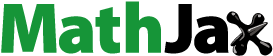
Abstract
Coal bursts caused by mining-induced seismicity occur in the working face in steeply inclined and extra thick coal seams (SIETCSs). This article presents a case study in SIETCS through discrete element simulation as well as field investigation. The evolution of the coal burst was studied from the perspective of stress distribution, crack propagation and coal fragment ejection. The results showed that dynamic failure mainly occurred in the coal near the roof. The deep bottom coal and the top coal near the roof are under high static stress due to the clamping effect of the roof and floor and the rotation of the deep roof. The coal burst in the working face was triggered by mining-induced seismicity. The coal burst occurred when the sum of the static stress and the dynamic stress caused by the mining-induced seismicity exceeds the sum of the ultimate strength of the coal and the support strength, which was called the ‘clamping-rotation-dynamic loads’ mechanism. During the coal burst, the cracks developed rapidly into the deep bottom coal and the top coal on the roof side. The results can serve as an important reference for the coal burst failure mechanism in the working face in SIETCSs.
1. Introduction
Coal burst is a violent hazard associated with the dynamic failure of coal. As the mining depth increases, coal bursts have been widely reported worldwide, including in Poland (Patynska Citation2013), the United States (Mark Citation2016), Canada (Keneti and Sainsbury Citation2018), China (He et al. Citation2017; Cai et al. Citation2018) and Australia (Zhang et al. Citation2017). Coal bursts were grouped into the self-initiated type and the triggered type (Mottahedi and Ataei Citation2019). Self-initiated coal bursts are related to the good energy storage capacity of coal, high unloading rates and high geo-stresses. A characteristic of the triggered coal burst is that the coal burst and mining-induced seismicity do not occur in the same area. The additional dynamic stress caused by mining-induced seismicity is the main contributor to triggered coal bursts.
There are a large number of SIETCSs in the northwest of China, such as Gansu, Ningxia and Xinjiang (Tu et al. Citation2015). In recent years, mining-induced seismicity-triggered coal bursts frequently occurred during the mining of SIETCSs (Li et al. Citation2021; Cao et al. Citation2023). The occurrence of coal bursts in SIETCSs is related to the evolution of stress and roof structures (Cao et al. Citation2020). Li et al. (Citation2017) studied the formation and failure of the overlying structures in SIETCS, which suggested that the rotation of the broken roof will result in the failure of the structure. Yun et al. (Citation2017) analysed the support pressures in the working face in SIETCS and found that the pressures increased significantly during roof fracture. Yang et al. (Citation2020) revealed the ‘toppling–slumping’ mechanism of roofs in SIETCS, and the results showed that the dynamic loads caused by the roof movement are the main reason for coal bursts in SIETCS. Wang et al. (Citation2019) established a mechanical model to reveal the coal burst mechanism, and the results showed that the abutment pressure near the roof side was higher. Cui et al. (Citation2019) found that the complex mining conditions and the strong dynamic disturbances were the main reasons for the formation of coal bursts in SIETCS. Yang et al. (Citation2020) obtained the instability criterion of the roof and demonstrated the evolution of dynamic failures in SIETCS. He et al. (Citation2020) established a mechanical model of the roof structures in SIETCS and concluded that the coal burst is mainly caused by roof breakage and horizontal stress. Wu et al. (Citation2020) analyzed asymmetric deformation and found that the tectonic stress and shear failure are important to the large deformation in SIETCS. Wang et al. (Citation2020) developed a mechanical model considering the different filling ratios of the gob and found that the filling ratio in the gob plays an important role in the breakage of the roof in SIETCS. Xu et al. (Citation2023) studied the coal burst mechanism in SIETCS through physical and numerical simulations and proposed the ‘squeeze-prying’ induced-failure mechanism. Wang et al. (Citation2022) analyzed the distribution of stress in the coal seam in SIETCS and proposed the failure process of the coal burst in SIETCS. Cao et al. (Citation2023) studied the stress distribution before the coal burst in SIETCS and found that a triangular stress concentration area formed on the roof side.
