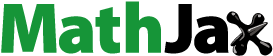
ABSTRACT
In modern buildings, it is evident that exterior glazing is highly desirable to enhance the visual environment and provide daylight. This study investigates the energy performance of polycarbonate glazing as a potential substitute for conventional glass. A detailed energy analysis is conducted using a design-builder simulation tool to simulate the performance of multiwall polycarbonate sheet and normal glass for a model residential building. The result shows that the polycarbonate sheet outperforms normal glass. The wall systems’ total annual cooling energy consumption for 16 mm triple 5-wall x-structure polycarbonate and the 3 mm regular single clear glass was 25,834 kWh and 39,565.18 kWh, respectively, resulting in 35% energy savings. Similarly, the skylights’ cooling energy consumption for the same polycarbonate types was 35,776.47 kWh and 63,340.74 kWh, respectively, resulting in 44% energy savings. The impact of aluminum and uPVC framings was insignificant. Therefore, polycarbonate sheets are an excellent alternative to glass.
1. Introduction
Due to recent advancements in the design of complex buildings attributable to increased client and occupant needs, architects and engineers are collaborating to achieve occupant satisfaction through innovative building designs and new building materials. Many modern building designs have an exterior glass system that provides natural light to interior spaces that residents value. However, the limitation of the exterior glazing system is its low thermal insulation in comparison to walls which increases energy consumption to achieve internal thermal comfort, particularly in hot climates such as Dhahran, Saudi Arabia. According to studies, 20% of individuals rely on artificial lighting for light, whereas 76% recognise the importance of natural daylight in indoor environments (Dolnikova, Katunsky, and Darula Citation2020). Because of the high transmission of thermal energy into and out of the interior spaces, the apertures such as windows, doors, and skylights are the weakest and most exposed point in the building envelope, contributing significantly to energy loss (Alqahtani and Elgizawi Citation2020; Li et al. Citation2023). Glass, the traditional exterior glazing material, is used in buildings with various systems, such as single, double, or triple glazing, to achieve an efficient system with improved thermal insulation by exploiting a cavity between glass panels (Aguilar-Santana et al. Citation2020). However, these conventional clear glasses have drawbacks such as high heat gain/loss, glare, poor thermal performance, and low impact resistance. These limitations, coupled with their significant impact on energy consumption and greenhouse gas (GHG) emissions, replacements of existing glazing systems should be carefully considered to promote sustainability (Ramana Maduru et al. Citation2022). The building sector’s transition to sustainability is critical for climate change mitigation (Cellura et al. Citation2018).
Petroleum-based polymers account for approximately 99% of all plastics manufactured today (Rabnawaz et al. Citation2017), with China, the world’s largest plastic producer, estimated to have 305 Mt (219 kg/capita) in use as of 2017, with 60% in the building and construction industries (Jiang et al. Citation2020). The worldwide plastics sector accounts for 16% of oil consumption (Jiang et al. Citation2020). It will account for 15% of the global carbon budget through GHG emissions by 2050 (Zheng and Suh Citation2019). Polymer-based high-end products, which have high potential to be manufactured locally and add value to buildings and constructions, are part of Saudi Arabia’s 2030 vision. Among these polymer-based materials are polycarbonate, which can provide daylight, a view of the building, and better thermal insulation than ordinary glass. Polycarbonate (PC) accounts for most engineering plastics applications, as it attracts special attention and plays a vital role in various disciplines due to its outstanding qualities, including excellent transparency, thermal stability lightweight, durability, fire, weather, and UV resistance (Fukuoka et al. Citation2019; Moretti et al. Citation2018). It is currently used globally in green building and skylight applications due to its numerous advantages compared to ordinary Glass (Moretti et al. Citation2018; Al-Obaidi, Ismail, and Abdul Rahman Citation2013).
Polycarbonate sheets are a high-potential alternative polymer-based material that is 250 times stronger (Teotia and Soni Citation2014) than glass in terms of safety while also allowing for light, visual view, and more excellent thermal insulation than standard Glass (Al-Obaidi, Ismail, and Abdul Rahman Citation2013). The global demand for PC surpassed 3.6 million tons in 2016. The increasing demand for engineering plastics is owing to superior features, such as outstanding impact resistance, good transparency, high heat resistance, and high flame retardancy (Fukuoka et al. Citation2019). Numerous applications of polycarbonates in buildings include fenestration systems, continuous windows, sheds, roofs, walls, and insulations using products with varying cell geometric properties, colors, and thicknesses. Moreover, PC panels are less expensive than traditional glazings and, when properly constructed, increase thermal performance, lowering energy expenditures significantly, particularly in commercial and industrial buildings(Moretti et al. Citation2018).
Polycarbonate windows are becoming increasingly popular, particularly when paired with other modern materials, such as nanomaterials, to reduce energy use in hot climatic regions, especially during the summer when air conditioning use is at its peak. Abdelhafez et al. (Citation2023) investigated two layers of polycarbonate panes filled with nanogel insulation as window openings to reduce heat transfer in Hail City of Saudi Arabia, showing a 14.3% decrease in annual energy use. Another study used experimental (thermal and optical) and numerical characterisation to explore three types of advanced multiwall PC panels (thickness 16, 25, and 40 mm) with translucent granular aerogel. The results show a significant impact on the aerogel, with a reduction in U-value of 46%−68% depending on the thickness of the aerogel layer. When the thickness of the sample was increased from the initial 16 mm thick to 40 mm, the U-value dropped from 1.4 W/m2K U-value to 0.6 W/m2K. The light transmittance for 16 and 40 mm is 0.61 and 0.42, respectively (Moretti et al. Citation2018). Similarly, Moretti, Zinzi, and Belloni (Citation2014) evaluated the performance of polycarbonate systems in buildings. They discovered that the thermal transmittance for 40 mm thick polycarbonate varied between 1.2 and 1.9 W/m2K. Furthermore, because of their various colors and typologies, polycarbonate materials can increase the material appearance (Moretti, Zinzi, and Belloni Citation2014).
Furthermore, A study investigated the performance of recycled plastics as a window glazing material, examining three samples, including polypropylene (PP), polystyrene (PS), and Polycarbonate (PC), to determine their optical properties and radiance. The outcome revealed that polycarbonate was the most transparent of the three products (Mashaly et al. Citation2017). Furthermore, PC panels are less expensive than traditional glazings; they significantly improve thermal performance and reduce energy costs when adequately designed, particularly in commercial and industrial buildings (Moretti et al. Citation2018). Therefore, polycarbonates could be a viable alternative to glass for building exterior glazing systems.
