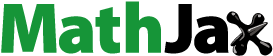
ABSTRACT
In recent years, significant efforts have been devoted towards the development of high-performance cermets with superior hardness and fracture toughness for engineering applications. In this study, a (Ti1-xTMx)C solid solution of a Ni cermet was prepared based on a combination of ab initio calculation and experimental results. The structural stability, mechanical properties, and microstructure of the cermet were investigated. A screening process was conducted using ab initio calculations to determine the optimal composition of (Ti1-xTMx)C (TM = V, Mo, and W) (x = 0–0.3125). The enhancement of the mechanical properties was analysed by calculating the electronic properties of the (Ti1-xTMx)C solid solutions. Additionally, we evaluated the powder morphology, microstructure, and mechanical properties of (Ti1-xTMx)C–20Ni by using experimental methods. The (Ti0.7W0.3)C–20Ni cermet exhibited enhanced hardness and fracture toughness in relation to conventional TiC–Ni cermets. Computational and experimental results indicated that the addition of secondary carbides improved the overall material properties.
Graphical abstract

Introduction
Cemented carbide WC–Co is widely used in the cutting tool industry owing to its high hardness and excellent abrasion resistance [Citation1,Citation2]. Recently, the demand for lithium-ion batteries has increased because of the importance of ecofriendly energy sources. In particular, alternatives to WC–Co must be explored because demand for cobalt, a rare metal for cathode materials, has been increasing [Citation3,Citation4]. A TiC–Ni cermet is a suitable alternative because of its advantageous characteristics, including excellent wear and oxidation resistance, high-temperature hardness, and appropriate chemical stability [Citation5–7].
Nevertheless, TiC-based cermets have limitations such as reduced fracture toughness in relation to WC–Co [Citation8]. In order to improve the mechanical properties of cermets, various studies have been conducted to add secondary carbides, such as WC, Mo2C, TaC, NbC, and HfC [Citation9,Citation10]. Additionally, transition carbides such as NbC and TaC are utilized in doped cermets to increase their thermal shock resistance and high-temperature durability [Citation11]. However, their mechanical properties are substantially inferior to those of WC–Co. Hence, a theoretical understanding of transition metal carbides is crucial for enhancing the mechanical properties of cermets.
The development of solid-solution carbides by adding secondary carbides is an important factor in obtaining high-performance cermets [Citation12,Citation13]. The experiment-based investigation of mechanical properties based on these carbide compositions is difficult to control because of the presence of multiple variables. This limitation can be overcome by using ab initio calculations, which save time and resources during the design of ideal solid-solution carbides that exhibit excellent mechanical properties. Furthermore, few studies have described the relationship between transition carbides and the mechanical properties of cermets through a combination of simulations and experiments. Therefore, we selected carbides based on combined ab initio calculation and experimental results to design cermets with the optimal composition and excellent mechanical properties.
In this study, ab initio calculations were conducted to investigate (Ti1-xTMx)C (TM = V, Mo, and W) and (x = 0.125, 0.1875, and 0.3125) solid solutions. The selected composition was experimentally investigated to determine the microstructure and mechanical properties of a (Ti1-xTMx)C–Ni (TM = V, Mo, and W, x = 0.1, 0.2, and 0.3) cermet. The effects of the composition on the phase stability, elastic modulus, hardness, and fracture toughness were investigated. The (Ti1-xTMx)C solid solutions, which theoretically have better mechanical properties, were optimized to enhance the hardness and fracture toughness of the (Ti1-xTMx)C–20Ni cermet. Therefore, compositional design based on calculations and experiments can improve the efficiency of material development by understanding and analyzing the addition secondary carbides mechanism.
