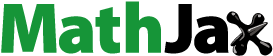
ABSTRACT
By analysing the flow field of the bipolar plate, considering the inlet and outlet direction, increasing the inclined baffle and the number of channels, an improved multi-channel serpentine flow channel on the opposite side of double baffles is obtained based on the traditional serpentine flow channel. And the hydrodynamic model, electrochemical model and equivalent circuit model are coupled into a hybrid model to obtain the relationship between pump loss current changes during charging and discharging. The experimental results show that the reaction time of the change curve is 52 s earlier and the charging cut-off voltage is 0.3 V higher in the charging and discharging state.
Nomenclature
E | = | potential (V) |
R | = | gas constant (8.314 J mol−1 K−1) |
T | = | temperature (K) |
F | = | Faraday constant (96847C mol−1) |
C | = | molar concentration (mol/L) |
= | the activity coefficient of ions (mol/L) | |
= | pressure loss (Pa) | |
SOC | = | state of charge |
f | = | loss coefficient |
D | = | diameter (mm) |
L | = | length (mm) |
V | = | volume (L) |
= | density (kg m−3) | |
Re | = | Reynolds number |
= | viscosity (kg m−1 s−1) | |
= | hydraulic resistance (Pa s m−3) | |
Q | = | flow rate (L min−1) |
I | = | current (A) |
P | = | power (W) |
A | = | cross area (mm2) |
N | = | cell number |
= | efficiency/diffusion ratio | |
K | = | hydraulic resistance coefficient |
v | = | flow velocity (m3/s) |
Subscript | ||
s | = | stack |
L | = | local |
D | = | friction |
p | = | pump |
c | = | tributary channel |
in | = | inlet |
out | = | outlet |
1. Introduction
With the continuous development of new energy vehicle technology, new energy vehicle has become one of the most potential and promising industries in the world (Thakur et al. Citation2023). However, the power battery management problems faced by new energy vehicles are becoming increasingly prominent, seriously affecting battery performance and battery safety (Khaboshan et al. Citation2023; Panchal et al. Citation2015, Citation2023). Lithium-ion batteries are sensitive to temperature and complex electrochemical reactions will occur at different temperatures. A high or low temperature may degrade battery performance or even cause thermal runaway. Therefore, a thermal management system must be introduced to control battery temperature and improve the temperature uniformity of modules (Braga et al. Citation2023; Li et al. Citation2022; Talele et al. Citation2023). The non-flammable electrolyte of a flow battery is mainly composed of water, and the risk of thermal runaway or fire is very low. Therefore, a flow battery has better safety than a lithium battery.
Energy density has always been a key issue in the research of flow batteries. Based on this, Li et al. (Citation2015) proposed a high-energy-density iodine zinc flow battery, which can achieve a discharge energy density of in
zinc iodide electrolyte that is close to neutral. The iodine zinc flow battery features low self-discharge, good cyclic performance, high energy density, non-corrosive neutral electrolyte, environment-friendly and other advantages. Although the research and development of iodine zinc flow battery are still in the experimental stage, it is still considered a very promising redox flow battery system for energy storage applications (Li et al. Citation2018; Xie et al. Citation2018; Zhang et al. Citation2018).
In domestic and international research, it has been found that the flow rate and concentration of the electrolyte solution are important factors affecting the charge–discharge characteristics and energy efficiency of VRB (Vanadium Redox Battery) through studies of its electrochemical model (Jung et al. Citation2017; Messaggi et al. Citation2022; Nikiforidis, Belhcen, and Anouti Citation2021; Yan, Lv, and Ma Citation2015). In the iodine zinc flow battery, which has a structure similar to VRB, the flow rate and distribution of the electrolyte solution are closely related to the bipolar plate flow channel structure. Therefore, the influence of different flow channel structures on battery performance has become one of the current research hotspots (Huang et al. Citation2022; Messaggi et al. Citation2018).
