Abstract
Within architecture, microalgae are employed to address sustainability issues and mitigate the impacts of anthropogenic carbon dioxide (CO2) emissions. This study proposes digital fabrication of ceramic ‘living’ building components as an investigative tool for design conditions. The health of the chlorophyte (green) microalga Chlorella vulgaris was monitored over two-week periods when immobilized in kappa carrageenan and clay binder-based hydrogels, and grown on a range of digitally fabricated ceramic components. The use of 3D printing is presented in relation to laboratory testing of controlled substrate variables including the impact of ceramic firing temperature, component wall thickness, three types of geometry for exploring cell growth, surface patterns to investigate cell migration, internal chamber subdivisions and clay type. The experiments reveal the benefits and limitations of creating micro-ecologies for algae growth through the introduction of geometry variation. In this study, the natural organismal sensing abilities are explored as a means for cell distribution.
Introduction
Bio-design is an emerging field in architecture that utilizes hybrid knowledge from a plethora of science and design disciplines. Bio-design often enlists biomimetic architecture principles to provide sustainable solutions by drawing inspirations from nature and integrating scientific findings during the design process (Chayaamor-Heil and Vitalis Citation2021). Such investigations often span digital computation, biology and craft to propose a new multidisciplinary mode of creation (Stefanova Citation2021). This is particularly pertinent as there is a growing need to reposition humanity’s relationship with nature and revise making practices that sustainably embrace biological solutions. There has been a steady shift from imitating nature in mechanical processes to integrating living organisms and their metabolic functions to replace the need for energy-demanding processes as well as potentially achieving multiple tasks in one system. Revolutionary perspectives on living materials research include using bacteria to stabilize ground conditions, create responsive muscle systems, using fungi to digest toxins, and cyanobacteria to produce bio-mineralized components (Guyet et al. Citation2018; Birch et al. Citation2021; Shekhar, Maurya, and Srivastava Citation2017; Heveran et al. Citation2020). A further example is the use of microalgae to bioremediate wastewater and capture carbon dioxide (CO2). Algae and cyanobacteria produce at least 50% of the world’s oxygen and have adapted to most environments, resulting in an abundance of specialized biodiversity (Chapman Citation2013; Guiry Citation2012). Careful consideration must be given to the needs of the species to be deployed for a given site. This necessitates the development of design and testing the design within human-made environments that support living organisms.
Biocomposite materials can provide a new palette of products for a sustainable building fabric that is grown and able to perform desirable functions previously serviced by mechanical systems (Stefanova, Bridgens, In-na, et al. Citation2020; Fazal et al. Citation2018; Månsson Citation2012; Su, Mennerich, and Urban Citation2012). Building on existing research that uses minimal moisture environments that sustain photosynthetic organisms through the hygroscopic properties of material substrates, the present study evaluated ceramic biocomposites and the effect of component wall thickness, internal subdivisions, clay type and different firing temperatures on the photosynthetic performance of living microalgae (Chlorella vulgaris) embedded within two matrix types (kappa carrageenan and clay binder) (In-na et al. Citation2020; Stefanova et al. Citation2021; In-na, Lee, and Caldwell Citation2021). The study postulates the creation of microenvironments through the use of designed geometries that permit living organisms to migrate to the most favourable growth zones, harnessing organismal intelligence.
Ceramics are of interest for the purposes of integrating biocomposites into the built environment due to their hygroscopic properties when unglazed, offering a natural means of distributing moisture and nutrients throughout the structure through liquid capillary flow as explored by Dudukovic (Dudukovic et al. Citation2021). Furthermore, ceramics present a wide range of applications from loadbearing unit-based components to tiles, screens and three-dimensional self-supporting products that present opportunities for probiotic architectural design (Ramirez-Figueroa and Beckett Citation2020). From a design perspective, such minimal moisture algae cultivation is less restrictive than the use of liquid algae cultures. A practical solution with minimal moisture is possible via biocomposite technology that can operate with very low water demand and would offer higher cell loading per unit area.
The craft of ceramic digital fabrication
Digital fabrication has steadfastly accompanied a large proportion of bio-design investigation (Elsacker et al. Citation2021; Zhou et al. Citation2021) where natural intelligence is paired with embedded digital intelligence (Zimbarg Citation2021). Within bio-architecture, 3D printing is present in studies with various living cells including printing of living mycelium for furniture design, bacterial cellulose printing, or printing with living algae cells on textiles (Fairs Citation2013; López et al. Citation2017; Stefanova, In-Na, et al. Citation2020). Digital fabrication via 3D printing gives a unique opportunity for the testing of parameters through prototyping where the level of precision, replaceability and ability to rapidly alter designs to respond to new data is particularly well suited for design investigations that utilize both laboratory and design tools. Pressure extrusion systems lend themselves to bio-design investigations as they can accommodate bespoke matrices as well as materials that may offer greater level of compatibility with living organisms than standardized filaments commonly used in heat-based extrusion. The use of digital manufacture within this study offers an alternative to manual techniques, for the development of the biocomposite substrate. Digital fabrication permits the manufacture of complex structures that provide control over the amount of surface area as well as the ability to create lightweight ceramic components that can be standardized and replicated outside of a commercial setting. The designed geometries are inspired by high surface area structures formed by the silicified shells of diatoms – a highly successful group of single-celled microalgae (Cassaignon et al. Citation2014) that present an example of a natural composite structure. The level of precision and uniformity within the created geometries, makes this method of fabrication particularly applicable within laboratory testing where the geometry of components can be assessed because of the consistency of final products.