Energy consumption is one of the most important fields of study and interest worldwide, particularly in building design and construction. Several studies have been conducted to illustrate building energy consumption in various countries. Buildings in Singapore consume approximately 57% of the primary energy requirement, 47% in Switzerland, 40% in the United States, 42% in Brazil, 28% in China, 39% in the United Kingdom, 23% in Spain, and 25% in Japan (Al-Obaidi, Ismail, and Abdul Rahman Citation2013). Furthermore, another study confirmed that buildings consume approximately 40% of global energy (Zekraoui and Zemmouri Citation2017). ‘According to the US Energy Information Administration (EIA), global totals of primary energy consumption increased by 85% from 1980 to 2012, with average annual increases of 2%’ (Cao, Dai, and Liu Citation2016). Residential and commercial buildings in developed countries consume 20–40% of total energy (Hee et al. Citation2015). Previous research found that most of the energy consumed in buildings was due to two significant factors: air conditioning systems and artificial lighting fixtures (Al-Obaidi, Ismail, and Abdul Rahman Citation2013). Furthermore, energy consumed in buildings is primarily used for space heating and cooling in residential and commercial buildings that are directly related to the air conditioning system [(Hee et al. Citation2015), as cited in (Teotia and Soni Citation2014)].
Since a significant number of people worldwide spend 90% of their time indoors, buildings have become one of the most energy-intensive industries in the world (Cao, Dai, and Liu Citation2016). In the USA, the total energy consumption in buildings increased from 33.7% to 41.1% between 1980–2010 (Cao, Dai, and Liu Citation2016). One of the most efficient ways to decrease building energy consumption is to reduce energy losses from heating, cooling, and ventilation. A good building envelope design can reduce energy consumption by installing a proper HVAC system (Čekon and Struhala Citation2018). An excellent and advanced building envelope design can reduce 40% of the cooling and heating load (Cao, Dai, and Liu Citation2016), which prompts this paper to focus on the glazing system, the weakest element in the building envelope, to reduce energy consumption.
The building envelope can be identified as the boundary between outer and inner space and one of the significant parts of maintaining internal spaces cooling energy consumption (Alqahtani and Elgizawi Citation2020). Arguably the weakest point in the building envelope is the openings that include windows and doors due to the high transmittance of thermal energy into and out of the interior spaces (Alqahtani and Elgizawi Citation2020). Those openings can be affected by factors such as wall to openings ratio, construction, and material thermal properties (Alqahtani and Elgizawi Citation2020). Thermal evaluations of multi-pane opening glasses such as double (Kirankumar et al. Citation2020), triple (Gorantla et al. Citation2021), quadruple (Arici, Karabay, and Kan Citation2015), and 6-pane glazing systems (Kralj et al. Citation2019) have resulted in significant energy savings in buildings when compared to single-pane glazing. Studies illustrated that 20% of people depend on artificial lighting as a light source, and 76% recognise the need for natural daylight for interior buildings (Dolnikova, Katunsky, and Darula Citation2020). It is possible to understand the importance of natural daylight for people even though it is considered the weakest point in the envelope. More than half of the people, about 53% based on a global survey, stated that daylight affects their sleep, and 63% noted that natural light affects their productivity [(Dolnikova, Katunsky, and Darula Citation2020), as cited in (SABIC Citation2020)].
Moreover, high-performance opaque and windowed walls are required for sustainable energy use in building environments (Gorantla et al. Citation2021). Window openings significantly affect building energy consumption performance. The effect varies depending on material properties and window-to-wall ratio (WWR), described as the portion of the exterior wall comprising windows (Troup et al. Citation2019). In contrast, windows can provide aesthetics, admit lights, views, and thermal enclosure to buildings (Troup et al. Citation2019). ‘WWR affects building energy use and occupant comfort through heat transfer (conduction), solar heat gain (radiation), air leakage or ventilation (infiltration), and daylighting (lighting demand offset)’ [(Troup et al. Citation2019), as cited in (Schwartz Citation2015)]. The heat gain in summer and the heat loss in winter are directly affected by windows, considered the weakest thermal element in the building envelope (Zekraoui and Zemmouri Citation2017). One way to limit heat gain and heat loss in buildings is to minimise window size, as windows are responsible for 20% to 40% of wasted energy in buildings, which will affect natural light penetration into the building (Hee et al. Citation2015). Window thermal gain is a significant energy and cost savings consideration when utilising low-conductance and low-transmittance window glazing systems (Alqahtani and Elgizawi Citation2020).
Likewise, the Façade openings configuration significantly impacts the overall energy consumption of a building as it represents the most energy-sensitive part of the building envelope (Zekraoui and Zemmouri Citation2017). A study established that windows are responsible for 25-30% of heat loss in buildings because of poor insulating of window glazing (Zekraoui and Zemmouri Citation2017; Schwartz Citation2015). Allowing natural daylight through rooftop skylights may result in significant energy savings up to certain limits by minimising artificial lighting during the daytime (Dolnikova, Katunsky, and Darula Citation2020). However, savings from lighting might be offset by additional cooling load due to solar heat gain, especially on sunny days, and heat loss when heating is required during winter. Even a double-glazed skylight has a much lower thermal resistance value than most of the studied roof insulation values, which are replaced by skylights (Dolnikova, Katunsky, and Darula Citation2020). Glazing materials significantly impact interior building energy consumption, as the poor design of windows, skylights, and glazing can cause discomfort indoors (Al-Obaidi, Ismail, and Abdul Rahman Citation2013). As a result, many options and alternatives can be considered when selecting glazing types to meet design requirements and save energy.
Studies show that the construction and glazing types result in annual cooling load savings between 3050 and 5000 KWh (Florides et al. Citation2002), making the glazing system selection one of the essential aspects of designing windows (Hee et al. Citation2015). Since the glazing type significantly impacts thermal energy consumption, considering polycarbonate sheets as alternatives and potential glazing materials to replace conventional glass in this paper is critical and timely. The study investigates glazing applications in buildings, such as skylights and windows, through an energy simulation-based comparison of a SABIC polycarbonate multiwall sheet and a conventional glass glazing system. Therefore, this paper aims to evaluate the energy-saving potentials of polycarbonate to replace traditional glass used in buildings, considering their physical properties. Polycarbonates are polymer-based materials worth considering as a replacement for conventional glass because their raw material is readily available as a by-product of oil and gas production. Since Saudi Arabia is the world's largest producer of crude oil, using polycarbonate glazing, an oil by-product, is a sustainable idea that will boost the GDP of the Kingdom, conserve building energy, and lower greenhouse gas emissions by requiring less glass to be transported into the country. The extreme climatic condition (hot-dry and hot-humid) of Saudi Arabia and the poor heat transfer performance of conventional glazing catalysed this research work to improve the effectiveness of transparent and translucent building envelope systems. The simulation results are limited to the type of glass system and polycarbonate sheets used in the model. In addition, the building energy analysis is limited to the hot climates of Dhahran in Saudi Arabia.