Therefore, based on the traditional serpentine runner, this paper optimised the flow channel structure by considering the inlet and outlet direction, increasing the number of channels and setting double baffles. The flow behaviour of electrolytes in a bipolar plate flow channel was simulated by the computational fluid dynamics method. The hydromechanical properties of the multi-channel serpentine flow channel and multi-channel serpentine flow channel on the opposite side of double baffles were compared, and the electrolyte distribution was optimised. A hybrid model of an iodine zinc flow battery was established to verify the relationship between pump loss current changes during charging and discharging. Finally, the experimental results show that the proposed multi-channel serpentine flow channel on the opposite side of the double baffles is beneficial to improve the uniformity of fluid distribution and improve the efficiency of the iodine zinc flow battery.
2. Modelling of iodine zinc flow battery
2.1. Electrochemical model of iodine zinc flow battery
The typical physical structure of the zinc iodide redox flow battery is similar to that of the traditional flow battery system. The electrolyte is continuously transported from the storage tank to the stack under the action of the circulating pump. Zinc ions and iodine ions undergo redox reactions in the stack, and the reaction equations are (1), (2) and (3).
Positive electrode:
(1)
(1) Negative pole:
(2)
(2) Total reaction:
(3)
(3) When there is current flow in the iodine zinc flow battery, the equilibrium potential
depends on the ion and proton concentrations participating in the reaction in the electrolyte of the iodine zinc flow battery, which can be represented by the Nernst equation:
(4)
(4) where
and
are the electromotive force of the reaction between the negative and positive poles, and the standard electromotive force is
. R is the molar gas constant, Ts is the stack temperature, F is the faraday constant.
and
are the molar concentrations of iodide ion and triiodide ion in the stack, respectively,
is the molar concentrations of zinc ion in the stack.
is the activity coefficient of various ions. Since
of different ions can be considered to cancel each other roughly, the following equation is obtained:
(5)
(5)
2.2. Equivalent circuit model of the iodine zinc flow battery
The circuit model must reflect the SOC, output input volt-ampere characteristics, dynamic response rate and energy loss of the iodine zinc flow battery.
Consideration for several factors: (1) Since the single cell current and SOC have an effect on the pump loss value, a controlled current source is used to simulate the pump loss. (2) Since the internal energy loss of the system occurs when the iodine zinc flow battery operates, the equivalent internal resistance loss of the iodine zinc flow battery is represented by the reaction resistance
and ohmic resistance
. (3) Since the value of SOC has an effect on the single cell voltage
of the iodine zinc flow battery, a controlled voltage source is used to simulate
. (4) The equivalent external system loss of the iodine zinc flow battery is represented by fixed-resistance
and pump loss current
and
represents the consumption current of fixed-resistance
. (5) The electrode capacitance
is used to represent the dynamic response capability of the iodine zinc flow battery.
and
represent the current and voltage of the electrode capacitance
, respectively. The port current is
and the open-circuit voltage is
. The equivalent circuit model of the iodine zinc flow battery is shown in .
2.3. Hydrodynamic model of the iodine zinc flow battery
When the electrolyte flows through the stack from the liquid storage tank and returns to the storage tank, part of the energy is consumed. The loss of this part consists of the pipeline pressure loss caused by flowing through the pipeline and the reactor pressure loss caused by flowing through the reactor (Castro et al. Citation2021).
Pipeline pressure loss
Pipeline pressure loss is mainly composed of friction loss caused by the friction generated by the electrolyte flowing in the pipeline and local loss
related to pipeline design, which can be expressed as follows:
(6)
(6) Friction loss and local loss can be obtained from the Darcy-Weisbach equation:
(7)
(7)
(8)
(8) where
is the friction coefficient,
is the local loss coefficient,
is the pipe diameter,
is the pipe length,
is the volume flow rate of electrolytic liquid and
is the fluid density. The local loss coefficient
will vary according to the different components of the pipeline through which the electrolyte flows.
In addition, the friction coefficient can be expressed as
(9)
(9)
(10)
(10) where
is the Reynolds coefficient and
is the dynamic viscosity coefficient of the fluid.
