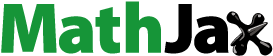
ABSTRACT
This paper assessed the technical and economic viability of biodiesel production from Second-generation feedstocks native to East Africa, which included Castor, Croton, and Jatropha. Their oils were converted to biodiesel by transesterification and characterizations of B100 and B10 done following ASTM D6751. ASPEN Plus V11 was used in process simulation and profitability analysis. Oil yields obtained ranged from 29.5% to 35.6%. B100 and B10 properties conformed to ASTM D6751. The negative Net Present Values obtained render B100 and B10 production uneconomical unless incentivized. Sensitivity analyses showed that NPV varied with feedstock cost and biodiesel selling prices. This assessment established that though a B10 policy based on second-generation feedstocks is technically viable, interventions are needed to make it profitable in Uganda.
1. Introduction
The Global demand for petroleum, a finite and nonrenewable energy resource, stands at about 100 million barrels per day, with over 90% used for transportation (IEA Citation2021). Transport emissions account for 23% of global energy-related greenhouse gas emissions (IPCC Citation2018). This is a matter of great concern as the world grapples with the escalating negative impacts of climate change. Additionally, most developing nations’ purchase and importation of petroleum products substantially impact their foreign exchange earnings (Tibesigwa, Olupot, and Kirabira Citation2021). The adoption of renewable energy sources, including biofuels, has been widely considered a measure for reversing these damaging impacts (UNEP Citation2012). These sustainable transport fuels are expected to enable countries to achieve their net-zero carbon emission targets, in line with the Paris Agreement on climate change. Relevant legal and policy frameworks aimed at decarbonising transport sectors through blending biofuels with fossil fuels have been put in place by different countries (Chrysa Citation2020). In 2018, a biofuels law that advocates for the mandatory blending of fossil fuels (diesel or petrol) with up to 10% of biofuels (biodiesel or bioethanol) was enacted by Uganda (MEMD Citation2018a).
Biodiesel as a potential substitute for petroleum diesel in different regions has gained significance owing to its environmental benefits and renewability. Biodiesel developments are mainly agriculturally oriented, with the propensity to spur job creation. Biodiesel is a liquid biofuel made up of long-chain monoalkylic esters of fatty acids. It can be used in diesel engines alone or blended with diesel oil, provided the requirements of ASTM D 6751 and EN 14214 are met (Silitonga et al. Citation2013). The features of the various individual fatty esters that comprise biodiesel determine the overall properties of the biodiesel fuel (Atabani and César Citation2014). The physicochemical properties of a fatty ester molecule are influenced by the following structural features: chain length, degree of unsaturation, and branching of the chain. These, in turn, influence the fuel properties of biodiesel, namely, cetane rating, exhaust emissions, the heat of combustion, cold flow, oxidative stability, viscosity, and lubricity (Borhanipour et al. Citation2014). Blends with diesel fuel are indicated as ‘Bx,’ where ‘x’ is the percentage of biodiesel in the blend. For instance, ‘B5’ indicates a blend with 5% biodiesel and 95% diesel fuel. Consequently, B100 indicates pure biodiesel, which is treated as a blendstock (Romano and Sorichetti Citation2011). However, biodiesel blends are more economically feasible alternatives to promote on the fuel market than pure biodiesel (Wakil et al. Citation2015).
Biodiesel can be produced from both edible and inedible feedstocks classified as follows: (i) First-generation feedstocks from edible oil seeds, food crops, and animals fats; (ii) Second generation feedstocks from non-edible oilseeds, waste cooking oil, lignocellulosic feedstock materials; and (iii) Third and fourth Generation feedstocks from algae and other microbes (Vignesh et al. Citation2021). Interest in second-generation biodiesel feedstocks is attributed to their potential to reverse sustainability concerns associated with first-generation biodiesel derived from edible oils (Bhuiya et al. Citation2014). Castor, Croton, and Jatropha were recommended as potential feedstocks for biodiesel production in Uganda due to factors that included the local familiarity with the crop, land-use efficiency, and estimated production variable costs (MEMD & NOVI Energy Citation2011). These second-generation feedstocks belong to the Euphorbiaceae family, are drought-tolerant, and do not compete with the food chain (Pandey et al. Citation2012). Oil is obtained from these seeds through mechanical, chemical, or solvent, enzymatic, supercritical fluid, and microwave-assisted extraction techniques. Mechanical pressing and solvent extraction are more popular due to the relatively lower investment cost and high oil yields, respectively (Bhuiya et al. Citation2016). Biodiesel conversion methods include dilution, micro-emulsion, thermal cracking, and transesterification (Yang et al. Citation2014). Several studies show that transesterification is the most common and widely accepted technology of biodiesel production and is presently one of the most attractive techniques (Tibesigwa, Olupot, and Kirabira Citation2021). Transesterification (alcoholysis) is a chemical reaction that involves the reaction of triglycerides and alcohol in the presence of a catalyst to form esters and glycerol (Salaheldeen et al. Citation2021). This process involves three consecutive reversible reactions; the conversion of triglycerides to diglycerides, followed by the conversion of diglycerides to monoglycerides. Glycerides are converted into glycerol, giving one ester in each step (Chyuan et al. Citation2019). Depending on the FFA content of the feedstock, biodiesel production is done either through a single step (alkali catalysis) or a two-step reaction, in which esterification precedes transesterification (Fattah et al. Citation2020). The critical factors in the biodiesel production process are the availability of the raw materials, the type and concentration of the catalyst, the mole ratio of oil to alcohol, the reaction temperature, the reaction time, the mixing intensity, the water content, and the stirring speed. An increase in temperature strongly affects the transesterification reaction resulting in higher reaction rates and product yields (Ahmed Elgharbawy et al. Citation2021). For Jatropha oil, the highest conversion was reported at 55°C for lipase catalyst and 50°C for cottonseed oil (Neupane Citation2022). The viscosity of biodiesel increases when the reaction temperature drops below 50 ◦C (Sabapathy et al. Citation2021).
