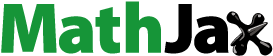
Abstract
We investigated the relationship between the corrosion of austenitic stainless steel (R-SUS304ULC) and the redox behavior of chromium in nitric acid solution under three conditions – boiling at atmospheric pressure, boiling at reduced pressure, and non-boiling – to evaluate the effects of the boiling phenomenon. In the Cr(III) oxidation rate measurement, about 20% of the Cr(III) was oxidized to Cr(VI) under atmospheric-pressure boiling at 384 K after 168 h. Under non-boiling conditions at 373 K, Cr(VI) was not observed. However, about 3% of Cr(III) oxidation was observed at 373 K with reduced-pressure boiling. Thermodynamic calculations showed that the abundance of Cr(VI) in boiling nitric acid was increased over that in non-boiling nitric acid, even at the same temperature. These results show that Cr(III) is more likely to oxidize under boiling conditions than non-boiling conditions. On the other hand, in the corrosion tests, we found that the apparent reduction rate of Cr(VI) as a result of corrosion of R-SUS304ULC was more than 10 times greater than the Cr(III) oxidation rate. Therefore, the corrosion of R-SUS304ULC appears to be dominated by the rate of Cr(VI) reduction in nitric acid solution regardless of the boiling or non-boiling conditions.
1. Introduction
The reprocessing of spent fuel by the plutonium and uranium recovery by extraction (PUREX) process creates a severely corrosive environment for structural materials because it is accompanied by a heating operation in nitric acid solution. At the first Japanese reprocessing plant in Tokai, corrosion problems were observed in heating equipment such as the dissolver and the high-level liquid waste (HLLW) evaporator [Citation1]. To solve these problems, ultra-low-carbon stainless steels were developed, which contain less than 0.02% carbon and reduced amounts of other impurity elements [Citation2,3]. These stainless steels have high corrosion resistance and are employed in the Rokkasho reprocessing plant [Citation4].
Corrosion is known to be accelerated by ions having high oxidizability in nitric acid solution, because they increase the corrosion potential of the stainless steel to the trans-passive state. Ions having high oxidizability, such as Ce, Ru, Pu, and Np [Citation5–10], are present in the spent fuel from nuclear reactors. Chromium is known to be generated as a corrosion product during processing; it results in the intergranular corrosion of non-sensitized stainless steels by Cr(VI) [Citation11]. Kajimura et al. [Citation12] examined the effects of corrosion products (such as Cr(VI), Cr(III), Fe(III), and Ni(II)) on the rate of stainless steel corrosion in nitric acid solution and found that only Cr(VI) rapidly increased the corrosion rate. It has been reported that boiling of the solution affects the redox behavior of Cr [Citation6,Citation12,Citation13]. This effect is an oxidation phenomenon of Cr(III) to Cr(VI) in nitric acid, and it has been attributed to the local over-concentration of the nitric acid upon boiling [Citation12]. In addition, McIntosh and Evans [Citation6] and Truman [Citation13] investigated the effects of NOx gas generated by the boiling of nitric acid solution. They reported that Cr(VI) becomes the stable oxidation state by the release of NO and NO2 gases from the nitric acid solution. Maness [Citation14] and Armstrong et al. [Citation15] found that Cr(VI) was reduced to Cr(III) by bubbling NO2 and NO in nitric acid solution. These studies indicate that the NOx gas component has a great influence on the oxidation state of chromium in nitric acid solution. Hence, it is necessary to consider the effects of such nitric acid boiling phenomena when evaluating the redox behavior of chromium.
In an actual reprocessing plant, the equipment may handle the nitric acid solution under reduced-pressure boiling conditions, such as in the HLLW and acid-recovery evaporators [Citation4]. Therefore, an evaluation of the relationship between the corrosion of austenitic stainless steel and the redox behavior of chromium in nitric acid under such conditions will provide useful information for equipment design and corrosion management in the reprocessing plant.
