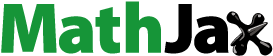
ABSTRACT
In this study, the thermal deformation behaviour of a high strength offshore steel at different temperatures and rates was investigated through thermal compression experiments.An Arrhenius constitutive model and a back propagation artificial neural network (BP-ANN) were established to address more complex deformation characteristics. The performances of both models were was evaluated using standard statistical parameters such as the correlation coefficient (R) and average absolute relative error (AARE). The results showed that both models can accurately predict the rheological stresses generated during deformation.The BP-ANN outperforms the Arrhenius equation model with correlation coefficients of fit greater than 99.9% and less than 0.8% relative error. At a strain rate of 0.01 s−1 and 10 s−1, the accuracy of the ANN decreases slightly due to the fact that it exceeds the strain rate range of the training set, as compared to the Arrhenius constitutive equations as these are more accurately predicted.
Introduction
The thermal deformation behaviour of metals is significantly influenced by the deformation parameters (temperature, deformation rate, etc.). During plastic deformation under different conditions, the phenomena of work hardening (WH), dynamic recovery (DRV), and dynamic recrystallisation (DRX) occur [Citation1,Citation2]. In WH the plastic properties of the material are reduced, and the rheological stress is increased. However, softening phenomena such as DRV and DRX reduce the rheological stress and restore plasticity [Citation3,Citation4]. Therefore, the interaction under thermal deformation conditions is an important reason for complex deformation behaviour [Citation5,Citation6].
In recent years, researchers have proposed various intrinsic constitutive equations to describe the high-temperature deformation behaviour of metallic materials. One of the most typical constitutive equations is the Arrhenius intrinsic constitutive equation, which considers the deformation temperature and strain rate [Citation7]. However, the traditional Arrhenius equation does not consider the effect of degree of deformation. Shi et al. [Citation8] combined the strain degree and temperature in the equation to obtain the flow stress constitutive equation of material strain parameters, which is widely used to predict the flow stress of various metals. Examples include P91 steel [Citation9], Ti-deformed austenitic stainless steel [Citation10], 800 H high-temperature alloy [Citation11], TC4-DT titanium alloy [Citation12], AZ81 magnesium alloy [Citation13], and 2124 aluminium alloy [Citation14]. In these studies, the average relative error (AARE) between the calculated and experimental values was mostly concentrated within the range of 5–9%, and artificial neural network (ANN) models that did not require repeated regression calculations were introduced to address the problem of low prediction accuracy [Citation15–19].
ANNs, a newer artificial intelligence technique, are more effective in solving highly complex problems compared to regression methods. The typical structure of a BP-ANN consists of an input layer, output layer, and one or more hidden layers with artificial neurons that select and weigh the inputs. The input layer receives the input data, and after processing, sends the data to the hidden layer. The hidden layer acts as a complex network structure to model the nonlinear relationship between the input and output layers. It processes the data computations, and sends the responses to the output layer, which produces outputs [Citation20,Citation21].
In recent years, an increasing number of researchers have used ANN models to dissect the relationship between material properties. Lin et al. [Citation22] established optimal hot-forming process parameters for 42CrMo steel based on ANN models. Zhao et al. [Citation23] characterised the thermal deformation of Ti600 titanium alloy using an instantaneous equation and ANN. Quan et al. [Citation24] developed an ANN model for cast Ti-6Al-2Zr-1Mo-1 V alloy over a wide temperature range involving phase transformation, and predicted the high-temperature flow behaviour of 20 MnNiMo alloys using an ANN [Citation25].
Intrinsic constitutive equations and ANNs have been applied to characterise the rheological behaviour of materials. Examples include titanium alloys [Citation26,Citation27], stainless steels [Citation28,Citation29], high-temperature alloys [Citation30], aluminium [Citation31,Citation32] and magnesium alloys [Citation33,Citation34]. The relationship between the process, microstructure, and properties can be accurately characterised after considering the effects of the parameters together. For the offshore steels, the thermal deformation behaviour also has a strong influence on the combination of strength and toughness [Citation35–43], which is of great significance for applications in the offshore engineering environments. In this study, the hot deformation stresses of high-strength offshore steels under different models were predicted separately using an Arrhenius equation-based model and a BP-ANN. Error analysis was performed to evaluate the performance of these models in predicting rheological stresses.
