Abstract
The particle’s surface property plays an important role on controlling the thermal insulation performance of fibrous silica compacts. In the present study, the effect of addition of hydrophobic silica on the thermal conductivity of the fibrous silica compacts is investigated. The measurement was conducted using laser flash method and differential scanning calorimeter (DSC) method. The thermal conductivity of fibrous silica compacts is only 0.042 W/m K. The addition of 5% hydrophobic silica further reduces the thermal conductivity of fibrous silica compacts to 0.033 W/m K. The thermal conductivity reaches a constant value with higher hydrophobic silica content. The flexural strength decreases with the increase of hydrophobic silica content. A compromise between the thermal insulation and strength is needed. The performance of fibrous silica compacts shows strong dependence on the surface structure of glass fibers.
1 Introduction
Global warming and heat pollutions are becoming serious problems to the world recently. To insulate the heat sources effectively is one of the solutions to solve these problems. So far, many studies have aimed at creating various high performance thermal insulation materials. Among them, advanced thermal insulation materials, such as fumed silica compacts, exhibit high potential [Citation1,Citation2]. For the compacts, a high porosity with nanoscale porous structure is the key to achieve low thermal conductivity. As the size of nano-pores is smaller than the mean free path of air molecules at ambient pressure, it leads to a low thermal conductivity [Citation1,Citation2]. In addition, a high porosity structure reduces the contacts between solid particles effectively in the compacts. Though the fumed silica compact exhibit excellent thermal insulation capability, its mechanical reliability is relatively poor [Citation1,Citation2].
Previous studies [Citation3,Citation4] indicated that the advanced thermal insulating silica compacts can be prepared successfully using a mechanical process with an attrition type mill. The compact composed of fumed silica powder [Citation5], glass fibers, and SiC powder. The fumed silica particles were aggregated together, and formed chain-like structure with the pores of several tens nanometers [Citation3,Citation4]. The fibers were added for improving the strength of the compact, and the SiC particles for reducing the radiation part of thermal conductivity. After the mechanical processing, the fiber’s surface was coated with a porous silica layer, composing of pores smaller than about 100 nm [Citation3,Citation4]. Therefore, the contact points between fibers were controlled by the silica layer. The surface coating nano-porous layer reduces the thermal conductivity. An extremely low thermal conductivity, 0.026 W/m K (at 100 °C), has been reported [Citation3,Citation4].
To determine the thermal conductivity of porous compact with low heat conduction is a challenging task. The thermal diffusivity of the fibrous silica compact board was determined using a cyclic heat method [Citation6 Citation2013;Citation10] and a laser flash method [Citation11 Citation2013;Citation14]. The thermal conductivity also shows dependence on the type of silica. As the compacts made of hydrophilic silica powder and of hydrophobic silica powder were measured with cyclic heat method [Citation6], the compact composing of hydrophobic silica exhibited higher thermal insulation ability than that of hydrophilic one within the temperature range from 100 °C to 300 °C. Nevertheless, the strength of the compact with hydrophobic silica showed a low strength value of 0.03 MPa, which was only 1/10 of the compact with hydrophilic silica. The mixing of both types of silica particles to prepare the thermal insulation compacts is thus an interesting alternative for the improvement of strength.
On the other hand, a rapid method on measuring thermal conductivity by combining laser flash and differential scanning calorimeter (DSC) [Citation15] techniques was proposed [Citation11]. The thermal conductivity of the compact made of hydrophilic silica was successfully determined at room temperature [Citation11]. The result was in good agreement with that using the cyclic heat method [Citation6]. Short measuring time and small specimen are the advantages of using such laser flash/DSC method.
The present study focuses on the effect of hydrophobic nano-silica particles addition on the thermal property of the fibrous silica compacts. The measurement was conducted by a laser flash/DSC method at room temperature in air. The mechanical property of the compacts was also investigated.
2 Experimental procedures
In the present study, the starting materials were hydrophilic type fumed silica powder (AEROSIL300, Nippon Aerosil, Tokyo, Japan), hydrophobic type fumed silica powder (AEROSILR812, Nippon Aerosil, Tokyo, Japan), and glass fibers (CS3J-888, Nittobo, Tokyo, Japan). The specific surface area of hydrophilic and hydrophobic silica powder was respectively 300 m2/g and 250 m2/g, as determined by the BET method (3Flex Surface Characterization Analyzer, Micromeritics Japan, Chiba, Japan). The equivalent size of hydrophilic and hydrophobic silica particles was 10 nm and 12 nm, respectively. These silica powders showed three-dimensional nano chain-like aggregated structure with the pore size of several tens of nanometers [Citation3,Citation4]. The glass fibers were added for improving the strength of thermal insulation compact [Citation3,Citation4]. The diameter and length of the glass fibers were around 10 μm and 3 mm, respectively.
