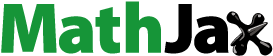
ABSTRACT
The perspective presented here underscores the part played by grain size, grain boundary chemistry and substructural features such as martensite lath and packet size in determining the fracture toughness of high strength iron-based metallic materials. Each of these features influences the degree of plasticity. The notion of grain boundary segregation isotherms and thermodynamics related to the systems is explained, along with the effects on toughness of segregation of alloying elements to grain boundaries in complex alloy systems, specifically precipitation hardened ferrous alloys and maraging steels. The extensive review of experimental metal processing technology has provided a means of analysing the relationship of toughness to microstructural features. Important instances include maraging steels, precipitation hardened stainless steels, low alloy steels, interstitial-free steels, and microalloyed steels.
Background
Significant advancements in materials science and technology over the past few years have made it possible to build materials that can adhere to strict specifications and satisfy the environment in which they are anticipated to function dependably. In this sense, a combination of great strength and high toughness [Citation1–9] is the most important aspect that continues to be of noteworthy interest. The underlying reason is that there is a continued push to reduce the weight of the component by increasing the strength without sacrificing ductility and toughness. While significant technological advances have been made in materials processing, but the motivation to recycle scrap leads to minimize cost and preserve natural resources leads to a situation where impurity elements that are detrimental to the inherent properties of engineering materials are unavoidable. With this as the background, an attempt is made to describe instances where the aim was to obtain the desired mechanical properties through a comprehensive and mechanistic understanding of scientific phenomena. Depending on the type of material and the technology used to produce it, microstructural control can permit the combination of high strength and high toughness in a variety of ways. New ideas that emerged because of better understanding of the variables that control toughness at particular strength levels are also illustrated. The examples described below from author’s extensive work in this field in diverse engineering metals and alloys underscore the significance of controlling different aspects in the attempt to obtain high toughness without comprising strength.
Ultrahigh strength maraging steels
Maraging steel is a class of ultrahigh strength steel with very low carbon content (0.03 wt.% max) with high content of Ni, Co and Mo and is used for strategic applications as a structural material [Citation10,Citation11]. The widely used solution annealing-ageing treatment consists of solution treatment at 820°C for 1 h/25 mm section thickness followed by air cooling and ageing at 480°C for 3 h. During processing, substantial data on the fracture toughness (KIC) and grain size were generated and are presented in [Citation10,Citation11]. The specified heat treatment in heavy forging structural product with non-uniform cross-section did not result in the required fracture toughness, KIC of 90 MPa m1/2.
Figure 1. Effect of heat treatment temperature (time 1 h) on KIC and grain size of maraging steel (250) (Bars indicate the range over which KIC and grain size values were measured at a particular temperature (adapted from reference [Citation10,Citation11]).
![Figure 1. Effect of heat treatment temperature (time 1 h) on KIC and grain size of maraging steel (250) (Bars indicate the range over which KIC and grain size values were measured at a particular temperature (adapted from reference [Citation10,Citation11]).](/cms/asset/54d51e17-8345-45f3-bbad-cdef25cbeb3d/ymte_a_2278000_f0001_b.gif)
A coarse grain size and well-developed precipitate network were formed at the grain boundary by the solution treatment. The presence of large grains suggested that recrystallization was incomplete at this temperature. The thermal treatment in the range 850–950°C refined the grain size (average ~40 µm) but failed to improve KIC simultaneously. However, the previous coarse grain boundaries were still marked by a precipitate network. Heat treatment at temperatures greater than 950°C led to coarsening of grains (100 µm) as expected, but the microstructure did not reveal the presence of any precipitate network and in fact indicated improvement in KIC. These observations implied that fine grain size by itself is not sufficient to ensure high KIC in this steel and that the precipitate network influences KIc deleteriously. Auger electron spectroscopy studies suggested the cause of low fracture toughness in the presence of duplex Ti2(CS)x/TiC precipitates at the grain boundaries, which can be referred to as thermal embrittlement [Citation11].
To achieve the requisite fracture toughness, it was suggested to dissolve the grain boundary precipitates at higher temperatures. This idea made sense in light of the fracture topography research. The standard solution treatment at 820°C resulted in a transgranular fracture mode () [Citation10,Citation11]. However, some areas indicated the presence of a pattern of straight ridges mapping out a set of crystallographic directions, while the heat treatment at 925°C, which yielded the lowest KIC of 70 MPa m1/2 gave predominantly intergranular fracture (). High magnification fractographs exhibited complicated surface topography indicating that some local tearing was involved. The fractograph of the sample heat treated at 1125°C and water quenched showed that the fracture mode was transgranular with well-pronounced dimples (). The average areal density of precipitates was considerably less (~1.2%), which is in accordance with the expectations that at temperatures >970°C, carbides tend to dissolve. For the same reason, the material also exhibits a high degree of toughness. It was concluded that the variation in KIC () [Citation10,Citation11] is due to variation in precipitate areal density (), which controls the fracture toughness and the mode of fracture [Citation10,Citation11].
Figure 2. Variation of KIC and atomic% titanium on fracture surface with heat treatment temperature (adapted from reference [Citation10,Citation11]).
![Figure 2. Variation of KIC and atomic% titanium on fracture surface with heat treatment temperature (adapted from reference [Citation10,Citation11]).](/cms/asset/941aafb1-2e84-418f-8b3f-50c523c93156/ymte_a_2278000_f0002_b.gif)
The precipitation at the grain boundary had an adverse impact on fracture toughness. Furthermore, the presence of grain boundary precipitates created a macroscopically continuous fracture path, although the fracture is of mixed mode type on the microscopic scale and consists of quasi-cleavage and dimple rupture, as schematically represented in [Citation10,Citation11].
Figure 3. Schematic representation of fracture process in steel with grain boundary TiC carbides (adapted from reference [Citation10]).
![Figure 3. Schematic representation of fracture process in steel with grain boundary TiC carbides (adapted from reference [Citation10]).](/cms/asset/d22b782b-b06c-48b8-89f4-786298924607/ymte_a_2278000_f0003_b.gif)
Another approach suggested was to adopt a three-stage heat treatment of 820°C + 950°C + 820°C [Citation12]. This approach led to serrated grain boundaries pinned by fine precipitates and fine sub-divided martensite. A summary of observations is presented in [Citation12].
Figure 4. Effect of anneal sequence on grain boundary precipitates (adapted from reference [Citation12]).
![Figure 4. Effect of anneal sequence on grain boundary precipitates (adapted from reference [Citation12]).](/cms/asset/44695514-3576-4c66-92fd-040804526f12/ymte_a_2278000_f0004_oc.jpg)
Figure 5. Effect of anneal sequence on martensite lath size (adapted from reference [Citation12]).
