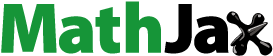
Abstract
The reduction of energy consumption in industrial processes is a challenge to be confronted within the framework of the United Nations’ Sustainable Development Goals. The present study compares the energy loss per cycle of two kinematically equivalent mechanisms: a slider-crank and an eccentric cam with a translational roller follower. We use the work-energy theorem to evaluate energy losses by using a viscous friction model in a stationary regime. The innovation of this study lies in the energetic comparison to identify the best and worst alternatives by analyzing the contribution of their main geometrical parameters, such as crank length, rod-crank length ratio, roller radius and follower offset. The aim is to provide guidelines to help machinery designers to take relevant preliminary decisions that affect energy efficiency. Herein, we include analytical models, numerical simulations and experimental results using a test stand that can be adapted to other planar one degree-of-freedom mechanisms. In this context, we conclude that an eccentric cam mechanism with a big roller radius and no offset provides the best energetic efficiency among the aforementioned mechanisms.
1. Introduction
The slider-crank mechanism () and the eccentric cam mechanism () are planar one degree-of-freedom mechanical transmission systems used to transform a full rotational input motion into a translational output motion. Both mechanisms are kinematically equivalent (Cardona and Clos Citation2009; Norton Citation2002; Rothbart Citation2003) and are common solutions in automated production machinery. The existing design guidelines (Norton Citation2002) state that a cam mechanism is more difficult and expensive to manufacture than an equivalent linkage mechanism. However, a cam mechanism can be more compact and easier to design for a specific output motion, and may be the only possible solution if, for example, the crank length is so small that it physically prevents the installation of two revolute pairs.
Pabiszczak and Kowal (Citation2022) studied the energetic efficiency of an eccentric rolling transmission (ERT) as an alternative to a gear transmission. As a function generator, Ottaviano et al. (Citation2008) compared a cam transmission with a noncircular gear coupled with a slider-crank mechanism. For circular-arc cams, acceleration, and torque analysis has been carried out as well (Lanni, Carbone, et al. Citation2006; Lanni, Ceccarelli and Cajun, Citation2006).
Even though previous authors have compared several mechanisms, there are few available studies that focus on energy loss or efficiency evaluation, despite being an issue that is gaining relevance in machinery design. Freudenstein, Mayourian, and Maki (Citation1983) proposed a coefficient to evaluate the energy loss in cam mechanisms with flat-faced followers for force-closed and form-closed systems; they studied several basic cam curves and compared the values for this coefficient. Yau and Longman (Citation2011) assessed the potential of reducing energy usage in a force-closed cam mechanism using variable pitch springs between the coils. For the specific case of an ERT, Pabiszczak and Kowal (Citation2022) calculated its efficiency and validated it experimentally using torque meters on the input and output shafts. Yang et al. (Citation2022) proposed a new nonlinear variable stiffness actuator (VSA) by using an eccentric cam mechanism with a translational roller follower against a variable-in-length leaf spring. They achieve a low-energy consumption VSA design that eliminates sliding friction in some pairs using a combination of rollers and rollers bearings.
Energy losses are related to friction. The quantification of friction between two solids is a complex problem, especially from a tribological perspective (Alakhramsing et al. Citation2018a, Citation2018b, Citation2019). There is plenty of scientific literature dealing with different friction force models. For example, Pennestrì et al. (Citation2016) presented a review and numerical efficiency comparison of eight widespread friction models and Marques et al. (Citation2016) reviewed 21 well-known different friction force models.
Several authors have applied Coulomb friction models to the translational lower pair that exists in the slider or follower link (Freudenstein, Mayourian, and Maki Citation1983; Norton Citation2002; Rothbart Citation2003; Wu et al. Citation2009). Other authors have applied viscous friction coefficients to cam mechanisms (Català et al. Citation2016; Ouyang et al. Citation2017) or in a rolling device based on a five-bar linkage mechanism (Yu et al. Citation2022). Moreover, at the cam-roller contact, other authors have applied a combination of Coulomb and viscous friction models (De Groote et al. Citation2022) and elastohydrodynamic lubrication (EHL) models (Català et al. Citation2013; Alakhramsing et al. Citation2018b). Bai et al. (Citation2022) studied a planar slider-crank mechanism assuming axial and radial dimensional clearances by using a modified Coulomb friction model that considers a sliding friction coefficient.
Experimental validations of dry friction, viscous friction and rolling resistance coefficients are reported in several works (De Groote et al. Citation2022; Li, Cheng, and Xie Citation2019; Li, Cheng, and Xie Citation2019).