In this study, the redox behavior of chromium was evaluated under three conditions for the nitric acid solution: atmospheric-pressure boiling, reduced-pressure boiling, and atmospheric-pressure non-boiling; then, the relationship between the corrosion of R-SUS304ULC (ULC: ultra-low carbon) stainless steel and this behavior was determined.
2. Experimental
2.1. Materials
The test solution for the Cr(III) oxidation rate and rest potential measurements consisted of 8 M HNO3 containing 10 mM Cr(III) (Cr(NO3)3·6H2O, Nacalai Tesque, Inc.). The test solution for the corrosion tests and polarization measurements was 8 M HNO3 containing 10 mM Cr(VI) (CrO3, Wako Pure Chemical Industries, Ltd.). The 8 M HNO3 concentration is equivalent to those used in the HLLW and acid recovery evaporators at the Rokkasho reprocessing plant [Citation4]; the concentration was determined by potentiometric titration with 0.1 M NaOH solution. The Cr concentration was established with respect to the literature value of 3.95 mM reported for the HLLW [Citation16]. All chemicals were of reagent grade.
shows the chemical composition of the R-SUS304ULC specimen. The specimens for the corrosion tests were plate-type (30 × 15 × 2t mm) and the specimens for the polarization measurements were flag-type (measurement part: 20 × 5 × 1t mm, cross section of lead part: 1 × 1 mm). The surfaces were wet polished with emery papers #800, and rinsed with pure water and acetone under sonication.
Table 1. Chemical composition of R-SUS304ULC (mass%).
2.2. Spectrophotometry
The UV–visible spectral measurements were obtained using a Shimadzu UV-2550 spectrophotometer. The test solution was sampled in 1 mL volumes, and the Cr(VI) concentration was determined at 350 nm (ϵ = 874 M−1 cm−1) against a calibration curve.
2.3. Electrochemical experiments
shows the apparatus for electrochemical experiments. The potentiostat was an ALS/CH Instruments Model 611DT electrochemical analyzer. A three-electrode system was utilized: a BAS 002013 Pt or an R-SUS304ULC working electrode (surface area: 2.5 cm2), a Hokuto Denko Corp. HX-C7 Pt counter electrode, and a BAS RE-1C reference electrode (SSE: silver-silver chloride electrode, Ag/AgCl, sat. KCl). The length of the lead part of the working electrodes was extended by spot-welding with copper wire, and coating with a Teflon tube. The reference electrode was connected by a porous ceramic salt bridge. The test solution (100 mL) was introduced into a 300-mL Pyrex flask with a thickness of about 4 mm. The ratio of the test solution volume and the surface area of the R-SUS304ULC specimen was about 40 mL cm−2. In the rest potential determinations using the Pt electrodes, measurements were carried out 24 h after the solution reached the boiling temperature. For the polarization measurements with the R-SUS304ULC specimens, measurements were performed after the rest potential was stable (about 30 min after reaching the boiling point). The scan rate was 5 mV s−1 and measured to the anode side from a potential of about 100 mV less noble than the rest potential.
2.4. Thermodynamic calculations using the SOLGASMIX software
Using the SOLGASMIX program, we calculated the thermodynamic phase equilibrium to evaluate the amounts of Cr(III) and Cr(VI) present in the nitric acid solution.
2.5. Corrosion tests
shows the apparatus for the corrosion tests. An open Allihn condenser was connected to a separable Pyrex flask that was heated with a mantle heater. The pressure control system consisted of a vacuum pump and a controller. The specimens were suspended on a Zr wire installed in the Pyrex glass instrument and was installed in the Pyrex flask of volume 500 mL with 4 mm thick walls. The solution volume was 430 mL, and the ratio of the solution volume to the surface area of the specimen was about 40 mL cm−2. The test conditions were 353 K (non-boiling at atmospheric pressure and reduced-pressure boiling at 0.032 MPa), 373 K (non-boiling at atmospheric pressure and reduced-pressure boiling at 0.068 MPa), and 384 K (boiling at atmospheric pressure). The specimens were changed every 48 h/batch by immersion, and the tests were carried out for a total of 192 h (48 h/batch × 4 batches). The test solution was not exchanged in order to evaluate the time variation of the Cr(VI) concentration, i.e., the same solution was used throughout the test. After the immersion of each batch for 48 h, the specimens were weighed to evaluate the periodic corrosion rate.