![Figure 5. Effect of anneal sequence on martensite lath size (adapted from reference [Citation12]).](/cms/asset/c30914ea-ca08-4efe-a565-0c7db22dbde0/ymte_a_2278000_f0005_b.gif)
Figure 6. Summary of the effect of heat treatment on microstructure based on transmission electron microscopy studies (adapted from reference [Citation12]).
![Figure 6. Summary of the effect of heat treatment on microstructure based on transmission electron microscopy studies (adapted from reference [Citation12]).](/cms/asset/0e44fd4c-d500-4cf1-9a92-ec40890f2202/ymte_a_2278000_f0006_oc.jpg)
Precipitation-hardened martensitic stainless steels
In another instance of 17Cr-4Ni precipitation-hardened stainless steel, used in applications requiring superior mechanical properties combined with corrosion resistance [Citation12–16], there was striking variation in impact toughness with bulk % carbon-content for identical heat treatment. Although the tensile properties, yield strength (1075–1115 MPa), and % reduction in area (53–64%) were consistent, the impact toughness varied over a wide range from 5 to 120 Nm for fixed bulk Nb-content of 0.28 wt% () [Citation13,Citation14].
Figure 7. Impact toughness, and intergranular atomic % C and P and ΔGo [P] and ΔGo [C] as a function of bulk weight % C (also Nb/C ratio) in 17–4 precipitation hardened stainless steel [Citation10,Citation13,Citation14].
![Figure 7. Impact toughness, and intergranular atomic % C and P and ΔGo [P] and ΔGo [C] as a function of bulk weight % C (also Nb/C ratio) in 17–4 precipitation hardened stainless steel [Citation10,Citation13,Citation14].](/cms/asset/9d97187f-567a-4bf7-a773-40b73b409e58/ymte_a_2278000_f0007_b.gif)
The strong dependence of impact toughness with bulk C-content was explained in terms of Nb-C and Nb–P interactions [Citation10,Citation13,Citation14]. It was believed that, with the increase in bulk C-content, the grain boundary concentration of P would increase, because more and more Nb gets tied-up with C as NbC, and less is available to interact with P to form NbP. NbP chemical interaction either in the form of clusters or precipitates is most likely to occur during ageing. This allowed grain boundary segregation of P to increase with bulk C-content. Phosphorus segregation was a maximum at a C-concentration of ~0.035%, corresponding approximately to the value necessary to precipitate all of the Nb as NbC with no Nb being available for interaction with P. The presence of free or excess C () in steel compositions with C-contents higher than 0.035% successfully displaced P from the grain boundary through a P-C, site-competitive process and further improved grain boundary cohesion. Thus, interactions of the type Nb-P and Nb-C were invoked to explain striking variation in the impact toughness in precipitation hardened stainless steels. One can, in fact, delineate the data presented in into two distinct regimes: (a) a low toughness regime (Nb/C ratio >6 but less than, say, 20) characterized by high grain boundary concentration of phosphorus and NbC formation owing to strong Nb–C interaction, (b) a high toughness regime (Nb/C <6), where grain boundary P is displaced by C through site competition. This segregation of C has two important effects: it alleviates the harmful effect of P and enhances grain boundary cohesion. Thus, the Nb/C ratio played an important role in influencing toughness () [Citation13,Citation14]. It is important to note that even though elements Nb and C in the steel may be within the specified range, it is the ratio that is more important as far as the property requirement is concerned () [Citation10].
Figure 8. Significance of Nb/C ratio in 17–4 precipitation hardened stainless steel to obtain desired toughness (adapted from reference [Citation10]).
![Figure 8. Significance of Nb/C ratio in 17–4 precipitation hardened stainless steel to obtain desired toughness (adapted from reference [Citation10]).](/cms/asset/33f0c27d-7899-452e-9cd3-cfaa1cede710/ymte_a_2278000_f0008_b.gif)
The rate of cooling after ageing step, water quenching, in lieu of normal air-cooling practice influenced impact toughness. For both adverse and favourable ratios, resulted in 30–40% increase in toughness resulted in insignificant loss in strength of ~ 2–3%. The steel that was prone to grain boundary embrittlement by P was eliminated () [Citation16].
Figure 9. The effect of post-aging quenching treatment on impact toughness of 17Cr-4Ni precipitation hardened stainless steels (adapted from reference [Citation16]).
![Figure 9. The effect of post-aging quenching treatment on impact toughness of 17Cr-4Ni precipitation hardened stainless steels (adapted from reference [Citation16]).](/cms/asset/d2489dd1-9d84-431c-b376-c25d402f9db8/ymte_a_2278000_f0009_b.gif)
A thermodynamic analysis in terms of free energy of segregation for the aforementioned two regimes was attempted [Citation10,Citation17] using Langmuir-McLean equation [Citation18] and Rice and co-workers thermodynamic framework [Citation19]. The first regime, which was characterized by low impact toughness and grain boundary segregation of P, the grain boundary segregation free energy of phosphorus was obtained from:
where θP is the grain boundary concentration of phosphorus, xb[P] is the bulk concentration of phosphorus, ΔG°b[P] is the segregation free energy of phosphorus, R is gas constant, and T is the temperature in Kelvin [Citation10,Citation17].
The values of ΔG°b[P] obtained from Equationequation 1(1)
(1) for regime I after substitution of grain boundary coverage were in the range of 38–49 kJ/mol.
For regime II, which was characterised by grain boundary displacement of P by carbon (site-competition process), Langmuir-McLean equation was written as:
where θc is the grain boundary segregation of C; Xb[C] is the bulk concentration of C; ΔG°b[C] is the grain boundary segregation free energy of carbon. In Equationequations (2)(2)
(2) and (Equation3
(3)
(3) ) it is assumed that there is no energetic interaction between C and P. The values of ΔG°b[P] and ΔG°b[C] were in the range of 33–42 kJ/mol and 60–72 kJ/mol, respectively, in regime II [Citation10,Citation17].