Digital and manual fabrication have often been framed as a dichotomy between mechanical processes and craft. It is often assumed that the digital is divorced from intuitive processes and that its predetermined outcome limits creativity, replacing it with automated precision. However, when printing with clay the nature of the material acquires an experiential quality during the making process that goes beyond digital instructions executed by the machine. Clay responds to gravity whilst wet, especially with an increased moisture content compatible with 3D printing. This material behaviour is taken into consideration when designing the components, which affects both the minimum wall thickness as well as the geometry angles. Designing for 3D printing is not a linear process and requires testing to help refine the final design and plays a role within the level of complexity. In this study, the fabrication process incorporates manual adjustment of the geometry during printing with various traditional tools such as a wet brush to aid layer adhesion, and pottery instruments for the creation of holes and refinement of geometry to ensure correct deposition and the incorporation of necessary openings. Although digital fabrication allows a high level of complexity that can serve to increase the surface area, it may not be possible to achieve a high level of resolution; therefore, strategies that provide smoother surfaces were explored for the proposed study as shown in Figure .
Method
The methods utilized in this paper are based on existing protocols used to develop algae-based biocomposites (In-na et al. Citation2020; Stefanova, Bridgens, Armstrong, et al. Citation2020; Stefanova et al. Citation2021). The bio-gel matrices incorporate the use of kappa carrageenan, a hydrocolloid polymer extracted from red seaweeds and a clay-based paint binder (Auro 331) (McHugh Citation2003; Auro Citationn.d.). The study was split into six parts: (a) kappa carrageenan and Auro binder-based matrices applied to (b) a range of wall thickness ceramic components (hereafter referred to as vessels) fired at (c) 1200°C, compared with a firing temperature of 1000°C, (d) four different clay types (157-1142 White Special Stoneware, Porcelain and Stoneware ES65 and White Fleck) fired at fired at 1000°C with two wall layers along with (e) two matrix types and (f) multiple internal chamber subdivisions (0% infill, 15% rectilinear infill, 25% aligned rectilinear infill, 25% cubic infill) fired at fired at 1000°C with two wall layers, using 157-1142 White Special Stoneware coated in both matrix types for comparison.
Substrate design, preparation and 3D printing
The porosity of the clay is used to distribute moisture and nutrients to provide a suitable environment for microalgae growth. The vessels were designed with a hollow centre to be filled with nutrient enriched water through a small round opening at the top. For this study, 157-1142 White Special Stoneware (sourced from http://www.potclays.co.uk) was used initially as smoother lower aggregate makeup clays are better suited to minimal moisture C. vulgaris cultivation (Stefanova, Bridgens, In-na, et al. Citation2020; Stefanova, Bridgens, Armstrong, et al. Citation2020). Clay pH (Mettler Toledo Seven Compact) was tested by suspending 1 g in 5 mL of deionized water. The geometries were modelled in 3D Studio Max 2018 and exported as.OBJ files into Slicer 3D software to generate a 3D printing file for a 3 mm nozzle clay extruder. The printer used was Lutum 4.5 air-based extrusion clay printer at a pressure of 60 psi. Wet clay sold in 12 kg bags was mixed with 10% w/w water to achieve a soft consistency compatible with the 3D printing equipment. The clay was manually loaded into 2 kg cartridges.
Geometry
Three orthographic pyramid geometries were developed based on a pyramidal geometry that permitted digital fabrication with a desktop size clay printer whilst permitting developmental assessment using Imaging-PAM M-Series equipment with homogenous illumination imaged area of 10 × 13 cm. Although it was initially inferred that greater area would accommodate larger number of cells the study seeks to establish how microclimatic conditions created by the variations of geometry affect the growth and saturation of the algae colonies. By pulling surfaces outward there is a greater increase of area compared to inward folding. However, surfaces present greater risk of sudden evaporation in corners that move away from the centre point. The base geometry offers the smallest surface area for deposition of cells however it provides the most constant conditions in terms of access to light and evaporation and therefore the least amount of microenvironmental conditions. All geometries share a common height dimension as well as base area offering a set of base constraints (Table ).
Table 1. Geometry variations as design in software, sowing values prior to kiln firing that resulted in 20% shrinkage.
Wall thickness
In the first assay, four wall thicknesses were tested, including one, two, three and four wall layers of 3 mm each. This was to establish the effect on water distribution in relationship to wall thickness. Wall thickness was added internally reducing the internal space, but maintaining the same outer shell dimensions (Figure ).
Internal chamber subdivision
Variations of internal chamber geometry were designed to establish if water distribution through internal partitions would influence cell development along with the impact on fabrication. The design of the internal subdivision patterns was generated in Sl3er 3D (open-source 3D printing software for the generation of 3D printer compatible files, available from slic3r.org). Wholes were placed manually during printing to connect adjacent pockets so as to permit water to fill the entire interior through a single external opening located at the top of each geometry. Therefore, this part of the study required a hybrid manufacture approach where digital and traditional fabrication was used to generate the final vessel (Figure ).
Clay type
Previous small scale controlled laboratory studies indicate a variation of response of Chlorella vulgaris microalgae in relationship to clay type (Stefanova, Bridgens, In-na, et al. Citation2020; Stefanova, Bridgens, Armstrong, et al. Citation2020). The current study builds on these findings and seeks to establish the impact of scaling and geometry variation upon the interaction between living cells and clay type. The same designs (2 walls, 3 geometries) were replicated in three clay types; porcelain, a smooth white clay, 157-1142 White Special Stoneware, an off-white clay with an even composition, White Fleck an off-white clay with low aggregate content and ES65, a red terracotta clay with aggregate (Figure ).
