ABSTRACT
The metallurgical industry simultaneously represents both one of the most crucial sectors of the industry and a sector with significant emissions. Alongside methods to mitigate the harmful impact on the environment, we need to consider reducing the hazardous, toxicological impact on the human organism. In this article, we explore the life cycle of two steel production methods: BF-BOF and EAF. The results of our research indicate that the EAF method has a lesser impact on the human organism. Our goal is to identify the key processes that constitute the primary source of emissions of hazardous substances in each of these two pathways. We investigated the distribution of the impact of production processes in each of the two aforementioned methods. In traditional steel production using oxygen converters, the primary source of emissions is the production of pig iron in blast furnaces. In the second case, it was the used electricity. For this study, we applied the LCA methodology, which enables determining the impact of the investigated process throughout its entire life cycle. In the conclusion, possible options for mitigating the harmful impact of each case are discussed.
1. Introduction
Alongside rapid progress, the world is faced with global challenges that must be addressed (Mitchell and Janzen Citation2010). One of the most crucial challenges of today is to prevent rapid global warming (Moser Citation2010). Addressing this issue requires a global scale approach (“Eggleston et al. Citation2006). Significant sources of greenhouse gas emissions include the metallurgical industry (Ren et al. Citation2021). This sector accounts for approximately 8% of global greenhouse gas emissions (Arens, Åhman, and Vogl Citation2021). Today, it is a highly important industrial sector, with steel being one of the most widely used materials worldwide. Global demand for steel has risen to 1.4 billion tons per year (Cullen, Allwood, and Bambach Citation2012). It is also projected that due to population growth and economic development, steel production will increase by 25–30% by the year 2050 (Holappa Citation2020). It becomes evident that to achieve goals related to halting global warming, it is essential to address emission reduction in the metallurgical industry. Currently, global steel is produced through two main pathways: BF-BOF and EAF (Bowman and Krüger Citation2009; C. Wang, Ryman, and Dahl Citation2009).
The escalation of global pollution in ecosystems by thousands of industrial and natural chemical compounds stands as a paramount environmental challenge confronting humanity (Schwarzenbach et al. Citation2006). Contemporary science has identified numerous toxic chemical substances, classifiable into various categories based on their properties and effects. Despite most of these compounds being present in low concentrations, many can induce significant toxicological issues, particularly when present as components of complex mixtures. Heavy metals are particularly hazardous among the substances in this list. The most dangerous include arsenic, cadmium, chromium, lead, and mercury, which are systemic toxicants known to cause damage to many organs, even at lower exposure levels (Tchounwou et al. Citation2012). They are also classified as human carcinogens (Tomatis et al. Citation1989). Since heavy metals are not biodegradable, they accumulate in the environment and enter the food chain, where their excessive accumulation in the human body leads to harmful consequences (Smiljanić et al. Citation2019). Stehle’s research indicates that industrial and domestic processes produce millions of tons of potentially toxic chemical substances (Stehle and Schulz Citation2015). Many scientists have different views on the impact of industry, particularly metallurgy, on the accumulation of potentially toxic elements in adjacent areas (Pawełczyk, Božek, and Grabas Citation2016). Petranikova et al. (Citation2020) considers the metallurgical industry as a source of wastewater and dust containing various polluting toxic substances. Moreover, numerous studies confirm that this sector has a harmful impact on the environment and human health (Wei et al. Citation2015). In steel production, metals, polycyclic aromatic hydrocarbons, binding compounds, carbon oxide, respiratory dust, quartz, and other harmful substances are released. J. Wang et al. (Citation2021). confirmed the exceeding of permissible levels of Tl, As, Pb, Cd, Cr, Cu, and Mn in soils near metallurgical plants. Results from other studies showed that the air in steel melting shops of metallurgical plants has an elevated content of heavy metals and is hazardous to human health, particularly with an increased level of Pb, increasing the risk of cancer (Dehghani et al. Citation2021). A long-term study of cancer incidence rates in areas adjacent to large metallurgical plants showed that the standardised incidence ratio (SIR) for lung cancer was 40% higher than the average in postal code areas located in two municipalities adjacent to the industrial zone (Breugelmans et al. Citation2013). Additionally, soils near metallurgical plants have elevated concentrations of Cd, Cr, and Pb, exceeding international standards and likely affecting human health (Alfaro et al. Citation2022). Therefore, vegetables grown in this area have an increased content of these elements, considered hazardous to humans. These results are not isolated. Ranko Dragovich’s research confirms elevated concentrations of heavy metals (Cd, Co, Cr, Cu, Fe, Mn, Ni, Pb, and Zn) in surface soils near a steel foundry compared to global norms (Dragović et al. Citation2014). In addition to heavy metals, dioxins and coplanar PCBs can also be emitted near metallurgical plants and accumulate in the bodies of residents in adjacent areas over an extended period (Fierens et al. Citation2007).
The level and type of harmful substances from metallurgical enterprises may vary depending on the method of steel production (Seppälä et al. Citation2002). Currently, two of the most common methods of steel production are known. The first is steel production in oxygen converters based on pig iron (BF-BOF), and the second is steel production in electric arc furnaces using scrap (EAF) (Kumar, Roy, and Kumar Sen Citation2020). A schematic representation of the mentioned processes is shown in .
Figure 1. The schematic representation of the steel production process in an oxygen converter and an electric arc furnace with delineated boundaries of the investigated system.
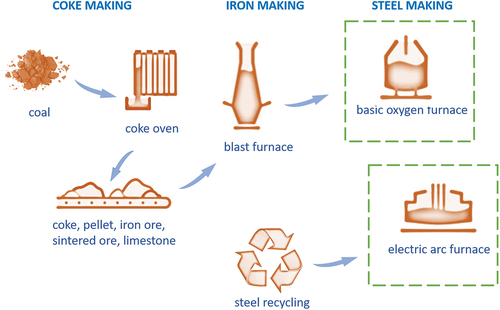
BF-BOF is more energy-intensive and requires a more significant amount of potential fuel (Li et al. Citation2018). Steel production in an oxygen converter involves the preliminary production of pig iron in a blast furnace, which, in turn, includes the production of coke and sinter (Aleksashin, Schnaltzger, and Hollias Citation2007). Each of these processes is a potentially hazardous source of harmful substances. The production of coke, which is the basis for pig iron production, leads to emissions of toxic heavy metals (Mu et al. Citation2012). Studies of blood samples from people living near a coke chemical plant show that the cancer risk for children exceeds the safe level by 30–200 times, indicating significantly increased concentrations of heavy metals in the air, soil, and water (Cao et al. Citation2014). Research analysing the soil near a coke chemical plant in Beijing found an increased concentration of PAHs (polycyclic aromatic hydrocarbons) and heavy metals such as lead and chromium (Zhao et al. Citation2021). In addition to this, research near a coke chemical plant demonstrated a high level of trichloroethylene, the increased content of which accounts for approximately 66–93% of the cancer risk in people (Chiang et al. Citation2010). Therefore, the production of coke, which is one of the leading materials necessary for steel production by BF-BOF, is characterised by an increased risk of both cancer and non-cancer diseases (Dehghani et al. Citation2020). Another material necessary for steel production by BF-BOF is sinter. Agglomeration plants are potential sources of emissions of Cd and Pb, which are highly toxic and dangerous metals (Sammut et al. Citation2010). One of the potential dangers is agglomeration gas, which is a source of substances hazardous to human health (Hartig, Stedem, and Lin Citation2006). The study of air samples at agglomeration plants indicates an elevated level of volatile organic compounds (VOCs), thereby increasing the risk of respiratory system diseases (Chiang et al. Citation2010). The operation of a blast furnace is also characterised by an increased impact of hazardous substances. People working directly with the blast furnace have a significantly higher risk of contracting not only lung cancer but also chronic bronchopneumonia, pneumonia, cardiac lung, and pulmonary tuberculosis (Z. Wang et al. Citation1996). The main pathway for the entry of non-carcinogenic and carcinogenic elements into the human body is oral (Timofeev, Kosheleva, and Kasimov Citation2019). Studies of vegetables and fruits grown near a metallurgical plant in Romania showed that the levels of Zn, Cu, Pb, and Cd significantly exceed the norm (Roba et al. Citation2016). A by-product of steel production in the blast furnace is slag, which is also characterised by the presence of substances toxic to the human body (Proctor et al. Citation2000). This product is considered environmentally hazardous due to the elevated content of heavy metals, especially mercury (Földi, Dohrmann, and Mansfeldt Citation2014). Also, during the granulation of slag, gaseous emissions of sulphur, H2S, and SO2 are formed, which are harmful pollutants for the environment and humans (Rehmus, Manka, and Upton Citation1973). Another potential source of hazardous substances characteristic of the mentioned process is blast furnace dust, which contains many recycled components such as iron, lead, zinc, and carbon (Hu et al. Citation2018). Such dust is one of the primary sources of heavy metal formation in areas adjacent to metallurgical plants (Dai et al. Citation2015). Research (Khaparde et al. Citation2016) confirms that blast furnaces are a source of uncontrolled PM10 emissions and associated polycyclic aromatic hydrocarbons. In addition, a significant amount of water is required for blast furnace operation, which, after use, contains toxic substances (Das et al. Citation2018). In summary, it can be concluded that blast furnaces are one of the most complex stages in the life cycle of BF-BOF, and the consequences of this production are hazardous to human health.
