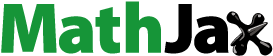
Abstract
The advent of non-pillar mining technology of self-formed roadway based on roof cutting theory (NPMTSFRRCT) has revolutionized the method of tackling the difficulties posed by hard suspended roofs in mining engineering. The design of roof cutting parameters plays a crucial role in determining the roof fracture characteristics. The principles of roof cutting parameter design have been analysed, with a focus on the key and challenging aspect of the collapse of single-layer thick hard rock under the condition of a thin immediate roof. A mechanical model of roof fracture has been established, and the impact of immediate roof thickness, roof cutting height, roof cutting angle, and main roof thickness on roof fracture has been analysed. A numerical model based on the UDEC software has been created, and the roof fracture, stress, and displacement variation characteristics have been studied using the failure criterion of polygonal blocks. The results of the theoretical analysis have been verified, and it was found that the roof fracture in partial roof cutting occurs in the form of hinge bite, while complete roof cutting results in step sinking. Engineering practice has shown that the deformation of the roadway surrounding rock has been effectively controlled.
1. Introduction
Since the twentieth century, roof accidents in both metal and coal mines have consistently accounted for a high proportion of incidents, resulting in significant fatalities and property damage (Maiti and Khanzode Vivek Citation2009; Palei and Das Citation2008; Indraratna et al. Citation2010; Islavath et al. Citation2020). The collapse and control of hard rock strata have become a pressing issue that has been extensively studied by researchers and engineers. There have been numerous successful cases of controlling hard rock strata using techniques such as blasting (Guo et al. Citation2022; Kuili and Sastry Citation2018; Li et al. Citation2020), mechanical cutting (Tai et al. Citation2020), and hydraulic fracturing (Huang and Wang Citation2015; Lv et al. Citation2018). This indicates that understanding the strength, layering, and thickness of rock layers is important for controlling the stability of hard roof and surrounding rocks in roadway (Jiang et al. Citation2023; Wang et al. Citation2022).
Due to the difficulty posed by hard suspended roofs and low coal recovery rates after coal mining, Chinese scholars developed non-pillar mining technology of self-formed roadway based on roof cutting theory (NPMTSFRRCT) (He, Gao, Yang, et al. Citation2017; He, Song, et al. 2017b). This technology involves: (1) excavate two roadways in the coal seam, (2) excavate the coal seam to form an open cut, (3) constructing drilling in the leading section of the reserved roadway, (4) using gathering energy blasting technology to create a pre-splitting surface in the hard rock layer, (5) the hard roof collapses in the gob along the pre-splitting surface after coal seam mining to form the roadway wall, and (6) the roadway is reserved for use in the next panel. This process makes it easier to reuse the roadway and reduces stress on the surrounding rock (Wang, Qin, et al. Citation2020; He, Gao, Yang, Gong et al. 2017; He et al. Citation2022). y:\tgnh\Vol01401\230108\FreshMss\TGNH_A_2272576_20231017071208277_17-Oct-2023_h13_m3\tgnh-2023-0219-20231016163721\graphic\NPMTSFRRCT is shown in . Including diagrammatic sketch of the overall model (), GSERRC (), and gather energy blasting ().
Figure 1. The diagrammatic sketch of NPMTSFRRCT. (a) Overall model, (b) GSERRC, and (c) gather energy blasting.