Computational and experimental methods
Ab initio calculations
The plane wave pseudopotential method, based on the density functional theory (DFT), implemented in the Vienna Ab initio Simulation Package (VASP) code, was used for all calculations in this study [Citation14]. The (Ti1-xTMx)C (TM = V, Mo, and W) solid solutions have the Fm-3 m space group, with the Ti and C atoms occupying sites (0, 0, 0) and (0.5, 0.5, 0.5), respectively. In addition, we investigated the structural and mechanical properties of the solid solutions of (Ti1-xTMx)C (x = 0.125, 0.1875, and 0.3125). The projection augmented wave method (PAW) was used to investigate the interaction between valence electrons and core ions [Citation15]. The generalized gradient approximation (GGA) uses the Perdew-Burke-Ernzerhof (PBE) function to describe the exchange-correlation potential [Citation16,Citation17]. Considering the computational cost and accuracy of carbides, the GGA-PBE method reported in previous studies was selected [Citation18]. Disordered solid-solution models with the rock salt structure, having 32 atoms were generated independently using the special quasi-random structures (SQSs) technique in the Alloy Theoretic Automated Toolkit (ATAT) software ( and S1 in the Supplementary Information) [Citation19]. The valence electrons of Ti, V, Mo, W, and C atoms are Ti–3d24s2, V–3d34s2, Mo–4d55s1, W–5d46s2, and C–2s22p2, respectively. The Monkhorst–Pack scheme sampling k-points is , and the mesh of k-points is lower than 0.01 Å−1 [Citation20]. All the calculated plane wave cut-off energies were set to 500 eV. Because all the models have a rock salt crystal structure, only three elastic constants (
,
, and
) that affect the elastic properties were considered. The formation and cohesive energies of the solid solutions were calculated using EquationEquations (1)
(1)
(1) and (Equation2
(2)
(2) ). The calculated elastic constant was used to derive the elastic properties based on EquationEquations (3)
(3)
(3) –(Equation7
(7)
(7) ) using the Voight-Reuss-Hill approximation [Citation21].
where is the total energy of the solid solution per unit of formula (f.u.).
,
, and
are the total energies of the stable reactants;
,
, and
are the energies of the isolated single atoms, and
is the number of atoms. In addition, the elastic properties, theoretical hardness (
), and fracture toughness (
) were expressed using the following empirical formula (8)–(10) [Citation22–24].
where is the Voigt shear modulus,
is the Reuss shear modulus, k is the Pugh’s constant (G/B). Furthermore,
is the volume per atom, and
is Poisson’s ratio.
Sample preparation via powder metallurgy
The raw materials, rutile TiO2 (99%, Junsei), V2O5 (99.2%, Alfa Aesar), MoO3 (>99.5%, Aldrich), WO3 (>99%, ~20 μm, Aldrich), and graphite (>99.8%, ~40 μm, Alfa Aesar) powders, were mixed to produce solution carbide powders (Ti1-xVx)C–20 wt.%Ni, (Ti1-xMox)C–20 wt.%Ni, and (Ti1-xWx)C–20 wt.%Ni. The mole fractions of Mo, V, and W were 0.1, 0.2, and 0.3, respectively. Elemental titanium and oxide powders were mixed and milled by mechanical alloying of the powder mixture in a high-energy milling machine (Fritsch pulverisette 5, Germany). The powders used in this study are listed in . It was equipped with a stainless-steel jar and tungsten carbide balls with diameters of 6 mm. The powders were milled at a rotational speed of 250 rpm for 20 h. The ball-to-powder weight ratio (BPR) was 40:1, using a tungsten carbide ball medium. Carbothermal reduction was performed at 1300–1400°C for 1 h in a graphite vacuum furnace. After reduction and carburization, the (Ti1-xVx)C, (Ti1-xMox)C, and (Ti1-xWx)C powders were added with 20 wt.% of Ni (>99%, ~4.2 μm) by horizontal ball milling at a speed 150 rpm for 24 h in ethanol media. After mixing, the mixture powder was dried in an oven at 90°C for 24 h and sieved through a 48-mesh. The powder mixture was compacted into a disk form under a pressure of 125 MPa. The compacts were then sintered at 1500°C for 1 h in a graphite vacuum furnace. The sintered bodied were mechanically ground and sequentially polished with 6 μm and 3 μm diamond paste.
Table 1. Calculated values for the lattice parameter ( in
), volume (
in
), density (
in
), formation energy (
in eV/atom), and cohesive energy (
in eV/atom), melting point (
in
) of the TiC and (Ti1-xTMx)C (TM = V, Mo, and W) and (x = 0.125, 0.1875, and 0.3125) solid solutions.
Characterization of microstructure and properties
The phase identification of the powders was achieved through using X-ray diffraction (XRD) (D-MAX2200, Rigaku, Japan), conducted using Cu Kα radiation source (λ = 1.5418 Å), operated at a voltage of 40 kV, current of 200 mA, and scanning speed of 5 °/min. The powder crystallite size was calculated using the following Debye-Scherrer equation: , where D is the average crystallite size, λ is 1.5418 Å (in the case of Cu Kα), d is the full width at half maximum (FWHM) intensity of the peak, β is the half high width of the diffraction peak of the sample, and cos θ is the diffraction angle [Citation29]. The specific surface areas of the powders were determined via N2 adsorption fitted with Brunauer–Emmett–Teller (BET) isotherms (Micromeritics, TRISTAR3000, U.S.A.). The composition of the powders was analysed using a carbon analyser (CS-600, LECO, US) and an oxygen and nitrogen analyser (TCH-600, LECO, US). The microstructures of the sintered powders were observed through scanning electron microscopy (SEM; JSM-6380, JEOL, Japan). The hardness and fracture toughness were measured by the Vickers indentation method (HV-114, Mitutoyo) using a 30 kg load applied over 15 s. The fracture toughness was measured using the methods developed by Evans and Charles, Anstis et al. as well as the direct crack measurement method [Citation30,Citation31].