1.1. Types of glass windows and skylights utilised in buildings
‘Glasses offer protection from natural and manmade disasters. Safety glasses used for construction are annealed, heat-strengthened, toughened, and laminated’ (Teotia and Soni Citation2014). Annealed Glass can be identified as the type of glass that slowly cools to relieve internal stresses; after it is formed, glass can be cut by scoring and snapping (Teotia and Soni Citation2014). Heat-strengthened glass has higher impact resistance and resistance to thermal stresses than annealed Glass (Teotia and Soni Citation2014). Fully tempered glass can also be described as toughened, which undergoes a thermal toughening process (Teotia and Soni Citation2014). Tempered glass is usually utilised when high-impact resistance safety glass is required in industrial locations or for commercial use. In addition, there is also laminated Glass, which consists of one or more glass panes of plastic glazing material laminated by an interlayer (Weimar and López Citation2018). Previously discussed glass types are specifically for panes utilised in windows or skylights, which is more related to the impact resistance property of glass rather than thermal insulation. Therefore, the types of glass that are usually applicable to windows or skylights, which focus on thermal insulation, directly impact building energy consumption. One of the famous window glazing types is doubled glazed window, which reduces energy consumption compared to a single-glazed window by improving the material’s insulating properties via the provided air gap between the panes as a thermal barrier [(Aguilar-Santana et al. Citation2020) as cited in 22]. Another window type is the triple-glazed window system, which reduces thermal transmittance due to its additional insulation, making it more advanced in thermal transmittance. The triple-glazed fenestration system allows less solar heat gain than a double-glazed window (Hee et al. Citation2015). “Another factor that makes three-layer glazed superior is its thickness, which decreases the thermal conductivity of the window as the window layer increases” (Hee et al. Citation2015).
1.2. The potential application of polycarbonate glazing
Polycarbonate (PC) is a high-performance thermoplastic that offers a combination of favorable properties such as transparency, high-impact resistance, and easy molding (Martínez et al. Citation2019). Polycarbonate is one of the materials capable of replacing traditional glass due to its light transmittance ability, lightweight, and insulation potential (Kua and Lu Citation2016). Polycarbonate is usually produced in three forms: solid sheets, corrugated sheets, and cellular or multiwall sheets (Schwartz Citation2015). It is frequently used in making translucent sheeting for building facades and roofing, such as corrugated roofing for garden sheds, multiwall extrusion sheeting for industrial buildings, and internally illuminated cladding for facades and internal walls (Kua and Lu Citation2016). Al-Obaidi, Ismail, and Abdul Rahman (Citation2013) indicate that polycarbonate benefits skylight systems in tropical regions by representing highly diffused light transmission and Low U-factors, making it an excellent daylighting material, often more robust than glass.
According to Moretti, Zinzi, and Belloni (Citation2014), the light transmittance of PC systems is 30–35% lower than that of similar glazing system solutions. Although the PC light transmission is diffused, it can decrease glare and increase visual comfort in specific circumstances. The measured light transmission value of PC systems is adequate for non-residential buildings because the transparent zones in such buildings are usually extensive and often cover the entire façade (Moretti, Zinzi, and Belloni Citation2014). Another study discovered that the Solar Factor (FS) varies between 75.4% in the colorless alveolar type to 47.7% in the white compact, as the Visible Light Transmittance (Tv) varies between 72% and 21.9% in the same polycarbonates, respectively. These values are lower than those of the same thickness, colorless compact polycarbonate, and colorless flat glass (Santos et al. Citation2018). Experimental tests indicate building heating and lighting energy consumptions are 66% and 89%, respectively, lower than the simulation predictions. It is concluded that the polycarbonate enclosure presents good thermal, solar, and optical behavior (Gallego Sánchez-Torija, Fernández Nieto, and Gálvez Huerta Citation2023).
Furthermore, Polycarbonate material technology is advancing, and currently, the material is protected from environmental degradation due to ultraviolet (UV) (Schwartz Citation2015). Polycarbonate provides clarity and UV protection due to coatings that can eliminate up to 99% UV, and it has high impact resistance (Al-Obaidi, Ismail, and Abdul Rahman Citation2013). It has a long history of application whenever a high-impact resistance is required due to its significant performance property (Schwartz Citation2015). Polycarbonate material can provide impact resistance 250 times greater than glass and 30 times more potent than acrylic sheets (Teotia and Soni Citation2014). The outstanding properties of polycarbonate make it worthwhile for various applications. Those properties are extreme toughness, resistance to burning (Self extinguish), transparency, and maintenance of engineering properties over a wide thermal range (Teotia and Soni Citation2014). It has also been used to harden entryways and ground-floor windows for security reasons to prevent intruders from accessing the building (Schwartz Citation2015). One of the studies in high ceiling warehouses and retail spaces reported outstanding performance of polycarbonate in terms of energy savings and well-being of occupants. The study published the positive impact of the case studies in major retailers in the USA, such as Costco and Walmart, that have experienced the benefits of plastic skylights (Schwartz Citation2015). A study investigated polycarbonate systems as a classic window in commercial buildings, obtaining U-values ranging from 1.2–1.9 W/m2K, providing an in-depth understanding of the thermal and optical behavior of polycarbonate panels as well as valuable data for accurate building integration analysis (Moretti, Zinzi, and Belloni Citation2014). However, the study was conducted in temperate climates of Italy, with the highest outdoor temperature of 20.20°C.
In terms of recyclability, polycarbonate also has an environmental advantage by waste recycling which involves two different kinds of processes: (1) Mechanical processing, where polycarbonate is pelletised by extrusion, then the produced particles can be employed for the elaboration of novel plastic products, and (2) Chemical processing that can reuse the plastic waste in cement concrete (Martínez et al. Citation2019). Based on Bristol daylighting system, polycarbonate is considered 100% recyclable. In contrast, many manufacturers only use 25%, as it is one of the materials utilised in Leadership in Energy and Environmental Design (LEED) projects (Al-Obaidi, Ismail, and Abdul Rahman Citation2013). Polycarbonate has been increasing as a possible replacement for glass, especially in architectural applications for buildings (Kua and Lu Citation2016).
1.3. Thermal properties of polycarbonate vs. glass
Traditional glass window systems are made of materials with a high heat transfer rate and High U-values compared to other elements, such as roofs, walls, and floors (Aguilar-Santana et al. Citation2020). U-value is identified as the total heat transfer coefficient or thermal transmittance, which is used to measure the effectiveness of windows insulation (Aguilar-Santana et al. Citation2020). Measured in W/m2K, the U-value is evaluated based on the air-to-air heat transfer through the window components (i.e. glazing, frame, the gap between the glass panes (if any), and spacers) from or into the building based on the ambient temperature difference (Aguilar-Santana et al. Citation2020). The thermal performance of windows is crucial in influencing cost-saving and energy consumption in buildings (Gustavsen, Uvsløkk, and Petter Jelle Citation2005). Windows can transport a large amount of energy in or out of facilities, such as in cold air, causing a large amount of heat loss which must be compensated by increasing the energy used for heating. The opposite happened in the hot climate, where a large amount of heat gain occurred, which must be balanced by increased energy used for cooling (Gustavsen, Uvsløkk, and Petter Jelle Citation2005). Hence, this section of the paper will focus on the thermal conductance comparison of conventional glass windows and polycarbonate as a possible replacement for glass for glazing systems to minimise a large amount of heat gain and loss because of windows and skylights. presents the thermal characteristics of conventional glazing and Polycarbonate (PC) Sheets window types and their characteristics(Hee et al. Citation2015; Čekon and Struhala Citation2018).