Second-generation biodiesel and its blends, produced in different regions globally, have been found to conform to ASTM D6751 and EN 14214 standards (Sims et al. Citation2010). The production and use of biodiesel from locally available second-generation feedstocks can contribute to reduced transport-related emissions in Uganda. However, inadequate reliable information on their suitability is a significant impediment that needs to be remedied. It is crucial to carry out physicochemical characterisations of the Fatty Acid Methyl Esters derived from Ugandan Castor, croton, and Jatropha oils, to assess their suitability for use as a blendstock for B10. The economic competitiveness of biodiesel is affected by the relatively high feedstock cost, which accounts for over 70% of the overall cost of biodiesel production (Maheshwari et al. Citation2022). This cost can be offset by proper utilisation of byproducts, proper selection of feedstock, and provision of a favourable policy regime. The Net-Present-Value of biodiesel production can be improved with the integrated co-production of solketal and glycerol carbonate, higher value-added products from glycerol (Al-Saadi, Eze, and Harvey Citation2022). For Uganda's proposed biodiesel industry, a specific analysis needs to be carried out to ascertain its economic viability. Total capital cost, total production cost, profitability, and sensitivity assessments are among the criteria that have been used in assessing the economic viability of biodiesel (Tibesigwa, Olupot, and Kirabira Citation2021). This paper analyzes the technical and economic viability of a B10 strategy for Uganda based on Castor, Croton, and Jatropha. Physicochemical characterisation of Biodiesel B100, and B10 derived from these second-generation feedstocks, was done according to ASTM D6751 standards. Also, chemical process simulation and evaluation of process economics for biodiesel production from the three feedstocks were done in this Techno-economic Assessment.
2. Materials and methods
2.1. Sourcing of oilseeds and reagents
Castor (Ricinus communis), Croton megalocarpus, and Jatropha curcas seeds used for this study were collected from Hoima (1° 25′ 0″ N, 31° 5′ 0″ E), Masaka (0° 22′ 0″ S, 31° 42′ 0″ E), and Lira (2° 20′ 0″ N, 33° 6′ 0″ E), respectively. These areas have tropical climatic characteristics (Mubiru et al. Citation2018). The fruits were harvested manually, sundried, transported in muslin bags, and stored at temperatures between 20–28°C at 75–80% relative humidity before laboratory analysis. n-hexane, methanol, H2SO4, and KOH of analytical grade used for oil extraction and biodiesel conversion, were sourced from chemical laboratory stores in Kampala City, Uganda. The biodiesel production was conducted on a laboratory scale in a batch-wise process.
2.2. Determination of the moisture content of the seeds
About 10 g of a clean sample was weighed and then dried in the oven at 80°C for 7 h, and the weight was recorded after every 2 h. The same procedure was repeated until a constant weight was obtained. After 2 h, the sample was removed from the oven and placed in the desiccator for 30 min to cool, then removed and re-weighed. The percentage moisture content in the seeds was calculated according to Equationequation 1(1)
(1) .
(1)
(1) Where, W1 is the original weight of the sample before drying and W2 is the weight of the sample after drying.
2.3. Preparation of samples and extraction of oil
Dried jatropha fruits were dehulled and split open to remove the seeds, followed by deshelling of the seeds to get the kernels. For the dried castor beans, the endocarp was removed. The kernels from jatropha seeds were dried to a moisture content of 4%. The shells and husks of the seeds were cracked and carefully removed to get the inner kernels. The kernels were ground using a mortar grinder mill model 911MPEMG100 and sieved using 0.5 mm sieve plates. Fifty grams of the meal was extracted with 350 mL of n-hexane. Oil was extracted by gently heating the mixture (solvent-to-solid ratio by weight 6:1) to a temperature of 68 °C for seven hours without interruption. Extraction time was from 7 h in a soxhlet apparatus. All chemicals used were of analytical grade (Ntalikwa Citation2021). Soxhlet apparatus was used to extract the oil from croton and castor seed. A ground sample of each was placed in a thimble and loaded into the Soxhlet extraction unit. A solid-to-solvent ratio of 0.01–0.1 g/ml, extraction time of 5 h, a temperature of 70°C, a solute-to-solvent ratio of 0.06 g/ml, and a particle size of 0.5 mm was employed. Finally, the solvent and oil were separated using a rotary evaporator, and the solvent was recovered using a condenser (Bayisa and Bullo Citation2021). The oils were further evaporated in an oven at 105 oC to eliminate residual solvent and moisture content. The solvent extraction method, using n-hexane as the solvent, was employed in extracting the oil from the ground seed meal. The choice of n-hexane as the extraction solvent is due to its non-poisonous nature, high volatility, high affinity for oil, and ease of recoverability.
2.4. Determination of the oil yield
The percentage of oil extracted was determined by measuring 10 g of the seed powder and then placed in a thimble for each of the three feedstocks separately and extracted using 60 ml n-hexane as solvent. The solvent was removed using a rotary evaporator. The oil extracted was determined as a percentage weight of the dry kernel powder using the expression in Equationequation 2(2)
(2) .
(2)
(2) Y1 and Y2 are the seed weights before and after extraction, respectively.
2.5. Physical and chemical properties of the oil
The physicochemical parameters of the extracted Castor, Croton, and Jatropha oils that were determined included: fatty acid composition, free fatty acid (FFA) composition, acid value, iodine value, saponification value, refractive index, and flashpoint. Standard American Society of Testing Methods (ASTM) and procedures or equivalent testing methods were used to determine these properties, as shown in .
Table 1. Determination of the physical and chemical properties of the raw oil.
2.6. Preparation of the biodiesel from oil
Transesterification was the process used for converting oils to biodiesel. Biodiesel conversion from Castor and Croton oils was done using single-step alkali-catalyzed transesterification reactions, as shown in .
Jatropha biodiesel was produced through a two-step reaction in which esterification preceded transesterification, as illustrated in the schematic drawing in .
