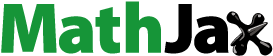
ABSTRACT
In order to achieve in-service safety evaluation of girth weld, property prediction of X80 self-shielded flux-cored girth weld metal based on strain ageing kinetics was conducted. Strength increment (ΔY) and toughness reduction (ΔCVN) relationship was obtained through tensile and Charpy impact test using specimens before and after strain ageing. 1% prestrain was conducted and then aged at different conditions (150°C/100°C for 1–6 h, 80°C/50°C for 1–120 days). Strain ageing kinetics was investigated based on experiment results, and diffusion activation energy (Q) was calculated as 88.1 kJ/mol. The correlation equation of ageing temperature and period was obtained: , T1<T2 <423 K. It is predicted that, since occurrence of 1% prestrain, toughness of girth weld metal would drop down to <80 J after 3.9 years service in the present case, and its service safety should be reconsidered. Other prediction should be based on experimental results of specific consumable and welding parameters.
Introduction
High strength pipeline steels, i.e. X70 and X80, were widely used in the construction of long distance gas transportation pipeline projects in order to elevate the transportation capacity as well as lower the cost [Citation1–3]. As we all know, materials forming technologies, i.e. welding, casting, forging, etc., are of significant to the microstructure, property as well as service safety for the structure [Citation4–7]. Welding is one of the most important procedures during pipeline construction which is virtual to the life cycle (usually more than 50 years) safety of the project. Safety of the girth welds is considered to be the lifeline of the high strength pipeline projects, especially after the occurrence of several exploding accidents, i.e. Myanmar-China Oil & Gas Pipeline Project accident in 2017 and 2018, induced by brittle fracture of girth weld metal [Citation8,Citation9].
Strain ageing embrittlement of high strength pipeline girth weld attracted more attention in recent years [Citation10,Citation11], because strain ageing is very likely to take place during the lifelong service of the pipelines. For the high strength pipelines, under matched weld joint were frequently found during the field welding due to the strength scattering of the base metal. Our previous research showed that the under matched weld joint is more prone to sustain strain concentration [Citation12] when geological movement (subsidence, landslide, earthquake, etc.) occurred or multiple stresses were coupled, which fulfils the ‘strain’ precondition for ‘strain-aging’. And, long period service ensures ageing time. Therefore, the girth weld joint may suffer from toughness deterioration induced by strain ageing.
It is widely accepted that strain ageing is caused by interaction of interstitial atoms (i.e. carbon and/or nitrogen) and dislocations [Citation13,Citation14]. The strain ageing process is usually accompanied by strength increment and toughness loss due to Cottrell atmosphere pining [Citation15–18]. Especially, due to poor protection condition of molten pool, the weld metal dissolves more nitrogen [Citation8,Citation19]. Therefore, the weld metal is more sensitive to strain ageing embrittlement, which is detrimental to the service safety of high strength pipelines. The weld metal of self-shielded flux-cored arc welding (FCAW), which was widely used in large scale construction of pipelines in China in the past decades, is more sensitive to strain ageing embrittlement due to higher nitrogen content up to 250–300 ppm [Citation20]. Previous research showed that influencing factors of strain ageing embrittlement include content of dissolved carbon and nitrogen [Citation21], type of microstructure [Citation22,Citation23], strain level [Citation24] and ageing temperature & period [Citation25].
In our previous research, strain ageing embrittlement behaviour of X80 FCAW girth weld metal was systematically studied [Citation26]. Meanwhile, strain ageing is a diffusion controlled process, and the relationship of ageing temperature and ageing period obeys the rule described by Arrhenius equation [Citation27]. Therefore, the in-service property of the girth weld metal can be predicted based on strain ageing kinetics and the accelerated test results with higher temperature and shorter ageing time in the laboratory [Citation28]. Strain ageing kinetics of steels was widely studied, however, corresponding research in weld metal was rarely reported. In the present paper, the in-service property prediction of X80 FCAW girth weld metal based on strain ageing kinetics was conducted through the mechanical property evolution during strain ageing at different strain ageing conditions. This work could be a guide for safety assessment of high strength in-service pipelines.