Table 1. Conventional Glass and Polycarbonate (PC) sheets window systems characteristics.
2. The approach
The study adopted a systematic approach to address the research objectives. The first stage is the review of relevant literature to identify the types, characteristics, properties, standards, and codes related to the application of conventional glass and polycarbonate sheets. The second stage of the approach is identifying an energy simulation tool, model development, weather data acquisition, and setting the essential boundary conditions, as illustrated in . The third stage is the comparative energy analysis of the traditional glass and polycarbonate sheets to compare their performance, considering both wall surface-to-windows and roof surface to skylights ratios. This stage implements building energy analysis simulation using a state-of-the-art design-builder software tool. The software is capable of performing both thermal and energy performance simulations. The simulation considers Dhahran’s weather data, which is a hot and humid climate. All the necessary boundary conditions have been set, including the thermal properties of the polycarbonate and glass materials, shapes and thickness, and all relevant standards and codes. The main weather parameters affecting polycarbonate performance include temperature, solar radiation, humidity, and wind speed, which are considered using the complete meteorological data of Dhahran, the study area in the simulation.
Moreover, the third stage of the approach analyses the results obtained in stage 2, which involves the application of simple descriptive statistics to analyse the outcome of the energy simulation considering. This stage also involves identifying the current and future potentials of polycarbonate as a replacement for conventional glass, considering different glazing configurations, including single, double, and triple glazing systems. The flowchart of the approach that resulted in energy efficient glazing system is illustrated in .
2.1. Thermal analysis simulation
This study conducted the thermal analysis simulation using design-builder energy plus software. The study used the Dhahran climate to simulate how different types of polycarbonate will affect thermal insulation in replacing different glass types of single, double, and triple glass systems in windows and skylights. The software created an imaginary building model to simulate an actual building in a hot, humid climate (Dhahran). The types of Polycarbonate and U-value used in the simulation are Multi-walls polycarbonate sheets from SABIC, categorised as highly insulated sheets, as shown in . As for the U-value for different glass types of single, double, and triple glazing, the U-value provided by the software will be utilised in the simulation. All simulation results of energy consumed for cooling to achieve thermal comfort are based on fanger.
2.2. Building model development
The building model was created using state-of-the-art design-builder simulation software. The 10 × 10 × 3.5 m building depicts a single-story building in Dhahran, Saudi Arabia. The building activity selected for the simulation model is a residential dwelling unit with a kitchen, and the construction type chosen for the building model is ‘project construction template.’ The details of the boundary conditions set for the simulation are presented in . The selected HVAC system is ‘Split + Separate Mechanical Ventilation,’ lighting type is set to default with a constant infiltration rate set to 0.3 ACH. The environmental control of heating and cooling is shown in . The simulations used fixed model setups, except for variations in types of windows and skylight glazings.
Table 2. Boundary conditions set for the simulation.
Table 3. U-Values & SHGC of Conventional Glass & Polycarbonate Sheets (SABIC, Citation2013; Citation2020; Design Builder, Citation2020).
The window-to-wall ratio applied for window opening simulation is a curtain wall 85% glazed, distributed on all sides of the buildings as shown in (a), which is fixed during the simulations of all alternatives, while the variation is in the various glazing type compared between Glass and Polycarbonate. However, the building model for skylight thermal analysis simulation is the same as the window opening model, except the model is not having any windows on building walls. The model has 100% horizontal glazing skylight roofing, as shown in (b). The skylight model only intended to study the effect of different glazing types focusing on skylights. The skylight simulation compares the Triple glass glazing system with a highly insulated single sheet of 5 wall x-structure polycarbonate (32 mm), the highest insulated sheet with the lowest U-value compared to others illustrated in . Since it is a skylight, the higher possible insulated system was selected for both Glass and Polycarbonate.
The U-values and solar heat gain coefficients (SHGC) are essential for studying building envelopes, particularly transparent ones such as glass and polycarbonate. These two parameters determine heat transfer and solar transmission through the envelope. Solar Heat Gain Coefficient (SHGC) measures how much solar energy passes through a window, expressed by a ratio of 0–1. It combines the glass solar transmittance and the re-radiated glass-absorbed heat to the indoor space (Liu and Wu Citation2022). Low emissivity glass has a comparatively low SHGC and high reflectance in the mid-infrared band. Low-e coatings save energy by reflecting thermal radiation from the outside (in summer) and inside (in winter) environments (Yi et al., Citation2021). Glazings’ total radiation transmitted, reflected, and absorbed is vital in calculating the SHGC. It is affected by the material’s optical properties, solar factor, incident solar radiation, overall heat transfer coefficient (U factor), and temperature difference between the outdoor and indoor environments (Sacht et al. Citation2021). The U-values and SHGC of all the conventional Glass and polycarbonate assemblies are presented in .
3. Results and discussion
This section presents the simulation results of all the investigated wall-opening and roof-opening (skylight) glazing alternatives, evaluating glazing systems using aluminum framing and unplasticized polyvinyl chloride (UPVC) framing systems. The twelve evaluated alternative wall and roof glazing systems are presented in the following sections.
3.1. The wall opening glazing alternatives with aluminum and UPVC framings
The study initially simulated the base case, a single 3 mm conventional Glass with aluminum frames, to identify energy consumption for cooling and heating interior space with a U-Value of 5.8 (W/m2K). The boundary conditions set to control the heating and cooling environment for the simulation are based on . The highest energy consumption was observed in August, and the lowest energy consumption was observed in January, February, and December, as illustrated in . The base-case 3 mm single clear glass was compared to 10 mm Single 5-wall rectangular polycarbonate, 16 mm Single 5-wall X-structure polycarbonate, and 16 mm Single 9-wall X-structure polycarbonate. The framing system used was aluminum without breakers. The outcome indicates that the energy consumption is highest in the base case compared to the other three alternatives. Based on the material data sheet, the single 16 mm 9-wall X-structure polycarbonate sheet has a U-value of 1.77 (W/m2K) and SHGC of 0.54. As a replacement for the single transparent Glass base-case simulation system, the single 16 mm 9-wall X-structure polycarbonate sheet consumes less cooling energy than all three single-glazing alternatives, as illustrated in . However, there is a flipped cooling energy consumption performance in the winter months of January, February, March, and December, as cooling requirements are negligible during these periods in the study area.
Likewise, the 3 mm double clear Glass was compared to 10 mm double 5-wall rectangular polycarbonate, 16 mm double 5-wall X-structure polycarbonate, and 16 mm double 9-wall X-structure polycarbonate with aluminum framing system without breakers. The result suggests that the cooling energy consumption is higher in the 3 mm double clear Glass with a 6 mm air gap than in the three double glazing alternatives. This outcome is evident due to the variation in the U-Value and other characteristics of the assemblies. Moreover, the 16 mm double 9-wall X-structure polycarbonate sheet consumes less cooling energy than all three glazing alternatives (3 mm double clear glass, 10 mm double 5-wall rectangular polycarbonate, 16 mm double 5-wall X-structure polycarbonate), as illustrated in . Moreover, the 10 mm double 5-wall rectangular polycarbonate has higher energy consumption than the 16 mm double 5-wall X-structure polycarbonate.
