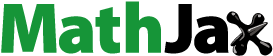
ABSTRACT
Here, we address the continuing challenges and scientific gaps in obtaining high strength and high elongation in medium-Mn steels. Electron microscopy and X-ray diffraction studies clearly underscored that the discontinuous transformation-induced plasticity played a determining role in impacting high strength–toughness combination in conjunction with the microstructural constituents. The discontinuous TRIP effect during deformation involved stress relaxation, which was responsible for high ductility. An excellent combination of a high tensile strength in the range of 1238–1502 MPa and a total elongation of 25–33.6% was obtained when the steels were subjected to an intercritical hardening in the temperature range of 600–750°C and low tempering at 200°C. The intercritical hardening influenced the co-existence of austenite, ferrite and martensite in a manner such that the deformation behaviour varies with the Mn-content.
Introduction
Transformation-induced plasticity (TRIP) steels have good crashworthiness, superior ductility, and high strength. Steel is a potential candidate for automotive applications. The enhanced work hardening rate and energy absorption behaviour are attributed to the TRIP effect, which is the transformation of retained austenite to martensite [Citation1,Citation2]. The conventional low-alloyed TRIP steels with Mn content of less than ~2.5% and a product of ultimate tensile strength and total elongation (PSE) of ~15 ± 10 GPa% consist of ferrite, retained austenite, a small amount of martensite, and occasionally bainite [Citation3–6]. The high-manganese twinning-induced plasticity (TWIP) steels with PSE of ~60 ± 10 GPa% are generally completely austenite [Citation7,Citation8].
Recently, a number of studies on research on strength and plasticity of advanced high strength steel have been conducted [Citation9–16]. The medium-Mn steels with PSE ≥ 30 GPa% are considered promising automobile steels. The composition of austenite greatly influences the austenite stability. It has been suggested [Citation12,Citation13] that austenite stability can be increased by the distribution of manganese between the austenite and ferrite during annealing in the intercritical region with sufficient holding time for the microstructure to reach phase equilibrium. Miller [Citation14] reported that the austenite fraction in 6.0% Mn steels could be as high as 30%. More recently, the retained austenite fractions of ~16.8% in 5.2Mn-0.10C steel, ~27.8% in 5.8Mn–0.10C steel, and ~38% in 7.1Mn-0.10C steel were obtained by Merwin [Citation11]. Therefore, mechanical properties, especially PSE, were significantly improved with the increasing Mn content, which led to the increasing volume fraction of retained austenite. The volume fraction of retained austenite was significantly increased with increasing Mn content, which increases with PSE.
In conventional TRIP steel, a two-stage heat treatment process is adopted to stabilize austenite during austempering [Citation17]. Regarding medium-Mn steels, the steel is first heated in the austenitic region and then quenched to obtain a complete martensite microstructure. Subsequently, annealing followed by air cooling stabilizes a high retained austenite fraction. The quenching and partitioning (Q&P) process basically consists of complete austenization followed by rapid cooling to the region between Ms and Mf. Annealing at the quenching temperature or above is subsequently conducted to facilitate the partitioning of carbon from martensite to austenite [Citation18–20]. The process of obtaining austenite from the initial martensite is referred to as ‘austenite reverted transformation’ (ART) [Citation10,Citation14,Citation18–22]. The heat treatments discussed above require cold rolling and a long annealing time (6–12 h). A long annealing time renders the austenite very stable and leads to the TRIP effect being significantly weakened.
Herein, for medium-manganese steel, two different traditional heat treatments (Q&P and ART processes) are described. The shortcomings of the two traditional heat treatments are summarized. Our purpose is to explain the necessity for putting forward a new heat treatment. Thus, a novel heat treatment is proposed for the experimental medium-Mn steels to obtain high strength/high elongation, constituting the objective of the study. The stress–strain plot is characterized by serrations in medium-Mn TRIP steels. The objective of the present study is to ascribe this phenomenon to the unique discontinuous TRIP effect played a positive role in excellent mechanical properties.