(2) | Reactor pressure loss |
The hydrodynamic model mainly reflects the momentum transfer process in the working process of the battery. The flow channels in the stack are generally composed of branch channels and channels. The electrolyte flows in the battery in a laminar flow mode, where the pressure loss caused by the electrolyte flow in the flow channel can be expressed as
(11)
(11) where the proportional coefficient
represents the flow resistance of the flow channel and
represents the total flow in the mth branch channel. Because of the complex flow path of the electrolyte in the stack, the flow resistance is difficult to be expressed by a fixed formula. Blanc and Rufer (Citation2008) used the finite element method to simplify the calculation method of flow resistance. Data
in the reference are quoted here.
(3) | Hydrodynamic model |
The fluid mechanic model mainly reflects the momentum transfer process in the working process of the battery. During the operation of iodine zinc flow batteries, the pipeline pressure loss and stack pressure loss caused by electrolyte flow jointly affect the magnitude of pump loss current (Ruiz-Martín et al. Citation2022).
The equation of pump loss current is as follows:
( 12)
( 12) where
is the pump power,
is the dynamic viscosity coefficient of fluid,
is the pipe length,
is the cross-sectional area of the pipe,
is the number of single batteries,
is the flow resistance,
is the pump efficiency and
is the total flow rate.
From Equation (12), it can be seen that the main parameter affecting the pump loss current is the electrolyte flow rate Q, which can be divided into stack flow rate , channel flow rate
and circulating pump flow rate
based on the different battery components flowing through by the electrolyte. When
is in different stages of charging and discharging, it will change accordingly, which can be expressed as follows:
(13)
(13) where
is the electrolyte flow coefficient,
is the electrolyte concentration at time
.
2.4. Hybrid model of the iodine zinc flow battery
The hybrid model couples the hydrodynamic module, the electrochemical module and the equivalent circuit module together. The coupling relationship of the three modules is shown in .
In the figure, represents the initial concentration of iodine ions with different valences
represents the iodine ion concentration corresponding to time
.
In the hydrodynamic module, the pump loss current is calculated by the hydrodynamic principle, pump loss power and stack voltage.
is fed back to the equivalent circuit module as the output of the hydrodynamic module to achieve the coupling effect between the hydrodynamic model and the equivalent circuit model.
In the electrochemical module, the concentration of iodine ions with different valence is obtained by using the principle of mass conservation and is fed back to the equivalent circuit module as the output of the electrochemical module to achieve the coupling effect between the electrochemical model and the equivalent circuit model.
The equivalent loss circuit module equates the relevant loss in the iodine zinc flow battery to the loss of internal resistance and calculates the charge–discharge voltage of the iodine zinc flow battery by combining the stack voltage
, the pump loss current
and the charge–discharge port current
.
The coupling relationship of the hybrid model is reflected by the correlation between the input and output of the hydrodynamic module, the electrochemical module and the equivalent circuit module. The hydrodynamic module and the electrochemical module are both affected by the input flow . The port current
of the equivalent circuit module is used as the input of the electrochemical module, and the monomer voltage
is used as the input of the hydrodynamic module. The hydromechanic module outputs
is used as the pump loss current of the equivalent circuit model, and the electrochemical module output
is used as the controlled voltage source of the equivalent circuit model.
3. Flow channel optimisation
3.1. Flow field analysis model
When the flow mode of the electrolyte in the flow channel is laminar flow, the flow of the electrolyte is generated by the pressure drop. Pressure drop can be expressed as follows:
(14)
(14) where
is the hydraulic resistance coefficient of the flow channel,
is the electrolyte density,
is the average flow velocity through the cross-sectional area of the flow channel,
is the total length of the runner and
is the diameter of the electrolyte flow channel.
Boersma and Sammes (Citation1997) proposed a hydrodynamic model of a parallel flow battery stack using a hydraulic resistance network, as shown in .