Firing temperature
Ceramics have a different porosity depending on the temperature of firing in a kiln. The kiln used was an Ecotop 43 L-UK from Helmut Rohde GmbH. The full firing cycle involved ramps of 60°C per hour until reaching 600°C followed by 250°C per hour until reaching 1200°C and a gradual cooling initiated upon reaching maximum temperature lasting 14 h. The brisk firing cycle involved ramps of 30°C per hour until 250°C, 50°C per hour until 600°C followed by 250°C per hour until reaching maximum temperature of 1000°C and gradually cooling for 12 h upon reaching maximum temperature. Surface characterization was conducted by scanning electron microscopy using a Hitachi TM 3000 SEM.
Algae matrix preparation
The inoculating liquid algae culture was grown in full strength Blue–Green medium (BG11) comprising 1.5 g/L NaNO3, 0.036 g/L CaCl2 · 2H2O, 0.075 g/L MgSO4 · 7H2O, 0.04 g/L K2HPO4 and 0.02 g/L Na2CO3, at 18 ± 2 °C with a 16:8 h light to dark photoperiod, at a light intensity of 2,500 lux (≈30.5 μmol m−2 s−1) provided by 30 W daylight-type fluorescent tubes (Sylvania Luxline Plus, n = 6) (Stanier et al. Citation1971; Thimijan and Heins Citation1983). The cultures were placed in 50 mL Falcon tubes and centrifuged at 1620 RCF (relative centrifugal force) for 10 min to produce a dense algae slurry. The algae slurry was mixed with the tested matrix at a ratio of 0.05 mL algae slurry per 1 mL of gel (Stefanova, Bridgens, In-na, et al. Citation2020).
Each bio-gel matrix was prepared in 20 mL batches in 50 mL beakers. For the baseline kappa carrageenan treatment, 0.8 g of kappa carrageenan (from >99.9% pure powder; Sigma Aldrich, UK) was added to 20 mL (0.04 g/mL) of full strength BG11 and stirred at room temperature. Once a gel-like consistency was achieved, 0.4 mL of C. vulgaris slurry was added and stirred until homogeneous. Auro 331 Clay Paint binder (AURO Paint Company, UK) were tested as additives to the kappa carrageenan baseline. For the Auro paint, 0.64 g of kappa carrageenan was dissolved in 16 mL of BG11 (0.04 g/mL), to which 10 mL of Auro 331 was added (equivalent to 50% w/w Auro content) (Stefanova et al. Citation2021).
Set up and incubation
An even layer of the two mixtures was added using a paintbrush, leaving the base and a strip of 0.5 cm off the base clear. Each vessel was placed within a plastic well plate lid (Figure ). The vessels were filled with 40 mL BG11 using a syringe and an additional 10 mL of BG11 was added to the well plate.
Figure 5. (A) Algae Auro binder and kappa carrageenan matrix being applied to an inset sample using a brush, (B) Algae kappa carrageenan matrix coated ceramic samples.
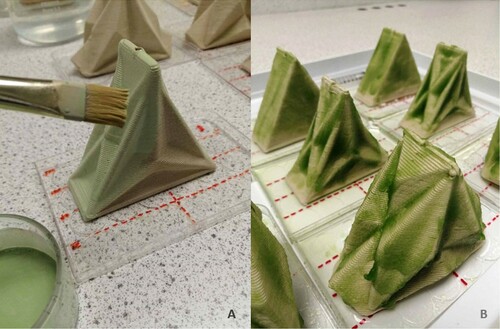
The samples were incubated in triplicate at room temperature with each sample set of ceramics and controls placed in a non-airtight clear plastic box measuring 47 × 35 × 24 cm and sprayed with deionized water once every 24 h. A 45 W plant growth light with 52 red and 28 blue lamp beds was used to illuminate the samples on a light (16 h) to dark (8 h) cycle.
Control samples were tested in triplicate as follows; BG11 and algae slurry suspension samples, algae slurry and carrageenan, algae slurry, carrageenan and Auro binder. Samples of 3 g/ 3 ml were cultivated in 6 well-plates that remained open for the duration of the test and were incubated in the same conditions as the ceramic samples.
Imaging PAM and visual observation
Cell viability was assessed using an imaging pulse amplitude modulated-fluorometer (Imaging-PAM M-Series; Walz GmbH) that quantifies the level of chlorophyll fluorescence using intense light pulses to stimulate photosystem II (Schreiber Citation2004). Data were collected every two days for 14 days by opening the plastic container and placing each individual sample along with its well plate lid within the imaging chamber and applying 1 μsec pulses of 660 nm (pulsed LED, 0.5 μmol quanta m−2 s−1) to induce photosynthesis using 16 red LEDs (660 nm) and 16 near infrared LEDs (780 nm) (Figure ).
Figure 6. (Left) Algae Auro binder matrix 1 Wall Day 0, imaged using I-PAM (Right) Same sample and imaging method Day 14 showing increase in cells and cell migration to the well-plate. Black indicates an absence of photosynthetic cells, whilst greens and blues indicate highest amount of chlorophyll fluorescence. [See Colour Online].
![Figure 6. (Left) Algae Auro binder matrix 1 Wall Day 0, imaged using I-PAM (Right) Same sample and imaging method Day 14 showing increase in cells and cell migration to the well-plate. Black indicates an absence of photosynthetic cells, whilst greens and blues indicate highest amount of chlorophyll fluorescence. [See Colour Online].](/cms/asset/734f7ca2-15b9-4c65-a114-540cecbe3a7d/tasr_a_2058908_f0006_oc.jpg)
Statistical analysis
Normality of the data was tested using the Anderson–Darling test using Minitab 18. Since all data were non-normally distributed with two factors, the non-parametric Scheirer–Ray–Hare test was conducted using RealStatistics add-in on Microsoft Excel.
