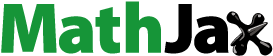
Abstract
The traditional index to determine the width of the stopping coal pillar (WSCP) is generally only the front abutment pressure, but the direction of the principal stress will deflect due to the mining action, which brings significant challenges to controlling the surrounding rock. Based on theoretical calculation and numerical simulation, we studied the deflection law of principal stress under mining action, quantified the bearing capacity of roadway surrounding rock, and determined WSCP. The results show that: (1) With the deflection of the principal stress, the distribution of the surrounding rock plastic zone also rotates; (2) and repeated mining dominate and aggravate the deflection angle and range of the principal stress in front of the working face, respectively. When
is close to 1, the deflection of principal stress should be paid attention to in determining WSCP; (3) The anchorage composite bearing structure (ACBS) provides a scientific basis for quantifying the bearing capacity of surrounding rock. WSCP of the lower coal seam is determined to be 60–75 m, and the corresponding principal stress deflection is about 135°. The control of the surrounding rock in the diagonal direction where the maximum principal stress is concentrated should be paid attention to.
1. Introduction
The main roadway typically has a long lifespan; hence, its surrounding rock must be stable. In high-pressure coal mines, WSCP is generally set to be more than 100 m, so the main roadway is outside the influence range of the front abutment pressure. Therefore, controlling the surrounding rock of the main roadway generally does not need to consider the interference of the mining stress. However, for the coal mine with low ground pressure, WSCP can be shortened to improve the resource recovery rate, and the main roadway can be located within the influence range of the front abutment pressure. Mining action will cause deflection of the direction of the maximum principal stress in front of the working face. In particular, the mining action will be more intense with repeated mining of close-distance coal seams. In this case, the determination of WSCP and the control of the roadway surrounding rock should not only consider the bearing pressure, but also pay attention to the magnitude and direction of the principal stress. Then we can clarify the deformation characteristics of surrounding rock and control surrounding rock pertinently.
The formation and evolution of the plastic zone of roadway surrounding rock have always been a hot issue. It is of great significance to master the distribution characteristics of the plastic zone of surrounding rock. Kastner (Citation1980) derived the analytical solution of the distribution of the plastic zone of the circular roadway’s surrounding rock under constant pressure, which is widely used in Engineering. Jiang et al. (Citation2001) predicted the development process of the plastic zone of the surrounding rock of the soft rock tunnel and proposed a judgement method for assessing the degree of rock failure. Li et al. (Citation2021) substituted the stress in the elastic zone into the plastic condition and solved the implicit equation of the boundary of the plastic zone of the surrounding rock of the circular roadway under unequal pressure. Based on Mohr-Coulomb strength criterion, some scholars solved the approximate solution of the non-axisymmetric elastoplastic problem using the complex variable function method (Detournay Citation1986; Tokar Citation1990). Hou et al. (Citation2014) solved the elasto-plastic problem of the axisymmetric circular roadway under unequal two-dimensional pressure by perturbation, and gave the perturbation analytical expression of the elastic-plastic boundary. Based on the elastic brittle plastic model, some scholars have solved the analytical solution of the plastic zone of surrounding rock (Dong and Gao Citation2019; Sharan Citation2005; Park & Kim Citation2006). Currently, the solution of the plastic zone distribution of surrounding rock is still mostly approximate, especially for rectangular roadway, which still needs further research.
Under the action of mining, the direction of the principal stress will deflect obviously, which brings significant challenges to controlling the surrounding rock of the roadway. Zuo et al. (Citation2019) studied that under the influence of mining, the stress field of the roadway will become relatively complex. The complexity is not only reflected in the increase or decrease of the stress field, but also the direction of the stress field. Li et al. (Citation2020) and Yu et al. (Citation2020) studied the asymmetric deformation and failure of the surrounding rock of the roadway due to the influence of the deflection principal stress due to the mining activities of the reserved roadway in the double lane arrangement, and puts forward the control method of the surrounding rock. Li (Citation2020) studied the butterfly failure mechanism and control technology of surrounding rock after the magnitude and direction of the principal stress on the roadway changed obviously due to the change of the coal pillar. Wang et al. (Citation2020a, Citation2020b) studied the influence of the rotation angle of mining stress on the stability of surrounding rock, and believed that the greater the rotation angle of mining stress, the worse the stability of surrounding rock. Wang et al. (Citation2018) established an ultrasonic model to accurately predict stress distribution, stress rotation, and ultrasonic velocity evolution. However, there are few studies on the deflection law of the principal stress in front of the working face, especially for the close-distance coal seams.