It can be assumed that the inlet and outlet flow channels of the electrolyte are cut into several small sections. The resistance coefficient of each small section of the electrolyte inlet channel is , the resistance coefficient of each small section of the outlet channel is
and the resistance coefficient of the flow channel in each branch passage is
.
refers to the total flow at the inlet,
refers to the flow in the nth branch channel and
refers to the flow in the jth branch channel, which are
and
(j = 1,2, … ,n)” according to the pressure distribution at the inlet and outlet.
It is assumed that the electrolyte flow state of the iodine zinc flow battery studied is laminar flow. The pressure drop of the jth branch channel is as shown in Equation (15), and the hydraulic resistance coefficient
of the branch channel is as shown in Equation (16).
(15)
(15)
(16)
(16) where
is the friction coefficient,
is the length of the tributary,
is the number of tributaries,
is the cross-sectional area of the tributary and
is the diameter of the tributary.
Let the electrolyte flow in the jth branch channel be expressed as Equation (17).
(17)
(17) whee the difference between
and
can be reduced by increasing the flow resistance
of the branch channel, thus increasing the uniformity of the distribution of electrolyte solution in the branch channel. The velocity
in the jth branch channel is
(18)
(18)
The pressure drop at the inlet and outlet of the flow channel is and
respectively, as shown in Equation (19) and Equation (20), respectively.
(19)
(19)
(20)
(20)
where and
are the flow rates at the inlet and outlet channel, respectively.
3.2. Flow channel geometry improvement and meshing
Analysis of the bipolar plate flow field is carried out by considering the inlet and outlet directions, increasing the inclined baffles and the number of channels. The flow chart for several optimisations is shown in . First of all, on the basis of the traditional serpentine flow channel, the inlet and outlet directions and the number of channels are optimised to obtain the multi-channel serpentine flow channel on the opposite and the multi-channel serpentine flow channel on the same side. Secondly, the multi-channel serpentine flow channel on the opposite side of a single baffle and the multi-channel serpentine flow channel on the same side of a single baffle are obtained by adding inclined baffles. Finally, by adding the inclined baffles at both ends, the multi-channel serpentine flow channel on the opposite side of the double baffles is obtained.
The basic geometric dimensions of the improved bipolar plate are shown in , and the modelling is shown in .
Table 1. Basic geometric dimensions of the iodine zinc flow battery bipolar plate (mm).
Modelling of the traditional straight parallel channel, multi-channel serpentine flow channel and multi-channel serpentine flow channel on the opposite side of double baffles was performed using CATIA software. The established models were then imported into Gambit for meshing, and the mathematical model was solved using the CFD software COMSOL. The total number of grids is about 160,000, and the grid diagram is shown in . The necessary conditions for the selection of boundary conditions are velocity inlet, pressure outlet, sidewall edge condition without sliding and surface pressure. The requirement of the inlet boundary is speed inlet, which is set as v = 0.01 m/s; The requirement of outlet boundary is pressure outlet, set pgauge = 0 atm. All other edge conditions are set to the wall. By modifying the pressure field with the SIMPLE algorithm, the continuity equation and momentum equation of the incompressible flow field can be calculated. The model equation is discretised by the second-order upwind difference scheme, and the convergence accuracy range is . The calculation model assumes that the flow of electrolytes is laminar flow and incompressible flow under a steady state and constant temperature.
3.3. Analysis of the uniformity of the channel electrolyte
The flow channel structure has an important influence on the uniform distribution of electrolytes in the iodine-zinc flow battery. It has been proved that the electrolyte flow rate is the same in each plane of the bipolar plate in the direction of plate thickness (Messaggi et al. Citation2018), so the difference in electrolyte flow rate in the direction of plate thickness can be neglected. An arbitrary horizontal plane in the direction of the bipolar channel thickness is taken as the object to compare the effects of different flow channel structures on the electrolyte flow distribution.