Results and discussions
Structural stability
The lattice parameters, volume, density, bond length, formation energy, and cohesive energy of the (Ti1-xTMx)C (TM = V, Mo, and W) solid solutions were calculated; the values are listed in . The lattice parameters of TiC showed slight deviation and were very close to the theoretical and experimental data acquired from previous studies. However, the lattice parameters of the (Ti1-xTMx)C (TM = V, Mo, and W) solid solutions differed in size, which is attributed to the TM atomic radius. The thermodynamic stability was analysed using the formation and cohesive energies, which indicated the ability of the materials to form from the standard states of pure elements or substances. A lower formation energy suggested a more stable structure. In all the solid solutions, the formation energy increased as the secondary carbide content increased. The formation energy of (Ti0.6875Mo0.3125)C was the highest, whereas that of (Ti0.875V0.125)C was the lowest. Therefore, among the solid solutions considered, (Ti0.875V0.125)C was the most stable. The (Ti0.6875W0.3125)C ceramic had the lowest formation energy and the highest corresponding melting point, whereas the (Ti0.875V0.125)C ceramic had the highest formation energy and the lowest corresponding melting point. The relationship between the melting point and formation energy has been experimentally verified in other binary systems [Citation32–36]. To confirm the accuracy of the melting points of the (Ti1-xTMx)C solid solutions, the melting point of TiC was calculated, which agreed well with the previously reported results [Citation37]. The (Ti1-xVx)C solid solution exhibited a melting point close to that of TiC and lower than those of the (Ti1-xMox)C and (Ti1-xWx)C solid solutions. The high melting point was because of the strong bonding interactions. Therefore, we analysed the electronic structure of the (Ti1-xTMx)C solid solutions. The cohesive energy is the total energy consumed to isolate all atoms in a material from one another by breaking all bonds. The cohesive energy of the (Ti1-xTMx)C solid solutions follows the order (Ti0.6875W0.3125)C >; (Ti0.8125W0.1875)C >; (Ti0.875W0.125)C >; (Ti0.875Mo0.125)C >; (Ti0.875V0.125)C >; (Ti0.8125Mo0.1875)C >; (Ti0.6875Mo0.3125)C >; (Ti0.6875V0.1875)C >; (Ti0.6875V0.3125)C, further indicating that (Ti0.6875W0.3125)C is the most stable among these (Ti1-xTMx)C solid solutions.
Mechanical properties of (Ti1-xTMx)C solid solutions
shows the calculation results of the bulk moduli, shear moduli, Young’s moduli, and theoretical hardnesses of the TiC and (Ti1-xTMx)C (TM = V, Mo, and W) solid solutions in the ground states. The calculated mechanical properties of the TiC and (Ti1-xTMx)C solid solutions agreed well with other theoretical and experimental results [Citation28,Citation38], indicating the accuracy of the calculated results. In general, the bulk modulus is an indicator of the strength of a crystal. shows that all solid solutions of (Ti1-xVx)C, (Ti1-xMox)C, and (Ti1-xWx)C were higher than those of the TiC solid solution. This indicates that the strength can be improved by adding V, Mo, and W. The bulk modulus of the (Ti1-xTMx)C solid solution follows the order (Ti0.6875W0.3125)C >; (Ti0.8125W0.1875)C >; (Ti0.875W0.125)C >; (Ti0.6875Mo0.3125)C >; (Ti0.8125Mo0.1875)C >; (Ti0.875Mo0.125)C >; (Ti0.6875V0.3125)C >; (Ti0.8125V0.1875)C >; (Ti0.875V0.125)C. This indicates that (Ti0.6875W0.3125)C has the highest strength among these (Ti1-xTMx)C solid solutions.
Figure 2. The calculated (a) bulk modulus, (b) shear modulus, and (c) Young’s modulus, and (d) theoretical hardness of (Ti1-xTMx)C (x = 0.125, 0.1875, and 0.3125) solid solutions.

