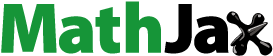
Abstract
With the increase in coal mining depth, many rock bursts triggered by fold structures have been observed, but the disaster mechanism is not clear. This research aims at investigating the influence of upright fold structure(UFS) on rock burst mechanisms. The mechanical model and numerical model of the UFS are constructed, and the mining stress evolution law and rock burst mechanism of working face in a UFS area are studied by utilizing engineering practice. The research shows that the occurrence of rock burst disasters in the fold structure area has obvious regional characteristics. The horizontal and vertical stress of the UFS in the horizontal distribution is similar to the periodic variation characteristics of the sine (cosine) curve. The stress state of the UFS area is divided into five areas. The horizontal and vertical stress concentration factors increase first and then decrease with the working face gradually approaching and away from the upright fold syncline axis. A roadway impact risk index I0 is proposed to determine whether the roadway is damaged, and the mechanism of inducing ground pressure during mining in UFS areas of deep mines is expounded. The control plan effectively reduces the stress levels of surrounding rock in working faces.
Article Highlights
The paper establishes a mechanical model for upright fold structure and theoretically analyzes the stress evolution characteristics of different regions of fold structures under the influence of different fold elements.
Based on the mechanism of induced rock burst by the superposition of dynamic and static loads, the mechanism of rock burst occurrence in the upright fold structure area is proposed, and the source of dynamic and static load force during the mining of the working face in the structure area.
The paper proposes a prevention and control approach for rock bursts in folded structural areas and verifies the effectiveness of the rock burst prevention and control plan based on engineering practice, which can provide a reference for the safe mining of working faces under similar geological conditions.
1. Introduction
Rock bursts, a dynamic geological hazard in underground coal mining, are characterized by the sudden and violent failure of coal and rock masses with a large energy release. They pose a serious threat to the production and safety of underground coal mining or surface buildings, and in some cases, may result in injury and loss of life (Cao et al. Citation2015; Akdag et al. Citation2021; Shirani Faradonbeh et al. Citation2022). Fold structure is formed by bending deformation of coal seam and rock stratum under vertical and horizontal stress extrusion and torsion. It is one of the most basic structural types in the process of crustal movement (Singh Citation1989; Zhang et al. Citation2021). In China’s coal mining, resource mining in folded structural areas accounts for a large proportion. Research shows that the tectonic stress in the folded area has a significant impact, and under the influence of mining and excavation disturbances in the working face, it is very easy to induce coal and rock dynamic disaster accidents (Jia et al. Citation2018; Ullah et al. Citation2022). The statistics of a large number of rock bursts show that the area affected by geological fold structure is more prone to dynamic disasters (Pan et al. Citation2018; Wang et al. Citation2018; Zhang et al. Citation2020). For example, On 2nd August 2019, the f5010 and f5009 roadways of Tangshan mine located at the axis of the syncline structure suffered a rock burst, resulting in seven people deaths and five people injuries (Cao et al. Citation2021). From March to September 2006, 28 rock burst accidents occurred in the first mining face of the 2502 mining district of Yan Bei Coal Mine near the syncline axis, causing extensive damage to the roadway, resulting in 1 person’s death and 3 people’s injuries (Chen et al. Citation2019). Otherwise, multiple rock bursts triggered by fold structure were recorded in many other countries, including the USA, Poland, Australia, South Africa, Germany, Russia, and Canada (Lovchikov Citation1997; Stewart et al. Citation2001; Lee et al. Citation2004; Maleki and Lawson Citation2017; Van Dyke et al. Citation2018; Zhou et al. Citation2023).
The uneven stress distribution in the fold structure area has an important influence on the sudden release of coal and rock energy. Many scholars have done different angles of analysis and obtained a lot of research results. Cheng et al. (Citation2023) analyzed and discussed the distribution law of the stress field of the mine fold structure and its relationship with microseismic events through field geological surveys, field measurements, and other methods. Cao et al. (Citation2018) research shows that the systematic and scientific analysis of fold structure characteristics and coal thickness variation characteristics is helpful to clarify the area where rock burst is prone to occur in the working face, thus improving the safety and productivity of coal mines. Wang et al. (Citation2018) analyzed the impact of syncline structure on working face mining through an accident case study. Wang et al. (Citation2019b) studied the mechanism of rock bursts in syncline structure areas by microseismic, energy density cloud, and seismic velocity tomography. Chen et al. (Citation2010) analyzed the relationship between roadway excavation direction and working face mining layout in fold structure area and rock burst and put forward targeted prevention measures from the perspective of strategic defense of rock burst.
Theoretical analysis and data statistical analysis is a powerful tool for assessing the rock burst potential. However, due to the limitations of model size, complex mechanical properties of coal and rock mass, and excavation sequence of a longwall face, a large-scale parametric investigation cannot be carried out. In comparison, the numerical technique has proved to be a powerful tool for studying the mechanics of underground rock (Starfield and Cundall Citation1988). Chen et al. (Citation2011) used numerical simulation to study the stress distribution law during the formation of fold structure and the variation law of the local stress field caused by working face mining. Guo et al. (Citation2022) studied the stress distribution characteristics of the tectonic zone by simulating the influence of geological factors on the tectonic static load stress and revealed the law of roadway rock burst instability in the tectonic zone. Lu et al. (Citation2020) used a numerical simulation method to analyze the stress evolution law in the process of coal seam mining in a folding area and explored the stress distribution characteristics of coal and rock in different positions of the fold area. Wang et al. (Citation2020) simulated and analyzed the evolution characteristics of the stress field in the fold structure area during the mining of the working face, and studied the law of mine pressure in different areas of the fold structure under the influence of mining.
In summary, many scholars have conducted multi-angle studies on the relationship between the stress evolution characteristics of the working face during mining in the fold structure area and the dynamic disaster of rock burst. However, due to the complexity of the fold structure, there are still many problems to be solved. Among them, the mechanical analysis of the stress evolution law of the fold area under the change of different fold structural elements, the vertical and horizontal stresses evolution characteristics, and the mechanism of induced punching during the mining of the working face still lack a complete description. Therefore, the mechanical model of the UFS is established, and the stress evolution law under different fold elements is discussed. At the same time, the numerical model under the geological conditions of fold structure is constructed. From the perspective of dynamic and static load superposition, the mechanism of rock burst in the mining of the fold structure area of the working face is discussed. Finally, the idea and scheme of rock burst prevention and control in the fold structure area are formulated, which can provide a reference for rock burst prevention and control in the fold structure area of the working face.
