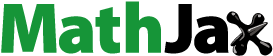
Abstract
Deep gob-side entry (DGSE) shows rock burst risk under the condition of kilometer depth and hard roof. Based on the established conditions of the Tengdong coal mine, theoretical analysis, microseismic (MS) monitoring, and numerical modeling were used to study the rock burst mechanism of DGSE. Results show that MS events mainly occurred on the solid side of DGSE and the intense dynamic load was mainly caused by the breaking of low hard roof strata, which can release 2.64 × 105 J elastic energy per meter. The surrounding stress of DGSE was asymmetrical due to the coal pillar yielding and hanging roof’s weight, and the load of coal pillar is negatively correlated with that of solid. Simulation shows the vertical stress evolution of coal pillar and solid shows significant diversity. Coal pillar’s vertical stress first drops sharply, and then increases gradually, finally stable at 10.6 MPa with the DGSE’s excavation. Contrarily, solid’s vertical stress gradually rises and was finally stable at 40.9 MPa. Under roof dynamic loading, the vibration velocity of the entry’s top was higher than that of the floor which was caused by the increase of the propagation distance and the reflection and diffraction effect of waves. The vibration velocity of the coal pillar was significantly higher than that of the solid which is because higher stress can lead to faster attenuation of vibration velocity. After dynamic loading, the coal pillar’s principal stress and principal stress difference decreased while that of the solid can be divided into two drop areas and one rising area. Periodic pressure relief that was carried out in the rising area can reduce the rock burst risk on the solid side of DGSE.
1. Introduction
Rock burst is a typical dynamic disaster that can cause sudden destruction of entry, casualties, and equipment damage (Dou et al. Citation2014; Iannacchione and Tadolini Citation2016). Studies have shown that rock burst occurs when the static and dynamic load superposition exceeds the critical strength limit of coal mass (He et al. Citation2017; Dou et al. Citation2021). The static load usually includes weight stress, abutment stress caused by mining and driving, and tectonic stress caused by faults, folds, etc. Whereas, dynamic load mainly includes roof fracture and coal explosion, which can be located using a microseismic (MS) monitoring system. Rock burst is more easily triggered by the dynamic load under high in-situ stress conditions. The frequency of the rock burst phenomenon increased in recent years, particularly in deep mines in eastern China, as mining depth and intensity increased (Xie et al. Citation2015; Ranjith et al. Citation2017; Li et al., Citation2021; Chen et al. Citation2022). Since large-size coal pillar, which stores a lot of elastic strain energy, can easily trigger rock burst under dynamic loading (Cai et al. Citation2018; Xue et al. Citation2019), narrow sections of coal pillar are widely used to prevent rock burst in many deep mines. However, the narrow coal pillar design still results in intense pressure and eventually, the rock burst phenomenon in gob-side entry (Tian et al. Citation2013; Yang et al. Citation2018; Zhang et al. Citation2017).
There have been numerous studies done that have provided a comprehensive understanding of gob-side entry failure. Coal pillar width optimization, large deformation roadway, basic roof fracture location, and entry support are the areas of research that are currently of particular interest. Zhang et al. studied the stress distribution of coal pillars of width from 3 m to 10 m at a depth of 400 m and found that gob-side entry was most accessible to maintain when the coal pillar width was 5 m (Zhang et al. Citation2015). Wang et al. proposed a method for determining the fracture position and fractured angle of key block B in gob-side entry and established a calculation method for the plastic zone width of gob-side entry (Wang et al. Citation2001). Li et al. found that the small width-to-height ratio of a coal pillar can cause its overall instability (Li et al. Citation2012). Using numerical simulation, Han et al. compared roof structural and deformation law of gob-side entry in six different cantilever lengths and proposed the optimal lateral cantilever length (7–8 m) under thick and hard direct roof conditions (Han et al. Citation2015). Several scholars have proposed new technologies to address the large deformation and maintenance difficulties of gob-side entries such as roadside filling and no-pillar mining. Liu et al. proposed quantitative filing design methods that consider the bearing characteristics of the coal wall, gob-side backfill, and gangues in gob (Liu et al. Citation2018). Chen et al. experimentally studied the effect of chloride on the strength of gangue-cemented paste backfill (Chen et al. Citation2020). They found that the strength of gangue-cemented paste backfill increased at an initial chlorine content of 10‰, while it decreased at an initial chlorine content of 40‰. Wu et al. invented a new gob-side pre-backfill driving method that eliminated coal pillar losses and enhanced gob-side entry stability (Wu et al. Citation2018). Wang et al. proposed a no-pillar mining technique with automatically formed gob-side entry retaining, and its field engineering applications showed a significant reduction in entry deformation (Wang et al. Citation2018).
A review of the previous studies introduced the main research directions of gob-side entry. Rock burst is caused by the superposition of static and dynamic loads, in other words, the nature of the rock burst is dynamic. Numerical simulations, which can include abundant related factors, provide a way to combine dynamic and static loads and thus, can be used to reveal the mechanism of the failure of gob-side entry and rock burst. Chen et al. used finite element/discrete coupled numerical simulation to analyze the failure characteristics of the deep buried circular entry under the influence of multiple structural planes and excavation unloading (Chen et al. Citation2020). They found that the inclination angle of the structural plane had a noticeable impact on the stability of the entry, and with the increased length of the structural plane, the possibility of the dynamic disaster of the entry gradually increased. Manouchehrian et al. studied the role of discontinuities around tunnels in rock burst using Abaqus and found that a weak plane in the model results in a higher amount of released kinetic energy and higher element velocity (Manouchehrian and Cai Citation2017; Manouchehrian and Cai Citation2018). Although the finite element method has been widely used to simulate the influence of discontinuity on the stability of entry, some researchers have used UDEC to simulate the dynamic and static loads of the mining field. Meng et al. simulated the stability of the backfill body along the gob-side entry (Meng et al. Citation2021). They found that compared with dynamic loads, static loads were the main factors leading to the failure of the backfill body, with dynamic loads having the least influence when the roof cutting angle was 70°. Mou et al. simulated the failure of the floor under the superposition of static and dynamic stresses (Mu et al. Citation2019). They found that the main controlling factors of floor failure were the width of the roadway and horizontal stresses. Some scholars also used FLAC to conduct dynamic and static load simulation research in the mining field. Wang et al. used the measured seismic wave to simulate the influence degree of dynamic load energy, position, and rock properties on the entry failure and found that the most sensitive to roadway failure was dynamic load position, followed by dynamic load energy, and finally, rock properties (Wang et al. Citation2019). Zhu et al. used numerical simulation to determine the height of the caving zone and fracture during the excavation process of the island working face (Zhu et al. Citation2017). The dynamic load strength arising from roof fracturing was quantified in the simulation. He et al. studied the action process of multi-period dynamic load on entry surrounding rock and revealed the process of entry tensile failure caused by stress wave reflections (He et al. Citation2016). Wang et al. simulated the distribution of principal stress and shear stress of the horizontal section mining of steeply inclined extra-thick coal seam. They found that the principal stress of the roof side was higher than that of the floor side, and the shear stress of the coal increased under the action of the dynamic load of the roof, which easily triggered the rock burst (Wang et al. Citation2022). The above literature review shows that scholars have used dynamic and static stress analysis methods to reveal the rock burst mechanism under various special conditions, and have made rich achievements. This shows that dynamic and static analysis is a reliable means to reveal the rock burst mechanism.