The present article compares the energy losses between two competitive solutions: a slider-crank mechanism and an eccentric cam mechanism with a translational roller follower. For each mechanism, we quantify the energy that is lost per cycle at the lower pairs by applying viscous friction models in a stationary regime, while assuming ideal kinematic pairs with no clearances and well-lubricated. Hence, only the kinematic solution is necessary, allowing for an immediate study to detect energy efficiency trends over a large range of dimensions of the main geometrical parameters: crank length, rod-crank length ratio, roller radius, and follower offset.
Nevertheless, for the higher pair between the eccentric cam and the roller, energy loss due to elastic deformation is evaluated using the mixed-elastohydrodynamic friction model based on Masjedi and Khonsari (Citation2015). Additionally, vector theorems have been solved for both mechanisms to allow the dynamic comparison transmission efficiency of force. Despite the fact that the highest Hertz pressures are located at the contact between the eccentric cam and the roller (finite contact line), we prove that energy loss is negligible for the case study and assume no sliding, as done by Sanmiguel-Rojas and Hidalgo-Martínez (Citation2016). Next, we assume that energy loss due to elastic deformations in the lower pairs with contact surface areas can be also neglected, as carried out by Alakhramsing et al. (Citation2018a, Citation2018b, Citation2019).
The innovations we present herein are: (i) the evaluation of the influence of the main geometric parameters in terms of the total energy losses to identify the best alternative among the kinematically equivalent mechanisms; and (ii) the validation of the trends in terms of energy losses (the best and worst options) using a test stand, which can be adapted to other planar one degree-of-freedom mechanisms, or to experimentally evaluate energy losses predicted for other friction models.
This article is organized as follows. In Section 2, we state the problem formulation. In Section 3, we first develop a numerical example and then describe our chosen assumptions in order to compare them in terms of the total energy loss per cycle. The results of this comparison are depicted for a range of scales of their main geometrical parameters. We present our experimental results in Section 4, and finally, we outline our conclusions in Section 5.
2. Problem formulation
2.1. Slider-crank mechanism formulation
A slider-crank mechanism () has four lower pairs with three movable links: a crank Equation(1)(1)
(1) , a rod Equation(2)
(2)
(2) and a slider Equation(3)
(3)
(3) .
According to , all possible configurations, velocities, and accelerations of the mechanism are described by generalized coordinates and the first and second temporal derivatives,
and
respectively. The independent coordinate is
By applying the closed loop method, we obtain two constraint equations, as presented in EquationEqs. (1)
(1)
(1) and Equation(2)
(2)
(2) .
(1)
(1)
(2)
(2)
The velocities of the mechanism are obtained with the first temporal derivative of EquationEqs. (1)
(1)
(1) and Equation(2)
(2)
(2) . Rearranging the terms, EquationEqs. (3)
(3)
(3) and Equation(4)
(4)
(4) are obtained to show the dependent velocities
and
as a function of the independent angular velocity
(3)
(3)
(4)
(4)
shows the Free Body Diagram (FBD) for the three links of the slider-crank mechanism. The parameters required for the dynamic simulations are explained in .
Table 1. Dynamic variables and parameters for the slider-crank mechanism.
EquationEquations (5–13) are obtained using vector theorems for each movable link of the mechanism.
(5)
(5)
(6)
(6)
(7)
(7)
(8)
(8)
(9)
(9)
(10)
(10)
(11)
(11)
(12)
(12)
(13)
(13)
The friction torques
and the friction force
are calculated with EquationEqs. (14–17), respectively.
(14)
(14)
(15)
(15)
(16)
(16)
(17)
(17)
Despite not being necessary in a slider-crank mechanism, an external force () has been added for comparison purposes with a force-closing eccentric cam mechanism.
The total energy loss for each cycle is quantified using EquationEq. (18)
(18)
(18) as the integral of instantaneous power losses,
(18)
(18)
2.2. Eccentric cam mechanism formulation
An eccentric cam mechanism () has three lower pairs and one higher pair, and 3 movable links: an eccentric cam Equation(1)(1)
(1) , a roller Equation(2)
(2)
(2) and a follower Equation(3)
(3)
(3) . The geometrical parameters presented in are described in .
Table 2. Geometric parameters for the eccentric cam mechanism.
The linear displacement function of the eccentric cam mechanism is equal to the output of the slider-crank mechanism, which means Considering EquationEqs (1)
(1)
(1) and Equation(2)
(2)
(2) ,
is defined according to EquationEq. (19)
(19)
(19) .