Since the implementation of NPMTSFRRCT in coal mining areas in China, it has made substantial contributions to improving coal recovery rates and reducing roadway excavation efforts (Wang, Liu, et al. Citation2020; Hu, Hou, et al. 2019). Given that the key technology is roof cutting, it is crucial to study the roof cutting height and roof cutting angle (Hu, He, et al. Citation2019; Sheng et al. Citation2022). The core idea behind NPMTSFRRCT is to sever the connection between the roadway roof and the gob side roof, thus relieving mining pressure. The design of roof cutting parameters is influenced by factors such as roof properties (strength and lithology), coal seam thickness, immediate roof thickness, roof swelling and breaking characteristics, main roof thickness, etc. Current research results suggest that roof cutting height and roof cutting angle play a decisive role in the collapse, crushing, and filling of gob waste. Increasing roof cutting height stabilizes the gob waste in advance, reduces roof movement time, and minimizes disturbance to the roadway (Gao et al. Citation2018; He et al. Citation2018). Additionally, given the diversity of lithology and composite layering in hard roofs, it is recommended to consider seeking the weak surface of layering as the roof cutting interface while ensuring that the collapsed waste can fill the gob, in order to facilitate rapid roof collapse (Ma et al. Citation2019). In addition, secondary factors such as porosity and water content in rock layers also have a slight impact on the cutting parameters, and these secondary factors will not be considered in this article (Zhu et al. Citation2021; Yang et al. Citation2019).
As NPMTSFRRCT becomes more widely adopted, its application scenarios have evolved from originally favourable geological conditions, such as thin coal seams and thin main roofs, to increasingly challenging and complex geological conditions, such as medium and thick coal seams, and thick and extra-thick main roofs, due to its evident benefits. However, further research is needed to address its challenges. Particularly in the case of thin immediate roofs and single, thick, or extra-thick main roofs, the hard roof has high strength and good integrity, making it difficult to completely cut it off. This is because as drilling depth increases, force transmission decreases, and the effect becomes more pronounced with a greater main roof thickness. Nevertheless, when roof cutting height exceeds the critical value, the uncut roof is expected to break and collapse under the influence of mine pressure. Thus, there is an urgent need to study incomplete roof cutting under current conditions to resolve the issue of hard-suspended roofs and achieve successful roadway formation.
2. Study on fracture conditions of hard roof
2.1. Basic principle of roof fracture
For clarity, we define a thin immediate roof as one that cannot fill the gob after mining, while a thick immediate roof refers to one that can fully fill the gob to support the overlying strata. Based on field experience, the crushing expansion coefficient of the immediate roof is typically between 1.2 and 1.35. For a coal seam that is 2.4 m high, the immediate roof thickness required to fill the gob is between 6.9 and 12 m. Therefore, the distinction between a thin and thick immediate roof can be easily determined based on this definition, which is specific to this articl.
The fracture behaviour of the hard main roof has a significant impact on both the safety of coal mining operations and the stability of the roadway. The design of roof cutting parameters of hard strata is largely influenced by its thickness and lithology. The basic principles of roof fracture are as follows:
Coal seam mining height and thick immediate roof. If immediate roof thickness is greater than that of the height of coal seam, this will cause the immediate roof to collapse and fill the gob according to the crushing and swelling properties, providing support to the overlying roof. In this case, the roof cutting height is equal to immediate roof thickness, as shown in .
Thin immediate roof. If immediate roof thickness is unable to fill the gob, then a significant portion of the main roof will form a suspended roof behind the working face. To ensure the safety of the working face and roadway, it is necessary to cut the roof and cause it to collapse, as illustrated in . The thickness and properties of the main roof are the important factors that influence the outcome:
The main roof thickness. When the main roof is of general thickness, the roof cutting height should reach the interface between the main roof and the overlying soft rock layer, as illustrated in . However, when the main roof is thick or extra thick, its properties must also be taken into account.