Materials and experimental procedure
E. De Moor et al. [Citation23] proposed a model that is used to design the composition of steels and predict the heat treatment temperature. The model suggests that the amount of austenite stabilized at room temperature depends on the content of carbon, aluminium, and manganese elements enriched in austenite [Citation15,Citation16,Citation19]. It further suggests that a temperature exists in the region that yields the maximum fraction of retained austenite at room temperature. In Thermo-Calc software, we input the composition of steel and set the temperature range. The prediction of the phase volume fraction of the experimental steels and composition of austenite can then be calculated.
The cast ingots were refined by Central Iron and Steel Research Institute in Beijing using a vacuum melting furnace. The real composition of the experimental steels was measured by atomic absorption spectrophotometry (SP-3803, Spectrum, Shanghai, China) and is given in . Then, the ingots were heated at 1250°C for 3 h and hot forged between 1200°C and 900°C into billets of section size 100 mm × 30 mm. Subsequently, the billets were cooled in air to room temperature (RT). Finally, the billets were heated at 1200°C for 2 h and hot rolled to sheets with 4 mm thickness after 7 passes of hot rolling (as shown in ); the primary rolling temperature was 1150°C, the final rolling temperature was not lower than 850°C, and the hot-rolled steel was finally cooled to room temperature in air.
Figure 1. Schematic diagram of hot-rolling and heat treatment schedule for steels using an effective and simple two-stage heat treatment process.

Table 1. Chemical composition (wt.%) of the two steels.
The traditional heat treatment for medium-Mn steels mentioned above requires a long holding time in the region, and it has been proved to be inapplicable to the experimental steels [Citation18–22]. The long annealing time also renders the retained austenite too stable. As a result, the TRIP effect is weakened. Thus, an effective and simple two-stage heat treatment process was adopted (as shown in ): (1) Intercritical hardening-the as-hot-rolled steels were heated in the inter-critical temperature region 550–800°C for 1 h and then immediately quenched in water to room temperature. (2) Tempering-the quenched steels were tempered at 200°C for 15 min, followed by air cooling to room temperature to obtain a good balance between ductility and strength. In the processes of annealing and tempering, carbon diffuses from ferrite to austenite, which enhances the stability of austenite, leading to superior ductility [Citation6].
Tensile specimens of a gauge width 12.5 mm and length 50 mm were taken parallel to the rolling direction and were machined from a heat-treated plate. A universal testing machine (SANSCMT5000, MTS, Saint Paul, MN, U.S.A.) was used at a constant crosshead speed of 3 mm·min−1 for tensile testing at room temperature. The microstructure was studied using an optical microscope (OM, OLYMPUS, OLYMPUS-GSX500, Tokyo, Japan), a field-emission scanning electron microscope (FE-SEM, SSX-550, Supra, Shimadzu, Tokyo, Japan), and a field-emission transmission electron microscope (FE-TEM, TECNAI G2–20, FEI, operated at 200 kV, Hillsboro, MO, U.S.A.). The OM and SEM samples were etched in an aqueous solution of 75% H2O +25% NaHSO3. The TEM samples were twin-jet polished (Struers, Tenupol-5, Copenhagen, Denmark) in a solution of 95% alcohol and 5% perchloric acid at ~20°C. Using a direct comparison method [Citation24], the austenite volume fraction was determined by X-ray diffraction (XRD, D/Max2250/PC, Rigaku, Tokyo, Japan) with CuKα radiation. The volume fraction of austenite was measured using the integrated intensities of the (311)γ and (220)γ peaks of austenite and the (211)α and (200)α peaks of ferrite. The austenite volume fraction, VA, is calculated using EquationEquation (1)(1)
(1) [Citation25]:
where Iγ and Iα are the integrated intensity values of the austenite and α-phase, respectively; N and M are the numbers of peaks of austenite and peaks of ferrite, respectively; and Rγ and Rα are the standardization constants of austenite and ferrite, respectively, such that Rγ, (311) = 2.282 m−1, Rγ, (220) = 1.796 m−1, Rα, (211) = 2.932 m−1, and Rα, (200) = 1.269 m−1.