2. Classification of fold structure under mining background
2.1. Classification of fold structure
The fold structure is formed by the bending deformation of the rock stratum due to the extrusion of crustal movement. It is the most basic geological structure type. The fold structure can be divided into the basic form of syncline and anticline (Foster and Gray Citation2000; DeCelles and Coogan Citation2006). As shown in , The rock stratum in the syncline area is concave downward, and the rock stratum in the anticline area is convex upward. The fold structure has many geometric features. The slopes on both sides of the fold are called limbs. The line connecting the maximum bending point in the syncline or anticline area is called the axial line. The surface is perpendicular to the maximum bending point in the syncline or anticline area is called the axial plane. The distance between the arc tops of two adjacent synclines or anticlines is the wavelength of the fold. The distance between the two arc tops of the adjacent syncline and anticline on the axial plane is twice the amplitude of the fold.
Affected by the geological environment, the occurrence forms of fold structures are complex and diverse. Based on the occurrence of the axial plane and the two wings of the fold, the fold can be divided into five forms: upright fold, overturned fold, recumbent fold, convolute fold, and inclined fold (Sanderson Citation1979; Ghosh et al. Citation2002), as shown in and .
Figure 2. Distribution map in the vertical profile of folds (a) upright fold (b) overturned fold (c) recumbent fold (d) convolute fold (e) inclined fold.

Table 1. The distribution of folds on a vertical section.
2.2. Influence of fold structure types on coal mining
Over the decades, with the coal resources in China rapidly getting exhausted, the mining depth has increased substantially, e.g. It was observed that the increasingly complicated engineering geological conditions had posed a great threat to the safety production of Chinese coal mines. The remarkable characteristics of coal seam mining in the fold structure area are undulating coal seam and rock stratum, complex structural form, the great influence of horizontal tectonic stress, and non-uniformity of stress distribution characteristics of roadway surrounding rock. Under the influence of mining engineering disturbance, it is easy to cause serious local deformation and failure of roadway, and even induce rock burst disaster.
In recent years, according to incomplete statistics, more than 130 rock bursts accidents have occurred in typical mines (Hua Ting Coal Mine, Yan Bei Coal Mine, and Hu Jiahe Coal Mine) affected by fold structures in Northwest China (Cai et al. Citation2020), as shown in . It can be seen from the statistical data that the occurrence of rock burst disasters in the fold structure area has obvious regional characteristics. The number of disasters in the syncline area is much larger than that in the anticline area and the fold limb area. At the same time, the range and degree of roadway damage caused by rock bursts in the fold syncline area are more severe.
Figure 3. Statistic diagram of rock burst frequency and damage range in a fold structure area of a typical mine.

shows the panel layout of Gao Jiapu Coal Mine is located in Xianyang City, northwest of Shaanxi Province, China. The Gao Jiapu Coal Mine has a high rock burst risk and is a characteristic coal mine with rock burst hazards. The average mining depth of 204 working faces (LW204) is 1000 m. The typical X3 UFS (syncline region) is developed in the middle of the working face. The syncline structure has an amplitude of 80 m, a wavelength of 1000 m, and an inter-wing angle of 155°. A microseismic monitoring system called SOS, developed by the Central Mining Institute of Poland, was installed in the Gao Jiabao Coal Mine, and the maximum locating errors are 20 m in the horizontal direction and 30 m in the vertical direction, respectively. On September 21, 2019, a rock burst accident occurred in the LW204. The SOS microseismic monitoring system monitored a mining tremors event with an energy of 4.60 × 106 J. The mining tremors event was located about 25 m ahead of the mining position of the LW204 and 15 m above the coal seam. The rock burst disaster caused different degrees of damage to the 100 m range of the haulage tunnel in the LW204. The maximum floor heave of the roadway floor was 2.0 m, the roof caving height of the roadway was 1.5 m, and the damage depth of the roadway side was 1.0 m.
is the distribution map of the fold structure in Hu Jiahe Coal Mine. The 402103 working face (LW402103) is the first mining face in the 402 panels. The average mining depth of the working face is 680 m. The working face has a typical UFS (A4 anticline and A5 syncline). The A4 anticline wavelength is 2000 m, the amplitude is 120 m, the wing angle is 170°, and the working surface is covered with a multi-layer thick hard sandstone layer. On October 27, 2016, at the end of LW402103, a mining tremors event with an energy of 2.76 × 105J occurred in the leading area of the working face, which was located in the axial area of the A4 anticline. The mining tremors event caused the roof subsidence of the haulage roadway in the working face to be obvious within 20-35 m ahead, and the subsidence amount was 600–1000 mm. The floor of the drainage roadway appeared floor heavy and cracking, the floor heave was about 200 mm, the crack width was about 40 mm, and the overall section deformation of the roadway was serious.
Figure 5. The location of the source of the strong mine earthquake and its onsite appearance (a) Coal mine fold structure form diagram (b) Mining tremors location (c)Haulage roadway scene pictures (d)Drainage roadway scene pictures.

It can be seen from the above cases that even the UFS with the lowest complexity of fold structure seriously threatens the safe mining of coal mines. Especially when the coal mining face is mining toward the anticline or syncline area, the interaction between tectonic stress and coal mining disturbance leads to a sharp increase in the degree of danger (a significant increase in the frequency of accidents). To avoid the occurrence of coal mine disasters, at the beginning of the design of the coal mining face, the working face will be designed as far as possible to avoid the working face in the fold structure affected area, to the influence of tectonic stress on the safe mining of the working face. However, due to the complexity of the geological environment, the fold structure cannot be completely avoided, and the fold parameters (amplitude, wavelength, mining depth) change at any time, which leads to the complexity of the tectonic stress field. Therefore, it is necessary to further systematically study the stress evolution law of fold structure and the mechanism of rock burst induced by fold structure, to guide monitoring and prevention of rock bursts during mining in the fold structure area.
