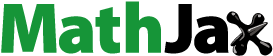
Abstract
The control of broken rock mass roadways has always been a difficult problem in metal hard rock mines. In this paper, the mechanical mechanism of anchor net support is characterized and simulated through the physical model test of the prestressed support self-bearing structure of the broken rock mass. The deformation characteristics and interaction relationships of the surrounding rock and the support body under different dynamic impact effects are obtained by using the embedded anchor strain gauge and rock micro-strain sensors. The stress evolution process and deformation characteristics of the anchor and rock mass of the prestressed support self-bearing structure of the broken rock mass under different loads are simulated by applying Phase2. The results are in good agreement with the results of the physical model test. Based on the theory of surrounding rock compression arch and the Hoek-Brown criterion, the minimum anchorage force of the prestressed anchor to maintain the stability of the surrounding rock is derived and calculated by the limit equilibrium rule. The research results explain the mechanical mechanism of the broken rock mass support from the aspects of physical experiments, numerical simulations and theoretical derivations, which can provide theoretical guidance for the support design of practical engineering.
1. Introduction
With the mining entering the deep part, the influence of complex geological conditions leads to an increasing number of engineering disasters (Ranjith et al. Citation2017; Dong et al. Citation2019). Support technology is the key to ensuring the construction and production safety of underground engineering such as mines(Wang et al. Citation2022; Kang et al. Citation2023; Wang et al. Citation2023). Compared with surface open-pit mining, underground mining often faces more complex geological conditions, which greatly increases the difficulty of roadway support work (Li et al. Citation2022). Especially for deep roadway, due to the influence of high ground stress, high ground temperature, high well depth, and mining disturbance in the engineering area, the rock mass is more fragmented, making the support work of the roadway more difficult (Guo et al. Citation2019; Rahimi et al. Citation2020).
In recent years, domestic and foreign scholars have proposed various methods for the stability control of the broken area in underground mines, which have solved many supporting problems of roadways in the broken area of underground mines. Zhu et al. proposed the "three-shell" collaborative support technology to solve the problems of large surrounding rock deformation around the large cross-section chamber in the deep mine and the instability of the supporting structure. The development range of the plastic zone in the surrounding rock is controlled by the stress shell, reducing the difficulty of surrounding rock control (Zhu et al. Citation2021). Chu et al. identified the advantages of multi-level support using FLAC-3D in view of the poor support effect and severe deformation and failure of the surrounding rock of the roadway under the stress of deep mining (Chu et al. Citation2022). Zhao et al. based on the plastic softening and dilatancy effect of the rock mass, found that the control effect of anchor rod support on the plastic zone of surrounding rock in deep wells is greater than that of lining support (Zhao, Qin, et al. Citation2023). Wang et al. developed a closed concrete (CC) support system, and the effectiveness of the CC support system in controlling the surrounding rock was demonstrated through field tests (Wang et al. Citation2017). Based on the analysis of the failure mechanism of fractured rock mass and the evaluation of rock mass quality, Zhao et al. proposed a corresponding support scheme, and obtained the validity test through numerical simulation and field tests (Zhao, Zhu, et al. 2023). Li et al. combined the methods of experience, numerical value, and field monitoring to conduct stability analysis and support design for the transportation roadway affected by mining activities, and used RS2 and UNWEDGE software to analyze the support system determined by the empirical method. It was found that the support design considering multiple aspects achieved a better support effect (Li et al. Citation2023). Yang et al. proposed an improved back baffle support control scheme based on the discrete element simulation method (UDEC software) (Yang et al. Citation2018). Qin et al. proposed the "Migrate-Transfer-Control" Support System, which has achieved good results in the field (Qin et al. Citation2023). Li et al. proposed an improved combined support scheme of "double-layer long anchor - net - shotcrete and CFST (concrete-filled steel tube)" based on the analysis of the failure mechanism of the surrounding rock (Li et al. Citation2020). Wang et al. proposed a suitable coupling support countermeasure based on the test results and mechanism transformation, including anchors, metal net, hollow grouting anchor cables, and steel fiber concrete, to reduce nonlinear large deformations and potential risks during the mining process (Wang et al. Citation2019). Skrzypkowski et al. presented a method regarding the yielding arch support of the prepared working face in the hard coal seam, which effectively decreased the deformation of the roadway (Skrzypkowski et al. Citation2022). Tahmasebinia et al. employed the anchor cable support featuring high strength and sensitivity during the process of roadway driving under the condition where the rock mass is cracked and tends to release seismic energy in the form of vibration, achieving good results (Tahmasebinia et al. Citation2022). However, due to the development of joint fissures in the underground broken area, low rock strength, diverse lithology, and complex mechanical environment, various support technologies still have limitations. Especially for deep roadways, under the influence of impact ground pressure and high mining-induced stress, sudden and high-intensity geological disasters such as rock bursts are prone to occur (Han et al. Citation2022). The commonly used support methods currently mainly include active support and passive support (Hao et al. Citation2021; Han et al. Citation2023; Li and Høien Citation2023).