Results and discussion
Design of the chemical composition of steels
The fraction of retained austenite as a function of the annealing temperature was predicted using the model proposed by De Moor et al. [Citation23]. The phase fraction at each temperature in the equilibrium state is calculated using Thermo-Calc.
According to the calculated content of each element in the austenite, the Ms point of the experimental steel can be calculated using EquationEquation (2)(2)
(2) [Citation26]:
According to the Koistinen – Marburger (K – M) equation, the amount of transformation from austenite to martensite during the cooling process is calculated using EquationEquation (3)(3)
(3) :
where T is the room temperature, which is taken as 20°C.
Based on the initial austenite fraction and the newly formed martensite during the cooling process calculated by EquationEquations (2)(2)
(2) and (Equation3
(3)
(3) ), the fraction of retained austenite at room temperature can be obtained. For 1.5Al steel, a pronounced peak (~77.1 vol.%) was observed at ~650°C, and for 3Al steel, the maximum fraction of retained austenite reached ~55.1 vol.% at about 750°C.
Microstructure evolution and mechanical properties
The microstructural constituents of the as-hot-rolled steels consisted of martensite and small amounts of austenite. During treatment, austenite reversion from martensite occurred. The distribution of carbon content in austenite is not uniform when austenite is heated. Carbon-depleted areas in austenite occur via diffusion. The ferrite is then nucleated in carbon-depleted austenite. Supersaturated carbon in ferrite diffuses to austenite to obtain carbon-rich retained austenite.
SEM micrographs of the 1.5Al and 3Al hardened and tempered steels are shown in . The microstructures of the 1.5Al and 3Al steels comprised of inter-critical ferrite (α-ferrite), δ-ferrite, retained austenite, and martensite, and the morphology and content of each phase varied significantly with change in the intec-ritical hardening temperature. It can be seen that various kinds of austenite exhibit in the annealed matrix, namely, blocky, granular and lathy austenite. The number of stripe-like ferrites decreased with increasing temperature, while the thin-lath martensite gradually thickened with increasing temperature. Similar morphological changes were observed for martensite. The thin-lath martensite was dispersed into packets (marked rectangle in ) in the parent austenite matrix, which was broadly divided into granular and thin layers in the temperature range of 700–750°C for 1.5Al steel and at 800°C for 3Al steel, respectively. The content of retained austenite in 1.5Al steel was higher than that in 3Al steel, while the ferrite content in 1.5Al steel was less than that in 3Al steel.
Figure 2. SEM micrographs of hot-rolled 1.5Al steels after quenching from different temperatures. (a) 1.5Al-600°C, (b) 1.5Al-650°C, (c) 1.5Al-700°C, (d) 1.5Al-750°C.

Figure 3. SEM micrographs of hot-rolled 3Al steels after quenching from different temperatures. (a) 3Al-650°C, (b) 3Al-700°C, (c) 3Al-750°C, (d) 3Al-800°C.

According to the Fe-C phase diagram, with increasing annealing temperature, the amount of ferrite decreased, the amount of austenite increased, and the austenite grains grew. With increasing austenite grain size, the stability of austenite decreases. During quenching, more austenite was transformed into martensite. Thus, with increasing annealing temperature, the amount of martensite increased after quenching. Austenite in the two steels comprised a high fraction in the temperature ranges of 550–650°C for 1.5Al steel and 600–750°C for 3Al steel, but when they were treated at 700°C and 800°C, respectively, the amount of austenite decreased markedly because of extensive martensitic transformation.
shows the XRD pattern and measured fraction of austenite in heat-treated 1.5Al and 3Al steels at room temperature. For the 1.5Al steel, the retained austenite volume fraction increased to 80 vol.% at 650°C, followed by a significant decrease to 34% at 700°C. A similar variation in austenite content as a function of temperature occurred for the 3Al steel. It attained a peak of 58 vol.% at 750°C. It is obvious that 1.5Al steel had higher austenite content than that in 3Al steel.