shows the composition of the fibrous silica compacts prepared in the present study. The mass ratio of fumed silica powder (hydrophilic and hydrophobic particle) and glass fibers in 100 g mixture was 75–25. For the part of fumed silica, the hydrophobic silica content was selected 0%, 5%, 10%, 30% and 50%, respectively. The starting powders were treated by a mechanical process [Citation16]. The mixing was conducted by the attrition type mill (Mechanofusion System, Hosokawa Micron Corp., Osaka, Japan). The mill includes a main chamber and a rotating rotor; the clearance between rotor and chamber was 3 mm [Citation16]. The mixing time and rotating speed were set at 10 min and 1000 rpm, respectively. During the processing, the powders received various mechanical stresses, such as compressive and shear stresses, without any media balls. The environmental temperature and humidity were set at around 25 °C and 50%, respectively. After the processing, the silica/fiber composite powder mixture was obtained. The microstructures of the processed mixtures were observed by scanning electron microscopy (JSM-6010LA, JEOL Ltd., Tokyo, Japan). The processed powder was then put in a square die and pressed to form the thermal insulation compact board [Citation17] (100 mm × 150 mm × 10 mm) under a uniaxial pressure of 2 MPa. The density and porosity of the resulted compact were determined using the dimensions and weight. One compact for each composition was measured. The inner structure of the compact board was also observed by scanning electron microscopy.
Table 1 Composition of the fibrous silica compacts prepared in the present study.
The thermal diffusivity was measured by a laser flash apparatus (LFA-502N, Kyoto Electronics Manufacturing CO., LTD, Japan) at room temperature in air. For the measurement, the specimens with the size of 10 mm in diameter and 2.5 mm in thickness were cut from the compact board carefully. Before the measurement, the specimen was dried at 120 °C for 1 day, and each surface was coated by carbon spray. Two or three specimens for each composition were measured. The details for the laser flash analysis can be found elsewhere [Citation11,Citation14]. The specific heat capacity was measured by a differential scanning calorimeter (DSC, PerkinElmer Co., USA) [Citation15]. The diameter and thickness of the specimen for DSC were 5 mm and 1.5 mm, respectively. The specimen was heated up to 200 °C before measuring. The hydrophobic silica content 0%, 30%, and 50% specimens were measured for 5–6 times at the temperature ranged from −10 °C to 390 °C. The thermal conductivity of the compact was obtained by using density, thermal diffusivity and specific heat capacity [Citation12].
A three-point bending test was used to determine the flexural strength. The dimensions of the specimens were 100 mm × 30 mm × 10 mm, as cut from the compact board by a cutting tool. The inner span was 80 mm; the crosshead speed was 1 mm/min. Three specimens for each composition were tested at room temperature.
3 Results
(a)–(d) shows the morphology of the glass fiber after the mechanical mixing of silica powder and fibers for 10 min. The hydrophobic silica content varies from 0% to 50%. The fiber was covered with nano-silica powder after mixing. The glass fiber with 0% hydrophobic silica exhibits the thickest coating layer, as shown in (a). In contrast, the fiber with 50% hydrophobic silica shows the thinnest coating layer. The thickness of the coating layer decreases roughly with increasing hydrophobic silica content. Such different silica coating layer structure may be related to different thermal conductivity and strength results.
Fig. 1 Coated glass fibers with (a) 0%, (b) 10%, (c) 30% and (d) 50% hydrophobic silica after mechanical processing.
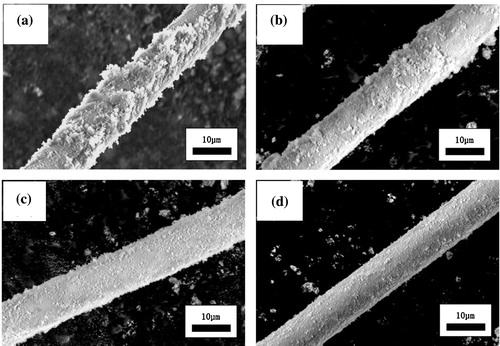
shows the values for the apparent density and porosity of fibrous silica compacts. The compacts show an apparent density of around 350 kg/m3. The density of the compact with 0% hydrophobic content exhibits a slightly higher value of 375 kg/m3. The theoretical densities of the silica and glass are close to each other, approximately 2700 kg/m3. The porosity in each compact is thus close to 87%. It demonstrates that the fibrous silica compacts with high porosity and light weight are successfully prepared in the present study.