Passive supports, such as steel arches and lining supports (Han et al. Citation2010; Editorial Citation2015). The principle of passive support mainly relies on the strength of the support structure itself to resist the damage of ground pressure on the roadway. For deep rock masses, the mining-induced stress is often much greater than the strength of the support body. Using traditional passive support, it is difficult to effectively ensure the stability of the surrounding rock of the roadway (Hou and Li Citation2001; Hua Citation2006). As illustrated in , when the mining-induced stress exceeds the maximum value that the steel arch can withstand, significant plastic deformation occurs in the U-steel arch. Furthermore, due to the unevenness of the excavation surface and the rigidity of the steel, the support structure often has difficulty fitting the surface of the surrounding rock. This support method often fails to ensure the safety of the working face.
Figure 1. Typical failure cases of passive support and active support: (a) passive support, (b) active support.

Active supports, such as anchor rod support and anchor cable support (Chen et al. Citation2012). The active support emphasizes the integrity of the support structure and the surrounding rock, and resists damage by enhancing the bearing capacity of the surrounding rock itself. As one of the most commonly used types of active support, anchor rod support is a rod-like structure that can be anchored inside the rock mass. Based on the anchoring method, it can be divided into expansion shell type, pipe seam type, hydraulic expansion anchor rod, resin anchor rod, cement mortar anchor rod, etc.(Hou and Gou Citation2000). Due to its simple and effective support method and low support cost, anchor rod support is widely used in underground mines and underground engineering at home and abroad. However, for the rock mass with severe weathering and alteration and developed joint fissures, anchor rod support cannot prevent the sliding of the broken rock between the anchor rods. Therefore, anchor rod support is generally combined with other support forms for joint support, such as metal net and shotcrete. However, the action mechanism of anchor rod support is not very clear at present. The selection of support methods and parameters in some mines is unreasonable, especially for the deep and strongly mining-induced rock mass. Under the action of dynamic impact, the supporting body cannot exert its anchoring effect on the surrounding rock, which easily leads to the failure of roadway support, and a large number of roadways fall into the situation of repeated support, with the previous repair and subsequent collapse. As shown in , in some mines using anchor rod support, the anchor rods do not tightly adhere to the surface of the surrounding rock, resulting in the anchor rods not forming an integral with the rock mass, and often fails to achieve a good supporting effect. The reason for this is also the unclear supporting mechanism (Xin et al. Citation2024). Therefore, the study of the supporting mechanism of anchor rods and the mechanical properties under dynamic impact is of great significance for the scientific and reasonable design of support methods.
The theory of roadway support mainly studies the interaction mechanism between the support structure and the surrounding rock, and its development process is gradually in-depth with the continuous progress of rock mechanics. At present, the theoretical support mechanism of anchors is mainly divided into the theory of suspending action, the theory of composite beam, and the theory of composite arch. The suspension theory means that the anchor rod can suspend and fix the weak rock layer of the roadway roof to the stable rock layer above (Dong et al. Citation1994; Zhang and Nian Citation2002; Kang Citation2005). The composite beam theory means that when the joint fissures of the rock mass in the roadway roof are more developed and there is no relatively stable rock mass within the anchorage range, the suspending effect of the anchor rod will not play a dominant role (Wang Citation2007; Kang Citation2016, Citation2021). At this time, the mechanism of the anchor rod is mainly to bond several relatively weak rock layers together, on the one hand, to prevent them from sliding and slipping along the structural plane, on the other hand, to combine several thinner rock layers into a thicker rock layer, thereby increasing its shear strength, and the overall strain and deflection will also become smaller.
The main content of the composite arch theory is that after the anchor rods are anchored in the broken area of the roof of the roadway, two end parts of the anchor rods will form a conical compressive stress field. At this time, if the adjacent spacing of the anchor rods is selected reasonably, the cones formed between adjacent anchor rods will overlap each other, and finally form an arched compressive stress zone, which is the composite arch (Yang Citation2010). The composite arch can bear the radial stress above the rock mass, thereby enhancing the overall strength of the rock mass. Since this theory was proposed, there has been no effective theoretical explanation and related experimental data verification. Therefore, this paper characterizes and measures the supporting mechanism through similar physical model experiments, verifies it through numerical simulation, and deduces the anchoring force based on the limit equilibrium rule.
2. Physical model test
2.1. Model preparation
The production of the physical model of the self-supporting structure of the pre-stressed support of the broken rock mass mainly includes the following six steps, as shown in :
Step 1: Select several pre-stressed anchor rods 0.5m long, and paste the 120-10AA type resistance strain gauge on the selected pre-stressed anchor rods. Four sets of strain gauges are pasted on each anchor rod. With the head of the anchor rod as the coordinate origin and the tail as the end point, the positions of each strain gauge are 0.05m, 0.2m, 0.3m, and 0.45m, respectively. The purpose is to measure the deformation at both ends and the middle part of the anchor rod, and use insulating tape to protect and fix the strain gauge and the conductor.