3. Results and discussion
3.1. Cr(III) oxidation rate measurements
In this experiment, we evaluated the rate of Cr(III) oxidation by measuring the variation in the concentration of Cr(VI) in nitric acid solution over time by UV–visible spectrophotometry. The apparatus for these experiments was the same as for the corrosion tests in (without the specimen, Zr wire, and glass instrument). The solution volume was 430 mL. Tests were performed at 363 K (non-boiling at atmospheric pressure and reduced-pressure boiling at 0.05 MPa), 373 K (non-boiling at atmospheric pressure and reduced-pressure boiling at 0.068 MPa), and 384 K (boiling at atmospheric pressure). Measurements were carried out for 168 h after the solution reached the boiling temperature.
shows the time variation of the Cr(VI) oxidation rate with respect to the initial concentration of Cr(III). At atmospheric boiling (384 K), about 20% of the Cr(III) was oxidized to Cr(VI) after 168 h. Previous studies by McIntosh and Evans [Citation6] and Kajimura et al. [Citation12] reported that the oxidation rate of Cr(III) in boiling 8 M HNO3 solution at atmospheric pressure was about 20% for tests of 200 h or more. Motooka et al. [Citation17] reported that ∼30% of the Cr(III) was oxidized after 300 h under similar test conditions. After boiling at 373 K under reduced pressure, about 3% of the Cr(III) oxidized after 168 h. In contrast, no Cr(VI) was observed under the non-boiling, 373 K conditions. Moreover, Cr(VI) was not observed under either the boiling or the non-boiling conditions at 363 K. From the results in , we determined the rate constant for the pseudo-first-order oxidation under each test condition. The rate equation for Cr(III) oxidation is expressed as follows:
(1)
(1)
Figure 3. Time variation of the production rate of Cr(VI) in 8 M HNO3 solution (initial concentration of Cr(III) is 10 mM).
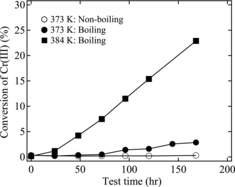
shows the k values for each test condition, calculated from the experimental results in and Equation (3). We see from that the rate constant for Cr(III) oxidation is governed by temperature. However, it is possible that the phenomenon of boiling affects the oxidation rate constant of Cr(III), because a rate constant of 3.428 × 10−8 s−1 was observed with reduced-pressure boiling at 373 K, whereas no oxidation was observed without boiling (non-boiling) at the same temperature. From these results, we considered that the Cr(III) oxidation rate was controlled by the chemical reactions of nitric acid. In particular, we observed that there is a close relationship between the oxidation rate and the boiling phenomenon of nitric acid. We will discuss this factor in Sections 3.2 and 3.3.
Table 2. Rate constants of pseudo-first-order oxidation of Cr(III) in 8 M HNO3.