Using Rice and co-workers thermodynamic framework [Citation18–20] for treating the embrittlement of interfaces by solute segregation in terms of the ideal work of interfacial separation, 2γint, where 2γint is conceived to predict the important, if not the exclusive, role in determining the resistance to interfacial embrittlement. Their hypothesis suggests that the control of 2γint is the most effective means of enhancing interracial fracture resistance and that the embrittlement (or ductilization) by impurity solute segregation can be explained in terms of the effect of segregation on 2γint, such that [Citation19,Citation20]
where (2γint)° is the work of separation of the clean interface, Γ is the excess interfacial solute coverage (concentration of segregant per unit area at the interface), and ΔG°b and ΔG°s are the free energies of segregation of the solute to the boundary and free surface respectively, evaluated at the temperature of fracture (taken as 300 K). EquationEquation 4(4)
(4) predicts that a segregating solute with a greater (more negative) segregation energy at a free surface compared to an intemal boundary will embrittle (reduced 2γint), while one with a lower energy at a boundary compared to the free surface will enhance interfacial cohesion (increased 2γint) [Citation19,Citation20]. The results of fracture experiments, which can enable the determination of the change in 2γint as a consequence of solute segregation, were not available. However, the effects of segregants were available in terms of change in ductile – brittle transition temperature (DBTT) brought about by varying embrittling elements. The effects of embrittling elements are reported as a variation δ(DBTT) in DBTT associated with variation in solute coverage, δ Γ and correlated as [Citation10,Citation17]:
where the Ē is the embrittlement sensitivity in Kelvin/atomic % of solute at the grain boundary. The best measure of embrittling sensitivity available is the shift of the intergranular ductile – brittle transition temperature per amount of segregated solute. According to the hypothesis of Rice and co-worker [Citation19,Citation20] solute segregation influences DBTT through its effect on 2γint. Thus, from the above discussion,
In the industrially processed 17–4 PH stainless steels, we did not have the value of DBTT for different heats containing varying carbon content, which would enable us to directly consider Equationequation 6(6)
(6) and apply the thermodynamic hypothesis of Rice and co-workers [Citation19,Citation20] to 17–4 PH stainless steel. However, DBTT was considered to be inversely related to impact toughness, and then we attempted to plot the inverse of the product of impact toughness and atomic % segregant (which can be considered to be representative of embrittlement sensitivity, Ē) as a function of ΔG°b - ΔG°s for different heats corresponding to regimes I and II. We denoted the inverse of the product of impact toughness and atomic % of segregant at the grain boundary as Ē. The plot of Ē as a function of free energy difference, ΔG°b - ΔG°s, is presented in [Citation10,Citation17] for both regimes I and II. In , the range of the observed values of the inverse of the product of impact toughness and atomic % of segregant at the grain boundary and the correponding ΔG°b - ΔG°s range for each of the heats is depicted in the form of a box enclosed by a solid line. This is followed by summarizing the entire data for phosphorus and carbon segregation by broken lines [Citation10,Citation17].
Figure 10. Inverse of the product of impact toughness and atomic % segregant (C or P) as a function of ∆G° b - ∆G° S in 17–4 PH stainless steel (adapted from reference [Citation17]).
![Figure 10. Inverse of the product of impact toughness and atomic % segregant (C or P) as a function of ∆G° b - ∆G° S in 17–4 PH stainless steel (adapted from reference [Citation17]).](/cms/asset/243e2e99-455a-48bb-8ff8-ca1503e630a3/ymte_a_2278000_f0010_b.gif)
It was noted from the plot of inverse of the product of impact toughness and atomic % of segregant, Ē versus ΔG°b - ΔG°s that an element with more positive ΔG°b - ΔG°s is more embrittling (in the present case, P) as compared to the element with less positive ΔG°b - ΔG°s, (in the present case carbon) [Citation10,Citation17].
Low alloy NiCrMoV steels
Attempts were undertaken to explore features of grain boundary segregation in multi-component engineering systems, where alloying additions are purposely added and impurities are unavoidable, after realizing the significance of fundamental elemental interactions in the processing of metals. As a result, the idea of grain boundary segregation isotherms was established, which offered an experimental framework to comprehend grain boundary segregation behaviour and its influence on time, temperature, stress, and chemical systems. The derived information was helpful in resolving real-world issues, and the idea of grain boundary segregation isotherms was put forth [Citation21–23]. An illustration of grain boundary segregation isotherms for a Ni-Cr-Mo-V steel corresponding to a temperature of 823 K is presented in [Citation21]. Two distinct regimes are delineated in the segregation isotherms of 823 K. The first is characterized by rapid cosegregation of Cr and N, both of which increase linearly in log t and attain an equilibrium coverage at t ≅ 10 ks. An increase in the concentration of N and Cr in the first stage is followed by an increase in the concentration of P and V in the second stage. At t ≅ 15 ks, the concentration of P, N, Cr and V continuously decreases with log t, the decrease being linear in log t for all the elements.
Figure 11. (A) grain boundary segregation isotherms recorded at 823 K for 2.6Ni-0.4Cr-0.28Mo-0.10V steel. Bars indicated on the figure represent the range over which the values were measured. (b) ratio of grain boundary [(θN+ θC)/(θCr+ θV)] as a function of isothermal heat treatment time at 823 K for 2.6Ni-0.4Cr-0.28Mo-0.10V steel. Bars indicated on the figure represent the range over which the values were measured (adapted from reference [Citation21]).
![Figure 11. (A) grain boundary segregation isotherms recorded at 823 K for 2.6Ni-0.4Cr-0.28Mo-0.10V steel. Bars indicated on the figure represent the range over which the values were measured. (b) ratio of grain boundary [(θN+ θC)/(θCr+ θV)] as a function of isothermal heat treatment time at 823 K for 2.6Ni-0.4Cr-0.28Mo-0.10V steel. Bars indicated on the figure represent the range over which the values were measured (adapted from reference [Citation21]).](/cms/asset/8a5cd10c-6f7f-4871-ad05-635808ea9109/ymte_a_2278000_f0011_b.gif)
In view of the anticipated interaction between carbide and nitride forming elements (Cr and V), (θN + θc)/(θCr + θV) were plotted as a function of time (); θ is the grain boundary coverage of the interacting element. In , the invariant behaviour of (θN + θc)/(θCr + θV) is indicative of strong coupling amongst these elements.
At higher temperatures (>823 K), a new interaction process similar to that of Cr and V with C and N was observed between segregating elements Ni and Sn. This was subsequently followed by site-competitive process involving displacement of segregated Sn with segregating S [Citation21,Citation22].