Step 2: To minimise the influence of the boundary of the metal frame on the test results, after taking into account the effects of the processing difficulty and the test site limitations, a metal frame with a length, width, and height of 2 m, 1.5, and 0.5 m was customised. Lay a detachable fixed plate at the bottom of the metal frame, and the temporary fixed plate needs to be perforated at the preset position of the anchor rod for the installation of nuts. The spacing of each hole is 0.25m. The length of the anchor rod is two times the row spacing between them, and this is considered based on the extreme case that the row spacing between the anchor rods commonly employed in the mine support engineering is not larger than half the length of the anchor rod. Set the tray at the opening position on the fixed plate, and then lay the metal net above the tray. Insert the rod body of the anchor rod into the opening of the fixed plate, and use the nut to connect the lower part of the fixed plate with the rod body of the anchor rod. The conductor of the resistance strain gauge on the rod body of the anchor rod passes through the pore for connection to the measuring equipment.
Step 3: Fill the broken rocks into the metal frame, and pre-embed three RH-300 type micro-strain sensors at the geometric center position of the model and lead out the wires, in order to prevent the inaccurate measurement of the deformation due to the influence of the boundary effect.
Step 4: After the metal frame is filled with enough rock to form the rock mass, install the tray and nut on the exposed part of the anchor rod at both ends of the rock mass, and make the torque reach 50N·m.
Step 5: Remove the temporary fixed plate, and after the support structure is completely stable, the physical model of the self-supporting structure of the pre-stressed support of the broken rock mass can be obtained.
Step 6: Connect each conductor to the AFT-CM-10 type static strain gauge for subsequent experimental measurement.
2.2. Impact test process
After removing the temporary fixed plate and waiting for the stability of the support structure, a bearing device is placed above the rock mass, which aims to apply the impact load uniformly on the rock mass, and at the same time means that the bearing device needs to have greater stiffness so that the elastic deformation of the device itself after being subjected to the impact load can be ignored. Select the weight of the drop hammer required for the test, and install the drop hammer on the drop hammer fixing device. Adjust the rotation axis of the impact device, the fixed arm, the angle adjusting mechanism, and the fixed arm to reach the required angle and height of the test. Connect the sensor to the collector and computer, and start collecting, so that the drop hammer fixing device releases the drop hammer, and the drop hammer impacts the bearing platform. The schematic diagram of the impact test is shown in .
Different impact loads are applied to the model by adjusting the mass of the drop hammer. The designed mass of the drop hammer in the test is shown in . At the same time, in order to ensure that the damage caused by the previous impact on the rock mass will affect the test results of the next impact, the model needs to be re-prepared according to steps 1 to 6 for each impact test.
Finally, the anchor rod deformation data collected by the resistance strain gauge and the rock mass deformation data collected by the micro-strain sensor are comprehensively analyzed to obtain the mechanical mechanism of the interaction between the anchor rod and the rock mass under the dynamic impact and the anchor rod anchoring performance, and to characterize the mechanism of the anchor net support.
2.3. Impact test results
2.3.1. Impact stress analysis
The drop hammer applies dynamic stress loads uniformly to the bearing platform through the impact, and the bearing platform applies the loads uniformly on the rock mass (He et al. Citation2005; Jiang et al. Citation2014). Based on the law of conservation of energy, the loss of other energies such as heat energy in the process of the drop hammer impact is ignored. It is assumed that the impact energy generated by the drop hammer falling is completely converted into the energy released by the support structure and the energy of surrounding rock deformation through the bearing platform.
Establish the theoretical model shown in , and make the following analysis:
(1)
(1)
In the equation, is kinetic energy,
is gravitational potential energy, and W is deformation energy.
During the impact process of the drop hammer, the kinetic energy before and after is both 0, so = 0. The action length of gravity is the vertical deformation of the bearing platform produced by the falling height of the drop hammer and the action of the drop hammer. Therefore, EquationEquation (1)
(1)
(1) can be written as:
(2)
(2)
In the equation, G is the weight of the drop hammer, h is the falling height, and is the dynamic deformation.
In the case where the impact load acts on the material in accordance with Hooke’s law:
(3)
(3)
In the equation, is the impact load, E is the elastic modulus of the bearing platform.
The increased deformation energy of the bearing platform can be expressed as the work done by the impact load:
(4)
(4)
By linking EquationEquations (2)(2)
(2) and Equation(4)
(4)
(4) , the following is obtained:
(5)
(5)
If the bearing platform undergoes elastic static deformation when subjected to static load G:
(6)
(6)
By combining EquationEquations (5)(5)
(5) and Equation(6)
(6)
(6) , we obtain:
(7)
(7)
Put in order to obtain:
(8)
(8)
Since the static deformation is much smaller than the dynamic deformation, the minus sign in EquationEquation (8)(8)
(8) is meaningless, resulting in:
(9)
(9)
In the equation, K is the dynamic load coefficient.