Chen et al. proposed that high ground stress and intense dynamic pressure were the leading causes of asymmetric deformation and maintenance difficulties in deep gob-side entry (DGSE) (Chen et al. Citation2021). However, limited reports are available on the evolution of static stress and the superposition law of static and dynamic stress in DGSE. The mining depth of the Tengdong (TD) coal mine is about 1 km. 18 mine tremors of energy higher than 104 J were experienced during the gob-side entry driving, and the anchor cable of the roof was broken, indicating a high risk of rock burst. Based on the gob-side entry driving of TD coal mine and the dynamic and static stress analysis method, this study analyzed the characteristic of dynamic and static load in the gob-side entry of TD coal mine. Furthermore, a FLAC3D numerical calculation model was established that considered the effectiveness of gob compaction and the strain-softening of coal. The evolution process of static stress during the driving of DGSE was reproduced, and the superposition law of dynamic and static stress was studied. The findings of the study could serve as a guide for preventing and controlling rock burst under similar conditions.
2. Site overview
2.1. Geological condition
The TD coal mine is located in the Yanzhou mining area, Shandong Province, China. Its ground elevation is +56 m, and the underground elevation is −920∼−960 m. The 3# coal seam with an average thickness of 5 m is mined. The inclination angle of the 3# coal seam is less than 5°. The TD coal mine employs the fully mechanized top coal caving mining technique, with a 3 m mining height and a 2 m caving height. The longwall mining workface (LW) 113 was mined first which was adjacent to LW115. A 5 m wide coal pillar was left between the two workfaces, as shown in . According to the key strata theory (Liang et al. Citation2017), the medium sandstone located 56.7 m from the 3# coal seam is the No. 1 inferior key strata (IKS), the conglomerate located 85.5 m from the 3# coal seam is the No.2 IKS, and the powder sandstone located 210 m from the 3# coal seam is the main key strata (MSK), as shown in .
Figure 1. Geological and mining conditions: (a) panel layout, (b) stratigraphic column of borehole TD3-2.

According to rock burst-prone identification conducted in the laboratory, the 3# coal seam, as well as its roof and floor, have a weak bursting liability. The physical and mechanical parameters of coal and rock masses found in the TD coal mine were tested and are listed in .
Table 1. Measured material parameters of coal and rock masses in the TD coal mine.
2.2. MS activity of DGSE
The MS monitoring system can monitor the tremor in the mining area in real-time, determine its location, and calculate the energy widely used in rock burst-prone mines (Jiang et al. Citation2006; Li et al., Citation2021). Roof fracture and stress concentration areas can be determined by analyzing MS events (Cai et al. Citation2020). Furthermore, MS data are used for early warning of rock burst (Si et al. Citation2020; Zhang et al. Citation2021). The SOS MS monitoring system had been installed on the LW115 to monitor mine tremors caused by mining. The positioning accuracy of various MS monitoring systems is compared in the literature (Qi et al. Citation2019). Generally, the horizontal positioning error of the SOS system is less than 20 m, and the vertical positioning error is less than 50 m.
Fortunately, complete data of MS events were collected while driving the LW115 track entry. The driving of the LW115 belt entry was ahead of the LW115 track entry, and two MS sensor stations (9#, 10#) were arranged after the belt entry driving was completed. Two MS sensor stations (6#, 8#) positioned in the main entry along with two MS sensor stations (9#, 10#) monitored the MS activity in the LW115 track entry driving area at the beginning of the entry driving. With the driving of the track entry, two MS monitoring stations (15#, 16#) were arranged in the entry. shows that the MS events were distributed along either side of the gob-side entry, however, the MS events on the solid side of the entry were more than that on the coal pillar side. The occurrence of MS events is associated with high-stress and high-stress differences, and the asymmetric plane distribution of MS events can reflect the stress distribution characteristics of gob-side entry. shows the MS events with energy higher than 104 J mainly occurred in roof strata within 50 m of the coal seam. According to the statistical data on MS events, a total of 690 MS events happened during the period of the LW115 track entry driving, the energy of 182 MS events varied from 103 to 104 J, and the energy of 18 MS events was above 104 J.
3. Overburden structure and theoretical analysis of DGSE
After LW113 was mined, there were areas of relatively low stress at the edge of the LW113 gob, which were the broken zone and the plastic zone. Driving a gob-side entry is much easier in a plastic zone. In conjunction with the established conditions of the TD coal mine, the roof structure and lateral plastic zone width were estimated to analyze the stress state of the LW115 track entry.
3.1. Overburden structure with narrow coal pillar
The original stress state of the gob roof was destroyed after coal resources were mined. As the advancement of LW113, the direct roof gradually collapsed. It was demolished and expanded to fill the gob and form the caving zone. Following that, the main roof and its upper strata separated, resulting in the formation of a fracture zone. Bending and sinking of overburdened rocks occurred, forming a subsidence zone. In the case of a large coal pillar, the critical rock block fracture always occurs above the coal pillar. Consequently, the abutment load was transferred to the gob. Thus, the maintenance of an entry with a large pillar is relatively easy (Xia et al. Citation2021). In contrast, the critical rock block fracture always occurs above the next entry if the size of the coal pillar is small, resulting in the deformation of the narrow coal pillar (). Thus, the maintenance of the entry with a narrow pillar is relatively difficult.
Figure 3. Roof structure with narrow coal pillar: (a) roof structure of gob along the inclination of the LW113, (b) ‘O-X’ shaped structure in the plane.

As shown in , with the advancement of the LW113, the main roof formed an ‘OX’ shaped structure and an arc-shaped triangular block B at the elastoplastic junction, which rotated and sunk to the gob at a certain angle to form a hinged structure with the adjacent rock blocks. The morphological characteristics and stability of the arc-shaped triangular block B directly affected the safety and stability of the gob-side entry. The length of the block B and the width of the lateral plastic zone after LW113 can be estimated according to the following formulas (Qian et al. Citation2010; Zhang and He Citation2016):
(1)
(1)
(2)
(2)
where,
is the roof cycle pressure distance of the adjacent working face (m),
is the width of the adjacent work face (m),
is the distance between the brake position of the block B and the coal wall of the gob (m),
is coal cohesion (MPa),
is coal internal friction angle (°),
is support resistance (MPa),
is stress concentration factor,
is lateral pressure coefficient,
is average bulk density of overburden (KN/m3),
is mining depth (m), and
is the thickness of coal seam (m).
and
were determined using the geological and production conditions of the LW113 and the actual measurement of the roof pressure law.
and
were determined based on the experience. The values of each parameter are listed in .
Table 2. The parameter of Formula (1) and Formula (2).
= 27.03 m,
= 14.01 ∼ 15.8 m were obtained by substituting the above parameters into the formula (1) and (2). Thus, the length of key block B was obtained as 27.03 m, which breaks at 14.01 ∼ 15.8 m from the coal wall.
3.2. Static load asymmetrically distributed
The in-situ stresses obtained in the TD coal mine were = 23.84 MPa,
= 32.76 MPa, and
= 19.78 MPa. The high ground stress caused the coal to reach the failure condition easily. Three months after the completion of LW113 mining, the track entry was driven, ensuring the stability of the LW113 gob. The destruction of coal pillars and the development of cracks in the process of coal failure were complex and affected by many factors (Chen et al. Citation2019; Zou et al. Citation2022). As shown in , the crack of the narrow coal pillar was large and deep, and the supporting steel belt was bent. This deteriorated the strength of the coal pillar, indicating that the coal pillar had intense deformation during gob-side entry driving.
Figure 4. Picture of coal pillar and force analysis of gob-side entry: (a) Picture of coal pillar side during gob-side entry driving, (b) Diagram of vertical stress distribution.

Under the influence of high in-situ stresses and mining disturbance, the narrow coal pillar of DGSE yielded. The narrow coal pillar still maintained a whole structure on the protection of arc-shaped triangular block B and the supporting of the anchor net cable and the steel belt. The residual strength of the narrow coal pillar was sufficient to support the above roof, which increased the actual span of gob-side entry. This led to stress transfer from the coal pillar side of the gob-side entry to the solid side, thus, the stress bias effect on both sides of the entry was significant.