The co-operative and site-competitive interaction processes derived from grain boundary segregation isotherms were depicted in terms of time-temperature plots () and referred as interaction maps or grain boundary segregation maps [Citation21–23]. The interaction maps were created by taking into account those kinetic regimes of the segregation isotherm that had clearly defined interaction processes and that had an increasing trend in the grain boundary coverage of the interacting elements. These interaction maps gave a comprehensive view of the potential interactions that can take place during isothermal heat treatment and might eventually affect the mechanical behaviour of engineering metals and alloys. The interaction maps revealed the impact of alloying elements on the interaction processes in addition to giving a perspective on thermodynamic interaction processes. The concept of grain boundary segregation isotherms was used in another significant application area to analyse how applied stress affected grain boundary chemistry. For instance, the stress field in front of a blunt notch can encourage grain boundary segregation of the impurity element sulphur prior to the start of a crack, which causes low ductility intergranular fracture [Citation24–27].
Figure 12. Grain boundary interactions (interaction maps) occurring amongst trace and alloying elements in 2.6 Ni-0.4Cr-0.28Mo-0.10V steel (adapted from reference [Citation22]).
![Figure 12. Grain boundary interactions (interaction maps) occurring amongst trace and alloying elements in 2.6 Ni-0.4Cr-0.28Mo-0.10V steel (adapted from reference [Citation22]).](/cms/asset/d63b8fdc-09c5-4c60-af77-6a349e4927f2/ymte_a_2278000_f0012_b.gif)
Interstitial-free rephosphorized steels
The understanding of grain boundary segregation and thermodynamic interaction processes in precipitation-hardened stainless steel facilitated kinetics of cold work embrittlement in rephosphorized interstitial free steels to be investigated and applied to alleviate cold work embrittlement. An optimized steel chemistry corresponds to a steel composition where there is some excess C, in addition to what is stoichiometrically required to tie-up all the available (or free) Nb as niobium carbides, i.e. the Nb/C wt% ratio ≤7 was considered for simulation of bath annealing cycle. A similar situation is applied to Ti and Nb containing interstitial free steels. A reduction in the intergranular concentration of P was observed for Nb/C <7, in contrast to higher Nb/C ratio. This palliative behaviour was the result of a site-competitive process involving C and P, where the more surface or interface active C segregates to the grain boundaries in advance, leading to the suppression of P segregation () [Citation29,Citation30].
Figure 13. Time-temperature diagrams of grain boundary segregation of P in 0.05 wt.%P interstitial-free steel, numbers labeling each curve are levels of P segregation in monolayers; computed horizontal lines denote equilibrium concentration of P (adapted from references [Citation28–30]).
![Figure 13. Time-temperature diagrams of grain boundary segregation of P in 0.05 wt.%P interstitial-free steel, numbers labeling each curve are levels of P segregation in monolayers; computed horizontal lines denote equilibrium concentration of P (adapted from references [Citation28–30]).](/cms/asset/c16e70ea-3d64-4d0d-8043-eb8abe810a28/ymte_a_2278000_f0013_b.gif)
Figure 14. (a) temperature dependence of batch annealing cycle (heating rate 15 K h−1 to 973 K, holding for 2 h at 973 K, cooling at 15 K h−1) and (b) associated grain boundary P concentration as function of time in the absence and presence of P-C site competitive process (adapted from references [Citation28–30]).
![Figure 14. (a) temperature dependence of batch annealing cycle (heating rate 15 K h−1 to 973 K, holding for 2 h at 973 K, cooling at 15 K h−1) and (b) associated grain boundary P concentration as function of time in the absence and presence of P-C site competitive process (adapted from references [Citation28–30]).](/cms/asset/2f70d792-eacd-4f56-a242-b86a2fc4da0c/ymte_a_2278000_f0014_b.gif)
Ultrahigh strength (770 MPa) hot rolled microalloyed steels
The experience of detrimental effect of grain boundary precipitation of titanium carbides/carbosulfides in maraging steels [Citation11] and phosphorus segregation in precipitation hardened stainless steel [Citation12,Citation13] were successfully used to develop 770 MPa hot rolled steel [Citation31] as a substitute for quenched and tempered steels. The application of knowledge-base involved controlled usage of titanium (for precipitation strengthening) and boron (for hardenability and moving the ferrite C-curve to the right).
Given that the development of 770 MPa hot-rolled was based on the production of a ferrite-bainite microstructure with impact toughness approaching ~135 J at −40°C and a ductile-to-brittle transition of less than −70°C. In the alloy design, the boron concentration was optimized to ensure boron segregates only to the required extent to austenite/ferrite boundaries, where it exhibits ferrite nucleation through strong interaction with lattice defects such as dislocation and vacancies, shifting ferrite-C-curve to the right (), but not to the level that it decreases toughness.
Figure 15. Schematic diagram showing role of B in retarding ferrite nucleation and promoting bainite formation in HSLA steels (adapted from reference [Citation31]).
![Figure 15. Schematic diagram showing role of B in retarding ferrite nucleation and promoting bainite formation in HSLA steels (adapted from reference [Citation31]).](/cms/asset/7dfc0f2f-4a44-45e0-93e6-41855a0750bc/ymte_a_2278000_f0015_b.gif)
Besides composition, microstructure, and precipitates, the properties of the steel are also influenced by the crystallographic texture. During the controlled rolling of steels, three types of processes, deformation, recrystallization and transformation, give rise to and induce changes in texture [Citation32,Citation33]. The {332} <113> transformation texture component is the most beneficial in achieving a good strength – toughness combination [Citation32,Citation33].
In , an ε fibre plot of relevance to toughness is presented. Important ideal {hkl}<uvw> orientations are indicated. It can be seen that the half- and quarter-depth plots indicate a significant {332}<113> component, which is the desired texture for toughness and may offset the effect of the undesired {110}<011> component. This accounted for the steel’s good strength–toughness combination, combined with good edge of formability. To obtain more {332}<113> in the final product, which would improve deep drawability, more {110}<112> needs to be encouraged in the deformed austenite during hot rolling. To accomplish this, hot mill lubrication and finishing temperature, are the two variables known to significantly influence hot band textures.
Figure 16. Skeletal ε fibre plot for indicated depths below surface in ultrahigh strength hot rolled microalloyed steel [Citation34].
![Figure 16. Skeletal ε fibre plot for indicated depths below surface in ultrahigh strength hot rolled microalloyed steel [Citation34].](/cms/asset/681dc723-ac2d-4eba-aff6-f9466881c675/ymte_a_2278000_f0016_b.gif)
The through thickness texture gradients are influenced by lubrication even when the material is completely recrystallized [Citation35]. Changes in friction that affect the state of stress in the nearby surface are another reason that might cause textural variations. Through thickness temperature differences, spray practice can also affect texture gradients. The gradient of the texture can also be impacted by hot mill drafting schedules. One study [Citation36] determined that heavy reductions early during hot rolling decreased the severity of the gradient.