The main roof properties. If the main roof is composed of several layers of hard rock strata, the key is to identify the weak interface between these hard rock layers as the cutting surface in order to achieve partial roof cutting and partial collapse. This will help fill the gob to support the rock stratum that has not collapsed, as shown in . On the other hand, if the main roof is composed of a single layer of thick and hard rock stratum, the focus should be on determining the highest roof cutting height that can cause the thick and hard roof to completely collapse along the roof cutting surface. This would result in partial roof cutting and overall collapse, as shown in .
Figure 2. Fracture effect of main roof under different conditions. (a) Thick immediate roof, (b) thin immediate roof, (c) composite main roof, And (d) single thick layer main roof.

In conclusion, the collapse of a single layer of thick hard rock stratum when there is a thin immediate roof is the crucial and challenging aspect of roof cutting design (as depicted in ). Additionally, if the main roof thickness varies significantly in the same geological conditions, the roof cutting parameters also need to be adjusted accordingly.
2.2. Construction of mechanical model
In view of the suspended roof formed after mining, the gob side roof is considered as a cantilever beam, and the load of overlying rock layer is applied above the cantilever beam as a uniform force. The roof cutting surface is inclined to gob side and the dip angle with the upright direction is The mechanical model is as illustrated in . It is worth noting that this model was established under the condition of suspended roof in the gob. The collapsed gangue in the gob has no supporting effect on the roof. This article only considers the fracture mechanism of the suspended roof under different conditions, aiming to cut the roof through the optimal cutting parameters. The compression of the gob gangue after cutting the roof is not considered.
According to the roof cutting separatrix, the roof is divided into cut roof and uncut roof. So as to ensure that the uncut roof completely caving along the roof cutting interface under its own weight and the pressure of overlying rock, the tensile stress of uncut roof surface shall be greater than its tensile strength, meeting the following formula:
(1)
(1)
where
is tensile stress of uncut roof surface, MPa;
is ultimate tensile stress of hard rock, MPa.
The tensile stress of uncut roof surface can be derived by the formula (2):
(2)
(2)
where
is the bending moment of uncut roof surface, N
m;
is the bending section coefficient of uncut roof surface.
The bending moment and bending section coefficient of uncut roof surface are calculated by the following formula:
(3)
(3)
where
is the overburden load borne by main roof, N/m;
is the distance from uncut roof surface to the end of cantilever beam, m;
is the density of main roof rock,
is the main roof thickness, m;
is the height of uncut roof part, m.
and
are calculated by the following formula:
(4)
(4)
where
is immediate roof thickness, m;
is the roof cutting height, m;
is the breadth of plastic zone, m;
is the roadway breadth, m;
is the horizontal projection distance of cutting line, m;
is the remove from limit equilibrium zone to end of cantilever beam, m.
is calculated by the following formula (Li et al. Citation2012):
(5)
(5)
where l is the periodic weighting interval of main roof, m; S is the length of mining panel, m.
The tensile stress of uncut roof surface is calculated:
(6)
(6)
2.2.1. Typical case study
The coal seam thickness is 2.4 m in the third panel area of north wing of the 2 # coal seam in Tongxin Mine, Datong City, Shanxi Province, China, and average burial depth is 480 m. At initial stage of coal seam mining, there are two working faces that adopt NPMTSFRRCT. The roadway width and height are 5.2 and 3.6 m, respectively, the dip length of working face is 180 m, the immediate roof is silty mudstone with a thickness of 2–11 m. The main roof is mainly medium coarse sandstone with a thickness of 5.1–38.59 m. The tensile strength of main roof measured in the laboratory is 6.88 MPa, and the compressive strength is 120.5 MPa (for intact and uncracked rock masses). The working face layout and rock stratum histogram are shown in . Because the variation range of rock stratum thickness under this engineering geological condition is large, a typical case study based on this engineering background is of great significance and reference value for most mines.
Figure 4. Working face layout and rock stratum histogram. (a) Working face layout and (b) stratum histogram of coal and rock.