Taking the roof as the force analysis object, the cantilever beam structure is formed under the clamp of the coal seam and the upper roof (). The weight of overburden was borne by the caving zone, narrow coal pillar, track entry, and solid coal. Since the edge of the gob was not well-filled, the supporting force of the gob was disregarded. Formula (3) can be obtained from vertical stress equilibrium.
(3)
(3)
where,
is the vertical stress distribution function of narrow coal pillar,
is the vertical stress distribution function of entry,
is the vertical stress distribution function of solid coal, q is an equivalent uniform load of overburden,
is the distance from the entry to the in-situ stress zone,
is the width of coal pillar,
is the width of entry.
is the length of the hanging roof and is related to the thickness of the roof, lithology, mining height, and filling degree of gob.
According to formula (3), the larger the the larger the roof total load. The smaller
and
are, the larger
is. That is the lower the bearing capacity of the coal pillar, the higher the stress of the solid side, and the stronger the stress deviation effect of the entry surrounding rock.
3.3. Dynamic load analysis of gob-side entry
Usually, entry driving does not cause an extensive range of roof movement like workface mining. However, in the condition of a gob-side entry driving with 1 km depth, the deflection of the hard roof was more severe than that under the mining condition of a large coal pillar or shallow coal seam due to the influence of high in-situ stress and coal pillar yield. MS monitoring data showed high-energy MS events were happening in the low thick hard rock stratum (). Based on the height of the high-energy MS events, it was inferred that the No. 1 IKS had been broken.
According to the elastic rock beam theory (Qian et al. Citation2010), the elastic energy accumulated in the rock layer is proportional to the fifth power of the length of the hanging roof, as shown in Formula (4):
(4)
(4)
where,
is the weight of the hard roof per unit length and the additional load of overburden,
is the elastic modulus, and
is the moment of inertia.
According to the established condition of the TD coal mine, the of medium sandstone was 111 MPa (), implying a hard roof. The overhanging length of the hard roof is related to the caving angle of the rock. Qian et al. showed that the caving angle of the hard roof is 30° (Qian et al. Citation2010). Meanwhile, the calculation result of the Formula (1) shows that the length of key block B (
) was 27.03 m and the
of medium sandstone was 29.78 GPa (). The parameters were substituted into Formula (4) and the energy released by the breaking of the No. 1 IKS per meter was obtained (). Additionally, when combined with the results of MS monitoring, it can be confirmed that the elastic energy released by the breaking of the low-key strata could be the primary source of intense dynamic load ().
Table 3. Elastic energy released by the breaking of the No. 1inferior key strata per meter.
In addition to the intense dynamic load generated by the braking of low IKS. Due to the strength of coal being much lower than rock, the rock strata above the coal will bend and produce the horizontal component force on the solid side of the entry. The deformation of the solid side of the entry was limited, which caused the coal body to accumulate energy and generated vibration ().
4. Numerical simulation study of DGSE
The overburden structure and theoretical analysis results reflect the asymmetric stress and deformation characteristics of DGSE. The low-key strata breaking was the source of the primary intense dynamic load supported by the position of MS events. In this section, FLAC3D numerical software was used to study the stress evolution of DGSE driving and the response law of DGSE under the dynamic load from the hard roof. The detailed simulation process was shown in .
4.1. Establishment of the numerical model
Based on the geological and production conditions of the TD coal mine, a three-dimensional numerical calculation model was established after appropriate simplification, as shown in . The dimensions of the model were 500 m × 300 m × 174 m (x, y, z). The static displacement boundary was applied around the models for the static analysis. Vertical stress of 19 MPa was applied to the top of the model. The three direction stresses of the model (X, Y, Z) were initialized according to in-situ stress test results, which were 32, 19, and 24 MPa, respectively. The applied gravity acceleration of the model was 9.8 m/s2.
This numerical model used three constitutive models to achieve accurate simulation. Mohr-coulomb constitutive was used for the rock strata. Its physical and mechanical parameters were obtained via the rock burst-prone identification test and a previously proposed parameter conversion method (Mohammad et al. Citation1997), as shown in . The coal seam was relatively weak compared to the rock strata, so the coal body was modeled using the Strain-softening constitutive model. Field observations show that mining-induced fractures in overburdened rock can be divided into three vertical zones from the gob bottom to the top: caving zone, fracture zone, and bending subsidence zone. The height of the caving zone determines the distribution law of stress and deformation of the gob. The treatment method of gob can significantly influence the simulation result using FLAC3D. The compaction effect of gob was also considered by using Double-yield constitutive. The calibration process of Strain-softening and Double-yield constitutive parameters was introduced in detail in Section 4.2.
Table 4. Rock mechanics parameter.
4.2. Determination and calibration of numerical parameters
4.2.1. Strain softening constitutive parameter calibration
Du et al. studied the influence of the variation in cohesion, friction angle, and tensile strength of coal and rocks on the softening effect and indicated that the softening effect was dominated by the change in cohesion (Du Citation2021; Zhou et al. Citation2022). The initial physical and mechanical properties of the coal in this study are listed in . They were determined based on a uniaxial compression test of small cuboid samples of 50 mm width and 100 mm height collected from the TD coal mine. A series of uniaxial compression numerical tests with cylinder samples of 100 mm height and 50 mm diameter were conducted to obtain the residual cohesion and the softening ratio of the coal samples. The residual cohesion and the softening ratio were amended by trial and error until they were identical to the experimental results. shows the numerical and experimental results of the coal sample. The softening rate of cohesion for coal was 0.5%, and the residual value of cohesion was 0.2 MPa.
4.2.2. Double yield constitutive parameter calibration
Determination of caving zone height involves physical simulation, numerical simulation, theoretical calculation, and field measurement. The caving zone height is affected by factors such as the mechanical properties of the roof strata, ground stress, and mining height. Bai et al. obtained the regression formula for calculating the height of the caving zone by statistically analyzing a large number of mines in China and America under different geological conditions (Bai et al. Citation1995).
(5)
(5)
where,
is the caving zone height,
is the mining height, and
and
are the strength coefficients of the rock strata (refer to for the values).
Table 5. Calculation coefficients of the average height of the caving zone (Bai et al. Citation1995).
The height of the caving zone can also be expressed as:
(6)
(6)
where,
is the bulking factor of the collapsed rock, which is determined by the height of the caving zone and the mining height.
Combined with Formula (5), the bulking factor of the collapsed rock is:
(7)
(7)
The stress-strain relationship of the caving zone was given in reference (Salah et al., Citation2003) by combining the result of experimental research (Pappas and Mark Citation1993) and the compaction theory of caved zone proposed by Salamon (Citation1990).
(8)
(8)
where,
is the vertical stress exerted on the rock mass in the caving zone,
is the initial elasticity modulus of the rock mass,
is the strain of the rock mass in the caving zone under vertical stress, and
is the maximum strain after the rock mass is crushed and expanded, which can be calculated using Formula (9).
(9)
(9)
The initial elasticity modulus of the rock mass can be calculated using the following empirical formula (Salamon Citation1990).
(10)
(10)
where,
represents the compressive strength of the rock mass.
Substituting Formula (9) and (10) into (8), the stress-strain relationship of the collapsed rock mass can be obtained as follows:
(11)
(11)
Using the Formula (5) and (8), the height of the caving zone and bulking factor of the collapsed rock
were calculated to be 18.9 m and 1.26, respectively. The
of the rock in the caving zone is taken as 110 Mpa. Substituting
and
into Formula (11), the stress-strain theoretical relationship of the collapsed rock in the gob can be obtained as follows:
(12)
(12)
As shown in , a cube model (1 m × 1m × 1m) is established for the uniaxial compression test, a fixed velocity is applied on the upper surface of the cube and the boundary is fixed. By repeatedly adjusting the physical parameters to make the stress-strain curve of the model coincide with the theoretical curve. The mechanical parameters of the rock in the collapse zone that meet the simulation requirements are finally obtained, as shown in .