From an ecological standpoint, research (Vestergaard et al. Citation1986) confirms a reduction in pollution levels after transitioning from BF-BOF to EAF, but it is unclear whether they are safer for the human body. EAF metallurgical plants can significantly contribute to both local and global emissions of PAHs, PCBs, and PBDEs (Odabasi et al. Citation2009). Exhaust gases released from electric arc furnaces (EAFs) are highly toxic and contain polychlorinated dibenzo-p-dioxins and polychlorinated dibenzofurans (PCDD/F), solid particles associated with heavy metals such as lead, zinc, and cadmium, among others (Markatos et al. Citation2020). Statistical studies show higher incidences of diabetes, cardiovascular diseases, and lung cancer-related mortality among workers at EAF-based electric steelmaking plants (Cappelletti et al. Citation2016). Scrap containing various chlorinated compounds, such as polyvinyl chloride, coatings, paints, and inks, poses a significant risk of PCDD/F formation during EAF operation (Lee et al. Citation2005). Research conducted (Chen et al. Citation2006) reports significantly higher levels of PCDD/F and PCBs in workers directly exposed to the EAF environment than those working further away from the furnace. Lower concentrations of dioxins and PCBs were observed in the melting shop near the EAF, in the foundry shop, and in the control cabin (Aries, Anderson, and Fisher Citation2008). Electric arc furnace dust (EAFD) is a hazardous industrial waste formed during the collection of solid particles in an electric arc furnace in the steel production process (Machado et al. Citation2006). It contains heavy metals such as Zn, Pb, Fe, Cd, and others, making its conventional disposal a threat to the environment and human health (Al-Harahsheh et al. Citation2019). Toxic effects may also be present in waste and slag. Today, slag is used in cement production, road construction, and other industrial sectors. However, the danger of its use lies in the presence of polluting chemical elements such as Cr, Ba, V, Mo, and others, which can be hazardous to humans and the environment (Mombelli et al. Citation2012). All the research examples presented show that steel production is a hazardous source of harmful substances. Currently, we cannot afford to abandon the use of this material completely, so our efforts should be focused on reducing this impact and choosing the safest option.
The first part of this article discusses the Life Cycle Assessment (LCA) methodology we selected for investigating steel production processes. The following presents an analysis of the life cycle of the two investigated methods of steel production. Subsequently, each of the studied processes is thoroughly examined, and aspects that contribute most to emissions are elucidated. In the final stage of the study, potential options for mitigating the adverse impact of the examined processes on both the environment and human health are discussed. The originality of this work lies in the fact that in addition to analysing the life cycle of the two main methods of steel production today, we focus specifically on the toxic impact of these processes on human health. This study reveals the key processes that have the greatest toxic impact in the 11 investigated impact categories. In addition to impact distribution, an analysis of possible options for reducing the toxic impact on the human body has been conducted. The authors also believe it is necessary for individuals to strive to protect their bodies from hazardous elements generated by industry. It is important to note that the issue of pollution in the vicinity of metallurgical plants is global, exacerbated by export systems. The particular attention to human health safety distinguishes this work from studies such as (Burchart-Korol Citation2013) or (Yellishetty et al. Citation2011), where the main focus is on the life cycle of the steel production process. The value of this work lies in its comprehensive information set. This article emphasises the importance of developing a circular economy, encourages the protection of our bodies, and promotes environmentally safe industrial development.
2. Methodology
In this work we explore the steel production process using the Life Cycle Assessment (LCA) methodology. Life Cycle Assessment (LCA) is an internationally standardised method for assessing and comparing the environmental impact of chemical emissions and resource consumption throughout the life cycles of products or services (Paulu et al. Citation2021). This methodology is convenient for analysing and evaluating various stages of the metal production life cycle and comparing their environmental impacts (Norgate, Jahanshahi, and Rankin Citation2007). The development of LCA research consists of four main parts: defining the purpose and scope, inventory analysis, impact assessment, and interpretation.
2.1. Define the goal and scope
This LCA study aimed to investigate the two most prevalent methods of steel production today: BF-BOF and EAF, identifying key aspects of their impact on the human body. The functional unit is 1 kilogram of low-alloy steel. The study focused on the low-alloy steel type, as this type of steel possesses characteristics that make it applicable in virtually every sphere of industry and economy (Williams and Nanstad Citation2019). Various spheres of our life require high-quality steel with corresponding characteristics, and these conditions can be met precisely through the use of alloying elements (Sha Citation2013). The system boundaries chosen for the study encompass the ‘cradle-to-gate’ perspective. These boundaries encompass the preparation of necessary materials at the metallurgical plant and extend to the finished material ready for further transportation or casting. The preparation and sorting of scrap are also included within the scope of the study. It is primarily generated in gold-silver mine operation and beneficiation or during waste treatment processes. The investigated system boundaries encompass all necessary raw materials, required additives, and fluxes. Additionally, the investigated boundaries include the energy required for the process and technical materials such as refractories, cooling water, or lubricants. Waste generated during this process is also considered. In accordance with the chosen methodology, all factors directly or indirectly related to this process have been taken into account.
2.2. Inventory analysis
Data inventory was obtained by averaging data from the EcoInvent database, the metallurgical plant (Burchart-Korol Citation2013), and the BAT/BREF documentation for steel production, including information from (Remus et al. Citation2013; Yellishetty et al. Citation2011). The process involved taking the relevant data points from each source and computing the arithmetic mean, providing a comprehensive and representative average for the given data inventory. Thus, the research results are representative of metallurgical plants in Europe. The conducted LCA analysis included all raw materials, fuel and additives, as well as the energy required to perform processes within the system.
Based on the information provided above, an analysis of reserves was carried out, and a model of the investigated processes in the LCA for experts software was developed. A schematic representation of the steel production process in BF-BOF and EAF is depicted in and , respectively. The main processes included in the steel production scheme are contained in the LCA for Experts and ecoinvent databases. The process scheme of steel production in an electric arc furnace can be seen in . Each rectangle represents a corresponding process, and the arrows between them represent flows.
Figure 2. Process scheme for the production of low-alloy steel in an oxygen converter, created in the software LCA for experts.
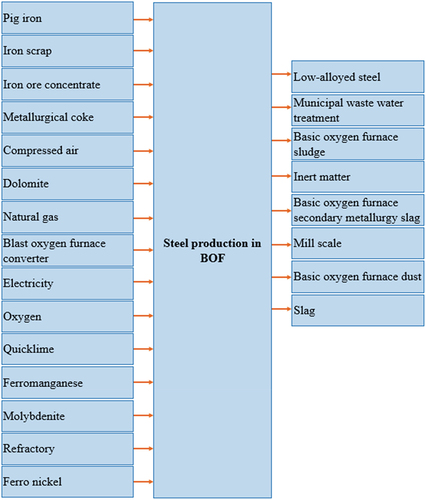
Figure 3. Process scheme for the production of low-alloy steel in an electric arc furnace, created in the software LCA for experts.
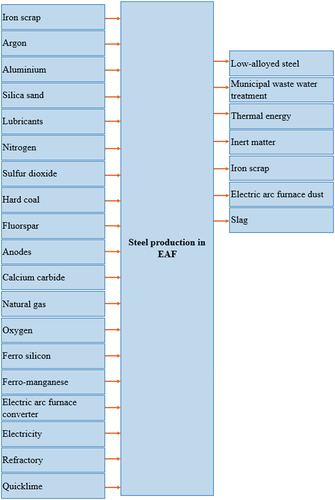
Similarly, the process diagram of steel production in an electric arc furnace is presented in .
Using data obtained from these models, the impact on the human organism of producing 1 kg of low-alloy steel in an oxygen converter and an electric arc furnace has been calculated, taking into account their life cycle within the selected system.
2.3. Life cycle impact assessment
To calculate the results of our study, we used the LCA for Experts software. The LCA for Experts software includes characterisation factors for elementary flows present in the system, and based on the specified flow values, it calculates impacts for various impact categories. The results were calculated according to the Environmental Footprint 3.0 methodology (Wiedmann and Barrett Citation2010). The calculated result is presented in .
Table 1. Тhe impact on the human body by producing 1 kg of low-alloy steel in BOF and EAF.
The table presented presents the results of the life cycle assessment of producing 1 kg of low-alloy steel in an oxygen converter and an electric arc furnace. The results are categorised based on their environmental impact. Each of these categories represents a specific aspect of the environmental impact, but in this case, we are specifically interested in those categories that directly relate to the impact on the human organism. Therefore, the subsequent analysis in this study focuses on evaluating the toxic impact on human health.
depicts the results of a comparative analysis of the impact of the investigated processes in categories directly related to the human body.