3. Theoretical analysis of stress evolution law in a UFS area of deep mine
3.1. Establishment of the mechanical model of the UFS
Affected by the geological environment, the occurrence of fold structures is complex and diverse. The UFS is the most common form of fold structure, which is formed by the strong extrusion and instability of the horizontal rock layer due to the force parallel to the surface. Therefore, this paper only discusses the stress evolution law of the UFS. Based on engineering practice, the theoretical model is appropriately simplified and the following assumptions are made: (1) In the ideal state, the fold does not deform along the axial direction, and the model is simplified to a plane strain problem; (2) During the process of fold deformation, the thickness of each rock layer has not changed; (3) The rock stratum is homogeneous and continuous, isotropic, close contact between rock strata.
The original state of the rock layer is in a horizontal distribution state. Under the extrusion of horizontal stress, the X axis and Z axis of the rock are deformed, and the Y axis direction of the rock changes little (). The stress field distribution after deformation is solved according to the plane strain problem (Liu Citation2019).
Before the rock stratum is formed by horizontal extrusion, its stratification is horizontal. The horizontal stress is uniformly distributed along the X axis, and its value is constant Cx; In the vertical direction, it is mainly affected by the weight of the rock stratum, and because the thickness of the rock stratum is smaller than the buried depth H, it is considered that the upper and lower surfaces are subjected to uniform stress. The stress in the rock layer can be regarded as constant D0. For simple calculation, the shear stress along the X axis and Z axis is zero, then:
where and
are the normal stress along the X axis and Z axis, respectively. The compressive stress is positive and the tensile stress is negative. The shear stress
is positive clockwise and negative counterclockwise.
After the rock stratum is squeezed to form a fold, its internal stress is no longer evenly distributed, but changes periodically along the X axis. To facilitate the calculation, a single fold is taken as the research object (), where the fold wavelength is 4S and the fold amplitude is 2 g.
For the plane strain problem, let the wrinkle stress function be Liu (Citation2019):
(1)
(1)
where A0 is the undetermined coefficient, D0 is the vertical stress in the rock layer (MPa), and Cx is the horizontal compressive stress (MPa).
EquationEquation (1)(1)
(1) satisfies the biharmonic equation:
(2)
(2)
Based on EquationEquation (1)(1)
(1) and Equation(2)
(2)
(2) , the stress distribution in the fold rock layer can be obtained:
(3)
(3)
The undetermined coefficient A0 and half-wavelength S in EquationEquation (3)(3)
(3) can be obtained by deformation and displacement analysis. For this purpose, geometric equations and physical equations are used:
(4)
(4)
(5)
(5)
where E is the elastic modulus of rock (GPa), is Poisson’s ratio. Substituting EquationEquations (3)
(3)
(3) into Equation(4)
(4)
(4) and Equation(5)
(5)
(5) and integrating them, the function of Z-axis displacement u concerning the X-axis is:
(6)
(6)
Let z = 0 in EquationEquation (6)(6)
(6) , and the shape equation of the center line of the fold rock stratum is obtained.
(7)
(7)
It can be seen that the center line of the fold rock stratum is similar to the cosine curve, which is undulating. At x = 2nS (n is 0, ±1, ±2, …), u = g.
so have:
(8)
(8)
The relationship between the undetermined coefficient A0 and the amplitude g can be signed by EquationEquation (8)(8)
(8) :
(9)
(9)
Substitute EquationEquations (9)(9)
(9) into Equation(3)
(3)
(3) can be obtained:
(10)
(10)
Based on the mechanical formula of UFS, it can be seen that along the X axis direction, the model at x = (nS) (n = 0, 1, 2, …) is located in the anticline axis of the fold, the model at x = (2/S + nS) is located in the syncline axis of the fold, and the model at x = (4/S + nS) is located in the limb area of the fold.
3.2. The stress evolution law under the change of different UFS elements
It can be known from EquationEquation (10)(10)
(10) that the distribution of tectonic stress affecting upright folds is mainly related to the initial length S (wavelength) of the fold rock layer and the amplitude g of folds. Based on the measured geological data of LW204 in Gao Jiabao Coal Mine, the rock elastic modulus E = 60GPa, Poisson’s ratio μ = 0.25, Cx = 37MPa, D0 = 25 MPa, variable fold wavelength S = 500–1000 m, amplitude g = 20–80m, can be used to calculate the evolution law of horizontal and vertical stress and shear stress in different regions of the UFS under the change of fold factors such as fold wavelength S and amplitude g, as shown in .
Figure 7. Evolution law of horizontal and vertical stress of rock strata in the axial region of upright fold anticline (a) Evolution law of horizontal stress under wavelength S change (b) evolution of vertical stress under wavelength S change (c) Evolution law of horizontal stress under amplitude g change (d) Evolution law of vertical stress under amplitude g change.

Figure 8. Evolution law of horizontal and vertical stress of rock strata in the axial region of upright fold synclinal (a) Evolution law of horizontal stress under wavelength S change (b) evolution of vertical stress under wavelength S change (c) Evolution law of horizontal stress under amplitude g change (d) Evolution law of vertical stress under amplitude g change.

Figure 9. Evolution law of rock shear stress in upright fold limb area: (a) under wavelength S change (b)under amplitude g change.

In , when the upright fold amplitude g is constant, the horizontal stress of the anticline axis area under different wavelengths S is symmetrical about the point (0,37), and the vertical stress is symmetrical about the point (0,25). In the direction of z > 0, the horizontal stress increases with the increase of S, from 14.28 MPa at S = 500m to 31.32 MPa at S = 1000m, with an increase of about 219% (at Z = 50m), and the growth rate gradually decreases exponentially. The vertical stress decreases with the increase of S, from 59.72 MPa at S = 500 m to 42.68 MPa at S = 1000m, with a decrease of about 28.5% (at Z = 50 m), and the decrease rate gradually decreases exponentially. In the region of Z < 0, the stress evolution law of surrounding rock is opposite to that in the region of Z > 0.