Table 6. Parameters of the gob material used in the numerical model.
4.2.3. Determination of dynamic load and damping setting
In the dynamic load numerical simulation, the viscous boundaries were applied to the strike, normal, and dip of all the boundaries of the numerical model to reduce the reflection of fluctuations on the model boundary. The mesh size of the model was generally 5 m. Some main research areas were encrypted, and the mesh size was 0.5 m. FLAC3D user manual requires that the grid should be less than 1/8–1/10 of the wavelength during the dynamic calculation. The dynamic frequency simulated in this study was 10 Hz, and the grid met the requirements.
shows the statistical curve of the G-R power rate of all MS events during LW113 track entry driving. Qi et al. proposed that the intersection point between this curve and the horizontal axis represents the maximum possible MS energy (Qi and Dou Citation2008). In this study, the MS event of 105 J was selected for dynamic simulation. He et al. did a statistical analysis of the relationship between MS energy and the vibration velocity in coal mine sites () (He Citation2013) and found that the maximum vibration velocity corresponding to MS of 105 J was about 3.6 m/s. According to seismological theory, the MS wave can be simplified as sine waves. The MS waveform has the characteristics of low frequency high energy and high frequency low energy. The dominant frequency of the MS waveform is lower than 20 Hz when the MS energy is larger than 105J (). In the present study, the initial direction of the dynamic load was negative along the -axis. The dynamic velocity was 3.6 m/s and its frequency was 10 Hz, as shown in . The position of the dynamic load was located above the track entry 50 m, which is close to No. 1 IKS ().
Figure 10. Determination of dynamic load: (a) G-R power law curve of MS events, (b) Velocity time history dynamic load, and (c) position of the dynamic load source.

Table 7. The statistical relation between the MS energy and its vibration velocity.
Rayleigh damping was used in this simulation, and the Rayleigh damping equation can be expressed as a matrix:
(14)
(14)
where,
is the damping matrix,
is the mass-proportional damping constant,
is the stiffness-proportional damping constant,
is a mass matrix, and
is a stiffness matrix.
According to the FLAC3D manual, the damping coefficient and center frequency must be determined for Rayleigh damping. For geological materials, the is generally 2%–5%. The damping coefficient selected in this study was taken as 2%. The
was determined using the natural frequency of the model and the input dynamic load frequency. The dynamic load frequency was considered and the natural frequency of the model was ignored and
was determined to be 10 Hz.
4.3. Numerical simulation of static load evolution
4.3.1. Stress evolution in the excavation of LW113
shows the vertical stress evolution during the LW113 excavation. With the excavation of LW113, the vertical stress of the advanced area and the caving zone of LW113 gradually increased due to the stress transfer and recovery (). And the vertical stress of the caving zone is not symmetrical distribution. The vertical stress near the open cut is significantly higher than the vertical stress near the stopping line, this shows that the vertical stress of the caving zone has gradually increased with the increase of the calculation steps of the model (). This distribution law is similar to the actual situation in the field. The compaction time of the gob that is closer to the working face is always less than that of the gob farther away from the working face. The maximum vertical stress of the middle of the caving zone increased from 2.9 MPa at 5 m excavation to 8.0 MPa at 400 m excavation. With the excavation of LW113, the vertical stress of monitoring line B gradually increased, from 26.6 MPa at 5 m excavation to 32.1 MPa at 400 m excavation (). The distance between the highest vertical stress point and the edge of LW113 gob increased first and stable with the excavation of LW113, from 5.6 m at 5 m excavation to 15.3 m at 350 m excavation. The elastoplastic junction was consistent with the position of the maximum value of the vertical stress, indicating that the depth of the lateral plastic zone was about 15.3 m after the LW113 excavation completion. The numerical simulation results of the depth of the maximum vertical stress were almost consistent with the calculation results of Formula (2), which proves the reliability of the numerical model.
Figure 11. Vertical stress evolution during LW113 excavation: (a) arrangement of vertical stress monitoring lines, monitoring line B moved with the excavation range and was always located in the middle position of the side of the gob domain, (b) vertical stress contour evolution in coal seam section with different excavation range, (c) vertical stress of line a with different excavation range, (d) vertical stress of line B with different excavation range.

4.3.2. Stress evolution during gob-side entry excavation
shows the vertical stress in the coal seam section with different excavation ranges of the LW115 track entry. As shown in , the maximum vertical stress of the solid side () increased from 33.1 MPa at entry excavation 5 m to 40.9 MPa at entry excavation 400 m. The maximum vertical stress of the coal pillar (
) fall first and then rises with the LW113 gob recompaction, eventually remaining basically stable. When the LW115 track entry was excavated 50 m, the
dropped to the minimum value. Later, with the excavation of the entry, the
slowly increased, and stress recovery occurred. This shows that the coal pillar zone yields first and the
drop, then the
slowly recover, this may be caused by the restoration of the stress of the caving zone near the coal pillar. When the excavation of the gob-side entry was completed,
reaches 1.64 times the initial stress, while
drops to 0.42 of the initial stress. The stress on the solid side of gob-side entry is about 4 times that on the coal pillar side, and the stress on both sides of the gob-side entry is very asymmetrical. With the excavation of the gob-side entry, the distance between the
and the gob-side entry gang is also changing. According to , the distance between the
and the entry gang is 4 m, 7 m, 11 m, 17 m, 20 m, 21 m, 21 m, 21 m, and the distance between the
and the entry gang is 3 m, 5 m, 6 m, 10 m, 11 m, 12 m, 12 m, 12 m. This shows that with the excavation of the entry, the stress peak position on both sides of the entry first gradually increases and finally tends to be stable. The stress peak position of the coal pillar side is in the gob, and this situation is caused by complete yield failure of the narrow coal pillar and stress recovery of the gob.
4.4. Effect of dynamic load released by hard roof strata on DGSE
4.4.1. Vibration velocity response law
During the dynamic loading period, the track entry velocity was monitored. The monitoring points (MP) were 1 m away from the coal wall, and the distance between two adjacent MP was 1 m ().
Figure 13. Characteristic of vibration velocity around track entry, (a) monitoring points arrangement, (b) evolution of vibration velocity at four corners of the track entry, and (c) distribution of maximum vibration velocity around track entry.

shows the velocity variation of the four corners around the entry in the dynamic loading process. At stage I (0–0.1 s), the vibration velocity of all MP quickly reached their maximum values. Following that, the fluctuation in velocity at each MP gradually decreased at stage II (0.1–0.7 s). Finally, the velocity at each MP gradually became stable at stage III (0.7–1 s). The maximum vibration velocities at MP-A, MP-B, MP-C, and MP-D were 0.196 m/s, 0.281 m/s, 0.021 m/s, and 0.018 m/s, respectively. This indicated that the moment when the dynamic load occurs, the possibility of entry damage caused by the dynamic load was largest, and the intensity of the dynamic load on the entry decreases rapidly with the extension of time. When the dynamic load propagates through the entry, the strength of the dynamic load will be greatly attenuated, and the speed will drop by 90%.
shows the distribution law of the maximum vibration velocity at all MP around the entry. It can be seen that the maximum vibration velocity of the top was significantly higher than that of the floor, and the maximum vibration velocity of the coal pillar side was higher than that of the solid side. The maximum vibration velocity of the entry’s top was higher than that of the floor which was caused by the increase of the propagation distance and the reflection and diffraction effect when the wave through the entry. Under the condition of the same dynamic loading propagation distance, the velocity of the coal pillar side of DGSE caused by dynamic load was higher than that of the solid side. This is caused by the stress on the solid side of the gob-side entry being higher than the stress on the coal pillar side. Studies have shown that the vibration velocity decays faster in a high-stress environment (Xin-Ping et al. Citation2016). In addition, the reflection of the wave may be a critical reason for the high vibration velocity of the coal pillar. The material properties of the gob filling area in the simulation are quite different from the coal pillar and the roof and floor (As shown in ), the strong reflection of the wave near the coal pillar will also lead to the increase of the vibration velocity.