By combining EquationEquations (3) (6)(6)
(6) , and Equation(9)
(9)
(9) , we get:
(10)
(10)
In light of the above theoretical analysis, combined with the experimental content, the dynamic load coefficient produced by different mass falling hammers is computed through EquationEquation (9)(9)
(9) , and the impact load generated by the impact device on the surrounding rock under the impact of different mass falling hammers is calculated through EquationEquation (10)
(10)
(10) , and the impact stress under this load is calculated. The results are shown in .
Table 1. Statistics of mechanical parameters for impact stress calculation.
2.3.2. Test data analysis
The deformation of hard rock mass under the action of load is very small, which makes it difficult to monitor. Therefore, this paper uses vibrating wire micro-strain sensors to monitor the deformation of the surrounding rock under different impact stresses (Wang et al. Citation2007; Yu et al. Citation2015). After the embedded strain gauge is fixed in the rock mass, it is tightly embedded with the rock through the ends, and the strained tube under middle force is wrapped with cloth to be separated from the rock. When the rock generates strain, the end drives the strained tube to deform, causing the internal stress of the steel string to change. The frequency value of the steel string after the deformation of the force can be measured by the frequency measuring instrument, and the true deformation value of the rock mass can be obtained.
Thus, the stress-strain curves of the rock mass under different impact stresses are shown in . In order to reduce the experimental error, three sensors are used in this experiment for measurement. It can be seen from the figure that with the increase of the impact stress, the deformation of the surrounding rock gradually increases, and the trends of the three sensors are basically the same. The maximum micro-strain value of the surrounding rock measured in the experiment is 133.6. When the stress value is 0, the sensor also produces a small amount of deformation, which is caused by the compressive stress in the compaction stage of the broken rock block. According to the stress-strain curve, the average elastic modulus of the rock mass can be obtained as 4.26 GPa, and the relevant data are shown in .
Table 2. Calculation of rock mass elastic modulus.
shows the deformation of the anchor rod at different positions under different impact stresses. It can be seen that with the increase of impact stress, the strain of the anchor rod increases nonlinearly. The exposed parts at both ends of the anchor rod do not participate in the deformation, therefore the strain is zero. Under impact stress, the strain value of the anchor rod presents an approximately "M"-shaped distribution, that is, there is a large deformation at both ends of the anchor rod. Among them, the maximum deformation occurs at the position of 0.45 m of the anchor rod, indicating that there is a large stress concentration at this position. Overall, the strain value of the middle section of the anchor rod does not change much and remains at the average level.
3. Numerical simulation analysis
3.1. Establishment of numerical model
Phase2 is a highly capable elastoplastic finite element analysis software in the field of geotechnical engineering, which is extensively employed in the support design of surface or underground excavations. In this paper, this software is utilized to simulate the aforementioned test process, and the deformation quantities of the surrounding rock and anchor as well as the nephograms of the stress distribution in the surrounding rock mass are acquired separately. Since the shape of the physical model is a regular rectangular parallelepiped, it can be converted into a 2D model for research, that is, to analyze one of the stress surfaces of the model. The size of the numerical model is designed strictly according to the physical model, with a size of 2 m × 0.5 m. In order to ensure the accuracy of the model, a four-node quadrilateral is used for meshing, and the mesh type is a hierarchical system with a hierarchical factor of 0.6. A total of 7315 nodes and 7164 quadrilateral elements are divided. Zero displacement constraints are applied on the left and right boundaries of the model to simulate the constraint effect of the metal frame of the model on the lateral deformation of the rock mass. Anchor rods of the two-end anchorage type are added to the inside of the model and a pre-loading force of 1000 N is applied. For ease of analysis, the rock mass is assumed to be an isotropic material that conforms to the Hoek-Brown yield criterion. The various initial physical and mechanical parameters of the rock mass and anchor rods are strictly set in accordance with the actual situation of the physical model test, and the relevant parameters are shown in and . Finally, a numerical model as shown in is established.
Table 3. Numerical model rock mass physical and mechanical parameters.
Table 4. Numerical model anchor rod physical and mechanical parameters.
3.2. Numerical simulation results
3.2.1. Strain analysis of rock mass
To simulate the impact test process of the physical model, impact stresses of 0.31, 0.35, 0.4, 0.43, and 0.47 MPa were applied to the top of the numerical model respectively, to obtain the stress-strain curves of the numerical model under different impact stresses as shown in . With the increase of the impact stress, the deformation of the surrounding rock mass increases nonlinearly, and the overall trend is in good agreement with the test results of the physical model. The elastic modulus of the rock mass calculated based on this curve is 5.38 GPa, and the percentage difference fitting degree with the 4.26 Gpa elastic modulus calculated by the physical model test is 79%.