In spite of the above comments, the significance of alloy chemistry on texture evolution cannot be ignored, given that Nb-Ti and V-Nb steels with similar yield strength of about 600 MPa and total elongation of 20 pct, which were processed under similar conditions, the Nb-Ti steels exhibited superior formability and toughness in relation to V-Cb steels [Citation34]. The improved formability and toughness of Nb-Ti steels was attributed to the cumulative contribution of relatively finer grain size, narrow ferrite grain size distribution, inherently more ductile behaviour and microplasticity, the reduced intensity of {110}<011> texture, and slightly higher intensity of the desired {332}<113> texture [Citation34].
Niobium-microalloyed high strength steels
Alternative high strength structural beam chemistries are currently in high demand. It is now crucial that the use of microalloying elements like niobium is coupled with a higher cooling rate to derive the maximum benefit in terms of both high strength and toughness because processing structural beams involves less mechanical deformation and alloy cost needs to be low. To produce massive structural beams with enhanced mechanical properties, we are currently developing a niobium-microalloying technique. The cooling rate (and toughness) were found to be significantly and favourably influenced by niobium. This behaviour was related to an increase in the content of degenerate pearlite with an increase in cooling rate which led to higher impact toughness () [Citation37]. Furthermore, it was possible to obtain bainitic microstructure.
Figure 17. Room temperature charpy v-notch impact toughness (adapted from reference [Citation37]).
![Figure 17. Room temperature charpy v-notch impact toughness (adapted from reference [Citation37]).](/cms/asset/d725e7e6-7961-41ff-add0-0ea7cd32e616/ymte_a_2278000_f0017_b.gif)
Representative bright field TEM micrographs of pearlite microstructures of Nb-microalloyed steels processed at low, intermediate, and high cooling rates are presented in , respectively. Also, with the increase in cooling rate, the cementite morphology in pearlite changed from lamellar pearlite to degenerate pearlite and finally to small cementite particles [. The steel processed at low cooling rate contained lamellar pearlite and degenerate pearlite at intermediate cooling rate. The SAD pattern analysis of degenerate pearlite indicated that the cementite exhibits [112]α//[122]Fe3C orientation relationship with ferrite matrix, which was close to ‘Pitsch’ orientation relationship that is commonly observed in lamellar pearlite [Citation37]. It was observed that the steel processed at low cooling rate contained polygonal ferrite (), at intermediate cooling rate the microstructure consisted of elongated ferrite grains (), and at high cooling rate the microstructure predominantly contained lath-type or bainitic ferrite (). The different types of ferrite morphologies must have formed by a different mechanism [Citation37].
Figure 18. (a) Bright field TEM micrograph of Nb-microalloyed steels processed at (a) low (or normal) cooling rate showing polygonal ferrite structure, (b) intermediate cooling rate showing elongated ferrite structure and (c) high cooling rate showing bainitic/lath-type ferrite structure (adapted from reference [Citation37]).
![Figure 18. (a) Bright field TEM micrograph of Nb-microalloyed steels processed at (a) low (or normal) cooling rate showing polygonal ferrite structure, (b) intermediate cooling rate showing elongated ferrite structure and (c) high cooling rate showing bainitic/lath-type ferrite structure (adapted from reference [Citation37]).](/cms/asset/48e1d50a-c665-4f85-8535-449ff5cb076d/ymte_a_2278000_f0018_b.gif)
Figure 19. Bright field TEM micrograph of Nb-microalloyed steels processed at (a) low (or normal) cooling rate showing lamellar pearlite structure and (b) intermediate cooling rate showing degenerate pearlite structure (adapted from reference [Citation37]).
![Figure 19. Bright field TEM micrograph of Nb-microalloyed steels processed at (a) low (or normal) cooling rate showing lamellar pearlite structure and (b) intermediate cooling rate showing degenerate pearlite structure (adapted from reference [Citation37]).](/cms/asset/48237d91-770a-4ffa-a9ea-3e5435d58e02/ymte_a_2278000_f0019_b.gif)
In the temperature range where normal pearlite transforms into upper bainite, degenerate pearlite is created by the nucleation of cementite at the ferrite/austenite interface, followed by layers of carbide-free ferrite encasing the cementite particles. Degenerate pearlite is created using the same diffusion mechanism as lamellar pearlite, but because of its different morphology, it cannot form continuous lamellae due to insufficient carbon diffusion [Citation38]. According to reports, degenerate pearlite has a broader interface between ferrite and cementite than conventional pearlite, which causes the ferrite grain boundary area of controlled-rolled steels containing degenerated pearlite to be higher than that of conventionally processed steel [Citation39]. Degenerate pearlite was believed to promote toughness [Citation39].
Lath ferrite/bainitic ferrite, degenerated pearlite and ferrite grain size are the microstructural factors that affect toughness. Given that coarse degenerate pearlite deforms inhomogeneously with strain localized in narrow slip bands, as opposed to fine degenerate pearlite, which exhibits uniform strain distribution during deformation (), it is anticipated that the finer cementite in degenerate pearlite will not only yield higher strength but also improve toughness [Citation40]. Due to the development of Orowan loops, fine cementite particles also accelerate the work hardening rate by generating a strain gradient close to the particles. We refer to the dislocations that make up the strain gradient as geometrically necessary dislocations [Citation41,Citation42]. Thus, the significant increase in toughness with cooling rates of Nb-microalloyed steels is related to toughening enhancing phase and degenerate pearlite bainite. A schematic illustration of formation of degenerate pearlite and its influence on toughness is illustrated in [Citation20].
Figure 20. A schematic illustration of formation of degenerate pearlite and its influence on toughness (adapted from reference [Citation37]). When cementite is distributed in pearlite with a fine rod or platelet phase, it is referred as”degenerate pearlite” or sometimes as “nodular bainite”..
![Figure 20. A schematic illustration of formation of degenerate pearlite and its influence on toughness (adapted from reference [Citation37]). When cementite is distributed in pearlite with a fine rod or platelet phase, it is referred as”degenerate pearlite” or sometimes as “nodular bainite”..](/cms/asset/7682c265-68ae-447a-84f1-e7ce98576e3e/ymte_a_2278000_f0020_b.gif)
700 MPa Nb-microalloyed pipeline steels
Utilizing the experience of 770 MPa, hot rolled steel, a similar approach was adopted to develop a new 700 MPa Nb-microalloyed pipeline steel with a lean chemistry [Citation38]. The Charpy impact toughness at 0°C was 27 J, and tensile elongation was 16%. Fine grain size, solid solution strengthening with extra interstitial hardening, precipitation hardening from carbides, and dislocation hardening all contributed to the ultrahigh strength. The microstructure was primarily characterized by polygonal ferrite, upper bainite and very fine (<10 nm) NbC precipitates (). An important aspect of the developed steel is significantly lean chemistry [Citation43].