3.2. Rest potential measurements
In these experiments, we measured the rest potential of an 8 M HNO3 solution containing Cr(III) to evaluate the redox potential of the test solution. Tests were performed at 373 K (reduced-pressure boiling) and 384 K (boiling at atmospheric pressure). shows the results from the rest potential measurements using a Pt electrode. The rest potentials were 1.11–1.13 V vs. SSE (=1.31–1.33 V vs. SHE (standard hydrogen electrode)) for reduced-pressure boiling at 373 K, and 1.13–1.14 V vs. SSE (=1.33–1.34 V vs. SHE) for atmospheric-pressure boiling at 384 K. Furthermore, we estimated the concentration ratios for HCrO4−/Cr3+ pairs from the experimental data. Kajimura et al. reported the following equations for the redox reactions of nitric acid and chromium [Citation12]:
(4)
(4)
(5)
(5)
The standard redox potentials (E0) were obtained from literature values [Citation18,19]. The Nernst equations corresponding to Equations (4) and (5) can be written as [Citation18,19]
(6)
(6)
(7)
(7)
(8)
(8)
(9)
(9) where R is the gas constant (8.3145 J mol−1 K−1), T is the temperature (K), F is the Faraday constant (9.6485 × 104 C mol−1), and G is the free energy (J mol−1). The value of E0 at each temperature was determined using reference thermodynamic data [Citation20]. However, for the calculations at 384 K, we used the value of E0 at 373 K, because no free energy or thermodynamic data were available for the higher temperature. From Equation (8) and the experimental results for the rest potential, then, for a redox potential (E) of 1.33 V under reduced-pressure boiling at 373 K, the concentration ratio of the HCrO4−/Cr3+ pair would be 5 × 10−7. Similarly, if the redox potential was 1.34 V under atmospheric-pressure boiling at 384 K, the pair was calculated as 1 × 10−6. These calculation results mean that Cr(VI) is not significantly generated. On the other hand, we observed the oxidation of Cr(III) to Cr(VI) to the extent of about 20% under atmospheric-pressure boiling conditions at 384 K and about 3% under the reduced-pressure boiling conditions at 373 K. To explore these results, we calculated the theoretical value of the redox potential at each temperature using Equations (6)–(9). shows the calculated values of the redox potentials of nitric acid and chromium. In the figure, the redox potentials are reversed at a certain temperature, which depends on the concentration ratio of the oxidant and reductant. Therefore, these results indicate that it is possible, from the viewpoint of equilibrium, to oxidize Cr(III) to Cr(VI) when the redox potential of nitric acid exceeds that of chromium. Furthermore, based on the experimental results of and the discussion in Section 3.1, we did not observe any clear differences in the Cr(VI) concentrations among the samples within 24 h. Thus, the oxidation of chromium did not occur in the time period allowed for the rest potential measurement in this study (24 h).
From the foregoing results, we considered that the boiling phenomenon increases the redox potential of nitric acid and affects the oxidation kinetics of chromium(III) ions. Motooka et al. [Citation17] reported the effects of NOx on the redox potential of boiling 8 M nitric acid. They assumed NO2 gas as the total gas component generated by the boiling of the nitric acid, and evaluated the effect of the NO2 partial pressure on the extent of chromium oxidation using the following equation:
(10)
(10)
The Nernst equation corresponding to Equation (10) is as follows [Citation19]:
(11)
(11)
Their calculations showed that Cr(III) is oxidized to Cr(VI) by about 2% in the case of an NO2 partial pressure of 10−2 atm. Therefore, in this study, we consider that the redox reaction of the chromium ion is also affected by the NOx gas component. Viewed in this light, it is possible that the oxidation kinetics of the chromium species is controlled by the formation of NOx gas above the boiling point of nitric acid.
3.3. Thermodynamic calculations using the SOLGASMIX software
The SOLGASMIX calculation code was developed by Eriksson et al. [Citation21,22]. It calculates the amount of each substance present in a system so as to minimize its total Gibbs free energy. The SOLGASMIX calculation code and the thermodynamic constants used in the calculations were obtained from the HSC Chemistry version 7.1 thermodynamic calculation software (Outokumpu Research, Finland). Kato et al. [Citation23] published a model calculation for boiling nitric acid using the SOLGASMIX program. They reported the significant nitrogen oxides involved in the determination of the redox potential of the nitric acid solution, namely NO3−, HNO3, HNO2, NO2, and NO. On this basis, we also included these nitrogen oxides in our calculations. shows the thermodynamic data for the chemical species of interest in this study. For the calculations, we assumed the substance to be in the ideal state. shows the initial values. We calculated the changes in the amounts of Cr(III) and Cr(VI) in the nitric acid solution with temperature and pressure. The initial concentration of nitrous acid was 1 mM, which is close to the measured value of the redox potential [Citation23].
Table 3. Constants of standard enthalpy, entropy and the coefficients of the heat capacity function for thermodynamic calculations.