shows the shear moduli, which are related to the hardness of the crystal structures. Generally, a material with a high shear modulus exhibits brittle behaviour. The shear moduli of the (Ti1-xVx)C solid solutions decreased as the transition metal content increased, while the shear modulus of the (Ti1-xMox)C solid solution increased with the increase in the transition metal content. Compared with the other calculated solid solutions, (Ti0.6875W0.3125)C exhibited the highest shear moduli. In addition, the Vickers theoretical hardness was determined to calculate the hardness of the (Ti1-xTMx)C solid solutions based on an empirical formula. The theoretical hardness of the (Ti0.6875W0.3125)C solid solution was the highest, while that of the (Ti0.6875V0.3125)C solid solution was the lowest. Therefore, it can be concluded that the shear moduli can indirectly govern the crystal hardness and that the influence of the bulk modulus on the hardness cannot be neglected. Consequently, shear moduli can indirectly reflect the hardness of the solid solution, and the bulk moduli can be considered a crucial parameter for hardness. The Young’s moduli of the (Ti1-xTMx)C solid solutions follow the order (Ti0.6875W0.3125)C >; (Ti0.8125W0.1875)C >; (Ti0.875W0.125)C >; (Ti0.6875Mo0.3125)C >; (Ti0.8125Mo0.1875)C >; (Ti0.875V0.125)C >; (Ti0.875Mo0.125)C >; (Ti0.6875V0.3125)C >; (Ti0.8125V0.1875)C. Furthermore, the Young’s moduli and shear moduli show similar trends, and (Ti0.6875W0.3125)C was found to exhibit the highest Young’s moduli and stiffness.
Pugh’s constant is an index used to determine the ductility or brittleness of a crystal structure. A material with Pugh’s constant of > 0.57 is considered brittle, while that with < 0.57 Pugh’s constant is ductile. As shown in Supplementary Figure S2, Pugh’s constants of the (Ti1-xTMx)C solid solutions were > 0.57, indicating that the (Ti1-xTMx)C solid solution is brittle. Furthermore, the addition of secondary carbides such as V, Mo, and W tends to improve the ductility of TiC. Poisson’s ratio is an indicator of the plasticity of a material. The (Ti0.6875V0.3125)C solid solution had the highest plasticity (0.223), whereas the (Ti0.875V0.125)C solid solution had the lowest plasticity (0.202).
Electronic properties of (Ti0.6875TM0.3125)C (TM = V, Mo, and W) solid solutions
shows the atomic interaction and electronic structure to understand the mechanical properties of the (Ti0.6875TM0.3125)C solid solution. In , the density of states (DOS) was calculated to obtain information related to the orbital distribution and bonding properties within the energy range [Citation39]. The DOS represents the number of electrons that can occupy a particular energy level of each carbide. In transition metals, the partial DOS (pDOS) of electron-filled d orbitals is indicated, while for carbon, the pDOS of p orbitals is indicated. The energy level of 0 eV on the x-axis indicates the Fermi energy (Ef) level of each carbide [Citation40]. In TiC, the region of overlap between the C 2p and Ti 3d orbitals indicates that the Ti–C interaction is dominant and crucial for the stability of the structure. TiC exhibits weak metallic properties because the Ti d–d interactions are greater than the Fermi level, whereas the Ti–C interactions are strong. As the transition metal (V, Mo, and W) content increased, the region of the d–d overlap below the Fermi level also expanded, indicating stronger metal interactions and a stronger influence on structural stability. This trend is also evident in the electron localization functions (ELF) between the two metals, as depicted in [Citation41]. The ELF map shows the difference in the atomic charge density between the (Ti1-xTMx)C solid solutions. The regions with a higher electron density are represented in red, while those with a lower density are in blue. The region around the transition metal atom is closer to red, indicating a loss in the electron density. Particularly, when V was added, a significant decrease in the electron density was observed, as is evident from the expansive blue region. In contrast, the model containing W is expected to have robust mechanical properties owing to its low electron density loss. Further studies are required to quantify the equilibrium between electronic coupling and charge to optimize the mechanical behaviour. In conclusion, adding 20 wt.% Ni to the (Ti0.6875TM0.3125)C solid-solution powder is expected to increase the hardness and fracture toughness in a cermet. Therefore, we experimentally verified the mechanical properties of (Ti0.6875V0.3125)C–20Ni, (Ti0.6875Mo0.3125)C–20Ni, and (Ti0.6875W0.3125)C–20Ni cermets.