4.4.2. Variation law of principal stress
In a numerical model based on the Mohr-Coulomb constitutive model, the magnitude of the maximum principal stress can reflect the stress of the surrounding rock, and the magnitude of the principal stress difference can reflect the failure tendency of the surrounding rock. The principal stress difference was obtained by subtracting minimum principal stress from maximum principal stress. A series of MP was arranged on the coal pillar and solid side of the entry to monitor the variation of principal stress under the dynamic loading ().
Figure 14. Analysis of principal stress and principal stress difference: (a) arrangement of monitoring point, (b) variation of maximum principal stress in coal pillar area, (c) variation of principal stress difference in coal pillar area, (d) maximum principal stress in the solid side area, (e) principal stress difference in the solid side area.

shows the evolution of the maximum principal stress in the coal pillar. The principal stress increases gradually from C1, C2, C3, and C4. This shows that the closer the coal pillar is to the LW113 gob, the greater the principal stress is. This is because the gob with double yield constitutive limits the lateral displacement of the coal pillar and improves the supporting ability of the coal pillar. Under the dynamic loading, the principal stress of C1, C2, C3, and C4 increased, then decimated, and finally declined after several fluctuations. The sudden increase of principal stress caused by dynamic load may lead to a rock burst of coal pillar. The maximum principal stress reduction rate of C1, C2, C3, and C4 is 1.52%, 0.97%, 0.58%, and 0.37%. After dynamic loading, the closer the coal pillar is to the surface of the entry, the greater the reduction rate in maximum principal stress. The dynamic loading makes the stress of the coal pillar adjust and transfer, and finally makes the principal stress of the coal pillar decrease. In conclusion, in the process of dynamic loading, dynamic loading causes the transient increase of coal pillar stress, which leads to the increase of rock burst risk. However, after dynamic loading, the stress of coal pillar is generally reduced due to stress adjustment and transfer, so the rock burst risk of coal pillar is reduced.
shows the evolution of the principal stress difference of C1, C2, C3, and C4. The variation law of principal stress difference was consistent with principal stress, and the principal stress difference was slightly reduced after dynamic loading. The principal stress difference decreases sequentially from C4, C3, C2, and C1. The closer the monitoring point is to the surface of entry, the smaller the principal stress difference is. The reduction rate of principal stress difference of C1, C2, C3, and C4 were 1.73%, 1.21%, 0.79%, and 1.48%, respectively. The reduction rate of the principal stress difference in the middle of the coal pillar is lower than that of the principal stress difference on both sides of the coal pillar, and the area near the coal pillar surface is less prone to instability failure after dynamic loading. The analysis of principal stress and principal stress difference shows that dynamic loading does not increase the rock burst risk of the coal pillar side.
shows the evolution of the maximum principal stress of S1–S13. The principal stress at S3 was 40.99 MPa, higher than other monitoring points, and increased to 41.09 MPa after dynamic loading. The maximum principal stress of S1, S2, S10, S11, S12 and S13 decreased, while the maximum principal stress of S3, S4, S5, S6, S7 S8, and S9 increased after the dynamic loading. The escalating rate of principal stress of S3, S4, S5, S6, S7, S8 and S9 were 0.24%, 0.79%, 3.24%, 6.13%, 8.73%, 7.64%, and 1.48%, respectively. And the increment of maximum principal stress at S7 was the largest. From the above analysis, it can be seen that after dynamic load, from the surface of the solid side of the gob-side entry to the depth, the principal stress drop area, rising area, and drop area appear in sequence. This indicates that dynamic load has different effects on different areas of the solid side of the entry. Areas with increased principal stress should be given special attention, because repeated dynamic loading may lead to a continuous increase in stress in this area, increasing the risk of rock burst. The monitoring point with the largest increase in principal stress is S7, which is 13 m from the surface of the gob-side entry and the area where the principal stress rises is 9 ∼ 21 m away from the entry. The pressure relief range in the field should include this rising area.
shows the evolution of the principal stress difference in the solid side of the entry. The principal stress difference at S4 was 15.91 MPa, higher than other monitoring points, and decreased to 15.18 MPa after dynamic loading. Similarly, the principal stress difference after dynamic loading is divided into drop area, rise area, and drop area. The principal stress difference of S1, S2, S3, and S4 decreased, while the principal stress difference of S5, S6, S7, and S8 increased. The principal stress difference of S9, S10, S11, S12, and S13 was also decreased. The escalating rate of principal stress differences of S5, S6, S7, and S8 were 0.75%, 1.86%, 7.34%, and 2.38%, respectively. The monitoring point with the highest principal stress is S3, and the monitoring point with the highest principal stress difference is S4, which are 21 m and 19 m away from the surface of the entry respectively. After the dynamic load, the principal stress and the principal stress difference both present three change areas, drop area, rise area, and drop area. This indicates that dynamic loads have different effects on the stress state of coal bodies in different regions. The rising range of principal stress is 7–21 m from the surface of the gob-side entry, and the rising range of principal stress difference is 9–19 m from the surface of the gob-side entry. Special attention should be paid to coal bodies whose principal stress and principal stress difference increase after dynamic loading. Multiple dynamic loads may cause their stress continuously increases, which may increase the risk of rock burst.
5. Discussion
5.1. MS events verification
MS events are caused by the energy release of coal rock mass, and MS events tend to occur in areas with high stresses and large stress differences (Cao et al. Citation2020). MS monitoring system realizes a wide range of vibration monitoring by using multiple high-sensitivity sensors and MS events are often used for rock burst assessment and prediction. Wang et al. proposed a calculation method of MS energy density, which had a good correspondence with the rock burst risk, and had been successfully used to predict the rock burst of Xing’an Coal Mine (Wang et al. Citation2018). A statistical method was been proposed in this paper to accumulate the count and energy of MS events that happened during the gob-side entry driving in multiple fixed statistical intervals. Taking the center of track entry as zero axis and 5 m as a statistical interval, the MS event cumulative energy, and cumulative count are presented in . The total MS energy and count on the solid side were higher than that on the gob side. The maximum value of total MS count and energy was 22 m from the zero axis, which was about 20 m away from the track entry coal wall (). The energy statistics of MS events in the vertical direction showed two peaks, one peak point was about 20 m from the coal seam, and the other was about 50 m from the coal seam. This indicates that the MS energy release may come from the rock strata near the coal seam and the No. 1 IKS. The cumulative count of MS events at 50 m above the coal seam was less than that at 20 m above the coal seam, indicating that the average energy of MS events at 50 m above the coal seam was relatively high ().
Figure 15. Statistics distribution of MS events energy and count: (a) MS inclination direction statistics, (b) MS vertical direction statistics.

The distribution of MS events proved that the roof breaking was the primary source of strong dynamic load and the asymmetric distribution of static load stress on both sides of the gob-side entry. The region with the highest MS events counts and energy was 20 m away from the wall of the entry, which was close to the numerical simulation result of principal stress and principal stress difference peak of 19 ∼ 21 m. This verifies the reliability of the numerical simulation results, indicating that the parameters used in the simulation are realistic.