Table 4. Initial conditions for thermodynamic calculations.
shows the calculation results. Under any conditions, the abundance of HNO2 continues to decrease with the simultaneous generation of NO2 gas. Similarly, above the boiling point, the generation of Cr(VI) in HCrO4− and H2CrO4 was confirmed with the simultaneous decrease in the abundance of Cr(III). While the boiling point was deviated from the calculation results of the temperature at gas generation, it is considered that the calculation code does not accurately calculate the vapor–liquid equilibrium. Kato et al. [Citation23] also reported the occurrence of a similar deviation. The results show that the oxidation of Cr(III) to Cr(VI) is facilitated by the increase in the redox potential of nitric acid, because the HNO2 concentration continually decreases with the discharge of NOx gas under the boiling conditions. We consider that, in addition to Equation (10), the decrease in HNO2 concentration is caused by thermal decomposition according to the following reactions [Citation24]:
(12)
(12)
(13)
(13)
(14)
(14)
(15)
(15)
Figure 6. Relationship between temperature and the amount of compounds in 8 M HNO3 solution calculated by thermodynamic boiling model at different pressures.
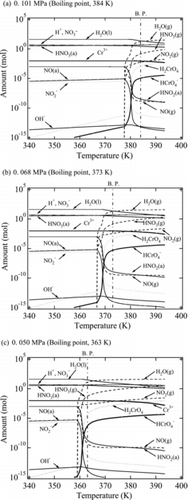
In (a), the abundance of HCrO4− at 0.101 MPa and 373 K was about 3 × 10−14 mol and that of H2CrO4 was about 2 × 10−12 mol. In contrast, at 0.068 MPa and 373 K ((b)), the Cr(VI) abundance increased, with ∼5 × 10−6 mol HCrO4− and ∼5 × 10−4 mol H2CrO4. These calculation results are consistent with the experimental results for the Cr(III) oxidation rate measurement, where oxidation to Cr(VI) was not observed under non-boiling conditions at 373, but was observed under reduced-pressure boiling at 373 K. Similarly, at 0.101 MPa ((a)), the abundance of HCrO4− was about 3 × 10−15 mol and H2CrO4 was about 2 × 10−13 mol at 363 K. On the other hand, at 0.050 MPa and 363 K ((c)), the abundance of Cr(VI) increased, with ∼4 × 10−7 mol HCrO4− and ∼3 × 10−5 mol H2CrO4. Therefore, these calculation results show that Cr(VI) is more likely to be generated under boiling conditions than non-boiling conditions from the viewpoint of equilibrium theory. Moreover, we consider that several hundred hours would be required for the Cr(VI) concentration to reach an equilibrium such as in , because the reaction does not attain equilibrium within 168 h, as shown by the measurements in .
3.4. Corrosion tests and Cr(VI) reduction rate measurements
We next examined the effects of temperature and boiling conditions on the periodic corrosion rate of R-SUS304ULC under each test condition. shows the periodic corrosion rate every 48 h under each test condition. The initial corrosion rates are large for the test conditions at 373 and 384 K, and the corrosion rates decrease rapidly with time regardless of the boiling or non-boiling conditions. However, the corrosion rate is maintained at ∼0.5 g m−2 h−1 regardless of the boiling or non-boiling conditions, even at 353 K. Motooka et al. [Citation17] also reported that the periodic corrosion rate of R-SUS304ULC decreased rapidly with time in 8 M boiling nitric acid solution at atmospheric pressure containing 20 mM Cr(VI). We considered that the effects of the boiling conditions on the corrosion rate are lower than those of the temperature.
Figure 7. Changes in the periodic corrosion rate of R-SUS304ULC in 8 M HNO3 solution with 10 mM Cr(VI).
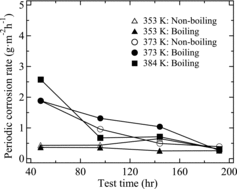
shows the scanning electron microscopy (SEM) image of the first-batch specimens (48 h) for each set of test conditions. Typical intergranular corrosion was observed under atmospheric-pressure boiling conditions at 384 K. Even under reduced-pressure boiling and non-boiling conditions at 373 K, intergranular corrosion was observed. Under reduced-pressure boiling and non-boiling conditions at 353 K, slight intergranular corrosion was observed.