Material and experiments
Experiments were conducted using forged ingots with a mass of approximately 65 kg, and the smelting process was conducted under complete vacuum (). From the ingots, Φ8 mm × 12 mm sized specimens were machined and introduced in a Gleeble-3800 testing machine for single pass hot compression tests. The specimens were heated at a rate of 5°C/s to 1200°C for 5 min, cooled at a rate of 5°C/s to the corresponding deformation temperatures (800°C, 900°C, 1000°C, 1100°C), held for 30 s, compressed at the corresponding strain rates (0.1 s−1, 0.5 s−1, 1 s−1, 5 s−1) with a 55% depression, and then water quenched after compression to retain the deformation morphology. Hot-compression tests were performed under Ar gas to avoid metal oxidation during heating and deformation.
Table 1. Chemical composition of high-strength offshore steel (in wt%).
The true stress-true strain curves of the experimental specimens deformed at different rates and temperatures for a single pass of compression, as shown in . As the deformation temperature decreases and the strain rate increases, the rheological stress of the material shows an increasing trend. The slow decrease in the rheological stress after the strain-hardening stage is due to dynamic softening caused by the occurrence of DRV and DRX. The rheological stress gradually tends to a steady state at 1100°C and 0.1 s−1, indicating a more balanced state between DRV, DRX and WH. These findings show that the stresses in high-strength offshore steel exhibit highly nonlinear behaviour in response to the three deformation parameters (temperature, strain, and strain rate)
Comparison between improved Arrhenius-type constitutive equation and BP-ANN model
Improved arrheniue constitutive equation
The Arrhenius-type constitutive equation is widely used as an image-only model to describe the intrinsic constitutive relationship of materials. However, strain, which has an important influence on the flow behaviour, has been neglected in equations proposed in previous studies. Thus, the previous Arrhenius-type constitutive equations could not predict flow behaviour accurately. Lin [Citation44] et al. first proposed a modified model considering the effect of strain, and used it to accurately describe the deformation behaviour of 42CrMo steel at high temperatures. Owing to the superiority of predictions of the revised model, the modified Arrhenius-type intrinsic constitutive equation has been successfully applied to describe the intrinsic constitutive relationships of various materials [Citation45–47].
In this study, the coefficients of the intrinsic constitutive equations are solved at a strain of 0.5. The natural logarithms of EquationEquations 1(1)
(1) Equationand 2
(2)
(2) can be expressed as
As shown in , the linear regression of the data under different deformation temperatures using the least-squares method can yield the value of at different temperatures, and the average value is 17.299. Similarly,
is 0.131 MPa−1, and
, which is obtained as 0.00757 MPa−1.
Figure 2. The relationship between flow stress and strain rate for the experimental steel: (a) plot; (b)
plot.

EquationEquation 6(6)
(6) is obtained by taking the natural logarithm of both sides of EquationEquation 3
(3)
(3) and applying a partial differential.
As shown in , the slope reciprocal of is evaluated as 6.001, and the slope of
is evaluated as 7.385, respectively.
Figure 3. Experimental rheological stress as a function of strain rate and deformationtemperature: (a) plot; (b)
plot.

The regression coefficient obtained from is introduced into EquationEquation 6(6)
(6) , and the heat deformation activation energy
is calculated to be 368.469 kJ·mol−1 for the experimental steel at a strain level of 0.5. By inserting
into the above EquationEquation 3
(3)
(3) the following relationships of Zener-Hollomon parameter (Z parameter) are obtained as EquationEquations 7
(7)
(7) Equation~9
(9)
(9) . In EquationEquation 9
(9)
(9) , the constants are the intercept and the slope of the regression line, which are 35.1464 and 5.9051, respectively, as shown in .
