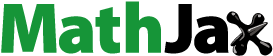
ABSTRACT
Biomethanol is a significant chemical in biochemicals and biofuels. Molasses is interested in producing biogas and biohydrogen for biomethanol. Biohydrogen, Enterobacter aerogenes digested molasses obtaining value organic chemicals and biohydrogen in appropriate ratios of H2/CO2 then transforming to H2/CO by RWGS. Biogas was converted to syngas then methanol synthesis. The biogas pathway was 4 steps and it was appropriate for sailing single product as biomethanol. The biohydrogen pathway was 3 steps and obtained income both valuable substances and biomethanol. Operating expenditure for 1 kg methanol by biohydrogen experiment and theory were 4.4148 and 4.0912 USD comparing with biogas 0.3446 USD based on commercial methanol price 0.449 USD/kg. The sale prices per kg of biomethanol by biohydrogen were 6.7243 USD (Exp.) and 5.7500 USD (Theory) comparing with biomethanol sailing from biogas pathway at 0.4486 USD. Margin caps were 30.19%, 39.66%, and 40.55% for biogas pathway, biohydrogen experiment and theory route respectively.
1. Introduction
Considering global warming, petroleum had been substituted by biofuels, such as ethanol and biodiesel, over the past three decades. Biofuels strongly supported the agricultural sector and bio-based industries. Biofuels are renewable and can act as replacement for petroleum-based fuel but they also emit carbon dioxide after getting into combustion engines. Considering the advantage of battery storage, electric vehicles are currently dominating internal combustion vehicles, which causes disruption effects on the transformation of the biofuel era to the carbon neutral era. The domino effect is on ethanol and biodiesel production systems and has a chain effect on the agricultural raw materials that are sources of these biofuel chains. Molasses is obtained from the sugar industry and is commonly used as a raw material for fertiliser production, animal feed ingredients, and biogas production for use in electricity generation and bioethanol generation. Ethanol was produced for blending in different ratios in gasoline depending on the policy of each country. Electric vehicles have currently gradually dominated gasoline vehicles, and using molasses for ethanol production has gradually decreased. Moreover, global molasses price sourced from Tridge global market has been continuously decreasing since 2011 (over 1 USD/kg) till now (0.10 USD/kg) in each year (Tridge Exhibition Citation2021) Molasses is a significant bio-renewable source for producing biomethane and biohydrogen (Detman et al. Citation2017). Both cases generate CO2 in the gas phase: biogas contains methane (CH4), carbon dioxide (CO2), and a small amount of hydrogen sulfide (H2S), while biohydrogen comprises hydrogen (H2) and CO2 (Detman et al. Citation2017). Directly using biogas and biohydrogen leads to CO2 emission to the atmosphere. Therefore, integrating biotechnology with thermochemical research aims to innovate the current research on using molasses for biogas and biohydrogen production and transforming both to biomethanol.
Methanol is crucial for chemical and fuel industries and acts as a solvent, thinner, and a reactant in biodiesel and petrochemicals. Thus, methanol is forecasted in the methanol market to grow from 110 million metric tons in 2018–220 in 2030 (Infoholic Research LLP Citation2019; Imarc Impactful Insights Citation2021; Grand View Research Citation2022; Prismane Consulting Citation2018; Mordor Intelligence Citation2022; Polaris Market Research Citation2019; Triton Market Research Citation2022; Inkwood Research Citation2019; Statista Research Department Citation2022). Commercial methanol (black/gray methanol) had been traditionally produced from steam reforming of coal or natural gas. However, the last decade focused on bio/green methanol, which has been widely studied to substitute conventional methanol. Consequently, the methanol in the market is divided into two groups: non-renewable and bio/green methanol. The methanol projection by the Council on Energy, Environment and Water and International Energy Agency advised that the cost of green methanol will be gradually decreased due to its competition with gray/black methanol in 2030 (Joshi Citation2019). The advantages of transforming molasses passing biogas and biohydrogen pathway to produce biomethanol would not only substitute bio/green methanol but also support increasing molasses usage and reduce CO2 from bioresource applications emitting to the atmosphere.