Scholars at home and abroad have rich research results on the theory and technology of roadway support. Kang (Citation2016) put forward the high prestressed robust bolt support technology, which has a good application effect in the field. (He et al. Citation2007; He Citation2014) proposed the roadway bolt coupling support technology and the constant resistance large deformation anchor cable, which has a good control effect on the soft rock roadway. Ma et al. (Citation2013) and Nemcik et al. (Citation2014) established a numerical model of the full-length anchor bolt under tension, and the predicted results are in good agreement. Khalymendyk & Baryshnikov (Citation2018) believe that the coordinated deformation of the support surrounding rock system and the particularity of the surrounding rock deformation mechanism should be considered in the roadway support design. Tao et al. (Citation2018) studied the failure characteristics of different steeply inclined layered soft rock roadways under the action of high static stress and horizontal tectonic stress, providing a scientific basis for roadway surrounding rock control under similar geological conditions. Cao et al. (Citation2017) conducted case studies on the failure mechanism and stability control technology of deep roadway under high-level in-situ stress, and achieved good engineering benefits. Most of the above studies are aimed at the surrounding rock control of deep mine large deformation roadway. Still, the quantification of the bearing capacity of surrounding rock has not been solved.
To sum up, the research on deformation characteristics and control technology of roadway surrounding rock mainly aims at vertical and horizontal pressure. Based on the close-distance coal seams of YZS coal mine, this study clarified the deflection law of the principal stress in front of the working face under the mining action, studied the bearing capacity of the surrounding rock of the main roadway, determined WSCP, analyzed the deformation characteristics of the surrounding rock of the main roadway, and proposed the surrounding rock control technology.
2. Project overview
2.1. Engineering background
YZS Coal Mine is located in Datong Coalfield, Shanxi Province, China, and has low gas content and simple hydrogeological conditions. The selected upper and lower coal seams were the No. 1 and No. 2 coal seams of the YZS coal mine and had a thickness of 7.5 m and 5.5 m, respectively. (Note: the original No. 4 is the upper coal seam, and No. 3 is the lower coal seam. For more logical expression, it is named No. 1 and No. 2 and will not affect the research results). The average spacing of coal seams is 25 m, and the buried depth of No.1 coal seam is about 400 m. We used the downward mining and fully mechanized top coal caving longwall mining method as well as the roof span management method. shows the rock stratum histogram.
The 1216 working face had stopped mining, and its WSCP was about 110 m. The 2216 Working face will enter the final mining stage. It is necessary to determine a proper stopping position. The striking profile of the working face is shown in .
The main roadway has a rectangular section. Since the roadway was excavated, the surrounding rock has no deformation, and the supporting structure and concrete surface spraying layer are complete, indicating that the bearing capacity of the surrounding rock has not been fully utilized. To further improve the mining rate of coal resources, it is necessary to determine WSCP in the 2216 working face and allow the main roadway to be within the influence range of the front abutment pressure.
2.2. Distribution of surrounding rock plastic zone
After excavating the roadway, the stress around the surrounding rock will be redistributed. Under the action of partial stress, the surrounding rock will form a plastic zone from the surface to the depth plastic zone. A rectangular roadway is generally simplified as a circumscribed circle to solve the distribution of plastic zone. Kastner solved the distribution of plastic zone of surrounding rock of circular roadway under constant pressure. However, due to the mining disturbance, the stress field in front of the working face will show an apparent unequal compression, and the direction of the principal stress will also deflect due to the extrusion movement of the rock stratum. For the solution of the plastic zone of the circular roadway under the condition of unequal compression and accompanied by the deflection of the principal stress, it can be assumed that the surrounding rock is still in an elastic state after excavation, and the distribution of the plastic zone can be solved by bringing the surrounding rock stress into the plastic Mohr-Coulomb criterion (Kastner Citation1980; Li et al. Citation2021).