When the wavelength S of the upright fold is constant, the horizontal and vertical stresses in the anticlinal axis region are symmetrical about points (0,37) and (0,25) at different wave amplitudes, respectively. That is, in the direction of z > 0, the horizontal stress decreases with the increase of g value, from 33.14 MPa at g = 20m to 21.55 MPa at g = 80 m, with a decrease of about 35% (at Z = 50m), and the reduction rate decreases linearly. The vertical stress increases with the increase of g value, from 28.99 MPa at g = 20 m to 40.98 MPa at g = 80 m, with an increase of about 141% (at Z = 50 m), and the growth rate increases linearly; In the region of Z < 0, the stress evolution law of surrounding rock is opposite to that in the region of Z > 0.
From , it can be seen that the horizontal and vertical stress values of the upright fold syncline axis region under different wavelengths S and amplitude g are symmetrical to the anticline axis region value about the Z coordinate axis. Therefore, the stress evolution law of the upright fold syncline axis area under the influence of different fold elements is opposite to that of the anticline axis area.
From , it can be seen that the shear stress of an upright folded limb under different wavelength S and amplitude g values are symmetric about the Z coordinate axis, whether in the direction of z greater than 0 or less than 0, the shear stress decreases with the increase of wavelength S, from 43.54 MPa at S = 500 m to 18.99 MPa at S = 1000 m, with a decrease of about 56.4% (at Z = 50 m), and the reduction rate decreases exponentially; as the amplitude g increases, it increases from 9.49 MPa at g = 20 m to 37.98 MPa at g = 80 m, with an increase of about 400% (at Z = 50 m), and the growth rate increases linearly.
shows the evolution law of stress in different regions of UFS (data at Z = 50 m). It can be seen from the figure that the horizontal stress and vertical stress along the horizontal distribution of the UFS are similar to the periodic variation characteristics of the sine or cosine curve. From EquationEquation (10)(10)
(10) , it can be seen that the stress component expressions of the syncline area and the anticline area are symmetrical about the z coordinate. In the z > 0 area, the horizontal stress value of the roadway in the syncline area is greater than that in the anticline area (the stress concentration factor is 1.52). The degree of stress concentration in the syncline area is higher than that in the anticline area, indicating that the risk of rock burst in the mine roadway in the vertical structure syncline area is higher than that in the anticline area. The field statistical data in also reflect this phenomenon. The horizontal and vertical stress components in the limb region of an upright fold are mainly determined by the original vertical and horizontal stresses, but the overall horizontal and vertical stress values are relatively small compared to synclines and anticlines, and the shear stress effect is more obvious.
Figure 10. Stress evolution law in different regions of the UFS: (a) Evolution law of horizontal stress under wavelength S change (b) evolution of vertical stress under wavelength S change (c) Evolution law of horizontal stress under amplitude g change (d) Evolution law of vertical stress under amplitude g change.

Therefore, the stress state of each part of the upright fold can be divided into five zones (): zone I is tensile stress in the vertical direction, compressive stress in the horizontal direction, and mainly horizontal compressive stress; the vertical direction of the II zone is compressive stress, the horizontal direction is tensile stress, and the vertical compressive stress is the main stress. The vertical and horizontal directions of zone III are both compressive stress and subjected to strong shear stress. The stress state of zone IV is the same as that of zone II; the stress state of zone V is the same as that of zone I. The research results show that when the deep coal mine roadway engineering is arranged in the above area, it is prone to disasters such as rock burst, roadway roof fall, working face spalling rib, and surrounding rock shear failure (Wei et al. Citation2018; Wang et al. Citation2019b).
3.3. Numerical model establishment of UFS area
To study the distribution characteristics of the stress field in the UFS area of LW204 in Gao Jiabao Coal Mine, based on the measured geological data of the working face, after appropriate adjustment, FLAC3D software is used to construct the numerical model under the condition of UFS, as shown in . The size of the model is 1200 m × 500m × 220m (X, Y, Z). The parameters of the fold structure of the model are set as follows: wavelength S = 1000 m, amplitude g = 80m, and limit the displacement of the x axis, y axis, and bottom of the model. Apply a vertical load of 20 MPa on the top of the model, simulate a buried depth of 800 m, and apply a horizontal stress of 30 MPa on the side (theoretically calculated stress concentration factor 1.52).
The numerical model adopts the Mohr–Coulomb strength failure criterion, and the physical and mechanical parameters of the model coal and rock layers are determined based on the measured results and appropriate reductions (Zhang and Einstein Citation2004; Wang et al. Citation2011), as shown in .
Table 2. Mechanical parameters of model coal and rock strata.
The gestation, development, and final formation of fold structures are fundamentally due to the continuous evolution of the tectonic stress field in an unstable state over time and space. Under the action of self-weight stress and horizontal tectonic stress, through numerical simulation analysis, the vertical stress and horizontal stress of the model show different states. The distribution of the original rock stress field of the fold structure has obvious regional spatial distribution. Under the action of horizontal tectonic stress, the horizontal stress of the LW204 increases sharply at the syncline axis, and the horizontal stress peak in the coal seam area of the syncline axis is about 48.65 MPa (in ). Based on EquationEquation (10)(10)
(10) , combined with the geological data of LW204, the horizontal stress peak in the upright fold syncline axis is 44.57 MPa (, S = 1000 m, g = 80 m). The difference between the simulation results and the theoretical calculation results is 4.08 MPa, and the error is about 8.4%. Considering the size of the model, it can be concluded that the simulation results are consistent with the theoretical calculation results.
Under the action of horizontal tectonic stress, the horizontal stress peak value of the coal seam area in the oblique axis of the LW204 working face is 48.65 MPa, and the stress concentration coefficient is about 1.95. The surrounding rock of the working face roadway has been affected by high static load stress, and the stress field of the surrounding rock of the roadway is in a dynamic equilibrium state. When the dynamic equilibrium is affected by external stress, the roadway is prone to instability and failure.