Phase evolution during carbothermal reduction of (Ti1-xTMx)C solid solutions
shows the XRD patterns and the results of the carbon, nitrogen, and oxygen (C/N/O) combustion gas analysis of the (Ti0.7V0.3)C, (Ti0.7Mo0.3)C, and (Ti0.7W0.3)C solid solutions after the carbothermal reduction process. (Figure S6 and S7 in the Supplementary Information). Depending on the composition of the mixture, different phases are observed after milling; however, after a carbothermal reduction process, the solid solutions with different phases transform to single-phase (Ti0.7TM0.3)C solid solutions without free carbon, other phases, or impurities. The only difference between the secondary carbides is the peak shift [Citation42]. The peak shift of the powder with secondary carbide addition was the most evident, suggesting a change between the lattice and particle size of (Ti0.7TM0.3)C. Since the atomic radius of Ti (R = 0.146 nm) is larger than that of V (R = 0.133 nm), Mo (R = 0.145) and W (R = 0.139 nm), XRD peaks of (Ti0.7V0.3)C, (Ti0.7Mo0.3)C, and (Ti0.7W0.3)C solid solutions shifted slightly to higher angles [Citation43]. The average crystallite sizes of the solid phase were calculated from the peak broadening shown in . The average crystallite size was estimated using the following Scherrer equation: , where
is the average grain size,
is the X-ray wavelength (0.154 nm), and
and
are the diffraction angle and FWHM of an observed peak, respectively [Citation44]. TiC exhibits the smallest size with an average carbide size of 59.28 nm and (Ti0.7V0.3)C with 57.03 nm, whereas for (Ti0.7Mo0.3)C and (Ti0.7W0.3)C, these values were approximately 58.06 and 60.13 nm, respectively. Considering this trend, the toughness of the (Ti0.7W0.3)C–20Ni cermets was expected to increase in relation to that of the TiC–20Ni cermets with larger grain sizes. In addition, the results of the C/N/O combustion gas analysis for all the compositions indicated that the contents of nitrogen and oxygen were negligible, as shown in . This suggests that the oxygen and nitrogen contents decrease with increasing V, Mo, and W contents in the solid-solution phase. This result may be related to the affinities of oxygen and nitrogen towards Ti, V, Mo, and W (Figure S8 in the Supplementary Information). In all carbide solid solutions, carbon was observed at a content of 10%–20%. Excess carbon prevents the growth of carbide particles by suppressing the dissolution of carbides owing to the high activity of carbon in the molten binder during the sintering stage [Citation45]. In addition, as the excess carbon content increases, the hardness and fracture toughness may decrease because many pores exist in the samples with high carbon content.
Microstructure and mechanical properties of (Ti0.7TM0.3)C–20Ni cermets
shows the microstructures, Vickers hardness, and fracture toughness of the (Ti0.7TM0.3)C–20Ni cermets (TM = V, Mo, and W) after sintering. The SEM backscattered electron mode images of the solid solutions are shown in ; the data in Figure S9 in the Supplementary Information reveal that the TiC–Ni and (Ti0.7V0.3)C–20Ni cermets have a coreless microstructure. In contrast, the (Ti0.7Mo0.3)C–20Ni and (Ti0.7W0.3)C–20Ni cermets exhibited a core–rim structure, suggesting their high toughness. The dark core is the partially dissolved original (Ti0.7Mo0.3)C and (Ti0.7W0.3)C phase, while the light-grey phase around the dark core corresponds to the other solid-solution phase. In the cermets containing MoC and WC as additives, the rim usually becomes enriched with Mo and W in relation to the other phases upon dissolution. To understand the core–rim structural elements of the solid-solution cermet, EDS elemental mapping was performed for determining the composition of (Ti0.7W0.3)C; the results are shown in (Figure S10 in the Supplementary Information) [Citation46]. The metallic atoms (W, and Ti) were detected at a relatively low content (approximately 1 wt.% for W and 4.5 wt.% for Ti). The presence of W and Ti in this metal binder is attributed to the dissolution of the hard phases during sintering.
Figure 5. SEM-BSE micrographs and mechanical properties of (Ti0.7TM0.3)C–20Ni cermets: (a) TiC, (b) (Ti0.7V0.3)C, (c) (Ti0.7Mo0.3)C, (d) (Ti0.7W0.3)C, (e) Vicker’s hardness, and (f) fracture toughness.

show the Vickers hardness and fracture toughness of the (Ti1-xTMx)C–20Ni cermets. The Vickers hardness and fracture toughness of the (Ti1-xTMx)C–20Ni cermet varied depending on the amount of secondary carbides and elements added. In general, as the hardness increases, the deformation and energy absorption capacities of a material decrease, resulting in decreased fracture toughness. However, it was calculated that the hardness and fracture toughness increased linearly with increasing Mo and W content in (Ti1-xTMx)C–20Ni. In contrast, with an increase in the V content, the hardness became higher than that of the TiC–20Ni cermet by up to 0.1%–0.2%; however, the fracture toughness decreased at all V contents. Specifically, the increase in the durability of the (Ti0.7W0.3)C–20Ni and (Ti0.7Mo0.3)C–20Ni cermets was due to the alloying effect of Mo or W in TiC [Citation47,Citation48].