Furthermore, the 3 mm triple clear Glass was compared to 10 mm triple 5-wall rectangular polycarbonate, 16 mm triple 5-wall X-structure polycarbonate, and 16 mm triple 9-wall X-structure polycarbonate with aluminum framing system without breakers. The result indicates that the 3 mm triple clear glass with a 6 mm air gap compared to the three triple glazing alternatives consumes higher cooling energy, as illustrated in . The 16 mm triple 9-wall X-structure polycarbonate sheets recorded the best energy-saving potentials compared to all other triple-glazing systems simulated. Akin to the double-glazing alternatives, the 16 mm double 5-wall X-structure polycarbonate has higher energy-saving possibilities than the 10 mm double 5-wall rectangular polycarbonate throughout the year.
Based on the above outcomes, the 3 mm single conventional glazing type consumed more energy compared to the 16 mm single 5-wall x-structure polycarbonate sheet, 10 mm single 5-wall rectangular polycarbonate sheet, and 16 mm single 9-wall x-structure polycarbonate sheet. Similar outcomes were recorded when the four types of double-glazing systems and four triple-glazing systems were compared. The most energy-efficient polycarbonate sheet based on the simulation with aluminum framing is the 16 mm triple 9-wall x-structure polycarbonate sheet, followed by the 16 mm triple 5-wall x-structure polycarbonate sheet. The 16 mm double 9-wall x-structure polycarbonate sheet and the 10 mm triple 5-wall rectangular polycarbonate sheet have similar energy performance.
However, the simulation for the cases with UPVC framing follows the same scenario as those with aluminum frames by initially simulating the base case, a single 3 mm conventional clear glass with UPVC frames. The highest energy consumption was observed in August, and the lowest was in January, February, and December. The comparative analysis of the outcomes for the cases with UPVC frames is the same with aluminum frames. However, the cases with aluminum frames consume less cooling energy than those with UPVC frames in almost all cases.
3.2. Skylight opening glazing alternatives with aluminum and UPVC framings
The simulation for the cases with skylight glass openings follows the same format as the previous cases with wall openings. The skylight simulation was also conducted for both aluminum and UPVC frames. The simulation was initiated with the base case, a single 3 mm conventional clear glass with aluminum frames for the cases with aluminum frames. The highest energy consumption was observed in July and August, and the lowest energy consumption was observed in January and December, . The base case (3 mm single clear glass) was compared to 10 mm Single 5-wall rectangular polycarbonate, 16 mm Single 5-wall X-structure polycarbonate, and 16 mm Single 9-wall X-structure polycarbonate. The framing system used was aluminum without breakers. The results indicate that the base case (3 mm single clear glass) consumed the highest cooling energy compared to the other three single-glazing polycarbonate alternatives. This outcome is evident due to the better performance of polycarbonate materials in excluding heat than conventional glass. presents the comparative analysis of the four single-glazing systems. Moreover, the 10 mm single 5-wall rectangular polycarbonate sheet as a replacement for the single glass system base-case simulation consumes less cooling energy than the 3 mm single glazing, as illustrated in . The 16 mm Single 9-wall X-structure polycarbonate sheet consumes lower cooling energy than other single-glazing alternatives.
Likewise, the study compared the 3 mm double clear Glass to 10 mm double 5-wall rectangular polycarbonate, 16 mm double 5-wall X-structure polycarbonate, and 16 mm double 9-wall X-structure polycarbonate sheets with aluminum framing system without breakers. The result suggests that the cooling energy consumption is higher in the 3 mm double clear Glass with a 6 mm air gap than in the three double-glazing polycarbonate alternatives (). This outcome further strengthens the superiority of polycarbonate glazing systems’ energy conservation over conventional glass assemblies. The 16 mm double 9-wall X-structure polycarbonate sheets with aluminum framing recorded the leased energy consumption compared to the clear glass and other two polycarbonate assemblies. Furthermore, the 10 mm double 5-wall rectangular polycarbonate sheet consumes less cooling energy than the conventional glazing alternative. It also consumed less energy than the 10 mm single 5-wall rectangular polycarbonate sheet, 16 mm single 5-wall x-structure polycarbonate sheet, and 16 mm single 9-wall x-structure polycarbonate sheet.
Similarly, the study investigated the 3 mm triple clear glass compared to 10 mm triple 5-wall rectangular polycarbonate, 16 mm triple 5-wall X-structure polycarbonate, and 16 mm triple 9-wall X-structure polycarbonate with aluminum framing systems without breakers. The result indicates that the 3 mm triple clear glass with a 6 mm air gap compared to the three triple glazing polycarbonate assemblies consumes higher cooling energy, as illustrated in . The 10 mm triple 5-wall rectangular polycarbonate sheets consume less energy than all types of conventional glazings, both 10 mm single and double 5-wall rectangular polycarbonate sheets, 16 mm single and double 5-wall x-structure polycarbonate sheets, and 16 mm single 9-wall x-structure polycarbonate sheet. The most energy-efficient polycarbonate sheet based on the simulation with aluminum framing is the 16 mm triple 9-wall x-structure polycarbonate sheet. The second most energy-efficient polycarbonate is the 16 mm triple 5-wall x-structure polycarbonate sheet and then the 16 mm double 9-wall x-structure polycarbonate sheet, as illustrated in .
Furthermore, the simulation for the skylight cases with UPVC framing follows the same format as the previous cases with aluminum frames by initially simulating the base case, a single 3 mm conventional clear glass with UPVC frames. The highest energy consumption was observed in July and August, while the lowest was in January and December. The comparative analysis of the outcomes for the cases with UPVC frames is the same as those with aluminum frames. Unlike the wall glazing systems, where aluminum frames consume less cooling energy than the cases with UPVC frames in almost all cases, the skylight recorded virtually the same energy consumption between aluminum and UPVC framing systems with negligible differences.
4. Findings and discussions
Based on the simulation results, various polycarbonate sheets performed better than conventional glazing systems, demonstrating the capabilities of polycarbonate sheets as a replacement for generic 3 mm single, double, and triple glazing systems. The availability of polycarbonate raw materials as a by-product of oil and gas is another crucial advantage for oil-producing countries such as Saudi Arabia that will exploit its ability to replace the conventional glazing system, mainly imported products. The judicious utilisation of available resources will significantly contribute to sustainability by eliminating transportation costs.