To quantitatively analyse the distribution uniformity of electrolyte flow in each branch channel of the iodine zinc flow battery bipolar plate, the following two criteria are introduced to determine: one is the simulated maximum error r and the other is the ideal maximum error R, which can be respectively represented by the following equations.
(21)
(21)
(22)
(22)
where is the maximum simulated flow of the branch,
is the minimum simulated flow of the branch,
is the analogue flow of the branch and
is the ideal flow of the branch.
shows the flow distribution of tributaries with different flow channel structures. As can be seen from the figure the traditional straight parallel flow channel has the least uniform electrolyte distribution. The improved serpentine flow channel divides the traditional single-channel serpentine flow channel into several sections, and each section is connected to the main flow channel, thus effectively reducing the loss of pressure drop and the flow rate distribution is more uniform than the traditional straight parallel flow channel. By adding double baffles, the flow distribution of the multi-channel serpentine flow channel on the opposite side of double baffles is more uniform.
is the flow velocity distribution diagram of the multi-channel serpentine flow channel. Since the multi-channel serpentine flow channel changes the traditional single-channel serpentine flow channel into five serpentine flow channels, the flow of each serpentine flow channel is significantly reduced, which not only combines the structural advantages of the traditional serpentine flow channel but also retains the structural advantages of straight parallel flow channels. From the flow velocity distribution diagram, it can be observed that the flow distribution and velocity distribution have great improvement space.
Based on this, the inlet and outlet directions are changed to the opposite side form, baffles are added at the inlet and outlet channels and the baffle inclination angle is changed. With the baffle inclination angle gradually increasing from small to large, the uniformity index of electrolyte flow rate in the flow channel, namely, the simulated maximum error and the ideal maximum error
, first decrease and then gradually increase and then tend to be stable, as shown in . When the baffle tilt angle is about 5.71 degrees, the uniformity of electrolyte flow and velocity distribution in the multi-channel serpentine flow channel on the opposite side of the double baffles is greatly improved, and its flow velocity distribution is shown in . The distribution of electrolyte flow and velocity in each branch channel is obviously more uniform than that shown in .
Figure 9. Flow and velocity distribution of multi-channel serpentine flow channel on the opposite side of the double baffles.

Table 2. Error analysis of electrolyte flow uniformity at different baffle tilt angles.
The hybrid model simulation in section 2.4 was built in MATLAB/Simulink, and the change curve of pump loss current during the charging and discharging process of multi-channel serpentine flow channel on the opposite side of double baffles, opposite side multi-channel serpentine channel and the traditional straight parallel channel was obtained, as shown in . After several channel optimisation, the pump loss current in the charging and discharging process of the iodine-zinc flow battery is reduced, and the pump loss current of the multi-channel serpentine flow channel on the opposite side of double baffles is the least .
4. Experiment
4.1. Preparation of experimental materials for the iodine zinc flow battery
As shown in , the experimental equipment for studying the iodine zinc flow battery includes the iodine zinc flow battery stack, the microcomputer, the thermostat, the meterable intelligent speed regulating peristaltic pump, the zinc iodide positive electrolyte, the negative electrolyte and the battery test system BT∼2016R. With reference to other charging and discharging test standards of the liquid flow battery, set the temperature condition at 25 ± 2°C, charge to the cut-off voltage of 1.51 V, leave it for 30 min, discharge to the cut-off voltage of 0.8 V, conduct cyclic charging and discharging several times and record the experimental data.
Figure 11. Experimental test equipment. 1. Microcomputer, 2. Tester, 3. Constant temperature test chamber, 4. Zinc iodide positive electrolyte, 5. Iodine zinc flow battery stack, 6. Negative electrolyte, 7. Circulating pump.

The following is a three-dimensional model of the stack structure of an iodine zinc flow battery: from left to right, the stack reinforcement plate, sealing gasket, collector plate, bipolar plate, flow guide plate (there are graphite carbon felt electrodes in the flow guide plate), ion exchange membrane, carbon felt electrode, flow guide plate, collector plate, silicone sealing gasket, and electric stack splint .