3.2.2. Strain analysis of anchor
shows the strain values of the anchor rod at different positions under different impact stresses in the numerical model. It can be seen that the overall deformation trend of the anchor rod is more complex, but still has certain regularity. With the increase of the impact stress, the strain at each position of the anchor rod basically shows a nonlinear increase, and large deformations appear at both ends. The maximum value appears at the lower part of the anchor rod, at a position about 0.44 m, which means that the anchor rod at this position is subjected to a greater stress. The variation of the middle section of the anchor rod is not significant. Compared with , the deformation trend of the anchor rod is very close to the measured results, mainly reflected in the relatively consistent position of the extreme value point, and the maximum strain value of the anchor rod under each impact stress is also more consistent.
3.2.3. Stress analysis of rock mass
shows the maximum principal stress distribution nephogram inside the rock mass in the no-load state and under different impact stresses. It can be seen from the figure that after the pre-stress is applied to the anchor rod, a continuous conical stress field is formed inside the rock mass, and the conical stress fields are superimposed on each other to form an overall compressive stress zone, which is the composite arch. The composite arch can bear the radial stress above the rock mass, thereby enhancing the overall strength of the rock mass. At the same time, it can be found that due to the influence of the self-weight stress of the rock mass, the stress concentration effect at the lower end of the anchor rod is more obvious, and it decreases concentrically towards the inside of the rock mass, which means that the end of the anchor rod needs to be in close contact with the rock mass, and the bottom part of the anchor hole should form a certain anchoring force with the rock mass to form an effective pre-stress field. And the support spacing of the anchor rod needs to be selected reasonably, otherwise the adjacent conical stress fields cannot overlap to form a composite arch. The stress vacuum zone between the cones is prone to the fall of the broken rock mass, and the volume of this part of the rock mass is often controllable. Therefore, the use of anchor net support can effectively solve this problem. The metal net is fixed to the rock mass through the anchor rod and can prevent the fall of the broken rock mass.
Figure 11. Nephograms of stress distribution of numerical model rock mass under different impact stresses: (a) σ1 = 0, σ1 = 0.31 MPa, σ1 = 0.35 MPa, σ1 = 0.40 MPa, σ1 = 0.43 MPa, σ1 = 0.47 MPa.

With the increase of impact stress, the stress concentration effect inside the rock mass becomes more and more obvious, and the compressive stress inside the rock mass also increases. Compared with the state without impact stress, the shape of the compression arch inside the rock mass has undergone some changes, and the shape of the lower part of the cone has a convergence phenomenon, which leads to an increase in the volume of the stress vacuum zone between adjacent cones. At the same time, due to the influence of the compressive stress, the broken rock mass in the vacuum zone is more likely to fall. For the site with larger impact stress, the use of anchor net support may not completely guarantee the stability of this part of the rock mass. Therefore, while using anchor net support, measures such as shotcrete support can also be added. At the same time, it can be found that the larger the impact stress, the gradually larger the stress vacuum zone at the upper part of the cone. When the impact stress is large enough, the two vacuum zones above and below will be connected, which means that the impact stress exceeds the ultimate stress that the compression arch can bear, which will lead to the complete collapse of the support body. Therefore, accurately assessing the size of the impact stress at the site is also the key to ensuring that the support design can meet the safety requirements.
4. Calculation of anchorage force of compression arch
Based on the limit equilibrium principle and the composite arch theory, a mechanical model as shown in is constructed.
Assuming that under the action of limit equilibrium, the rock mass after support still conforms to the Hoek-Brown strength criterion (Eberhardt Citation2012):
(11)
(11)
In the equation, and
respectively represent the maximum and minimum principal stresses in the surrounding rock mass, m is the hardness constant of the rock mass, and s is the integrity constant of the rock mass. For the broken rock mass, s is equal to 0.
When the stress state of any point in the surrounding rock of the compression arch satisfies EquationEquation (11)(11)
(11) , it indicates that the surrounding rock of the compression arch is about to enter a failure state. And the stress applied at the inner wall of the compression arch is generally equal to the restraint force of the anchor body, that is,
=
After comprehensive analysis, the strength criterion of the surrounding rock in the compression arch can be expressed as:
(12)
(12)
The supporting force of the anchor body can be calculated by the following equation:
(13)
(13)
In the equation, Q is the anchoring force of the anchor rod, d is the spacing between and row of the anchor rod, and is the stress of the anchor rod support.
To calculate the combined bearing force T of the surrounding rock compression arch per unit length along the axial direction of the roadway, the following differential relationship is needed:
(14)
(14)
In the equation, is the differential length unit of the center arc of the compression arch, R is the radius of the roadway,
is the differential angle unit of the surrounding rock compression arch along the center of the roadway, L is the thickness of the surrounding rock composite arch (it is assumed here that the anchorage length of the anchor rod is the thickness of the surrounding rock compression arch).