4. Mechanism of rock burst in a UFS area of deep mine
4.1. Stress evolution characteristics of surrounding rock in coal seam mining in the UFS area
To study the stress evolution law of LW204 during mining in the UFS area, a numerical model shown in is established. The mining direction of the working face is consistent with the actual project. It advances from the fold limb to the syncline axis, and the mining length is 25 m each time. A monitoring line is set up on the roof along the strike of the fold structure to observe the stress evolution of the working face during mining when the working face is gradually approaching and away from the syncline axis.
is the evolution law of horizontal and vertical stress during mining in the area affected by the syncline structure. It can be seen from the diagram that as the LW204 is gradually approaching the syncline axis, the horizontal stress and vertical stress show different degrees of growth. The horizontal stress and vertical stress concentration coefficients increased from 3.02 and 2.65 at 260 m from the syncline axis to 3.64 and 3.48 at the syncline axis, with growth rates of 121% and 131%, respectively. As the mining of the LW204 gradually approaches the syncline axis, the influence range of the advanced support pressure of the working face gradually expands, and the influence range of the advanced support pressure reaches the maximum when the working face is mined to the syncline axis area. As the mining face gradually moves away from the syncline axis, the horizontal and vertical stress concentration coefficients decrease from 3.64 and 3.48 at the syncline axis to 3.18 and 2.80 at 190 m from the syncline axis, with a reduced rate of 12.6% and 19.5%, respectively. As the working face gradually moves away from the synclinal axis, the influence range of the advanced bearing pressure on the working face gradually decreases.
Figure 14. Mining stress evolution characteristics of the working face in syncline structure affected area: (a) horizontal stress (b) vertical stress (c) Stress concentration factor.

The simulation results show that with the mining of the working face gradually approaching and away from the syncline axis, the horizontal and vertical stress concentration coefficients increase first and then decrease first. This is because the stress of coal and rock mass is in equilibrium before it is affected by mining disturbance. When the working face is mined, the equilibrium state of coal and rock mass around the roadway will be broken, and the weight of the overlying strata in the goaf will be transferred to the fulcrum around the goaf. The stress concentration area in the coal seam in front of the working face will cause energy accumulation. At this time, under the influence of synclinal tectonic stress superposition, the stress concentration area becomes larger and the stress peak becomes higher, and the surrounding rock of the working face is in a high static load state. If the stress level in this area exceeds the strength limit of coal and rock mass, it will cause damage and induce rock bursts.
4.2. Microseismic event activity law during mining of working face in the UFS area
From August 20, 2019, to September 20, 2019, a total of 120 m was mined in LW204. According to the occurrence characteristics of the UFS in the working face, the whole mining area can be divided into two stages. Stage I: from August 20 to September 5, 2019, the working face is far away from the syncline axis area; Stage II: From September 06 to September 20, 2019, the mining of the working face is gradually approaching the syncline axis, which is in the mining stage of the area affected by the UFS.
According to the statistical analysis of microseismic events in LW204 (see ), in stage I, the average daily energy of microseismic events is about 3.44 × 105J, and the average daily frequency is about 5.9. The average daily energy of stage II microseismic events is about 16.7 × 105J, and the average daily frequency is about 10.7. The average daily energy and frequency of microseismic events in stage II were 385.5% and 81.4% higher than those in stage I, respectively. The microseismic events showed that with the mining of LW204 gradually approaching the syncline axis, the microseismic activity of the working face increased significantly, and the dangerous mining tremors (microseismic energy > 1 × 106J) were distributed along the haulage roadway. From , it can be seen that the strong microseismic events in the LW204 are mainly distributed in the 21.06 m thick kern stone layer, indicating that the fracture of thick and hard rock layers will lead to a large amount of elastic energy release, thereby causing dynamic load disturbance to the working face tunnel system.
Figure 15. Activity characteristics of microseismic events: (a) Energy and frequency diagram of microseismic events (b) Microseismic event distribution plan (c) Microseismic event profile positioning map.

The distribution characteristics of microseismic events show that the microseismic activity of the working face increases as the working face gradually approaches the syncline axis. And as the working face mining gradually approaches the syncline axis area, the stability of the working face roof gradually decreases, the roofing activity gradually increases, and the dynamic load stress disturbance caused by the roof fracture increases, the risk of rock burst in the working face is enhanced.
4.3. Mechanism of mining rock burst in a UFS area of deep mine
Due to the mining of the working face, the side abutment pressure of the surrounding rock of the roadway rises. Assuming that the vertical stress is constant, the horizontal stress needs to consider the influence of the pressure coefficient λ on the original basis. Based on EquationEquation (10)(10)
(10) , the stress distribution of the surrounding rock of the syncline axis roadway is solved, and the vertical stress q1 and horizontal stress q2 of the syncline axis roadway affected by the abutment pressure during the mining of the working face can be expressed as:
(11)
(11)
The polar coordinate expression of the stress distribution of the surrounding rock of the inclined shaft roadway after the mining of the working face is (Jaeger Citation1979):
(12)
(12)
where σρ is the radial normal stress in the direction of ρ (MPa); σѳ is the tangential normal stress of the roadway along the ѳ direction (MPa); τρѳ is the shear stress of the roadway (MPa); r0 is the width of roadway (m); ρ is the polar diameter in the polar coordinate system; ѳ is the polar angle in the polar coordinate system (°).
According to the relevant research results (Hearn Citation1997), the conversion relationship between the maximum and minimum principal stress of roadway surrounding rock and the radial, circumferential, and shear stress of surrounding rock under polar coordinate conditions can be expressed as:
(13)
(13)
Based on the rock failure criterion in the coordinate system of the Mohr–Coulomb criterion (Singh et al. Citation2011), the maximum and minimum principal stresses of rock failure can be expressed as:
(14)
(14)
where is the internal friction angle of rock (°); c is rock cohesion (MPa). It can be judged whether the coal and rock layer of the syncline axis roadway is damaged.
The dynamic load stress disturbance caused by the energy released by roof breaking is also an important influencing factor of rock burst disasters induced by working faces. The elastic energy released after the fracture of the low-lying strata will be directly loaded on the coal seam, while the elastic energy released when the high-lying roof is broken will propagate in the coal and rock medium in the form of vibration waves, which will cause the particle vibration of the coal and rock medium, and even induce rock burst accidents.
Since the energy of the elastic energy vibration wave will gradually attenuate during the propagation of the coal–rock medium (Wang et al. Citation2019a), the relationship between the dynamic load and the propagation distance of the elastic energy vibration wave can be expressed as:
(15)
(15)
where ρ0 is the density of the rock layer (kg.m−3); Ud0 is the mine earthquake energy (J), which can be monitored using microseismic monitoring equipment; Ld is the propagation distance of the vibration wave (m); η is the attenuation index, which can be obtained based on a statistical analysis of mine microseismic data (Zhou et al. Citation2020).