(19)
(19)
It is common to define using EquationEq. (20)
(20)
(20) , where:
is a motion law defined with its minimum value equal to zero (
) and
is the prime circle radius. This is shown in and is calculated according to EquationEq. (21)
(21)
(21) after choosing a value for the base circle cam radius
and a value for the roller radius
(20)
(20)
(21)
(21)
The motion law is defined as from , it is derived that
Then
is obtained using EquationEq. (22)
(22)
(22)
(22)
(22)
By combining EquationEq. (20)(20)
(20) with Equation(22)
(22)
(22) and recognizing that
the prime circle radius for an eccentric cam is thus
The first and second derivatives of with respect to
and
using EquationEq. (19)
(19)
(19) are
(23)
(23)
(24)
(24)
In the literature, it has been demonstrated that the distance between point O and
is equal to
(), which only depends on geometric parameters and is independent of the angular velocity of the cam.
The common geometrical indexes to evaluate whether a cam profile is acceptable are presented in : the pressure angle and the radius of curvature of the cam profile
where
is the radius of curvature of the pitch curve, when using its equivalence to a slider-crank mechanism as being equal to the rod length,
Values between are recommended for angle
for translational followers in order to avoid a jam in the follower’s guide (Norton Citation2002; Rothbart Citation2003). For the case of circular-arc cams, which are equivalent to slider-crank mechanisms per circular arc portions, Lanni, Carbone, et al. (Citation2006) recommend that, for reducing pressure angle and acceleration peaks, one solution is to add an offset
to the follower. Circular-arc cams are feasible for low-cost and low-speed small transmissions.
To avoid high surface stresses at the contact between a cam and a roller, the recommendation is that the minimum radius of curvature of the cam pitch curve should be at least 1.5 to 3 times larger than the radius of the roller follower
(Norton Citation2002).
shows the FBD for the three links of the eccentric cam mechanism. The parameters required for the dynamic simulations are explained in .
Table 3. Dynamic variables and parameters for the eccentric cam mechanism.
EquationEquations (25–33) are obtained using vector theorems for each movable link of the mechanism. Sliding is assumed to be null at contact point J.
(25)
(25)
(26)
(26)
(27)
(27)
(28)
(28)
(29)
(29)
(30)
(30)
(31)
(31)
(32)
(32)
(33)
(33)
The friction torque is calculated as in the former case using EquationEq. (14)
(14)
(14) and the friction torque
is calculated using EquationEq. (34)
(34)
(34) , where
is the angular velocity of the roller.
(34)
(34)
If the roller rotation is blocked, sliding at the cam-roller contact will occur. The modulus of the sliding velocity is calculated as
using EquationEq. (35)
(35)
(35) , as can be deduced from .
(35)
(35)
If the roller can rotate freely around revolute pair B, and assuming no sliding at the cam-roller contact, the roller rotates with an angular velocity We calculate
using EquationEq. (35)
(35)
(35) , and the angular acceleration of the roller
is obtained as the first temporal derivative of EquationEq. (36)
(36)
(36) .
(36)
(36)
(37)
(37)
The friction force is calculated analogously to the former case using EquationEq. (17)
(17)
(17) , being aware that
The external force is required to avoid follower jump in a force-closure cam mechanism. This force is provided with a linear spring using EquationEq. (38)
(38)
(38) , where
is the minimum dead point from
obtained using EquationEq. (39)
(39)
(39) .
(38)
(38)
(39)
(39)
If the external force is provided by a compression spring, it does not affect the energy loss per cycle because it is assumed to be a conservative force. EquationEq. (40)
(40)
(40) evaluates the total energy loss
per cycle.
(40)
(40)
EquationEquation (40)(40)
(40) considers no energy loss associated with sliding velocities at the cam-roller contact, as assumed in others studies (Sanmiguel-Rojas and Hidalgo-Martínez Citation2016). Nevertheless, to validate this assumption, a model to evaluate energy loss due to sliding and elastic deformation is presented. The friction force in the direction of the sliding velocity
is obtained using EquationEq. (41)
(41)
(41) , where
is a traction coefficient calculated according to Masjedi and Khonsari (Citation2015). Their friction model considers elastic deformations at the contact, which requires to determine internal reactions in pairs, for example using vector theorems. The substitution of the internal tangential force
for
is required in EquationEqs. (25–30).
(41)
(41)
The energy loss per cycle for the higher pair is calculated with EquationEq. (42)
(42)
(42) , as the integral of instantaneous power loss,
where SRR is a slide-to-roll ratio (SRR) (Alakhramsing et al. Citation2018a, Citation2018b; Gromadova Citation2021) and
is the sliding velocity calculated with EquationEq. (35)
(35)
(35) .