From EquationEquations (12)(12)
(12) and Equation(14)
(14)
(14) , it can be obtained:
(15)
(15)
In this equation: T is the bearing capacity of the compression arch per unit length along the axial direction of the roadway, and k is the radial stress increase slope. In the anchorage of the broken rock mass, k = 0, then EquationEquation (15)(15)
(15) can be simplified to:
(16)
(16)
For the circular composite arch, the surrounding rock is subjected to a uniform load Q on the outside. Assuming that under the action of the supporting stress the circumferential axial force
generated by the surrounding rock composite arch is obtained, and the symmetry can be utilized:
(17)
(17)
It can be derived from above:
(18)
(18)
It is evident from the above that the bearing capacity T of the compression arch must be greater than the circumferential axial force to ensure the stability of the surrounding rock. In the case of a limit equilibrium state of the compression arch, T=
which can be derived from EquationEquations (13) (16)
(16)
(16) and Equation(18)
(18)
(18) :
(19)
(19)
From EquationEquation (19)(19)
(19) , it can be seen that the anchoring force Q is a function that is influenced by the rock mass quality, anchoring length, spacing between and row of anchor rods, and geometrical shape of the roadway.
5. Discussion
Support has always been a prerequisite for safe and efficient mine production. However, for domestic underground metal mines, there are significant problems in the selection of support methods and the determination of support parameters in most mines.
Currently, due to considerations of support costs and traditional concepts, many mines still adopt passive support methods such as steel arches. In areas with better shallow geological conditions and less mining ground pressure influence, the use of steel arch support can effectively ensure the safety of the roadway. However, with the increase in mining depth and the increase in mining ground pressure, this support method is undoubtedly unreasonable.
Active support, as a more scientific and reasonable type of support, emphasizes the interaction between the support structure and the rock mass to increase the strength of the surrounding rock itself, thus better resisting the potential threats to the roadway caused by geological influences such as rock burst. Anchor rod support is widely praised because of its superior anchoring force, relatively low cost, and more convenient construction. With the improvement of production concepts, many mines are also gradually phasing out traditional passive support methods and adopting more popular anchor rod support. However, anchor rod support also has certain limitations, such as not preventing the weathering of the surrounding rock and not preventing the spalling of the rock between anchor rods. Therefore, anchor rod support often needs to be combined with other support methods, such as metal net and shotcrete support. In terms of on-site practical applications, the biggest problem with anchor rod support is actually the lack of sufficient scientific basis for the determination of support parameters. Although most mines have adopted advanced anchor rod support, due to the unreasonable selection of support parameters and non-compliant construction processes, a large number of cases of support failure have occurred. The fundamental reason is actually the lack of sufficient understanding of the support mechanical mechanism of anchor rod support in mines. In this paper, through physical model experiments and numerical simulations, the above issues are explored in depth, characterizing that the extremely fragmented rock mass can resist the impact of strong dynamic impacts under the action of anchor net support, and the stress distribution contour within the rock mass also intuitively indicates the importance of the reasonable selection of parameters such as anchoring force, anchor spacing, and anchor length, as well as the coordinating effect of auxiliary supports such as metal net and shotcrete on anchor rod support. It is not difficult to find that to form an effective composite arch, the anchoring force is crucial. Therefore, based on the Hoek-Brown strength criterion of the rock mass and the composite arch theory, the ultimate equilibrium rule is used to derive the anchoring force of the anchor rod, and it is finally found that the anchoring force of the anchor rod is a function influenced by multiple parameters such as the quality of the rock mass, the anchoring length, the spacing between and row of anchor rods, and the geometrical shape of the roadway. This equation explains the mechanical mechanism of anchor rod support under the composite arch theory at the theoretical level and can be applied to the support design in the actual production of mines.
6. Conclusion
Based on the current problems of support failure in the metal mine field, this paper further explores the mechanism of anchor net support by physical model tests, numerical simulation, and theoretical analysis. The main research results are as follows:
The outcomes indicate that the model simulation results are highly consistent with the experimental results. The mean elastic modulus of the rock mass measured through the physical model experiment is 4.26 GPa, and the elastic modulus of the rock mass derived from the numerical simulation calculation is approximately 5.38 GPa, with a percentage difference coincidence rate of 79%. In the meantime, under diverse impact stresses, the peak deformation amount of the anchor rod in the numerical simulation is largely consistent with the results of the physical model experiment, and the deformation of the anchor rod both exhibits an "M"-shaped distribution.
With the aid of the nephograms, the stress distribution within the surrounding rock under the anchor net support can be intuitively elaborated. In the support design, only by selecting reasonable intervals between and rows of anchor rods and pre-stress can an effective combined arch be formed, and the assessment of impact stress and stress vacuum areas is likewise the key to ensuring the validity of the support.