Results
Substrate characterization
The pH of the clay was 7.5, which is compatible with C. vulgaris survival. The higher firing temperature produced reduced porosity as shown in Figure and greater strength of the ceramic as suggested by the smaller pore size (Cultrone et al. Citation2004).
Kappa carrageenan matrix
The samples fired at 1000°C outperformed those fired at 1200°C (Scheirer–Ray–Hare, n = 64, d.f. = 1, H = 20.48, P ≤ 0.001), although both sets supported positive fluorescence yields for the duration of the experiment. Geometry wall thickness was also significant (Scheirer–Ray–Hare, n = 64, d.f. = 3, H = 8.81, P = 0.032), with the 4-walled vessels supporting the highest fluorescence yield, although there was no clear trend among the other multi-walled vessels. There were no significant interactions between the two variables (Scheirer–Ray–Hare, n = 64, d.f. = 3, H = 2.14, P = 0.544) (Figures and ).
Binder and kappa carrageenan matrix
There was a clear differentiation between samples fired at 1200°C and 1000°C, with the former retaining less water and prone to higher levels of evaporation due to the binder drying quicker than a carrageenan gel matrix as observed upon application. In this set of experiments firing temperature was a significant factor (Scheirer–Ray–Hare, n = 64, d.f. = 1, H = 47.26, P ≤ 0.001) whereas geometry wall thickness was not (Scheirer–Ray–Hare, n = 64, d.f. = 3, H = 0.40, P = 0.940), the interaction between the two variable was also not significant (Scheirer–Ray–Hare, n = 64, d.f. = 3, H = 0.52, P = 0.914) (Figures and ).
Internal chamber subdivision
The samples of various internal subdivisions with gel coatings exhibited more consistent performance throughout the experiment whereas binder coated samples showed greater fluctuation, however matrix type was not significant (Scheirer–Ray–Hare, n = 80, d.f. = 1, H = 3.74, P = 0.053). Internal chamber subdivision was significant (Scheirer–Ray–Hare, n = 80, d.f. = 4, H = 11.68, P = 0.020). There were no significant interactions between the two variables (Scheirer–Ray–Hare, n = 80, d.f. = 4, H = 7.48, P = 0.113) (Figures and ).
Clay type
The samples of various clay types with gel coating exhibited more consistent performance throughout the experiment with ES65 being the only one to show decline in maximum fluorescence yield, whereas Auro 331 coated samples underwent a period of decline followed by gradual increase in fluorescence yield. Matrix composition was a significant factor in this assay (Scheirer–Ray–Hare, n = 64, d.f. = 1, H = 6.44, P = 0.011). Glay type was also significant (Scheirer–Ray–Hare, n = 64, d.f. = 3, H = 20.35, P = 0.000) and there was significant interactions between the two variables (Scheirer–Ray–Hare, n = 64, d.f. = 3, H = 13.85, P = 0.003) (Figures and ).
Visual observations
The translucent nature of the carrageenan mixture allowed imaging of cells that were locked within the matrix using PAM, which appeared as a higher density of cell in the early stage visible to the naked eye and showing clearly in I-PAM (Figure ). The Auro binder matrix, however, offered an impermeable surface where the colour of the mixture was considerably lighter and cells located below the surface were not imaged. Over the 14 days period however more saturated patches began to appear in the case of 1000°C fired ceramic samples. The distribution indicated that cells grew away from outward folds and that smooth surfaces or inward folds offered a more hospitable environment. This is likely due to higher levels of moisture at the inward folds along with the lower level of algae cell wash off that typically occurs at exposed folding channels.
Figure 16. Photograph and I-PAM of 2 Wall sample fired at 1000°C with Auro binder (A) day 0 (B) day 14. The images demonstrate how the matrix visibly acquires a darker green colour indicating higher cell density whilst the I-PAM images demonstrate lighter areas in outward folds except for top edge which offers a flat surface.
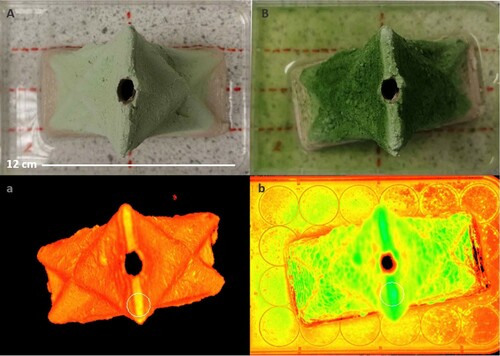
Discussion
This study employed Chlorella vulgaris, a naturally occurring, single cell photosynthetic microalga that is compatible with conditions presented within interior building settings, such as temperatures ranging between 18°C and 24°C, as well as a light and dark cycle that is typically found within offices and other public use buildings (Serra-Maia et al. Citation2016). In addition to its compatibility with many interior environments, C. vulgaris is a resilient species that is less susceptible to issues of contamination, can withstand limiting factors such as moisture level fluctuation and can utilize waste products such as human urine as nutrients (Stefanova, Bridgens, In-na, et al. Citation2020). The current work builds upon previous biocomposite studies that rely on immobilizing microorganisms (including living photosynthetic cells) within a protective layer, such as sol–gel ceramics, bio-polymer plastic alternatives (Soltmann and Böttcher Citation2008; Mihranyan Citation2011; Wahid et al. Citation2013; Vasilieva, Lobakova, and Solovchenko Citation2021). The demonstrated work follows the strand of architectural research that has manifested in a number of speculative and realized algae building projects that explore the potential for integration of living algae cells in an architectural contexts (Malik et al. Citation2020; Kim Citation2013; Lofgren Citation2013; Bruno, Jothinathan, and Rajkumar Citation2018). Here, we identified that the clay type and the design of the internal subdivision of the component have an impact on the development of the algae laden matrices. From our findings, it became apparent that a hollow chamber offers better growth conditions on the surface of the component compared to smaller subdivisions for both matrix types, whilst smoother clays such as Porcelain, 1142 White Special and White Fleckperform similarly in relationship to cell growth whereas ES65 exhibited a decline when combined with gel and outperformed the other clay types when paired with binder matrix. This indicated that the surface conditions responsible for algae growth are impacted by both the composition of the ceramic substrate as well as by both the internal and external geometry of the component.