The studies mentioned above have enhanced our understanding of coal bursts in SIETCSs. Most studies were based on investigations of the dynamic failures that occurred in roadways in SIETCSs. However, as the mining depth increases, coal burst occurs in the working face in SIETCS, resulting in severe dynamic damage to the hydraulic supports. The mechanism and failure process of the coal burst in the working face need to be further studied. In addition, previous studies focused on the stress distribution in the bottom coal of the working face, however, the thickness of the top coal of the working face in SIETCSs is usually 6–9 m. Therefore, the stress evolution of the top coal during coal bursts also needs to be analyzed.
In this study, the in-situ damage characteristics and failure mechanism of the coal burst that occurred in the 5521-20 working face in Yaojie III Coal Mine were first analysed. Then, a calibrated UDEC model considering the top coal and supports was developed to study the development of the coal burst in SIETCS based on the case study. The stress distribution and evolution, crack propagation and fragments ejection pattern during the coal burst were investigated. Finally, the failure mechanism of coal bursts in the working face in SIETCS was discussed.
2 Case study
2.1. Geological and mining conditions
Yaojie III Coal Mine is located in the northwest of China, at the border of Gansu Province and Qinghai Province. The dip angle of the coal seam is about 60° and the thickness ranges from 36 to 115 m. The headentry and the tailentry are designed near the roof and the floor respectively, as shown in . The 5521-20 working face is mined at a depth of about 500 m, with a mining length of 1020 m and an inclination width of 34 ∼ 80 m. Horizontal section and top-coal caving mining technology were employed in the working face. The coal seam in Yaojie III Coal Mine was divided into different mining sections with the same section height, and the working face was arranged within the sections. As shown in , the height of each section is 12 m. The height of full-mechanized mining and the height of top coal in the 5521-20 working face are 3 m and 9 m, respectively. The geological profile is shown in , the main stratum in the roof are oil shale and sandstone. According to the calculation results based on the method proposed by Qian et al. (Citation2000), the key stratum is the oil shale with a thickness of 44 m.
2.2. The coal burst in Yaojie III coal mine
According to the site investigation results, there was no dynamic failure in Yaojie III Coal Mine during the mining of the shallow parts of the coal seam. However, some small coal bumps in the roadway ribs were recorded during the mining of the 5521-19 working face. Furthermore, dynamic failures occurred when mining the deep parts of the coal seam, which caused two casualties. As shown in , the main damaged area of the coal burst was located in the working face rather than the roadway. According to the micro-seismic monitoring system, mining-induced seismicity with an energy of 5.0E5 J occurred in the oil shale. The workers reported that the coal burst occurred after hearing a loud sound that was transmitted from the roof. The coal burst caused severe dynamic damage in a total of 22 m long area within the working face, the damaged area was close to the headentry and located on the roof side. Coal fragments were thrown into the headentry. And a large number of columns of the hydraulic supports were bent and destroyed, as shown in .
Figure 2. The coal burst in the 5521-20 working face: (a) location of the coal burst, (b) rollover of equipment, (c) broken hydraulic supports and (d) bending of hydraulic supports.

There are three characteristics of the coal burst: (1) Coal bursts in underground coal mining generally occur in the roadway. However, the dynamic failure areas of the coal burst occurred in the 5521-20 working face, including a wide range of rising of the bottom coal, the falling of the top coal and the destruction of a large number of supports in the working face. (2) The coal burst showed an obvious asymmetry failure characteristic. The large deformation and serious damage to the supports occurred in the areas near the roof. (3) There was no coal burst that occurred when mining in the shallow area, but coal burst occurred when mining in the deep area. In addition, the coal burst is closely related to mine tremors. The coal burst is the dynamic failure in the working face triggered by mining-induced seismicity during horizontal section mining of SIETCS.
2.3. Failure mechanism of the coal burst
The failure mechanism of the coal burst in the working face in SIETCS is shown in . A major reason for the formation of the SIETCS is that the coal seam suffered from large squeezing forces in the horizontal direction. The squeezing forces also play an important role in the mining process, which is called the clamping effect in SIETCS. The shallow roof broke after the upper section was excavated. However, the damage did not develop to the deep roof (e.g. key stratum). After mining the 5521-20 working face, there are mainly two different forms of rock movement in the steeply inclined roof. The displacement of the broken shallow roof in the upper gob increased with the increase of the mining area. The unbroken deep roof gradually rotated toward the upper gob, and the pivot point and rotation direction are shown in . A pair of forces which in the normal directions of the roof and floor, was formed because of the rotation of the deep roof, as shown in . Therefore, the coal seam near the roof side was in high static horizontal stress
as a result of the clamping effect and the rotation of the deep roof.