Experimental methods
Materials and welding method
The material used here for strain ageing study is weld metal of X80 FCAW girth weld. The pipe of Φ1219 mm × 18.4 mm was used to fabricate the girth weld. Surface tension transfer (STT) welding was used for root weld, using BOHLER SG3-P welding wires. FCAW was used for hot, filling and cap welding passes, using HOBART 81N1 welding wires. All the welding parameters were set according to the welding procedure specifications of West-East III project [Citation29], which was most frequently used during large scale construction of high strength (X70, X80) pipelines.
Test method
All-weld-metal tension test specimens were machined along girth weld seam, and the location and specimen size are presented in . The specimens were machined 3 mm below the outer surface to ensure only weld metal of filling passes (major part of the girth weld join) were contained in the specimen, avoiding gap pass and hot pass, within which the thermal history and corresponding microstructure are notably different from filling passes. Prestrain was conducted using slow strain rate tensile test machine (Letry WDML-5), with strain rate of 0.0045 mm/s. When the strain reached 1.5%, the prestrain was stopped, and the plastic strain was considered to be 1% since Rt0.5 is the most frequently used yield strength index in the industry. After prestrain, the specimens were aged at different temperatures (50°C–150°C) for varied period (0.5 h–120 days). The detailed ageing parameters are listed in . Tensile tests were conducted using specimens before and after strain ageing, in order to reveal the strength variation induced by strain ageing strengthening.
Table 1. Aging temperature and period for the strain aging.
Through thickness tensile test was performed for the prestrain of strain ageing samples on WDW-600 test machine. The schematic of tensile specimen is presented in according to GBT228.1-2010 standard. During prestrain, extensometer with length of 30 mm was used to monitor the strain of weld joint. Tensile was stopped when the total strain reached 1.5%, demonstrating 1% plastic strain was sustained in the weld metal. After prestrain, the through thickness specimen was milled to V-notched Charpy impact test (CVN) specimen (10 mm × 10 mm × 55 mm) according to . CVN specimens were then aged at 150°C/100°C for 1–6 h, 80°C for 1–30 days and 50°C for 15–120 days, and finally impact tests were performed at −10°C using CTS-I450 impact test machine.
Prediction method based on strain aging kinetics
Since strain ageing by the formation of ‘Cottrell atmospheres’ is diffusion controlled, the time and temperature required for producing any change in mechanical properties is in accordance with the relationship depicted by Arrhenius equation [Citation14]:
where: t = time for strain ageing to reach a certain stage; A = constant; Q = activation energy for strain ageing, kJ/mol; T = absolute temperature, K; R = gas constant, 8.314 J/(mol·K).
EquationEquation (1)(1)
(1) (can be rewritten as:
And, then the following relationship can be developed based on EquationEquation (2)[2]
[2] :
All variables in EquationEquation (3)[3]
[3] , except the activation energy Q, are known. And, activation energy Q can be determined by conducting series of tensile tests under different ageing temperature-period conditions. Mechanical property variation before and after stain ageing can be determined according to the method depicted in Ref. [Citation15]. Yield strength increment (ΔY) was considered to better characterize the strain ageing behaviour of metals, compared to tensile strength increment (ΔU) and decrease of total elongation (ΔE) induced by strain ageing. In order to avoid the influence of property variation between different specimens, ΔY was determined via comparing the tensile curves of the same specimen before and after strain ageing in the present paper, and the schematic is presented in . Value of Q/R can be determined by fitting of ΔY & ageing temperature/period curves, and hence Q can be calculated.
Figure 3. Schematic of calculation method of ΔY [Citation15].
![Figure 3. Schematic of calculation method of ΔY [Citation15].](/cms/asset/44c31534-ffa6-420f-be94-db8274256a2a/ymte_a_2271305_f0003_b.gif)
Once activation energy Q was determined, the mechanical property of the in-service girth weld could be predicted through EquationEquation (3)[3]
[3] and the coupled correlation of tensile and CVN test results, which will be discussed in detail in the following sections. The precondition for the above mentioned prediction method is that the diffusion mechanism stays unchanged during the ageing temperature variation. In the present case, strain ageing of girth weld during service condition is mainly induced by N because the service temperature of buried pipelines is around ambient and earth temperature. Therefore, the top temperature in the present case is 150°C in order to prevent the influence of C induced strain ageing or nitride precipitation at temperature higher than 150°C [Citation14,Citation30].