Based on the limit equilibrium principle, the derivation of the anchoring force of the anchor rod under the combined arch theory has been carried out. The equation shows that the anchoring force is a function that is affected by the quality of the rock mass, the length of anchorage, the spacing between and row of the anchor rods, and the geometric shape of the roadway, and this equation can be practically applied to the on-site support design.
Acknowledgements
Extremely thankful to the editorial board and reviewers of this paper.
Data availability statement
It can be obtained from the corresponding or first author upon reasonable request.
Disclosure statement
No potential conflict of interest was reported by the author(s)
Additional information
Funding
References
- Chen H, Ren W, Shu Z, Li D. 2012. Model test study and numerical analysis of mechanism of anchor bolt under different supporting conditions. Rock Soil Mech. 33(S1):277–282.
- Chu HB, Li GQ, Liu ZJ, Liu XS, Wu YH, Yang SL. 2022. Multi-level support technology and application of deep roadway surrounding rock in the Suncun Coal Mine, China. Materials. 15(23):8665. doi:10.3390/ma15238665.
- Dong F, Song H, Guo Z, Lu S, Liang S. 1994. Roadway support theory based on broken rock zone. J China Coal Soc. 19(01):21–32.
- Dong LJ, Tong XJ, Li XB, Zhou J, Wang SF, Liu B. 2019. Some developments and new insights of environmental problems and deep mining strategy for cleaner production in mines. J Cleaner Prod. 210:1562–1578. doi:10.1016/j.jclepro.2018.10.291.
- Eberhardt E. 2012. The Hoek-Brown failure criterion. Rock Mech Rock Eng. 45(6):981–988. doi:10.1007/s00603-012-0276-4.
- Editorial. 2015. Review on China’s tunnel engineering research: 2015. China J Highway Transp. 28(05):1–65.
- Guo ZB, Wang Q, Li ZH, He MC, Ma ZB, Zhong FX, Hu J. 2019. Surrounding rock control of an innovative gob-side entry retaining with energy-absorbing supporting in deep mining. Int J Low-Carbon Technol. 14(1):23–35. doi:10.1093/ijlct/cty054.
- Han B, Wang X, Wen Y. 2010. Drift support technology with wet shotcrete method in weak rock mass. J Central South Univ. 41(06):2381–2385.
- Han Z, Li D, Li X. 2022. Dynamic mechanical properties and wave propagation of composite rock-mortar specimens based on SHPB tests. Int J Mining Sci Technol. 32(4):793–806. doi:10.1016/j.ijmst.2022.05.008.
- Han Z, Li J, Wang H, Zhao J. 2023. Initiation and propagation of a single internal 3D crack in brittle material under dynamic loads. Eng Fract Mech. 285:109299. doi:10.1016/j.engfracmech.2023.109299.
- Hao J, Li X, Song Y, Zhang P, Liu H. 2021. Analysis of mining roadway with large deformation of broken soft coal and research on supporting technology: a case study in Xin’an coal mine, China. Eng Fail Anal. 130:105761. doi:10.1016/j.engfailanal.2021.105761.
- He M, Xie H, Peng S, Jiang Y. 2005. Study on rock mechanics in deep mining engineering. Chin J Rock Mech Eng. 24(16):2803–2813.
- Hou C, Gou P. 2000. Mechanism study on strength enhancement for the rocks surrounding roadway supported by bolt. Chin J Rock Mech Eng. 19(03):342–345.
- Hou C, Li X. 2001. Stability principle of big and s mall structures of rock surrounding roadway driven along goaf in fully mechanized top coal caving face. J China Coal Soc. 26(01):1–7.
- Hua X. 2006. Development status and improved proposals on gob-side entry retaining support technology in China. Coal Sci Technol. 34(12):78–81.
- Jiang Y, Pan Y, Jiang F, Dou L, Ju Y. 2014. State of the art review on mechanism and prevention of coal bumps in China. J China Coal Soc. 39(02):205–213.
- Kang H. 2005. Study and application of complete rock bolting technology to coal roadway. Chin J Rock Mech Eng. 24(21):161–166.
- Kang H. 2016. Sixty years development and prospects of rock bolting technology for underground coal mine roadways in China. J China Univ Mining Technol. 45(06):1071–1081.
- Kang H. 2021. Seventy years development and prospects of strata control technologies for coal mine roadwaysin China. Chin J Rock Mech Eng. 40(01):1–30.
- Kang HP, Gao FQ, Xu G, Ren HW. 2023. Mechanical behaviors of coal measures and ground control technologies for China’s deep coal mines - a review. J Rock Mech Geotech Eng. 15(1):37–65. doi:10.1016/j.jrmge.2022.11.004.
- Li CC, Høien AH. 2023. An issue in the current definition of the factor of safety for rock slopes and suggestions for improvement. IOP Conf Ser Earth Environ Sci. 1124(1):012105. doi:10.1088/1755-1315/1124/1/012105.
- Li G, Ma F, Guo J, Zhao H, Liu G. 2020. Study on deformation failure mechanism and support technology of deep soft rock roadway. Eng Geol. 264:105262. doi:10.1016/j.enggeo.2019.105262.