2.6.1. Laboratory preparation of biodiesel from Castor and Croton oil
Castor and Croton oils were converted to biodiesel in a one-step base-catalyzed transesterification process () since their free fatty acids (FFA) compositions were found to be 0.45% and 0.14%, respectively. Castor oil was transesterified at 35°C with methanol using a 6:1 molar ratio of methanol to oil, sodium hydroxide catalyst (1% wt of oil), and residence time of 60 min. On the other hand, croton oil was transesterified at 50°C with methanol using a 6:1 molar ratio of methanol to oil, Potassium hydroxide catalyst (1% wt of oil), agitation speed of 500 rpm, and residence time of 60 min. Biodiesel was then formed with glycerin as a byproduct. The biodiesel was then separated from glycerin using a separating funnel and, repeatedly washed with warm water, dried until crystals were clear. The biodiesel was then dried to the maximum amount of allowable water content of 0.050% vol, as specified in ASTM D6751.
2.6.2. Laboratory preparation of biodiesel from jatropha oil
Jatropha oil was converted to biodiesel in a two-step process () since its FFA composition was found to be 7.95%. The first step was acid-catalyzed esterification, in which free fatty acids in the Jatropha oil were converted to methyl esters. This was followed by base-catalyzed transesterification using NaOH as the catalyst. The experimental set-up consisted of 100 ml of oil taken in a three-necked 500 ml round-bottomed flask equipped with a reflux condenser to minimise alcohol loss. The flask was placed on an electric heater with a temperature controller and magnetic stirrer. Sulfuric acid was mixed as a catalyst with methanol's required amount and transferred into the reaction medium. The reaction continued until the FFA of oil reduced to below 1%.
The reaction contents were then cooled to room temperature. The reaction product was washed with hot water until clear water flowed. The organic phase was collected and dried under a vacuum at 100°C for 30 min. The dried sample (50 ml) was put into a three-necked 500 ml. round-bottomed flask equipped with a reflux condenser for base-catalyzed transesterification (second step). Sodium hydroxide pellets were mixed with methanol. The molar ratio of methanol to oil was taken in excess at varying amounts for the total conversion of triglycerides to biodiesel. The flask was placed on an electric heater at a temperature of 60°C and a magnetic stirrer of speed 350 rpm for 60 min.
After completing the process, the mixture was allowed to settle for 8 h and then poured into a separatory funnel to draw off the bottom layer of glycerin, extra methanol, catalyst, and other byproducts. The pH of the biodiesel layer was measured, and appropriate amounts of phosphoric acid were added to the biodiesel layer to neutralise the catalyst residue. The upper layer of methyl ester or biodiesel was washed several times with warm water to remove methanol, residual catalyst, and soaps until clear crystals were formed. During the washing process, gentle agitation was required to avoid the emulsion. After separating the layer for 30 min, the wash water layer was drained off from the bottom of the separating funnel. The biodiesel layer was filtered to remove impurities, and then the biodiesel was heated up to 100°C for 150 min to remove any remaining water. The biodiesel was tightly sealed and stored at −2°C, awaiting analysis.
2.6.3. Optimisation of jatropha biodiesel production process
a) Determination of Methanol: FFA ratio, residence time, acid concentration, and temperature for jatropha oil esterification (first step)
The acid value was determined as per the ISO 660:2009(en), following the washing of the sample with distilled water to remove any residue catalyst. The esterification catalyst used was sulphuric acid at concentrations of 3 and 7 wt% relative to the total acidity, with oleic acid as the free fatty acid. Free fatty acids were esterified with anhydrous methanol, using a methanol/oleic mole ratio of 10:1–80:1 for both acid concentrations. The influence of temperature on the esterification rate was studied at a fixed methanol/oleic ratio of 60:1, the two catalyst concentrations, and temperatures of 40, 45, 50, 55, and 60°C.
b) Determination of optimal conditions for jatropha oil transesterification (second step)
Keeping catalyst concentration (1 wt%) and temperature (60°C) constant, the transesterification reaction was performed under varying methanol: oil ratios of 1:1 - 8:1 for 60 mins, and corresponding percent conversions to biodiesel were determined. The transesterification reaction was performed under various ratios of methanol: oil (1:1–10:1) at a constant temperature of 60 oC and 1 wt% NaOH concentration. Keeping all reaction conditions constant and changing only temperature, the effect of temperature was studied at temperatures of 40,45,50,55,60, and 65 oC.
2.7. Preparation of B10 biodiesel blend
The Castor, Croton, and jatropha biodiesel blends (B10) were produced by heating 90cm3 of petrodiesel in a 250cm3 beaker at 50°C on a hotplate magnetic stirrer agitating at 600 rpm. Then 10 cm3 of biodiesel was also added and allowed under the same conditions for 20 min.
2.8. Physicochemical properties of the biodiesel B100 and B10 blend
The physical and chemical properties of the produced biodiesel B100 and B10 blends, which are listed in , were determined following ASTM D6751.
Table 2. Determination of the fuel properties of the biodiesel B100.
2.9. Statistical analysis
The tests were done in triplicates, and the mean was reported. Descriptive statistics during data analysis were done on Graph pad prism version 9.2.0 software. Results with a P-value < 0.05 were taken as significant.
2.10. Process simulation and optimisation of biodiesel from jatropha oil
The alkali-catalyzed transesterification process for castor and croton biodiesel production and the two-step process for converting Jatropha oil to biodiesel were simulated by ASPEN Plus V11. Because of the presence of polar compounds in the process, non-random two liquid (NRTL) was the thermodynamic model selected for this simulation. Process descriptions for Biodiesel Conversion from Castor and Croton Oils using alkali-transesterification are summarised in Appendix A and the Process Flow Diagram in Appendix B. Similarly, those for the two-step conversion process for Jatropha oil to biodiesel are shown in Appendices C and D, respectively. Assumptions made for the simulation are listed in Appendix E.