Repeating the method of solving the coefficients of each principal equation for a strain of 0.5, the coefficients of each stress-strain principal equation (α, β, n, Q and lnA) can be obtained for different strains (0.1, 0.2, 0.3, 0.4, 0.45, 0.55, 0.6, 0.65, 0.7), and the results are shown in .
Table 2. Coefficients of the equation at different degrees of deformation.
Therefore, in order to describe the intrinsic structure of the experimental steel under the aforementioned deformation conditions more precisely, the relationship between the equation coefficients (α, β, n, Q and lnA) and strain is established by polynomial equations of order6 considering the degree of deformation. The fitting curve of polynomial coefficients is shown in . The constitutive EquationEquation 11(11)
(11) is obtained from and EquationEquation 10
(10)
(10) . show the high correlation between the predicted and actual stress values.
Table 3. Polynomial coefficients of α, β, n, Q and lnA.
Figure 5. The variation of material constants for the constitutive equation with true strains: (a) α; (b) β; (c) n; (d) Q; (e) lnA.

Development of BP-ANN model
In this study, a BP-ANN model for the correlation of hot compression rheological stress with strain, strain rate and temperature for high-strength offshore steel is developed. The deformation temperature (T), strain rate (), and strain (
) are the input variables and the actual stress (
) is the only output. A schematic of the structure is shown in . To develop an accurate BP-ANN model, it is crucial to determine the appropriate number of hidden layers and the number of neurons in each hidden layer. As experimental data, such as temperature, strain, strain rate, and stress, are measured in different units, these data must be normalised to dimensionless units before training, which reduces the convergence speed and accuracy of the model. Assuming that one and two hidden layers are used for testing, the appropriate number of hidden layers is determined by evaluating the predicted data from the training and testing using the experimental data with appropriate tolerances. In addition, an empirical equation is proposed to determine the range of E-values, i.e. the range of number of neurons per hidden layer, and the range is calculated accordingly as 3–12. Finally, the accuracy of the neural network model is guaranteed using a two-layer hidden layer structure.
where is the number of neurons in each hidden layer,
and
are the number of neurons in the input and output layers of the network, respectively.
= 3,
= 1. and
is a ranging from 1 to 10.
The values of the input and output variables are distributed over different ranges and uniform dimensions, which leads to poor convergence speed and prediction accuracy of ANN models. Therefore, normalisation of the initial experimental stress-strain data is essential to ensure dimensionless and approximately similar quantitative values of the input and output variables. In this study, the magnitude of the normalised data is narrowed to adjust the parameters to within 0–0.3, with coefficients of 0.05 and 0.25 in the regression equation. The pilot algorithm demonstrates that such magnitudes can improve convergence speed and forecast accuracy. Excessive errors caused by a wide range are avoided. In addition, it should be noted that the initial value of the true strain rate has a large magnitude. Thus, we take the logarithm to convert the true strain rate data prior to normalisation:
where is the normalised value of
,
is the experimental data,
and
are the maximum and minimum values of, respectively.
In this study, R and AARE were used as statistical indicators to comprehensively evaluate the predictive ability of the ANN model, and are expressed as Equations 15 and 16, respectively. A high R value close to 1 indicates that the predicted value agrees well with the experimental value, while a low AARE value close to 0 indicates that the sum of the errors between the predicted and experimental values tends to zero.
where E and P are the experimental and predicted values of the true stress, respectively, and
are the average values of
and
, respectively,
is the predicted stress value,
is the corresponding experimental stress value, and N is the number of predicted points.