The first pathway (A) involves the application of molasses for biogas. Generally, biogas had been produced from fermented organic residues but is mostly in small and medium scales. Molasses is an abundant source for large scales of biogas production. Biogas contained approximately 55% (v/v) CH4, 43% (v/v) CO2, 2% (v/v) water, and a small amount of H2S (Janke et al. Citation2015; Suwanasri et al. Citation2015; Chaiprasert Citation2011). The transformation of molasses to biomethanol requires a four-step process as shown in . Pathway A: (1) Biogas Production (BG), wherein molasses was diluted by water and fermented under anaerobic condition to obtain crude biogas. (2) Biogas Refinery (BGR), wherein crude biogas was refined by removing H2S by bioscrubber (Nishimura and Yoda Citation1997) or Fe-EDTA solution (Thongkhao et al. Citation2019). (3) Biogas Reforming (BGF), wherein CH4 and CO2 were reacted by dry reforming (1) and steam reforming (2) to obtain syngas under Metal/Al2O3 catalyst under 600°C to 900°C in the atmosphere (Zhao et al. Citation2020). However, the optimised condition of biogas reforming was used followed by Jitrwung et al. (Citation2022a). (4) Methanol synthesis (MS), wherein H2 in syngas was hydrogenated on CO/CO2 by (4)/(5) and both reactions occurred under Cu/ZnO/Al2O3 catalyst (Sun, Metcalfe, and Sahibzada Citation1999); the optimised condition of CO hydrogenation was 170°C and 40 barg. After molasses passed through four steps, it was then transformed into crude biomethanol containing over 96% (v/v) methanol and contaminated 3% (v/v) of water, 0.02% (v/v) ethanol, and a small amount of impurities (Jitrwung et al. Citation2022b).
Figure 1. Pathway A: Molasses to biogas and biomethanol; Pathway B: Molasses to biohydrogen and biomethanol.

The second pathway (B) involves an innovation route, namely passing biohydrogen route, which had been researched by using biosugar sources, such as glucose, fructose, molasses, and glycerol. Molasses was extensively investigated due to its wide use and abundance. Moreover, molasses is the cheapest source among other sugar sources. Producing biohydrogen is close to the biogas fermentation because it is produced from biosugar sources by bacterial digestion (Özgür et al. Citation2010; Kumar et al. Citation2015). Biohydrogen obtained from molasses comprised only hydrogen (H2) and carbon dioxide (CO2). The ratio of H2/CO2 was produced on the basis of bacterial strains and conditions; thus, in the use of Enterobacter aerogenes, the ratio of H2/CO2 was 1 following the metabolic pathway of glucose (Ren et al. Citation2006). Enterobacter aerogenes was utilised in biohydrogen fermentation because its temperature of 30°C is similar to equatorial room temperature and facultative condition. H2/CO2 ratio of biohydrogen was in the range of 0.5–1.0 (Jitrwung and Yargeau Citation2015). Only three steps were required to convert molasses to biomethanol as shown in . Pathway B: (1) Biohydrogen Fermentation (BHF), wherein molasses was diluted by nutrient solution and then fermented under facultative condition obtaining crude biohydrogen. (2) Biohydrogen Conversion, wherein CO2 and H2 were reacted by reverse water gas shift (3) to obtain syngas (Daza and Kuhn Citation2016) under Cu/ZnO/Al2O3 catalyst under 500°C and atmospheric pressure; a side reaction of CO and H2O and reversed CO and H2 was observed and referred to as water gas shift (WGS) (6) (Wang et al., Citation2017). (3) MS, wherein H2 was added into CO by (4) or added into CO2 by (5), demonstrating the occurrence of both reactions under Cu/ZnO/Al2O3 catalyst at 170°C and 40 barg. Biomethanol was only three steps when passing biohydrogen pathway.