2.11. Assessment of process economics
The criteria used to determine the economic viability of biodiesel production included the total capital investment, the total operating cost estimation, and profitability analysis. The total capital investment was divided into fixed and working capital costs. Some of the parameters used for economic analysis, including the plant capacity, plant lifetime, and production rate of biodiesel from different oils, are listed in . Plant capacity for biodiesel production was calculated based on Uganda's biofuels blending mandate (MEMD Citation2018b), which will require all imported petroleum products to be blended with 10% biofuels (MEMD Citation2016). The plant capacity was therefore estimated to be about 10% of total Ugandan diesel imports per year, which are 1.03 billion litres (MEMD Citation2022). This translates to an annual requirement of 100 million litres of biodiesel for blending with petroleum diesel used in this analysis. Projected flow rates for jatropha, croton, and Castor oil were calculated in the ASPEN simulation using optimal parameters (methanol to oil ratio, temperature, residence time) obtained from experimental production of biodiesel from jatropha, croton, and Castor oil. A plant lifetime of 20 years, a cost price per litre of US$3 for each oil, and a biodiesel selling price of US$ 1.5 per litre were assumed. These prices compare with the prevailing average prices of refined oil and diesel in Uganda.
Table 3. Parameter values used in the analysis.
Fixed capital costs included the costs of equipment, installation, piping, instrumentation, electrical, building, utilities, storage, site development, ancillary buildings, design, contractor's fee, and contingencies. contains estimations for equipment considered for biodiesel production from the three feedstocks. The Total Capital Investment comprising fixed and working capital costs are summarised in .
Table 4. Estimation of equipment costs.
Table 5. Estimation of Total Capital Investment
The total operating cost estimation involved the cost needed to run the project. These consisted of variable costs, fixed costs, and general expenses. Variable costs included costs of raw materials and utilities. Fixed costs included the cost of maintenance, operating labour, supervision, plant overheads, capital charges, Insurance rates, taxes, and Royalties. Computations of operating costs for jatropha, croton, and castor oil are included in .
Table 6. Estimation of Total Operating Costs.
The Aspen Process Economics Analyser was used for equipment sizing and cost estimation prior to profitability analysis/computation of the net present value (NPV). Appendix G is the economic model applied in the calculation of NPV. Sensitivity analysis was conducted for biodiesel production processes to investigate the effects on profitability resulting from changes in the cost of feedstocks and the selling price of biodiesel.
3. Results and discussion
3.1. Moisture and oil content of the seeds
The moisture contents obtained for the Castor, Croton, and jatropha seed samples were 4%, 3%, and 10%, respectively. Similar moisture contents obtained in previous studies included 4.15% (Mohammed, Danjuma Muhammed, and Gutti Citation2017), and 9.1% (Moulana, Supardan, and Aina Citation2013), for Castor and Jatropha, respectively. However, differences in the moisture contents in the same seed types may occur due to the differences in humidity, soil fertility, and geographical conditions. Very high moisture content may also be due to the poor storage and handling facilities. If kept dry and stored at optimum conditions, seeds with moisture contents of 6–10% can have shelf lives of up to 12 months without loss of oil content (Gonfa et al., Citation2019 ). The moisture content is a determinant of the quantity, physical properties, and shelf life of the extracted oil(Garnayak et al. Citation2008). The oil yields obtained were 29.5%. 36% and 35.6%, and were in the same range as those for previous studies for Castor (Isah Citation2006), Croton (Kafuku and Mbarawa Citation2010), and jatropha (Ong et al. Citation2011), respectively.
3.2. Assessment of the physical and chemical properties of the oil
3.2.1. Fatty acid compositions
contains the obtained fatty acid compositions of castor oil, croton, and jatropha. The fatty acid profiles are consistent with findings from previous studies for castor oil (Aldo Okullo, Ogwok, and Ntalikwa Citation2017) and croton megalocarpus oil (Kafuku and Mbarawa Citation2010), and jatropha oil (Ong et al. Citation2013). Ricinoleic acid, the abundant fatty acid in castor oil, accounts for its high viscosity and miscibility in all proportions, with short-chain alcohols, including methanol, for the transesterification process for biodiesel conversion (Owolabi, Usman, and Onoh Citation2017).
Table 7. Fatty acid profile for castor, croton, and jatropha oil.
3.3.3. Physical and chemical properties of the oils
Results obtained for acid value (AV), saponification value (SV), refractive index (RI), and flash point (FP) from the analysis of the castor, croton, and jatropha oil samples, are summarised in . The acid value shows the amounts of fatty acids present in the oil. Fats and oils contain both saturated fatty acids and unsaturated fatty acids. The higher the number of fatty acids, the higher the acid value of the oil. Only croton oil had an acid value complying with the maximum AV of 0.5 mg KOH/g that ASTM D6751 stipulates. Therefore, these oils need to be processed further to biodiesel before use in ICEs to avoid corrosion and engine deposits, particularly in the fuel injectors, associated with high fuel acidity.
Table 8. Characteristics of the oil.
Castor and Jatropha oils had Iodine values (IV) within the ASTM D 6751 limit of 120 g I2/100 g. However, croton oil's IV was higher than the limit. The iodine value determines the level of oils’ unsaturation and the number of double bonds (Moser Citation2009). The iodine value is related to oxidative stability and reflects an oil or fat's propensity to oxidise, polymerise, and form engine deposits(Bart, Palmeri, and Cavallaro Citation2010). The saponification values of all the oils were all within the ASTM maximum limit of 370 mgKOH/g of oil. High saponification values show a higher propensity for soap formation and affect the yield of biodiesel produced (Ibeto, Ofoefule, and Ezewgue Citation2011).
The refractive index indicates the level of unsaturation of the fatty acid. It affects the engine performance by directly affecting the calorific value and the viscosity. All the oils had a refractive index within the ASTM limits. The flashpoint is the temperature at which the substance burns when exposed to heat. The flashpoint helps to monitor the safety and safe storage of the oil. As shown in , all the oils had a flashpoint of more than 130°C. The ASTM D6751 recommended limit for oils is above 130°C. The higher the flashpoint, the safer the oil and easier to transport (Lu et al. Citation2009a).