Results and discussions
Mechanical property variations
Strain aging strengthening behavior
The yield strength increment (ΔY) of girth weld metal after 1% prestrain and aged at different temperature for varied period is summarized in . According to the data in , ΔY gradually increased with the increasing ageing period or higher ageing temperature, which demonstrates that the progression of diffusion controlled strain ageing strengthening process induces sustaining property variation. For example, after aged at 150°C for 0.5 h, average ΔY is 50.4 MPa, while aged for 1 and 3 h, ΔY increased to 75.4 and 84.9 MPa. With lower ageing temperature, longer ageing period is needed to reach similar strength increment. Meanwhile, ΔY tends to be stable (around 80–90 MPa) when the strain ageing is sufficiently proceeded, i.e. 100°C aged for 6 h, 80°C aged for 7 days and 50°C aged for 120 days. It should be pointed out that scattering of strength or toughness data of FCAW girth weld was frequently found, because the stability of welding process is easily influenced by the homogeneity of flux core and welding spatter, and hence microstructure of weld metal at different locations varied during fabrication. Since the tensile test results are more stable than Charpy impact toughness, strength increment (ΔY) was used to evaluate the extent of strain ageing process.
Table 2. Yield strength variations before and after strain ageing.
All the above data were plotted in , and the trend of strength variation during different strain ageing process could be clearly presented. And, the strain ageing kinetics could be studied based on these curves through calculating equivalent ageing time which induced similar ΔY at different ageing temperatures, and this will be discussed in the following sections.
Strain aging embrittlement behavior
The variation of Charpy impact toughness of girth weld metal after 1% prestrain and aged at different temperature for varied period is summarized in . The toughness of as-welded FCAW weld metal samples is also enclosed for comparison. The results showed that the original toughness of the as-welded FCAW weld metal is good (158.8 J), and with the progress of strain ageing process, the CVN absorbed energy notably decreased. For example, 150°C ageing for 3 h, 100°C ageing for 6 h, 80°C ageing for 30 days and 50°C ageing for 120 days all induced low toughness of ~60 J (ΔCVN around −98 J), which demonstrates that when the ageing process is fully yielded the toughness also dropped to a certain level and kept steady, i.e. around 60 J in the present case. The detailed strain ageing embrittlement behaviour of X80 FCAW girth weld metal was systematically discussed in our previous publication [Citation26]. The toughness data presented here is for the prediction of in-service properties based on strain ageing kinetics in the following section.
Table 3. Charpy impact toughness variations before and after strain ageing.
Correlation of strength and toughness variation during strain aging
The variation of strength and CVN absorbed energy of girth weld metal during strain ageing is plotted in , using the original data listed in . It can be clearly found that the strength increment (ΔY) and toughness loss (ΔCVN) has obvious positive correlation. Therefore, it is reasonable to implement the in-service property prediction based on the strain ageing kinetic and ΔY-ΔCVN correlation.
Strain aging kinetics
The critical CVN absorbed energy in the specification of West-East Pipeline Project No. 2 and No. 3 is 80 J for minimum average and 60 J for minimum single. Therefore, 80°C ageing for 3 days was chosen as the critical ageing condition in the present case, because its average CVN absorbed energy is 80.1 J () which is nearly equal to the required value. And hence, the ΔY at this condition, which is 70.3 MPa (), was chosen as the critical strength increment for the property prediction of girth weld at in-service ageing condition. Namely, once the ΔY at certain ageing condition reached 70.3 MPa, it is believed that its corresponding toughness dropped below the critical value (80 J) and hence the service safety of the girth weld joint needs to be reconsidered.