Based on the above analysis and geological parameters, we can get:
By substituting the above equation, we can get the expression between tensile stress of uncut roof surface and roof cutting height, roof cutting angle and roof thickness, as follows:
(7)
(7)
In order to study the roof fracture conditions, the immediate roof thickness is 2 and 4 m, respectively, and the main roof thickness is 10, 15, 20, 25 and 30 m, respectively. The expression of tensile stress of uncut roof surface under different conditions is shown in .
Table 1. Tensile stress of uncut roof surface under different conditions.
2.2.2. Result discussion
2.2.2.1. The influence of immediate roof thickness
In this article, the roof cutting height refers to the sum of immediate roof thickness and main roof thickness, and effective roof cutting height refers to main roof thickness to be cut.
The tensile stress of uncut roof surface changes with the roof cutting height and roof cutting angle when main roof thickness is 10 m and immediate roof thickness is 2 and 4 m, respectively, is shown in and . The specific analysis is as follows:
Figure 5. Change of tensile stress with roof cutting height and roof cutting angle when =2 m、
=10 m. (a) Change of tensile stress with roof cutting height and (b) change of tensile stress with roof cutting angle.

Figure 6. Change of tensile stress with roof cutting height and roof cutting angle when =4 m、
=10 m. (a) Change of tensile stress with roof cutting height and (b) change of tensile stress with roof cutting angle.

According to and , when the immediate roof thickness is 2 m and the roof cutting angle is 0° and 20°, respectively, the roof cutting height required for tensile stress of uncut roof surface to be greater than the ultimate tensile strength of main roof is 6.2 and 7.4 m, respectively. When the immediate roof thickness is 4 m, the above values are 8.2 and 9.8 m, respectively. It shows that when the roof cutting angle is the same, with the increase of immediate roof thickness, the roof cutting height required for tensile stress of uncut roof surface to reach the ultimate tensile strength of main roof increases, but the increase of roof cutting height is approximately equal to increase of immediate roof thickness. Therefore, under the condition of thin immediate roof, the influence of the change of immediate roof thickness on the roof cutting effect is relatively small; at the same time, with the increase of immediate roof thickness, the tensile stress of uncut roof surface decreases at the same roof cutting height and roof cutting angle.
According to and , when the immediate roof thickness is 2 m, the range of minimum roof cutting angle allowed when the tensile stress of uncut roof surface reaches the ultimate tensile stress of main roof is 14.7°, and the range of maximum roof cutting angle is 44.4°, when the immediate roof thickness is 4 m, the above values are 11.5° and 39.6°, respectively. It shows that with the increase of immediate roof thickness, the range of reasonable roof cutting angle allowed by the tensile stress of uncut roof surface reaching the ultimate tensile strength of main roof decreases.
2.2.2.2. The influence of roof cutting height and roof cutting angle
It shows from that tensile stress on uncut roof surface is proportional to roof cutting height and negatively correlated with roof cutting angle. Under the effect of roof cutting height, tensile stress of uncut roof surface increases slowly or remains unchanged at first, and then increases sharply; when the roof cutting height is small, the tensile stress of uncut roof surface decreases slowly as the increase of roof cutting angle, when the roof cutting height is large, the tensile stress of uncut roof surface decreases sharply with the increase of roof cutting angle.
As shown in , when the roof cutting angle is 0°, the roof cutting height required for the tensile stress of uncut roof surface to be greater than the ultimate tensile strength of main roof is 6.2 m, when the roof cutting angle is 20°, the above values are 7.4 m. It shows that with the increase of roof cutting angle, the roof cutting height required for the tensile stress of uncut roof surface to reach the ultimate tensile stress of main roof increases. As shown in , when the roof cutting height is 7 and 11 m, respectively, the allowable roof cutting angle range for the tensile stress of uncut roof surface to be greater than the ultimate tensile strength of main roof is 0–14.7° and 0–44.4° respectively. It shows that under the condition of a certain main roof thickness, the range of roof cutting angle allowed by the tensile stress of uncut roof surface is greater than the ultimate tensile strength of main roof increases with the increase of roof cutting height. Therefore, the higher roof cutting height, the smaller limit on roof cutting angle.
2.2.2.3. The influence of main roof thickness
As shown in , when the roof cutting angle is 20° and the main roof thickness are 10, 15, 20, 25, and 30 m, respectively, the roof cutting height required for the tensile stress of uncut roof surface to reach the ultimate tensile strength of main roof shall be at least 7.4, 12.8, 18.5, 24.5, and 30.8 m, respectively, the effective roof cutting height are 5.4, 10.8, 16.5, 22.5, and 28.8 m, respectively, accounting for 54%, 72%, 82.5%, 90%, and 96% of main roof thickness. Compared with complete roof cutting, the quantities of roof cutting are reduced by 4.6, 4.2, 3.5, 2.5, and 1.2 m, respectively. It shows that the greater main roof thickness, the greater roof cutting height required for the tensile stress of uncut roof surface to reach the same value.
It shows from that when the main roof thickness is 10, 15, 20, 25, and 30 m, respectively, the maximum allowable roof cutting angles are 44.4°, 34.5°, 28.1°, 23.6°, and 20.3°, respectively. It shows that with the increase of main roof thickness, the range of allowable reasonable roof cutting angle decreases.
The relationship between reasonable roof cutting height with roof cutting angle and main roof thickness is shown in . As main roof thickness increases, the roof cutting height required for the uncut surface to reach the ultimate tensile strength of the main roof gradually rises with changes in roof cutting angle, at rates of 19.35%, 23.08%, 25.85%, 28.27%, and 31.06%, respectively. This indicates that the influence of roof cutting angle on roof cutting effectiveness is dependent on main roof thickness. When main roof thickness is small, the influence of roof cutting angle is also small. However, as main roof thickness increases, the effect of roof cutting angle becomes more pronounced. During site construction, roof cutting angle is typically selected within a narrow range of 5°–20° to balance the reduction of roof collapse impact on the roadway with the suspended roof length and construction quantity. Therefore, the impact of roof cutting angle on the roof cutting effect is much smaller than that of roof cutting height and main roof thickness.
Figure 7. Change of tensile stress with roof cutting height and roof cutting angle when =2 m、
=15 m. (a) Change of tensile stress with roof cutting height and (b) change of tensile stress with roof cutting angle.