Figure 4. Comparison of the impact of the investigated processes on the human body.
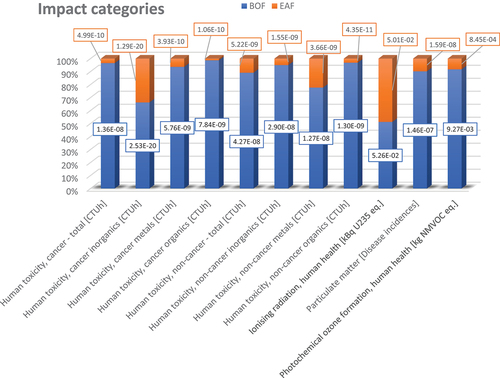
The results of the conducted comparative analysis indicate that steel production in an oxygen converter has a more significant impact on the human organism than in an electric arc furnace. The elevated level of impact is characteristic of each of the investigated categories. According to the results, the greatest hazard to human health is Ionising radiation, human health kBq U235 eq. This category assesses the impact on the human body associated with the release of radionuclides.
Although the process itself is not a source of radionuclides, like some other industrial processes, there are several indirect pathways through which steel production in oxygen converters can potentially impact cancer development. One of the potential sources of radionuclides affecting the increased risk of cancer is asbestos, which was once widely used in various insulation and construction materials, including at metallurgical plants. Despite its reduced use, old steelmaking facilities may still interact with this material during maintenance, repair, or demolition, which is a known risk factor for the development of mesothelioma – a rare but aggressive cancer affecting the lining of the lungs, heart, and other organs. In addition to this, the processing of raw materials, such as coal or iron ore, serves as a source of radionuclides.
As for steel production in electric arc furnaces, the most significant impact arises in the category of Ionising radiation, human health kBq U235 eq. and photochemical ozone formation. Although electric arc furnaces emit fewer greenhouse gases than other steel production methods, they produce emissions that can indirectly contribute to ozone formation. For example, electric furnaces emit nitrogen oxide (NOx) compounds during the steel melting process. Released into the atmosphere, NOx serves as a precursor to ozone formation. In the presence of sunlight, NOx reacts with volatile organic compounds (VOCs), forming ground-level ozone. Ozone is a key component of photochemical smog. This indicator is also influenced by emissions of volatile organic compounds and particulate matter, which do not directly impact ozone formation but affect the atmospheric condition and contribute to the formation of secondary pollutants. Steel production in an EAF is a large consumer of energy. Depending on the type of energy being investigated, its production process serves as a significant source of radiation emissions and hazardous substances. Particularly, in the case of electricity generation in thermal power plants where coal is used. The next task was to determine the processes that are the primary source of the aforementioned emissions.
2.4. Interpretation
A detailed analysis of each process included determining the key factors that most significantly affect each of the investigated categories. Below is presented the study of impact categories in the production of 1 kg of steel in an oxygen converter, considering the life cycle assessment. For clarity, the diagram () depicts processes whose impact constitutes more than 1%, while processes with an impact of less than 1% are grouped together and labelled as ‘Others’.
Figure 5. The distribution of the impact on the human body by the process of producing 1 kg of steel in oxygen converters is presented in each of the researched impact categories.
(a) The category of Human toxicity, cancer – total [CTUh]. The production of cast iron and additives such as ferromanganese and ferronickel plays a key role in this category.
(b) The category of Human toxicity, cancer inorganics [CTUh]. Oxygen and additives such as ferronickel play a key role in this category.
(c) The category of Human toxicity, cancer metals [CTUh]. Alloying additives such as ferromanganese and ferronickel play a key role in this category.
(d) The category of Human toxicity, cancer organics [CTUh]. All negative impact in this category is attributed to the process of cast iron production.
(e) The category of Human toxicity, non-cancer – total [CTUh]. The majority of harmful impact in this category is caused by cast iron production, but in addition, ferronickel and refractories exert a noticeable influence.
(f) The category of Human toxicity, non-cancer inorganics [CTUh]. The main portion of hazardous emissions is caused by the process of cast iron production.
(g) The category of Human toxicity, non-cancer metals [CTUh]. Half of the hazardous impact in this category is caused by the steel production process, while the other portion is attributed to refractories and alloying additives.
(h) The category of Human toxicity, non-cancer organics [CTUh]. The majority of the harmful impact in this category is caused by molybdenite, while another portion is attributed to cast iron production.
(i) The category of Ionizing radiation, human health [kBq U235 eq.]. Half of the harmful impact in this category is caused by the process of cast iron production. Additionally, noticeable influence here is attributed to oxygen and alloying additives.
(j) Category Particulate matter [Disease incidences]. In this category, more than half of the hazardous impact is caused by the cast iron production process.
(k) Category Photochemical ozone formation, human health [kg NMVOC eq.]. In this category, the main portion of the hazardous impact is caused by the cast iron production process. Additionally, alloying additives have a noticeable influence on this category.
![Figure 5. The distribution of the impact on the human body by the process of producing 1 kg of steel in oxygen converters is presented in each of the researched impact categories.(a) The category of Human toxicity, cancer – total [CTUh]. The production of cast iron and additives such as ferromanganese and ferronickel plays a key role in this category.(b) The category of Human toxicity, cancer inorganics [CTUh]. Oxygen and additives such as ferronickel play a key role in this category.(c) The category of Human toxicity, cancer metals [CTUh]. Alloying additives such as ferromanganese and ferronickel play a key role in this category.(d) The category of Human toxicity, cancer organics [CTUh]. All negative impact in this category is attributed to the process of cast iron production.(e) The category of Human toxicity, non-cancer – total [CTUh]. The majority of harmful impact in this category is caused by cast iron production, but in addition, ferronickel and refractories exert a noticeable influence.(f) The category of Human toxicity, non-cancer inorganics [CTUh]. The main portion of hazardous emissions is caused by the process of cast iron production.(g) The category of Human toxicity, non-cancer metals [CTUh]. Half of the hazardous impact in this category is caused by the steel production process, while the other portion is attributed to refractories and alloying additives.(h) The category of Human toxicity, non-cancer organics [CTUh]. The majority of the harmful impact in this category is caused by molybdenite, while another portion is attributed to cast iron production.(i) The category of Ionizing radiation, human health [kBq U235 eq.]. Half of the harmful impact in this category is caused by the process of cast iron production. Additionally, noticeable influence here is attributed to oxygen and alloying additives.(j) Category Particulate matter [Disease incidences]. In this category, more than half of the hazardous impact is caused by the cast iron production process.(k) Category Photochemical ozone formation, human health [kg NMVOC eq.]. In this category, the main portion of the hazardous impact is caused by the cast iron production process. Additionally, alloying additives have a noticeable influence on this category.](/cms/asset/d36deb0d-4efe-4c5f-8832-c198f0105d73/tsue_a_2349873_f0005a_oc.jpg)
According to the conducted analysis, the most hazardous process for the human body in the steel production process in an oxygen converter is pig iron production in blast furnaces. Pig iron is the primary material in the steel production process using this method. The production of pig iron in blast furnaces involves the smelting of iron ore to obtain iron, with the process typically including the use of coke as fuel. One of the most dangerous substances emitted is carbon monoxide (CO). CO is formed during the combustion of carbonaceous materials, such as coke. Inhalation of carbon monoxide is highly dangerous, as it hinders the transportation of oxygen in the body, leading to symptoms such as headaches, dizziness, and, in severe cases, fatal outcomes. Emissions of heavy metals are particularly hazardous. Heavy metals can enter steel production from various sources, primarily from the raw materials used in the steelmaking process. Metals such as lead, cadmium, chromium, and nickel can be released at different stages of pig iron production. For example, iron ore, a fundamental raw material for pig iron production, may contain traces of heavy metals such as lead, cadmium, and nickel, which can be released into the atmosphere during processing. Another source of heavy metal emissions present in coal is the burning of coke. The most common heavy metals, in this case, are lead and mercury. In addition, the investigated process is characterised by the formation of polycyclic aromatic hydrocarbons (PAHs). Some PAHs are known carcinogens, and prolonged exposure increases the risk of developing cancer, especially lung cancer. The main source of PAHs in the steel production process is typically the use of carbonaceous materials, such as coal and coke, as fuels and reductants. Furthermore, pig iron production is associated with the emission of hazardous substances such as sulphur dioxide (SO2) and nitrogen oxides (NOx). These substances affect the human body directly and contribute to smog formation, which, in turn, adversely affects human health. Substances such as ferromanganese and ferronickel are the second-highest contributors to the impact of the investigated process on the human body. Manganese acts as a deoxidiser, aiding in removing oxygen and other impurities from steel. Nickel is a crucial alloying element that enhances the properties of steel, increasing its strength, viscosity, and corrosion resistance. Chronic exposure to high levels of manganese leads to neurological consequences, including manganism, a condition resembling Parkinson’s disease. Inhalation of nickel can cause respiratory tract irritation and elevate the risk of lung cancer. The significant impact on the human body during steel production is attributed to the use of refractory materials. Refractories play a vital role in the steel production process, lining furnaces and other high-temperature vessels, providing insulation, and protecting against excessive heating. Although refractories themselves are generally not considered highly toxic, their use in the metallurgical industry may involve the influence of specific materials and substances that pose a health risk. For instance, a common component of many refractories is silica (silicon dioxide). Prolonged inhalation of crystalline silica dust, generated during the transportation, installation, maintenance, or removal of refractories, can lead to silicosis – a serious and irreversible lung disease. Silica is also a known carcinogen. Refractories may contain various materials such as alumina, magnesia, chromite, zirconium, and other metal oxides, which, when inhaled over an extended period, pose a danger to the human body. The analysis conducted indicates that the most significant impact on the human body during steel production in an oxygen converter is associated with pig iron, alloying additives, and refractory materials necessary for the implementation of this process.
