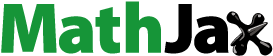
Abstract
Inertization of lead nitrate Pb(NO3)2, a representative of soluble lead compound, with five cements pastes based on either ordinary Portland cement (OPC) or blended Portland cement with granulated blast-furnace slag (GBFS) or metakaolin (MK) was studied. Various mixes were prepared by using a water/solid ratio (W/S) of 0.28 (by weight). Two ratios of Pb ions (1.0% and 2.0% of the solid binder) was used by adding to the mixing water. Hydration characteristics of the different cement pastes were investigated via the examination of chemically combined water content, compressive strength, X-ray diffraction analysis and thermal analysis (DTA/TGA). Leaching of lead ions from various hardened cement pastes was examined. The results showed that lead nitrate retards cement hydration through the formation of plumbate salt CaPbO3. The obtained results of leaching showed a high degree of immobilization of Pb ions in the various cement pastes. Moreover, partial replacement of Portland cement by MK is more efficient than granulated blast-furnace slag GBFS.
Introduction
Solidification/stabilization (s/s) of heavy metal-bearing sludge, industrial residues and contaminated soil is an attractive technology to reduce their toxicity and facilitate handling prior to landfill. In terminology, stabilization is a process of converting a toxic waste to a physically and chemically more stable form, that is, alters hazardous waste chemically to produce a less toxic or less mobile form. It involves the interactions between waste and the cement phases [Citation1–Citation2]. Hydration of cement can be modified by heavy metals due to coating around cement grains. Three-dimensional structures up to 100–300 nm thick containing heavy metal can form coatings around cement grains [Citation3].
Heavy metals retarded the precipitation of portlandite due to the reduction of pH resulted from the hydrolysis of heavy metal ions during C3S hydration. Heavy metals are co-precipitated with calcium as double hydroxide [Citation4–Citation6] such as Ca2Cr(OH)7·3H2O, Ca2(OH)4·4Cu(OH)2·2H2O and CaZn2(OH)6·2H2O and CaZn2(OH)6·2H2O.2Ca(OH)2 + M(OH)2 + 2H2O → Ca2(OH)4·M(OH)2·2H2O where M = Cr, Cu, Zn.
Metals form the least soluble hydroxides retard hydration reactions while those that form more soluble hydroxides exhibit only a slight degree of retardation; and metals forming soluble hydroxides behave as accelerators of cement hydration. Retardation has been attributed to the reduction in the permeability caused by these reaction products that is the precipitation of insoluble metal colloidal gels on cement grain surfaces.
The leaching of heavy metals in the S/S materials can be considered as PH dependent and the corresponding metal hydroxide solubility controlled process. Mineral additions enter the hydration reactions in the mixtures and favor the formation of specific microstructure promoting the immobilization of hazardous elements [Citation7].
It was reported that lead sulfate in which nitrate retards the hydration reaction of Portland cement [Citation8]. Lead ions are mostly stabilized through physical encapsulation by the hardened slag pastes hydrate matrix [Citation9].
The aim of this study is to investigate the effect of lead nitrate on the hydration characteristics of the different cement pastes used as well as the capacity of these cement pastes to immobilize lead ions.
Experimental
Materials and specimens
The materials used in this investigation were; ordinary Portland cement (OPC), granulated blast-furnace slag (GBFS), metakaolin (MK) and lead nitrate. The chemical analysis of the utilized materials is given in .
Table 1 Chemical oxide composition of the starting materials (Wt.,%).
Various cement mixes were prepared namely; neat Portland cement (M1), 80% OPC + 20% GBFS (MII), 60% OPC + 40% GBFS (MIII), 80% OPC + 20% MK (MIV) and 60% OPC + 40% MK (MV).
Two ratios of lead ions were used; 1.0 and 2.0 wt.% of the solid binder was added to the mixing water. The water/solid ratio used was 0.28 for all mixes. The pastes were molded in the one inch cubic molds and cured at about 100% relative humidity for the first 7 days. Then the samples were immersed in tap-water for the rest of hydration times up to 90 days.
Methods of investigation
The hydration characteristics of the different cement mixes were investigated via the determination of chemically combined water contents, compressive strength, phase composition using XRD technique and thermal analysis (DTA/TGA). The degree of immobilization of lead ions in the different cement pastes was evaluated through measuring of the leached lead ions concentration using a static process [Citation10].