(42)
(42)
3. Simulation results
In this Section, we first compare a slider-crank mechanism with specific dimensions to two alternatives of eccentric cam mechanisms in terms of the total energy loss per cycle, the internal reactions in pairs and the transmission efficiency of force. Secondly, we solve a range of geometrical parameter scales required for these mechanisms and plot workspaces used to: i) determine which presents the lowest values of a slider-crank or an eccentric cam mechanism; and ii) identify trends in how modifying geometrical parameters affects
3.1. Case study
summarizes the required parameters for the chosen slider-crank mechanism and the two equivalent eccentric cam mechanisms: one with a smaller roller radius than the eccentric cam radius of curvature; and one with a larger roller radius than the eccentric cam radius of curvature. These three mechanisms, with parameters shown in , are assembled on the experimental test stand, as explained in Section 4.
Table 4. Required parameters for the numerical examples.
To facilitate comparison between these kinematically equivalent mechanisms, we consider:
All mechanisms have the same lubrication conditions. Revolute pair O is grease-sealed lubricated. Revolute pairs A, B, the prismatic pair and the higher pair are lubricated with Vaseline oil (Krafft Citationn.d.).
In all mechanisms there exist the revolute pairs O, B and the prismatic pair, so the same viscous friction coefficients
and
are assumed, as can be observed in . Their experimental determination is explained in Appendix A.
shows the transmission efficiency of motion evaluated as the ratio between the output linear velocity and the input angular velocity
shows the linear acceleration of the follower and the slider,
required for vector theorems. For the three mechanisms both curves are the same because they are kinematically equivalent mechanisms.
Figure 5. (a) Transmission efficiency of motion; (b) Linear acceleration of the slider and the follower.
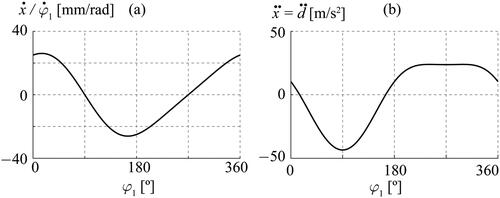
shows the angular velocities and the angular accelerations
for both eccentric cam mechanisms, respectively. The rod’s angular velocities
and angular accelerations
of the slider-crank mechanism are also depicted.
depicts the internal reactions in each pair, that require solving vector theorems. depicts the transmission efficiency of force evaluated as the ratio between the external force (output force) and the input torque motor
Figure 7. Internal reactions for each pair: (a) Slider-crank; (b) Eccentric cam with small roller radius; (c) Eccentric cam with big roller radius; (d) Transmission efficiency of force.
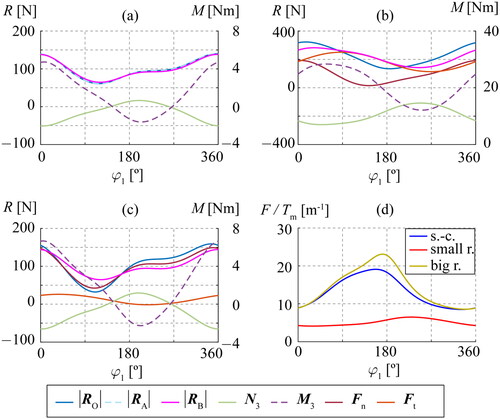
For all the pairs, the case with the highest internal reactions is the eccentric cam mechanism with the small roller radius. The slider-crank mechanism and the eccentric cam mechanism with the big roller radius present similar curve shapes for the internal reactions in the common pairs, despite values being slightly lower for the slider-crank mechanism. The mechanism with the best transmission efficiency of force (highest values) is the eccentric cam mechanism with the big roller radius, followed closely by the slider-crank mechanism.
If deformation and sliding are considered, the friction force in the direction of the sliding velocity is obtained using EquationEq. (41)
(41)
(41) , with the mean value of the normal force
being 94 N and 93 N according to for the eccentric cam with the big roller radius and the small roller radius, respectively. An SRR = 5% is assumed, which is a maximum case compared to other studies of cam mechanisms (Alakhramsing et al. Citation2018b; Norton Citation2002). presents the values required to calculate
some obtained from the eccentric cam mechanism assembled on the experimental test stand explained in Section 4. The traction coefficients are 0.046 and 0.014 for the big and small roller radii cases, respectively.
Table 5. Required parameters for traction coefficient (Masjedi and Khonsari Citation2015).
Using EquationEq. (42)(42)
(42) ,
values are 0.04 and 0.03 J for the eccentric cam with the big and small roller radii, respectively. These negligible levels in
associated with the sliding friction force component and elastic deformation agree with Alakhramsing et al. (Citation2018a, Citation2018b, Citation2019).
depicts the per cycle. For the slider-crank mechanism, we use EquationEq. (18)
(18)
(18) and for the eccentric cams, EquationEq. (40)
(40)
(40) .
The mechanism with the lowest is the eccentric cam with the big roller radius (44.3 J), then the slider-crank (47.4 J, a 7% increase), and finally the eccentric cam with the small roller radius (122.5 J, a 175% increase).