Figure 8. Change of tensile stress with roof cutting height and roof cutting angle when =2 m、
= 20 m. (a) Change of tensile stress with roof cutting height and (b) change of tensile stress with roof cutting angle.

Figure 9. Change of tensile stress with roof cutting height and roof cutting angle when =2 m、
= 25 m. (a) Change of tensile stress with roof cutting height and (b) change of tensile stress with roof cutting angle.

Figure 10. Change of tensile stress with roof cutting height and roof cutting angle when =2 m、
= 30 m. (a) Change of tensile stress with roof cutting height and (b) change of tensile stress with roof cutting angle.

Figure 11. The relationship between reasonable roof cutting height with roof cutting angle and main roof thickness.

To sum up, the tensile stress of uncut roof surface is affected by immediate roof thickness, roof cutting height and roof cutting angle, and main roof thickness, among which the roof cutting height and the main roof thickness are significant factors.
3. Numerical simulation research
3.1. Establishment of numerical model
Based on the above theoretical research, numerical simulation verification is carried out through the discrete element software UDEC. Establish a two-dimensional numerical model based on the geological conditions of the above typical working face, the length and height of model are 145.2 and 75 m, respectively. The horizontal displacement is fixed at left and right boundaries of model, the vertical displacement is fixed at the lower boundary of model. Mohr Coulomb criterion is used as the judgment criterion for simulating blocks, and Coulomb slip criterion is used as the judgment criterion for joints. The numerical model is shown in . The mechanical properties of coal and rock blocks are derived by processing and testing the samples taken on site in the laboratory, and then calibrating them by rock mass mechanics parameter analysis software (Roclab-rock strength analysis software) based on Hoek-brown criterion (Hoek and Brown Citation1997, Citation1980; He et al. Citation2020), as shown in . Where, GSI is the constant index for evaluating fractured rock mass, is material parameter of complete rock, D is the degree of rock fragmentation. Apply 12 MPa vertical stress on the top of model to represents 480 m high rock stratum.
Table 2. Mechanical properties of coal and rock mass.
3.2. Generation of polygonal blocks in UDEC
When simulating mining engineering problems in UDEC model, regular rectangular blocks are often used to simulate the breaking and collapse of rocks. Research on the fractures characteristics and location of roof often presuppose fissure at the location of predicted fractures, so that it is easy to get the results predicted by the author. However, it is questionable whether artificial tectonic fissure have an impact on the simulation of real situation. Voronoi joint generator can divide a regular block into polygonal blocks of any size, and the connection between blocks is completed through point contact, when the stress between polygon blocks exceeds their bonding strength, the rock will break. This method is beneficial and true to the study of roof fracture characteristics and crack propagation (Kazerani and Zhao Citation2010; Kazerani Citation2013a, Citation2013b; Li et al. Citation2016).
3.3. Simulation scheme
In order to verify the theoretical analysis results, a reasonable simulation scheme is designed. In the simulation scheme, the immediate roof thickness is 2 m, the roof cutting angle is 15°, and the main roof thickness is 10–30 m. The immediate roof thickness is selected according to the conditions of thin immediate roof. The selection of roof cutting angle is due to the analysis in Section 2.2.2 that its impact on the roof cutting effect is less than the roof cutting height and the main roof thickness, and the roof cutting angle is 15° in the field practice. Therefore, the variation of the roof cutting angle is not considered in numerical simulation. According to the theoretical research, the selection of the roof cutting height in each simulation scheme is shown in . For Scheme 1, the roof cutting height of 0 and 5 m are added to investigate the effects of no roof cutting and unreasonable partial roof cutting, in comparison to reasonable partial roof cutting and complete roof cutting.
Table 3. Numerical simulation project.
The research process involved the analysis of roof fracture characteristics and stress evolution under different roof cutting conditions in Sections 3.4.1 and 3.4.2. In Section 3.4.3, the displacement characteristics of the four roof cutting plans in Scheme 1 were studied and compared to the displacement situation in Scheme 2 for a comprehensive analysis.
3.4. Discussion and analysis of simulation results
3.4.1. Roof fracture characteristics under different roof cutting conditions
The roof fracture characteristics under different roof cutting conditions are shown in , and the analysis is as follows:
Figure 13. Roof fracture characteristics under different roof cutting conditions. (a) =10m-
=0 m, (b)
= 10m-
=5 m, (c)
= 10 m-
= 7 m, (d)
= 10 m-
=12 m, (e)
=15 m-
= 12 m, (f)
= 15 m-
= 17 m, (g)
= 20 m-
=17.5 m, (h)
= 20 m-
=22 m, (i)
=25 m-
= 23 m, (j)
= 25 m-
=27 m, (k)
= 30 m-
= 28.5 m, and (l)
= 30 m-
= 32 m.

shows the roof fracture characteristics of no roof cutting, unreasonable partial roof cutting, reasonable partial roof cutting and complete roof cutting under the same roof conditions (Scheme 1). It can be seen that when the roof cutting height is 7 and 12 m, the main roof fracture along the cutting surface, indicating that when the partial roof cutting height reaches the roof cutting height allowed by the ultimate tensile strength of main roof, the partial roof of no cutting will break and fall under mine pressure, which providing effective protection to the roadway. However, when the roof cutting height is 0 and 5 m, due to insufficient roof cutting height or no roof cutting, the main roof above the goaf side has no fracture dislocation, which cause great disturbance to the roadway in the process of bending and sinking, which is intuitively shown as roof sinking and side bulge ().
shows the numerical simulation diagram of reasonable partial and complete roof cutting under different main roof thickness. Analysing from the smoothness of roof fracture surface, because the gob side roof will pull the roadway roof when it collapses under the condition of reasonable partial roof cutting, resulting in rough and uneven fracture surface, which is in the form of hinge bite. When the roof is completely cut, because cuts off the connection between roadway roof and gob side roof, the impact of gob side roof collapse on roadway roof is relatively small, and the fracture surface is relatively flat, which is in the form of step sinking. When the roof collapses the roadway roof is equivalent to a short cantilever beam, which inclines from the virgin coal side to gob side, and is mainly supported by virgin coal, gob gangue and roadway support.
3.4.2. Stress variation characteristics of roof fracture under different roof cutting conditions
The pre-cracking of hard roof, the mining of coal seam, and the collapse of roof lead to redistribution of stress around the roadway. It is important to understand the stress changes under the conditions of different main roof thickness and different roof cutting height for roof cutting design and roadway maintenance. The stress variation characteristics of roof fracture under different roof cutting conditions are illustrated in . For the same main roof thickness, the higher roof cutting height, the smaller the stress concentration level and region of roadway, indicating that increasing the roof cutting height reduces the impact on roadway roof when rock stratum above coal seam collapses, and stress relief degree is more obvious, as shown in . Although the roof cutting height increases, the stress of roadway surrounding rock increases with the increase of main roof thickness (). This is because the thicker the main roof is, the stronger ground pressure appearance caused by its collapse. Although the roof is cut, the roadway surrounding rock is inevitably affected by the collapse of thick and hard rock strata, indicating that the increase of main roof thickness has greater impact on the roadway surrounding rock than the increase of roof cutting height to a certain extent.
3.4.3. Characteristics of roadway displacement change of roof fracture under different roof cutting conditions
The displacement change characteristics of roadway roof and side with roof fracture under different roof cutting conditions are shown in and , respectively. The specific analysis is as follows:
Figure 15. Vertical displacement of roadway roof under different roof cutting conditions. (a) Vertical displacement of roadway roof with the same main roof and different roof cutting height and (b) vertical displacement of roadway roof with different main roof and different roof cutting height.