Figure 3. The mechanism of the coal burst in the working face in SIETCS: (a) movement of the roof and floor, (b) location of the high static stress and (c) the coal burst.

Mining-induced seismicity occurred due to the rock breakage, block rotation, slip and overturn of the roof structures. An additional dynamic stress was formed as the propagation of mining-induced seismicity (He et al. Citation2016). As illustrated in , the coal burst occurred under the effect of the superstition of static stress and dynamic stress. The main forms include the high-speed downward movement of the top coal and the high-speed upward movement of the bottom coal.
The ‘clamping-rotation-dynamic loads’ mechanism of the coal burst in the working face in SIETCS is proposed. With the increase of the gob, the deformation of the stratum on the two sides and the rotation of the deep roof increased. Therefore, the static stress in the coal near the roof side increased. In addition, the dynamic stress caused by the mining-induced seismicity increases with the increase of the gob. The total stress in coal is the sum of the static stress and the dynamic stress, the critical stress of the coal burst is the sum of the critical stress of coal and the strength of hydraulic supports, and the coal burst occurs as the total stress exceeds the critical stress, as shown in EquationEq. (1)(1)
(1) and EquationEq. (2)
(2)
(2)
(1)
(1)
(2)
(2)
where
and
are the total stress, dynamic stress and static stress in coal, respectively.
can be calculated by EquationEq. (6)
(6)
(6) , where
is the density of coal,
is the propagation velocities of the wave,
is the particle vibration velocities of the mining-induced seismicity.
can be obtained by conducting in-situ stress measurements in the field.
and
are the critical stress of coal burst, critical stress of coal and strength of hydraulic supports, respectively.
can be obtained by conducting a series of tests in the laboratory.
3. Numerical simulation method
3.1. Model setup
The top coal as well as the supports in the 5521-20 working face was considered in the numerical simulation. The model is 180 m in length and 90 m in height, and the dip angle is 60°, as shown in . In UDEC simulation, inappropriate block and zone sizes will produce incorrect simulation results regarding stress wave propagation and failure modes. Gao and Stead (Citation2014) analysed the effect of block size on failure patterns and concluded that the block size should be small enough that block size does not affect the failure modes of the model. The minimum triangular block size in the range of 0.2–0.5 m is reasonable at the same model scale as the one used in this study (Gao and Stead Citation2014; Cao et al. Citation2023). To improve computational efficiency, a strategy of ‘different block and zone sizes in different areas’ was adopted. The area around the 5521-20 working face is defined as the critical study area. In order to observe the fracture development during the coal burst, the block and zone within the critical study area have smaller sizes, with a minimum block size of 0.3 m and a minimum zone size of 0.1 m. The outer block size in coal gradually increases to 0.6, 1.5 and 2 m. The outer zone size gradually increases to 0.3, 0.6, 1 and 2 m. The coal burst in the field indicates that the coal of the working face was the main failure area, and the roof was not the major failure area. Therefore, the rock mass in the roof and floor were subdivided into rectangular blocks to simulate the rock blocks after mining, and the interlayer in the rock mass was not considered.
In numerical simulations, mining-induced seismicity is usually considered as stress or vibration waves, including reasonably simplified waves and waves measured from coal mines, which are then applied to the target area (He et al. Citation2016; Mu et al. Citation2019). However, the waveforms as well as the location of the seismic waves in the field are very complex. The simulation of the self-initiated seismicity was conducted in this study. The micro-mechanical parameters in the key stratum were reduced during the dynamic calculation stage, so that the adjacent blocks would slide and move. Therefore, the simulated mining-induced seismicity caused by the failure of the key stratum occurred. The location of the mining-induced seismicity was determined according to the monitoring results in the field. In UDEC, the dynamic failure simulation needs to be carried out in the dynamic mode. The selection of the damping parameters in the dynamic calculation is important. In order to reduce the wave reflection, viscous boundaries were used. Rayleigh damping is widely used in dynamic analysis. The critical damping ratio is generally 2%–5%. A small value of the critical damping ratio should be used when performing large displacement simulations (Itasca Consulting Group Inc Citation2014). Therefore, Rayleigh damping was used at the critical damping ratio of 2%. To study the stress and fragments ejection velocity in the coal during the coal burst, two groups of monitoring points were set to monitor the stress and velocity respectively, as shown in . The support and top coal in the 5521-20 working face are shown in .