This article aims to provide a comparison using molasses for biomethanol. The comparison involved the four and three steps of molasses to biomethanol by biogas pathway and biomethanol by biohydrogen route to obtain the engineering view and cost.
Methane Reforming (MR)
(1)
(1)
(2)
(2)
Reverse Water Gas Shift (RWGS)
(3)
(3)
Methanol Synthesis (MS)
(4)
(4)
(5)
(5)
Water Gas Shift (WGS)
(6)
(6)
2. Materials and methods
2.1. Raw materials
Molasses, a byproduct of the sugar production process of Khon Kaen Sugar Industry Public Company Limited (KSL).
Simulation biogas: Mixed gas contained a ratio of CH4/CO2 55/45% (v/v) received from Thai Special Gas Co., Ltd., which referred biogas composition from Tanachewasap Co., Ltd., Thailand (Biogas plant) and RE Power Service Co., Ltd.
Simulation biohydrogen gas: Mixed gas contained a ratio of H2/CO2 40/60, 50/50, 60/40, and 70/30% (v/v) received from Thai Special Gas Co., Ltd.
The Ni/Al2O3 catalyst was a commercial grade from Tianjin Hutong Global Co., Ltd.
The Cu/ZnO/Al2O3 catalyst was a commercial grade from Xi’an Sunward Aeromat Co., Ltd.
2.2. Biohydrogen preparation and synthesis
Bacterial strain was Enterobacter aerogenes (E.A.) (TISTR 1540) obtained from the Biodiversity Research Centre of Thailand Institute of Scientific and Technological Research (TISTR).
Nutrients preparation for E.A. incubation: Before experiments, bacteria were incubated in the following prescribed media: beef extract (1.0 g/L), yeast extracts (2.0 g/L), peptone (5.0 g/L), and NaCl (5.0 g/L) were in deionised water at 24 h incubation.
The fermentation media used for the biohydrogen production contained the following: (NH4)2SO4 (4.0 g/L), KH2PO4 (4.0 g/L), Na2HPO4 (4.0 g/L), yeast extract (1.0 g/L), and MgSO4 (0.20 g/L). By contrast, the trace element solution comprises the following: 2.0 ml/L of HCl (1.0 ml/L), MnCl2.4H2O (100 mg/L), ZnCl2 (70 mg/L), H3BO3 (60 mg/L), CoCl2.6H2O (200 mg/L), CuCl2.2H2O (10 mg/L), NiCl2 (20 mg/L), and Na2MoO4.2H2O (30 mg/L).
2.3. Apparatus and analytical methods for biomethanol
The gas composition was measured by a gas analyzer from the MRU model Vario Luxx.
Bioreactor: 10 L bioreactor with a 5 L working volume from Marubishi in model MDFT-10 L ().
A pilot scale fixed-bed reactor comprised two reactors: 5 kg Ni/Al2O3 catalyst filled in the reactor (Reforming case)/5 kg Cu/ZnO/Al2O3 catalyst filled in the reactor (RWGS case) and 5 kg catalyst filled in the MS reactor. The maximum capacity for producing 5 L/day of biomethanol is given in .
Biogas/Biohydrogen pathway to biomethanol
Figure 3. Two fixed-bed reactors for reforming (RF) methanol synthesis (MS) for biogas pathway, reverse water gas shift (RWGS), and methanol synthesis (MS) for biohydrogen pathway.

Biogas composition was obtained from biogas plant companies. Simulation biogas CH4 55% (v/v) and CO2 45% (v/v) were then mixed followed by the biomethanol process comprising two step reactions: Reforming (RF) and MS reactions. By contrast, biohydrogen composition was obtained from molasses fermentation. Simulation varying ratios of biohydrogen (H2/CO2: 40/60, 50/50, 60/40, and 70/30% (v/v)) were mixed followed by the biomethanol process comprising two step reactions: RWGS and MS reactions.