We examined the variation of the Cr(VI) concentration over time in order to evaluate the relationship between the corrosion rate of R-SUS304ULC and the reduction rate of Cr(VI). shows a plot of the time variation of Cr(VI) concentration under each testing condition. In addition, we evaluated the influence of iron ions leached from the test specimen on the determination of Cr(VI) concentration as follows. From the Pourbaix diagram, iron ions are present as Fe(III) in nitric acid solution [Citation25]. Also, the molar absorbance coefficient of Fe(III) in 8 M nitric acid is 57.4 M−1 cm−1 (at 350 nm) by preliminary measurement. In this study, the maximum amount of material leached from the R-SUS304ULC until the end of the corrosion test was 0.233 g (reduced-pressure boiling at 373 K). Thus, we estimated that the maximum leaching of Fe(III) was about 0.17 g, based on the chemical composition in . In this case, the molarity of Fe(III) was about 7.1 mM in the test solution, and we considered that the influence on the measurement of the Cr(VI) concentration was less than 0.5 mM from the molar absorbance coefficient of Fe(III) and Cr(VI). Therefore, we ignored the influence of iron ions in this study because this concentration was less than 5% of the initial concentration of Cr(VI).
From , we confirmed that the Cr(VI) concentration decreased exponentially regardless of the boiling or non-boiling conditions. Therefore, we assumed the reduction of the Cr(VI) concentration to be a pseudo-first-order reaction and determined the corresponding rate constants for the various test conditions from the experimental results in . The reaction rate equation for Cr(VI) reduction is expressed as follows:
(16)
(16) where the variables are as previously defined. Next, we assume that k″ is the rate constant for the pseudo-first-order reduction of Cr(VI), including the back reaction, i.e., Cr(III) oxidation. Hence, we consider Equation (16) as follows:
(17)
(17)
The following equation was obtained by solving the differential equation,
(18)
(18) where [Cr(VI)]0 is the initial concentration of Cr(VI). shows the k″ values for the various test conditions calculated from the experimental results in and Equation (18). We see from and that the k″ values are one order of magnitude greater than the oxidation rate constant, k: under atmospheric-boiling conditions at 384 K, k″ was ∼10 times k; and under reduced-pressure boiling at 373 K, k″ was ∼70 times k (we consider that the actual rate constant of Cr(VI) reduction is larger than the k″ value because the k″ value is underestimated by the back reaction of Cr(III) oxidation and the effects of iron ions). Therefore, we find from these results that the rate of Cr(VI) reduction is faster than the rate of Cr(III) oxidation on the basis of kinetics.
Table 5. Rate constants of pseudo-first-order reduction of Cr(VI) in 8 M HNO3.
shows a plot of the periodic corrosion rate of R-SUS304ULC versus the Cr(VI) concentration as determined from the experimental data presented in and . indicates that the periodic corrosion rate of R-SUS304ULC and the extent of Cr(VI) concentration change are positively correlated regardless of the boiling or non-boiling conditions. shows the Arrhenius plot obtained from . We see from that the rate of Cr(VI) reduction follows Arrhenius’ law regardless of the boiling or non-boiling conditions. An activation energy of 73 kJ mol−1 was calculated from the plot. Matsuhashi et al. [Citation26] reported that the activation energy for the corrosion of Fe–Cr–Ni stainless steel was about 50 kJ mol−1 in 10.2 mol kg−1 H2SO4 solution. These findings reveal that the corrosion of R-SUS304ULC follows Arrhenius’ law, regardless of the boiling or non-boiling conditions.