The Mohr-Coulomb elastic model was adopted for blocks, and the Coulomb slip model with residual strength was adopted for the joints between different blocks. According to the measurement results in Yaojie III Coal Mine, the initial horizontal stress and the initial vertical stress of the bottom boundary were set to 22.7 MPa and 12.5 MPa, respectively. Both sides and bottom were set as the displacement boundary, and the velocity was set to 0 m/s. The top boundary of the model was set as the stress boundary. Considering that the overlying stratum was not completely included in the model, an equivalent stress of 12.5 MPa was applied to the top boundary. Different from the traditional mechanical parameters, the parameters used in the UDEC model are called micro-mechanical parameters. Same to the method adopted by Cao et al. (Citation2020, Citation2023), the micro-mechanical parameters were determined through three steps as follows: (1) The conventional mechanical properties of coal, oil shale and sandstone were obtained by conducting tests in the laboratory, including Poisson’s ratio, cohesion, friction angle and elastic modulus. (2) According to the RQD method (Zhang and Einstein Citation2004) presented in EquationEq. (3)(3)
(3) , the elastic modulus of the coal seam and rock mass were obtained. The rock mass compressive strength was obtained based on EquationEq. (4)
(4)
(4) (Singh and Seshagiri Rao Citation2005). (3) The micro-mechanical parameters were calculated by EquationEq. (5)
(5)
(5) and EquationEq. (6)
(6)
(6) presented in UDEC (Itasca Consulting Group Inc Citation2014). The trial-and-error method combined a series of uniaxial compression simulations and Brazil splitting simulations were conducted to calibrate the micro-mechanical parameters. The numerical model used for the calibration tests and the simulation results are shown in . The block size of the calibration model was also 0.3 m, the same as the block size of the critical study area in order to reduce the effect of block sizes. As presented in , the bottom plate of the model was fixed and the top plate was loaded at a velocity of 0.01 m/s. The micro-mechanical parameters of the coal, oil shale and sandstone used in the large-scale UDEC model are present in .
(3)
(3)
where
is the elastic modulus obtained in laboratory experiments.
is the elastic modulus of coal and rock mass in the UDEC numerical model.
(4)
(4)
where
is the compressive strength obtained in laboratory experiments.
is the compressive strength of coal and rock mass in the UDEC numerical model. In this study, n = 0.63 was used.
(5)
(5)
where
and
are the bulk and shear moduli used in the UDEC numerical model, respectively. μ is Poisson’s ratio obtained in laboratory experiments.
(6)
(6)
where
and
are the normal stiffness and shear stiffness of the contact.
is the smallest length of zone and
is a scaling factor (usually set to 10).
Table 1. Calibrated micro-properties for UDEC numerical model.
3.2. Modelling procedure
According to the mining conditions of the 5521-20 working face, there were three calculation stages after the numerical model was calculated to the initial stress balance under the given boundary conditions. Stages I and II were performed in the static calculation mode, and Stage III was performed in the dynamic calculation mode. Stage I: as shown in , the upper section was excavated first. The top coal was not fully mined out to simulate the broken rock and coal formed during the horizontal section mining of the steeply inclined extra-thick coal seam. Stage II: as shown in , the 5521-20 working face was excavated. The height of the excavation was 3 m and the height of the top coal was 9 m. After the 5521-20 working face was excavated, the support was arranged between the top coal and the bottom coal. Stage III: the micro-mechanical parameters of the oil shale were reduced so that the mining-induced seismicity was simulated. The coal burst was triggered by mining-induced seismicity, as shown in .
4. Results and analyses
4.1. Characteristic of stress before the coal burst
shows the stress distribution characteristics around the 5521-20 working face before the coal burst occurred. As shown in , different destress zone appeared in the top coal and bottom coal due to mining. The horizontal stress and shear stress in destress zone were significantly decreased. However, on the one hand, the excavation of the upper section and the 5521-20 working face resulted in the deformation of the stratum. The horizontal stress in the deep bottom coal increased due to the deformation of the stratum on the two sides. On the other hand, the rotation of the key stratum occurred. As a result, high-stress zones are formed in the coal on the roof side and in the deep bottom coal.