The process flow diagram (PFD) is shown in . The PFD presents two types of feed: the flow rate of biogas (mixture of ratio CH4/CO2) or biohydrogen (mixed gas of ratio H2/CO2) was controlled by mass flow controller (MF-1), preheated in a heat exchanger (HX-1), and then fed to the first reactor (RX-1) for RF or RWGS reaction. The reaction was controlled temperature 600°C (RF case) or 500°C (RWGS case). After the reaction was continued in the reactor, the fluid product was generated and cooled down in a heat exchanger (HX-2). The product was condensed and trapped, and then the fluid was separated into two phases. The liquid phase was water, which was separated by opening the valve (CV-1). The gas phase was mixed gas (syngas) comprising H2, CO2, and CO, and its composition was measured by a gas analyzer before storing in a low-pressure vessel (V-1). The syngas was compressed by a compressor (CP-1) to reach the required pressure (40–50 barg) and then sent to absorption units (AB-1/2) for trapping contaminates, such as water and oil, before passing the syngas to the second reactor (RX-2). The syngas was then fed and controlled by mass flow controller (MF-2), and the methanol reaction was induced in the reactor (RX-2) under an operating temperature of 170°C and pressure of 40 barg. The fluid product was cooled down and trapped in a heat exchanger (HX-3), and the liquid or methanol was then condensed and pulled out by the valve (CV-2). The gas phase pressure was reduced to atmospheric level by a relief valve (CV-3) for recycling of gas to RX-1 or adjusting to atmospheric pressure for sending to the environment by control valve (CV-7). This vent gas composition was measured with a gas analyzer through valve (CV-5). Considering performing only the MS reaction, the mixed gas of H2/CO2/CO was directly fed into the MF-2 and the RX-2 procedure was continued until the methanol product was obtained.
3. Results and discussion
First, data of molasses to biogas pathway and BGR were obtained from two biogas companies in Thailand, namely RE Power Service Co., Ltd. and Tanachewasap Co., Ltd., Thailand. Considering molasses to crude and refinery biogas, simulation biogas was then experimented to generate syngas and produce biomethanol in a 5 L/day continuous process. Finally, data of biohydrogen pathway were obtained from 10 L bioreactor, and simulation biohydrogen gases were then experimented to obtain syngas and produce biomethanol in a 5 L/day continuous process.
3.1. Four-step process of molasses to biogas and biomethanol ()
3.1.1. Molasses to crude biogas (CB)
The operating expenditure (OPEX) of crude biogas obtained by molasses fermentation in 10,000 m3/day biogas plant (Tanachewasap Co., Ltd.,) was 3.5 THB/m3 biogas compared with 2.0 THB/m3 biogas produced from cassava residue in 100,000 m3/day biogas plant (RE Power Service Co., Ltd). Therefore, OPEX-CB was 3.50 THB/m3 biogas (0.1 USD/m3 biogas).
3.1.2. Biogas refinery (BGR)
Crude biogas required two stages for H2S removal. Stage (1) 50,000 ppm of hydrogen sulfide (H2S) in biogas was removed by bioscrubber, reducing H2S concentration from 50,000 to 500 ppm. The OPEX (H2S-Bio) cost was around 0.40 THB/m3 biogas as reported by the RPS biogas company. Stage (2) 500 ppm of H2S was separated by chemical absorption techniques using the Fe-EDTA solution to adsorb H2S in the form of sulfur (S) solid using the method of absorption (Thongkhao et al. Citation2019). The optimum condition for the adsorption was feeding of 4 L/min blending of 0.1 mol/L Fe-EDTA with 2 mol/L NaOH in counter current contacted with 1 L/min biogas. The final H2S in biogas product remained lesser than 10 ppm. The OPEX (H2S-FeS) cost was around 0.10 THB/m3 biogas. The concentration of refined biogas remaining at 60% CH4 and 40% CO2 based on the total OPEX-BGR was 4.00 THB/m3 biogas (0.114 USD/m3 biogas).