3.5. Polarization measurements
In order to further evaluate the corrosion behavior of R-SUS304ULC for each test condition, we determined the corrosion potential from the polarization curve. shows the polarization curve for the various testing conditions, and shows the corrosion potentials (Ecorr). We see from and that the corrosion potential is shifted to the noble side as the temperature increases. In addition, the current density of the cathode increases as the temperature increases. On the other hand, there is no significant difference in the corrosion potential under the boiling and non-boiling conditions at the same temperature. Takeuchi et al. [Citation9] proposed a model for the transition mechanisms of the Ecorr due to activation of the cathode reaction shown in . Ecorr is shifted to the noble side (Ecorr(1) → Ecorr(2) → Ecorr(3)) when the cathode reaction is increased under certain conditions of the anode reaction (ired(1) → ired(2) → ired(3)), because Ecorr is determined by the balance of the dissolution reaction of the material side (anode reaction) and the reduction reaction of the environment (solution) side (cathode reaction). Therefore, we find that the corrosion potential of R-SUS304ULC depends on temperature regardless of the boiling or non-boiling conditions, which supports the results of the corrosion tests.
Table 6. Corrosion potential, Ecorr, of R-SUS304ULC.
Figure 13. Concept of the potential shift of Ecorr to the noble direction [Citation9].
![Figure 13. Concept of the potential shift of Ecorr to the noble direction [Citation9].](/cms/asset/c334fe83-4f88-473d-ab42-324cd33139de/tnst_a_962637_f0013_b.gif)
4. Conclusions
In this study, we evaluated the relationship between the corrosion of R-SUS304ULC steel and the redox behavior of chromium in nitric acid solution under three conditions: boiling at atmospheric pressure; boiling at reduced pressure; and non-boiling. By measuring the time dependence of the chromium concentration as well as performing electrochemical tests, thermodynamic calculations, and corrosion studies, the following conclusions may be drawn.
The oxidation of Cr(III) to Cr(VI) is closely related to the boiling phenomenon of the nitric acid solution. From the viewpoint of equilibrium theory, oxidation to Cr(VI) is more likely for the boiling state than the non-boiling state, even at the same temperature. This is related to the increase of potential by decrease in HNO2 concentration due to the formation of NOx gas in addition to the local over-concentration of nitric acid.
The apparent rate of Cr(VI) reduction, as consumed by corrosion, is more than 10 times greater than the rate of Cr(III) oxidation in 8 M nitric acid solution. This indicates that the rate of Cr(VI) reduction by corrosion is kinetically faster than the rate of Cr(III) oxidation in the bulk solution. In addition, the apparent rate of Cr(VI) reduction and the rate of R-SUS304ULC corrosion are positively correlated. Therefore, the corrosion of R-SUS304ULC apparently follows Arrhenius’ law in 8 M nitric acid solution containing Cr(VI), regardless of the boiling or non-boiling conditions.
References
- Maki A. [Corrosion circumstance in the Tokai reprocessing plant and evaluation of the corrosion rate]. JNC Tech Rev. 2002;14:39–63. Japanese.
- Hyakubu T, Inazumi T, Takagi Y, Masumura K. Corrosion resistance and long term durability of improved austenitic stainless steel for nuclear fuel reprocessing plants. In: Shoji T and Shibata T, editors. Proceedings of International Symposium on Plant Aging and Life Prediction of Corrodible Structures; 1995 May 15–18; Sapporo, Japan: NACE International; p. 847–852.
- Inazumi T, Hyakubu T, Takagi Y, Okimoto S, Ehira Y, Ohashi M. [Development of highly corrosion resistant R-SUS304ULC for nuclear fuel reprocessing plant]. NKK Tech Rev. 1993;144:20–25. Japanese.
- Wada F. [Improvement of reliability in nuclear fuel reprocessing plant]. Zairyo-to-Kankyo. 1999;48:771–775. Japanese.
- Okubo M, Shintani M, Ishimaru H, Tokunaga K, Nagayama M, Itoh A. Demonstration tests on corrosion resistance of equipment for spent-fuel reprocessing process. Proceedings of RECOD 87; 1987 Aug 23–27; Paris, France: SFEN; p. 1181–1188.
- McIntosh AB, Evans TE. The effect of metal species present in irradiated fuel elements on the corrosion of stainless steel in nitric acid. Proceedings of the 2nd International Conference on Peaceful Uses of Atomic Energy; 1958 Sep 1–13; Geneva, Switzerland: United Nations; p. 206–215.