4.2. Stress evolution
illustrates the horizontal, shear and vertical stress evolution in the top and bottom coal. It shows that stress evolutions are different at different stages. The three stages in the modelling procedure are presented in section 3.2, including stage I: mining of the upper section; stage II: mining of the 5521-20 working face; and stage III: coal burst.
Figure 8. The change of stresses before and during the coal burst: (a) horizontal stress in top coal, (b) horizontal stress in bottom coal, (c) shear stress in top coal, (d) shear stress in bottom coal, (e) vertical stress in top coal and (f) vertical stress in bottom coal.

Stage I: As shown in , due to the decompression effect of mining, the horizontal stress in the top coal decreased significantly, and the maximum reduction value is 12.98 MPa. However, the horizontal stress in the bottom coal remains at a high level. As shown in , the shear stress in both the top and bottom coal increased under the effect of the forces which in the normal directions of the roof and floor, and the increasing values of the top coal were greater. The vertical stresses of 1#, 5# and 6# increased and the increasing values were 4.15, 4.24 and 1.84 MPa, respectively, indicating that the vertical stress in the coal on the roof side increased because of the roof rotation. The vertical stresses in the coal which were far from the roof decreased, as shown in . The stress evolution in stage I showed that after the upper section was mined, the horizontal and vertical stresses in the bottom coal were higher than those in the top coal.
Stage II: After mining of the 5521-20 working face, the horizontal, shear and vertical stresses in the top coal decreased, as shown in . This is due to the increased failure in the top coal. However, it should be noted that the horizontal stress, shear stress and vertical stress of 1# monitoring point were 15.99, 8.25 and 9.24 MPa, respectively, which indicates that the top coal near the roof side was still in a stress concentration zone. As shown in , the horizontal, shear and vertical stresses in the bottom coal near the roof increased, and the horizontal, shear and vertical stresses in the bottom coal far from the roof decreased. Therefore, we can conclude that: after mining of 5521-20 working face, the static stress concentration zone was formed in the coal near the roof under the clamping effect of the roof and floor, including the top coal and the bottom coal. The analysis in Section 2.3 is verified by the results of the numerical simulation. The energy stored in the coal near the roof rises under the influence of high stress, causing a higher risk of coal bursts.
Stage III: When the time was 2.021 s, the coal burst in the 5521-20 working face was triggered by the mining-induced seismicity. As shown in , the horizontal stress, shear stress and vertical stresses in the coal suddenly decreased after the coal burst occurred, indicating that the coal was severely damaged in the coal burst.
4.3. Crack development in the coal burst
shows the crack propagation in the coal burst. Before the coal burst occurred, there were a large number of cracks formed around the 5521-20 working face. It should be noticed that there are only a few cracks in the area near the roof. As can be seen from , the height of crack development in the bottom coal of the working face was small, and there was no crack in the deep bottom coal and the top coal near the roof before the coal burst. As shown in , shear failure began to occur in the coal near the roof as the dynamic time was 0.01s. With the increase of dynamic time, the cracks gradually developed into deep coal. The top coal was destroyed, and the height of crack development in the bottom coal increased, as shown in . When the dynamic time was 0.05s, some typical failures in the 5521-20 working face were observed. As can be seen from , the coal burst resulted in a large displacement of the coal around the working face as well as the overturn of the supports. The failure characteristics in simulation results are consistent with the observations in the coal burst. Tensile cracks were the dominant damage type in the shallow bottom coal, while shear cracks were the dominant damage type in the deep bottom coal. This is because, after the mining of 5521-20 working face, the shallow bottom coal was in the biaxial stress state, while the deep bottom coal was in the triaxial stress state. When the sum of the static stress and the dynamic stress exceeded the ultimate strength of the coal, tensile failure occurred in the shallow bottom coal, and shear failure occurred in the deep bottom coal.