Figure 4. XRD patterns and measured austenite fractions of 1.5Al and 3Al steels heat treated at different temperatures. (a) XRD patterns for 1.5Al steels, (b) XRD patterns for 3Al steels, (c) measured austenite fractions.

depicts a schematic representation of austenite, ferrite and martensite volume fractions in 1.5Al steel and 3Al steel intercritically hardened at different temperatures. The volume fraction of austenite was measured by XRD. The approximate fraction of ferrite and martensite showing the trend in the change in the volume fraction of ferrite and martensite is shown in .
Figure 5. Schematic diagram of the volume fraction of ferrite, austenite and martensite in (a) 1.5Al steels and (b) 3Al steels heat-treated at different temperatures.

With increasing annealing temperature, the austenite volume fraction increased and the volume fraction of ferrite decreased. Thus, the austenite volume fraction increased with increasing temperature when 1.5Al steel and 3Al steel were intercritically annealed at 550–650°C and 600–750°C, respectively. Compared with the 3Al steel, the 1.5Al steel had a larger austenite content. With increasing temperature, the grain size of the austenite increased gradually, which resulted in a decrease in the austenite stability [Citation27,Citation28]. The higher the annealing temperature, the more austenite transformed to martensite during quenching when 1.5Al steel was intercritically annealed in the temperature range of 700–750°C. Because of the martensitic transformation, the volume fraction of austenite decreased for 3Al steel intercritically annealed at 800°C.
The mechanical properties are presented in . At least five samples for each temperature were examined in the experiment. The standard deviation is also presented in the results in . As shown in , the yield strength of 1.5Al steel and 3Al steel increased with increase in temperature after attaining minimum value of 645 MPa on quenching from 650°C (1.5Al-650 steel) and 652 MPa on quenching from 750°C (3Al-750 steel), respectively. The grain size of austenite for 1.5Al steel and 3Al steel increased with increase in temperature upon quenching from temperatures below 650°C and 750°C, respectively. The yield strength and austenite grain size followed Hall–Petch relationship. However, the yield strength for 1.5Al steel and 3Al steel increased after quenching from 700°C to 800°C, respectively, was because of the high fraction of martensite.
Figure 6. Tensile properties of 1.5Al steel and 3Al steel. (a) yield strength comparisons between 1.5Al steel and 3Al steel, (b) ultimate tensile strength and total elongation of 1.5Al steel, (c) ultimate tensile strength and total elongation of 3Al steel, (d) product of ultimate tensile strength and total elongation comparisons between 1.5Al steel and 3Al steel (UTS-ultimate tensile strength, TEL-total elongation).

show that the ultimate tensile strength (UTS) increased continuously with increasing temperature, whereas the total elongation (TEL) almost decreased with increasing temperature after attaining peak values of 33.6% for 1.5Al-650 steel and 36.7% for 3Al-750 steel. From the plots of TEL, UTS and product of UTS and TEL in , it can be seen that the product of UTS and TEL of the 1.5Al steel were obviously superior to those of the 3Al steel, which mainly resulted from a greater austenite amount in the 1.5Al steel, as apparent from . As shown in , the 1.5Al-650 steel exhibited a TEL of 33.6%, UTS of 1387 MPa and PSE of 46.60 GPa%, while 3Al-750 steel was characterized by a TEL of 36.7%, UTS of 1116 MPa and PSE of 40.96 GPa%. In contrast, as shown in [Citation9,Citation11,Citation13,Citation29], other medium-Mn TRIP steels had lower or similar ductility with similar strength but required additional cold rolling work and a prolonged annealing time. Therefore, 1.5Al and 3Al steel heat treated at 650°C and 750°C, respectively, and tempered at 200°C are significantly important. In particular, the two samples had a superior product of ultimate tensile strength and total elongation.
Table 2. Comparisons of medium Mn TRIP steel.