The annual cooling energy consumption analysis for various conventional and skylight glazing alternatives indicates that the 3 mm traditional single clear Glass installed as a skylight has the highest energy consumption compared to those installed on walls. The total cooling energy consumption for the wall glazing is 39,565.18 kWh (aluminum framing) and 39, 541.64 kWh (UPVC framing), while for the skylight glazing, 63,340.74 kWh (aluminum framing) and 63, 340.84 kWh (UPVC framing), as illustrated in . This outcome is not unconnected with the direct exposure of skylights to solar radiation throughout the day compared to walls that receive shading based on the solar position, altitude, and movement. However, a significant improvement in energy consumption was noticed with the 16 mm triple 5-wall x-structure polycarbonate sheet. The total annual energy consumption for cooling interior space was 25,834 kWh (aluminum framing) and 25,818 kWh (UPVC framing) for wall glazing systems and 35,776.47 kWh (aluminum framing) and 35,776.57 kWh (UPVC framing) for skylight glazing. Thus, the total annual energy consumption for interior cooling of wall systems in the 16 mm triple 5-wall x-structure polycarbonate sheet and the 3 mm conventional single clear glass was 25,834 kWh and 39,565.18 kWh, respectively, resulting in 35% energy savings. Similar outcomes were recorded for the skylights, with the cooling energy consumption for the 16 mm triple 5-wall x-structure polycarbonate sheet and the 3 mm conventional single clear glass was 35,776.47 kWh and 63,340.74 kWh, respectively, resulting in 44% energy savings.
Figure 10. Annual cooling Energy (electric) consumption for various conventional and skylight glazing types (kWh).

Furthermore, the total cooling energy-saving potentials of the various glazing alternatives for walls and skylights were analysed. The results indicated that, compared to the base case (3 mm single clear glass), the 16 mm triple 9-wall X-structure polycarbonate scored the highest energy-saving percentage. This consumption is followed by the 16 mm triple 5-wall X-structure polycarbonate, the 16 mm double 9-wall X-structure polycarbonate, and the 10 mm triple 5-wall rectangular polycarbonate. The 16 mm double 9-wall X-structure polycarbonate sheets saved the highest cooling energy for skylight glazing cases. In comparison, 10 mm triple 5-wall rectangular polycarbonate sheets saved more cooling energy for the wall glazing cases, as illustrated in . This finding implies that the internal structure of polycarbonate assemblies is critical to their performance in horizontal (skylight) and vertical (wall) positions, as some polycarbonate sheets are better for wall glazing than others, depending on internal structures. In the fourth position in terms of energy-saving is the 16 mm double 5-wall X-structure polycarbonate sheet (). According to the findings, polycarbonate sheets of various configurations and properties can save significant energy compared to conventional glazing systems considering the hot and humid climates of the study area (Dhahran, Saudi Arabia).
Figure 11. Total cooling Energy (electric) savings for various conventional and skylight glazing types (%).

However, comparing similar glazing assemblies, the polycarbonate sheets have outperformed the conventional glazing systems in all assembles. The best-case analysis (16 mm triple 9-wall X-structure polycarbonate sheet) shows significant energy-saving compared to the traditional 3 mm triple clear glazing. The best case also saved more energy than the 16 mm triple 5-wall X-structure polycarbonate sheet glazing and 10 mm triple 5-wall rectangular polycarbonate sheet, as illustrated in . Similarly, the 16 mm double 9-wall X-structure polycarbonate sheet also saved higher cooling energy than conventional 3 mm double clear glazing, 16 mm double 9-wall X-structure polycarbonate sheet, and 10 mm double 5-wall rectangular polycarbonate sheet. Likewise, the 16 mm single 9-wall X-structure polycarbonate sheet saved higher energy compared to conventional 3 mm single glazing, 16 mm single 5-wall X-structure polycarbonate sheet, and 10 mm single 5-wall rectangular polycarbonate sheet, as illustrated in . Thus, applying locally available polycarbonate sheets in buildings in hot and oil-producing countries such as Saudi Arabia is more sustainable than imported conventional glazing.
4.1. The impact of glazing alternatives on the window-to-wall ratio (WWR)
Window openings affect building energy consumption performance, depending on material properties and window-to-wall ratio (WWR), described as the percentage of the exterior wall made up of windows (Troup et al. Citation2019). This study examined the impacts of the window-to-wall ratio (WWR) by decreasing the WWR from 85% to 30% in four (4) different types of window glazings, as illustrated in . The outcome indicated that WWR significantly impacts the cooling energy consumption of all glazing alternatives. The average cooling electric energy consumption increase is 50% when the WWR is changed from 85% to 30%. The effect of WWR is similar for both traditional glass and polycarbonate glazing alternatives. Thus, depending on the building’s daylight requirement and visual comfort needs, WWR shall be considered from the design stage to strike a balance between daylight requirement, visual comfort, and building energy consumption.
4.2. The impact of glazing alternatives on green house gas (GHG) emission
The sustainability parameter of this study is the prudent use of available resources that will significantly contribute to sustainability by eliminating transportation costs. Rather than importing regular glass outside the kingdom, the existing material (polycarbonate) will be used to perform all glass functions in buildings, thus reducing GHG emissions. The environmental impact of the annual total energy consumption of the case study model building is affected by the type of glazing used for external openings. To measure the environmental impact of the different glazing types, estimate the greenhouse gas emission using an oil and natural gas conversion factor presented in . The total conversion in Saudi Arabia (KSA) is calculated based on 61% natural gas and 39% oil, the percentage of natural gas and oil, the two primary fuel for electricity in the kingdom in the year 2021.
Table 4. Conversion factor from GHG emissions in kg to energy unit of kWh (UK Government Citation2022, June 22)
Thus, the greenhouse emission factor in Saudi Arabia can be estimated using the following relationship:
(1)
(1)
While to calculate the total gas emissions per year, equation 2 below is used.
(2)
(2)
The results of annual total greenhouse gas (GHG) emissions of the case study model building for the different types of windows glazing and skylight glazing panes are presented in and , respectively. The windows openings’ highest total greenhouse gas emissions (CO2 + CH4 + N2O) were as follows for single glazing was the 3 mm single ordinary clear glass, the annual total greenhouse gas emission is 9,301 kg, which is the highest of all alternatives, and the lowest emission of 5,740 kg was recorded by the 16 mm Triple 9-wall X-structure polycarbonate/6 mm air, as illustrated in . This result translates to a 38% reduction in GHG emissions by changing the glazings from 3 mm regular glass to 16 mm Triple 9-wall X-structure polycarbonate. Compared to the 16 mm triple 5-wall X-structure polycarbonate, which recorded 6,073 kg of GHG emission, the best alternative, 16 mm triple 9-wall X-structure polycarbonate, recorded 5,740 kg, translating to a 6% decrease in GHG emission ().
Figure 14. Total annual GHG emissions of different types of glazings sheet alternatives in skylights.

Furthermore, the skylight glazing cases recorded similar outcomes, with the 3 mm single clear glazing recording the highest GHG emission of 15, 891 kg and the lowest GHG emission of 7,631 kg was recorded by the 14 mm triple 9-wall X-structure polycarbonate, as illustrated in . Although 16 mm double 9-wall X-structure polycarbonate with GHG emission of 9408 kg is a double glazing skylight alternative, it has lower GHG emission than 3 mm triple clear glazing, which recorded 13,648 kg, translating to a 30% decrease in GHG emission ().