Stack reinforcement plate and flow guide plate made of acrylic material plate and metal plate adhesion, the use of bolts to a collector plate, bipolar plate, flow guide plate, carbon felt electrode, ion exchange membrane fastened in the splint, fastening at the same time can also on the stack up to the sealing effect, as shown in .
Collector plate: The collector plate is also known as the bipolar plate. The collector plate used in the experiment is made of carbon material combined with metal material. The metal material is made of a 0.08 mm copper strip cut by laser, and the carbon material is made of a 0.06 mm high-purity graphite sheet, as shown in .
The raw materials for the iodine zinc flow battery stack used in the experiment are listed in .
Table 3. Summary of chemical reagents and raw materials used in the experiment.
4.2. Experimental testing equipment
The iodine zinc flow battery test platform used in this paper is the battery test system BT-2018R, a high-precision battery comprehensive test system developed by Hubei Rambo New Energy Equipment Co., LTD. Items that can be tested include detailed data of charge and discharge, cycle life, charge and discharge curve, charge and discharge efficiency, capacity attenuation, specific capacity, specific energy, DC resistance, leakage (self-discharge) current, over-charge/over-discharge, etc. The temperature control equipment used in this experiment is the SPX-50 constant temperature test chamber produced by Tianjin Honnuo Instrument Co., LTD., as shown in the following figure.
In the test of the basic characteristics of the iodine zinc flow battery, 35 ml 0.5M cathode electrolyte was installed in the storage tank and stack of the iodine zinc flow battery. Through the HPPC discharge test of the iodine zinc flow battery, the battery could be deeply discharged and the actual capacity of the battery could be obtained. The theoretical capacity of 35 ml cathode fluid is 469.09 mAh. The HPPC discharge test shows that the actual capacity of the battery is 405 mAh, with a difference in 64.09 mAh and the theoretical capacity is 86.33%. The actual capacity of the battery is ideal .
4.3. Analysis of experimental results
shows the change curve of charge-discharge V-t of the multi-channel serpentine flow channel on the opposite side of double baffles of the iodide-zine flow battery. The trend and value of the simulation curve and the experimental curve are relatively consistent, but there are also errors. The reason is that during charging and discharging, the temperature of the ion-exchange membrane and electrolyte has an impact on the flow rate of the electrolyte, which is accompanied by the generation of insoluble iodine crystals, making the experimental data value lower than the simulation data value. The maximum relative errors of charge and discharge are 2.46% and 2.52%, respectively. shows the variation curve of charging and discharging V–t in the traditional straight parallel flow channel of the iodine zinc flow battery. Compared with , it can be seen that the response time of the change curve of the multi-channel serpentine flow channel on the opposite side of the double baffle is 52 s earlier and the charging cut-off voltage is 0.3 V higher than that of the traditional straight parallel channel under the charging and discharging conditions.
Figure 16. V-t change curve of charge and discharge in multi-channel serpentine flow channel on the opposite side of double baffles of iodine zinc flow battery.

Figure 17. V-t change curve of traditional straight parallel flow channel charge and discharge of the iodine zinc flow battery.

shows the simulation test diagram of pump loss current. The trend and value of the simulation curve and test curve are relative fit, which reflects the change of pump loss current in the process of charging and discharging. When the charging current is fixed, the SOC value increases, due to the increase in the number of iodide ions in the electrolyte, to ensure a stable number of iodide ions participating in the electrochemical reaction, the pump power decreases, resulting in the flow rate slowing down, and the corresponding
also decreases relatively. When the discharge current is constant, with the continuous decrease in SOC, the flow rate of the pump increases and the corresponding
also increases relatively due to the decrease in the number of iodide ions in the electrolyte. In the model,
is obtained according to Formula (12), and the loss of the approximate pump is obtained. Through the storage unit of the pump, the value of the current is recorded, and the trend of the current is obtained by a computer.