We have demonstrated the role of digital fabrication in the development and laboratory testing of living ceramic biocomposite materials. The digital fabrication of 3D printing allows for consistency and variable testing of geometries. For each geometry, a single sample area was used from high cell density patches which offers an overview of the performance of optimal areas. Further studies that consider the whole area or multiple, equally distributed sample areas would be useful to determine the average performance of each unit. The variation of topography produced heterogeneous distribution and growth rate of cells, confirming it is possible to manipulate surface geometry to produce feasible microenvironments that able to function in desirable conditions.
Although, the geometry of the samples was not quantitatively assessed, a larger surface area offers more spaces for algae cells to be deposited per unit. Thus, the complexity that 3D printing permits is a welcome aspect in the design of such components and opens a plethora of bespoke design solutions that can incorporate greater level of bespoke design and flexibility. Based on the findings, we have gone on to prototype building size interlocking, unit-based components that have the potential to be stacked to create hollow interior partitions that can be internally supplied with water and nutrients (Figure ). Furthermore, digital manufacture and designs of tested geometries can be distributed virtually through open-source systems that would allow the onsite manufacture of pre-assessed components in places where laboratory settings are not possible.
Figure 17. 3D printed ceramic, interlocking hollow building block designs that feature an increased surface area and a large internal nutrient storage capacity. The designs present interlocking and reconfigurable units that add a level of flexibility within the building fabric. Work by Assia Crawford.
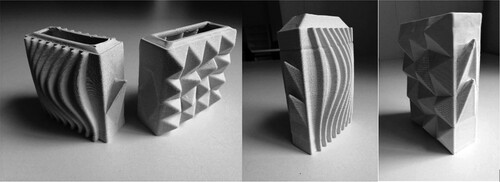
Maintenance and care become a vital factor in the successful performance of the proposed living material components similar to other living building proposals such as interior and exterior green facades (Pérez et al. Citation2014; Perini et al. Citation2011). This can act both as a limiting factor deterring widescale adoption or as a tool for cultivating a culture of care and a sense of responsibility (Puig de la Bellacasa Citation2017). There are alternatives to human labour such as mechanical monitoring and maintenance that would allow the components to be integrated on a large scale and where optimal conditions can be guaranteed. The system would have to be studied against the energy running requirements. This is possible if the energy sources for running the mechanical systems, such as artificial lighting, humidifiers and nutrient distribution systems that this type of living building component may require, are sourced from sustainable sources such as hydroelectric power. In addition to that water distribution and nutrient delivery need to be investigated as within the controlled study excess water caused cell wash off and contributed to cell migration within the well-plate container. Therefore, direct water delivery via rain, sprinklers and other high water content alternatives are unsuitable as they are likely to result in cell depletion or algae blooms caused by runoff.
Although, there is a level of resilience that comes from the design of hollow components that can hold a reserve of water and nutrients, surface evaporation occurs quickly and is likely to be exacerbated by air movement and types of inhabitation. This points to the need for an evaporation retardation strategy and a study of the components in appropriate in vivo settings such as offices and interiors of public buildings. Equally, the creation of hollow ceramic walls can be envisaged as an in situ 3D printed system using an air-drying alternative that can tap into the buildings plumbing and utilize human urine and rainwater as nutrient and water sources (Chen et al. Citation2019; Nerella and Mechtcherine Citation2019).
The design of a full building setup and the scale of fabrication goes beyond the scope of this study and merits separate investigation in an in vivo experiment. However, the design is likely to take the form of either a rigid or a tensile layer that can create an air pocket that limits the amount of air movement and evaporation and that may be able to direct and trap moisture from sources such as humidifiers or natural evaporation from water bodies, such as interior water features or it can be paired with water harvesting technologies (Chandler Citation2018).
The visible changes exhibited by the components over time illustrate live behaviour, therefore giving inhabitants a sense of coexistence with living biota. This phenomenon may strengthen recognition of the material as different from traditional building components, fostering a probiotic attitude to human environments. The study suggests a building fabric that is sustained through mucous membranes, that has agency and that cannot be fully standardized and that is the subject of speculative design thinking that explores the possibility of a living architecture (Armstrong Citation2018; Proksch Citation2018; Tandon and Joachim Citation2014). The type of architecture therefore will ask inhabitants to consciously share their environments, a concept that departs from anti-biotic notions of hygiene prevalent within twentieth century design thinking (Pike Citation2008; Lorimer Citation2020).
Conclusion
The study demonstrates a method for the digital manufacture of ceramic substrates for living building biocomposites. It reveals how the design of the geometry, wall thickness and firing temperature of the substrate actively influence the behaviour and performance of living photosynthetic microalgae within two types of matrices. The performance of the components is influenced predominantly by evaporation and moisture levels and therefore the results point to a need for a vapour control system. The experiments offer vital fundamental data that can inform further development of commercially viable, full system designs. In addition, the method of testing and fabrication sets out a blueprint for further investigations into ceramic-based biocomposites that rely on interdisciplinarity collaboration, method adaptation, and knowledge exchange.