Because the damage degree of coal and rock layer caused by the shear wave is greater than that of a longitudinal wave, and the energy released by the shear wave is greater when the thick and hard roof is broken, the deformation and failure induced by transverse wave load stress will be more severe.
When the dynamic and static loads are superimposed, the ways of inducing coal and rock layer failure include: the maximum principal stress increases and the minimum principal stress decreases, or the maximum principal stress increases and the minimum principal stress decreases at the same time, so the Mohr-Coulomb failure criterion will change. when the static load of surrounding rock and the dynamic load of roof fracture are superimposed, taking the single principal stress variable as an example, the principal stress difference can be expressed as:
(16)
(16)
Establish the roadway rock burst hazard index I0:
(17)
(17)
According to the I0 index, it can be judged whether the surrounding rock system of the roadway will be destabilized, to judge the risk of rock burst in the syncline axis roadway.
Based on the measured geological data of LW204, combined with numerical simulation and theoretical calculation results, taken σ0=44.57 MPa, σ1=λσ0MPa, λ = 2.5(numerical simulation results show that the stress concentration factor in the syncline structure influence area is greater than 2.5), σ3 = 29.43 MPa, c = 8MPa, η = 0.7, Udo=4.60 × 106J (microseismic energy inducing rock burst accident in LW204 roadway), ld=15m, Cs=4500m/s, ρ0=2500kg.m−3, According to EquationEq. (17)
(17)
(17) , it can be calculated: I0=111.43/105.64 = 1.05 > 1. It is shown that when the mining position of LW204 is close to the syncline axis, the high static load stress stack strengthens the dynamic load disturbance, reaching the stress condition for the instability and failure of the surrounding rock of the roadway, thus inducing the rock burst accident on September 21, 2019.
In summary, the mechanism of rock burst in the UFS area of the deep mine can be described as that the surrounding rock system of roadway in the fold structure area of the working face is in the dynamic equilibrium state of high static load stress under the action of self-weight stress, tectonic stress and advance support pressure of working face. In , when the dynamic load released by the thick and hard roof of the working face is superimposed with the high static load, if it exceeds the critical value of dynamic instability of the roadway surrounding the rock system, it is easy to induce rock burst disaster (He et al. Citation2017).
5. Practice rock burst control in a UFS area of a deep mine
5.1. Prevention ideas of rock burst
Based on the above research results, it can be seen that as the mining of the working face gradually approaches the syncline axis, the influence of the stress level of the surrounding rock system of the roadway on the stability of the coal wall gradually increases, and the activity of the roof and floor strata affected by the tectonic horizontal stress increases (the energy and frequency of microseismic events increase significantly), and the rock burst risk of the working face gradually increases. The main reason for the rock burst disaster in the roadway of the working face in the fold structure area is that the dynamic load released by the breaking of the roof and floor strata and the high static load superimposed on the surrounding rock of the roadway are greater than the minimum stress value that the surrounding rock system can resist the instability and failure, which leads to the instability and failure of the surrounding rock of the roadway. Therefore, the key point of preventing and controlling this kind of rock burst is to effectively release the elastic energy accumulated in the roof structure of the fold structure area, destroy the integrity of the rock stratum, and reduce the dynamic load disturbance caused by the roof fracture (Wang et al. Citation2013; Lu et al. Citation2021). The elastic energy accumulated in the coal seam is released to reduce the static load stress concentration of the coal seam (Xue et al. Citation2022). In addition, strengthening the support strength of the surrounding rock system of the working face can effectively improve the ability of the surrounding rock to resist the impact, and reducing the mining speed of the working face can effectively weaken the activity of the overlying rock.
5.2. Rock burst prevention scheme
Combined with the geological characteristics of the UFS area of the LW204, based on reducing the mining speed of the working face and increasing the support strength of the roadway, the blasting pressure relief scheme of the roadway roof and coal seam of the working face is designed to destroy the integrity of the coal seam and the thick and hard roof, and the induced accumulation of elastic energy is released quickly. The arrangement of pressure relief blasting holes is shown in , and the blasting parameters are shown in .
Table 3. Coal seams and roofs pressure relief parameters of working face.
5.3. Control effect test of rock burst
5.3.1. Comparative analysis of microseismic data
When the mining of LW204 gradually approached the syncline axis area (from August 20 to September 20, 2019), the frequency and energy of strong mining tremors events increased significantly. In October 2019, the working face carried out multiple rounds of roof and coal seam blasting pressure relief projects in the mining roadway.
The paper selects microseismic data from August 20 to September 20, 2019 (before pressure relief), September 20 to October 20, 2019 (during pressure relief), October 20 to November 20, 2019 (mining to pressure relief area) for analysis, as shown in .
Figure 18. Analysis chart of microseismic monitoring data: (a) Energy and frequency diagram of microseismic events (b) Daily average microseismic event energy and frequency diagram.

From September 20 to October 20, the average daily released energy of LW204 decreased from 96.8 × 104 J from August 20 to September 20 to 52.9 × 104 J, with a decrease of about 45.37%. From October 20 to November 20, the average daily released energy of LW204 decreased from 52.9 × 104 J from September 20 to October 20 to 43.1 × 104J, with a decrease of about 18.53%. The daily average microseismic frequency of LW204 from September 20 to October 20 increased from 8.2 from August 20 to September 20 to 26.9, with an increase of about 228.05%, indicating that the roofing activity began to be dominated by small energy microseismic events. The daily average microseismic frequency of LW204 from October 20 to November 20 decreased from 26.9 from September 20 to October 20 to 24.1, with a decrease of about 10.41%.
The daily average microseismic event energy of LW204 before, during, and after pressure relief, in the upright fold syncline structure area decreased significantly, and the frequency increased significantly. The overall microseismic data showed a stable release state of high frequency and low energy, indicating that the stress level of roadway surrounding rock in the fold structure area was effectively reduced after pressure relief (Cao et al. Citation2016).