Table 2 Density and porosity of fibrous silica compacts with various hydrophobic silica contents.
shows the fracture surface of fibrous silica compacts containing 0% and 50% hydrophobic silica. The fracture surface is perpendicular to the die-pressing direction. The (a) shows a preferred orientation for the glass fibers. The exposed fibers tend to lie on the plane perpendicular to the pressing direction. While the hydrophobic content increases up to 50%, the micrograph (b) shows an almost similar structure. Therefore, it is suggested that the fibers within the compact form a preferred orientation. From such structure, it is expected that the fibers would be pulled out at the fracture surface during the flexural test.
Fig. 2 Fracture surface of fibrous silica compacts containing (a) 0% and (b) 50% hydrophobic silica.
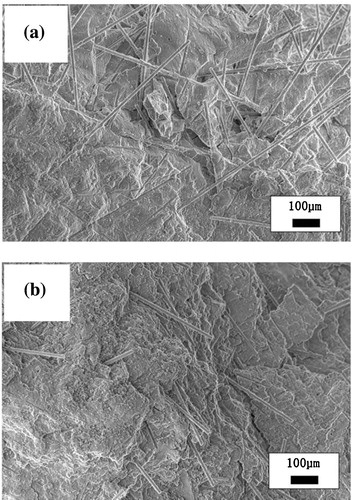
For the present study, the thermal diffusivity was measured by a laser flash method and the specific heat capacity by a DSC method. The specific heat capacity of the compact with hydrophobic silica content of 0%, 30% and 50% specimens is 0.740 J/K g, 0.739 J/K g and 0.746 J/K g at 300 K, respectively. The average value, 0.742 J/K g, is employed in calculating following thermal conductivities in the study. shows the thermal conductivities for the compacts with various hydrophobic silica contents. When the hydrophobic silica content was 0%, its thermal conductivity is 0.042 W/m K. With the addition of only 5% of hydrophobic silica, the thermal conductivity reduces to 0.033 W/m K. Then the value remains around 0.035 W/m K with increasing hydrophobic silica content up to 50%. The figure demonstrates that the addition of hydrophobic silica can reduce the thermal conductivity of fibrous silica compacts effectively.
shows the results for the flexural strength. Error bars in the figure indicates the standard deviations. The strength of the fibrous silica compacts with 0% hydrophobic silica content is 0.44 MPa. The strength is high enough to allow subsequent machining. Nevertheless, with the addition of 5%–10% of hydrophobic silica, the strength decreased significantly to around 0.18 MPa. The strength then decreased slightly with increasing the hydrophobic silica content up to 50%, and reached a low value of 0.1 MPa. On the whole, the experimental results indicate that the thermal conductivity and strength depends strongly on the amount of hydrophobic silica.
4 Discussion
Two functional groups, silanol and siloxane, are reported on the surface of hydrophilic silica particles used in the present study [Citation18]. Silanol group with the connectivity Si–O–H is a hydrophilic functional group; siloxane group with the connectivity Si–O–Si is a hydrophobic functional group [Citation18]. The hydrophobic silica particle used is a product prepared from the hydrophilic silica [Citation18]. After treated by hexamethyldisilazane ((CH3)3SiNHSi(CH3)3), the silica property changes from hydrophilic to hydrophobic type, due to the existence of Si–O–Si–(CH3)3 on particle surface. A previous report [Citation19] indicated that the density of silanol on the surface of hydrophilic silica used in the present study is 2.2 SiOH/nm2. After the treatment, the density of silanol decreased to 0.54 SiOH/nm2; the surface thus shifted to hydrophobic type.
shows the schematics for the interactions between the silica particles after the mechanical processing. While the hydrophobic particle content amount is 0%, as in (a) the Si–O–Si bonding between silanol groups can be formed easily after receiving mechanical energy during the processing, which is high enough to produce dehydration condensation reaction between OH groups [Citation4,Citation6]. It increases the contact area between silica particles. On the contrary, with the addition of hydrophobic particles, the Si–O–Si bonding formed by hydrophilic Si–OH groups will be sterically hindered by the hydrophobic Si–O–Si–(CH3)3 groups, as in (b). The contact area between particles may decrease after the mechanical processing. It is expected that the contact area between particles will decrease with increasing the hydrophobic silica. Such bonding situation is related to the different silica layer coating structure on the processed fibers. As a result, the addition of hydrophobic particles led to a decreased surface layer’s thickness, as shown in (a)–(d).
Fig. 5 Schematics for fibrous silica composite particles (a) with only hydrophilic particles and (b) with the mixtures of hydrophilic and hydrophobic silica particles.