4.4. Ejection velocity pattern
shows the evolution of fragments ejection during the coal burst. Before the coal burst occurred, the velocity around the working face was 0 m/s and no dynamic failure occurred around the 5521-20 working face. When the dynamic time was 0.01 s, the coal burst occurred. In the early stage of the coal burst, coal fragments were ejected from the top coal and bottom coal at the same time, as shown in . The distance between the high-velocity zone in the top coal and the roof was smaller compared with the bottom coal. An asymmetric high ejection velocity zone was formed in the coal. As the dynamic time increased, the high-velocity zones in the top coal gradually moved away from the roof, and the high velocity in the bottom coal developed to the deep zone. As shown in , when the dynamic time was 0.05 s, three high ejection velocity regions appeared, which were the top coal, the bottom coal and the coal near the roof in the working face, indicating that coal bursts occurred in these regions. Compared with the coal burst in the top coal, there is a larger area of coal burst in the bottom coal. This is because the area of static stress concentration in the deep bottom coal is larger, while the stress in the top coal that is far from the roof decreased after mining of the 5521-20 working face.
Figure 10. Evolution of the ejection velocities in the coal burst: (a) the velocity before the coal burst, (b) dynamic time is 0.01s, (c) dynamic time is 0.02s, (d) dynamic time is 0.03s, (e) dynamic time is 0.04s and (f) dynamic time is 0.05s.

The changes in the coal fragment ejection velocity near the working face during the coal burst were shown in . There were two stages of the coal burst according to the change in ejection velocity: the coal burst development stage and the coal burst completed stage. In the coal burst development stage, the ejection velocities increased with the dynamic time. When the dynamic time was 0.0254s, the development of coal burst in the top coal was completed. The maximum ejection velocity of 1, 2, 3 and 4 # monitoring points were 9.65, 15.93, 13.53 and 7.37 m/s. As the dynamic time was 0.0433s, the development of coal burst in the bottom coal was completed. The maximum ejection velocity of 5, 6, 7 and 8 # monitoring points were 4.58, 13.81, 15.17 and 16.32 m/s. The ejection velocities of the fragments obtained in the numerical simulation are in good agreement with previous studies (Ortlepp and Stacey Citation1994; Li et al. Citation2021; Yang et al. Citation2020).
Figure 11. Ejection velocities during the coal burst: (a) the velocities in the top coal and (b) the velocities in the bottom coal.

shows the evolution of the velocity vectors during the development of the coal burst. As shown in , when the dynamic time was 0.01 s, the coal burst was in its early stages. The velocity direction of the top coal was southeast, the velocity direction of the bottom coal was northwest, and the direction of the coal near the roof was southeast and northeast. With the increase of dynamic time, the ejection direction gradually changed, and the value of ejection velocity increased continuously. Finally, the ejection direction in the top coal was changed downward, and the ejection direction in the bottom coal was changed upward, as shown in .
5. Discussions
The steeply inclined coal seam is mainly subjected to horizontal stresses and forces
which are perpendicular to the face of the seam, as shown in . The numerical simulation results show that the characteristics of static stress in the steeply inclined coal seam are different in different areas after the workings are mined. The static stresses in the shallow bottom coal and most of the top coal are at low levels due to the unloading effect caused by the mining of the working face, as shown in the green part in . The deep-bottom coal is in the static stress concentration zone, which is consistent with the results presented in these studies (Wang et al. Citation2019; Wang et al. Citation2022; Cao et al. Citation2023). The stress in the bottom coal increases under the clamping effect and the rotation of the deep roof. However, it should be noted that the top coal near the roof is also in the static stress concentration zone, as shown in the yellow part in , which is mainly related to the rotation and compression of the inclined roof. Therefore, both the deep bottom coal and the top coal near the roof are high coal burst risk areas, which has been verified by field investigation and numerical simulation. Of course, the area located far from the working face is still in the in-situ static stress, as shown in the blue part in . Mining-induced seismicity plays a triggering role in coal bursts. The coal burst in the working face occurs when the sum of the static stress in the stress concentration zone and the dynamic stress caused by the mining-induced seismicity exceeds the sum of the ultimate strength of the coal and the support strength, which is known as the ‘clamping-rotation-dynamic loads’ mechanism.
The control of coal bursts is important in mining practice. Wang et al. (Citation2019) implemented blasting in the bottom coal to reduce static load stresses. He et al. (Citation2020) proposed to conduct a large number of shallow and deep hole blasting in the roof to reduce the risk of coal bursts. Cao et al. (Citation2020) suggested performing large-diameter drilling to reduce the stresses in the rib of the roadway. However, the top coal near the roof was not considered. This study shows that the top coal near the roof is also the main static stress concentration area and dynamic failure area. In addition, the severe failure of supports in the working face should also be noted. Therefore, in the prevention strategy of coal bursts in the working face in SIETCSs, the destress measures in the top coal and the new supports with greater support strength should also be considered.