Figure 16. Horizontal displacement of roadway side under different roof cutting conditions. (a) Horizontal displacement of roadway side with the same main roof and different roof cutting height and (b) horizontal displacement of roadway side with different main roof and different roof cutting height.

shows the roadway roof displacement under the conditions of the same main roof and different roof cutting height (Scheme 1). It can be seen that the overall displacement of the roadway roof presents asymmetric deformation from solid coal side to goaf side. The smaller the roof cutting height is, the greater the roof subsidence is, and the more obvious the asymmetry is. When the roof cutting height is 0 and 5 m, respectively, due to no roof cutting or insufficient roof cutting height, the subsidence of roadway roof increases sharply, and the maximum displacement is 587.2 mm. When the roof cutting height is 7 and 12 m, respectively, the roof subsidence is much smaller, indicating that reasonable partial roof cutting can basically achieve the same effect as complete roof cutting. Therefore, when it is difficult to construct under thick main roof conditions, reasonable partial roof cutting is an economic and effective means.
shows the vertical displacement of roadway roof with reasonable partial roof cutting and complete roof cutting under different main roof thickness. It can be seen that with the increase of main roof thickness, the roadway roof subsidence increases. Compared with the roof subsidence when the roof cutting height is insufficient in , although the main roof thickness has increased, a reasonable roof cutting has been carried out, and so the roadway surrounding rock condition is relatively good, which again proves the effectiveness of reasonable partial roof cutting.
Based on the coordinated deformation of roadway roof and side, the horizontal displacement trend of roadway side in is roughly the same as that in . The main area of roof deformation is at the roof cutting side, while the primary location of side deformation is at the middle of the solid coal side.
Based on the above theoretical analysis and numerical simulation research, it is found that the main roof thickness and roof cutting height have a significant impact on the stress environment and displacement characteristics of the roadway surrounding rock. The main manifestation is that a larger cutting height can reduce the stress and displacement of the roadway surrounding rock, which is consistent with the research in many literature (Hu, He, et al. Citation2019; Tai et al. Citation2020). In engineering practice, it is necessary to carry out complete roof cutting if the roof cutting conditions permit. But in view of the complexity and difficulty of the site construction, reasonable partial roof cutting can also solve the problem of hard suspended roof, basically achieving the same effect as complete roof cutting.
Taking a 1000 m long roadway as an example, the main roof thickness is 10 m, the drill hole spacing is 0.5 m, the charge length is 0.2 m, 200 g per roll of explosives, the 43,321 charge structure is adopted in single hole, and the length of shaped charge tube is 1.5 m. If a reasonable partial roof cutting is carried out, the amount of drilling work of about 10,000 m can be reduced, and the amount of explosives of 3466 kg can be saved.
4. Field application
Taking the above-mentioned cases as engineering background, the theoretical analysis and numerical simulation were carried out on the site to verify. In the second working face for GSERRC, the typical sections are selected for research. The main roof thickness at selected typical sections is 10 and 15 m, respectively. According to the theoretical and numerical research, it is obtained that under the insufficient roof cutting, the roof cutting height allowed that the tensile stress of uncut roof surface is greater than ultimate tensile stress of main roof is at least 7 and 12 m, respectively. The field test process is shown in .
Figure 17. The field test process. (a) Roof presplitting preparation, (b) symmetrical crack in borehole peering, and (c) the formation effect of GSERRC.

Five monitoring stations are set in the above two typical sections to monitor surrounding rock deformation, including the convergence of roof and floor, and convergence of virgin coal. The measuring points are selected in the two typical sections for data statistics, as shown in . The monitoring data shall be recorded when working face lags behind measuring station by 60 m until the surrounding rock deformation becomes stable.
Figure 18. Surrounding rock deformation monitoring curve when main roof thickness is 10 and 15 m, respectively. (a) main roof thickness is 10 m and (b) main roof thickness is 15 m.