The results of the analysis of steel production in an electric arc furnace are presented in .
Figure 6. The distribution of the impact on the human body by the process of producing 1 kg of steel in an electric arc furnace is presented in each of the impact categories.
(a) The category of Human toxicity, cancer - total [CTUh]. The highest impact in this category is caused by dust from electric arc furnaces.
(b) The category of Human toxicity, cancer inorganics [CTUh]. Most of the hazardous effects are due to oxygen.
(c) The category of Human toxicity, cancer metals [CTUh]. In this category, the main exposure is to electric arc dust.
(d) The category of Human toxicity, cancer organics [CTUh]. In this category, the hazardous impact is caused by quicklime and the electricity required for this process.
(e) The category of Human toxicity, non-cancer - total [CTUh]. In this category, electricity and arc dust have a significant impact.
(f) The category of Human toxicity, non-cancer inorganics [CTUh]. More than half of the hazardous impacts are caused by the electricity used.
(g) The category of Human toxicity, non-cancer metals [CTUh]. In this category, the hazardous effects are attributed to arc furnace dust, electrical energy, and refractories.
(h) The category of Human toxicity, non-cancer organics [CTUh]. The largest impact in this category is from the electricity used to run the process.
(i) The category of Ionizing radiation, human health [kBq U235 eq.]. The main impact in this category is caused by electricity.
(j) Category Particulate matter [Disease incidences]. This category is mainly influenced by electricity and alloying additives.
(k) Category Photochemical ozone formation, human health [kg NMVOC eq.]. In this category, the hazardous impact is caused by the electricity used and ferromanganese.
![Figure 6. The distribution of the impact on the human body by the process of producing 1 kg of steel in an electric arc furnace is presented in each of the impact categories.(a) The category of Human toxicity, cancer - total [CTUh]. The highest impact in this category is caused by dust from electric arc furnaces.(b) The category of Human toxicity, cancer inorganics [CTUh]. Most of the hazardous effects are due to oxygen.(c) The category of Human toxicity, cancer metals [CTUh]. In this category, the main exposure is to electric arc dust.(d) The category of Human toxicity, cancer organics [CTUh]. In this category, the hazardous impact is caused by quicklime and the electricity required for this process.(e) The category of Human toxicity, non-cancer - total [CTUh]. In this category, electricity and arc dust have a significant impact.(f) The category of Human toxicity, non-cancer inorganics [CTUh]. More than half of the hazardous impacts are caused by the electricity used.(g) The category of Human toxicity, non-cancer metals [CTUh]. In this category, the hazardous effects are attributed to arc furnace dust, electrical energy, and refractories.(h) The category of Human toxicity, non-cancer organics [CTUh]. The largest impact in this category is from the electricity used to run the process.(i) The category of Ionizing radiation, human health [kBq U235 eq.]. The main impact in this category is caused by electricity.(j) Category Particulate matter [Disease incidences]. This category is mainly influenced by electricity and alloying additives.(k) Category Photochemical ozone formation, human health [kg NMVOC eq.]. In this category, the hazardous impact is caused by the electricity used and ferromanganese.](/cms/asset/0fd8b20d-cfb1-4c02-9abf-7fc700a1a6ee/tsue_a_2349873_f0006a_oc.jpg)
In this case, the results are less straightforward; however, it is evident that the most significant impact on the human organism from the steel production process in the electric arc furnace (EAF) is attributed to the emission of dust characteristic of this process and the required electrical energy for its implementation. Similar to the process discussed above, additives and necessary refractories significantly influence this process. The dust emitted from the electric arc furnace (EAF) during steel production can pose various health and safety risks to the human organism. The danger level depends on the dust composition, which can vary based on the materials used in the steel production process. The most prevalent components encompass metal oxides, solid particles, and potentially hazardous trace elements. EAF dust may contain heavy metals such as chromium, nickel, cadmium, and lead. Some of these metals are known or suspected carcinogens. For instance, hexavalent chromium (Cr(VI)), a form of chromium often encountered in industrial processes, is a well-known human carcinogen when inhaled.
The production of electrical energy required for melting scrap in an electric arc furnace has a significant impact on the human organism compared to other included processes. Such energy production involves the combustion of fossil fuels, emitting various pollutants into the air, including heavy metals, sulphur dioxide (SO2), nitrogen oxides (NOx), and carbon monoxide. Heavy metals present in fossil fuels are released during combustion. When coal is burned for energy production, mercury is released into the air. Suspended in the air, mercury can travel long distances and ultimately settle in bodies of water. Mercury transforms into methylmercury in aquatic environments, a highly toxic form that accumulates in fish. Consuming contaminated fish can lead to severe health problems, particularly affecting the nervous system. Another heavy metal, lead, present in small amounts in coal, oil, and natural gas, can be released into the air as fine particles during combustion. Energy production is accompanied by significant emissions of carbon monoxide, volatile organic compounds, sulphur dioxide (SO2), and nitrogen oxides (NOx). Furthermore, electricity serves as a source of ionising radiation. Prolonged exposure to low doses of ionising radiation can increase the risk of cancer, especially in radiation-sensitive organs such as the thyroid gland, lungs, and bone marrow (Brenner et al. Citation2003). Considering that the electrical energy required for the investigated process is one of the main factors of hazardous impact, nine scenarios of steel production in an arc furnace using various types of electrical energy have been developed. For the investigation, we compared the following types of electrical energy: nuclear, wind, solar, hydro, natural gas, hard coal, waste, biogas, and the electricity grid mix used in the study. The electricity grid mix used for the investigation is taken from the Sphere database and is relevant for the year 2023. Other types of electrical energy were also sourced from the Sphere database, and the calculation is relevant for the year 2023. As for the geographical scope, the processes selected for investigation are characteristic of the European electricity market. The results of the comparison are presented in .
Figure 7. Impact on the human organism of the steel production process in an electric arc furnace using various types of electrical energy.
(a) The category of Human toxicity, cancer – total [CTUh]. In this category, the scenario involving the use of electrical energy generated from wind power will have the highest negative impact, while the safest option will be the use of electrical energy from nuclear power.
(b) The category of Human toxicity, cancer inorganics [CTUh]. In order to minimize the hazardous impact in this category, it is necessary to use electrical energy from hydroelectric power.
(c) The category of Human toxicity, cancer metals [CTUh]. In this case, the use of electrical energy generated from natural gas will have the highest hazardous impact.
(d) The category of Human toxicity, cancer organics [CTUh]. The lowest level of toxic organic substances causing cancer that we can achieve for the investigated process is by using electrical energy from nuclear power. The most hazardous option in this case is the use of electrical energy from biogas.
(e) The category of Human toxicity, non-cancer – total [CTUh]. In this category, the most hazardous is the use of electrical energy obtained from natural gas.
(f) The category of Human toxicity, non-cancer inorganics [CTUh]. In this case, the highest level of danger is associated with the use of electrical energy generated from biogas. The safest option is hydroelectric power usage.
(g) The category of Human toxicity, non-cancer metals [CTUh]. The highest level of danger is posed by the use of electrical energy generated from natural gas.
(h) The category of Human toxicity, non-cancer organics [CTUh]. In this category, the safest option is the use of electrical energy from hydroelectric power.
(i) The category of Ionizing radiation, human health [kBq U235 eq.]. The use of electrical energy from nuclear power provokes the highest level of ionizing radiation emissions.
(j) Category Particulate matter [Disease incidences]. The use of electrical energy from biogas will have the highest emissions level in this category for the investigated process.
(k) Category Photochemical ozone formation, human health [kg NMVOC eq.]. For the investigated process in this category, the use of electrical energy from biogas yields the highest hazardous outcome.