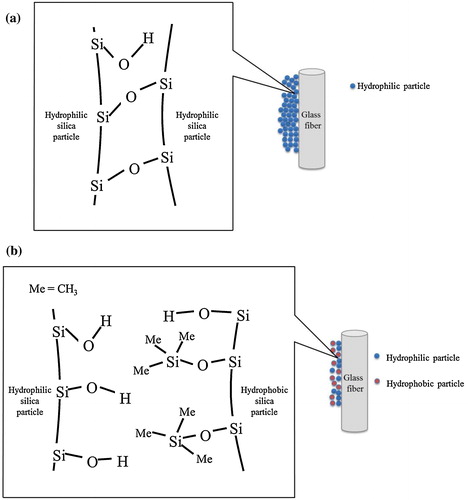
As shown in (a) and (b), the coated layer amount on the fiber surface is decreased with the addition of only 10% hydrophobic silica. It leads to the decreasing of conductive heat transfer of solid, due to the decreasing of the contacting area between silica particles. While the hydrophobic content increases from 10% to 50%, the thermal conductivity remains low. As in (b)–(d), the silica surface layer is similar with each other; consequently, their thermal conductivities are close to each other.
On the other hand, the flexural strength of the compact with 0% hydrophobic silica is decreased by half as 5%–10% of hydrophobic silica was added. The strength of a thermal insulation compact is mainly dominated by the contact area between fibers and silica particles. From the above-mentioned reason, the contact area between coated fibers decreases due to the addition of a small amount of hydrophobic particles. Besides, the cohesive force between hydrophilic silica particles would decrease after the addition of hydrophobic silica particles. This is because the hydrophobic silica particle has rich Si–CH3 group on its surface, and the chemical bonding of Si–O–Si is decreased after the addition of hydrophobic particles. Due to these two effects, the mechanical strength of the compact would decrease after the addition of hydrophobic silica.
5 Conclusions
The effect of ratio of hydrophilic to hydrophobic silica on the properties of the fibrous silica compact is investigated. With the addition of only 5% of hydrophobic silica, the thermal conductivity decreased from 0.042 W/m K to 0.033 W/m K; a low value remained with increasing hydrophobic content up to 50%. The mechanical strength shows a similar trend with that of thermal conductivity. The strength decreases after the addition of 5% hydrophobic silica; then decreases slightly with increasing content from 10% to 50%. The change of thermal conductivity and strength was related to the surface structure of fiber in the compact. With increasing hydrophobic silica content, the contact area between fiber and particles and the cohesive force between silica nanoparticles are decreased. Such decrease results in lower thermal conductivity and lower mechanical strength.
References
- D.R.SmithJ.G.HustNISTIR 89-39011989National Institute of Standards and TechnologyU.S
- D.R.SmithApparent thermal conductivity of fumed-silica standard reference materialsC.J.CremersH.A.FineThermal Conductivityvol. 211990Plenum PressNew York261276
- H.AbeI.AbeK.SatoM.NaitoJ. Am. Ceram. Soc.88200513591361
- I.AbeK.SatoH.AbeM.NaitoAdv. Powder Technol.192008311320
- H.BarthelM.HeinemannM.StintzB.WesselyChem. Eng. Technol.211998745752
- T.W.LianA.KondoT.KozawaT.OhmuraW.H.TuanM.NaitoCeram. Int.41201599669971
- T.OhmuraM.TsuboiNetsu Bussei131999264270
- T.OhmuraM.TsuboiM.OnoderaT.TomimuraReports of Institute of Advanced Material Study Kyushu Universityvol. 1620021317
- T.OhmuraM.TsuboiM.OnoderaT.TomimuraTherm. Sci. Eng.1120034344
- T.OhmuraI.AbeY.ItoK.SatoH.AbeM.NaitoJ. Soc. Powder Technol. Jpn.462009461466
- T.W.LianA.KondoM.AkoshimaH.AbeT.OhmuraW.H.TuanM.NaitoAdv. Powder Technol.272016882885
- W.J.ParkerR.J.JenkinsC.P.ButlerG.L.AbbottJ. Appl. Phys.32196116791684
- J.A.CapeG.W.LehmanJ. Appl. Phys.347196319091913
- M.AkoshimaB.HayM.NedaM.GrelardInt. J. Thermophys.342013778791
- K.D.MaglićA.CezairliyanV.E.PeletskyCompendium of Thermophysical Property Measurement Methods, Survey of Measurement Techniquesvol. 11984669685
- M.NaitoA.KondoT.YokoyamaISIJ Int.331993915924
- D.TaharaY.ItohT.OmuraH.AbeM.NaitoCeram. Trans.1462004173177
- Technical Bulletin 11: Basic Characteristics of AEROSILR Fumed Silica2006Evonik Industries
- J.MathisG.WannemacherJ. Colloid Interface Sci.12519886168