6. Conclusions
This article presents a case study of the coal burst in the working face during section mining of SIETCS. The stress evolution, crack development and fragments ejection pattern were studied through UDEC numerical simulation and field investigation. The main conclusions of this study are as follows:
Due to the clamping effect of the roof and floor and the rotation of the deep roof, the deep bottom coal and the top coal near the roof are under high static stress during the mining of sharply inclined coal seams. Accordingly, these areas are at high risk of coal bursts. The ‘clamping-rotation-dynamic loads’ mechanism of the coal burst in the working face in SIETCS was proposed.
The cracks developed rapidly into the deep bottom coal and the coal near the roof during the coal burst. After the development of the coal burst, a large number of supports failed. Tensile cracks were the dominant damage type in the shallow coal, while shear cracks were the dominant damage type in the deep bottom coal.
The mining-induced seismicity was simulated by reducing the micro-mechanical parameters of the key stratum. The coal burst in the working face was triggered by the mining-induced seismicity, and dynamic failure occurred in both the top and bottom coal on the roof side. The maximum ejection velocity of coal fragments exceeds 16 m/s. The simulated results are in good agreement with the field observations, indicating that the adopted method can reproduce the coal bursts triggered by mining-induced seismicity well. This method needs to be validated by applying it to different conditions in future studies.
Acknowledgements
The first author Jinrong Cao would like to express his sincere thanks to the China Scholarship Council (CSC) for the financial support for his study at TU Bergakademie Freiberg, Germany.
Data availability statement
The data that support the findings of this study are available from the first author, Jinrong Cao, upon reasonable request.
Disclosure statement
The authors declare they have no conflict of interest to this work.
Additional information
Funding
References
- Cai W, Dou L, Zhang M, Cao W, Shi J-Q, Feng L. 2018. A fuzzy comprehensive evaluation methodology for rock burst forecasting using microseismic monitoring. Tunnel Undergr Space Technol. 80:232–245.
- Cao J, Dou L, He J, Zhu G, Wang Z, Bai J, Han Z. 2023. Failure mechanism and control of coal bursts triggered by mining-induced seismicity in steeply inclined and extra thick coal seam. Front Earth Sci. 10:1042539.
- Cao J, Dou L, Zhu G, He J, Wang S, Zhou K. 2020. Mechanisms of rock burst in horizontal section mining of a steeply inclined extra-thick coal seam and prevention technology. Energies. 13(22):6043.
- Cui F, Lei Z, Chen J, Chang B, Yang Y, Li C, Jia C. 2019. Research on reducing mining-induced disasters by filling in steeply inclined thick coal seams. Sustainability. 11(20):5802.
- Gao FQ, Stead D. 2014. The application of a modified Voronoi logic to brittle fracture modelling at the laboratory and field scale. Int J Rock Mech Min Sci. 68:1–14.
- He J, Dou L, Gong S, Li J, Ma Z. 2017. Rock burst assessment and prediction by dynamic and static stress analysis based on micro-seismic monitoring. Int J Rock Mech Min Sci. 93:46–53.
- He J, Dou L, Mu Z, Cao A, Gong S. 2016. Numerical simulation study on hard-thick roof inducing rock burst in coal mine. J Cent South Univ. 23(9):2314–2320.
- He S, Song D, He X, Chen J, Ren T, Li Z, Qiu L. 2020. Coupled mechanism of compression and prying-induced rock burst in steeply inclined coal seams and principles for its prevention. Tunnelling Underground Space Technol. 98:103327.
- Itasca Consulting Group Inc. 2014. UDEC manual, Version 6.0. U.S. Minneapolis.
- Keneti A, Sainsbury B-A. 2018. Review of published rockburst events and their contributing factors. Eng Geol. 246:361–373.
- Li J, Zhao J, Gong SY, Wang HC, Ju MH, Du K, Zhang QB. 2021. Mechanical anisotropy of coal under coupled biaxial static and dynamic loads. Int J Rock Mech Min Sci. 143:104807.