![Figure 7. Impact on the human organism of the steel production process in an electric arc furnace using various types of electrical energy.(a) The category of Human toxicity, cancer – total [CTUh]. In this category, the scenario involving the use of electrical energy generated from wind power will have the highest negative impact, while the safest option will be the use of electrical energy from nuclear power.(b) The category of Human toxicity, cancer inorganics [CTUh]. In order to minimize the hazardous impact in this category, it is necessary to use electrical energy from hydroelectric power.(c) The category of Human toxicity, cancer metals [CTUh]. In this case, the use of electrical energy generated from natural gas will have the highest hazardous impact.(d) The category of Human toxicity, cancer organics [CTUh]. The lowest level of toxic organic substances causing cancer that we can achieve for the investigated process is by using electrical energy from nuclear power. The most hazardous option in this case is the use of electrical energy from biogas.(e) The category of Human toxicity, non-cancer – total [CTUh]. In this category, the most hazardous is the use of electrical energy obtained from natural gas.(f) The category of Human toxicity, non-cancer inorganics [CTUh]. In this case, the highest level of danger is associated with the use of electrical energy generated from biogas. The safest option is hydroelectric power usage.(g) The category of Human toxicity, non-cancer metals [CTUh]. The highest level of danger is posed by the use of electrical energy generated from natural gas.(h) The category of Human toxicity, non-cancer organics [CTUh]. In this category, the safest option is the use of electrical energy from hydroelectric power.(i) The category of Ionizing radiation, human health [kBq U235 eq.]. The use of electrical energy from nuclear power provokes the highest level of ionizing radiation emissions.(j) Category Particulate matter [Disease incidences]. The use of electrical energy from biogas will have the highest emissions level in this category for the investigated process.(k) Category Photochemical ozone formation, human health [kg NMVOC eq.]. For the investigated process in this category, the use of electrical energy from biogas yields the highest hazardous outcome.](/cms/asset/7f2206a1-dfff-41ce-995e-46a592e4b4f5/tsue_a_2349873_f0007a_oc.jpg)
The results of the conducted comparative analysis indicate that the safest option for the human organism in steel production in electric arc furnaces would be the utilisation of hydroelectric energy. The highest level of impact in the investigated categories was associated with the use of electrical energy from biogas and natural gas. To achieve the goal of reducing the hazardous impact of the steel production process on the human organism, a prudent approach would be to transition to steel production in electric arc furnaces using hydroelectric energy. It is important to note that various types of uncertainty, such as parameter, scenario, and model uncertainties, influence the results of LCA. Thus, further research into the methodological aspects of data quality analysis for LCI and LCA studies is necessary to ensure reliable and credible data processed within the framework of this LCA study.
3. Discussion
In this situation, it is also important to note that the technological models of the investigated processes are quite complex, and therefore it is necessary to consider their tendency towards a high level of uncertainty. The use of LCA as a decision support tool can, however, be hampered by the numerous uncertainties embedded in the calculation, as well as the fact that the results cannot be verified, validated, or confirmed due to many constraints (technical, conceptual, legal, etc.) (Oreskes, Shrader-Frechette, and Belitz Citation1994). Uncertainty analysis helps identify potential scenarios and the range of results that may arise due to uncertainties in the variables involved in the process. For this study, uncertainty analysis is presented in .
Table 2. Uncertainty analysis of investigated processes.
Understanding it enables the determination of the most influential factors affecting the obtained results, assessing the reliability of research conclusions, and is crucial in setting further priorities. provides a description of the main sensitive variables.
Table 3. Sensitivity Analysis of Variables for the studied steel production processes.
Based on the results of the research, to mitigate the hazardous impact on the human organism from the steel production process, a prudent solution would be to transition to steel production in electric arc furnaces. However, according to statistics, less than a third of the world’s steel is produced in the EAF (“Fact sheet Steel and raw materials” Citation2023). A 100% transition to electric steel production at present is confronted with a series of challenges, the resolution of which requires a considerable timeframe. Therefore, a current priority is addressing the issue of the toxic impact on the human organism from steel production, both in electric arc furnaces and oxygen converters.
Regarding steel production in oxygen converters, to reduce the impact on the human organism, it is advisable to explore options for diminishing the hazardous effects of pig iron production in blast furnaces since this process is particularly influential in this context. There are two approaches need consideration to prevent potential harmful effects. The first involves reducing the use of fossil fuels for pig iron production and associated processes and exploring potential alternative options. The second entails improving the capture of hazardous substances and preventing their release into the environment. One possible improvement method is directly reducing iron ore by hydrogen, where iron ore is directly reduced using hydrogen as a reducing agent. This process employs gaseous hydrogen to reduce iron ore (usually iron oxide) to metallic iron without an intermediate melting stage. This process generates water vapour as a byproduct instead of carbon dioxide, reducing the harmful impact on the human organism. However, the cost and availability of hydrogen pose challenges, limiting widespread implementation on an industrial scale. Another potential option is biomass gasification, where synthesis gas obtained from wood or agricultural residues serves as a reducing agent. While biomass gasification holds promise for iron ore reduction and hydrogen production, challenges and considerations arise, such as the source and quality of biomass feedstock. Ensuring a constant and reliable supply of biomass materials requires careful planning to avoid negative impacts on ecosystems and food production. Additionally, drawbacks include the formation of resin and other condensed organic compounds, along with energy and economic efficiency concerns. Another potential but less-explored method is the electrolysis of molten oxide, involving the electrolysis of iron ore in a bath of molten oxide to obtain iron with minimal carbon emissions. Challenges with this technology include high energy consumption due to the need to maintain high operating temperatures and the quality requirements of the raw materials.
Concerning the second approach to reduce the hazardous impact of pig iron production on the human organism, effective gas cleaning systems for capturing and removing pollutants, including heavy metals and solid particles, from the exhaust gases produced during steel production should be considered. Advanced technologies such as electrostatic precipitators and bag filters can be utilised for this purpose. Bag filters significantly reduce emissions of solid particles, including heavy metals, into the atmosphere during pig iron production. Equally important in this scenario is efficient water purification systems to minimise emissions of pollutants into water bodies and prevent contamination. Additionally, the beneficial effect of addressing this issue will be the utilisation of by-products generated during steel production, such as slag and dust, for constructive purposes like building materials or as raw materials for other industries. Although it is crucial to prioritise the implementation of comprehensive strategies, eliminating all risks can be a challenging task. It is difficult to determine which of the mentioned methods will yield the best results in reducing the toxic impact on the human organism. However, each technology, in one way or another, involves a reduction in emissions of substances hazardous to humans, thereby diminishing the impact on the human organism. In any industrial process, it is crucial to assess the overall environmental impact, including potential emissions from the process.
When considering reducing the impact on the human organism caused by steel production in electric arc furnaces, efforts can be directed in three main directions. The first and most impactful, as demonstrated earlier, is to utilise an alternative form of electrical energy, namely hydroelectric power. According to the results of our comparison, this type of electrical energy is the safest for the human organism in the process of steel production in electric arc furnaces. The question of the availability of hydroelectric power for European metallurgical plants remains open, and whether it is sufficient to fully meet the production capacity needs.
Secondly, improving the quality of scrap, the primary raw material for this process, is another viable option. Scrap is the source of the majority of emissions of heavy metals and volatile organic compounds released during the operation of the electric arc furnace. This is because scrap may contain various chlorinated compounds, such as polyvinyl chloride, coatings, paints, and inks. These residues and compounds adversely affect both the quality of steel and the human organism. Various technologies are currently being considered to enhance the quality of scrap sorting. Conventional mechanical sorting is insufficient in this situation. Technologies capable of identifying the presence of contaminants in scrap are required. Near-infrared (NIR) technology effectively identifies, and sorts of materials based on their molecular composition. This method can distinguish various types of plastics, paper, and metals, including contaminants such as varnishes and paints. Although this technology is environmentally friendly compared to others, it has limitations related to penetration depth and sensitivity to surface characteristics. An alternative perspective involves foam flotation technology, utilising differences in the chemical composition of surfaces to separate materials based on their hydrophobic or hydrophilic properties. The advantage of this technology lies in its effective separation and versatility, while the drawback is its most efficient application for materials showing significant differences in buoyancy. It may be less effective for sorting materials with similar buoyancy characteristics. Magnetic resonance tomography, known for its ability to clearly determine the type and composition of scrap, is primarily applied for sorting electronic waste. In the modern world, advanced robotic sorting systems equipped with artificial intelligence are also considered promising. They can be trained to recognise and remove specific contaminants. This technology is universal and adaptable to various types of harmful substances. Its benefits include high efficiency and precision, but it comes with a high initial cost.