5.2. Mechanism of rock burst of DGSE
The typical characteristic of gob-side entry driving is asymmetric stress distribution (Zhao et al. Citation2022). The lateral abutment pressure and rotary extrusion force caused by the cantilever beam are the mechanical causes of asymmetric deformation and failure (Zhao et al. Citation2022). Xie simulated the stress distribution of different coal pillar widths in gob-side entry with a buried depth of 700 m, and found that the stress of the solid side was about 40 MPa and the stress of the coal pillar was 16 MPa when the coal pillar’s width was 5 m (Xie Citation2021). In this article, the detailed stress evolution of gob-side entry driving was reproduced. With the excavation of the gob-side entry, the vertical stress on the coal pillar of the gob-side entry drops sharply at first, then increases with the gradual compaction of the gob, and finally remains basically stable at 10.6 MPa. In this process, the vertical stress on the solid gradually rises and finally reaches 40.9 MPa. Under the condition of 1 km depth, the asymmetric stress distribution phenomenon was more significant due to the higher overburden gravity (). The solid side of DGSE was clamped under the bending hard roof, which resulted in the coal on the solid side being prone to accumulate large amounts of elastic energy and was a potential source of dynamic load ().
A rock burst is triggered when the superposition of the static stress () and the dynamic stress (
) exceeds the critical stress (
) (Li et al. Citation2015).
can be caused by the gob-side entry driving (
) and the abutment stress of the gob (
).
can be caused by the breaking of roof strata (
) and the fracturing of coal in the solid side of gob-side entry (
). shows the stress distribution after the superposition of
and
The maximum vertical stress increased to 40.88 MPa from 31.89 MPa after gob-side entry driving. shows the vertical stress after the superposition of
and
According to the vertical stress change, it is divided into two drop areas and one rising area. The rising area of vertical stress is close to the surface of entry, which indicates the increased of rock burst risk on the solid side of the gob-side entry due to the increased static stress (
) of the surrounding rock. It should be noted that this is only a vertical stress increase due to a one-time dynamic load. The conceptual model of the rock burst mechanism in the DGSE is depicted in . In coal and rock stara, the dynamic load intensity decays rapidly with the increase of propagation distance. The distance between the source of
and
and the free surface of the gob-side entry is significantly different, a small scale of
may cause more serious damage to the entry than
In addition, the simulation results show that
can cause the principal stress and principal stress difference to increase in the rising area, and the energy of
is more intense when the dynamic failure of coal happened in the rising area.
Figure 16. The variation of stress around the entry. (a)variation of vertical stress caused by entry driving, (b)variation of vertical stress caused by dynamic loading.

Therefore, some measures are necessary to prevent the rock burst in the stress rising area and should be implemented every once in a while, to release the stress in time in the stress-rising area under the action of dynamic load. Current rock burst control techniques can be classified into preventative and mitigating controls. Preventive controls are mainly employed to weaken the hard roof strata, aiming to reduce the length of the cantilever beam above the entry. Whereas, preventative controls can fundamentally change the stress environment of gob-side entry and alleviate the asymmetrical stress distribution, including no section coal pillar by cutting the roof along the entry (He et al., Citation2017; Wang et al. Citation2020) and blasting the lateral roof when mining the previous working face (Lu et al. Citation2021; Kan et al. Citation2022). Mitigating techniques can prevent and control the stress concentration of the solid side of the gob-side entry, including hydraulic fracturing, water infusion, stress relief drilling, bump cutter, and explosive charge (Wei et al. Citation2018). Although preventative controls and mitigating controls can reduce the probability of rock burst, the top of gob-side entry needs stronger support to avoid the failure of entry top under intense dynamic loading from roof strata (Ma et al. Citation2018).
6. Conclusions and Prospects
6.1. Conclusions
Based on the engineering background of gob-side entry with a 1 km buried depth and hard roof, this paper studied the stress evolution and rock burst risk of gob-side entry driving using theoretical analysis, MS monitoring, and numerical simulation. The main conclusions are as follows:
MS monitoring and theoretical analysis showed that the roof breaking position of the DGSE was on the solid side of the entry and the low IKS were the primary source of strong dynamic load. Further, the yielding of the coal pillar indirectly increased the hanging length of the hard roof, which increased the stress of the entry’s solid.
Theoretical calculation shows that the width of the plastic zone after LW113 was mined is 14.01 ∼ 15.8m, which is close to the numerical simulation results of 15.3m. The release elastic energy of the breaking of the IKS per meter is 2.64 × 105 J, which is the primary source of dynamic load.
With the gob-side entry’s excavation, the vertical stress of the coal pillar first drops sharply and then increases gradually with the compaction of the gob, however, the vertical stress on the solid side gradually rises. Finally, the stress on the solid of DGSE is around 4 times that on the coal pillar.
Under dynamic loading, the velocity of the entry’s top was significantly higher than that of the entry’s floor and the velocity of the coal pillar was higher than that of the solid. After dynamic loading, the principal stress and principal stress difference of the coal pillar decreased, while the principal stress that 7–21m from the gob-side entry’s surface and the principal stress difference that 9–19m from the gob-side entry’s surface were rising, which aggravated the rock burst risk of the solid.
Statistical analysis of MS events verified the accuracy of the numerical simulation results and showed the high rock burst risk of DGSE’s solid. Periodic decompression of stress-rising areas on the gob-side entry’s solid side can reduce the rock burst risk of DGSE.
6.2. Prospects
At a buried depth of 1 km and with a hard roof, the two sides of the gob-side entry showed typical asymmetric characteristics in stress, deformation, and dynamic load response. This mainly reflected that the solid had higher stress, while the coal pillar had more serious deformation and was easier affected by dynamic load. The maintenance of gob-side entry in this condition should adopt an asymmetric strategy. For the stress concentration area on the solid, pressure relief should be carried out periodically, to transfer the high stress and reduce rock burst risk of the solid. Ensuring the integrity of coal pillar is the key content of coal pillar treatment, which can be achieved through full anchor support and grouting reinforcement measures. Further, the root cause of the asymmetric characteristics of gob-side entry is the cantilever beam of the hard roof. Cutting off the hard roof before gob-side entry driving is very effective to reduce the coal pillar deformation and reduce the solid stress. In addition, since the stress in some areas of the solid will rise under dynamic load, it is necessary to carry out repeated pressure relief on the solid in the driving process to ensure that the roadway is free from rock burst.
Due to the limited article length, the paper only studies the asymmetric response characteristics of gob-side entry from the perspective of dynamic stress and static stress. The asymmetric deformation and elastic energy evolution of gob-side entry are worthy of further study. Asymmetrical measures for gob-side entry maintenance are also a direction worthy of detailed research. The inadequacies of this study are kindly understood by experts and scholars.
Author contributions
Conceptualization: Zepeng Han and Linming Dou; Data curation: Xiaoyi He; Formal analysis: Zepeng Han, Siyuan Gong, Shuai Chen, and Jiliang Kan; Funding acquisition: Linming Dou and Zepeng Han; Methodology: Zepeng Han; Resources: Xiaoyi He; Supervision: Linming Dou; Writing—original draft: Zepeng Han, Jiliang Kan, and Shuai Chen; Writing—review and editing: Linming Dou and Siyuan Gong.
Abbreviations | ||
DGSE | = | Deep gob-side entry |
G-R | = | Gutenberg and Richter |
IKS | = | Inferior key strata |
LW | = | Long mining workface |
MP | = | Monitoring point |
MS | = | Microseismic |
MSK | = | Main key strata |
TD | = | Tengdong |
Data availability statement
The data that support the findings of this study are available from the corresponding author, [Linming Dou, Zepeng Han], upon reasonable request.
Disclosure statement
The authors declare that they have no known competing financial interests or personal relationships that could have appeared to influence the work reported in this paper.
Additional information
Funding
References
- Bai M, Kendorski FS, Van Roosendaal DJ. 1995. Chinese and North American high-extraction underground coal mining strata behavior and water protection experience and guidelines. Proceedings of the 14th International Conference on Ground Control in Mining; Morgantown, WV. pp. 209–217.
- Cai W, Bai XX, Si GY, Cao WZ, Gong SY, Dou LM. 2020. A monitoring investigation into rock burst mechanism based on the coupled theory of static and dynamic stresses. Rock Mech Rock Eng. 53(12):5451–5471. doi: 10.1007/s00603-020-02237-6.