3.4. Physical and chemical properties of the biodiesel B100
Results obtained for the physical and chemical properties of the biodiesel B100 are summarised in and compared with the limits specified in ASTM D6751 for biodiesel and petroleum diesel. Castor, croton, and jatropha biodiesel B100 all conformed to the ASTM D6751 limits. Castor biodiesel had the highest viscosity, and croton had the lowest viscosity. A high viscosity interferes with the fuel injection process (Canakci and Sanli Citation2008). Kinematic viscosity is an important fuel property that shows the resistance of the flow of the liquid (Ong et al. Citation2011). Viscosity increases with the increase in chain length and decreases with an increase in double bonds (Canakci and Sanli Citation2008).
Table 9. Physical and Chemical characteristics of the Biodiesel B100.
The calorific values of Castor, Croton, and jatropha biodiesel B100 were all lower than the lower limit of ASTM D6751 for petrodiesel. Jatropha biodiesel B100 had a higher calorific value than castor and croton biodiesel B100. Therefore, Jatropha B100 has better combustion properties. This finding is consistent with other studies, and the relatively lower calorific value of biodiesel B100 is attributed to its higher oxygen content (Teixeira da Silva de La Salles et al. Citation2010). However, (Canakci and Sanli Citation2008) reported a higher calorific value of biodiesel compared to conventional diesel.
The ASTM D6751 limits for the flashpoint for biodiesel are between 100oC-170°C. However, those for conventional diesel are between 60oC-80°C. The higher flashpoint for biodiesel implies that it is safer/easier to handle and has fewer volatile impurities (Williams et al. Citation2011). Flashpoints for Castor and Croton B100 were within the ASTM D6751 limits for biodiesel. However, jatropha had a slightly higher flashpoint, similar to the findings by (Ong et al. Citation2011). The specific gravities of biodiesel B100 from Croton and Jatropha were lower than the lower ASTM D6751 limit for biodiesel. However, that for Castor B100 was within range. The specific gravity of biodiesel affects the combustion properties of the fuel.
3.5. Physical and chemical properties of B10 blend
Results obtained for the physical and chemical properties of the B10 are summarised in and compared with the limits specified in ASTM D6751 for biodiesel and petroleum diesel. Kinematic viscosities for the Castor, Croton, and Jatropha B10 blends all conform to the ASTM D6751 standard limits for petroleum diesel and with the ASTM D7476 standard for B6 to B20. Croton B10 had the lowest viscosity and therefore has better fuel injection properties (Ali et al. Citation2015). The calorific values for Castor, Croton, and Jatropha B10 were higher than the 35 MJ/Kg stipulated in the EN 14214 standard for biodiesel. However, they were slightly lower than ASTM petro-diesel.
Table 10. Physical and chemical characteristics of the B10 blend.
Flashpoints of the biodiesel B10 blends were lower than the standard ASTM D6751 limits for B100 but within the ASTM than for petro-diesel. Hence Castor, Croton, and Jatropha B10 would be safer to transport and store than conventional diesel (Lu et al. Citation2009) (Williams et al. Citation2011). The Castor, Croton, and jatropha B10 biodiesel all had specific gravities that conformed to ASTM D6751 for B100 and ASTM D7467 for B6 to B20.
3.6. Optimal conditions for the jatropha biodiesel production process
3.6.1. Jatropha oil esterification
(i) Methanol: FFA ratio, residence time, and acid concentration
shows the variation of the acid value with the methanol: FFA mole ratio at sulphuric acid concentrations of 3 and 7 wt%. In both cases, the reaction rate increased with the increasing mole ratio. Above 70:1, however, the increase was negligible, so this ratio was adopted as the experimental limit in order to avoid unnecessarily increasing operational costs and the reactor size. On the other hand, an increased catalyst concentration increased the esterification rate. Thus, at a methanol: FFA mole ratio of 50:1, a catalyst concentration of 3% provided an acid value of 3.85 mg KOH/g oil within 120 min, whereas one of 7 wt% gave 2 mg KOH/g oil at the same time. A methanol: FFA mole ratio of 70:1 and 3 wt% was adopted as optimal, and the influence of temperature studied was examined.
Figure 3. Variation of acid value with Methanol: FFA mole ratio at sulphuric acid concentration of 3 wt% and 7%.

(ii) Temperature
As illustrated in , raising the temperature increased the esterification rate. The highest rate was obtained at 60°C, which is close to the boiling point of methanol at atmospheric pressure. A methanol: FFA mole ratio of 70:1, a sulphuric concentration of 3%, residence time of 120 min, and a temperature of 60 °C provided an acid value below 0.5 mg KOH/g oil, which is the ASTM D 6751 and EN 14214 maximum recommended level for ensuring a good yield of FAME while facilitating their separation from glycerin in the transesterification reaction. Higher acid values result in saponification by reaction with the catalyst, decreasing surface tension and facilitating emulsification.
3.6.2. Transesterification process for biodiesel production
(i) Effect of Methanol: Oil ratio on conversion
shows that increasing the methanol: oil mole ratio increases the reaction rate. It is also noteworthy that any ratio greater than 7.5: 1 has a small effect on the conversion percentage. This is because increasing the ratio would increase the amount of methanol, and it would be difficult to recover all the methanol that has not been treated, and more energy will be used. Also, some methanol can be lost through evaporation.
(ii) Effect of NaOH (alkali catalyst) concentration on transesterification
As illustrated in , increasing the catalyst concentration increases the reaction conversion until it reaches constant conversion at 0.95 wt.%. of NaOH. Therefore, increasing the concentration above 0.95 wt% would be unnecessary, especially at high temperatures, since there is very little change in conversion.
(iii) Effect of reaction temperature on percent conversion
With all reaction conditions kept constant, as shown in the simulation results in , increasing reaction temperature increased reaction conversion at the same reaction time. It was also noted that with higher residence time, the effect of increasing temperature above 60°C on conversion is negligible and would be energy wasting.