Results and discussion
Hydration characteristics
Combined water content (Wn%)
The results of chemically combined water content are graphically plotted as a function of cure time in for all mixes in absence and presence of lead nitrate. It is obvious that there is a continuous and gradual increase in the combined water content for all mixes with increasing age of hydration up to 90 days. This increase may be due to the progress of hydration of the various components of the used mixes. The main hydration products for all mixes are calcium silicate hydrate (CSH) and calcium hydroxide (CH) in addition to the hydrates of the aluminate phases. In the mixes which contain blast-furnace slag or metakaolin, the liberated calcium hydroxide from the hydration of silicate phases (C3S, β-C2S) of Portland cement are supposed to react with the alumina silicate produces more (CSH) as well as (ASH) which is considered as the main binding agent. The formed calcium silicate hydrates have the following formula; xCaO·SiO2·yH2O (CxSHy), where x and y may vary over a wide range. This depends on many factors such as; water/solid ratio, composition of impurities, temperature and time of hydration. A pervious study [Citation11] showed that the initially formed high lime CSH (having high water content) transforms into low lime and CSH with low water content.
The mixes made with lead nitrate showed higher water contents than those without lead ions at most of the hydration ages. This is mainly attributed to the formation of calcium plumbate CaPbO3·xH2O. As the concentration of lead ions increases from 1 to 2 wt.% of the cement blended or OPC, the combined water increases.
Compressive strength
A decrease in the compressive strength values can be observed on the addition of Pb ions compared with those of the control mixes (see, ). The increase in the ratio of Pb2+ ions from 1.0% to 2.0 wt.% showed larger decrease in the compressive strength values. In the precipitation of cement hydration products, heavy metal ions may be adsorbed on their surfaces and then enter the lattice to form a solid-solution, altering their structures, particles size and solubility [Citation12]. Therefore, the compressive strength of CSH gel decreases. This observation may be an indication for a retardation effect caused by Pb(NO3)2. This result agrees with pervious studies [Citation8]. The Pb(NO3)2 accelerates the hydration of cement which increases the combined water content but the formed complex coats on the hydration products. This can decrease the compressive strength soluble alkali salts act as accelerators. Many common contaminants, particularly heavy metals, can affect the hydration of cement [Citation5]. Copper, lead and chromium all accelerate the hydration of cement paste, while zinc can retard the hydration.
Cocke and Mollah [Citation12] explained this retardation effect as a result of the quick precipitation of lead hydroxide in the high alkaline environment of the cement mix coating the cement grains. Lead hydroxide is amphoteric and could be re-dissolved in an excess of hydroxide ions to form soluble plumbates (). This consumes both calcium and hydroxide ions, hereby delaying the normal cement hydration process in which calcium and hydroxide ions gradually saturate the mix water until super-saturation is reached and solid Ca(OH)2 is precipitated out along with the formation of CSH gel. The obtained results in the present work are in a good agreement with such explanation.
Phase composition
The well crystallized hydration product of ordinary Portland cement or that blended with GBFS or MK is the calcium hydroxide (CH) phase. Therefore, the change in the intensity of the XRD peaks characteristic for CH can be considered as an indication for the degree of hydration of the investigated cement pastes. It is obvious from that the intensity of CH peaks increases with hydration time for all mixes. This may be due to the progress of the hydration reaction with time. Mixes (MIII) and (MV) which contain GBFS and metakaolin respectively, show less CH compared to neat cement mix (MI). This can be attributed to the pozzolanic reaction of GBFS and metakaolin with the liberated CH as a result of Portland cement hydration. All mixes with 2.0 wt.% lead ions show less intensity for CH peaks as compared with the mixes made without lead. This could be an indication for the retarding effect of lead nitrate for the hydration of the investigated mixes. Such result is correlated with the obtained results of the compressive strength due to formation of more plumbate salt CaPbO3.
Table 2 X-ray diffraction analysis of mixes I, III and V in presence and absence of Pb ions at various ages.
Thermal analysis
Thermal analysis techniques such as differential thermal analysis (DTA) and thermo-gravimetric analysis (TGA) were used to give more qualitative and quantitative information. and show the DTA and TAG curves of the control mix M1 in absence and presence of 2.0 wt.% Pb hydrated for 28 days. It can be noticed that the endothermic peaks in the DTA curves at 50–120 °C can be attributed to the evaporation of the physically and chemically combined water in CSH [Citation13–Citation14]. While as, the endothermic peaks at about 450 °C are due to the decomposition of calcium hydroxide (CH). Obviously, the intensities of the endothermic peaks of the decomposition of CH in presence of Pb waste (this endotherm due to CH dehydroxylation) are less than those of the control mix. This indicates that the presence of Pb forms plumbite with librated Ca(OH)2 therefore the endothermic peak decreases. Such observation supports the results of X-ray diffraction analysis. In addition, the TGA curves can give quantitative information about the loss in the sample weight with increasing temperature. The total loss in weight on heating up to 90 °C in presence of lead is greater than that in the control mix. This result is in a good agreement with that of the combined water content. Therefore, the presence of Pb favors the formation of Ca plumbite with more combined water content.
Leaching behavior
pH measurements
The measured pH values of the leachate solution for most mixes were in the range 12.22–12.94 during the hydration period (1–90 days). Except mix (MV) made with 40% metakaolin which showed pH values in the range 11.88–12.74 during the same hydration period.