The amount of added by revolute pair O and the prismatic pair are the same for all three mechanisms. The differences come from revolute pairs A and B. Revolute pair A contributes to
only in the slider-crank. For both eccentric cams, we assume that the higher pair contribution is null. The differences in relative angular velocities () affect the values of
associated with revolute pair B. Even though the eccentric cam with the big roller radius has a higher
at revolute pair B, its contribution is lower than the one from revolute pair A of the slider-crank.
3.2. Energy loss comparison workspaces
In this Section we present the energetic comparison between the analyzed mechanisms by means of plotting two workspaces. These allow for a sensitivity analysis of against a range of the main geometrical parameters.
For a slider-crank, the output motion of slider is a function of
and
For an eccentric cam, we obtain the prime circle as
thus, only the radius of the roller
is needed as an extra parameter.
Restrictions Equation(43)(43)
(43) to Equation(46)
(46)
(46) define the imposed conditions between the four geometric parameters.
(43)
(43)
(44)
(44)
(45)
(45)
(46)
(46)
The crank length is the input parameter. For the offset of the slider
only two extreme cases are studied:
and
Restriction Equation(45)
(45)
(45) ensures a full crank rotation and pressure angle recommendations,
Restriction Equation(46)
(46)
(46) ensures the cam pitch curve (
) recommendations by imposing values for roller radius
shows for the three mechanisms. The values imposed on
and the viscous friction coefficients are the ones shown in .
In , the comparison must be done individually for each crank length The conclusions to reduce energy loss per cycle are:
The most favorable cases are always for the eccentric cam with the largest roller radius (
) and null offset (
).
is slightly higher for the slider-crank with the null offset. The reduction of the roller radius (
) causes an increment of the angular velocity of the roller
(). Therefore, the
associated with revolute pair B increases.
The non-null offset cases have higher
than the null ones.
depicts the relative differences with regard to the most efficient case. We conclude that the maximum differences in are obtained for small-sized mechanisms (
around 10 mm) and for low
ratios ().
4. Experimental results
4.1. Test stand description
The test stand shown in was built to validate the classification in terms of observed with the simulated results: the best alternative is the eccentric cam mechanism with the big roller radius, then the slider-crank mechanism, and finally the eccentric cam mechanism with the small roller radius. The mechanisms can be assembled by sharing the following common elements: 1) fixed frame; 2) DC motor with a double stage gear reduction; 3) shaft coupling; 4) flywheel; 5) main shaft; 6) final shaft coupling; and 7) translational output element with a closure spring. The mechanism under study is assembled through the final shaft coupling, where the crank is embedded. The test stand includes two inductive sensors. The first one (highlighted in green in ) points outward to a 30-tooth pulley fixed to the main shaft, which acts as an angular digital encoder. The angular velocity of the main shaft
is obtained as the first temporal derivative of this measure. The second inductive sensor (highlighted in red in ) points outward to the translational output element. It is used to output a step signal per cycle. Measurements are recorded by a digital signal analyzer with a 2 MHz sampling rate. gathers information about the shared components for this test stand.
Table 6. Test stand specifications of the shared components.
shows the three kinematically equivalent mechanisms assembled on the test stand. Mechanism parameters and lubrication conditions are those explained in Section 3.1.
4.2. Comparison of energy loss per cycle
All experimental tests begin in a stationary regime, then the machine is switched off and the transient period is recorded until standstill. shows an example for each mechanism. The left grey region indicates the initial stationary regime. The right grey region indicates a rebound of the translational output elements due to the follower closure spring just before standstill. The blue lines indicate a complete cycle.
Figure 13. Test results: (a) Eccentric cam with small roller radius; (b) Eccentric cam with big roller radius; (c) Slider-crank.

The experimental comparison of energy loss per cycle is carried out by applying the work-energy theorem using EquationEq. (47)(47)
(47) . The theorem is applied over the whole system between two different mechanical states, 1 and 2, which correspond to an entire number of complete cycles of
Notice that, for an entire cycle, the work carried out by conservative forces is null.
(47)
(47)
We obtain the variation in the kinetic energy via EquationEq. (48)
(48)
(48) , where:
is the inertia of the whole system reduced to the angular coordinate
is the angular velocity at the end of a cycle (state 2), and
is the angular velocity at the beginning of a cycle (state 1).
(48)
(48)
For the slider-crank is calculated using EquationEq. (49)
(49)
(49) and for the eccentric cam mechanisms
is calculated with EquationEq. (50)
(50)
(50) , where C is obtained using EquationEq. (51)
(51)
(51) .
is dependent on
according to EquationEq. (2)
(2)
(2) . The moment of inertia of the eccentric cam, along the z-axis, referring to its center of inertia (
) is 3.9·10−3 kg·m2 and 2.5·10−4 kg·m2 for the small and big roller mechanisms, respectively.