5. Conclusion and recommendation
In conclusion, the thermal analysis simulation for multiwall polycarbonate sheet and conventional glass reveals that polycarbonate sheet performs better in window and skylight opening simulations. However, the triple glass system performed slightly better in skylight thermal analysis than the double and single polycarbonate sheets. Therefore, according to the results of the model building simulation, polycarbonate sheets outperformed glass in most cases of thermal performance and energy savings in both walls and skylight openings. As a result, polycarbonate sheets can be an excellent alternative to glass due to their thermal and physical properties. Polycarbonate sheets are known for their high-impact resistance, safety, and lightweight design, which are the main strengths of polycarbonate. Based on this study, polycarbonate sheets can significantly differ in thermal performance compared to glass, as they outperformed glass in most instances.
The result shows that the polycarbonate sheet performs better than ordinary glass. However, the triple glass system performed slightly better for skylight thermal analysis than the polycarbonate sheet. The 3 mm conventional single clear glass installed as a skylight has the highest energy consumption compared to those installed on walls. The total annual energy consumption for interior cooling of wall systems in the 16 mm triple 5-wall x-structure polycarbonate sheet and the 3 mm conventional single clear glass was 25,834 kWh and 39,565.18 kWh, respectively, resulting in 35% energy savings. Similar outcomes were recorded for the skylights, with the cooling energy consumption for the 16 mm triple 5-wall x-structure polycarbonate sheet and the 3 mm conventional single clear glass was 35,776.47 kWh and 63,340.74 kWh, respectively, resulting in 44% energy savings. The difference in energy consumption between the aluminum and UPVC framing systems is negligible.
On the other hand, traditional glass is considered a better option whenever visible clarity is required, as most multiwall polycarbonate has less than 50% visual clarity (SABIC, Citation2013). Polycarbonate is used primarily for skylights, green buildings, and safety glazing, owing to its lightweight, strength, and daylight allowability. Polycarbonate sheets could be a viable alternative to glass for curtain wall facades and windows, with visibility and thermal performance improved to the point where they can outperform glass in thermal performance and at least match it in visibility.
5.1. Limitations and further studies
Due to resource and time constraints, the study does not cover some essential polycarbonate sheets performance, such as the visual performance of polycarbonate glazing, the environmental impact of polycarbonate sheets, the impact resistance of the polycarbonate glazing system, and the economic analysis of polycarbonate glazing. These critical issues will be addressed in subsequent publications.
Disclosure statement
No potential conflict of interest was reported by the author(s).
Acknowledgements
The author wishes to acknowledge the support provided by King Fahd University of Petroleum and Minerals, Dhahran, Saudi Arabia.
References
- Abdelhafez, M. H. H., A. A. Aldersoni, M. M. Gomaa, E. Noaime, M. M. Alnaim, M. Alghaseb, and A. Ragab. 2023. “Investigating the Thermal and Energy Performance of Advanced Glazing Systems in the Context of Hail City, KSA.” Buildings 13(3): 752–768. https://doi.org/10.3390/buildings13030752.
- Aguilar-Santana, J., H. Jarimi, M. Velasco-Carrasco, and S. Riffat. 2020. “Review on Window-Glazing Technologies and Future Prospects.” International Journal of Low-Carbon Technologies 15: 112–120. https://doi.org/10.1093/ijlct/ctz032.
- Al-Obaidi, K., M. Ismail, and A. Abdul Rahman. 2013. “A Review of Skylight Glazing Materials in Architectural Designs for a Better Indoor Environment.” Modern Applied Science 8: 68–82. https://doi.org/10.5539/mas.v8n1p68.
- Alqahtani, L., and L. Elgizawi. 2020. “The Effect of Openings Ratio and Wall Thickness on Energy Performance in Educational Buildings.” International Journal of Low-Carbon Technologies 15: 155–163. https://doi.org/10.1093/ijlct/ctz064. Advance Access publication December 4, 2019.
- Arici, M., H. Karabay, and M. Kan. 2015. “Flow and Heat Transfer in Double, Triple, and Quadruple Pane Windows.” Energy and Buildings 86: 394–402. https://doi.org/10.1016/j.enbuild.2014.10.043.
- Cao, X., X. Dai, and J. Liu. 2016. “Building Energy-Consumption Status Worldwide and the State-of-the-art Technologies for Zero-Energy Buildings During the Past Decade.” Energy and Buildings 128: 198–213. https://doi.org/10.1016/j.enbuild.2016.06.089.
- Čekon, M., and K. Struhala. 2018. “Polycarbonate Multiwall Panels Integrated in Multi-Layer Solar Façade Concepts.” IOP Conference Series: Materials Science and Engineering 415: 012019–012027. https://doi.org/10.1088/1757-899X/415/1/012019.
- Cellura, M., F. Guarino, S. Longo, and G. Tumminia. 2018. “Climate Change and the Building Sector: Modelling and Energy Implications to an Office Building in Southern Europe.” Energy for Sustainable Development 45: 46–65. https://doi.org/10.1016/j.esd.2018.05.001.
- DesignBuilder (2020). DesignBuilder Software Ltd - Simulation. Retrieved October 29, 2022, from https://designbuilder.co.uk/simulation#:∼:text=DesignBuilder%20is%20the%20most%20established,renewables%2C%20HVAC%20and%20financial%20analysis.
- Dolnikova, E., D. Katunsky, and S. Darula. 2020. “Assessment of Overcast sky Daylight Conditions in the Premises of Engineering Operations Considering two Types of Skylights.” Building and Environment 180: 106976–106990. https://doi.org/10.1016/j.buildenv.2020.106976.
- Florides, G., S. Tassou, S. Kalogirou, and L. Wrobel. 2002. “Measures Used to Lower Building Energy Consumption and Their Cost Effectiveness.” Applied Energy 73: 299–328. https://doi.org/10.1016/S0306-2619(02)00119-8.
- Fukuoka, S., I. Fukawa, T. Adachi, H. Fujita, N. Sugiyama, and T. Sawa. 2019. “Industrialization and Expansion of Green Sustainable Chemical Process: A Review of Non-Phosgene Polycarbonate from CO2.” Organic Process Research & Development 23 (2): 145–169. https://doi.org/10.1021/acs.oprd.8b00391.
- Gallego Sánchez-Torija, J., M. A. Fernández Nieto, and MÁ Gálvez Huerta. 2023. “Thermal, Lighting, and Energy Performances of Buildings Constructed with Polycarbonate Panels. Case Study of a Classroom in Madrid.” Energy Efficiency 16 (5): 35–49. https://doi.org/10.1007/s12053-023-10120-w.
- Gorantla, K., S. Shaik, K. J. Kontoleon, D. Mazzeo, V. R. Maduru, and S. V. Shaik. 2021. “Sustainable Reflective Triple Glazing Design Strategies: Spectral Characteristics, air-Conditioning Cost Savings, Daylight Factors, and Payback Periods.” Journal of Building Engineering 42: 103089–103107. https://doi.org/10.1016/j.jobe.2021.103089.
- Gustavsen, A., S. Uvsløkk, and B. Petter Jelle. 2005. “Numerical and Experimental Studies of the Effect of Various Glazing Spacers on the Window U-Value and the Glazing Temperature.” Proceedings of the 7th Symposium on Building Physics in the Nordic Countries 1: 1003–1010.