The elastic stress solution of the axisymmetric in is:
(1)
(1)
(2)
(2)
(3)
(3)
Taking formulas (1–3) into (4–6), we use MATLAB software to calculate, which can draw the distribution of the surrounding rock plastic zone with the change of side pressure coefficient and the deflection of principal stress, as shown in .
(4)
(4)
(5)
(5)
(6)
(6)
where
is radial stress, MPa;
is Tangential stress, MPa;
is side pressure coefficient;
is crustal stress, MPa;
is roadway radius, m;
is support stress, MPa;
is deflection angle of principal stress;
is shear stress, MPa;
and
are maximum and minimum principal stress.
According to , it can be analyzed that:
When
=1.0, the distribution of plastic zone of surrounding rock is circular, and there is no change with the deflection of principal stress;
For
=1.3, when the principal stress is not deflected, the plastic zone of the surrounding rock is elliptical with two large sides; When the principal stress rotates by 45°, the elliptical distribution rotates by 45°, which shows that the plastic zone in the upper left and lower right corners of the roadway surrounding rock is large; When the principal stress rotates by 135°, the elliptical distribution also rotates by 135°, which shows that the plastic zone at the lower left and upper right corner of the surrounding rock of the roadway is large;
When
=0.7, the distribution of plastic zone of roadway surrounding rock is opposite to that when
=1.3.
For the Rectangular roadway in unequal compression and with the deflection of the principal stress, if the shoulder angle of the roof is located at the position where the range of the plastic zone is the largest, it will bring potential danger to the stability of the surrounding rock of the roadway.
Therefore, mastering the deflection law of the principal stress in front of the working face under mining action, assessing the bearing capacity of the surrounding rock, and mastering the deformation characteristics of the surrounding rock of the main roadway are the premises of shortening WSCP, improving the mining rate, and ensuring the stability of the surrounding rock of the main roadway.
3. Study on deflection law of principal stress induced by mining
3.1. Model establishment and scheme introduction
Using numerical simulation to study engineering problems is a common method (Wang et al. Citation2016; He et al. Citation2022). In this section, FLAC3D numerical simulation software is used to study the deflection law of principal stress before and after repeated mining of close-distance coal seams. According to the geological conditions, the model size was 600 m (X) × 140 m (Y) ×300 m (Z). The X-axis represented the mining direction of the working face. The horizontal and bottom boundary velocities of the model are limited to 0. The upper boundary is the stress boundary condition. According to the measured in-situ stress, the measured side pressure coefficient was 1.2. The mechanical parameters of numerical simulation are shown in .
Table 1. Mechanical parameters of coal and rock mass in calculation model.
According to the single factor analysis method, the deflection law of the principal stress in front of the working face is studied under different side pressure coefficient, different burial depth (taking the roof of No. 1 coal seam as reference) and different coal seams spacing. Scheme 3 is the actual geological condition. The schemes are shown in .
Table 2. Schemes of numerical simulation.
3.2. Mining scheme and the layout of the measuring line
The model is excavated from left to right. Since the research focus of this study is the final mining stage of the working face, the mining sequence is: (1) A 70 m boundary was set at the left side of the model for excavation and the 1216 working face was mined to a depth of 210 m, and the model was calculated to achieve balance; (2) A 50 m boundary was set at the left side of the model and the 2216 working face was excavated to 50 m before 1216 working face, and then the model was calculated to achieve balance. Next, the model was excavated once every 10 m and calculated to balance, and until the 2216 working face was excavated to 50 m behind 1216 working face, as shown in .
Five measuring lines are arranged along the model from No. 1 coal seam to No. 2 coal seam. The total of 150 measuring points are arranged for each measuring line, with a spacing of 1 m, set from left to right, as shown in .