5.3.2. Comparative analysis of periodic weighting of working face
The average periodic weighting step distance is about 25.5 m (August 10–September 16) when the mining of the LW204 is gradually approaching the syncline axis. The average periodic weighting step distance during the pressure relief period of the working face is about 19.5 m (September 30–October 24). The average periodic weighting step distance after the pressure relief of the working face is about 16.9 m (October 28–December 12). The periodic weighting step distance of the working face during and after the pressure relief is reduced by 23.5% and 33.7% respectively compared with that before the pressure relief, and the value of the periodic weighting step distance decreases significantly (). It shows that the deep hole blasting of the roof achieves the expected purpose, destroys the integrity of the roof, reduces the strength of the roof, and the pressure relief effect is good (Konicek et al. Citation2013).
Figure 19. Working face pressure analysis: (a) Variation diagram of periodic weighting step of working face, (b) Working face hydraulic support resistance program.

At the same time, it can be found from the hydraulic support resistance cloud map during the mining of LW204 (). Before the rock burst accident on September 21, the support resistance value of the working face was generally high, most of which were greater than 30 MPa. After the roof and coal seam blasting, the support resistance value of the working face decreased as a whole, most of the support resistance values were less than 30 MPa, which reflected the good pressure relief effect of LW204.
6. Conclusions
In underground burst-prone coal mines, the fold structure has become the critical factor that induced rock bursts potential. The types of UFS were first classified in this work. On this basis, the rock burst mechanism and control factors were systematically investigated. The following conclusions can be drawn:
According to the occurrence of the axial plane and the two limbs of the fold structure, the folds are divided into five forms: upright fold, overturned fold, recumbent fold, convolute fold, and inclined fold. The accident statistics show that the occurrence of rock bursts in the fold structure area has obvious regional characteristics.
Based on the mechanical model of the UFS area, the stress evolution law of the structural area under different fold wavelengths S and amplitude g is solved. Under different fold elements, the horizontal stress and vertical stress along the transverse distribution of the UFS show periodic variation characteristics similar to sine or cosine curves. The stress state of each part of the upright fold area is divided into five areas, and the principal stress form of each area is clarified.
Based on the principle of rock burst induced by dynamic and static load superposition, the rock burst risk index I0 is proposed to determine whether the roadway is unstable or not, and the mechanism of rock burst induced by mining in the UFS area of deep mine is expounded.
The prevention and control idea of rock burst in the working face of the fold structure area is clarified, and the prevention and control scheme of roof and coal seam blasting pressure relief is formulated. The monitoring data show that the prevention and control scheme can effectively reduce the risk of rock bursts in the working face. It has a guiding significance for the prevention and control of rock burst in working face under similar conditions.
Availability of data
Not applicable.
Code availability
Not applicable.
Disclosure statement
The authors declared that they have no conflicts of interest in this work.
Additional information
Funding
References
- Akdag S, Karakus M, Nguyen GD, Taheri A, Bruning T. 2021. Evaluation of the propensity of strain burst in brittle granite based on post-peak energy analysis. Underground Space. 6(1):1–11.
- Cai W, Bai X, Si G, Cao W, Gong S, Dou L. 2020. A monitoring investigation into rock burst mechanism based on the coupled theory of static and dynamic stresses. Rock Mech Rock Eng. 53(12):5451–5471.
- Cao A-y, Dou L-m, Wang C-b, Yao X-x, Dong J-y, Gu Y. 2016. Microseismic precursory characteristics of rock burst hazard in mining areas near a large residual coal pillar: a case study from Xuzhuang Coal Mine, Xuzhou, China. Rock Mech Rock Eng. 49(11):4407–4422.
- Cao A, Dou L, Cai W, Gong S, Liu S, Jing G. 2015. Case study of seismic hazard assessment in underground coal mining using passive tomography. Int J Rock Mech Min Sci. 78:1–9.
- Cao A, Jing G, Dou L, Wu Y, Zhang C. 2018. Statistical analysis of distribution patterns of coal seams in fold zones in Northwest China. Int J Min Sci Technol. 28(5):819–828.
- Cao A, Liu Y, Jiang S, Hao Q, Peng Y, Bai X, Yang X. 2021. Numerical investigation on influence of two combined faults and its structure features on rock burst mechanism. Minerals. 11(12):1438.
- Chen F, Cao A, Dou L, Jing G. 2019. A quantitative evaluation method of coal burst hazard based on zone division and an analytic hierarchy process: a case study on Yanbei coal mine, Gansu Province, China. Geosci J. 23(5):833–848.
- Chen G, Guo b, Dou L. 2010. Discussion on relationship between mining layout of coal mining face and rockburst in geological fold Area. Coal Sci Technol. 10:27–30.
- Chen G, Dou L, Wang Z. 2011. The study on prevention of rockburst when mining in folding structure areas, 2011 Asia–Pacific Power and Energy Engineering Conference, p. 1–4.
- Cheng X, Qiao W, Dou L, He H, Ju W, Zhang J, Song S, Cui H, Fang H. 2023. In-situ stress field inversion and its impact on mining-induced seismicity. Geomat Nat Hazards Risk. 14(1):176–195.
- DeCelles PG, Coogan JC. 2006. Regional structure and kinematic history of the Sevier fold-and-thrust belt, Central Utah. GSA Bull. 118(7–8):841–864.
- Foster DA, Gray DR. 2000. Evolution and structure of the Lachlan fold belt (Orogen) of Eastern Australia. Annu Rev Earth Planet Sci. 28(1):47–80.
- Ghosh SK, Sengupta S, Dasgupta S. 2002. Tectonic deformation of soft-sediment convolute folds. J Struct Geol. 24(5):913–923.
- Guo W, Cao A, Hu Y, Xue C, Liu Y, Lv D. 2022. Stress distribution and rockburst characteristics of roadway group under the influence of fault and fold structures: a case study. Geomat Nat Hazards Risk. 13(1):736–761.
- He J, Dou L, Gong S, Li J, Ma Z. 2017. Rock burst assessment and prediction by dynamic and static stress analysis based on micro-seismic monitoring. Int J Rock Mech Min Sci. 93:46–53.
- Hearn EJ. 1997. Chapter 14: complex strain and the elastic constants. In: Hearn EJ, editor. Mechanics of materials 1. 3rd ed. Oxford: Butterworth-Heinemann; p. 361–400.
- Jaeger C. 1979. Rock mechanics and engineering. Cambridge: Cambridge University Press.