(49)
(49)
(50)
(50)
(51)
(51)
plots for the three mechanisms using the values from and .
Even though is function of
as a first approach, we assume that the inertia of the whole system is equivalent and constant between the three mechanisms. The contribution of the inertia of the shared elements
is constant and is much higher than the contribution of the inertia of the elements of each mechanism. The differences between the value of
and the higher values are: for the slider-crank mechanism, 1.4%, for the eccentric cam with the big roller radius, 2.1% and for the eccentric cam with the small roller radius, 7.4%.
Assuming the same constant value of for the three mechanisms, we can state that the energy loss per cycle
is, as a first approach, proportional to
shows as function of
because when using a viscous friction model, energy losses vary as a function of relative velocities. The three sets of experiments for each mechanism carried out have been represented in . On the right-hand side, a zoomed region around
30 rad/s is shown and the mean value of the three experiments per alternative is represented with a dot.
In , the starting point is at rad2/s2, indicating that the system is in a stationary regime. It should be pointed out that the mean stationary angular velocity
using a small roller (around 36 rad/s) is lower than the angular velocity using a big roller or a slider-crank (around 37.5 rad/s). Moreover, the system speed in a stationary regime is sensitive to friction variations because the voltage of the DC motor is constant (controlled).
During the transient period, the variation of is a function of angular velocity, which agrees with a viscous friction model. The results shown in ranks the alternatives in terms of reducing
per cycle. The best is the eccentric cam mechanism with the big roller radius, then the slider-crank mechanism, and finally the eccentric cam mechanism with the small roller radius. Furthermore, the derived experimental data show only slight differences between the slider-crank and the eccentric cam with the big roller radius. Both experimental trends agree with the trends presented for the simulated results in Section 3.1 and 3.2.
5. Conclusions
This study compares the total energy loss per cycle between kinematically equivalent slider-crank and eccentric cam mechanisms. Our aim is to provide machinery designers with the knowledge to evaluate energy losses in order to decide among the types of mechanisms and the values for geometrical parameters within a given system.
From our analysis we conclude that an eccentric cam mechanism, with a roller radius closer to 1.5 times the minimum cam pitch curve and without a follower offset, is the best solution to reduce the energy loss, while considering recommendations provided by Norton (Citation2002) in order to avoid high Hertzian pressures. Furthermore, it also provides the best transmission efficiency of force. Reducing the roller radius and providing follower offset increase the total energy loss. For small mechanisms, the energy loss sensitivity is higher while modifying the geometrical parameters (crank length, rod-crank length ratio, roller radius and follower offset).
Based on our experimental validations we can conclude that a viscous friction model is an effective preliminary approach. If a deeper analysis is required to fine tune the amount of energy loss, more complex friction models could be used, despite then having to calculate internal reactions in pairs using for example vector theorems and while including other tribological parameters.
Finally, we consider that: i) the proposed methodology can be expanded to other cam mechanisms such as circular arc cams; and ii) the experimental approach presented to evaluate energy losses can be further used to compare with other planar one degree-of-freedom mechanisms or friction models.
Disclosure statement
No potential conflict of interest was reported by the author(s).
References
- Alakhramsing, S. S., M. B. de Rooij, M. Drogen, and D. J. Schipper. 2019. “The Influence of Stick–Slip Transitions in Mixed-Friction Predictions of Heavily Loaded Cam–Roller Contacts.” Proceedings of the Institution of Mechanical Engineers, Part J: Journal of Engineering Tribology 233 (5): 676–691. https://doi.org/10.1177/1350650118789515
- Alakhramsing, S. S., M. B. de Rooij, D. J. Schipper, and M. Drogen. 2018a. “A Full Numerical Solution to the Coupled Cam–Roller and Roller–Pin Contact in Heavily Loaded Cam–Roller Follower Mechanisms.” Proceedings of the Institution of Mechanical Engineers, Part J: Journal of Engineering Tribology 232 (10): 1273–1284. https://doi.org/10.1177/1350650117746899
- Alakhramsing, S. S., M. B. de Rooij, D. J. Schipper, and M. Drogen. 2018b. “Lubrication and Frictional Analysis of Cam–Roller Follower Mechanisms.” Proceedings of the Institution of Mechanical Engineers, Part J: Journal of Engineering Tribology 232 (3): 347–363. https://doi.org/10.1177/1350650117718083
- Bai, Z., T. Liu, J. Li, and J. Zhao. 2022. “Numerical and Experimental Study on Dynamic Characteristics of Planar Mechanism with Mixed Clearances.” Mechanics Based Design of Structures and Machines 51 (11): 6142–6165. https://doi.org/10.1080/15397734.2022.2036998
- Cardona, S., and D. Clos. 2009. Teoria de màquines. 2nd ed. Barcelona: Edicions UPC.