The relative error () in the equation represents the percentage error of each stress-strain prediction relative to the corresponding experimental value, and is introduced for a more in-depth and detailed evaluation of the ANN model. The parameters
and
are the mean and standard deviation, respectively. For a smaller
value, the precision is higher. Information on the values is provided by calculating and counting the
values of all prediction points, including the training and testing points. shows the correlation between predicted and true stress values for the training and test data. shows a histogram of the relative errors in the training and testing parts. The relative errors are within a narrow range of 0–6% for both the training and testing parts. More notably, most of the
values are concentrated around the ideal value of 0. In the training part, 79.03% of the points with ~ 6% error are within the [−1%, 1%] interval. In the test part, 78.47% of the points are concentrated within the [−1%, 1%] interval. These results, generated using statistical data, provide direct evidence that the ANN model achieves high accuracy in both the training and testing phases.
where is the predicted stress value and
is the corresponding experimental stress value.
is the relative error,
and
are the mean and standard deviation of
, respectively, and
is the number of relative errors.
Figure 9. Correlation between predicted and true stress values for the (a) training and (b) test data.

Figure 10. Relative error distribution of predicted true stress values for the (a) training and (b) test points.

As shown in , the data points with the true stress values as the horizontal axis and the predicted stress as the vertical axis are consistent with the best linear fit line, indicating excellent prediction performance. The correlation coefficients, R, for the training and test points are 0.99974 and 0.9998, respectively. In addition, the AARE values calculated from the training and test parts are 0.74575% and 0.70758%, respectively. The small errors in both cases fully illustrate the high-accuracy prediction performance of the BP-ANN in training and testing.
Based on the well-trained ANN model, the actual stress values under experimental conditions are included to predict the deformation conditions corresponding to the previously trained and tested points. compares the stress values predicted by the BP-ANN model with the experimental stress values. The predicted values follow the same trend as the true values, and increase with decreasing temperature or increasing strain rate. This indicates that the BP-ANN model is more accurate compared to the Arrhenius-type constitutive equation in determining the variation law of the rheological stress.
Figure 11. Comparison of predicted stress values from the BP-ANN model with experimental values at temperatures of 1073 ~ 1373 K and at the strain rates of (a) 0.1 s−1, (b) 0.5 s−1, (c) 1 s−1, and (d) 5 s−1.

The experimental stress-strain curves, predictions from the BP-ANN model and Arrhenius constitutive equation at 1123 K and strain rates 0.01 s−1, 0.03 s−1 and 10 s−1, are shown in . The new deformation temperature and deformation rates are introduced. Among the three curves predicted by BP-ANN, when the strain rate is 3 s−1, it shows good predictive tracking ability in the range of 0.1 s−1 to 5 s−1 of the training set. However, as the rates of 0.01 s−1and 10 s−1exceeded the training range of the training set, although the trend was consistent, the accuracy of the ANN model is lower than that of the Arrhenius constitutive mode.
Conclusions
A BP-ANN model of high-strength offshore steel is developed based on isothermal compression test data from a Gleeble 3800 thermal simulator. The established neural network model can effectively simulate complex thermal deformation behaviour and has good generalisation ability over a wide range of temperatures and strain rates.
In the BP-ANN model, the deformation temperature (
), strain rate (
), and strain (
) are the input variables, and true stress (
) is the output variable. The higher R values, lower AARE values, and stable percentage error distribution results indicate that the BP-ANN model has a better predictive performance than the Arrhenius-type intrinsic constitutive equation under limited experimental conditions.
The ANN model has excellent potential for application in investigating the thermal deformation processes. The accuracy of the predicted rheological stress provides strong theoretical support for the determination of parameters for processes such as rolling and for the heat treatment of high-strength offshore steel.
Acknowledgments
This research was financially supported by Science and Technology Research Projects of the CNPC (No.2021ZG14 and LHT-2023-02).
Disclosure statement
No potential conflict of interest was reported by the author(s).