Deformation behaviour
A comparison of the XRD patterns of undeformed 1.5Al-650 and 3Al-750 steels with fractured samples is shown in . The results showed that the amount of austenite decreased to a small amount after tensile failure. The retained austenite volume fractions measured by XRD analysis of the 1.5Al-650 and 3Al-750 fractured samples were ~13.2 and ~9.7 vol.%, respectively, and the original austenite volume fractions of the 1.5Al-650 and 3Al-750 steels were 80.0 and 58.3 vol.%, respectively. Thus, it is indicated that a significant TRIP effect occurred during tensile deformation.
Figure 7. XRD patterns of the fractured and undeformed steels. (a) 1.5Al-650 steel, (b) 3Al-750 steel.

shows stress–strain curves superimposed with the change in volume fraction of retained austenite as a function of tensile strain in the 1.5Al-650 sample. It is fascinating that the austenite essentially remained intact during the yielding stage, indicating that much of the strain-transformation occurred within the localized deformation zone until the occurrence of the work hardening stage. This is an exceptional evidence given that the martensitic transformation during deformation is strain-induced because the stress alone has little influence on austenite in the region ahead of the work hardening stage. It is also indicated that the TRIP effect can significantly improve strain hardening ability.
Figure 8. Engineering stress–strain curve and change in the volume fraction of austenite during deformation in 1.5Al-650 steel.

The true stress–strain plots of 1.5Al and 3Al hardened and tempered steels are presented in . Interestingly, an obvious difference is the observed serrations in the plots of 1.5Al-650 steel and 3Al-750 steel. The true stress–strain plot, work hardening rate and comparison between work hardening rate and true stress–strain plots of 1.5Al-650 sample are presented in . According to previous studies [Citation10,Citation30], the work hardening rate evolution presents three domains in steels containing 5–7% Mn content: (1) a rapid decrease in the work hardening rate (WH), (2) an increase in the WH, and (3) a final smooth decrease in the WH. Shi et al. [Citation10] suggested that the three-stage WH exists only when the volume fraction of retained austenite is greater than ~15%. A majority of studies [Citation10,Citation30–36] have concluded that the first stage is mainly associated with ferrite deformation, the second intermediate stage is related to the occurrence of the TRIP effect, and the third stage may be related to straining of martensite and ferrite because martensite-phase transition in this stage is inactive. In the second stage (stage 2, as shown in ), the work hardening rate and the true stress–strain plot have significant regularity. As shown in , in the first stage (a1-a3) of stage 2, the increase in work hardening rate is ascribed to the TRIP effect. In the rising stage, when a certain critical stress is attained, martensitic transformation is activated, and retained austenite with similar stability continuously transforms to martensite. The abrupt drop in stress (a1-a2) is ascribed to the onset of the TRIP effect, which relaxes and transfers the local stress to the surrounding ferrite and austenite. On the other hand, the gradual increase in stress (a2-a3) is a consequence of competition between the increase in tensile stress and stress relaxation and transfer induced by the TRIP effect. The second stage (a3-b1) concerns accumulation of stress. The work hardening rate decreases and rebounds when the stress is sufficiently large (point b1), initiating a second round of the TRIP effect (stage b1-b3). The TRIP effect that occurs discontinuously in the 1.5Al-650 sample during tensile. In conclusion, the serrated behaviour in the true stress–strain plot can be attributed to the discontinuous TRIP effect involving stress relaxation and transfer during deformation with a consequent enhancement in ductility.
Figure 9. True strain-stress plots of 1.5Al steels and 3Al steels quenched from different temperatures. (a)1.5Al steels, (b) 3Al steels.

Figure 10. True stress–strain curve and work-hardening rate plot of 1.5Al-650 sample. (a) true stress–strain curve, (b) work-hardening rate, (c) partial magnification of the true stress–strain and work-hardening rate plots.