Conclusion
We performed ab initio calculations to determine the elastic and electronic properties of (Ti1-xTMx)C solid solutions. We studied the effect of the microstructure and mechanical properties after the powder-metallurgy-based synthesis of the (Ti1-xTMx)C–20Ni cermet. The equilibrium lattice parameters for the (Ti1-xTMx)C solid solutions (TM = V, Mo, and W) were found to be highly accurate, as determined by comparison with experimental data and other calculation results. As the secondary carbide content increased in the (Ti1-xTMx)C solid solutions, the bulk moduli increased for all compositions. In contrast, the shear and Young’s moduli of (Ti0.8125W0.1875)C were the highest. Brittleness, which is closely related to the toughness of a bulk material, was estimated using Poisson’s ratio and Pugh’s constant. The results indicated that (Ti0.8125V0.1875)C is the most brittle of the (Ti1-xTMx) solid solutions. Based on the theoretical studies of solid-solution carbides, (Ti1-xWx)C was selected as an optimal composition to prepare as a cermet. The successful synthesis of single-phase (Ti1-xTMx)C solid-solution particles was confirmed through XRD. Both (Ti0.7Mo0.3)C–20Ni and (Ti0.7W0.3)C–20Ni cermets possessed a core–rim structure and exhibited toughness higher than that of TiC. (Ti0.7W0.3)C–20Ni showed enhanced hardness and fracture toughness in relation to conventional TiC cermets. In summary, the (Ti1-xTMx)C solid-solution cermet exhibits an attractive microstructure and mechanical properties. We expect that this study will provide useful guidelines for the design of various related systems, such as nuclear reactor materials and hard coatings.
Data abailability
All data generated or used during the study appear in the submitted article.
Author contributions
Jiwoong Kim conveyed the idea and designed and supervised the study; Myungjae Kim and Hyokyeong Kim developed the theory and performed ab initio calculations; Jiho Kim and Jinyong Lee verified the analytical methods; Myungjae Kim drafted the manuscript; Myungjae Kim and Jiho Kim revised the manuscript; Jongwook Kwak and Sooah Kyung helped analyse the data; All authors discussed the results and contributed to the final manuscript.
Supplemental Material
Download MS Word (6.8 MB)Acknowledgments
This study was supported by the Soongsil University Research Fund (New Professor Support Research) of 2019.
Disclosure statement
No potential conflict of interest was reported by the author(s).
Supplemental data
Supplemental data for this article can be accessed online at https://doi.org/10.1080/10667857.2023.2251293.
Additional information
Funding
References
- Wu X, Shen J, Jiang F, et al. Study on the oxidation of WC-Co cemented carbide under different conditions. Int J Refract Hard Met. 2021;94:105381–10. doi: 10.1016/j.ijrmhm.2020.105381
- Jiang W, Lu H, Liu X, et al. Outstanding high-temperature oxidation-and wear-resistance of WC based cermets. J Mater Sci Technol. 2023;155:33–46. doi: 10.1016/j.jmst.2022.12.071
- Seck GS, Hache E, Barnet C. Potential bottleneck in the energy transition: the case of cobalt in an accelerating electro-mobility world. Resour Policy. 2022;75:102516–102532. doi: 10.1016/j.resourpol.2021.102516
- Padmakumar M, Dinakaran, Dinakaran D. A review on cryogenic treatment of tungsten carbide (WC-Co) tool material. Mater Manuf Process. 2021;36(6):637–659. doi: 10.1080/10426914.2020.1843668
- Ettmayer P, Kolaska H, Lengauer W, et al. Ti (C, N) cermets—metallurgy and properties. Int J Refract Hard Met. 1995;13(6):343–351. doi: 10.1016/0263-4368(95)00027-G
- Han C, Den C, Zhao D, et al. Milling performance of TiC–Ni cermet tools toughened by TiN nanoparticles. Int J Refract Hard Met. 2012;30(1):12–15. doi: 10.1016/j.ijrmhm.2011.06.005