5. Conclusion and future work
By coupling the hydrodynamic model, the electrochemical model and the equivalent circuit model into a hybrid model, the variation of charge and discharge voltage and pump loss current are simulated. To reduce the energy loss of the pump, the inlet and outlet direction, the number of the parallel serpentine flow channel and the inclined baffle at the inlet and outlet were considered to optimise the flow channel. The numerical simulation results show that the multi-channel serpentine flow channel on the opposite side of the double baffles can not only ensure the uniformity of velocity and flow in the channel but also reduce the pump loss and save energy. The experimental results show that the reaction time of the curve is 52 s earlier and the charging cutoff voltage is 0.3 V higher.
In the numerical simulation of a liquid flow battery, some influencing factors are simplified, while the influence of ion exchange membrane and electrolyte temperature on the flow rate and flow rate of electrolyte is neglected. A more accurate simulation of flow distribution in the flow channel can be used in future research work.
Disclosure statement
No potential conflict of interest was reported by the author(s).
References
- Blanc, C., and A. Rufer. 2008, November. “Multiphysics and Energetic Modeling of a Vanadium Redox Flow Battery.” 2008 IEEE International Conference on Sustainable Energy Technologies (pp. 696–701). IEEE.
- Boersma, R. J., and N. M. Sammes. 1997. “Distribution of Gas Flow in Internally Manifolded Solid Oxide Fuel-Cell Stacks.” Journal of Power Sources 66 (1–2): 41–45. https://doi.org/10.1016/S0378-7753(96)02469-X
- Braga, R., A. Mevawalla, S. Gudiyella, S. Panchal, M. Giuliano, G. Nicol, and Y. Zheng. 2023. “Transient Electrochemical Modeling and Performance Investigation Under Different Driving Conditions for 144Ah Li-ion Cell with Two Jelly Rolls (No. 2023-01-0513).” SAE Technical Paper.
- Castro, M. T., J. A. D. Del Rosario, M. N. Chong, P. Y. A. Chuang, J. Lee, and J. D. Ocon. 2021. “Multiphysics Modeling of Lithium-ion, Lead-Acid, and Vanadium Redox Flow Batteries.” Journal of Energy Storage 42: 102982. https://doi.org/10.1016/j.est.2021.102982
- Huang, Z., A. Mu, L. Wu, and H. Wang. 2022. “Vanadium Redox Flow Batteries: Flow Field Design and Flow Rate Optimization.” Journal of Energy Storage 45: 103526. https://doi.org/10.1016/j.est.2021.103526
- Jung, H. Y., G. O. Moon, S. Jung, H. T. Kim, S. C. Kim, and S. H. Roh. 2017. “Low Permeable Hydrocarbon Polymer Electrolyte Membrane for Vanadium Redox Flow Battery.” Journal of Nanoscience and Nanotechnology 17 (4): 2563–2566. https://doi.org/10.1166/jnn.2017.13371
- Khaboshan, H. N., F. Jaliliantabar, A. A. Abdullah, and S. Panchal. 2023. “Improving the Cooling Performance of Cylindrical Lithium-ion Battery Using Three Passive Methods in a Battery Thermal Management System.” Applied Thermal Engineering 227: 120320. https://doi.org/10.1016/j.applthermaleng.2023.120320
- Li, Y., L. Liu, H. Li, F. Cheng, and J. Chen. 2018. “Rechargeable Aqueous Zinc–Iodine Batteries: Pore Confining Mechanism and Flexible Device Application.” Chemical Communications 54 (50): 6792–6795. https://doi.org/10.1039/C8CC02616E
- Li, B., Z. Nie, M. Vijayakumar, G. Li, J. Liu, V. Sprenkle, and W. Wang. 2015. “Ambipolar Zinc-Polyiodide Electrolyte for a High-Energy Density Aqueous Redox Flow Battery.” Nature Communications 6 (1): 6303. https://doi.org/10.1038/ncomms7303
- Li, W., Y. Xie, X. Hu, M. K. Tran, M. Fowler, S. Panchal, J. Zheng, and K. Liu. 2022. “An Internal Heating Strategy for Lithium-ion Batteries Without Lithium Plating Based on Self-Adaptive Alternating Current Pulse.” IEEE Transactions on Vehicular Technology, 72 (5): 5809–5823. https://doi.org/10.1109/TVT.2022.3229187.