- Jia T, Feng Z, Wei G, Ju Y. 2018. Shear deformation of fold structures in coal measure strata and coal–gas outbursts: constraint and mechanism. Energy Explor Exploit. 36(2):185–203.
- Konicek P, Soucek K, Stas L, Singh R. 2013. Long-hole destress blasting for rockburst control during deep underground coal mining. Int J Rock Mech Min Sci. 61:141–153.
- Lee SM, Park BS, Lee SW. 2004. Analysis of rockbursts that have occurred in a waterway tunnel in Korea. Int J Rock Mech Min Sci. 41:911–916.
- Liu J. 2019. Stress field of fold structure and its evolution. J Geomech. 25(3):341–348.
- Lovchikov AV. 1997. Mine tectonic shocks in Russia: statistics and analysis. J Min Sci. 33(2):120–128.
- Lu A, Dou L, Bai J, Chai Y, Zhou K, Kan J, Cao J, Song S. 2021. Mechanism of hard-roof rock burst control by the deep-hole blasting: numerical study based on particle flow. Shock Vib. 2021:1–14.
- Lu C, Zhang X, Xiao Z, Wang C, Wang B, Zhou T, Li H, He Z. 2020. Study on controlling law of fold structure on evolution of mining stress in deep mines. Coal Sci Technol. 02:44–50.
- Maleki H, Lawson H. 2017. Analysis of geomechanical factors affecting rock bursts in sedimentary rock formations. Proc Eng. 191:82–88.
- Pan j, Shuwen L, Shaohong, Q. Zihan. 2018. Rock burst start-up mechanism of peripheral roadway in double entry layout workface. J Min Saf Eng. 35(2):291–299.
- Sanderson DJ. 1979. The transition from upright to recumbent folding in the Variscan fold belt of southwest England: a model based on the kinematics of simple shear. J Struct Geol. 1(3):171–180.
- Shirani Faradonbeh R, Taheri A, Karakus M. 2022. The propensity of the over-stressed rock masses to different failure mechanisms based on a hybrid probabilistic approach. Tunnelling Underground Space Technol. 119:104214.
- Singh M, Raj A, Singh B. 2011. Modified Mohr–Coulomb criterion for non-linear triaxial and polyaxial strength of intact rocks. Int J Rock Mech Min Sci. 48(4):546–555.
- Singh SP. 1989. Classification of mine workings according to their rockburst proneness. Min Sci Technol. 8(3):253–262.
- Starfield AM, Cundall PA. 1988. Towards a methodology for rock mechanics modelling. Int J Rock Mech Min Sci Geomech Abstr. 25(3):99–106.
- Stewart RA, Reimold WU, Charlesworth EG, Ortlepp WD. 2001. The nature of a deformation zone and fault rock related to a recent rockburst at Western deep levels gold mine, Witwatersrand Basin, South Africa. Tectonophysics. 337(3–4):173–190.
- Ullah B, Kamran M, Rui Y. 2022. Predictive modeling of short-term rockburst for the stability of subsurface structures using machine learning approaches: t-SNE, K-means clustering and XGBoost. Mathematics. 10(3):449.
- Van Dyke MA, Su WH, Wickline J. 2018. Evaluation of seismic potential in a longwall mine with massive sandstone roof under deep overburden. Int J Min Sci Technol. 28(1):115–119.
- Wang F, Tu S, Yuan Y, Feng Y, Chen F, Tu H. 2013. Deep-hole pre-split blasting mechanism and its application for controlled roof caving in shallow depth seams. Int J Rock Mech Min Sci. 64:112–121.
- Wang G-f, Gong S-y, Dou L-m, Li G, Cai W, Fan C-j. 2019a. A Novel Experimental Technique to Simulate Shock Behaviour and Bursting Failure of roadways. Shock Vib. 2019:1–13.
- Wang G, Gong S, Dou L, Cai W, Yuan X, Fan C. 2019b. Rockburst mechanism and control in coal seam with both syncline and hard strata. Saf Sci. 115:320–328.
- Wang G, Gong S, Dou L, Wang H, Cai W, Cao A. 2018. Rockburst characteristics in syncline regions and microseismic precursors based on energy density clouds. Tunnell Underground Space Technol. 81:83–93.
- Wang H, Deng D, Jiang C, Shi R, Yan X. 2020. Study on evolution characteristics of uneven stress field in mining-induced fold tectonic area. Coal Sci Technol. 02:59–69.
- Wang X, Zhao Y, Lin X. 2011. Determination of mechanical parameters for jointed rock masses. J Rock Mech Geotech Eng. 3:398–406.
- Wei C, Zhang C, Canbulat I, Cao A, Dou L. 2018. Evaluation of current coal burst control techniques and development of a coal burst management framework. Tunnell Underground Space Technol. 81:129–143.
- Xue C, Cao A, Guo W, Liu Y, Wang S, Dong J, Gu Y. 2022. Mechanism and energy evolution characteristics of coal burst in mining thick, deep, and large inclined coal seams: a case study from a Chinese coal mine. Geofluids. 2022:1–18.
- Zhang G, Guo J, Xu B, Xu L, Dai Z, Yin S, Soltanian MR. 2021. Quantitative analysis and evaluation of coal mine geological structures based on fractal theory. Energies. 14(7):1925.
- Zhang K, Wang L, Cheng Y, Li W, Kan J, Tu Q, Jiang J. 2020. Geological control of fold structure on gas occurrence and its implication for coalbed gas outburst: case study in the Qinan Coal Mine, Huaibei Coalfield, China. Nat Resour Res. 29(2):1375–1395.
- Zhang L, Einstein HH. 2004. Using RQD to estimate the deformation modulus of rock masses. Int J Rock Mech Min Sci. 41(2):337–341.
- Zhou K, Dou L, Gong S, Li J, Zhang J, Cao J. 2020. Study of rock burst risk evolution in front of deep longwall panel based on passive seismic velocity tomography. Geofluids. 2020:1–14.
- Zhou Z, Ullah B, Rui Y, Cai X, Lu J. 2023. Predicting the failure of different rocks subjected to freeze–thaw weathering using critical slowing down theory on acoustic emission characteristics. Eng Geol. 316:107059.