Degree of immobilization
and show the values of the degree of immobilization of the different hardened cement pastes contained 1.0 and 2.0 wt.% Pb ions of solid, respectively, using the static leaching process. Generally, all pastes show a slight and continuous decrease in the immobilization percent with the leaching period up to 90 days. The highest immobilization degrees after 90 days were 99.961% and 99.951% for mixes containing 40% metakaolinites MVD1 and MVD2, respectively. While as, the least immobilization percents was 99.829% and 99.853% for mixes containing 20% slag MIID1 and MIID2, respectively. The immobilization values did not greatly change with the amount of added lead nitrate. The stabilization of lead ions by hydraulic binders probably occurs by one or a combination of the following mechanisms [Citation15].
Table 3 The immobilization% of lead ions for various mixes made with 1.0% Pb(NO3)2 (static mode) at various leaching times.
Table 4 The immobilization% of lead ions for various mixes made with 2.0% Pb(NO3)2 (static mode) at various leaching times.
Addition: C-S-H + Pb = Pb-C-S-H
Substitution: C-S-H + Pb = Pb-S-H + calcium
Precipitation of new compounds: Pb + OH + Ca + SO4 = mixed salts
Conclusion
• | Blended cement pastes containing granulated blast-furnace slag or metakaolin showed less compressive strength values as compared to the neat Portland cement paste at all hydration ages up to 90 days. | ||||
• | The decrease of compressive strength caused by lead nitrate in all the examined pastes is more likely due to the formation of a gel surface layer around cement grains as well as the formation of plumbite ions. These reactions consume calcium and hydroxide ions from solution and delay the supersaturation and precipitation of calcium hydroxide and development of CSH gel. | ||||
• | XRD analysis did not indicate the formation of any new phases, but did confirm the retarding effect caused by lead nitrate due to coating of Pb2+ plumbite on the cement. | ||||
• | Thermal analysis showed that the presence of Pb salt favors the formation of CSH with more combined water content due to the increase of complex formation. | ||||
• | All cement pastes showed high degree of immobilization of lead but Portland cement – metakaolin blends showed the highest values. |
Notes
Peer review under responsibility of Housing and Building National Research Center.
References
- S.VallsE.VazguezStabilization and solidification of sewage sludge with Portland cementCement & Concrete Research30200016711678
- C.CollierN.B.MilestoneI.M.HillI.M.GodfreyThe disposal of radioactive ferric flocWaste Management262006769775
- B.S.CannellT.T.EghmyE.J.KrzowHeavy metals stabilization in municipal solid waste combustion bottom ash using soluble phosphateWaste Management202000135148
- Q.Y.ChenC.D.HillsM.TyrerI.SlipperH.G.ShenA.BroughCharacterization of products of tricalcium silicate hydration in the presence of heavy metalsJournal of Hazardous Materials1472007817824
- Q.Y.ChenM.TyrerC.D.HillsX.M.YangP.CareyImmobilisation of heavy metals in cement-based solidification/stabilizationWaste Management292009390403
- C.S.PoonZ.Q.ChenO.W.H.WaiThe effect of flow-through leaching on the diffusivity of heavy metals in stabilized/solidified wastesJournal of Hazardous Materials812001179192
- Z.GiergicznyA.KrólImmobilization of heavy metals (Pb, Cu, Cr, Zn, Cd, Mn) in the mineral additions containing concrete compositesJournal of Hazardous Materials1602008247255
- N.L.ThomasD.A.JamesonD.D.DoubleThe effect of lead nitrate on the early hydration of Portland cementCement & Concrete Research111981143153
- C. Yoon Rha, S. Keun Kang, C.K. Eun, Investigation of the stability of hardened slag paste for the stabilization/solidification of wastes containing heavy metal ions, Journal of Hazardous Materials 73 (2000) 255–267.
- NEN 7341, Determination of the availability for leaching from granular and monolithic, 1994.
- S.A. Abo El-Enein, E.E. Hekal, M. Abdel-khalik, F.I. El-Hosiny, Autoclaved calcium silicate hydrates: II surface area and pore structure. Il Cement 87 (1990) 147–154.
- D.L. Cocke, M.Y.A. Mollah, The chemistry and leaching mechanisms of hazardous substances in cementitious solidification/stabilization systems, in: R.D. Spence (Ed.), The Chemistry and Microstructure of Solidified Waste Forms, Lewis Publishers, 1993, pp. 187–242.
- J.DweckP.M.BuchlerHydration of Portland cement blended with calcium carbonateJournal of Thermochimica Acta3462000105113
- J. Dweck, P.E.F. Da Silva, R.S. Aderne, Evaluation cement hydration by non-conventional DTA. Application to waste solidification, Journal of Thermal Analysis and Calorimetry 71 (2003) 821–827.
- G.TheveninJ.PeraInteractions between lead and different bindersCement Concrete Research29199916051610