The third option to reduce the harmful impact on the human organism, in this case, is to improve the purification and capture systems for harmful gases. One of the most common methods is the use of bag filters and gas scrubbers. Large fabric filters capture solid particles from the exhaust gases generated during steel production. Gases pass through fabric bags, and particles collect on the surface. Gas scrubbers, also known as wet scrubbers, are widely used for removing harmful gases from exhaust gases. In this process, exhaust gases pass through a liquid (usually water or a chemical solution) that absorbs and neutralises pollutants. Bag filters effectively remove solid particles, while gas scrubbers efficiently capture gases such as sulphur dioxide and other pollutants. The application of such technologies is justified from the perspective of reducing the environmental impact of steel production. These systems are aimed at minimising emissions of harmful substances into the atmosphere, contributing to improved air quality and reduced health risks for neighbouring communities. This may be significant for the future development of environmental declarations and the calculation of environmental externalities. The steel industry in general is often associated with the privatisation of profits and the socialisation of environmental and health burdens.
Attention should also be given to refractory materials used in these processes. Research results indicate that these materials are a source of substances hazardous to the human organism, including carcinogens. Today, various types of refractory materials are available. Magnesia or dolomite-based refractories are considered fundamental and basic. In environments with acidic conditions, silica is used. For zones with high temperatures and aggressive conditions, magnesia-chrome bricks and other materials containing chrome are utilised. Dust and solid particles emissions during the installation, repair, or dismantling of refractory lining are quite hazardous to the human organism. Therefore, alternative materials that do not contain hazardous substances should be considered. Refractory ceramic fibres made from aluminium oxide and silicon dioxide are considered an alternative. They may be less toxic than some traditional fibres. Some new alloys and ceramic materials may have improved properties and a lesser impact on health compared to traditional refractory materials. Additionally, research is underway on refractory materials made from recycled or renewable sources, which can help reduce environmental impact and dependence on unstable resources. Regarding the individuals directly working in metallurgical plants, it is essential to emphasise the significant role of work organisation and adherence to safety rules in protecting their health. Special attention should be given to personal protective equipment. Employees in metallurgical plants should wear helmets, gloves, protective eyewear, and boots with steel toes to safeguard themselves from potential hazards such as falling objects, extreme temperatures, and exposure to chemicals. Another crucial aspect is training and education for employees. Workers need to undergo training on the safe use of equipment, handling of materials, and actions in emergency situations. This education helps employees understand potential risks and how to mitigate them. Continuous monitoring and health surveillance are also important. Regular health monitoring and surveillance programmes aid in the early detection and resolution of potential health issues. This enhances safety levels and compliance with environmental norms and standards.
It is important to consider the situation from another perspective as well. People should also strive to protect themselves from potential toxicological influence (Vandenberg et al. Citation2023). To protect the body from the toxic impact of industry, it is important to prioritise personal hygiene and environmental awareness. This involves proper nutrition, regular physical activity to improve circulation and toxin elimination. Additionally, it includes promoting stricter environmental standards and supporting sustainable practices that contribute to overall community health and safety. It is also important to understand that the danger of exposure to toxic substances in the human body is a global issue rather than a local one. This is because hazardous substances, such as heavy metals, for example, can enter the bodies of people who do not live near metallurgical plants through the food importation system (Emami et al. Citation2023).
4. Conclusion
In addition to efforts to reduce the carbon footprint of steel production, it is crucial to consider the impact on human health, which is also significantly influenced by this process. The most effective approach in this case is Life Cycle Assessment (LCA) methodology, as it accounts for the impact on the human body not only of the investigated process but also of processes directly related to production. According to the results of the study of two most common methods of steel production today, the EAF route is considered safer for the human body. This is observed in each of the investigated impact categories. Due to the impossibility of fully transitioning to the electric arc method of steel production, it is important to research ways to reduce toxic impact in both aforementioned production methods. Regarding steel production via the BOF route, the primary source of hazardous toxic substances is the iron production process in the blast furnace. In the case of electric arc steel production, the highest hazardous impact is attributed to the electrical energy required for the process. The best way to reduce the hazardous impact of steel production in the EAF on the human body is to use the necessary electrical energy from hydroelectric power for the process.
Аuthor contributions
Ivanna Harasymchuk was responsible for the concept, design and writing of the article. Data interpretation was made by Ivanna Harasymchuk and Vladimír Kočí. Critical revision for intellectual content was made by Tatiana Trecáková. The submitted version of the manuscript was reviewed and approved by all authors. Final approval was made by Vladimír Kočí. All authors agree to be responsible for all aspects of the work, ensuring that they have properly researched and resolved issues related to the accuracy or integrity of any part of the work.
Acknowledgments
This research was made possible within the study of a doctoral programme at the Department of Sustainability and Product Ecology, VSСHT, Prague and the support of the Czech Technical Agency.
Disclosure statement
No potential conflict of interest was reported by the author(s).
Data availability statement
The data that support the findings of this study are available from the corresponding author, I. Harasymchuk, upon reasonable request.
Additional information
Funding
Notes on contributors
Ivanna Harasymchuk
Ivanna Harasymchuk student. Researching the optimisation of BAT for the steel industry with an attention to life cycle assessment. In addition, working on the issue of steel decarbonisation with regard to its impact on the human body.
Vladimír Kočí
Vladimír Kočí focuses primarily on reducing the environmental impacts of products, technologies, and organisations in his professional work. He is generally involved in the issues of product ecology and sustainability. The basic tool of his work is the Life Cycle Assessment (LCA) method.
Tatiana Trecáková
Tatiana Trecáková work and interests focused on life cycle assessment (products and organisations), sustainability management, innovation.
References
- Aleksashin, A. L., I. Schnaltzger, and G. Hollias. 2007. “Creation and Growth of Oxygen-Converter Steelmaking.” Metallurgist 51 (1): 60–65. https://doi.org/10.1007/s11015-007-0014-4.
- Alfaro, M. R., O. M. Ugarte, L. H. V. Lima, J. R. Silva, F. B. V. da Silva, S. A. da Silva Lins, and C. W. A. Do Nascimento. 2022. “Risk Assessment of Heavy Metals in Soils and Edible Parts of Vegetables Grown on Sites Contaminated by an Abandoned Steel Plant in Havana.” Environmental Geochemistry and Health 44 (1): 43–56. https://doi.org/10.1007/s10653-021-01092-w.
- Al-Harahsheh, M., J. Al-Nu’airat, A. Al-Otoom, I. Al-Hammouri, H. Al-Jabali, M. Al-Zoubi, and S. Abu Al’asal. 2019. “Treatments of Electric Arc Furnace Dust and Halogenated Plastic Wastes: A Review.” Journal of Environmental Chemical Engineering 7 (1): 102856. https://doi.org/10.1016/j.jece.2018.102856.
- Arens, M., M. Åhman, and V. Vogl. 2021. “Which Countries Are Prepared to Green Their Coal-Based Steel Industry with Electricity? – Reviewing Climate and Energy Policy As Well As the Implementation of Renewable Electricity.” Renewable and Sustainable Energy Reviews 143:110938. https://doi.org/10.1016/j.rser.2021.110938.
- Aries, E., D. R. Anderson, and R. Fisher. 2008. “Exposure Assessment of Workers to Airborne PCDD/Fs, PCBs and PAHs at an Electric Arc Furnace Steelmaking Plant in the UK.” The Annals of Occupational Hygiene 52 (4): 213–225. https://doi.org/10.1093/annhyg/men011.
- Bowman, B., and K. Krüger. 2009. Arc Furnace Physics. Düsseldorf: Verlag Stahleisen https://books.google.cz/books?id=EshLygAACAAJ.
- Brenner, D. J., R. Doll, D. T. Goodhead, E. J. Hall, C. E. Land, J. B. Little, J. H. Lubin, et al. 2003. “Cancer Risks Attributable to Low Doses of Ionizing Radiation: Assessing What We Really Know.” Proceedings of the National Academy of Sciences 100 (24): 13761–13766. https://doi.org/10.1073/pnas.2235592100.
- Breugelmans, O., C. Ameling, M. Marra, P. Fischer, J. van de Kassteele, J. Lijzen, A. Oosterlee, et al. 2013. “Lung Cancer Risk and Past Exposure to Emissions from a Large Steel Plant.” Journal of Environment and Public Health 2013:684035. https://doi.org/10.1155/2013/684035.
- Burchart-Korol, D. 2013. “Life Cycle Assessment of Steel Production in Poland: A Case Study.” Journal of Cleaner Production 54:235–243. https://doi.org/10.1016/j.jclepro.2013.04.031.
- Cao, S., X. Duan, X. Zhao, J. Ma, T. Dong, N. Huang, C. Sun, B. He, and F. Wei. 2014. “Health Risks from the Exposure of Children to As, Se, Pb and Other Heavy Metals Near the Largest Coking Plant in China.” Science of the Total Environment 472:1001–1009. https://doi.org/10.1016/j.scitotenv.2013.11.124.
- Cappelletti, R., M. Ceppi, J. Claudatus, and V. Gennaro. 2016. “Health Status of Male Steel Workers at an Electric Arc Furnace (EAF) in Trentino, Italy.” Journal of Occupational Medicine and Toxicology 11:1. https://doi.org/10.1186/s12995-016-0095-8.