3.7. Economic analysis
Based on the computed costs, including total capital investment and operating costs that were applied to the model in Appendix G, the Net Present Values were determined. Profitability analysis for biodiesel production processes from each of the three feedstocks gave negative NPVs, as illustrated in . Therefore, based on these results, the production of the blendstocks for the production of B10 from any of the three feedstocks (Castor, croton, or Jatropha) is not economically viable. This is mainly due to the high costs of biodiesel feedstocks. To attract investment in biodiesel production, it may be crucial for Government to put in place a subsidy and tax incentive scheme.
Sensitivity analysis results in shows that an increase in feedstock cost resulted in reduced NPV and increased NPV for decreasing feedstock costs. As shown in , a reverse trend was observed for increasing and reducing biodiesel selling prices. These biodiesel projects can only break-even at feedstock costs lower than $1/kg or with over 1.7 times increase in biodiesel selling price. However, high selling prices can inhibit biodiesel use. Therefore, competitive feedstock costs and product selling prices are crucial factors for the success of a B10 biodiesel project.
4. Conclusions
This paper assessed the techno-economic viability of biodiesel production in Uganda using second-generation feedstocks, including castor, croton, and jatropha. Physicochemical characterisation of the oils, B100 (blendstocks), and B10 blends confirmed their compliance with ASTM D6751 quality standards. Castor and croton biodiesel were synthesised using alkali catalyzed transesterification process. A two-step process, starting with esterification and followed by alkali-transesterification, was applied for jatropha biodiesel conversion due to the high % FFA found in the jatropha oil. Negative Net Present Values were obtained from the profitability analysis for producing B100 blendstocks from the three feedstocks used in B10 blending. Therefore, based on these results, the production of the biodiesel blendstocks for the production of B10 from any of the three feedstocks (castor, croton, or jatropha) is not economically viable. Sensitivity analyses showed that an increase in feedstock cost resulted in reduced NPV and vice versa for reduced feedstock costs or higher biodiesel selling prices. The study established that it is technically viable to produce biodiesel blendstocks for B10 from castor, croton, and jatropha. The findings of this techno-economic assessment contributed to closing the knowledge gap on the viability of a B10 mandate based on East African second-generation feedstocks. It revealed that for a B10 policy based on these locally available second-generation biodiesel feedstocks to be viable, interventions would be needed to lower feedstock costs and guarantee competitive biodiesel selling prices. Future studies should explore the effects of revenue from biodiesel byproducts on the profitability of B10. Also, the impact of government subsidies and tax incentives on the economic viability of a B10 policy can be assessed.
Acknowledgments
The authors acknowledge with gratitude the remote training undertaken on Chemical Process Design and Techno-economic Assessments in a Developing Country Context at the Thayer School of Engineering at Dartmouth College, USA, courtesy of BioInnovate Africa. We also extend our sincere thanks to our Research Assistants/Chemical Engineers team: Achileo Kivumbi, Serwadda Joseph, and Kasule Hannah Talinda.
Disclosure statement
No potential conflict of interest was reported by the author(s).
References
- Ahmed Elgharbawy, A., Wagih Sadik, Olfat Sadek, and Mosaad Kasaby. 2021. “Transesterification Reaction Conditions and low-Quality Feedstock Treatment Processes for Biodiesel Production- A Review.” Journal of Petroleum and Mining Engineering 0 (0): 98–103. doi:10.21608/jpme.2021.67482.1076.
- Al-Saadi, L. S., V. C. Eze, and A. P. Harvey. 2022. “Techno-economic Analysis of Processes for Biodiesel Production with Integrated co-Production of Higher Added Value Products from Glycerol.” Biofuels 13 (4): 489–496. doi:10.1080/17597269.2020.1767495.
- Aldo Okullo, A. K. Temu, P. Ogwok, and J. W. Ntalikwa. 2017. “Physico-Chemical Properties of Biodiesel from Jatropha and Castor Oils.” International Journal of Renewable Energy Research 2 (1): 47–52.
- Ali, E., A. Supervisor, P. I. Rashid, A. Co -Supervisor, P. Sharif, and M. Musameh. 2015. “Faculty of Graduate Studies, An-Najah National University-Nablus.” Physics.
- Atabani, A. E., and S. César. 2014. “Calophyllum Inophyllum L . – A Prospective non-Edible Biodiesel Feedstock. Study of Biodiesel Production, Properties, Fatty Acid Composition, Blending and Engine Performance.” Renewable and Sustainable Energy Reviews 37: 644–655. doi:10.1016/j.rser.2014.05.037.
- Bart, J. C. J., N. Palmeri, and S. Cavallaro. 2010. “Emerging new Energy Crops for Biodiesel Production.” Biodiesel Science and Technology, 226–284. doi:10.1533/9781845697761.226.
- Bayisa, Y. M., and T. A. Bullo. 2021. “Optimization and Characterization of oil Extracted from Croton Macrostachyus Seed for Antimicrobial Activity Using Experimental Analysis of Variance.” Heliyon 7 (9), doi:10.1016/j.heliyon.2021.e08095.
- Bhuiya, M. M. K., M. G. Rasul, M. M. K. Khan, N. Ashwath, and A. K. Azad. 2014. “Second Generation Biodiesel : Potential Alternative to- Edible Oil-Derived Biodiesel.” Energy Procedia 61: 1969–1972. doi:10.1016/j.egypro.2014.12.054.
- Bhuiya, M. M. K., M. G. Rasul, M. M. K. Khan, N. Ashwath, and A. K. Azad. 2016. “Prospects of 2nd Generation Biodiesel as a Sustainable Fuel — Part : 1 Selection of Feedstocks, oil Extraction Techniques and Conversion Technologies.” Renewable and Sustainable Energy Reviews 55: 1109–1128. doi:10.1016/j.rser.2015.04.163.