The following is an overview of the monitoring results:
The deformation monitoring curve undergoes following three stages, of which three stages when main roof thickness is 10 m are accelerated deformation stage (the working face is −60∼+12.5 m away from measuring station), slow deformation stage (the working face is +12.5∼+78.3 m away from measuring station), and stable stage (the distance between working face and measuring station is more than +78.3 m) (see ). When the main roof thickness is 15 m, the surrounding rock deformation has the same rule (see ).
The maximum convergence of roof and floor is 116.9 and 157.3 mm, respectively, and the maximum deformation of solid coal wall is 44.5 and 68.5 mm, respectively, indicating that the surrounding rock deformation is also large under the condition of large main roof thickness. Second, it shows from the comparison in that the accelerated deformation distance when main roof thickness is 15 m is greater than that when main roof thickness is 10 m.
From the field view, after the mining, the roadway surrounding rock is basically within the controllable range of deformation, and the roadway remains stable for a long time, achieving a reasonable partial roof cutting and successful formed roadway, which is consistent with theoretical research and numerical simulation.
5. Conclusions
The roof cutting design depends on various factors such as the height of the coal seam being mined, the immediate roof thickness, the crushing and swelling properties of the collapsed rock, the main roof thickness, and the layering of the main roof. The collapse of a single, thick, hard rock stratum under conditions of a thin immediate roof presents a significant challenge in the roof cutting design process. The findings of this study are as follows:
The tensile stress on the uncut roof surface is proportional to the roof cutting height and inversely related to the roof cutting angle. As the roof cutting angle increases, the roof cutting height required for the tensile stress of uncut roof surface to reach the ultimate tensile strength of main roof increases. However, compared to the roof cutting height, the impact of the roof cutting angle on the roof fracture is minimal.
With increasing immediate roof thickness, the roof cutting height required for tensile stress of uncut roof surface to reach the ultimate tensile stress of main roof increases, but the roof cutting height increase is roughly equal to the increase in immediate roof thickness, therefore immediate roof thickness has no effect on the effective roof cutting height.
The higher the main roof thickness, the higher the roof cutting height required to reach the same tensile stress on the uncut roof surface. With the main roof thickness increase, the allowable range of the reasonable roof cutting angle decreases, but the influence of the roof cutting angle on the roof cutting effect increases.
The influence of the increase of the main roof thickness on the roadway surrounding rock under the reasonable roof cutting condition is greater than the increase of the roof cutting height to a certain extent.
Partial roof cutting results in a hinge bite fracture, while complete roof cutting results in a step sink fracture.
Acknowledgements
The authors also thank the reviewers for their helpful comments.
Disclosure statement
The authors declare that they have no known competing financial interests or personal relationships that could have appeared to influence the work reported in this article.
Data availability statement
The data used to support the findings of this research are included within the article.
Additional information
Funding
References
- Gao YB, He MC, Yang J, Ma XG. 2018. Experimental study of caving and distribution of gangues influenced by roof fracturing in pillarless mining with gob-side entry retaining. J China Univ Min Technol. 47(01):21–31 + 47.
- Guo S, Zhang Q, He M, Wang J, Liu J, Ming C, Guo L, Fan L. 2022. Numerical investigation on rock fracture induced by a new directional rock-breaking technology. Eng Fract Mech. 268:108473. doi:10.1016/j.engfracmech.2022.108473.
- He F, Xu X, Qin B, Li L, Lv K, Li X. 2022. Study on deformation mechanism and control technology of surrounding rock during reuse of gob side entry retaining by roof pre-splitting. Eng Fail Anal. 137:106271. doi:10.1016/j.engfailanal.2022.106271.
- He MC, Gao YB, Yang J, Guo ZB, Wang EY, Wang YJ. 2017. An energy-gathered roof cutting technique in no-pillar mining and its impacton stress variation in surrounding rocks. Chin J Rock Mech Eng. 36(6):1314–1325.
- He M, Gao Y, Yang J, Gong W. 2017. An innovative approach for gob-side entry retaining in thick coal seam longwall mining. Energies. 10(11):1785. doi:10.3390/en10111785.
- He MC, Guo PF, Wang J, Wang H. 2018. Experimental study on gob-side entry formed by roof cut of broken roof at shallow depth of Hecaogou No. 2 Coalmine. Chin J Geotech Eng. 40(03):391–398.
- He MC, Song ZQ, Wang A, Yang HH, Qi HG, Guo ZB. 2017. Theory of longwall mining by using roof cuting shortwall team and 110method—the third mining science and technology reform. Coal Sci Technol Magaz. 1:1–9 + 13.
- He WR, He FL, Zhao YQ. 2020. Field and simulation study of the rational coal pillar width in extra‐thick coal seams. Energy Sci Eng. 8(3):627–646. doi:10.1002/ese3.538.