3.1.3. Refined biogas to syngas (BS) and syngas to biomethanol (SM)
The 10.0 L/min refined biogas combined with 6.0 ml/min water was sent to the reforming reactor, which was filled with 5 kg of Ni/Al2O3 commercial catalyst operated under 600°C and pressure atmosphere. The product was water and syngas contained H2, CO2, and CO with the ratio of H2/CO around 2.10. The syngas was then separated from water and compressed to 50 barg for sending to the MS reactor, which was packed with 5 kg of Cu/ZnO/Al2O3 commercial catalyst by operating conditions (temperature 170°C and pressure 40 barg pressure). The raw biomethanol generated by 5.0 kg/day contained 96% methanol and was contaminated with small amounts of water, ethanol, and isopropanol (Jitrwung et al. Citation2022b). shows that material balance based on 1 kg of crude biomethanol required in 1.35 kg of refined biogas containing 60% CH4 and 40% CO2 reacted with 0.61 kg of water. The byproduct is off gas containing 0.76 kg CO2, 0.13 kg CO, and 0.07 kg H2, with a heating value of 9.80 MJ/kg MeOH. This off gas can be returned and mixed with biogas for electricity generator. Considering 1 kg of crude biomethanol refined and obtained 0.72 kg refined biomethanol and 0.28 kg off grade biomethanol, the OPEX-BMR (Biomethanol Refinery) was 0.60 THB/kg biomethanol (0.0171 USD/kg biomethanol) (Jitrwung et al. Citation2022a).
3.2. Three-step process of molasses to biohydrogen and biomethanol ()
3.2.1. Molasses to biohydrogen (MH)
The optimal condition of biohydrogen production was experimented in a 10 L batch reactor with a working volume of 5 L containing 40 g/L molasses concentration in media solution and applying 4 g/L CaO (ranging from 0 to 5 g/L CaO). The optimal result of biohydrogen was 0.0089 g H2/g molasses with H2/CO2 ratio of 0.67 compared with 0.0090 g H2/g molasses with H2/CO2 ratio of 0.425 by Kumar et al. (Citation2015) (Kumar et al. Citation2015). Therefore, the OPEX calculation of this research would be 0.009 g H2/g molasses and H2/CO2 ratio of 0.67. The OPEX-MH was 20.93 THB/m3 biohydrogen (0.598 USD/m3 biohydrogen). The biohydrogen price was more expensive compared with biogas because 1 mol of molasses was digested to 1 mol of H2 and 1 mol of CO2 following glucose metabolic pathway, resulting in H2/CO2 equal to 1 by theory and obtaining other organic substances, such as ethanol, acetic acid, propanoic acid, and pyruvic acid, as reported by Ren et al. (Citation2006).
3.2.2. Biohydrogen to syngas (HS) and syngas to biomethanol (SM)
Considering biomethanol production on the biohydrogen pathway, the biohydrogen contained only CO2 and H2 and then the RWGS reaction was used to transform CO2 to CO through H2 following Equation (3). RWGS was a reverse reaction, which was balanced with WGS, as shown in Equation (4). The H2/CO2 ratio obtained from the biohydrogen product was 0.67. However, H2/CO2 ratios were varied depending on methods, type of bacteria, and raw materials. The results of varying H2/CO2 ratios for observing syngas products and MS are reported in . Varying H2/CO2 in the range of 0.67, 1.00, 1.50, and 2.30 by feeding % ratio H2/CO2 of 40/60, 50/50, 60/40, and 70/30, respectively, were experimented in 5 kg of Cu/ZnO/Al2O3 commercial catalyst operated under 500°C and pressure atmosphere. The product was water and syngas contained H2, CO2, and CO with the ratio of H2/CO around 1.75, 2.16, 2.48, and 2.95. The syngas was then separated from water and compressed to 50 barg for sending to the MS reactor, which was packed with 5 kg of Cu/ZnO/Al2O3 commercial catalyst by operating conditions (temperature 170°C and pressure 40 barg pressure). The raw biomethanol was generated by 1.92, 2.23, 2.95, and 3.06 kg/day, containing 96% methanol. CO2 conversions were 16.56, 19.70, 35.95, and 44.69% and H2 conversions were 98.49, 78.88, 67.59 and 65.74% respectively. In addition, the RWGS of CO2 by using H2 at H2/CO2 minimum ratio yielded the highest in H2 conversion but not CO2 conversion. However, the result showed that RWGS can convert low H2/CO2 to high values from 0.67–1.02, 1.00–1.55, 1.50–2.03, and 2.33–3.65, balancing the H2/CO ratios of 1.75, 2.16, 2.48, and 2.95 when increasing H2/CO2 feeding 0.67, 1.00 1.50, and 2.33, respectively. Therefore, the appropriate ratio of H2/CO was over 1.5, facilitating methanol conversion following (4). The data were balanced by obtaining based on 1 kg of biomethanol from the experimental ratio of H2/CO2 0.67 and comparing it with other H2/CO2 ratios shown in and . Thus, 1 kg of biomethanol produced by the experiment was different from the 1.16 kg by theory (approximately 16%).