- Català, P., M. A. de los Santos, J. M. Veciana, and S. Cardona. 2013. “Evaluation of the Influence of a Planned Interference Fit on the Expected Fatigue Life of a Conjugate Cam mechanism- A Case Study.” Journal of Mechanical Design 135 (8): 081002. https://doi.org/10.1115/1.4024373
- Català, P., M. A. de los Santos, J. M. Veciana, and S. Cardona. 2016. “Avoiding Early Failures in conjugate cam Mechanism by Means of Different Design Strategies.” Journal of Mechanical Design 138 (1): 1–9. https://doi.org/10.1115/1.4031805
- De Groote, W., S. V. Hoecke, and G. Crevecoeur. 2022. “Prediction of Follower Jumps in Cam-Follower Mechanisms: The Benefit of Using Physics-Inspired Features in Recurrent Neural Networks.” Mechanical Systems and Signal Processing 166: 108453. https://doi.org/10.1016/j.ymssp.2021.108453
- Freudenstein, F., M. Mayourian, and E. R. Maki. 1983. “Energy Efficient Cam-Follower Systems.” Journal of Mechanisms, Transmissions, and Automation in Design 105 (4): 681–685. https://doi.org/10.1115/1.3258534
- Gromadova, M. 2021. “Sliding at the Cam Mechanisms.” In New Advances in Mechanisms, Mechanical Transmissions and Robotics: Proceedings of MTM & Robotics 2020, ed. E. C. Lovasz, I. Maniu, I. Doroftei, M. Ivanescu, and C. M. Gruescu, 364–374. Cham: Springer. https://doi.org/10.1007/978-3-030-60076-1_33
- Krafft. n.d. Vaseline Oil Data Sheet. https://www.krafft.es/aceite-de-vaselina/. Accessed April 23, 2023.
- Lanni, C., G. Carbone, M. Ceccarelli, and E. Ottaviano. 2006. “Numerical and Experimental Analyses of Radial Cams with Circular-Arc Profiles.” Proceedings of the Institution of Mechanical Engineers, Part C: Journal of Mechanical Engineering Science 220 (1): 111–125. https://doi.org/10.1243/095440605X69282
- Lanni, C., M. Ceccarelli, and C. L. Cajun. 2006. “An Experimental Validation of Three Circular-Arc Cams with Offset Followers.” Mechanics Based Design of Structures and Machines 34 (3): 261–276. https://doi.org/10.1080/15397730600830351
- Li, M., W. Cheng, and R. Xie. 2019. “Design and Experimental Validation of a Cam-Based Constant-Force Compression Mechanism with Friction Considered.” Proceedings of the Institution of Mechanical Engineers, Part C: Journal of Mechanical Engineering Science 233 (11): 3873–3887. https://doi.org/10.1177/0954406218806015
- Marques, F., P. Flores, J. C. Pimenta, and H. M. Lankarani. 2016. “A Survey and Comparison of Several Friction Force Models for Dynamic Analysis of Multibody Mechanical Systems.” Nonlinear Dynamics 86 (3): 1407–1443. 016-2999-3. https://doi.org/10.1007/s11071-
- Masjedi, M., and M. M. Khonsari. 2015. “An Engineering Approach for Rapid Evaluation of Traction Coefficient and Wear in Mixed EHL.” Tribology International 92: 184–190. https://doi.org/10.1016/j.triboint.2015.05.013
- Norton, R. L. 2002. Cam design and manufacturing handbook. New York: Industrial Press, Inc.
- Ottaviano, E., D. Mundo, G. A. Danieli, and M. Ceccarelli. 2008. “Numerical and Experimental Analysis of Non-Circular Gears and Cam-Follower Systems as Function Generators.” Mechanism and Machine Theory 43 (8): 996–1008. https://doi.org/10.1016/j.mechmachtheory.2007.07.004
- Ouyang, T., P. Wang, H. Huang, N. Zhang, and N. Chen. 2017. “Mathematical Modeling and Optimization of Cam Mechanism in Delivery System of an Offset Press.” Mechanism and Machine Theory 110: 100–114. https://doi.org/10.1016/j.mechmachtheory.2017.01.004
- Pabiszczak, S., and M. Kowal. 2022. “Efficiency of the Eccentric Rolling Transmission.” Mechanism and Machine Theory 169: 104655. https://doi.org/10.1016/j.mechmachtheory.2021.104655
- Pennestrì, E., V. Rossi, P. Salvini, and P. P. Valentini. 2016. “Review and Comparison of Dry Friction Force Models.” Nonlinear Dynamics 83 (4): 1785–1801. https://doi.org/10.1007/s11071-015-2485-3
- Rothbart, H. A. 2003. Cam design handbook. New York: McGraw-Hill, Inc.