- Lee T, Jeong W, Chung S, et al. Effects of TiC on the microstructure refinement and mechanical property enhancement of additive manufactured Inconel 625/TiC metal matrix composites fabricated with novel core-shell composite powder. J Mater Sci. 2023;164:13–26. doi: 10.1016/j.jmst.2023.04.033
- Kim J, Ahn S, Kang S. Effect of the complete solid-solution phase on the microstructure of Ti(CN)-based cermet. Int J Refract Hard Met. 2009;27(2):224–228. doi: 10.1016/j.ijrmhm.2008.07.012
- Liu N, Xu Y, Li H, et al. Effect of nano-micro TiN addition on the microstructure and mechanical properties of TiC based cermets. J Eur Ceram Soc. 2002;22(13):2409–2414. doi: 10.1016/S0955-2219(02)00010-9
- Kim S, Min KH, Kang S. Rim structure in Ti(C0.7 N0.3)-WC-Ni cermets. Journal Of The American Ceramic Society. 2003;86(10):1761–1766. doi: 10.1111/j.1151-2916.2003.tb03551.x
- Kwon WT, Park JS, Kim S-W, et al. Effect of WC and group IV carbides on the cutting performance of Ti(C, N) cermet tools. Int J Mach Tools Manuf. 2004;44:341–346. doi: 10.1016/j.ijmachtools.2003.10.023
- Park S, and Kang S. Toughened ultra-fine (Ti, W)(Cn)–Ni cermets. Scripta Materialia. 2005;52(2):129–133. doi: 10.1016/j.scriptamat.2004.09.017
- Liu N, Han CL, and Ying WH, et al. Microstructure, hardness and fracture toughness of TiC based cermets with nano TiN powders addition. Powder Metall. 2007;50(2):142–147. doi: 10.1179/174329007X186534
- Hafner J. Ab‐initio simulations of materials using VASP: density‐functional theory and beyond. J Comput Chem. 2008;29(13):2044–2078. doi: 10.1002/jcc.21057
- Kresse G, Joubert D. From ultrasoft pseudopotentials to the projector augmented-wave method. Phys Rev B. 1999;59(3):1758–1775. doi: 10.1103/PhysRevB.59.1758
- Perdew JP, Burke K, Ernzerhof M. Generalized gradient approximation made simple. Phys Rev Lett. 1996;77(18):3865–3868. doi: 10.1103/PhysRevLett.77.3865
- Hammer B, Hansen LB, Nørskov JK. Improved adsorption energetics within density-functional theory using revised Perdew-Burke-Ernzerhof functionals. Phys Rev B. 1999;59:7413–7421. doi: 10.1103/PhysRevB.59.7413
- Kim J, Kim M, Roh K-M, et al. Bond characteristics, mechanical properties, and high-temperature thermal conductivity of (Hf1−x Tax)C composites. J Am Ceram Soc. 2019;102(10):6298–6308. doi: 10.1111/jace.16466
- Kim K, Zhou B-C, and Wolverton C. First-principles study of crystal structure and stability of T1 precipitates in Al-Li-Cu alloys. Acta Mater. 2018;145:337–346. doi: 10.1016/j.actamat.2017.12.013
- Wisesa P, McGill KA, and Mueller T.Efficient generation of generalized monkhorst-pack grids through the use of informatics. Phys Rev B. 2016;93(15):155109–155118. doi: 10.1103/PhysRevB.93.155109
- Voight W. Lehrbuch der kristallphysik. Teubner: Leipzig; 1928.
- Soderholm K-J. Review of the fracture toughness approach. Dent Mater. 2010;26(2):e63–e77. doi: 10.1016/j.dental.2009.11.151
- Hussainova I, Kubarsepp J, and Pirso J. Mechanical properties and features of erosion of cermets. Wear. 2001;250(1–12):818–825. doi: 10.1016/S0043-1648(01)00737-2
- Gao F. Theoretical model of intrinsic hardness. Phys Rev B. 2006;73(13):132104–132107. doi: 10.1103/PhysRevB.73.132104
- Rajabi A, Ghazali M, Daud A. Chemical composition, microstructure and sintering temperature modifications on mechanical properties of TiC-based cermet–A review. Mater Des. 2015;67:95–106. doi: 10.1016/j.matdes.2014.10.081
- Seo M, Kim J, Kang S. Effect of carbon content on the microstructure and properties of (Ti0.7W0.3) C-Ni cermet. Int J Refract Hard Met. 2011;29(4):424–428. doi: 10.1016/j.ijrmhm.2011.01.004
- Kerdsongpanya S, Alling B, Eklund P. Effect of point defects on the electronic density of states of ScN studied by first-principles calculations and implications for thermoelectric properties. Phys Rev B. 2012;86(19):195140–195146. doi: 10.1103/PhysRevB.86.195140
- Cankurtaran M, Onder M, Celik H, et al. Energy bands, carrier density and Fermi energy in bi in a uniform magnetic field. Phys Solid State. 1987;20(25):3875–3886. doi: 10.1088/0022-3719/20/25/015