- Li H, Wang C, Hua X, Zhao X, Dai B, Huang Z. 2023. Stability analysis and support requirements for haulage drift in the vicinity of mined stopes. Geomat Nat Hazards Risk. 14(1):14.
- Li XS, Wang YM, Hu YJ, Zhou CB, Zhang H. 2022. Numerical investigation on stratum and surface deformation in underground phosphorite mining under different mining methods. Front Earth Sci. 10. doi:10.3389/feart.2022.831856.
- Qin T, Duan B, Duan Y, Ni Y, Hou X, Ma P, Yang Y. 2023. “Migrate-transfer-control" support system of surrounding rock in the deep roadway and its application. Appl Sci-Basel. 13(10):6325. doi:10.3390/app13106325.
- Rahimi B, Sharifzadeh M, Feng XT. 2020. Ground behaviour analysis, support system design and construction strategies in deep hard rock mining - justified in Western Australian’s mines. J Rock Mech Geotech Eng. 12(1):1–20. doi:10.1016/j.jrmge.2019.01.006.
- Ranjith PG, Zhao J, Ju MH, De Silva RVS, Rathnaweera TD, Bandara A. 2017. Opportunities and challenges in deep mining: a brief review. Engineering. 3(4):546–551. doi:10.1016/J.ENG.2017.04.024.
- Skrzypkowski K, Zagórski K, Zagórska A, Apel DB, Wang J, Xu H, Guo L. 2022. Choice of the arch yielding support for the preparatory roadway located near the fault. Energies. 15(10):3774. doi:10.3390/en15103774.
- Tahmasebinia F, Yang A, Feghali P, Skrzypkowski K. 2022. A numerical investigation to calculate ultimate limit state capacity of cable bolts subjected to impact loading. Appl Sci-Basel. 13(1):15. doi:10.3390/app13010015.
- Wang D, Jiang Y, Sun X, Luan H, Zhang H. 2019. Nonlinear large deformation mechanism and stability control of deep soft rock roadway: a case study in China. Sustainability. 11(22):6243. doi:10.3390/su11226243.
- Wang H, Zhou C, Bi Q, Zhu H, Ding Z, Zhang C. 2023. Adaptive modification of TBM tunneling in coal mine roadway and disaster control technology for complex geological conditions. Processes. 11(5):1389. doi:10.3390/pr11051389.
- Wang J. 2007. New development of rock bolting technology for coal roadway in China. J China Coal Soc. 32(02):113–118.
- Wang Q, Pan R, Jiang B, Li SC, He MC, Sun HB, Wang L, Qin Q, Yu HC, Luan YC. 2017. Study on failure mechanism of roadway with soft rock in deep coal mine and confined concrete support system. Eng Fail Anal. 81:155–177. doi:10.1016/j.engfailanal.2017.08.003.
- Wang R, Li Z, Ren G, Zhang S. 2007. Experimental study and numerical simulation of the dynamic response of concrete filled steel tubes under lateral impact load. China Civil Eng J. 24(10):34–40.
- Wang S, Li XL, Qin QZ. 2022. Study on surrounding rock control and support stability of ultra-large height mining face. Energies. 15(18):6811. doi:10.3390/en15186811.
- Xin S, Cheng J, Wan Z, Lv J, Liu K, Gao K. 2024. Analysis of the support failure mechanism caused by bolt pre-tightening force loss. Processes. 12(1):113. doi:10.3390/pr12010113.
- Yang S. 2010. Study on the surrounding rock control theory of roadway in coal mine. J China Coal Soc. 35(11):1842–1853.
- Yang X, Wang E, Wang Y, Gao Y, Wang P. 2018. A study of the large deformation mechanism and control techniques for deep soft rock roadways. Sustainability. 10(4):1100. doi:10.3390/su10041100.
- Yu S, Wu X, Chen G, Dai H, Hong W. 2015. Wireless sensor networks for bridge structural health monitoring. J Softw. 26(06):1486–1498.
- Zhang L, Nian W. 2002. Research on status quo of anchorage theory of rock and soil. Rock Soil Mech. 23(05):627–631.
- Zhao X, Qin S, Li Y, Yu W, Wu T. 2023. Analyzing support stability of deep shaft based on plastic softening and dilatancy of hard rock mass. Processes. 11(1):186. doi:10.3390/pr11010186.
- Zhao X, Zhu Q, Westman E, Yang S. 2023. Research on failure mechanism and support technology of fractured rock mass in an undersea gold mine. Geomat Nat Hazards Risk. 14(1):31.
- Zhu C, Yuan Y, Wang WM, Chen ZS, Wang SZ, Zhong HW. 2021. Research on the "three shells" cooperative support technology of large-section chambers in deep mines. Int J Mining Sci Technol. 31(4):665–680. doi:10.1016/j.ijmst.2021.05.002.