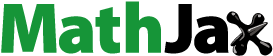
ABSTRACT
In this study, the oxidation of various accident tolerant fuel candidates produced under different conditions have been evaluated and compared relative to the reference standard – UO2. The candidates considered in this study were UN, U3Si2, U3Si5, and a composite material composed of UN–U3Si2. With the spark plasma sintering (SPS) method, it was possible to fabricate samples of UN with varying porosity, as well as a high-density composite of UN–U3Si2 (10%). Using thermogravimetry in air, the oxidation behaviors of each material and the various microstructures of UN were assessed. These results reveal that it is possible to fabricate UN to very high densities using the SPS method, such that its resistance to oxidation can be improved compared to U3Si5 and UO2, and compete favorably with the principal ATF candidates, U3Si2, which shows a particularly violent reaction under the conditions of this study, and the UN–U3Si2 (10%) composite.
1. Introduction
Following the Fukushima Nuclear Accidents of 2011, an intense campaign was begun in the USA, whose main objective was to find a fuel and cladding combination which would offer improved tolerance of severe accident conditions that were experienced in Japan. In particular, there has been great interest in exploring innovative fuel concepts which can be used in conjunction with non-zirconium-based cladding. Several leading candidates being explored are UN, U3Si2, and U3Si5, and composites between UN and the silicides, all of which offer considerably improved thermal conductivity to the reference UO2 fuels used today [Citation1]. In addition, UN and U3Si2 have been given special attention due to their higher heavy metal densities, an important factor in improving fuel economy. However, the principal objective of any accident tolerant fuel is to improve safety, and in this respect, high-temperature interactions between fuel and coolant – or in the case of water cooled reactors, the fuel and steam – are of great importance.
The poor resistance of uranium nitride to oxidation in air and steam is quite well known and has been documented repeatedly in the literature [Citation2,Citation3]. Indeed, it is this inherent pyrophoricity and intolerance to water attack which has largely been responsible for limiting the adoption of this fuel as a candidate for lightweight reactor (LWR) applications. In addition, the notable resistance of this material to conventional sintering has also proven prohibitive in obtaining samples of useful densities, i.e. greater than 90% of theoretical; 95% density, for example, has been found to require temperatures in excess of 2300 °C [Citation4–6], which is known to be both costly and difficult [Citation7]. Various proposals have been put forth to decrease the costs associated with this, perhaps most notably the use of a second phase with a lower melting point and making use of so-called ‘liquid phase sintering,’[Citation8] which has succeeded in reaching 90% at 1700 °C, which otherwise required over 1900 °C for UN alone [Citation9]. On the other hand, recent studies into the sintering behavior of UN using the spark plasma sintering (SPS) method have demonstrated a reproducible technique for obtaining sintered UN pellets to relative densities exceeding 90%, and even up to 99.9% at 1650 °C or less, which marks a dramatic reduction in temperature when compared to the conventional and liquid-phase sintering techniques [Citation10,Citation11].
The alloys of the silicides have received recent consideration due to a perceived increased oxidation resistance compared to nitrides, as well as their ability to aid in the sintering of UN using conventional means. Pilot studies conducted at LANL have indicated a performance on par with those of the nitride [Citation12]. In that study, the use of thermogravimetry allowed for in situ monitoring of the oxidation reaction, albeit under conditions not representative of an LWR environment. The use of autoclave testing, on the other hand, has permitted the reproduction of reactor-type environments, but has produced somewhat ambiguous results due to an inability to quantify the progress of the reaction and define a specific reaction onset temperature [Citation13]. The objective of this study, therefore, was to use the thermogravimetric method on a variety of ATF materials and microstructural characteristics in order to better understand the material parameters which govern the oxidation reaction.