Disclosure statement
No potential conflict of interest was reported by the author(s).
Additional information
Funding
References
- Armstrong, Rachel. 2018. Soft Living Architecture: An Alternative View of Bio-Informed Practice. 1st ed. London: Boomsbury Visual Arts.
- Auro. n.d. “Clay Paint, White | Auro.” Auro. Accessed September 29, 2020. https://auropaint.co.uk/product/high-grade-clay-paint-no-331/.
- Birch, Emily, Ben Bridgens, Meng Zhang, and Martyn Dade-Robertson. 2021. “Bacterial Spore-Based Hygromorphs: A Novel Active Material with Potential for Architectural Applications.” Sustainability 13 (7): 4030. doi:https://doi.org/10.3390/su13074030.
- Bruno, Benedict, D. Jothinathan, and M. Rajkumar. 2018. “Microbial Fuel Cells: Fundamentals, Types, Significance and Limitations.” In Microbial Fuel Cell Technology for Bioelectricity, edited by Kiyoshi Omine, Venkataraman Sivasankar, and Prabhakaran Mylsamy, 23–48. Cham: Springer.
- Cassaignon, Sophie, Robin de Maleprade, Nadine Nassif, and Jacques Livage. 2014. “From Living Light to Living Materials.” Materials Today: Proceedings 1: 209–215. doi:https://doi.org/10.1016/j.matpr.2014.09.024.
- Chandler, David L. 2018. “New System Recovers Fresh Water from Power Plants.” Massachusetts Institute of Technology. June 8, 2018. https://news.mit.edu/2018/new-system-recovers-fresh-water-power-plants-0608.
- Chapman, Russell Leonard. 2013. “Algae: The World’s Most Important ‘Plants’ – an Introduction.” Mitigation and Adaptation Strategies for Global Change 18 (1): 5–12. doi:https://doi.org/10.1007/s11027-010-9255-9.
- Chayaamor-Heil, Natasha, and Louis Vitalis. 2021. “Biology and Architecture: An Ongoing Hybridization of Scientific Knowledge and Design Practice by Six Architectural Offices in France.” Frontiers of Architectural Research 10 (2): 240–262. doi:https://doi.org/10.1016/J.FOAR.2020.10.002.
- Chen, Yu, Fred Veer, Oguzhan Copuroglu, and Erik Schlangen. 2019. “Feasibility of Using Low CO2 Concrete Alternatives in Extrusion-Based 3D Concrete Printing.” In First RILEM International Conference on Concrete and Digital Fabrication – Digital Concrete 2018, edited by T. Wangler and R. Flatt, 269–276. Cham: Springer. doi:https://doi.org/10.1007/978-3-319-99519-9_25.
- Cultrone, Giuseppe, Eduardo Sebastián, Kerstin Elert, Maria José de la Torre, Olga Cazalla, and Carlos Rodriguez-Navarro. 2004. “Influence of Mineralogy and Firing Temperature on the Porosity of Bricks.” Journal of the European Ceramic Society 24 (3): 547–564. doi:https://doi.org/10.1016/S0955-2219(03)00249-8.
- Dudukovic, Nikola A., Erika J. Fong, Hawi B. Gemeda, Joshua R. Deotte, Maira R. Cerón, Bryan D. Moran, Jonathan T. Davis, Sarah E. Baker, and Eric B. Duoss. 2021. “Cellular Fluidics.” Nature 58: 595. doi:https://doi.org/10.1038/s41586-021-03603-2.
- Elsacker, Elise, Asbjørn Søndergaard, Aurélie Van Wylick, Eveline Peeters, and Lars De Laet. 2021. “Growing Living and Multifunctional Mycelium Composites for Large-Scale Formwork Applications Using Robotic Abrasive Wire-Cutting.” Construction and Building Materials 283: 122732. doi:https://doi.org/10.1016/j.conbuildmat.2021.122732.
- Fairs, Marcus. 2013. “Mycelium Chair by Eric Klarenbeek Is 3D-Printed with Living Fungus.” Dezeen, October 20. https://www.dezeen.com/2013/10/20/mycelium-chair-by-eric-klarenbeek-is-3d-printed-with-living-fungus/.
- Fazal, Tahir, Azeem Mushtaq, Fahad Rehman, Asad Ullah Khan, Naim Rashid, Wasif Farooq, Muhammad Saif Ur Rehman, and Jian Xu. 2018. “Bioremediation of Textile Wastewater and Successive Biodiesel Production Using Microalgae.” Renewable and Sustainable Energy Reviews 82: 3107–3126. doi:https://doi.org/10.1016/j.rser.2017.10.029.
- Guiry, Michael D. 2012. “How Many Species of Algae Are There?” Journal of Phycology 48 (5): 1057–1063. doi:https://doi.org/10.1111/j.1529-8817.2012.01222.x.
- Guyet, Aurelie, Martyn Dade-Robertson, Anil Wipat, John Casement, Wendy Smithtadr, Helen Mitrani, and Meng Zhang. 2018. “Mild Hydrostatic Pressure Triggers Oxidative Responses in Escherichia Coli.” PLOS ONE 13 (7): e0200660. doi:https://doi.org/10.1371/journal.pone.0200660.