3.3. Deflection law of principal stress
direction is the mining direction of the working face, and
direction is the height direction;
is the maximum principal stress (maximum absolute value);
is the deflection angle of the maximum principal stress. In this study, it is specified that the initial direction of the default maximum principal stress is horizontal. So we set the deflection angle of the maximum principal stress as 0°–180°, and counter clockwise rotation is positive. If the calculated maximum principal stress deflection angle is less than 0°, add 180° to
for positive value processing, as shown in .
Due to space limitations, the principal stress deflection curves of measuring lines 1# and 4# in the three mining stages of each scheme are placed in the paper: (1) the 1216 working face mining 210 m; (2) 20 m before 1216 working face; (3) 20 m behind 1216 working face. The principal stress deflection diagram of 20 m before 1216 working face of each scheme is placed in the paper, as shown in .
Figure 7. Deflection law of maximum principal stress.
According to , it can be analyzed that:
As shown in and , when
=0.5 and
=2, the initial principal stresses are vertical and horizontal stresses respectively. The maximum principal stress is close to the initial state about 40 m from the working face. It is not necessary to pay attention to the deflection of the principal stress to determine WSCP.
As shown in , when
=1, as the distance from the working face increases, the difference between the values of
and
decreases rapidly, and the more minor shear stress can cause the deflection of the maximum principal stress, so the deflection range increases. It is necessary to pay attention to the deflection of the principal stress to determine WSCP.
As shown in , this scheme corresponds to the actual geological conditions. When
=1.2, the initial maximum principal stress is the horizontal stress. Within the range of 45–75 m in front of the working face, the principal stress deflection is about 140°–165° before repeated mining and about 120°–150° after repeated mining. The angle and range of principal stress deflection are obviously increased. It is necessary to pay attention to the deflection of the principal stress to determine WSCP.
As shown in , the deflection law of principal stress is the same. Burial depth and layer spacing do not affect the deflection law of principal stress.
The side pressure coefficient and repeated mining dominate and aggravate the deflection angle and range of the principal stress in front of the working face, respectively.
We need to quantify the bearing capacity of the surrounding rock, and then determine WSCP, and carry out targeted control on the surrounding rock in combination with the deflection of the principal stress.
4. Quantification of bearing capacity of surrounding rock in roadway and determination WSCP
Zhang (Citation2013) and Zhao et al. (Citation2021) proposed ACBS, which provides a scientific basis for quantifying the bearing capacity of surrounding rock. We assume that the roadway is under hydrostatic pressure and is densely supported, and establish the mechanical model of ACBS, as shown in .
(7)
(7)
(8)
(8)
(9)
(9)
(10)
(10)
(11)
(11)
(12)
(12)
(13)
(13)
(14)
(14)
According to Formula (7–14), Formula (15) can be obtained:
(15)
(15)
=0.35 MPa
where is the thickness of ACBS, m;
is the roadway radius, 2.8 m; L is the length of the anchor bolt, 2.4 m;
is the number of anchor bolt, 10;
is the support strength, MPa;
is stress increment along the radial direction of roadway,
MPa;
is the bearing strength of ACBS, MPa;
is the working resistance of the anchor bolt, 0.2 MN;
is the row spacing of anchor bolt, 1 m*1 m;
is the vertical load on the bottom of ACBS, MPa;
is internal friction angle, 28°;
is the cohesion of the shallow part of the roadway surrounding rock, 0.1 MPa;
is the external load of ACBS;
is the total load of roadway surface support.
The surrounding rock of the roadway will form a natural balance arch in the deep surrounding rock. The thickness of the potentially loose rock layer of the roof is:
(16)
(16)
(17)
(17)
where
is stress concentration coefficient of roadway, 2;
is the stress disturbance coefficient, 2;
is rock weight, 25 kN/m3;
is burial depth, 400 m;
is height of roadway, 3.5 m;
is width of roadway, 4.5 m;
is width of potential loose zone of two sides, m;
is coal seam inclination;
is roof rock stability coefficient, 0.75;
is rock hardness coefficient, 2.