It is known that C and Mn which are strong austenite stabilizers have strong influence on austenite stability [Citation37–39]. shows the SEM and TEM micrographs of the 1.5Al-650 sample and the corresponding carbon concentration and manganese partitioned into blocky austenite and lath-like austenite by EPMA and TEM-EDS. We compare the region marked with a rectangle with the region marked with an oval circle in . It is clear that the carbon content in lath-like austenite was higher than the blocky austenite. show TEM micrograph and the corresponding concentration of Mn in blocky and lath-like austenite. It is clear that the higher Mn and C content present in lath-like austenite can explain higher austenite stability. The different morphology of austenite results in different degree of stability of austenite and leads to discontinuous TRIP effect. It can be seen from the results in that the discontinuous TRIP effect only occurs when the 1.5Al steel and 3Al steel are quenched from 650°C to 750°C, respectively, corresponding to the optimal mechanical properties among all the samples quenched from different temperatures. Thus, the discontinuous TRIP effect in the 1.5Al-650 and 3Al-750 steels contributed to its superior mechanical properties.
Figure 11. SEM and TEM micrograph of 1.5Al-650 sample and the corresponding carbon concentration and manganese partitioned in blocky austenite and lath-like austenite by EPMA and TEM-EDS. (a) Micrograph of 1.5Al-650 sample, (b) distribution of carbon correspond to the micrograph in figure (a) by EPMA, (c) TEM micrograph of 1.5Al-650 sample, (d) manganese-concentration correspond to the micrograph in figure (c) by TEM-EDS.

Conclusions
With the change in the temperature, the maximum volume fraction of retained austenite at room temperature can be obtained based on the model proposed by De Moor [Citation23]. For 1.5Al steel, a pronounced peak (~77.1 vol.%) was observed at ~650°C, and for 3Al steel, the maximum fraction of retained austenite reached ~55.1 vol.% at about 750°C.
Optimal mechanical properties were obtained in 1.5Al and 8Al steels when they were subjected to inter-critical hardening at 650°C and 750°C, respectively, and identical tempering at 200°C. The 1.5Al-650 steel was characterized by an excellent combination of a TEL of 33.6%, UTS of 1387 MPa and UTS × TEL of 46.6 GPa%. The mechanical properties of the two experimental steels were superior to those of other medium-Mn TRIP steels, with the advantage of reduced cold rolling work and a shorter annealing time.
The stability of lath-like austenite was higher than that in blocky austenite, which was mainly ascribed to the non-uniform Mn-distribution and C-content in lath-like austenite and blocky austenite. The discontinuous TRIP effect, which is primarily ascribed to the different grades of austenite stability, played a positive role as the superior product of ultimate tensile strength and total elongation of the 1.5Al-650 and 3Al-750 steel.
Acknowledgments
This research was funded by the National Natural Science Foundation of China, grant number 52005304, Science and Technology Plan for Youth Innovation Team in Colleges and Universities of Shandong Province (2022KJ219), the National Natural Science Foundation of China (52175342), the Natural Science Foundation of Shandong (ZR2021ME129). I sincerely thank my former advisor at the University of Texas at El Paso for the review of the study presented here.
Disclosure statement
No potential conflict of interest was reported by the authors.
Data availability statement
The raw/processed data required to reproduce these findings cannot be shared at this time as the data also form part of an ongoing study.
Additional information
Funding
References
- Mertinger V, Nagy E, Tranta F, et al. Strain-induced martensitic transformation in textured austenitic stainless steels. Mater Sci Eng A. 2008;481-482:718–11.
- Oliver S, Jones T, Fourlaris G. Dual phase versus TRIP strip steels: comparison of dynamic properties for automotive crash performance. Mater Sci Technol. 2007;23(4):423–431.
- Sugimoto K, Iida T, Sakaguchi J, et al. Retained austenite characteristics and tensile properties in a TRIP type bainitic sheet steel. ISIJ Int. 2000;40(9):902–908. DOI:10.2355/isijinternational.40.902
- De Cooman B. Structure-properties relationship in TRIP steels containing carbide-free bainite. Opin Solid St M. 2004;8(3–4):285–303.