The 83.7 MPa line is plotted as the dotted horizontal line in , and its intersecting points with ΔY versus ageing time curves were obtained, which represent the time which produced the same ΔY at different ageing conditions. The values of the intersecting points were plotted in the form of lg t versus 1/T as presented in . According to EquationEquation (3)[3]
[3] , if the strain ageing mechanism or namely diffusion mechanism were not varied at these ageing conditions, the plot of lg t versus 1/T should be a straight line. And, the slope of the straight line is therefore equal to Q/R. According to the fitting results of , Q/R was calculated to be 10,597.4, and hence Q was calculated to be 88.1 kJ/mol, which is similar to the previous reported data [Citation14,Citation15,Citation21]. Also, the equivalent ageing time relationship could be obtained by substituting Q/R in EquationEquation (3)
[3]
[3] as following:
EquationEquation (4)[4]
[4] can be used for predicting equivalent strain ageing time at different ageing temperatures, i.e. in-service temperature 20°C. Substituting T1 = 20°C (253 K), T2 = 80°C (193 K), t2 = 3 days into EquationEquation (4)
[4]
[4] , the equivalent ageing time for the girth weld at service temperature can be calculated to be 2,013,062.9 min, which is about 3.9 years. Namely, since the occurrence of 1% prestrain, the toughness of the X80 FCAW girth weld metal (HOBART 81N1 welding wires) would drop down <80 J after 3.9 years service, and its service safety should be reconsidered. It should be noted that since strain ageing is sensitive to chemical content, microstructure and strain level, property prediction on other girth weld should be based on the similar experimental results as above on specific consumable and welding parameters.
Conclusions
In the present paper, the in-service property prediction of X80 FCAW girth weld metal based on strain ageing kinetics was conducted, with condition of 1% prestrain and aged at different conditions (150°C/100°C ageing for 1 h–6 h, and 80°C/50°C for 1–120 days). The following conclusions can be obtained:
With the progression of strain ageing process, strength increment (ΔY) and toughness reduction (ΔCVN) relationship was obtained through tensile test and Charpy impact test using the specimen before and after strain ageing.
The strain ageing kinetics was studied based on the experiment results, and the diffusion activation energy (Q) was calculated to be 88.1 kJ/mol in the present case. The correlation equation of ageing temperature and ageing period was obtained:
, T1<T2 <423 K.
It is predicted that, since the occurrence of 1% prestrain, the toughness of the X80 FCAW girth weld metal (HOBART 81N1 welding wires) would drop down to <80 J after 3.9 years service, and its service safety should be reconsidered. The prediction here is only suitable for present case, any other property prediction should be based on the experimental results of specific consumable and welding parameters.
Acknowledgments
The authors wish to acknowledge the financial support from the project of “National Defense Science and Technology Innovation Special Zone Project” (No. 22-05-CXZX-04-04-29) and “Research on failure mechanism for girth weld of high steel pipeline” (NO.WZXGL202105).
Disclosure statement
No potential conflict of interest was reported by the authors.
References
- Cui TC, Zheng L, Wu HF. Effect of strain aging on mechanical properties of high strength pipeline steel with different composition. Mater Mech Eng. 2010;34(5):30–32+55.
- Park HS, Kang JS, Yoo JY, et al. In situ TEM and APT analysis on the dislocations associated with solute carbons in strain-aged low carbon pipeline steels. Mater Sci Forum. 2010;654:122–8. doi: 10.4028/www.scientific.net/MSF.654-656.122
- Zhao WG, Chen M, Chen SH, et al. Static strain aging behavior of an X100 pipeline steel. Mater Sci Eng A, 2012, 550: 418–422.
- Ning H, Li X, Meng L, et al. Effect of Ni and Mo on microstructure and mechanical properties of grey cast iron. Mater Technol. 2023;38(1):2172991. doi: 10.1080/10667857.2023.2172991
- Li Q, Zuo H, Feng J, et al. Strain rate and temperature sensitivity on the flow behaviour of a duplex stainless steel during hot deformation. Mater Technol. 2023;38(1):2166216. doi: 10.1080/10667857.2023.2166216
- Niu G, S ZH, K MRD, et al. Superior fracture toughness in a high-strength austenitic steel with heterogeneous lamellar microstructure. Acta Materialia. 2022;226:117642. doi: 10.1016/j.actamat.2022.117642
- Misra RDK, Challa VSA, Injeti VSY. Phase reversion-induced nanostructured austenitic alloys: an overview. Mater Technol. 2022;37(7):437–449. doi: 10.1080/10667857.2022.2065621
- Wang HK, Shang XX, Liu W, et al. Study on strain aging embrittlement of girth weld of high grade oil and gas pipeline. Pressure Vessel Technol. 2021;38(5):8–13.