Figure 21. Bright field TEM micrographs illustrating the general microstructure of the 700 MPa pipeline steel with lean chemistry. (a) non-equiaxed or quasi-polygonal ferrite, (b) precipitate–dislocation interaction in the ferrite matrix, (c) upper bainite and (d) obtained from carbon extraction replica showing fine scale precipitation (adapted from reference [Citation43]).
![Figure 21. Bright field TEM micrographs illustrating the general microstructure of the 700 MPa pipeline steel with lean chemistry. (a) non-equiaxed or quasi-polygonal ferrite, (b) precipitate–dislocation interaction in the ferrite matrix, (c) upper bainite and (d) obtained from carbon extraction replica showing fine scale precipitation (adapted from reference [Citation43]).](/cms/asset/b2f33d40-8491-48d5-9f83-b4550fbfdf97/ymte_a_2278000_f0021_b.gif)
An interesting aspect that emerged from pipeline steel development was that reducing the manganese content led to interphase precipitation of NbC in addition to regular precipitation [Citation44]. A portion of the grain experienced precipitation that began at transformation temperature but did not finish, resulting in the general precipitation that took place in the remaining portion of the grain at lower temperatures. There is little thermodynamic potential for general precipitation to happen in the same grain if interphase precipitation happened throughout the grain. These observations in low Nb microalloyed steel are important because these precipitates are known to be stable and do not coarsen on temperature cycling due to low surface energy. For example, interphase precipitation () will be very effective in preventing grain coarsening in HAZ region during thermal cycling of base plate in welding operation involved in pipe making.
Figure 22. (a) Bright field image showing ferrite grain with array of fine precipitate inside the grain and (b) dark field image taken using NbC (−13–1) diffraction spot (adapted from reference [Citation43]).
![Figure 22. (a) Bright field image showing ferrite grain with array of fine precipitate inside the grain and (b) dark field image taken using NbC (−13–1) diffraction spot (adapted from reference [Citation43]).](/cms/asset/b904a591-c32c-4010-9321-8442f9b68a46/ymte_a_2278000_f0022_b.gif)
Concluding remarks
While some of the strategies described here are anticipated to be useful in the creation of the third generation of sophisticated high strength steels with high strength–ductility combinations. An approach that is being increasingly considered derives its inspiration from transformation-induced plasticity (TRIP) steels, which have a considerable portion of austenite that, upon deformation, turns into martensite and contributes to higher degrees of strain hardening. This aspect constitutes one of the focal themes towards the current development of advanced high strength steels with significantly high-volume fraction of austenite, without adversely affecting the fabrication of structural components including welding. In this regard, processing routes that can enable stabilization of austenite through diffusion of carbon from martensite to austenite (), in a manner that transitional carbide formation () is inhibited, are a viable approach [Citation45]. During straining, the higher elongation is connected to gradual and progressive transformation of austenite to martensite at higher levels of strain depending on the metastability of the alloy in question, and the grain size will be of lesser importance, as is the case with nanograined/ultrafine-grained austenitic stainless steel [Citation46]. This would enable the work hardening rate to increase and with twinning and dislocation glide being the possible primary deformation mechanisms. The challenge, however, is the degree to which stabilization can be accomplished.
Figure 23. Bright field images (left) and corresponding dark field images (right) of medium-carbon silicon-containing steels quenched at 150°C for 20 s and partitioned for 30 s at 200°C. Dark field images were taken using 220 austenite reflection (adapted from reference [Citation45]).
![Figure 23. Bright field images (left) and corresponding dark field images (right) of medium-carbon silicon-containing steels quenched at 150°C for 20 s and partitioned for 30 s at 200°C. Dark field images were taken using 220 austenite reflection (adapted from reference [Citation45]).](/cms/asset/f9eb67dc-f8d5-4bdf-897a-ae40ec2df0ad/ymte_a_2278000_f0023_b.gif)
Figure 24. Bright field (left) and corresponding dark field image (right) of medium-carbon steel quenched to 100°C for 20 s and partitioned at 350°C for 10–30 s. Dark field images were taken using 020 ε-carbide reflection (adapted from reference [Citation45]).
![Figure 24. Bright field (left) and corresponding dark field image (right) of medium-carbon steel quenched to 100°C for 20 s and partitioned at 350°C for 10–30 s. Dark field images were taken using 020 ε-carbide reflection (adapted from reference [Citation45]).](/cms/asset/db2e6e7b-a7ef-438b-b1f6-b109cf611467/ymte_a_2278000_f0024_b.gif)
More recently, the potential of the concept of phase reversion process to obtain nanograined (NG) structure with high strength–high ductility combination and to fundamentally understand the deformation and fracture mechanisms is described [Citation47–51]. In the phase reversion approach, deformation (~60–80%) of austenite at room temperature leads to transformation of face-centred cubic austenite to body-centred cubic martensite (α’) (). Upon annealing, martensite reverts to austenite via diffusional or shear mechanism. The uniqueness of the concept is that it enables us to obtain a spectrum of grain size from the NG to the coarse-grain (CG) regime through a single set of parameters (extent of cold deformation and temperature-time annealing sequence). Deformation studies carried out as a function of grain size suggested that there was a distinct difference and fundamental transition in the deformation behaviour of NG and CG austenitic alloy, such that ‘deformation twinning’ contributed to the excellent ductility of ‘high strength’ NG alloy, while ductility was also good in ‘low strength’ CG alloy, but because of strain-induced martensite nucleation at shear bands. It was postulated that in a given austenitic stainless steel used for biomedical devices, the decrease in grain size from the CG to NG regime increases the stability of austenite such that there is a change in the deformation mechanism from strain-induced martensite in the CG structure to nanoscale twinning in the NG structure, supported by the theoretical calculation of the critical resolved shear stress. Furthermore, the change in the deformation mechanism impacted the mode of fracture such that it was striated fracture in the high strength–high ductility combination NG alloy and microvoid coalescence in the low strength–high ductility CG counterpart. The appearance of striated fracture in the NG alloy was attributed to the quasi-static step-wise crack growth mechanism.
Figure 25. A schematic representation of phase reversion concept to obtain nanograined structure (adapted from references [Citation50,Citation51]). Similar approach was proven in microalloyed steels.