According to and , it can be analyzed that:
When the buried depth increases, the loose range of the two sides increases, resulting in the thickness of the potential loose rock layer of the roof also increasing. With mining of the 2216 working face, the disturbance of mining stress to the surrounding rock of the roadway is also increasing, which can be equivalent to the increase of buried depth.
When the strength of ACBS is greater than the rock load under the natural balance arch, the surrounding rock of the roadway can be maintained stable.
is safety factor. The value of
can be 2–3. So,
=4.7–7.0 m.
When =530 m,
=4.7, the actual buried depth of main roadway is about 400 m. It is equivalent to that the main roadway is located at 1.3 times the original rock stress.
4.1. Determination WSCP
4# measuring line is the stratum where the main roadway is located. The abutment pressure data of 4# in Scheme 3 in Section 3.2 can be drawn as curves.
According to , it can be analyzed that:
After repeated mining, the influence range of front abutment pressure is obviously increased;
When the 2216 working face is located 20–50 m before the 1216 working face, the abutment pressure distribution is the same. The abutment pressure of 60–75 m in front of the working face is close to 1.3
When the 2216 working face is located 20–50 m behind the 1216 working face, the abutment pressure distribution is the same. The abutment pressure of 55–75 m in front of the working face is close to 1.3
WSCP of the 2216 working face can be set as 60–75 m, and the corresponding maximum principal stress deflection angle is about 120°–150°, with an average of 135°.
5. Study on the control of surrounding rock of roadway affected by mining
Mastering the deformation characteristics of surrounding rock is the basis for the design of the surrounding rock support scheme. In this section, FLAC3D numerical simulation software is used to study the characteristics of surrounding rock deformation of the main roadway affected by mining.
5.1. Model establishment
The model size was 50 m (X) × 7 m (Y) ×50 m (Z). The horizontal and bottom boundary velocities of the model are limited to 0. The upper boundary is the stress boundary condition and the stress value is applied according to the influence of mining. Although the measured side pressure coefficient was 1.2, due to mining action, the side pressure coefficient at 1.3 in front of the working face will be close to 1. The initial direction of the default maximum principal stress is horizontal and so the scheme of numerical analysis is: (1) Scheme a is not affected by mining, the principal stress is not deflected and the roadway is not supported; (2) Scheme b is affected by mining, the principal stress is deflected and the roadway is not supported; (3) Scheme c is affected by mining, the principal stress is deflected and roadway support is the original-support; (4) Scheme d is affected by mining, the principal stress is deflected and roadway support is the optimized-support. The mechanical parameters of numerical simulation are shown in . The numerical analysis scheme is shown in . The numerical model applies the principal stress of deflection, as shown in .
Table 3. Mechanical parameters of coal and rock mass in calculation model.
Table 4. Schemes of numerical simulation.
5.2. Deformation characteristics of roadway surrounding rock
When the roadway is not supported, the cloud diagram of the surrounding rock plastic zone and maximum principal stress is shown in .
According to , it can be analyzed that:
Before mining, the maximum principal stress is concentrated in the surrounding rock of the roof and floor of the roadway. The width of the plastic zone of the two sides and the roof is about 2 m and 2.5 m, respectively;
After mining, the maximum principal stress is concentrated in the lower left and upper right corners of the roadway, and plastic failure occurs at the corresponding positions. The depth of the plastic zone of other parts has not significantly increased compared with that before mining.
5.3. Support scheme of roadway surrounding rock
Based on the original support, we added an anchor bolt and anchor cable at the lower left corner of the roadway, as is shown in . The mechanical and geometric parameters of cable structure element are shown in .
Table 5. Mechanical and geometric parameters of cable structure element.