- Sanmiguel-Rojas, E., and M. Hidalgo-Martínez. 2016. “Cam Mechanisms Based on a Double Roller Translating Follower of Negative Radius.” Mechanism and Machine Theory 95: 93–101. https://doi.org/10.1016/j.mechmachtheory.2015.08.018
- Veciana, J. M., L. Jordi, and E. Lores. 2021. “Residual Vibration Reduction in Back- and Forth Moving Systems Driven by Slider-Crank Mechanisms Working through a Dead Point Configuration.” Mechanism and Machine Theory 158: 104239. https://doi.org/10.1016/j.mechmachtheory.2020.104239
- Wu, L. I., C. H. Liu, K. L. Shu, and S. L. Chou. 2009. “Disk Cam Mechanisms with a Translating Follower Having Symmetrical Double Rollers.” Mechanism and Machine Theory 44 (11): 2085–2097. https://doi.org/10.1016/j.mechmachtheory.2009.05.012
- Yang, Z., X. Li, J. Xu, R. Chen, and H. Yang. 2022. “A New Low-Energy Nonlinear Variable Stiffness Actuator for the Knee Joint.” Mechanics Based Design of Structures and Machines 51 (11): 6041–6055. https://doi.org/10.1080/15397734.2022.2033626
- Yau, H., and R. W. Longman. 2011. “Investigation of the Potential for reducing energy Usage in Cam Follower Systems by Means of Variable Pitch Springs.” “.” In IMECE011: Proceedings of the International Mechanical Engineering Congress and Exposition, IMECE 2011, 7:361–69. Denver: ASME. https://doi.org/10.1115/IMECE2011-63214
- Yu, L., Y. Zhang, N. Feng, T. Zhou, X. Xiong, and Y. Wang. 2022. “Energy Consumption Analysis of a Rolling Mechanism Based on a Five-Bow-Shaped-Bar Linkage.” Applied Sciences 12 (21): 11164. https://doi.org/10.3390/app122111164
Appendix A.
Experimental determination of viscous friction coefficients
A.1 Determination of 

In the test carried out, the linear bushing in the prismatic pair has relative vertical motion while the translation output element of is fixed. The bushing is between two springs in parallel as shown in .
(a) shows the test stand assembled to a shaker table to carry out a vibration test and experimentally obtain the damping coefficient of the bushing. To register input and output signals, two accelerometers are used: the input signal comes from the accelerometer located at the base; the output signal comes from the one attached to the bushing. As an input signal, a random acceleration (between 5 Hz and 300 Hz) with a power spectral density of 0.5 (m/s2)2/Hz is used. The sample frequency is 100 Hz recording for a 10 min period and the signals are processed within a 10 000 sample sliding window. The experimental viscous friction coefficient is 24.40 N/(m/s).
A.2 Determination of 
and 

The methodology applied is based on the steps described in Veciana, Jordi, and Lores (Citation2021). A pendulum system shown in is built for the experimental determination of the viscous damping friction coefficient of the flanged sintered bronze bushings used in revolute pairs A and B (). The revolute pair O is constructed using the same flanged sintered bronze bushing and the same steel cylindrical pin used in revolute pair B.
The linearized motion equation assuming small oscillations around 0 is
(A52)
(A52)
The values of the parameters used in EquationEq. (A52)(A52)
(A52) are:
0.603 kg,
492 mm and
2.62·10−2 kg·m2.
A set of 5 experiments is carried out, applying vaseline oil to the bushing (Krafft n.d.). The angular velocity is experimentally measured with a gyroscope attached to the pendulum bar. The analytical general solution
of EquationEq. (A52)
(A52)
(A52) is known and the first temporal derivative
is obtained. The parameters of
are obtained by minimizing the accumulated differences between
and
using the least squares method as an objective function. Then, the viscous damping friction coefficient is determined as an optimized parameter of
This is done for each set of experiments and the obtained mean value of
and
is 0.026 N·m/(rad/s).
A.3 Determination of 

The test stand is mounted only with elements 1 to 6 of , without any of the compared mechanisms. The friction torque is obtained by rotating at low speed through indirect measure of the force (gauge) at the flywheel radius. The averaged experimental value of is 0.17 N·m/(rad/s). This value corresponds to the viscous damping friction coefficients of the shared elements, including the row double greased-sealed angular ball bearings that support the main shaft.