![Figure 25. A schematic representation of phase reversion concept to obtain nanograined structure (adapted from references [Citation50,Citation51]). Similar approach was proven in microalloyed steels.](/cms/asset/bf877c7a-2e3b-4813-8739-524ca4fddf8b/ymte_a_2278000_f0025_b.gif)
Acknowledgments
The author gratefully acknowledges several students, post-doctoral scholars, friends, colleagues, and their respective institutions with whom the author interacted and collaborated in the work presented here as an overview. Many of them have directly or indirectly contributed and spearheaded the work described here as an overview. In view of a long list of contributors and participants, the author preferred to defer the listing. Every attempt was made to cite relevant references to the described work and any omission is unintentional, particularly when only selected articles were considered during the preparation of the overview. Furthermore, it is pertinent to mention that the present article is brief or succinct overview with a focus on highlighting the salient aspects that are important in the context of strength–ductility–toughness combination.
Disclosure statement
No potential conflict of interest was reported by the author.
Data availability statement
Given that it is an overview article, data availability is not relevant. The author has done his best in citing the relevant articles. However, inadvertently there may be a situation where an article has not been appropriately cited. All figures adapted from references and reference numbers are indicated in the figure caption.
References
- Ning H, Li X, Meng L, et al. Effect of Ni and Mo on microstructure and mechanical properties of grey cast iron. Mater Technol; Adv Perform Mater. 2023;38(1):2172991. doi: 10.1080/10667857.2023.2172991
- Guo L, Su X, Dai L, et al. Strain ageing embrittlement behaviour of X80 self-shielded flux-cored girth weld metal. Mater Technol Adv Perform Mater. 2023;38(1):2164978. doi: 10.1080/10667857.2023.2164978
- Yang C, Xu H, Wang Y, et al. Hot tearing analysis and process optimisation of the fire face of al-cu alloy cylinder head based on MAGMA numerical simulation. Mater Technol Adv Perform Mater. 2023;38(1):2165245. doi: 10.1080/10667857.2023.2165245
- Li Q, Zuo H, Feng J, et al. Strain rate and temperature sensitivity on the flow behaviour of a duplex stainless steel during hot deformation. Mater Technol Adv Perform Mater. 2023;38(1):2166216. doi: 10.1080/10667857.2023.2166216
- Misra RDK. Strong and ductile texture-free ultrafine-grained magnesium alloy via three-axial forging. Mater Lett. 2023;31:133443. doi: 10.1016/j.matlet.2022.133443
- Misra RDK. Enabling manufacturing of multi-axial forging-induced ultrafine-grained strong and ductile magnesium alloys: a perspective of process-structure-property paradigm. Mater Technol. 2023;38(1):2189769. doi: 10.1080/10667857.2023.2189769
- Li SF, Misra RDK, Liu ZQ. Towards strength-ductility synergy in nanosheets strengthened titanium matrix composites through laser power bed fusion of MXene/Ti composite powder. Mater Technol. 2023;38:2181680. doi: 10.1080/10667857.2023.2181680
- Niu G, Zurpb H, Guyuen M, et al. Superior fracture toughness in a high-strength austenitic steel with heterogeneous lamellar microstructure. Acta Materialia. 2022;226:117462. doi: 10.1016/j.actamat.2022.117642
- Misra RDK, Challa VSA, Injeti VSY. Injeti, advanced performance materials. Mater Technol. 2022;37(7):437–18. doi: 10.1080/10667857.2022.2065621
- Misra RDK. Proceeddings of International Conference on thermo-mechanical simulation and processing of steels conference, Materials and Manufacturing Processes. 2010;25:60–71.
- Misra RDK, Balasubramanian TV, Rama Rao P. AES analysis of fracture toughness variation with heat treatment in an 18 Ni (250 grade) maraging steel. J Mater Sci Lett. 1987;6(2):125–130. doi: 10.1007/BF01728960
- Rama Rao P. Private communication – unpublished study conducted at DMRL. Hyderabad, India; 1987.
- Misra RDK, Prasad CY, Balasubramanian TV, et al. Effect of phosphorus segregation on impact toughness variation in 17-4 precipitation hardened stainless steel. Scr Metall Mater. 1986;20(5):713. doi: 10.1016/0036-9748(86)90497-7
- Misra RDK, Prasad CY, Balasubramanian TV, et al. On variation of impact toughness in 17-4 precipitation hardened stainless steels. Scr Metall Mater. 1987;21:1067. doi: 10.1016/0036-9748(87)90251-1
- Misra RDK, Prasad CY, Balasubramanian TV, et al. On the role of molybdenum on impact toughness of precipitation hardened stainless steel. Scr Metall Mater. 1986;20(10):1339. doi: 10.1016/0036-9748(86)90091-8
- Misra RDK, Prasad CY, Balasubramanian TV, et al. Effect of post-aging quenching treatment on impact toughness of 17-4 precipitation hardened stainless steel. Scr Metall Mater. 1988;22:1323. doi: 10.1016/S0036-9748(88)80155-8
- Misra RDK, Rama Rao P. An analysis of grain boundary cohesion in precipitation hardened stainless steel. Scr Metall Mater. 1993;28(12):1531–1536. doi: 10.1016/0956-716X(93)90587-I
- Erhart H, Grabke HJ. Equilibrium segregation of phosphorus at grain boundaries of fe–P, fe–C–P, fe–Cr–P, and fe–Cr–C–P alloys. Metal Sci. 1981;15(9):401. doi: 10.1179/030634581790426877
- Rice JR, Wang JS. Embrittlement of interfaces by solute segregation. MateSci Eng A. 1989;107:23. doi: 10.1016/0921-5093(89)90372-9
- Olsen, in innovations in ultra-high strength steel technology. In: G.B. Olson, M. Azrin and E.S. Wright, editors. Proceedings of the 34th Sagamore Army Research Conference. 1990. https://api.semanticsscholar.org/Corpus ID: 136229017
- Misra RDK, Balsubramanian TV, Rao PR. On interaction amongst trace and alloying elements at the grain boundaries of low alloy steel. Acta Metallurgica et Materialia. 1987;35:2995. doi: 10.1016/0001-6160(87)90298-7
- Misra RDK, Balsubramanian TV. Cooperative and site-competitive interaction processes at the grain boundaries of NiCrMoV low alloy steel. Acta Metallurgica et Materialia. 1989;37:1475. doi: 10.1016/0001-6160(89)90179-X
- Misra RDK, Balsubramanian TV. Stress enhanced grain boundary segregation of impurity elements in a low alloy steel. Acta Metallurgica et Materialia. 1990;38:1263. doi: 10.1016/0956-7151(90)90197-O
- Misra RDK, Balasubramanian TV. Effects of microstructure on grain boundary segregation processes in low alloy steels. Acta Metallurgica et Materialia. 1990;38(11):2357. doi: 10.1016/0956-7151(90)90103-N
- Misra RDK, Rama Rao P. Grain boundary segregation in a low alloy steel under tensile loading conditions. Acta Metallurgica et Materialia. 1992;40:1223. doi: 10.1016/0956-7151(92)90420-J
- Misra RDK, Rama Rao P. Influence of tensile stress on behaviour of grain boundary segregants and related interactions between trace and solute elements in 2·6Ni–Cr–Mo–V low alloy steel. Mater Sci Technol. 1993;9(6):497. doi: 10.1179/mst.1993.9.6.497
- Misra RDK. Issues concerning the effects of applied tensile stress on intergranular segregation in low alloy steels. Acta Materialia. 1996;44(3):885. doi: 10.1016/1359-6454(95)00249-9
- Misra RDK. Grain boundary segregation and fracture resistance of engineering steels. Surf Interface Anal. 2001;31(7):509. doi: 10.1002/sia.1079
- Misra RDK, Weatherly GC, Embury JD. Kinetics of cold work embrittlement of interstitial-free steels. Mater Sci Technol. 2000;16:9. doi: 10.1179/026708300773002618
- Misra RDK. Temperature-time dependence of grain boundary segregation of phosphorus in interstitial-free steels. J Mater Sci. 2002;21:1275.