- Cai W, Dou LM, Zhang M, Cao WZ, Shi JQ, Feng LF. 2018. A fuzzy comprehensive evaluation methodology for rock burst forecasting using microseismic monitoring. Tunn Undergr Sp Tech. 80:232–245. doi: 10.1016/j.tust.2018.06.029.
- Cao W, Durucan S, Cai W, Shi J-Q, Korre A, Jamnikar S, Rošer J, Lurka A, Siata R. 2020. The role of mining intensity and pre-existing fracture attributes on spatial, temporal and magnitude characteristics of microseismicity in longwall coal mining. Rock Mech Rock Eng. 53(9):4139–4162. doi: 10.1007/s00603-020-02158-4.
- Chen LX, Kang HP, Jiang PF, Li WZ, Yang JW, Zhen YF, Yi K. 2021. Deformation and failure characteristics and control technology of surrounding rocks in deeply gob-side entry driving. J Min Saf Eng. 38:227–236.
- Chen SJ, Du ZW, Zhang Z, Zhang HW, Xia ZG, Feng F. 2020. Effects of chloride on the early mechanical properties and microstructure of gangue-cemented paste backfill. Constr Build Mater. 235:117504. doi: 10.1016/j.conbuildmat.2019.117504.
- Chen S-J, Feng F, Wang Y-J, Li D-Y, Huang W-P, Zhao X-D, Jiang N. 2020. Tunnel failure in hard rock with multiple weak planes due to excavation unloading of in-situ stress. J Cent South Univ Technol. 27(10):2864–2882. doi: 10.1007/s11771-020-4515-7.
- Chen SJ, Yin DW, Jiang N, Wang F, Guo WJ. 2019. Simulation study on effects of loading rate on uniaxial compression failure of composite rock-coal layer. Geomech Eng. 17:333–342.
- Chen SJ, Zhao ZH, Feng F, Zhang MZ. 2022. Stress evolution of deep surrounding rock under characteristics of bi-modulus and strength drop. J Cent South Univ. 29(2):680–692. doi: 10.1007/s11771-022-4945-5.
- Dou LM, Mu ZL, Li ZL, Cao AY, Gong SY. 2014. Research progress of monitoring, forecasting, and prevention of rockburst in underground coal mining in China. Int J Coal Sci Technol. 1(3):278–288. doi: 10.1007/s40789-014-0044-z.
- Dou LM, Zhou KY, Song SK, Cao AY, Cui H, Gong SY, Ma XT. 2021. Occurrence mechanism, monitoring, and prevention technology of rockburst in coal mines. J Eng Geol. 29:917–932.
- Du XL. 2021. Numerical simulation study of the effect of cohesion on simulation of strain-softening model. J Henan Polytech Univ Nat Sci. 40:186–193.
- Han CL, Zhang N, Li BY, Si GY, Zheng XG. 2015. Pressure relief and structure stability mechanism of hard roof for gob-side entry retaining. J Cent South Univ. 22(11):4445–4455. doi: 10.1007/s11771-015-2992-x.
- He J, Dou LM, Gong SY, Li J, Ma ZQ. 2017. Rock burst assessment and prediction by dynamic and static stress analysis based on micro-seismic monitoring. Int J Rock Mech Min Sci. 93:46–53. doi: 10.1016/j.ijrmms.2017.01.005.
- He J, Dou LM, Mu ZL, Cao AY, Gong SY. 2016. Numerical simulation study on hard-thick roof inducing rock burst in coal mine. J Cent South Univ. 23(9):2314–2320. doi: 10.1007/s11771-016-3289-4.
- He J. 2013. Research of mining dynamic loading effect and its induced rock burst in coal mine. [doctoral Thesis]. Xuzhou (China): China University of Mining and Technology.
- He MC, Guo PF, Chen SY, Gao YB, Wang YJ. 2017. Supporting technology of roadside in gob-side entry in 110 longwall mining method. 1st International Conference on Materials Science, Energy Technology, Power Engineering, Hangzhou, China, 15–16 April 2017.
- Iannacchione AT, Tadolini SC. 2016. Occurrence, prediction, and control of rock burst events in the U.S. Int J Min Sci Technol. 26(1):39–46. doi: 10.1016/j.ijmst.2015.11.008.
- Jiang FX, Yang SH, Cheng YH, Zhang XM, Mao ZY, Xu FJ. 2006. A study on microseismic monitoring of rock burst in coal mine. Chin J Geophys. 49:1511–1516.
- Kan JL, Dou LM, Li XW, Cao JR, Bai JZ, Chai YJ. 2022. Study on influencing factors and prediction of peak particle velocity induced by roof pre-split blasting in underground. Underground Space. 7(6):1068–1085. doi: 10.1016/j.undsp.2022.02.002.
- Li XH, Liang S, Yao QL, Zhai QD. 2012. Control principle and its application of rock burst in roadway driving along goaf with outburst-proneness surrounding rocks. J Min Saf Eng. 29:751–756.
- Li XL, Chen SJ, Li ZH, Wang EY. 2021. Rockburst mechanism in coal rock with structural surface and the microseismic (MS) and electromagnetic radiation (EMR) response. Eng Fail Anal. 124:105396. doi: 10.1016/j.engfailanal.2021.105396.
- Li ZL, Dou LM, Wang GF, Cai W, He J, Ding YL. 2015. Risk evaluation of rock burst through theory of static and dynamic stresses superposition. J Cent South Univ. 22(2):676–683. doi: 10.1007/s11771-015-2570-2.
- Liang S, Elsworth D, Li XH, Fu XH, Sun BY, Yao QL. 2017. Key strata characteristics controlling the integrity of deep wells in longwall mining areas. Int J Coal Geol. 172:31–42. doi: 10.1016/j.coal.2017.01.012.
- Liu XS, Ning JG, Tan YL, Xu Q, Fan DY. 2018. Coordinated supporting method of gob-side entry retaining in coal mines and a case study with hard roof. Geomech Eng. 15:1173–1182.
- Lu AL, Dou LM, Bai JZ, Chai YJ, Zhou KY, Kan JL, Cao JR, Song SK. 2021. Mechanism of hard-roof rock burst control by the deep-hole blasting: numerical study based on particle flow. Shock Vib. 2021:1–14. doi: 10.1155/2021/9527956.
- Ma Q, Tan YL, Zhao ZH, Xu Q, Wang J, Ding K. 2018. Roadside support schemes numerical simulation and field monitoring of gob-side entry retaining in soft floor and hard roof. Arab J Geosci. 11(18):1–13. doi: 10.1007/s12517-018-3904-9.
- Manouchehrian A, Cai M. 2017. Analysis of rockburst in tunnels subjected to static and dynamic loads. J Rock Mech Geotech. 9(6):1031–1040. doi: 10.1016/j.jrmge.2017.07.001.
- Manouchehrian A, Cai M. 2018. Numerical modeling of rockburst near fault zones in deep tunnels. Tunn Undergr Sp Tech. 80:164–180. doi: 10.1016/j.tust.2018.06.015.
- Meng NK, Bai JB, Chen Y, Wang XY, Wu WD, Wu BW. 2021. Stability analysis of roadside backfill body at gob-side entry retaining under combined static and dynamic loading. Eng Fail Anal. 127:105531. doi: 10.1016/j.engfailanal.2021.105531.
- Mohammad N, Reddish DJ, Stace LR. 1997. The relation between in situ and laboratory rock properties used in numerical modelling. Int J Rock Mech Min. 34(2):289–297. doi: 10.1016/S0148-9062(96)00060-5.
- Mu ZL, Liu GJ, Yang J, Zhao Q, Javed A, Gong SK, Cao JL. 2019. Theoretical and numerical investigations of floor dynamic rupture: a case study in Zhaolou Coal Mine, China. Safety Sci. 114:1–11. doi: 10.1016/j.ssci.2018.12.016.