Table 1. Gas compositions by varying H2/CO2 feed ratios.
Table 2. Gas compositions and biomethanol produced by varying H2/CO2 feed ratios.
3.3. OPEX comparison
The price of raw materials and energy are based on prices in Thailand and exchange conversion (35 THB equal to 1 USD). The material and energy balance of molasses to biomethanol pathway between biogas and biohydrogen pathways are presented for economic evaluation (). Price assumption is shown in . The OPEX of both pathways were calculated and presented in .
Table 3. Materials and energy balance of molasses to biomethanol by biogas and biohydrogen pathway.
Table 4. Price assumption (based on Thailand 35THB/USD) and catalyst duration.
Table 5. OPEX calculation for molasses to biomethanol by passing the biogas and biohydrogen routes.
The OPEX for 1 kg of crude methanol by passing biohydrogen pathway experiment and theory were 4.4148 and 4.0912 USD compared with that of passing biogas pathway 0.3446 USD based on commercial methanol price 0.449 USD/kg. The OPEX of biohydrogen pathway were more expensive than that of the biogas route around 12.82 and 11.87 times, respectively. However, when adding by products, such as valuable organic substances, which were produced by the biohydrogen pathway, the total sale prices per kg biomethanol produced were 6.7243 USD (Exp.) and 5.7500 USD (Theory) compared with only single biomethanol obtained from biogas pathway at 0.4486 USD/kg of produced biomethanol. The margin caps were around 30.19%, 39.66%, and 40.55% for biogas pathway, biohydrogen experiment, and theory route, respectively.
4. Conclusion
Commercial methanol can be replaced by biomethanol using molasses as an abundant raw material. Molasses can be digested under bacteria by biogas and biohydrogen pathway, syngas conversion, and MS. The choices were dependent on the following presented conditions. (1) The biogas pathway was appropriate in the case of sailing single products as biomethanol. (2) The biohydrogen pathway was suitable for adding organic refinery to obtain income from valuable organic substances along with sailing biomethanol.
Acknowledgments
This research was supported by Silpakorn University Research, Innovation, and Creative Fund, and the Department of Mechanical Engineering, Faculty of Engineering and Industrial Technology, Silpakorn University, Thailand. Author special thanks to the Thailand Institute of Scientific and Technological Research (TISTR) for all the support provided. We also appreciate Khon Kaen Sugar Industry Public Company Limited (KSL) for providing raw materials for this research.
Disclosure statement
No potential conflict of interest was reported by the author(s).
Additional information
Funding
References
- Chaiprasert, P. 2011. “Biogas Production from Agricultural Wastes in Thailand.” Journal of Sustainable Energy & Environment. Special Issue, 63–65.