- Borhanipour, M., P. Karin, M. Tongroon, N. Chollacoop, and K. Hanamura. 2014. “Comparison Study on Fuel Properties of Biodiesel from Jatropha, Palm and Petroleum Based Diesel Fuel.” SAE Technical Paper Series 1 (August), doi:10.4271/2014-01-2017.
- Canakci, M., and H. Sanli. 2008. “Biodiesel Production from Various Feedstocks and Their EVects on the Fuel Properties.” Journal of Industrial Microbiology & Biotechnology 35: 431–441. doi:10.1007/s10295-008-0337-6.
- Chrysa, G. 2020. Analysis: EU Biofuels 2020 Policy Framework Headache for Blenders.
- Chyuan, H., J. Milano, A. Susan, M. Haji, A. Halim, C. Wang, T. Meurah, et al. 2019. “Biodiesel Production from Calophyllum Inophyllum - Ceiba Pentandra oil Mixture : Optimization and Characterization.” Journal of Cleaner Production 219: 183–198. doi:10.1016/j.jclepro.2019.02.048.
- Fattah, I. M. R., H. C. Ong, T. M. I. Mahlia, M. Mofijur, and A. S. Silitonga. 2020. State of the Art of Catalysts for Biodiesel Production 8 (June): 1–17. doi:10.3389/fenrg.2020.00101.
- Garnayak, D. K., R. C. Pradhan, S. N. Naik, and N. Bhatnagar. 2008. “Moisture-dependent Physical Properties of Jatropha Seed (Jatropha Curcas L.” Industrial Crops and Products 27 (1): 123–129. doi:10.1016/J.INDCROP.2007.09.001.
- Gonfa, Y., K. Jorge, and M. Marchetti. 2019. “Temperature and Pretreatment Effects on the Drying of Different Collections of Jatropha Curcas L. Seeds.” SN Applied Sciences 1(8): 1–11. doi:10.1007/s42452-019-0969-3.
- Ibeto, C. N., A. U. Ofoefule, and H. C. Ezewgue. 2011. Fuel Quality Assessment of Biodiesel Produced from Groundnut Oil (Arachis hypogea) and its Blend with Petroleum Diesel (pp. 798–803). American Journal of Food Technology. doi:10.3923/ajft.2011.798.803.
- IEA. 2021. Statistics report Key World Energy Statistics 2021.
- IPCC. 2018. Emissions from the Transport Sector- : 599–670.
- Isah, A. G. 2006. “Production of Detergent from Castor Oil.” Leonardo Electronic Journal of Practices and Technologies 9: 153–160.
- Kafuku, G., and M. Mbarawa. 2010. “Biodiesel Production from Croton Megalocarpus oil and its Process Optimization.” Fuel 89 (9): 2556–2560. doi:10.1016/j.fuel.2010.03.039.
- Lu, H., Y. Liu, H. Zhou, Y. Yang, M. Chen, and B. Liang. 2009. “Production of Biodiesel from Jatropha Curcas L. Oil.” Computers & Chemical Engineering 33 (5): 1091–1096. doi:10.1016/J.COMPCHEMENG.2008.09.012.
- Maheshwari, P., M. B. Haider, M. Yusuf, J. J. Klemeš, A. Bokhari, M. Beg, A. Al-Othman, R. Kumar, and A. K. Jaiswal. 2022. A review on Latest Trends in Cleaner Biodiesel Production: Role of Feedstock, Production Methods, and Catalysts. In Journal of Cleaner Production (Vol. 355). Elsevier Ltd. doi:10.1016/j.jclepro.2022.131588.
- MEMD. 2016. The Biofuels Bill.
- MEMD. 2018a. The Biofuels Act, 2018.
- MEMD. 2018b. The Biofuels Act, 2018.
- MEMD. 2022. Petroleum Imports data- Uganda 2019 to 2022.
- MEMD & NOVI Energy. 2011. Balancing Biofuels and Food Security. 224.
- Mohammed, Danjuma H., D. Danjuma Muhammed, and B. Gutti. 2017. “Extraction and Characterization of Castor Seed Oil.” International Journal of Scientific & Engineering Research 8 (4).
- Moser, B. R. 2009. “Biodiesel Production, Properties, and Feedstocks.” In Vitro Cellular & Developmental Biology - Plant 2009 45:3 45 (3): 229–266. doi:10.1007/S11627-009-9204-Z.
- Moulana, R., Md Supardan, and W. Aina. 2013. Effect of Moisture Content and amount of Hexane on in-situ Transesterification of Jatropha Seeds for Biodiesel Production 1.
- Mubiru, D. N., M. Radeny, F. B. Kyazze, A. Zziwa, J. Lwasa, J. Kinyangi, and C. Mungai. 2018. Climate Trends, Risks and Coping Strategies in Smallholder Farming Systems in Uganda. (pp. 22, 4–21). Climate Risk Management. doi:10.1016/J.CRM.2018.08.004.
- Neupane, D. 2022. “Biofuels from Renewable Sources, a Potential Option for Biodiesel Production.” Bioengineering 10 (1): 29. doi:10.3390/bioengineering10010029.
- Ntalikwa, J. W. 2021. “Solvent Extraction of Jatropha Oil for Biodiesel Production: Effects of Solvent-to-Solid Ratio, Particle Size, Type of Solvent, Extraction Time, and Temperature on Oil Yield.” Journal of Renewable Energy 2021: 1–8. doi:10.1155/2021/9221168.
- Ong, H. C., T. M. I. Mahlia, H. H. Masjuki, and R. S. Norhasyima. 2011. “Comparison of Palm oil, Jatropha Curcas and Calophyllum Inophyllum for Biodiesel : A Review.” Renewable and Sustainable Energy Reviews 15 (8): 3501–3515. doi:10.1016/j.rser.2011.05.005.
- Ong, H. C., A. S. Silitonga, H. H. Masjuki, T. M. I. Mahlia, W. T. Chong, and M. H. Boosroh. 2013. “Production and Comparative Fuel Properties of Biodiesel from non-Edible Oils : Jatropha Curcas, Sterculia Foetida and Ceiba Pentandra.” Energy Conversion and Management 73: 245–255. doi:10.1016/j.enconman.2013.04.011.