- Messaggi, M., P. Canzi, R. Mereu, A. Baricci, F. Inzoli, A. Casalegno, and M. Zago. 2018. “Analysis of Flow Field Design on Vanadium Redox Flow Battery Performance: Development of 3D Computational Fluid Dynamic Model and Experimental Validation.” Applied Energy 228: 1057–1070. https://doi.org/10.1016/j.apenergy.2018.06.148
- Messaggi, M., C. Gambaro, A. Casalegno, and M. Zago. 2022. “Development of Innovative Flow Fields in a Vanadium Redox Flow Battery: Design of Channel Obstructions with the aid of 3D Computational Fluid Dynamic Model and Experimental Validation Through Locally-Resolved Polarization Curves.” Journal of Power Sources 526: 231155. https://doi.org/10.1016/j.jpowsour.2022.231155
- Nikiforidis, G., A. Belhcen, and M. Anouti. 2021. “A Highly Concentrated Vanadium Protic Ionic Liquid Electrolyte for the Vanadium Redox Flow Battery.” Journal of Energy Chemistry 57: 238–246. https://doi.org/10.1016/j.jechem.2020.09.001
- Panchal, S., S. Mathewson, R. Fraser, R. Culham, and M. Fowler. 2015. “Experimental Measurements of Thermal Characteristics of LiFePO4 Battery. https://doi.org/10.4271/2015-01-1189
- Panchal, S., V. Pierre, M. Cancian, O. Gross, F. Estefanous, and T. Badawy. 2023. “Development and Validation of Cycle and Calendar Aging Model for 144Ah NMC/Graphite Battery at Multi Temperatures, DODs, and C-Rates (No. 2023-01-0503).” SAE Technical Paper.
- Ruiz-Martín, D., D. Moreno-Boza, R. Marcilla, M. Vera, and M. Sánchez-Sanz. 2022. “Mathematical Modelling of a Membrane-Less Redox Flow Battery Based on Immiscible Electrolytes.” Applied Mathematical Modelling 101: 96–110. https://doi.org/10.1016/j.apm.2021.08.020
- Talele, V., M. S. Patil, S. Panchal, R. Fraser, M. Fowler, and S. R. Gunti. 2023. “Novel Metallic Separator Coupled Composite Phase Change Material Passive Thermal Design for Large Format Prismatic Battery Pack.” Journal of Energy Storage 58: 106336. https://doi.org/10.1016/j.est.2022.106336
- Thakur, A. K., R. Sathyamurthy, R. Velraj, R. Saidur, A. K. Pandey, Z. Ma, Punit Singh, et al. 2023. “A State-of-the art Review on Advancing Battery Thermal Management Systems for Fast-Charging.” Applied Thermal Engineering 226: 120303. https://doi.org/10.1016/j.applthermaleng.2023.120303.
- Xie, C., H. Zhang, W. Xu, W. Wang, and X. Li. 2018. “A Long Cycle Life, Self-Healing Zinc–Iodine Flow Battery with High Power Density.” Angewandte Chemie 130 (35): 11341–11346. https://doi.org/10.1002/ange.201803122
- Yan, G., Y. Lv, and W. Ma. 2015. “Effects of Pump Losses on Performance of Vanadium Redox Battery.” Chinese Journal of Power Sources 39 (12): 2647–2649.
- Zhang, J., G. Jiang, P. Xu, A. G. Kashkooli, M. Mousavi, A. Yu, and Z. Chen. 2018. “An all-Aqueous Redox Flow Battery with Unprecedented Energy Density.” Energy & Environmental Science 11 (8): 2010–2015. https://doi.org/10.1039/C8EE00686E