- Isnarti R. The potential threat of China-myanmar gas pipeline. AEGIS: J Int Relat. 2017;1(2). doi: 10.33021/aegis.v2i2.425
- Lee S, Hwang B. Correlation of microstructure with tensile behavior and properties of API X70 pipeline steels subjected to strain aging. J Iron And Steel Res Int. 2020;27(3):319–324. doi: 10.1007/s42243-019-00313-y
- Zhukov D, Konovalov S, Afanasyev A. Morphology and development dynamics of rolled steel products manufacturing defects during long-term operation in main gas pipelines. Eng Fail Anal. 2020;109:104359. doi: 10.1016/j.engfailanal.2019.104359
- Xu LL. Research on the effect of strength matching on root cracking of girth weld of high-strength pipelines [D]. Qingdao, China: China University of Petroleum (East China); 2023.
- Cottrell AH, Bilby BA. Dislocation theory of yielding and strain aging of iron. Proc Phys Soc A. 1949;62(1):49–62. doi: 10.1088/0370-1298/62/1/308
- Baird JD. The effects of strain-ageing due to interstitial solutes on the mechanical properties of metals. Metallurgical Review. 1971;16(1):1–18. doi: 10.1179/mtlr.1971.16.1.1
- Rashid MS. Strain-aging of vanadium, niobium or titanium-strengthened high-strength low-alloy steels. Metall Trans A. 1975;6(7):1265–1268. doi: 10.1007/BF02658536
- K NB, Brady N, Y WY, et al. Effect of strain ageing on yield strength and post yield behavior of FCAW-G ferritic weld metal. International Pipeline Conference; Calgary, Canada, 2010: 569–576.
- Liang GC, Peng X, Juan ES, et al. Strain aging of X100 steel in service and the enhanced susceptibility of pipelines to stress corrosion cracking. J Materi Eng And Perform. 2013;22(12):3778–3782. doi: 10.1007/s11665-013-0683-z
- Li Y, Chi Q, Feng H, et al. Effect of strain aging on properties of X90 line pipe. Eng Fail Anal. 2020;118:104844. doi: 10.1016/j.engfailanal.2020.104844
- Kakovkin OS, Pen’kov VB. Special features of absorption of nitrogen by metal in arc welding. Welding International. 1988;2(1):42–44. doi: 10.1080/09507118809451128
- Yu P, Tian ZL, Pan C, et al. Gas in weld of self shielded flux cored wire. Trans China Weld Inst. 2007;28(2):67–70.
- Achar DRG, Koçak M, Evans GM. Effect of nitrogen on toughness and strain age embrittlement of ferritic steel weld metal. Sci Tec Weld Joining. 1998;3(5):233–243. doi: 10.1179/stw.1998.3.5.233
- Mcconnell P, Hawbolt EB. A strain age study of acicular ferrite X-70 pipeline steels. J Mater Energy Sys. 1979;1(2):25–31. doi: 10.1007/BF02833975
- Patrocínio AB, Novovic M, Bowen P. Effect of prestraining and strain-aging on toughness of MnMoNi steel weld metal. J Mater Process Technol. 2004;155-116:1124–1131. doi: 10.1016/j.jmatprotec.2004.04.285
- Wu X. Strain-aging behavior of X100 line-pipe steel for a long-term pipeline service condition [D]. Calgary, Canada: University of Calgary; 2010.
- Yang J, Bi ZY, Nan HH, et al. Strain aging behavior and sensitive temperature of X90 high strength pipeline steel. Chin J Mater Res. 2021;35(10):769–777.
- Guo L, Su X, Dai L, et al. Strain ageing embrittlement behaviour of X80 self-shielded flux-cored girth weld metal. Mater Technol. 2023;38(1):2164978. doi: 10.1080/10667857.2023.2164978
- Rashid MS. Strain aging kinetics of vanadium or titanium strengthened high-strength low-alloy steels. Metall Trans A. 1976;7(4):497–503. doi: 10.1007/BF02643965
- Rashid MS. Strain-aging of vanadium, niobium or titanium-strengthened high-strength low-alloy steels. Metall Trans A. 1975;6(6):1265–1268. doi: 10.1007/BF02658536
- Sui YL. Current situation and development trend of girth welding technology for oil and gas pipeline. Electr Weld Mach. 2020;50(9): 53–59. In Chinese.
- Herman WA. SA of micro-alloyed steels. Welding Research Council Bulletin. 1987;322:1–13.