- Holzwarth U, Gibson N. The Scherrer equation versus the ‘Debye-Scherrer equation’. Nat Nanotech. 2011;6(9):534. doi: 10.1038/nnano.2011.145
- Ag E, Ea C. Fracture toughness determinations by indentation. J American Ceramic Society. 1976;59(7–8):371–372. doi: 10.1111/j.1151-2916.1976.tb10991.x
- Anstis G, Chantikul P, Lawn BR, et al. A critical evaluation of indentation techniques for measuring fracture toughness: I, direct crack measurements. J Am Ceram Soc. 1981;64:533–538. doi: 10.1111/j.1151-2916.1981.tb10320.x
- Jiang D, Li S, Hu W, et al. Theoretical prediction of mechanical and thermodynamic properties of TiMC2 (M = Hf, Mo, Nb and W) ceramics: very promising excellent TiC-based solid solution materials. Int J Refract Hard Met. 2023;114:106240–110651. doi: 10.1016/j.ijrmhm.2023.106240
- Wu L, Yao T, Wang Y, et al. Understanding the mechanical properties of vanadium carbides: nano-indentation measurement and first-principles calculations. J Alloys Compd. 2013;548:60–64. doi: 10.1016/j.jallcom.2012.09.014
- Liu Y, Jiang Y, Feng J, et al. Elasticity, electronic properties and hardness of MoC investigated by first principles calculations. Physica B Condens Matter. 2013;419:45–50. doi: 10.1016/j.physb.2013.03.016
- Herrmann M, Raethel J, Berger L-M. On the possibility of the incorporation of al into the WC lattice. Int J Refract Hard Met. 2013;41:495–500. doi: 10.1016/j.ijrmhm.2013.06.008
- Liu Y, Jiang Y, Zhou R, et al. Mechanical properties and chemical bonding characteristics of WC and W2C compounds. Ceram Int. 2014;40(2):2891–2899. doi: 10.1016/j.ceramint.2013.10.022
- Xiang M, Song M, Zhu Q, et al. Facile synthesis of high‐melting point spherical TiC and TiN powders at low temperature. J Am Ceram Soc. 2020;103(2):889–898. doi: 10.1111/jace.16810
- Savin A, Nesper R, Wengert S, et al. ELF: the electron localization function. Angew Chem Int Ed. 1997;36(17):1808–1832. doi: 10.1002/anie.199718081
- Kim YK, Shim J-H, Cho YW, et al. Mechanochemical synthesis of nanocomposite powder for ultrafine (Ti, Mo)C–Ni cermet without core-rim structure. Int J Refract Hard Met. 2004;22:193–196. doi: 10.1016/j.ijrmhm.2004.06.004
- Al-Jumaili BE, Rzaij JM, Ibraheam A. Nanoparticles of CuO thin films for room temperature NO2 gas detection: annealing time effect. Mater Today Proc. 2021;42:2603–2608. doi: 10.1016/j.matpr.2020.12.588
- Ollilainen V, Kasprzak W, Holappa L. The effect of silicon, vanadium and nitrogen on the microstructure and hardness of air cooled medium carbon low alloy steels. J Mater Process Technol. 2003;134(3):405–412. doi: 10.1016/S0924-0136(02)01131-7
- Münch B, Martin LH, and Leemann A. Segmentation of elemental EDS maps by means of multiple clustering combined with phase identification. J Microsc. 2015;260(3):411–426. doi: 10.1111/jmi.12309
- Chen M, Zhang X, and Xiao X, et al. Effect of secondary carbides on the core-rim structure evolution of TiC-based cermets. Mater Res Express. 2021;8:076501. doi: 10.1088/2053-1591/ac0d92
- Kim J, Seo M, Kang S. Microstructure and mechanical properties of Ti-based solid-solution cermets. Mater Sci Eng A. 2011;528(6):2517–2521. doi: 10.1016/j.msea.2010.11.076
- Kim J, Kang S. Microstructure evolution and mechanical properties of (Ti0.93W0.07) C–xWC–20Ni cermets. Mater Sci Eng A. 2011;528(7–8):3090–3095. doi: 10.1016/j.msea.2010.12.038
- Kim J, Kang S. Elastic and thermo-physical properties of TiC, TiN, and their intermediate composition alloys using ab initio calculations. J Alloys Compd. 2012;528:20–27. doi: 10.1016/j.jallcom.2012.02.124
- Sun W, Ehteshami H, Korzhavyi PA. Structure and energy of point defects in TiC: an ab initiostudy. Phys Rev B. 2015;91(13):134111–134121. doi: 10.1103/PhysRevB.91.134111
- Chang R, Graham LJ. Low‐temperature elastic properties of ZrC and TiC. J Appl Phys. 1966;37(10):3778–3783. doi: 10.1063/1.1707923