According to , it can be analyzed that:
Compared with Scheme 2, the depth of the plastic zone of the roof, floor and two sides of the roadway is basically not reduced. However, the plastic zone at the corner of the roadway decreases greatly; Compared with no support, the compressive stress in the shallow part of the surrounding rock is increased, which indicates that the anchor bolt can effectively improve the stress state in the shallow part of the surrounding rock;
When the mining action causes the deflection of the principal stress, anchor bolt and cable can effectively control the occurrence of the plastic zone of diagonal position of surrounding rock with the maximum principal stress concentration.
6. Conclusion
Under the condition of unequal compression, with the deflection of the direction of the maximum principal stress, the distribution of the surrounding rock plastic zone also rotates, and the depth and area of the surrounding rock plastic zone at the corner of the roadway will obviously increase;
The side pressure coefficient and repeated mining dominate and aggravate the deflection angle and range of the principal stress in front of the working face, respectively; When
is close to 1, the principal stress deflection is still apparent at the far position in front of the working face; When
is small or large, the direction of the maximum principal stress can be restored to the initial state at about 30–40 m in front of the working face;
The bearing capacity of surrounding rock is 0.35 MPa calculated by ACBS; According to the increase of equivalent buried depth, WSCP in the 2216 working face can be 60–75 m, and the principal stress deflection at the corresponding position is about 135°;
Anchor bolt and cable can effectively control the occurrence of the plastic zone of the diagonal position of surrounding rock with the maximum principal stress concentration.
Acknowledgments
The authors also thank the reviewers for their helpful comments.
Disclosure statement
No potential conflict of interest was reported by the authors.
Data availability statement
The data used to support the findings of this research are included within the paper.
Additional information
Funding
References
- Cao RH, Cao P, Lin H. 2017. A kind of control technology for squeezing failure in deep roadways: a case study. Geomatics Nat Hazards Risk. 8(2):1715–1729. doi:10.1080/19475705.2017.1385542.
- Detournay E. 1986. An approximate statical solution of the elastoplastic interface for the problem of Galin with a cohesive-frictional material. Int J Solids Struct. 22(12):1435–1454. doi:10.1016/0020-7683(86)90054-5.
- Dong HL, Gao QC. 2019. Approximate solution on plastic zone of roadway surrounding rock under unequal compression in two directions by considering rheology. J China Coal Soc. 44(02):419–426. (In Chinese). doi:10.13225/j.cnki.jccs.2018.1660.
- He FL, Yang Y, Li L, Ou YF, Zhang X, Fu LH. 2022. Determining reasonable position of roadway for close coal seam. J Min Sci Technol. 7(4):505–512. (In Chinese).
- He MC. 2014. Progress and challenges of soft rock engineering in depth. J China Coal Soc. 39(8):1409–1417. (In Chinese).doi:10.13225/j.cnki.jccs.2014.9044.
- He MC, Qi G, Cheng C, Zhang GF, Sun XM. 2007. Deformation and damage mechanisms and coupling support design in deep coal roadway with compound roof. Chin J Rock Mech Eng. 26(5):987–993. (In Chinese).
- Hou GY, Li JJ, Zhao WW, Liu Y, Chen ZC, Tian L. 2014. Perturbation solutions for elasto-plastic problems of circular tunnel under unequal compression. Chin J Rock Mech Eng. 33(S2):3639–3647. (In Chinese).
- Jiang Y, Yoneda H, Tanabashi Y. 2001. Theoretical estimation of loosening pressure on tunnels in soft rocks. Tunn Undergr Space Technol. 16(2):99–105. doi:10.1016/S0886-7798(01)00034-7.
- Kang HP. 2016. Sixty years development and prospects of rock bolting technology for underground coal mine roadway in China. J China Univ Min Technol. 45(6):1071–1081. (In Chinese)
- Kastner H. 1980. Tunnel and trench statics. Shanghai: Shanghai Scientific and Technical Publishers. p. 41–60. (In Chinese).
- Khalymendyk I, Baryshnikov A. 2018. The mechanism of roadway deformation in conditions of laminated rocks. J Sustain Min. 17(2):41–47. doi:10.46873/2300-3960.1120.