- Hoek E, Brown ET. 1997. Practical estimates of rock mass strength. Int J Rock Mech Min Sci. 34(8):1165–1186. doi:10.1016/S1365-1609(97)80069-X.
- Hoek E, Brown ET. 1980. Underground excavation in rock. London: Institute of Mining and Metallurgy.
- Huang BX, Wang YS. 2015. Field investigation on crack propagation of directional hydraulic fracturing in hardroof. J Chin Coal Soc. 40(9):2002–2008.
- Hu J, He M, Wang J, Ma Z, Wang Y, Zhang X. 2019. Key parameters of roof cutting of gob-side entry retaining in a deep inclined thick coal seam with hard roof. Energies. 12(5):934. doi:10.3390/en12050934.
- Hu T, Hou GY, Li ZX, Li ZH, Xie BB, Chen JP, Cui YK. 2019. Study on influence of advanced deep-hole blasting pre-splitting roof on stability of gob side entry retaining. J Min Sci Technol. 4(04):299–307.
- Indraratna B, Oliveira DA, Brown ET, de Assis AP. 2010. Effect of soil–infilled joints on the stability of rock wedges formed in a tunnel roof. Int J Rock Mech Min Sci. 47(5):739–751. doi:10.1016/j.ijrmms.2010.05.006.
- Islavath SR, Deb D, Kumar H. 2020. Development of a roof-to-floor convergence index for longwall face using combined finite element modelling and statistical approach. Int J Rock Mech Min Sci. 127:104221. doi:10.1016/j.ijrmms.2020.104221.
- Jiang B, Xin Z, Zhang X, Deng Y, Wang M, Li S, Ren W. 2023. Mechanical properties and influence mechanism of confined concrete arches in high-stress tunnels. Int J Min Sci Technol. 33(7):829–841. doi:10.1016/j.ijmst.2023.03.008.
- Kazerani T. 2013a. A discontinuum-based model to simulate compressive and tensile failure in sedimentary rock. J Rock Mech Geotech Eng. 5(5):378–388. doi:10.1016/j.jrmge.2013.07.002.
- Kazerani T. 2013b. Effect of micromechanical parameters of microstructure on compressive and tensile failure process of rock. Int J Rock Mech Min Sci. 64:44–55. doi:10.1016/j.ijrmms.2013.08.016.
- Kazerani T, Zhao J. 2010. Micromechanical parameters in bonded particle method for modelling of brittle material failure. Num Anal Meth Geomech. 34(18):1877–1895. doi:10.1002/nag.884.
- Kuili S, Sastry VR. 2018. A numerical modelling approach to assess the behaviour of underground cavern subjected to blast loads. Int J Min Sci Technol. 28(6):975–983. doi:10.1016/j.ijmst.2018.05.015.
- Li MZ, Ma ZM, Xue DL, Yuan YH. 2020. Research of cumulative energy blasting technology with deep and shallow hole combined in hard roof. J Min Sci Technol. 5(06):616–623.
- Li X, Ju M, Yao Q, Zhou J, Chong Z. 2016. Numerical investigation of the effect of the location of critical rock block fracture on crack evolution in a gob-side filling wall. Rock Mech Rock Eng. 49(3):1041–1058. doi:10.1007/s00603-015-0783-1.
- Li YF, Hua XZ, Cai RC. 2012. Mechanics analysis on the stability of key block in the gob-side entry retaining and engineering application. J Min Safety Eng. 29(03):357–364.
- Lv HY, Liu F, Li LH, Chen ZB. 2018. Study on directional hydraulic fracturing of prefabricated fissures in top coal. J Min Sci Technol. 3(6):553–560.
- Ma XG, He MC, Li Z, Liu YX, Yu GY, Du HR. 2019. Key parameters of gob-side entry retaining automatically formed by roof cuttingand blasting in compound roof condition. J Chin Univ Min Technol. 48(02):236–246.
- Maiti J, Khanzode Vivek V. 2009. Development of a relative risk model for roof and side fall fatal accidents in underground coal mines in India. Saf Sci. 47(8):1068–1076. doi:10.1016/j.ssci.2008.12.003.
- Palei SK, Das SK. 2008. Sensitivity analysis of support safety factor for predicting the effects of contributing parameters on roof falls in underground coal mines. Int J Coal Geol. 75(4):241–247. doi:10.1016/j.coal.2008.05.004.
- Sheng FT, Zhang Y, Wei WS, Duan YQ, Mao KB. 2022. Influence of roof cutting parameters on stability of surrounding rock OFGOB-side entry retaining. J Min Sci Technol. 7(3):322–332.
- Tai Y, Yu B, Xia B, Li Z, Xia H. 2020. Research on stress release for the gob-side roadway using the roof-cuttingtechnology with a chainsaw arm. R Soc Open Sci. 7(3):191663. doi:10.1098/rsos.191663.
- Wang Q, Qin Q, Jiang B, Jiang Z, He M, Li S, Wang Y. 2020. Geomechanics model test research on automatically formed roadway by roofcutting and pressure releasing. Int J Rock Mech Min Sci. 135:104506. doi:10.1016/j.ijrmms.2020.104506.
- Wang Q, Xu S, Xin Z, He M, Wei H, Jiang B. 2022. Mechanical properties and field application of constant resistance energy-absorbing anchor cable. Tunnell Underground Space Technol. 125:104526. doi:10.1016/j.tust.2022.104526.
- Wang Y, Liu J, Yang J, Wang Q, Huang R, Tian X, He M. 2020. Stability characteristics of a fractured high roof under nonpillar mining with an automatically formed roadway by using a visualized discrimination approach. Energy Sci Eng. 8(5):1541–1553. doi:10.1002/ese3.611.
- Yang X, Wang J, Zhu C, He M, Gao Y. 2019. Effect of wetting and drying cycles on microstructure of rock based on SEM. Environ Earth Sci. 78(6):183. doi:10.1007/s12665-019-8191-6.
- Zhu C, He MC, Jiang B, Qin XZ, Yin Q, Zhou Y. 2021. Numerical investigation on the fatigue failure characteristics of water-bearingsandstone under cyclic loading. J Mt Sci. 18(12):3348–3365. doi:10.1007/s11629-021-6914-0.