- Heveran, Chelsea M., Sarah L. Williams, Jishen Qiu, Juliana Artier, Mija H. Hubler, Sherri M. Cook, Jeffrey C. Cameron, and Wil V. Srubar. 2020. “Biomineralization and Successive Regeneration of Engineered Living Building Materials.” Matter 2 (2): 481–494. doi:https://doi.org/10.1016/j.matt.2019.11.016.
- In-na, Pichaya, Jonathan Lee, and Gary Caldwell. 2021. “Living Textile Biocomposites Deliver Enhanced Carbon Dioxide Capture.” Journal of Industrial Textiles. doi:https://doi.org/10.1177/15280837211025725.
- In-na, Pichaya, Abbas A. Umar, Adam D. Wallace, Michael C. Flickinger, Gary S. Caldwell, and Jonathan G. M. Lee. 2020. “Loofah-Based Microalgae and Cyanobacteria Biocomposites for Intensifying Carbon Dioxide Capture.” Journal of CO2 Utilization 42: 101348. doi:https://doi.org/10.1016/j.jcou.2020.101348.
- Kim, Kyoung-Hee. 2013. “Beyond Green: Growing Algae Facade.” In Architectural Research Conference University of North Carolina, edited by J. Chris, 500–505. Charlotte: Architectural Research Centers Consortium.
- Lofgren, Kristine. 2013. “Algae Powered House Biofacade Splitterwerk ARUP Colt International SCC Green Power Building ‘Inhabitat – Green Design, Innovation, Architecture, Green Building’.” Inhabitat. https://inhabitat.com/splitterwerk-architects-design-worlds-first-algae-powered-building-for-germany/algae-powered-house-biofacade-splitterwerk-arup-colt-international-scc-green-power-building/.
- López, Marlén, Ramón Rubio, Santiago Martín, and Ben Croxford. 2017. “How Plants Inspire Façades. From Plants to Architecture: Biomimetic Principles for the Development of Adaptive Architectural Envelopes.” Renewable and Sustainable Energy Reviews 67: 692–703. doi:https://doi.org/10.1016/j.rser.2016.09.018.
- Lorimer, Jamie. 2020. The Probiotic Planet. London: University of Minnesota Press. doi:https://doi.org/10.5749/j.ctv19cw9vg.
- Malik, Shneel, Julie Hagopian, Sanika Mohite, Cao Lintong, Laura Stoffels, Sofoklis Giannakopoulos, Richard Beckett, et al. 2020. “Robotic Extrusion of Algae-Laden Hydrogels for Large-Scale Applications.” Global Challenges 4 (1): 1900064. doi:https://doi.org/10.1002/gch2.201900064.
- Månsson, Stina. 2012. Cultivation of Chlorella Vulgaris in Nutrient Solution from Greenhouse Tomato Production. Swedish University of Agricultural Sciences. http://stud.epsilon.slu.se.
- McHugh, Dennis J. 2003. A Guide to the Seaweed Industry. Rome: Food and Agriculture Organization of the United Nations. http://www.fao.org/3/y4765e/y4765e00.htm#Contents.
- Mihranyan, Albert. 2011. “Cellulose from Cladophorales Green Algae: From Environmental Problem to High-Tech Composite Materials.” Journal of Applied Polymer Science 119 (4): 2449–2460. doi:https://doi.org/10.1002/app.32959.
- Nerella, Venkatesh Naidu, and Viktor Mechtcherine. 2019. “Studying the Printability of Fresh Concrete for Formwork-Free Concrete Onsite 3D Printing Technology (CONPrint3D).” In 3D Concrete Printing Technology, edited by Jay G. Sanjayan, Ali Nazari, and Behzad Nematollahi, 333–347. Oxford: Elsevier. doi:https://doi.org/10.1016/b978-0-12-815481-6.00016-6.
- Pérez, Gabriel, Julià Coma, Ingrid Martorell, and Luisa F. Cabeza. 2014. “Vertical Greenery Systems (VGS) for Energy Saving in Buildings: A Review.” Renewable and Sustainable Energy Reviews 39: 139–165. doi:https://doi.org/10.1016/j.rser.2014.07.055.
- Perini, Katia, Marc Ottelé, E. M. Haas, and Rossana Raiteri. 2011. “Greening the Building Envelope, Façade Greening and Living Wall Systems.” Open Journal of Ecology 1 (1): 1–8. doi:https://doi.org/10.4236/oje.2011.11001.
- Pike, Steve. 2008. “Manipulation and Control of Micro-Organic Matter in Architecture.” Neoplasmatic Design (Architectural Design) 78 (6): 21–23.
- Proksch, Gundula. 2018. “Built to Grow: Blending Architecture and Biology.” Technology Architecture + Design 2 (1): 118–119. doi:https://doi.org/10.1080/24751448.2018.1420972.
- Puig de la Bellacasa, M. 2017. Matters of Care: Speculative Ethics in More Than Human Worlds. Minneapolis: University of Minnesota Press. https://libsearch.ncl.ac.uk/primo-explore/fulldisplay?docid=NCL_ALMA21128631000002411&context=L&vid=NEWUI&lang=en_US&search_scope=NotPC&adaptor=Local Search Engine&tab=default_tab&query=any,contains,matters of care&offset=0.
- Ramirez-Figueroa, Carolina, and Richard Beckett. 2020. “Living with Buildings, Living with Microbes: Probiosis and Architecture.” Arq: Architectural Research Quarterly 24 (2): 155–168. doi:https://doi.org/10.1017/S1359135520000202.
- Schreiber, Ulrich. 2004. “Pulse-Amplitude-Modulation (PAM) Fluorometry and Saturation Pulse Method: An Overview.” In Chlorophyll a Fluorescence, 279–319. Dordrecht: Springer. doi:https://doi.org/10.1007/978-1-4020-3218-9_11.