- Misra RDK, Weatherly GC, Hartmann JE, et al. Ultrahigh strength hot rolled microalloyed steels – microstructural aspects of development. Mater Sci Technol. 2001;17(9):1119. doi: 10.1179/026708301101511040
- Ray RK, Jonas JJ. Transformation textures in steels. Inter Metallurgical Rev. 1990;35(1):1. doi: 10.1179/095066090790324046
- Lequeu P, Jonas JJ. Modeling of the plastic anisotropy of textured sheet. Metall Trans A. 1988;19A(1):105. doi: 10.1007/BF02669819
- Misra RDK, Anderson JP. Evolution of textures in hot rolled Nb-Ti and V-Nb microalloyed steels. Mater Sci Technol. 2002;18:1513. doi: 10.1179/026708302225007286
- Inagaki H, Kurihara K, Kozasu I. Influence of crystallographic texture on the strength and toughness of control-rolled high tensile strength steel. Trans Iron Steel Inst Jpn. 1977;17(2):75. doi: 10.2355/isijinternational1966.17.75
- Hashimoto S, Yakushuji T, Kashima T, et al. Proceedings Of International Conference On Physical Metallurgy Of Thermomechanical Processing Of Steels And Other Metals. 1988;2:652.
- Shanmugam S, Misra RDK, Mannering T, et al. Impact toughness and microstructure relationship in niobium and vanadium microalloyed steels processed with varied cooling rates to similar yield strength. Mater Sci Eng A. 2006;437(2):436. doi: 10.1016/j.msea.2006.08.007
- Matsuo M, Saki T, Suga Y. Origin and development of through-the-thickness variations of texture in the processing of grain-oriented silicon steel. Metall Trans A. 1986;17A(8):1313. doi: 10.1007/BF02650112
- Ohmori Y, Honeycombe RWK. Proceedings of ICSTIS (suppl.). Trans Iron Steel Inst Jpn. 1971;11:1160.
- Yamane T, Hiyayuki K, Kawazu Y, et al. Improvement of toughness of low carbon steels containing nitrogen by fine microstructures. J Mater Sci. 2002;37(18):3875. doi: 10.1023/A:1019695104094
- Joung Sim H, Bum Lee Y, Nam WJ. Ductility of hypo-eutectoid steels with ferrite-pearlite structures. J Mater Sci. 2004;39:1849. doi: 10.1023/B:JMSC.0000016201.77933.c2
- Song R, Ponge D, Raabe D. Improvement of the work hardening rate of ultrafine grained steels through second phase particles. Scripta Meterialia. 2005;52:1075. doi: 10.1016/j.scriptamat.2005.02.016
- Shanmugam S, Misra RDK, Hartmann JE, et al. Microstructure of high strength niobium containing pipeline steel. Mater Sci Eng A. 2006;441:215. doi: 10.1016/j.msea.2006.08.017
- Shanmugam S, Ramisetti NK, Misra RDK, et al. Microstructure and high strength–toughness combination of a new 700MPa Nb-microalloyed pipeline steel. Mater Sci Eng A. 2008;478(1–2):26. doi: 10.1016/j.msea.2007.06.003
- Nayak SS, Misra RDK, Hartmann J, et al. Microstructure and properties of low manganese and niobium containing HIC pipeline steel. Mater Sci Eng A. 2008;494(1–2):456. doi: 10.1016/j.msea.2008.04.038
- Nayak SS, Anamolu R, Misra RDK, et al. Microstructure-hardness relationship in quenched and partitioned medium-carbon and high-carbon steels containing silicon. Mater Sci Eng A. 2008;498:442. doi: 10.1016/j.msea.2008.08.028
- Misra RDK, Nayak S, Venkatsurya P, et al. Nanograined/ultrafine-grained (NG/UFG) structure and tensile deformation behavior of shear reversion induced 301 austenitic stainless steel. Metall Mater Trans A. 2010;41A(8):2162–2174. doi: 10.1007/s11661-010-0230-6
- Misra RDK, Nayak S, Mali S, et al. Microstructure and deformation behavior of phase-reversion induced nanograined/ultrafine-grained (NG/UFG) austenitic stainless steel. Metall Mater Trans A. 2009;40(10):2498–2509. doi: 10.1007/s11661-009-9920-3
- Misra RDK, Nayak S, Mali S, et al. On the significance of nature of strain-induced martensite on phase-reversion induced nanograined/ultrafine-grained (NG/UFG) austenitic stainless steel. Metall Mater Trans A. 2010;41(1):3–12. doi: 10.1007/s11661-009-0072-2
- Misra RDK, Challa VSA, Venkatasurya PKC, et al. Interplay between grain structure, deformation mechanism and austenite stability in phase-reversion-induced nanograined/ultrafine-grained austenitic ferrous alloy. Acta Materialia. 2015;84:339–348. doi: 10.1016/j.actamat.2014.10.038
- Misra RDK, Injeti VYS, Somani MC. The significance of deformation mechanisms on the fracture behavior of phase reversion-induced nanostructured austenitic stainless steel. Sci Rep. 2018;8(1):1–13. doi: 10.1038/s41598-018-26352-1