- Li C, Wu Z, Zhang WL, Sun YH, Zhu C, Zhang XH. 2020. A case study on asymmetric deformation mechanism of the reserved roadway under mining influences and its control techniques. Geomech Eng. 22(5):449–460.
- Li J. 2020. The coal pillar design method for a deep mining roadway based on the shape of the plastic zone in surrounding rocks. Arab J Geosci. 13(12):454. doi:10.1007/s12517-020-05501-9.
- Li J, Qiang XB, Ma NJ, Zhang RG, Li B. 2021. Formation mechanism and engineering application of the directionality of butterfly leaf in the butterfly plastic zone of roadway rock surrounded. J China Coal Soc. 46(09):2838–2852. (In Chinese).
- Ma SQ, Nemcik J, Aziz N. 2013. An analytical model of fully grouted rock bolts subjected to tensile load. Constr Build Mater. 49:519–526. doi:10.1016/j.conbuildmat.2013.08.084.
- Nemcik J, Ma SQ, Aziz N, Ren T, Geng XY. 2014. Numerical modelling of failure propagation in fully grouted rock bolts subjected to tensile load. Int J Rock Mech Min Sci. 71:293–300. doi:10.1016/j.ijrmms.2014.07.007.
- Park KH, Kim YJ. 2006. Analytical solution for a circular opening in an elastic-brittle-plastic rock. Int J Rock Mech Min Sci. 43(4):616–622. doi:10.1016/j.ijrmms.2005.11.004.
- Sharan SK. 2005. Exact and approximate solutions for displacements around circular openings in elastic-brittle-plastic Hoek-Brown rock. Int J Rock Mech Min Sci. 42(4):542–549. doi:10.1016/j.ijrmms.2005.03.019.
- Tao ZG, Zhu C, Zheng XH, Wang DS, Liu YP, He MC, Wang YB. 2018. Failure mechanisms of soft rock roadways in steeply inclined layered rock formations. Geomat Nat Hazards Risk. 9(1):1186–1206. doi:10.1080/19475705.2018.1497712.
- Tokar G. 1990. Generalization of Galin’s problem to frictional materials and discontinuous stress fields. Int J Solids Struct. 26(2):129–147. doi:10.1016/0020-7683(90)90047-Y.
- Wang JC, Wang ZH, Yang SL. 2020a. Stress analysis of longwall top coal caving face adjacent to the gob. Int J Min Reclam Environ. 34(7):476–497. doi:10.1080/17480930.2019.1639007.
- Wang JC, Wang ZH, Yang J, Tang YS, Li BB, Meng QB. 2020b. Mining-induced stress rotation and its application in longwall face with large length in kilometer deep coal mine. J China Coal Soc. 45(3):876–888. (In Chinese).
- Wang ZH, Wang JC, Yang SL. 2018. An ultrasonic-based method for longwall top-coal cavability assessment. Int J Rock Mech Min Sci. 112:209–225. doi:10.1016/j.ijrmms.2018.10.019.
- Wang ZQ, Guo L, Su ZH, Wang JM, Xu J. 2016. Application of visible post-processing method of FLAC3D model node dis-placement in surface subsidence. J Min Sci Technol. 1:249–255. (In Chinese).
- Yu Y, Bai JB, Zhang SJ, Guo YH, Zhang LY. 2020. Disaster mechanism of surrounding rock with double wing mining roadway group and its repair and reinforcement system. J Min Safety Eng. 37(6):1133–1141. (In Chinese).
- Zhang YD. 2013. Study on bearing characteristic of composite bolt-rock bearing structure and its application in roadway bolting design [Ph.D. thesis]. China University of Mining and Technology.
- Zhao GM, Liu CY, Meng XR, Wang C. 2021. The composite anchorage bearing structure in high stress roadway and its load-bearing effect. J Min Saf Eng. 38(01):68–75. (In Chinese).
- Zuo J, Wang J, Jiang Y. 2019. Macro/meso failure behavior of surrounding rock in deep roadway and its control technology. Int J Coal Sci Technol. 6(3):301–319. doi:10.1007/s40789-019-0259-0.