- Li H, Jiang R, He L, et al. Influence of deformation degree and cooling rate on microstructure and phase transformation temperature of B1500HS steel. Acta Metall. Sin. 2018;31(1):33–47. doi:10.1007/s40195-017-0594-3.
- Kamoutsi H, Gioti E, Haidemenopoulos G, et al. Kinetics of solute partitioning during intercritical annealing of a medium-Mn steel. Metall Mater Trans A. 2015;46(11):4841–4846. DOI:10.1007/s11661-015-3118-7
- Grässel O, Krüger L, Frommeyer G, et al. High strength Fe-Mn-(Al, Si) TRIP/TWIP steels development-properties-application. Int J Plast. 2000;16(10–11):1391–1409. DOI:10.1016/S0749-6419(00)00015-2
- Yoo J, Park K. Microband-induced plasticity in a high Mn-Al-C light steel. Mater Sci Eng A. 2008;496(1–2):417–424.
- Ning H, Li X, Meng L, et al. Effect of Ni and Mo on microstructure and mechanical properties of grey cast iron. Mater Technol Adv Perform Mater. 2023;38(1):2172991. DOI:10.1080/10667857.2023.2172991
- Guo L, Su X, Dai L, et al. Strain ageing embrittlement behaviour of X80 self-shielded flux-cored girth weld metal. Mater Technol Adv Perform Mater. 2023;38(1):2164978. DOI:10.1080/10667857.2023.2164978
- Yang C, Xu H, Wang Y, et al. Hot Tearing analysis and process optimisation of the fire face of Al-Cu alloy cylinder head based on MAGMA numerical simulation. Mater Technol Adv Perform Mater. 2023;38(1):2165245. DOI:10.1080/10667857.2023.2165245
- Li Q, Zuo H, Feng J, et al. Strain rate and temperature sensitivity on the flow behaviour of a duplex stainless steel during hot deformation. Mater Technol Adv Perform Mater. 2023;38(1):2166216. DOI:10.1080/10667857.2023.2166216
- Misra RDK. Strong and ductile texture-free ultrafine-grained magnesium alloy via three-axial forging. Mater Lett. 2023;331:133443.
- Misra RDK. Enabling manufacturing of multi-axial forging-induced ultrafine- grained strong and ductile magnesium alloys: a perspective of process-structure- property paradigm. Mater Technol Adv Perform Mater. 2023;38(1):2189769.
- Wang L, Li J, Liu Z, et al. Towards strength-ductility synergy in nanosheets strengthened titanium matrix composites through laser power bed fusion of MXene/Ti composite powder. Mater Technol Adv Perform Mater. 2023;38(1):2181680. DOI:10.1080/10667857.2023.2181680
- Niu G, Zurob H, Misra RDK. Superior fracture toughness in a high-strength austenitic steel with heterogeneous lamellar microstructure. Acta Mater. 2022;226:117642.
- Misra RDK, Challa VSA, Injeti VSY. Phase reversion-induced nanostructured austenitic alloys: an overview. Mater Technol Adv Perform Mater. 2022;37(7):437–449.
- Li Z, Misra R, Ding H, et al. The significant impact of pre-strain on the structure-mechanical properties relationship in cold-rolled medium manganese TRIP steel. Mater Sci Eng A. 2018;712:206–213.
- Li Z, Zhang X, Mou Y, et al. The impact of intercritical annealing in conjunction with warm deformation process on microstructure, mechanical properties and TRIP effect in medium-Mn TRIP steels. Mater Sci Eng A. 2019;746:363–371.
- Wu Z, Tang Y, Chen W, et al. Exploring the influence of Al content on the hot deformation behavior of Fe-Mn-Al-C steels through 3D processing map. Vacuum. 2019;159:447–455.
- Liang Z, Li Y, Huang M. The respective hardening contributions of dislocations and twins to the flow stress of a twinning-induced plasticity steel. Scr Mater. 2016;112:28–31.
- Han J, Nam J, Lee Y. The mechanism of hydrogen embrittlement in intercritically annealed medium Mn TRIP steel. Acta Mater. 2016;113:1–10.
