–325.
- Lianxi H, Yuping L, Erde W, et al. “Ultrafine grained structure and mechanical properties of a LY12 Al alloy prepared by repetitive upsetting-extrusion,”. Mat Sci Eng A. 2006;422(1–2):327–332.
- Nayeb-Hashemi AA. Phase diagrams of binary magnesium alloys: Metals Park; 1998.
- Hort N, Huang Y, Fechner D, et al. Magnesium alloys as implant materials – Principles of property design for Mg–RE alloys☆. Acta Biomaterialia. 2010;6(5):1714–1725.
- Lu L, Schwaiger R, Shan ZW, et al. Nano-sized twins induce high rate sensitivity of flow stress in pure copper. Acta Materialia. 2005;53:2169–2179.
- Schwaiger R, Moser B, Dao M, et al. Some critical experiments on the strain-rate sensitivity of nanocrystalline nickel. Acta Materialia. 2003;51(17):5159–5172.
- Misra RDK, Challa VSA, Venkatsurya PKC, et al. “Interplay between grain structure, deformation mechanisms and austenite stability in phase-reversion-induced nanograined/ultrafine-grained austenitic ferrous alloy,”. Acta Materialia. 2015;84:339–348.
- Gouldstone A, Koh H-J, Zeng K-Y, et al. Discrete and continuous deformation during nanoindentation of thin films. Acta Materialia. 2000;44(9):2277–2295.
- Gerberich WW, Nelson JC, Lilleodden ET, et al. Indentation induced dislocation nucleation: the initial yield point. Acta Materialia. 1996;44(9):3585–3598.
- Krenn CR, Roundy D, Cohen ML, et al. Connecting atomistic and experimental estimates of ideal strength. Phys Rev B. 2002;65(13):134111–134114.
- Sandlöbes S, Friák M, Neugebauer J, et al. Basal and non-basal dislocation slip in Mg-Y, Mater. Sci Eng A. 2013;576:61–68.
- Dixit N, Xie KY, Hemker KJ, et al. Microstructural evolution of pure magnesium under high strain rate loading. Acta Materialia. 2015;87:56–67.
- Sandlöbes S, Zaefferer S, Schestakow I, et al. On the role of non-basal deformation mechanisms for the ductility of Mg and Mg–Y alloys. Acta Materialia. 2011;59(2):429–439.
- Somekawa H, Schuh CA. Nanoindentation behavior and deformed microstructures in coarse-grained magnesium alloys,”. Scripta Materialia. 2013;68(6):416–419.
- Ando S, Tanaka M, Tonda H. Pyramidal slip in magnesium alloy single crystals. Mater Sci Forum. 2003;419-422:87–92.
- Ando S, Tondo H. “Non-basal slip in magnesium and magnesium-lithium alloys single crystals,”. Mater Sci Forum. 2000;350-351:350–351.
- Yan H, Chen R, Zheng N, et al. Effects of trace Gd concentration on texture and mechanical properties of hot-rolled Mg–2Zn–xGd sheets. J Magnes Alloy. 2013;1(1):23–30.
- Wang WY, Shang SL, Wang Y. “Effects of alloying elements on stacking fault energies and electronic structures of binary Mg Alloys: a first-principles study,”. Mater Res Lett. 2014;2(1):29–36.
- Sandlöbes S, Friák M, Zaefferer S. The relation between ductility and stacking fault energies in Mg and Mg–Y alloys. Acta Materialia. 2012;60(6–7):3011–3021.
- Dun JH, Choi CS. Variation of stacking fault energy with austenite grain size and its effect on the MS temperature of γ→ε martensitic transformation in Fe–Mn alloy. Materials Science & Engineering A. 1998;257(2):353–356.
- Johnson KL. Contact Mechanics: Cambridge University; 1985.
- Shim S, Bei H, George EP, et al. “A different type of indentation size effect,”. Scr Mater. 2008;59(10):1095–1098.
- Ahn T-H, Oh C-S, Kim DH, et al. “Investigation of strain-induced martensitic transformation in metastable austenite using nanoindentation,”. Scr Mater. 2010;63(5):540–543.
- Chen P, Li DL, Yi JX, et al. “Structural, elastic and electronic properties of β’ phase precipitate in Mg-Gd alloy system investigated via first-principles calculation,” Solid State Science. ; 200911 (2009):2156–2162.
- Honeycombe RW. Plastic deformation of metals. 2nd (UK: Hodder Arnold) ed; 1984.