- Chen, H.-L., T.-S. Shih, P.-C. Huang, C.-Y. Hsieh, and C.-C. Lee. 2006. “Exposure of Arc-Furnace-Plant Workers to Polychlorinated Dibenzo-P-Dioxins and Dibenzofurans (PCDD/Fs.” Chemosphere 64 (4): 666–671. https://doi.org/10.1016/j.chemosphere.2005.10.059.
- Chiang, H. L., W. H. Lin, J. S. Lai, and W. C. Wang. 2010. “Inhalation Risk Assessment of Exposure to the Selected Volatile Organic Compounds (VOCs) Emitted from the Facilities of a Steel Plant.” Journal of Environmental Science & Health: Part A, Toxic/Hazardous Substances & Environmental Engineering 45 (11): 1397–1405. https://doi.org/10.1080/10934529.2010.500932.
- Cullen, J. M., J. M. Allwood, and M. D. Bambach. 2012. “Mapping the Global Flow of Steel: From Steelmaking to End-Use Goods.” Environmental Science & Technology 46 (24): 13048–13055. https://doi.org/10.1021/es302433p.
- Dai, Q.-L., X.-H. Bi, J.-H. Wu, Y.-F. Zhang, J. Wang, H. Xu, L. Yao, L. Jiao, and Y.-C. Feng. 2015. “Characterization and Source Identification of Heavy Metals in Ambient PM10 and PM2.5 in an Integrated Iron and Steel Industry Zone Compared with a Background Site.” Aerosol & Air Quality Research 15 (3): 875–887. https://doi.org/10.4209/aaqr.2014.09.0226.
- Das, P., G. C. Mondal, S. Singh, A. K. Singh, B. Prasad, and K. K. Singh. 2018. “Effluent Treatment Technologies in the Iron and Steel Industry – A State of the Art Review.” Water Environment Research 90 (5): 395–408. https://doi.org/10.2175/106143017X15131012152951.
- Dehghani, F., F. Omidi, R. A. Fallahzadeh, and B. Pourhassan. 2021. “Health Risk Assessment of Occupational Exposure to Heavy Metals in a Steel Casting Unit of a Steelmaking Plant Using Monte-Carlo Simulation Technique.” Toxicology and Industrial Health 37 (7): 431–440. https://doi.org/10.1177/07482337211019593.
- Dehghani, F., F. Omidi, O. Heravizadeh, S. Barati Chamgordani, V. Gharibi, and A. Sotoudeh Manesh. 2020. “Occupational Health Risk Assessment of Volatile Organic Compounds Emitted from the Coke Production Unit of a Steel Plant.” International Journal of Occupational Safety and Ergonomics 26 (2): 227–232. https://doi.org/10.1080/10803548.2018.1443593.
- Dragović, R., B. Gajić, S. Dragović, M. Đorđević, M. Đorđević, N. Mihailović, and A. Onjia. 2014. “Assessment of the Impact of Geographical Factors on the Spatial Distribution of Heavy Metals in Soils Around the Steel Production Facility in Smederevo (Serbia).” Journal of Cleaner Production 84:550–562. https://doi.org/10.1016/j.jclepro.2014.03.060.
- Eggleston, H. S., L. Buendia, K. Miwa, T. Ngara, and K. Tanabe. 2006. 2006 IPCC Guidelines for National Greenhouse Gas Inventories, 2108–2111. Kamiyamaguchi, Hayama, Kanagawa (Japan): Japan: IPCC National Greenhouse Gas Inventories Programme, Intergovernmental Panel on Climate Change IPCC, Institute for Global Environmental Strategies IGES.
- Emami, H., F. S. Mohammad, S. Mohammadzadeh, A. Fahim, M. Abdolvand, S. Ali Ehsan Dehkordi, S. Mohammadzadeh, and F. Maghool. 2023. “A Review of Heavy Metals Accumulation in Red Meat and Meat Products in the Middle East.” Journal of Food Protection 86 (3): 100048. https://doi.org/10.1016/j.jfp.2023.100048.
- “Fact sheet. Steel and raw materials”. 2023. World Steel Association. https://worldsteel.org/.
- Fierens, S., H. Mairesse, J. F. Heilier, J. F. Focant, G. Eppe, E. De Pauw, and A. Bernard. 2007. “Impact of Iron and Steel Industry and Waste Incinerators on Human Exposure to Dioxins, PCBs, and Heavy Metals: Results of a Cross-Sectional Study in Belgium.” Journal of Toxicology & Environmental Health A 70 (3–4): 222–226. https://doi.org/10.1080/15287390600884628.
- Földi, C., R. Dohrmann, and T. Mansfeldt. 2014. “Mercury in Dumped Blast Furnace Sludge.” Chemosphere 99:248–253. https://doi.org/10.1016/j.chemosphere.2013.11.007.
- Hartig, W., K. H. Stedem, and R. Lin. 2006. “Sinter Plant Waste Gas Cleaning – State of the Art.” Metallurgical Research and Technology 103 (6): 257–265. https://doi.org/10.1051/metal:2006138.
- Holappa, L. 2020. “A General Vision for Reduction of Energy Consumption and CO2 Emissions from the Steel Industry.” Metals 10 (9): 1117.
- Hu, W.-T., H.-W. Xia, D.-L. Pan, X.-L. Wei, J. Li, X.-J. Dai, F. Yang, X. Lu, and H.-J. Wang. 2018. “Difference of Zinc Volatility in Diverse Carrier Minerals: The Critical Limit of Blast Furnace Dust Recycle.” Minerals Engineering 116:24–31. https://doi.org/10.1016/j.mineng.2017.11.001.
- Khaparde, V. V., A. D. Bhanarkar, D. Majumdar, and C. V. Chalapati Rao. 2016. “Characterization of Polycyclic Aromatic Hydrocarbons in Fugitive PM10 Emissions from an Integrated Iron and Steel Plant.” Science of the Total Environment 562:155–163. https://doi.org/10.1016/j.scitotenv.2016.03.153.
- Kumar, B., G. G. Roy, and P. Kumar Sen. 2020. “Comparative Exergy Analysis Between Rotary Hearth Furnace-Electric Arc Furnace and Blast Furnace-Basic Oxygen Furnace Steelmaking Routes.” Energy and Climate Change 1:100016. https://doi.org/10.1016/j.egycc.2020.100016.
- Lee, W. S., G. P. Chang-Chien, L. C. Wang, W. J. Lee, K. Y. Wu, and P. J. Tsai. 2005. “Emissions of Polychlorinated Dibenzo-P-Dioxins and Dibenzofurans from Stack Gases of Electric Arc Furnaces and Secondary Aluminum Smelters.” Journal of the Air & Waste Management Association 55 (2): 219–226. https://doi.org/10.1080/10473289.2005.10464613.
- Li, X. L., W. Q. Sun, L. Zhao, and J. J. Cai. 2018. “Material Metabolism and Environmental Emissions of BF-BOF and EAF Steel Production Routes.” Mineral Processing & Extractive Metallurgy Review 39 (1): 50–58. https://doi.org/10.1080/08827508.2017.1324440.
- Machado, J. G. M. S., F. Andrade Brehm, C. A. M. Moraes, C. A. dos Santos, A. C. F. Vilela, and J. B. M. da Cunha. 2006. “Chemical, Physical, Structural and Morphological Characterization of the Electric Arc Furnace Dust.” Journal of Hazardous Materials 136 (3): 953–960. https://doi.org/10.1016/j.jhazmat.2006.01.044.
- Markatos, N. C., G. M. Sideris, M. N. Christolis, and N. C. Markatos. 2020. “Numerical Simulation of Pollutants Dispersion Around an Electric-Arc-Furnace in Case of an Accidental Release.” Biodiversity International Journal 4 (1): 50‒57. https://doi.org/10.15406/bij.2020.04.00164.
- Mitchell, N. J., and F. J. Janzen. 2010. “Temperature-Dependent Sex Determination and Contemporary Climate Change.” Sexual Development 4 (1–2): 129–140. https://doi.org/10.1159/000282494.
- Mombelli, D., C. Mapelli, A. Gruttadauria, C. Baldizzone, F. Magni, P. L. Levrangi, and P. Simone. 2012. “Analisys of Electric Arc Furnace Slag.” Steel Research International 83 (11): 1012–1019. https://doi.org/10.1002/srin.201100259.
- Moser, S. C. 2010. “Communicating Climate Change: History, Challenges, Process and Future Directions.” WIREs Climate Change 1 (1): 31–53. https://doi.org/10.1002/wcc.11.
- Mu, L., L. Peng, X. Liu, H. Bai, C. Song, Y. Wang, and Z. Li. 2012. “Emission Characteristics of Heavy Metals and Their Behavior During Coking Processes.” Environmental Science & Technology 46 (11): 6425–6430. https://doi.org/10.1021/es300754p.
- Norgate, T. E., S. Jahanshahi, and W. J. Rankin. 2007. “Assessing the Environmental Impact of Metal Production Processes.” Journal of Cleaner Production 15 (8): 838–848. https://doi.org/10.1016/j.jclepro.2006.06.018.