- De Moor E, Matlock D, Speer J, et al. Austenite stabilization through manganese enrichment. Scr Mater. 2011;64(2):185–188. DOI:10.1016/j.scriptamat.2010.09.040
- Srivastava A, Bhattacharjee D, Jha G, et al. Microstructural and mechanical characterization of C-Mn-Al-Si cold-rolled TRIP-aided steel. Mater Sci Eng A. 2007;445:549–557.
- Van Dijk N, Butt A, Zhao L, et al. Thermal stability of retained austenite in TRIP steels studied by synchrotron X-ray diffraction during cooling. Acta Mater. 2005;53(20):5439–5447. DOI:10.1016/j.actamat.2005.08.017
- Speer J, Streicher A, Matlock D, et al. Quenching and partitioning: a fundamentally new process to create high strength trip sheet microstructures. Symposium on the Thermodynamics, Kinetics, Characterization and Modeling of: Austenite Formation and Decomposition. 2003;505–522.
- Challa V, Wan X, Somani M, et al. Significance of interplay between austenite stability and deformation mechanisms in governing three-stage work hardening behavior of phase-reversion induced nanograined/ultrafine-grained (NG/UFG) stainless steels with high strength-high ductility combination. Scr Mater. 2014;86:60–63.
- Misra R, Challa V, Venkatsurya P, et al. Interplay between grain structure, deformation mechanisms and austenite stability in phase-reversion-induced nanograined/ultrafine-grained austenitic ferrous alloy. Acta Mater. 2015;84:339–348.
- Zhao J, Yan X, Wen S, et al. Microstructure and mechanical properties of high manganese TRIP steel. J Iron Steel Res Int. 2012;19(4):57–62. DOI:10.1016/S1006-706X(12)60088-0
- Arlazarov A, Gouné M, Bouaziz O, et al. Evolution of microstructure and mechanical properties of medium Mn steels during double annealing. Mater Sci Eng A. 2012;542:31–39.
- Dan W, Li S, Zhang W, et al. The effect of strain-induced martensitic transformation on mechanical properties of TRIP steel. Mater Des. 2008;29(3):604–612. DOI:10.1016/j.matdes.2007.02.019
- Jha B, Avtar R, Dwivedi V, et al. Applicability of modified Crussard-Jaoul analysis on the deformation behaviour of dual-phase steels. J Mater Sci Lett. 1987;6(8):891–893. DOI:10.1007/BF01729860
- Cai Z, Ding H, Xue X, et al. Microstructural evolution and mechanical properties of hot-rolled 11% manganese TRIP steel. Mater Sci Eng A. 2013;560:388–395.
- Cai Z, Ding H, Kamoutsi H, et al. Interplay between deformation behavior and mechanical properties of intercritically annealed and tempered medium-manganese transformation-induced plasticity steel. Mater Sci Eng A. 2016;654:359–367.
- Cai Z, Ding H, Xue X, et al. Significance of control of austenite stability and three-stage work-hardening behavior of an ultrahigh strength-high ductility combination transformation-induced plasticity steel. Scr Mater. 2013;68(11):865–868. DOI:10.1016/j.scriptamat.2013.02.010
- Cai M, Li Z, Chao Q, et al. A novel Mo and Nb microalloyed medium Mn TRIP steel with maximal ultimate strength and moderate ductility. Metall Mater Trans A. 2014;45(12):5624–5634. DOI:10.1007/s11661-014-2504-x
- Cai Z, Ding H, Misra R, et al. Austenite stability and deformation behavior in a cold-rolled transformation-induced plasticity steel with medium manganese content. Acta Mater. 2015;84:229–236.
- Bhadeshia H, Edmonds D. Bainite in silicon steels: new composition-property approach Part 1. Metal Sci. 1983;17(9):411–419.
- Chiang J, Lawrence B, Boyd J, et al. Effect of microstructure on retained austenite stability and work hardening of TRIP steels. Mater Sci Eng A. 2011;528(13–14):4516–4521. DOI:10.1016/j.msea.2011.02.032