- Owolabi, Rasheed Uthman, M. A. Usman, and E. N. Onoh. 2017. “Ricinoleic Acid Methyl Ester (Rame): Synthesis, Characterization and Determination of Optimum Process Parameters.” Anadolu University Journal of Science and Technology A - Applied Sciences and Engineering 18 (1): 262–262. doi:10.18038/aubtda.300437.
- Pandey, V. C., K. Singh, J. S. Singh, A. Kumar, B. Singh, and R. P. Singh. 2012. “Jatropha Curcas: A Potential Biofuel Plant for Sustainable Environmental Development.” Renewable and Sustainable Energy Reviews 16 (5): 2870–2883. doi:10.1016/j.rser.2012.02.004.
- Romano, S. D., and P. A. Sorichetti. 2011. “Dielectric Spectroscopy in Biodiesel Production and Characterization.” Green Energy and Technology 29, doi:10.1007/978-1-84996-519-4.
- Sabapathy, S. P., A. M. Ammasi, E. Khalife, M. Kaveh, M. Szymanek, G. K. Reghu, and P. Sabapathy. 2021. “Comprehensive Assessment from Optimum Biodiesel Yield to Combustion Characteristics of Light Duty Diesel Engine Fueled with Palm Kernel oil Biodiesel and Fuel Additives.” Materials 14 (15), doi:10.3390/ma14154274.
- Salaheldeen, M., A. A. Mariod, M. K. Aroua, S. M. A. Rahman, M. E. M. Soudagar, and I. M. R. Fattah. 2021. Current State and Perspectives on Transesterification of Triglycerides for Biodiesel Production. In Catalysts (Vol. 11, Issue 9). MDPI. doi:10.3390/catal11091121.
- Silitonga, A. S., H. H. Masjuki, T. M. I. Mahlia, H. C. Ong, W. T. Chong, and M. H. Boosroh. 2013. “Overview Properties of Biodiesel Diesel Blends from Edible and non-Edible Feedstock.” Renewable and Sustainable Energy Reviews 22 (October 2017): 346–360. doi:10.1016/j.rser.2013.01.055.
- Sims, R. E. H., W. Mabee, J. N. Saddler, and M. Taylor. 2010. “An Overview of Second Generation Biofuel Technologies.” Bioresource Technology 101 (6): 1570–1580. doi:10.1016/j.biortech.2009.11.046.
- Teixeira da Silva de La Salles, K., S. M. P. Meneghetti, W. Ferreira de La Salles, M. R. Meneghetti, I. C. F. dos Santos, J. P. V. da Silva, S. H. V. de Carvalho, and J. I. Soletti. 2010. “Characterization of Syagrus Coronata (Mart.) Becc. oil and Properties of Methyl Esters for use as Biodiesel.” Industrial Crops and Products 32 (3): 518–521. doi:10.1016/J.INDCROP.2010.06.026.
- Tibesigwa, T., P. W. Olupot, and J. B. Kirabira. 2021. “The Critical Techno-Economic Aspects for Production of B10 Biodiesel from Second Generation Feedstocks: A Review.” International Journal of Sustainable Energy, 1–21. doi:10.1080/14786451.2021.1976181.
- UNEP. 2012. Biofuels and Biodiversity. 65.
- Vignesh, P., A. Remigious, P. Kumar, S. Ganesh, V. Jayaseelan, K. Sudhakar, and N. S. Ganesh. 2021. “Biodiesel and Green Diesel Generation: An Overview.” Oil & Gas Science and Technology 76 (6), doi:10.2516/ogst/2020088ï.
- Wakil, M. A., M. A. Kalam, H. H. Masjuki, A. E. Atabani, and I. M. Rizwanul Fattah. 2015. “Influence of Biodiesel Blending on Physicochemical Properties and Importance of Mathematical Model for Predicting the Properties of Biodiesel Blend.” Energy Conversion and Management 94: 51–67. doi:10.1016/j.enconman.2015.01.043.
- Williams, A., J. Luecke, R. L. Mccormick, A. Geisselmann, K. Voss, K. Hallstrom, M. Leustek, J. Parsons, and H. Abi-Akar. 2011. Impact of Biodiesel Impurities on the Performance and Durability of DOC, DPF and SCR Technologies Preprint Rasto Brezny Manufacturers of Emission Controls Association.
- Yang, L., M. Takase, M. Zhang, T. Zhao, and X. Wu. 2014. “Potential non-Edible oil Feedstock for Biodiesel Production in Africa: A Survey.” Renewable and Sustainable Energy Reviews 38: 461–477. doi:10.1016/j.rser.2014.06.002.
- Zhang, Y., et al. 2003. “Biodiesel Production from Waste Cooking oil : 1.” Process Design and Technological Assessment 89: 1–16. doi:10.1016/S0960-8524(03)00040-3.
Appendices
Appendix A. Process description for biodiesel conversion from castor and croton oils using alkali –transesterification
Appendix B. Process flow diagram for biodiesel conversion from castor and croton oils using alkali –transesterification
Appendix C. Process description for biodiesel conversion from jatropha oil using a two-step process
Appendix D. Process flow diagram for biodiesel conversion from jatropha oil using a two-step process
Appendix E. Simulation assumptions
Some assumptions considered in this work are outlined below:
1) Laboratory-scale optimised reaction conditions of castor and croton were assumed to be appropriate for large-scale production and set as the reactor(s) operating conditions in Aspen Plus software.
2) The transesterification reactor is a perfectly mixed flow (continuous stirred tank reactor).
3) Anhydrous alcohol and anhydrous catalyst were used.
4) Oil feed is 100% solid particle-free.
5) Multi-stage distillation was used to recover the excess methanol, as well as in the final purification of biodiesel and glycerine products since the large difference in the boiling points of the components facilitated distillation (Zhang et al. Citation2003)