Additional information
Funding
References
- Chen MS, Lin YC, Ma XS. The kinetics of dynamic recrystallization of 42CrMo steel. Mater Sci Eng A. 2012;556:260–11. doi: 10.1016/j.msea.2012.06.084
- Zhu H, Chen F, Zhang H, et al. Review on modeling and simulation of microstructure evolution during dynamic recrystallization using cellular automaton method. Sci China Technol Sci. 2020;63(3):357–396. doi: 10.1007/s11431-019-9548-x
- Liu G, Du D, Wang K, et al. Epitaxial growth behavior and stray grains formation mechanism during laser surface re-melting of directionally solidified nickel-based superalloys. J Alloys Compd. 2021;853:157325. doi: 10.1016/j.jallcom.2020.157325
- Guo C, Liu SH, Hu RZ, et al. Adv Mater Sci Eng. 2020;2020: 8470738.
- Lin YC, Chen XM. A critical review of experimental results and constitutive descriptions for metals and alloys in hot working. Mater Des. 2011;32(4):1733–1759. doi: 10.1016/j.matdes.2010.11.048
- Wu B, Li MQ, Ma DW. The flow behavior and constitutive equations in isothermal compression of 7050 aluminum alloy. Mater Sci Eng A. 2012;542:79–87. doi: 10.1016/j.msea.2012.02.035
- Sellars CM, McTegart WJ. On the mechanism of hot deformation. Acta Metall. 1966;14(9):1136–1138. doi: 10.1016/0001-6160(66)90207-0
- Shi Z, Yan X, Duan C. Characterization of hot deformation behavior of GH925 superalloy using constitutive equation, processing map and microstructure observation. J Alloys Compd. 2015;652:30–38. doi: 10.1016/j.jallcom.2015.08.118
- Samantaray D, Mandal S, Bhaduri AK. A comparative study on Johnson Cook, modified Zerilli–Armstrong and Arrhenius-type constitutive models to predict elevated temperature flow behaviour in modified 9Cr–1Mo steel. Comput Mater Sci. 2009;47(2):568–576. doi: 10.1016/j.commatsci.2009.09.025
- Mandal S, Rakesh V, Sivaprasad PV, et al. Constitutive equations to predict high temperature flow stress in a Ti-modified austenitic stainless steel. Mater Sci Eng A. 2009;500(1–2):114–121. doi: 10.1016/j.msea.2008.09.019
- Cao Y, Di HS, Misra RDK, et al. Hot deformation behavior of alloy 800H at intermediate temperatures: constitutive models and microstructure analysis. J Mater Eng Perform. 2014;23(12):4298–4308. doi: 10.1007/s11665-014-1220-4
- Peng X, Guo H, Shi Z, et al. Constitutive equations for high temperature flow stress of TC4-DT alloy incorporating strain, strain rate and temperature. Mater Des. 2013;50:198–206. doi: 10.1016/j.matdes.2013.03.009
- Changizian P, Zarei-Hanzaki A, Roostaei AA. The high temperature flow behavior modeling of AZ81 magnesium alloy considering strain effects. Mater Des. 2012;39:384–389. doi: 10.1016/j.matdes.2012.02.049
- Lin YC, Xia YC, Chen XM, et al. Constitutive descriptions for hot compressed 2124-T851 aluminum alloy over a wide range of temperature and strain rate. Comput Mater Sci. 2010;50(1):227–233. doi: 10.1016/j.commatsci.2010.08.003
- Zhao J, Ding H, Zhao W, et al. Modelling of the hot deformation behaviour of a titanium alloy using constitutive equations and artificial neural network. Comput Mater Sci. 2014;92:47–56. doi: 10.1016/j.commatsci.2014.05.040
- Ashtiani HRR, Shahsavari P. A comparative study on the phenomenological and artificial neural network models to predict hot deformation behavior of AlCuMgPb alloy. J Alloys Compd. 2016;687:263–273. doi: 10.1016/j.jallcom.2016.04.300