- Pappas DM, Mark C. 1993. Behavior of simulated longwall gob material. Pittsburgh (PA): Department of the Interior, Bureau of Mines RI.
- Qi QX, Dou LM. 2008. Chongji Diya Lilun Yu Jishu. Xuzhou (China): China University of Mining and Technology Press.
- Qi QX, Li YZ, Zhao SK, Zhang NB, Zhen WY, Li HT, Li HY. 2019. Seventy years development of coal mine rockburst in China: establishment and consideration of theory and technology system. Coal Sci Technol. 47(9):1–40.
- Qian MG, Shi PW, Xu JL. 2010. Kuangshan Yali Yu Yanceng Kongzhi. Xuzhou (China): China University of Mining and Technology Press.
- Ranjith PG, Zhao J, Ju MH, De Silva R, Rathnaweera TD, Bandara AKMS. 2017. Opportunities and challenges in deep mining: a brief review. Engineering. 3(4):546–551. doi: 10.1016/J.ENG.2017.04.024.
- Salah AB, Ozbay U, Kieffer S; Salamon M. 2003. Three-dimensional strain softening modeling of deep longwall coal mine layouts. In: Andrieux P, Brummer R, Detournay C, Hart R, editors. Proceedings of the 3rd International FLAC Symposium, Sudbury, Canada; October 22–24; p. 233–239.
- Salamon M. 1990. Mechanism of caving in longwall coal mining. In: Rock Mechanics Contributions and Challenges: Proceeding of the 31st US Symposium; Golden, CO. p. 161–168.
- Si GY, Cai W, Wang SY, Li X. 2020. Prediction of relatively high-energy seismic events using spatial–temporal parametrisation of mining-induced seismicity. Rock Mech Rock Eng. 53(11):5111–5132. doi: 10.1007/s00603-020-02210-3.
- Tian ZC, Dong LH, Ma M, Liu YJ. 2013. Prevention and control technology research on rock burst of fully mechanized caving faces and gob-side entry. AMM. 353–356:303–306. doi: 10.4028/www.scientific.net/AMM.353-356.303.
- Wang GF, Gong SY, Dou LM, Wang H, Cai W, Cao AY. 2018. Rockburst characteristics in syncline regions and microseismic precursors based on energy density clouds. Tunn Undergr Sp Tech. 81:83–93. doi: 10.1016/j.tust.2018.06.026.
- Wang LH, Cao AY, Dou LM, Guo WH, Zhang ZY, Zhi S, Zhao YX. 2019. Numerical simulation on failure effect of mining-induced dynamic loading and its influential factors. Safety Sci. 113:372–381. doi: 10.1016/j.ssci.2018.12.011.
- Wang Q, He MC, Yang J, Gao HK, Jiang B, Yu HC. 2018. Study of a no-pillar mining technique with automatically formed gob-side entry retaining for longwall mining in coal mines. Int J Rock Mech Min. 110:1–8. doi: 10.1016/j.ijrmms.2018.07.005.
- Wang SW, Cao AY, Wang ZY, Cao JR, Liu YQ, Xue CC, Guo WH. 2022. Study on mechanism of rock burst in horizontal section mining of a steeply inclined extra-thick coal seam. Lithosphere. 2022(Special 11):7058797. doi: 10.2113/2022/7058797.
- Wang WJ, Hou CJ, Li XH. 2001. Analysis of rational positioning of roadway along goaf with fully mechanized caving under given deformation of main roof. J Hunan Univ Sci Technol. 2:1–4.
- Wang YJ, He MC, Yang J, Wang Q, Liu JN, Tian XC, Gao YB. 2020. Case study on pressure-relief mining technology without advance tunneling and coal pillars in longwall mining. Tunn Undergr Sp Tech. 97:103236. doi: 10.1016/j.tust.2019.103236.
- Wei CC, Zhang CG, Canbulat I, Cao AY, Dou LM. 2018. Evaluation of current rock burst control techniques and development of a rock burst management framework. Tunn Undergr Sp Tech. 81:129–143. doi: 10.1016/j.tust.2018.07.008.
- Wu R, He QY, Oh J, Li ZC, Zhang CG. 2018. A new gob-side entry layout method for two-entry longwall systems. Energies. 11(8):2084. doi: 10.3390/en11082084.
- Xia Z, Yao QL, Meng GS, Xu Q, Tang CJ, Zhu L, Wang WN, Shen Q. 2021. Numerical study of stability of mining roadways with 6.0-m section coal pillars under influence of repeated mining. Int J Rock Mech Min. 138:104641. doi: 10.1016/j.ijrmms.2021.104641.
- Xie FX. 2021. Control of gob-side roadway with large mining height in inclined thick coal seam: a case study. Shock Vib. 1–14.
- Xie HP, Gao F, Ju Y, Gao MZ, Zhang R, Gao YN, Liu JF, Xie LZ. 2015. Quantitative definition and investigation of deep mining. J China Coal Soc. 40: 1–10.
- Xin-Ping L, Qian D, Ting-Ting L. 2016. Model test on propagation of blasting stress wave in jointed rock mass under different in-situ stresses. Chin J Rock Mech Eng. 35(11):2188–2196.
- Xue Y, Cao Z, Shen W. 2019. Destabilization and energy characteristics of coal pillar in roadway driving along gob based on rockburst risk assessment. R Soc Open Sci. 6(7):190094. doi: 10.1098/rsos.190094.
- Yang ZQ, Liu C, Tang SC, Dou LM, Cao JL. 2018. Rock burst mechanism analysis in an advanced segment of gob-side entry under different dip angles of the seam and prevention technology. Int J Min Sci Techno. 28(6):891–899. doi: 10.1016/j.ijmst.2017.11.001.
- Zhang GC, He FL. 2016. Asymmetric failure and control measures of large cross-section entry roof with strong mining disturbance and fully-mechanized caving mining. J Rock Mech Geotech Eng. 35:13.
- Zhang KX, Zhang YJ, Ma ZQ, Bi WG, Yang YM, Li Y. 2015. Determination of the narrow pillar width of gob-side entry driving. J Min Saf Eng. 32:446–452.
- Zhang WL, Huo TH, Li C, Wang CW, Qu XC, Xin HW. 2021. Characteristics of valuable microseismic events in heading face of an underground coal mine using microseismic system. Shock Vib. 2021:1–10. doi: 10.1155/2021/6683238.
- Zhang YC, Yang SQ, Chen M, Zhang CW, Long JK. 2017. Deformation and failure mechanism of entity coal side and its control technology for roadway driving along next goaf in fully mechanized top coal caving face of deep mines. Rock Soil Mecha. 38:1103–1113.
- Zhao Y, Li X, Hou J. 2022. Research on asymmetric failure mechanism and control technology of roadway along gob in extra thick coal seam. Geotech Geol Eng. 40(2):1009–1021. doi: 10.1007/s10706-021-01940-7.
- Zhou KY, Dou LM, Li XW, Song SK, Cao JR, Bai JZH, Ma XT. 2022. Coal burst and mining-induced stress evolution in a deep isolated main entry area–A case study. Eng Fail Anal. 137:106289. doi: 10.1016/j.engfailanal.2022.106289.
- Zhu GA, Dou LM, Wang CB, Li J, Cai W, Ding ZW. 2017. Numerical investigation of the evolution of overlying strata and distribution of static and dynamic loads in a deep island coal panel. Arab J Geosci. 10(24):549. doi: 10.1007/s12517-017-3300-x.
- Zou QL, Zhang TC, Ma TF, Tian SX, Jia XQ, Jiang ZB. 2022. Effect of water-based SiO2 nanofluid on surface wettability of raw coal. Energy. 254:124228. doi: 10.1016/j.energy.2022.124228.