- Li X, Wang Z, Zhang J. 2017. Stability of roof structure and its control in steeply inclined coal seams. Int J Min Sci Technol. 27(2):359–364.
- Li Z, He S, Song D, He X, Dou L, Chen J, Liu X, Feng P. 2021. Microseismic temporal-spatial precursory characteristics and early warning method of rockburst in steeply inclined and extremely thick coal seam. Energies. 14(4):1186.
- Mark C. 2016. Coal bursts in the deep longwall mines of the United States. Int J Coal Sci Technol. 3(1):1–9.
- Mottahedi A, Ataei M. 2019. Fuzzy fault tree analysis for coal burst occurrence probability in underground coal mining. Tunnelling Underground Space Technol. 83:165–174.
- Mu Z, Liu G, Yang J, Zhao Q, Javed A, Gong S, Cao J. 2019. Theoretical and numerical investigations of floor dynamic rupture: a case study in Zhaolou Coal Mine, China. Saf Sci. 114:1–11.
- Ortlepp WD, Stacey TR. 1994. Rockburst mechanisms in tunnels and shafts. Tunnelling Underground Space Technol. 9(1):59–65.
- Patynska R. 2013. The consequences of the rock burst hazard in the Silesian companies in Poland. Acta Geodynamica et Geomaterialia. 10(2):227–235.
- Qian M, Miao X, Xu J. 2000. Key strata theory in ground control. Xuzhou: China University of Mining and Technology Press.
- Singh M, Seshagiri Rao K. 2005. Empirical methods to estimate the strength of jointed rock masses. Eng Geol. 77(1–2):127–137.
- Tu H, Tu S, Yuan Y, Wang F, Bai Q. 2015. Present situation of fully mechanized mining technology for steeply inclined coal seams in China. Arab J Geosci. 8(7):4485–4494.
- Wang H, Wu Y, Liu M, Jiao J, Luo S. 2020. Roof-breaking mechanism and stress-evolution characteristics in partial backfill mining of steeply inclined seams. Geomatics Nat Hazards Risk. 11(1):2006–2035.
- Wang S, Cao A, Wang Z, Cao J, Liu Y, Xue C, Guo W. 2022. Study on mechanism of rock burst in horizontal section mining of a steeply inclined extra-thick coal seam. Lithosphere. 2022(Special 11):7058797.
- Wang Z, Dou L, Wang G. 2019. Coal burst induced by horizontal section mining of a steeply inclined, extra-thick coal seam and its prevention: a case study from Yaojie No. 3 coal mine, China. Shock Vib. 2019:1–13.
- Wu G, Chen W, Jia S, Tan X, Zheng P, Tian H, Rong C. 2020. Deformation characteristics of a roadway in steeply inclined formations and its improved support. Int J Rock Mech Min Sci. 130:104324.
- Xu H, Lai X, Shan P, Yang Y, Zhang S, Yan B, Zhang Y, Zhang N. 2023. Energy dissimilation characteristics and shock mechanism of coal-rock mass induced in steeply-inclined mining: comparison based on physical simulation and numerical calculation. Acta Geotech. 18(2):843–864.
- Yang S, Li L, Deng X. 2020. Disaster-causing mechanism of roof “toppling–slumping” failure in a horizontal sublevel top-coal caving face. Nat Hazards. 100(2):757–780.
- Yang X, Ren T, Tan L. 2020. Estimation of average ejection velocity generated by rib burst under compression load. Int J Rock Mech Min Sci. 128:104277.
- Yang Y, Lai X, Shan P, Cui F. 2020. Comprehensive analysis of dynamic instability characteristics of steeply inclined coal-rock mass. Arab J Geosci. 13(6):241.
- Yun D, Liu Z, Cheng W, Fan Z, Wang D, Zhang Y. 2017. Monitoring strata behavior due to multi-slicing top coal caving longwall mining in steeply dipping extra thick coal seam. Int J Min Sci Technol. 27(1):179–184.
- Zhang C, Canbulat I, Hebblewhite B, Ward CR. 2017. Assessing coal burst phenomena in mining and insights into directions for future research. Int J Coal Geol. 179:28–44.
- Zhang L, Einstein HH. 2004. Using RQD to estimate the deformation modulus of rock masses. Int J Rock Mech Min Sci. 41(2):337–341.