- Peng WW, Zeng WD, Wang QJ, et al. Comparative study on constitutive relationship of as-cast Ti60 titanium alloy during hot deformation based on Arrhenius-type and artificial neural network models. Mater Des. 2013;51:95–104. doi: 10.1016/j.matdes.2013.04.009
- Sabokpa O, Zarei-Hanzaki A, Abedi HR, et al. Artificial neural network modeling to predict the high temperature flow behavior of an AZ81 magnesium alloy. Mater Des. 2012;39:390–396. doi: 10.1016/j.matdes.2012.03.002
- Liu Y, Li HY, Jiang HF, et al. Artificial neural network modelling to predict hot deformation behaviour of zinc–aluminium alloy. Mater Sci Technol. 2013;29(2):184–189. doi: 10.1179/1743284712Y.0000000127
- Zhu YC, Zeng WD, Sun Y, et al. Artificial neural network approach to predict the flow stress in the isothermal compression of as-cast TC21 titanium alloy. Computational Materials Science. 2011;50(5):1785–1790. doi: 10.1016/j.commatsci.2011.01.015
- Sheikh H, Serajzadeh S, Mater J. Estimation of flow stress behavior of AA5083 using artificial neural networks with regard to dynamic strain ageing effect. Process Technol. 2008;196(1–3):115–119. doi: 10.1016/j.jmatprotec.2007.05.027
- Lin YC, Zhang J, Zhong J. Application of neural networks to predict the elevated temperature flow behavior of a low alloy steel. Comput Mater Sci. 2008;43(4):752–758. doi: 10.1016/j.commatsci.2008.01.039
- Zhao JW, Ding H, Zhao WJ, et al. Modelling of the hot deformation behaviour of a titanium alloy using constitutive equations and artificial neural network. Comput Mater Sci. 2014;92:47–56. doi: 10.1016/j.commatsci.2014.05.040
- Quan GZ, Lv WQ, Mao YP, et al. Prediction of flow stress in a wide temperature range involving phase transformation for as-cast Ti–6Al–2Zr–1Mo–1V alloy by artificial neural network. Mater Des. 2013;50:51–61. doi: 10.1016/j.matdes.2013.02.033
- Quan GZ, Yu CT, Liu YY, et al. A comparative study on improved Arrhenius-type and artificial neural network models to predict high-temperature flow behaviors in 20MnNiMo alloy. Sci World J. 2014;2014:1–12. doi: 10.1155/2014/108492
- Zhao JW, Ding H, Zhao WJ, et al. Modelling of the hot deformation behaviour of a titanium alloy using constitutive equations and artificial neural network. Comput Mater Sci. 2014;92:47–56. doi: 10.1016/j.commatsci.2014.05.040
- Sun Y, Zeng WD, Zhao YQ, et al. Modeling constitutive relationship of Ti40 alloy using artificial neural network. Mater Des. 2011;32(3):1537–1541. doi: 10.1016/j.matdes.2010.10.004
- Gupta AK, Singh SK, Reddy S, et al. Prediction of flow stress in dynamic strain aging regime of austenitic stainless steel 316 using artificial neural network. Mater Des. 2012;35:589–595. doi: 10.1016/j.matdes.2011.09.060
- Xiao X, Liu GQ, Hu BF, et al. A comparative study on Arrhenius-type constitutive equations and artificial neural network model to predict high-temperature deformation behaviour in 12Cr3WV steel. A Comput Mater Sci. 2012;62:227–234. doi: 10.1016/j.commatsci.2012.05.053
- Bariani PF, Bruschi S, Dal Negro T, et al. Prediction of nickel-base superalloys’ rheological behaviour under hot forging conditions using artificial neural networks. Process Technol. 2004;152(3):395–400. doi: 10.1016/j.jmatprotec.2004.04.416
- Toros S, Ozturk F. Flow curve prediction of al–mg alloys under warm forming conditions at various strain rates by ANN. Appl Soft Comput. 2011;11(2):1891–1898. doi: 10.1016/j.asoc.2010.06.004