- Hee, W., M. Alghoul, B. Bakhtyar, O. Elayeb, M. Shameri, M. Alrubaih, and K. Sopian. 2015. “The Role of Window Glazing on Daylighting and Energy Saving in Buildings.” Renewable and Sustainable Energy Reviews 42: 323–343. https://doi.org/10.1016/j.rser.2014.09.020.
- Jiang, X., T. Wang, M. Jiang, M. Xu, Y. Yu, B. Guo, D. Chen, et al. 2020. “Assessment of Plastic Stocks and Flows in China: 1978-2017.” Resources, Conservation and Recycling 161: 104969–104978. https://doi.org/10.1016/j.resconrec.2020.104969.
- Kirankumar, G., S. Saboor, S. S. Vali, D. Mahapatra, A. B. Talanki Puttaranga Setty, and K.-H. Kim. 2020. “Thermal and Cost Analysis of Various air Filled Double Glazed Reflective Windows for Energy Efficient Buildings.” Journal of Building Engineering 28: 101055–101069. https://doi.org/10.1016/j.jobe.2019.101055.
- Kralj, A., M. Drev, M. Žnidaršič, B. Černe, J. Hafner, and B. P. Jelle. 2019. “Investigations of 6-Pane Glazing: Properties and Possibilities.” Energy and Buildings 190: 61–68. https://doi.org/10.1016/j.enbuild.2019.02.033.
- Kua, H., and Y. Lu. 2016. “Environmental Impacts of Substituting Tempered Glass with Polycarbonate in Construction – An Attributional and Consequential Life Cycle Perspective.” Journal of Cleaner Production 137: 910–921. https://doi.org/10.1016/j.jclepro.2016.07.171.
- Li, N., Q. Meng, L. Zhao, H. Li, J. Wang, N. Zhang, P. Wang, and S. Lu. 2023. “Thermal Performance Study of Multiple Thermal Insulating Glazings with Polycarbonate Films as Interval Layers.” Journal of Building Engineering 76: 107159–107172. https://doi.org/10.1016/j.jobe.2023.107159.
- Liu, X., and Y. A. Wu. 2022. “A Review of Advanced Architectural Glazing Technologies for Solar Energy Conversion and Intelligent Daylighting Control.” Architectural Intelligence 1(10): 1–32. https://doi.org/10.1007/s44223-022-00009-6.
- Martínez, A., G. Barrera, C. Díaz, L. Córdoba, F. Núñez, and D. Hernández. 2019. “Recycled Polycarbonate from Electronic Waste and its use in Concrete: Effect of Irradiation.” Construction and Building Materials 201: 778–785. https://doi.org/10.1016/j.conbuildmat.2018.12.147.
- Mashaly, I. A., Y. Rashed, S. El-Haggar, and K. Nassar. 2017. The Viability of Using Different Types of Recycled Plastic as Glazing in Windows. Building Simulation Applications, 2017-February, 13–18.
- Moretti, E., M. Zinzi, and E. Belloni. 2014. “Polycarbonate Panels for Buildings: Experimental Investigation of Thermal and Optical Performance.” Energy and Buildings 70: 23–35. https://doi.org/10.1016/j.enbuild.2013.11.045.
- Moretti, E., M. Zinzi, F. Merli, and C. Buratti. 2018. “Optical, Thermal, and Energy Performance of Advanced Polycarbonate Systems with Granular Aerogel.” Energy and Buildings 166: 407–417. https://doi.org/10.1016/j.enbuild.2018.01.057.
- Rabnawaz, M., I. Wyman, R. Auras, and S. Cheng. 2017. “A Roadmap Towards Green Packaging: The Current Status and Future Outlook for Polyesters in the Packaging Industry.” Green Chemistry 19: 4737–4753. https://doi.org/10.1039/C7GC02521A.
- Ramana Maduru, V., S. Shaik, E. Cuce, A. Afzal, H. Panchal, and P. Mert Cuce. 2022. UV-coated Acrylics as a Substitute for Generic Glazing in Buildings of Indian Climatic Conditions. CO: Prospective for energy savings.
- SABIC. 2013. LEXAN Thermoclear Multiwall Polycarbonate Sheet. Jubail, Eastern Province: SABIC.
- SABIC. 2020. LEXAN Sheet Portfolio. Jubail, Eastern Province: SABIC.
- Sacht, H. M., L. Bragança, M. Almeida, and R. Caram. 2021. “Specification of Glazings for Façades Based on Spectrophotometric Characterization of Transmittance.” Sustainability 13 (10): 5437–5456. https://doi.org/10.3390/su13105437.
- Santos, J. C. P. D., M. S. Temp, M. R. Fernandes, and R. C. A. de Lima. 2018. “Comportamento ótico de Vidros e Policarbonatos Translúcidos Frente à Radiação Solar.” Matéria (Rio de Janeiro) 23 (3): e12159–12172. https://doi.org/10.1590/S1517-707620180003.0493.
- Schwartz, K. 2015. “Polycarbonates in Construction.” The IAPD Magazine.
- Teotia, M., and R. Soni. 2014. “Polymer Interlayers for Glass Lamination-A Review.” International Journal of Science and Research (IJSR) 3 (8): 1264–1270. https://www.ijsr.net/getabstract.php?paperid=2015595.
- Troup, L., R. Phillips, M. J. Eckelman, and D. Fannon. 2019. “Effect of Window-to-Wall Ratio on Measured Energy Consumption in US Office Buildings.” Energy and Buildings 203: 109434–109444. https://doi.org/10.1016/j.enbuild.2019.109434.
- UK Government. 2022. Greenhouse gas Reporting: Conversion Factors 2022. GOV.UK. The Publication of the UK Government Department for Energy Security and Net Zero and Department for Business, Energy & Industrial Strategy. Retrieved November 11, 2022, from https://www.gov.uk/government/publications/greenhouse-gas-reporting-conversion-factors-2022.
- Weimar, T., and S. López. 2018. Research on Thin Glass-Polycarbonate Composite Panels. Conference on Architectural and Structural Applications of Glass. https://doi.org/10.7480/cgc.6.2148.
- Yi, Z., Yingyan l., Dikai X., Jingtao X., Hua Q., Dongliang Z., and Ronggui Y. 2021. “Energy saving analysis of a transparent radiative cooling film for buildings with roof glazing.” Energy and Built Environment 2(2): 214–222. https://doi.org/10.1016/j.enbenv.2020.07.003.
- Zekraoui, D., and N. Zemmouri. 2017. “The Impact of Window Configuration on the Overall Building Energy Consumption Under Specific Climate Conditions.” Energy Procedia 115: 162–172. https://doi.org/10.1016/j.egypro.2017.05.016.
- Zheng, J., and S. Suh. 2019. “Strategies to Reduce the Global Carbon Footprint of Plastics.” Nature Climate Change 9 (5): 374–378. https://doi.org/10.1038/s41558-019-0459-z.