- Odabasi, M., A. Bayram, T. Elbir, R. Seyfioglu, Y. Dumanoglu, A. Bozlaker, H. Demircioglu, H. Altiok, S. Yatkin, and B. Cetin. 2009. “Electric Arc Furnaces for Steel-Making: Hot Spots for Persistent Organic Pollutants.” Environmental Science & Technology 43 (14): 5205–5211. https://doi.org/10.1021/es900863s.
- Oreskes, N., K. Shrader-Frechette, and K. Belitz. 1994. “Verification, Validation, and Confirmation of Numerical Models in the Earth Sciences.” Science 263 (5147): 641–646. https://doi.org/10.1126/science.263.5147.641.
- Paulu, A., J. Bartacek, M. Seresova, and V. Koci. 2021. “Combining Process Modelling and LCA to Assess the Environmental Impacts of Wastewater Treatment Innovations.” Water 13 (9). https://doi.org/10.3390/w13091246.
- Pawełczyk, A., F. Božek, and K. Grabas. 2016. “Impact of Military Metallurgical Plant Wastes on the population’s Health Risk.” Chemosphere 152:513–519. https://doi.org/10.1016/j.chemosphere.2016.03.031.
- Petranikova, M., V. Ssenteza, C. M. Lousada, B. Ebin, and C. Tunsu. 2020. “Novel Process for Decontamination and Additional Valorization of Steel Making Dust Processing Using Two-Step Correlative Leaching.” Journal of Hazardous Materials 384:121442. https://doi.org/10.1016/j.jhazmat.2019.121442.
- Proctor, D. M., K. A. Fehling, E. C. Shay, J. L. Wittenborn, J. J. Green, C. Avent, R. D. Bigham, et al. 2000. “Physical and Chemical Characteristics of Blast Furnace, Basic Oxygen Furnace, and Electric Arc Furnace Steel Industry Slags.” Environmental Science & Technology 34 (8): 1576–1582. https://doi.org/10.1021/es9906002.
- Rehmus, F. H., D. P. Manka, and E. A. Upton. 1973. “Control of H2S Emissions During Slag Quenching.” Journal of the Air Pollution Control Association 23 (10): 864–869. https://doi.org/10.1080/00022470.1973.10469856.
- Remus, R., M. A. Aguado-Monsonet, S. Roudier, and L. D. Sanc. 2013. Best Available Techniques (BAT) Reference Document for Iron and Steel Production. European IPPC Bureau: European Union. https://doi.org/10.2791/97469.
- Ren, L., S. Zhou, T. Peng, and X. Ou. 2021. “A Review of CO2 Emissions Reduction Technologies and Low-Carbon Development in the Iron and Steel Industry Focusing on China.” Renewable and Sustainable Energy Reviews 143:110846. https://doi.org/10.1016/j.rser.2021.110846.
- Roba, C., C. Roşu, I. Piştea, A. Ozunu, and C. Baciu. 2016. “Heavy Metal Content in Vegetables and Fruits Cultivated in Baia Mare Mining Area (Romania) and Health Risk Assessment.” Environmental Science and Pollution Research 23 (7): 6062–6073. https://doi.org/10.1007/s11356-015-4799-6.
- Sammut, M. L., Y. Noack, J. Rose, J. L. Hazemann, O. Proux, M. Depoux, A. Ziebel, and E. Fiani. 2010. “Speciation of Cd and Pb in Dust Emitted from Sinter Plant.” Chemosphere 78 (4): 445–450. https://doi.org/10.1016/j.chemosphere.2009.10.039.
- Schwarzenbach, R., B. Escher, K. Fenner, T. Hofstetter, C. Johnson, U. Gunten, and B. Wehrli. 2006. “The Challenge of Micropollutants in Aquatic Systems.” Science (New York, NY) 313:1072–1077. https://doi.org/10.1126/science.1127291.
- Seppälä, J., S. Koskela, M. Melanen, and M. Palperi. 2002. “The Finnish Metals Industry and the Environment.” Resources, Conservation & Recycling 35 (1): 61–76. https://doi.org/10.1016/S0921-3449(01)00122-7.
- Sha, W. 2013. “High-Strength Low-Alloy Steel.” In Steels: From Materials Science to Structural Engineering, edited by W. Sha, 27–58. London: Springer.
- Smiljanić, S., N. Tomić, M. Perusic, L. Vasiljević, and S. Pelemis. 2019. “The Main Sources of Heavy Metals in the Soil and Pathways Intake. VI International Congress “Engineering, Environment and Materials in Processing Industry”. https://doi.org/10.7251/EEMEN1901453S.
- Stehle, S., and R. Schulz. 2015. “Agricultural Insecticides Threaten Surface Waters at the Global Scale.” Proceedings of the National Academy of Sciences of the United States of America 112. https://doi.org/10.1073/pnas.1500232112.
- Tchounwou, P. B., C. G. Yedjou, A. K. Patlolla, and D. J. Sutton. 2012. “Heavy Metal Toxicity and the Environment.” Molecular, Clinical and Environmental Toxicology 101:133–164. https://doi.org/10.1007/978-3-7643-8340-4_6.
- Timofeev, I., N. Kosheleva, and N. Kasimov. 2019. “Health Risk Assessment Based on the Contents of Potentially Toxic Elements in Urban Soils of Darkhan, Mongolia.” Journal of Environmental Management 242:279–289. https://doi.org/10.1016/j.jenvman.2019.04.090.
- Tomatis, L., A. Aitio, J. Wilbourn, and L. Shuker. 1989. “Human Carcinogens so Far Identified.” Japanese Journal of Cancer Research 80 (9): 795–807. https://doi.org/10.1111/j.1349-7006.1989.tb01717.x.
- Vandenberg, L. N., S. D. G. Rayasam, D. A. Axelrad, D. H. Bennett, P. Brown, C. C. Carignan, N. Chartres, et al. 2023. “Addressing Systemic Problems with Exposure Assessments to Protect the public’s Health.” Environmental Health 21 (1): 121. https://doi.org/10.1186/s12940-022-00917-0.
- Vestergaard, N. K., U. Stephansen, L. Rasmussen, and K. Pilegaard. 1986. “Airborne Heavy Metal Pollution in the Environment of a Danish Steel Plant.” Water, Air, and Soil Pollution 27 (3): 363–377. https://doi.org/10.1007/BF00649418.
- Wang, Z., D. Dong, X. Liang, G. Qu, J. Wu, and X. Xu. 1996. “Cancer Mortality Among Silicotics in China’s Metallurgical Industry.” International Journal of Epidemiology 25 (5): 913–917. https://doi.org/10.1093/ije/25.5.913.
- Wang, C., C. Ryman, and J. Dahl. 2009. “Potential CO2 Emission Reduction for BF–BOF Steelmaking Based on Optimised Use of Ferrous Burden Materials.” International Journal of Greenhouse Gas Control 3 (1): 29–38. https://doi.org/10.1016/j.ijggc.2008.06.005.
- Wang, J., L. Wang, Y. Wang, D. C. W. Tsang, X. Yang, J. Beiyuan, M. Yin, et al. 2021. “Emerging Risks of Toxic Metal(loid)s in Soil-Vegetables Influenced by Steel-Making Activities and Isotopic Source Apportionment.” Environment International 146:106207. https://doi.org/10.1016/j.envint.2020.106207.
- Wei, J., M. Chen, J. Song, F. Luo, L. Han, C. Li, and M. Dong. 2015. “Assessment of Human Health Risk for an Area Impacted by a Large-Scale Metallurgical Refinery Complex in Hunan, China.” Human and Ecological Risk Assessment: An International Journal 21 (4): 863–881. https://doi.org/10.1080/10807039.2014.890479.
- Wiedmann, T., and J. Barrett. 2010. “A Review of the Ecological Footprint Indicator—Perceptions and Methods.” Sustainability 2 (6): 1645–1693.
- Williams, T., and R. Nanstad. 2019. “Chapter 10 – Low-Alloy Steels.” In Structural Alloys for Nuclear Energy Applications, edited by G. R. Odette and S. J. Zinkle, 411–483. Boston: Elsevier.
- Yellishetty, M., M. M. Gavin, P. G. Ranjith, and A. Tharumarajah. 2011. “Environmental Life-Cycle Comparisons of Steel Production and Recycling: Sustainability Issues, Problems and Prospects.” Environmental Science & Policy 14 (6): 650–663. https://doi.org/10.1016/j.envsci.2011.04.008.
- Zhao, S., W. Xu, S. Zong, L. Yao, J. Liu, F. Lu, Y. Yi, et al. 2021. “The Pollution Characteristics and Full-Scale Risk Assessment of Coking Plant Soil Co-Contaminated with Polycyclic Aromatic Hydrocarbons and Heavy Metals.” Environmental Engineering Science 38 (9): 867–876. https://doi.org/10.1089/ees.2020.0416.