- Quan GZ, Wang T, Li YL, et al. Artificial neural network modeling to evaluate the dynamic flow stress of 7050 aluminum alloy. J Mater Eng Perform. 2016;25(2):553–564. doi: 10.1007/s11665-016-1884-z
- Yan LM, An D, Shi G, et al. A comparative study of constitutive and neural network models for flow behavior of mg-5.9Zn-1.6Zr-1.6Nd-0.9Y alloy and processing maps. J Mater Eng Perform. 2017;26(5):2368–2376. doi: 10.1007/s11665-017-2643-5
- Kappatos V, Chamos AN, Pantelakis SG. Assessment of the effect of existing corrosion on the tensile behaviour of magnesium alloy AZ31 using neural networks. Mater Des. 2010;31(1):336–342. doi: 10.1016/j.matdes.2009.06.009
- Ning H, Li X, Meng L, et al. Effect of Ni and Mo on microstructure and mechanical properties of grey cast iron. Mater Technol Adv Perform Mater. 2023;38(1):2172991. doi: 10.1080/10667857.2023.2172991
- Misra RDK, Challa VSA, Injeti YS. Phase reversion-induced nanostructured austenitic alloys: an overview. Mater Technol Adv Perform Mater. 2022;37(7):437–449. doi: 10.1080/10667857.2022.2065621
- Guo L, Su X, Dai L, et al. Strain ageing embrittlement behaviour of X80 self-shielded flux-cored girth weld metal. Mater Technol Adv Perform Mater. 2023;38(1):2164978. doi: 10.1080/10667857.2023.2164978
- Li SF, Misra RDK, Liu ZQ. Towards strength-ductility synergy in nanosheets strengthened titanium matrix composites through laser power bed fusion of MXene/Ti composite powder. Mater Technol Adv Perform Mater. 2023;38(1):2181680. doi: 10.1080/10667857.2023.2181680
- Niu G, Zurpb H, Guyuen M, et al. Superior fracture toughness in a high-strength austenitic steel with heterogeneous lamellar microstructure. Acta Mater. 2022;226:117462. doi: 10.1016/j.actamat.2022.117642
- Yang C, Xu H, Wang Y, et al. Hot tearing analysis and process optimisation of the fire face of al-cu alloy cylinder head based on MAGMA numerical simulation. Mater Technol: Adv Perform Mater. 2023;38(1):2165245. doi: 10.1080/10667857.2023.2165245
- Li Q, Zuo H, Feng J, et al. Strain rate and temperature sensitivity on the flow behaviour of a duplex stainless steel during hot deformation. Mater Technol: Adv Perform Mater. 2023;38(1):2166216. doi: 10.1080/10667857.2023.2166216
- Misra RDK. Strong and ductile texture-free ultrafine-grained magnesium alloy via three-axial forging. Mate Lett. 2023;31:133443. doi: 10.1016/j.matlet.2022.133443
- Misra RDK. Enabling manufacturing of multi-axial forging-induced ultrafine-grained strong and ductile magnesium alloys: a perspective of process-structure-property paradigm. Mater Technol Adv Perform Mater. 2023;38(1):2189769. doi: 10.1080/10667857.2023.2189769
- Lin YC, Chen M-S, Zhong J. Constitutive modeling for elevated temperature flow behavior of 42CrMo steel. Comp Mater Sci. 2008;42(3):470–477. doi: 10.1016/j.commatsci.2007.08.011
- Pu ZJ, Wu KH, Shi J, et al. Development of constitutive relationships for the hot deformation of boron microalloying TiAl?Cr?V alloys. Mater Sci Eng A. 1995;192:780–787. doi: 10.1016/0921-5093(94)03314-5
- Slooff FA, Zhou J, Duszczyk J, et al. Constitutive analysis of wrought magnesium alloy mg–Al4–Zn1. Scripta Mater. 2007;57(8):759–762. doi: 10.1016/j.scriptamat.2007.06.023
- Haghdadi N, Zarei-Hanzaki A, Abedi HR. The flow behavior modeling of cast A356 aluminum alloy at elevated temperatures considering the effect of strain. Mater Sci Eng A. 2012;535:252–257. doi: 10.1016/j.msea.2011.12.076