- Serra-Maia, Rui, Olivier Bernard, Ana Gonçalves, Sakina Bensalem, and Filipa Lopes. 2016. “Influence of Temperature on Chlorella Vulgaris Growth and Mortality Rates in a Photobioreactor.” Algal Research 18: 352–359. doi:https://doi.org/10.1016/j.algal.2016.06.016.
- Shekhar, Sujata, Chandan Maurya, and J. N. Srivastava. 2017. “Remediation of Wastewater Using Mushroom: Pleurotus Ostreatus (Oyster Gill Mushroom).” International Journal of Scientific & Engineering Research 8 (7). http://www.ijser.org.
- Soltmann, U., and H. Böttcher. 2008. “Utilization of Sol–Gel Ceramics for the Immobilization of Living Microorganisms.” Journal of Sol-Gel Science and Technology 48 (1–2): 66–72. doi:https://doi.org/10.1007/s10971-008-1753-9.
- Stanier, R. Y., R. Kunisawa, M. Mandel, and G. Cohen-Bazire. 1971. “Purification and Properties of Unicellular Blue-Green Algae (Order Chroococcales).” Bacteriological Reviews 35 (2): 171–205. http://www.ncbi.nlm.nih.gov/pubmed/4998365.
- Stefanova, Assia. 2021. “Practices in Bio-Design: Design Research Through Interdisciplinary Collaboration.” In ICoRD 2021: Design for Tomorrow–Volume 3. 1st ed., edited by Amaresh Chakrabarti, Ravi Poovaiah, Prasad Bokil, and Vivek Kant, 41–52. Singapore: Springer Nature. doi:https://doi.org/10.1007/978-981-16-0084-5_4.
- Stefanova, Assia, Ben Bridgens, Rachel Armstrong, Pichaya In-Na, and Gary S. Caldwell. 2020. “Engineering a Living Building Realm: Development of Protective Coatings for Photosynthetic Ceramic Biocomposite Materials.” In The 7th International Conference on Architecture and Built Environment with Architecture AWARDs, 362–372. Tokyo: Get It Published Verlag.
- Stefanova, Assia, Ben Bridgens, Pichaya In-na, Gary Caldwell, and Rachel Armstrong. 2020. “Architectural Laboratory Practice for the Development of Clay and Ceramic-Based Photosynthetic Biocomposites.” Technology Architecture +Design 4 (2): 200–210. doi:https://doi.org/10.1080/24751448.2020.1804764.
- Stefanova, Assia, Pichaya In-Na, Gary S. Caldwell, Ben Bridgens, and Rachel Armstrong. 2020. “Flexible Photosynthetic Textile Biocomposites: Using Laboratory Testing and Digital Fabrication for the Development of Flexible Living Building Materials.” In 3rd International Conference on Materials Design and Applications, edited by Lucas F. Martins da Silva. Porto: University of Porto.
- Stefanova, Assia, Pichaya In-na, Gary Stephen Caldwell, Ben Bridgens, and Rachel Armstrong. 2021. “Photosynthetic Textile Biocomposites: Using Laboratory Testing and Digital Fabrication to Develop Flexible Living Building Materials.” Science and Engineering of Composite Materials 28 (1): 223–236. doi:https://doi.org/10.1515/secm-2021-0023.
- Su, Yanyan, Artur Mennerich, and Brigitte Urban. 2012. “Synergistic Cooperation Between Wastewater-Born Algae and Activated Sludge for Wastewater Treatment: Influence of Algae and Sludge Inoculation Ratios.” Bioresource Technology 105: 67–73. doi:https://doi.org/10.1016/J.BIORTECH.2011.11.113.
- Tandon, Nina, and Mitchell Joachim. 2014. Super Cells: Building with Biology. Vol. 41. TED Conferences. https://www.amazon.com/kindle/dp/B00ICXN3VA/ref=rdr_kindle_ext_eos_detail.
- Thimijan, Richard W, and Royal D Heins. 1983. “Photometric, Radiometric, and Quantum Light Units of Measure: A Review of Procedures for Interconversion.” HortScience 18 (6): 818–822.
- Vasilieva, Svetlana, Elena Lobakova, and Alexei Solovchenko. 2021. “Biotechnological Applications of Immobilized Microalgae.” In Environmental Biotechnology Vol. 3. Environmental Chemistry for a Sustainable World, Vol. 50, edited by K. M. Gothandam, S. Ranjan, N. Dasgupta, and E. Lichtfouse, 193–220. Cham: Springer Nature. doi:https://doi.org/10.1007/978-3-030-48973-1_7.
- Wahid, M. Haniff, Ela Eroglu, Xianjue Chen, Steven M. Smith, and Colin L. Raston. 2013. “Entrapment of Chlorella Vulgaris Cells Within Graphene Oxide Layers.” RSC Advances 3 (22): 8180–8183. doi:https://doi.org/10.1039/c3ra40605a.
- Zhou, Jiwei, Bahareh Barati, Jun Wu, Diana Scherer, and Elvin Karana. 2021. “Digital Biofabrication to Realize the Potentials of Plant Roots for Product Design.” Bio-Design and Manufacturing 4 (1): 111–122. doi:https://doi.org/10.1007/S42242-020-00088-2/FIGURES/13.
- Zimbarg, Ana. 2021. “Bio-Design Intelligence.” Proceedings of the 2021 DigitalFUTURES, July, 92–101. doi:https://doi.org/10.1007/978-981-16-5983-6_9.