- Daza, Y.A., and J.N. Kuhn. 2016. “CO2 Conversion by Reverse Water gas Shift Catalysis: Comparison of Catalysts, Mechanisms and Their Consequences for CO2 Conversion to Liquid Fuels.” RSC Advances 6 (55): 49675–49691. doi:10.1039/C6RA05414E
- Detman, A., A. Chojnacka, M. Błaszczyk, W. Kaźmierczak, J. Piotrowski, and A. Sikora. 2017. “Biohydrogen and Biomethane (Biogas) Production in the Consecutive Stages of Anaerobic Digestion of Molasses.” Polish Journal of Environmental Studies 26 (3): 1023–1029. doi:10.15244/pjoes/68149
- Grand View Research. 2022. “Methanol Market Size, Share & Trends Analysis Report By Application (Formaldehyde, Acetic Acid, MTBE, DME, Fuel Blending, MTO, Biodiesel), By Region, And Segment Forecasts, 2019–2025.” Report ID: GVR-4-68038-016-3. https://www.grandviewresearch.com/industry-analysis/methanol-market.
- Imarc Impactful Insights. 2021. “Methanol Market: Global Industry Trends, Share, Size, Growth, Opportunity and Forecast 2022–2027.” Report ID: SR112023A650. IMARC Group. India. https://www.imarcgroup.com/methanol-technical-material-market-report.
- Infoholic Research LLP. 2019, March. “Methanol Market by Applications (Formaldehyde, MTBE/TAME, Fuel Blending, Acetic Acid, MTO, DME, Biodiesel and Solvents) and By Geography – Global Drivers, Restraints, Opportunities, Trends, and Forecast to 2023. Karnataka. India.” https://www.infoholicresearch.com/report/methanol-market/.
- Inkwood Research. 2019. “Global Methanol Market Forecast 2019–2027.” https://inkwoodresearch.com/reports/global-methanol-market/.
- Janke, L., A. Leite, M. Nikolausz, T. Schmidt, J. Liebetrau, M. Nelles, and W. Stinner. 2015. “Biogas Production from Sugarcane Waste: Assessment on Kinetic Challenges for Process Designing.” International Journal of Molecular Sciences 16 (9): 20685–20703. doi:10.3390/ijms160920685
- Jitrwung, R., K. Krekkeitsakul, C. Kumpidet, J. Tepkeaw, K. Jaikengdee, A. Wannajampa, H. Jinda, and W. Patthaveekongka. 2022a. “Economic Study of Alternative Using Biogas for Biomethanol Substituting Commercial Methanol in Biodiesel Production.” Paper presented at the Proceedings of Pure and Application Chemistry International Conference (PACCON 2022), 123–127.
- Jitrwung, R., K. Krekkeitsakul, C. Kumpidet, J. Tepkeaw, K. Jaikengdee, A. Wannajampa, H. Jinda, and W. Patthaveekongka. 2022b. “Effect of CH4/CO2 Ratio to Quantity and Quality of Biomethanol Produced from Biogas.” Paper presented at the Proceedings of Pure and Application Chemistry International Conference (PACCON 2022), 138–143.
- Jitrwung, R., and V. Yargeau. 2015. “Biohydrogen and Bioethanol Production from Biodiesel-Based Glycerol by Enterobacter Aerogenes in a Continuous Stir Tank Reactor.” International Journal of Molecular Sciences 16 (5): 10650–10664. doi:10.3390/ijms160510650
- Joshi, A. 2019, October 17. “160,000 Jobs can be Created by Manufacturing Petrochems Using Green Methanol: CEEW. ET EnergyWorld.” https://energy.economictimes.indiatimes.com/news/oil-and-gas/160000-jobs-can-be-created-by-manufacturing-petrochems-using-green-methanol-ceew/. 71423985.
- Kumar, V., R. Kothari, S. Ahmad, and S.K. Tyagi. 2015. “Improvement of Biohydrogen Production with Optimized Initial pH Using Industrial Organic Residue (Molasses) with Enterobacter aerogenes.” Paper presented at the International Conference on “Advances in Power Generation from Renewable Energy Sources” (APGRES), Kota, India. http://apgres.in.