- Hirose Y, Yusa H, Sasahira A, Masaoka I, Yoshida T, Furutani Y. Implication of ruthenium in the acidic liquid evaporation processes. Proceedings of RECOD 87; 1987 Aug 23–27; Paris, France: SFEN; p. 501–506.
- Arai Y, Sasahira A, Honda T. [Corrosion mechanism of stainless steel in nitric acid solutions containing ruthenium compounds]. Zairyo-to-Kankyo. 1999;48:235–241. Japanese.
- Takeuchi M, Takeda S, Nagai T, Koizumi T. [Effect of chemical species in spent nuclear fuel reprocessing solution on corrosion of austenitic stainless steel]. Trans At Energy Soc Jpn. 2005;5:32–44. Japanese.
- Motooka T, Kiuchi K. Effect of neptunium on corrosion of stainless steel in nitric acid solution. J Nucl Sci Technol Suppl. 2002;3:367–370.
- Armijo JS. Intergranular corrosion of nonsensitized austenitic stainless steels-I. Environmental variables. Corrosion. 1965;21:235–244.
- Kajimura H, Morikawa H, Nagano H. [Formation mechanism of Cr6+ ions and their accelerating effect on the corrosion of stainless steel in high temperature concentrated nitric acid]. Boshoku Gijyutsu. 1987;36:636–642. Japanese.
- Truman JE. Factors affecting the testing of stainless steels in boiling concentrated nitric acid. J Appl Chem. 1954;4:273–283.
- Maness RF. Effects of Cr(VI) and Fe(III) on PUREX plant corrosion. Richland (WA): Company Report, Hanford Atomic Products Operation; 1962. (Report no. HW-72076).
- Armstrong RD, Cleland GE, Whillock GO. Effect of dissolved chromium species on the corrosion of stainless steel in nitric acid. J Appl Chem. 1998;28:1205–1211.
- Mimura H, Akiba K, Igarashi H. Removal of heat-generating nuclides from high-level liquid wastes through mixed zeolite columns. J Nucl Sci Technol. 1993;30:239–247.
- Motooka T, Kato C, Yamamoto M. [Effect of re-oxidation rate of chromium and vanadium ions on corrosion rate of stainless steel in boiling nitric acid solutions]. Zairyo-to-Kankyo. 2010;59:19–24. Japanese.
- Pourbaix M. Atlas of electrochemical equilibria in aqueous solutions. 2nd ed. Houston (TX): National Association of Corrosion Engineers; 1974. p. 493–503.
- Pourbaix M. Atlas of electrochemical equilibria in aqueous solutions. 2nd ed. Houston (TX): National Association of Corrosion Engineers; 1974. p. 256–271.
- Electric Power Research Institute. Computer-calculated potential pH diagrams to 300 °C. Vol. 2; 1983.
- Eriksson G. Thermodynamic studies of high temperature equilibria III. SOLGAS, a computer program for calculating the composition and heat condition of an equilibrium mixture. Acta Chem Scand. 1971;25:2651–2658.
- Besmann TM. SOLGASMIX-PV, a computer program to calculate equilibrium relationships in complex chemical systems. TN (USA): Oak Ridge National Laboratory; 1977. (no. TM-5775).
- Kato C, Kiuchi K, Sugimoto K. [Thermodynamic study on redox reactions of boiling nitric acid solutions]. Zairyo-to-Kankyo. 2003;52:44–52. Japanese.
- Benedict M, Pigford TH, Levi HW. Nuclear chemical engineering. 2nd ed. NY (USA): McGraw-Hill; 1981. Chapter 10, Fuel reprocessing; p. 457–564.
- Pourbaix M. Atlas of electrochemical equilibria in aqueous solutions. 2nd ed. Houston (TX): National Association of Corrosion Engineers; 1974. p. 307–321.
- Matsuhashi R, Ito S, Sato E. [Relationship between the apparent activation energy of corrosion reaction and alloy contents of stainless steels]. Zairyo-to-Kankyo. 1993;42:521–528. Japanese.