- Mordor Intelligence. 2022, June. “Methanol Market-Growth, Trends, and Forecast. Mordor Intelligence Report. Hyderabad. India.” https://www.mordorintelligence.com/industry-reports/methanol-market.
- Nishimura, S., and M. Yoda. 1997. “Removal of Hydrogen Sulfide from an Anaerobic Biogas Using a bio-Scrubber.” Water Science and Technology 36 (6-7): 349–356. doi:10.2166/wst.1997.0610
- Özgür, E., A.E. Mars, B. Peksel, A. Louwerse, M. Yücel, U. Gündüz, İ Eroğlu, et al. 2010. “Biohydrogen Production from Beet Molasses by Sequential Dark and Photofermentation.” International Journal of Hydrogen Energy 35 (2): 511–517. doi:10.1016/j.ijhydene.2009.10.094
- Polaris Market Research. 2019, March. “Methanol Market Share, Size, Trends Industry Analysis Report, by Feedstock (Natural Gas, Coal), by Derivatives (Formaldehyde, Acetic Acid, Gasoline, MTO, Gasoline, MMA), by End-Use (Automotive, Construction, Electronics, Paints Coatings, Pharmaceuticals), by Regions: Segment Forecast, 2019-2026.” Report ID: PM1543. https://www.polarismarketresearch.com/industry-analysis/methanol-market.
- Prismane Consulting. 2018. “Global Methanol Market Study 2016–2032.” Report Id: GMB-049. Prismane Consulting report. Maharashtra. India. https://prismaneconsulting.com/report_details/53/Global-Methanol-Market-Study-2016—2032.
- Ren, N., J. Li, B. Li, Y. Wang, and S. Liu. 2006. “Biohydrogen Production from Molasses by Anaerobic Fermentation with a Pilot-Scale Bioreactor System.” International Journal of Hydrogen Energy 31 (15): 2147–2157. doi:10.1016/j.ijhydene.2006.02.011
- Statista Research Department. 2022, July. “Market Size of Methanol Worldwide in 2021, with a Forecast until 2030.” https://www.statista.com/statistics/1065891/global-methanol-production-capacity/.
- Sun, J.T., I.S. Metcalfe, and M. Sahibzada. 1999. “Deactivation of Cu/ZnO/Al2O3 Methanol Synthesis Catalyst by Sintering.” Industrial & Engineering Chemistry Research 38 (10): 3868–3872. doi:10.1021/ie990078s
- Suwanasri, K., S. Trakulvichean, U. Grudloyma, W. Songkasiri, T. Commins, P. Chaiprasert, and M. Tanticharoen. 2015. “Biogas–key Success Factors for Promotion in Thailand.” Journal of Sustainable Energy & Environment 25: 30.
- Thongkhao, N., R. Jitrwung, K. Krekkeitsakul, A. Poonanan, S. Piticharoenphun, and W. Patthaveekongka. 2019. “The Removal of H2S in Biogas Using Chemical Absorption for Reforming Process.” Paper presented at the Proceedings of Pure and Application Chemistry International Conference (PACCON 2019), 1–7.
- Tridge Exhibition 365. 2021. “Molasses.” https://www.tridge.com/intelligences/molasses/price.
- Triton Market Research. 2022, June. “Global Methanol Market 2019–2027.” https://www.tritonmarketresearch.com/reports/methanol-market.
- Wang, L., Liu, H., Chen, Y., & Yang, S. (2017). Reverse Water–gas Shift Reaction Over co-Precipitated Co–CeO2 Catalysts: Effect of Co Content on Selectivity and Carbon Formation. International Journal of Hydrogen Energy, 42(6), 3682-3689. doi:10.1016/j.ijhydene.2016.07.048
- Zhao, X., B. Joseph, J. Kuhn, and S. Ozcan. 2020. “Biogas Reforming to Syngas: A Review.” IScience 23 (5): 101082. doi:10.1016/j.isci.2020.101082