2. Experimental
2.1. Oxidation reactions
In any high-temperature, high-oxygen environment, all of the previously mentioned fuels will oxidize. In an LWR, this oxidation would be driven by interactions between fuel and water, in which case the chemical equations proposed for this oxidation can be given as follows:
(1)
(1)
(2)
(2)
(3)
(3)
(4)
(4)
In each case, a reduction in density is observed between the initial phase, and U3O8, the presumed final product for each reaction, and this reduction results in the conversion of the initially solid fuel material into finer particulates, along with the production of hydrogen gas. However, the use of thermogravimetry in high-temperature steam environments presents some challenges and requires specialized equipment, and therefore, air was chosen as the oxidizing atmosphere in order to establish a preliminary basis of comparison. In an air environment, oxidation occurs solely by reaction with O2 gas, while the product of oxidation remains U3O8.
2.2. Material characteristics
In , some relevant material characteristics are presented. For each material, its beginning of life (BoL) thermal conductivity is listed, as well as melting point. Using this data, and assuming the adaptation of each fuel into an existing and otherwise unchanged power reactor concept, relevant accident tolerant parameters can be approximated; in this case, the fuel centerline temperature and margin to melt. In addition, the expected mass increase of each material assuming the preceding reactions is also listed. Centerline fuel temperatures were calculated using Equation (Equation5(5)
(5) )[Citation14], and reference LWR parameters were used for fuel radius, peak fuel surface temperature, and peak linear power, namely 4.45 mm, 1070 K and 45
:
(5)
(5)
Table 1. Various properties of ATF fuels.
2.3. Sample preparation and characterization
UN powder was synthesized using the hydriding–nitriding method using raw metal as the source material. Following synthesis, this UN was sintered using SPS in such a way so as to provide varying amounts of material porosity, as has been described previously [Citation11]. Additionally, samples of U3Si2, and U3Si5 were prepared using arc-melting and evaluated for homogeneity and microstructure using XRD, LOM, and SEM. These evaluations revealed a high degree of homogenization within the material, while XRD () detected U3Si2 and U3Si5 as the only phases in their respective samples. Representative SEM micrographs can be seen in and were used to estimate a phase purity of 98.3% and 97.3% U3Si2 and U3Si5, respectively, when evaluated using ImageJ [Citation15]. It is regarded that the secondary phases (seen in LOM) are sufficiently diffuse so as to escape detection by XRD. An composite was fabricated by milling of U3Si2, mixing with UN powder, and sintering via SPS, as described previously [Citation1]. In each case, samples were weighed and measured for porosity. For UN, this porosity varied between <1% and up to 9% of the total volume, while for the silicides – as they were produced in an as-cast condition via arc melting – porosity was <1%. Pellets of UO2 were obtained (courtesy of Westinghouse), and were measured to contain 4% porosity. For each sample, the distribution of open and closed porosity was also determined using a method described previously [Citation11].
For each sample, optical microscopy was also performed in order to assess the grain size of the material, which was performed according to ASTM E112 [Citation21]. For the UN prepared by SPS; this grain size varied between 6 and 8.3 μm, while for UO2, the grain size was 16.3 μ m. The silicides, prepared by arc-melting revealed a large and irregular grain size, in excess of 80 μm. The composite contained slightly larger grains than those ordinarily observed in UN, and were measured to be 9.1 μm.
Each sample was cracked by the application of mechanical pressure, and fragments of nearly cubic shape were collected and lightly ground down to a mass of 10–20 mg and placed in a platinum boat belonging to a PerkinElmer Model TGS-2 System4 TGA. The use of larger fragments of material – as opposed to powder – had the advantage of preserving the microstructural characteristics of the material and permitted the assessment of their influence on oxidation. A cover made of Macor was placed over the sample to prevent the loss of any powders, produced during oxidation, from the measuring tray while also permitting the free exchange of atmosphere. The samples were then heated up to 800 °C using a 5 °C/min heating rate in air, resulting in an oxidation of the material and an increase in its total mass. The low mass of sample required for each test permitted multiple runs for each sample, which showed a high degree of reproducibility. In this paper, only one oxidation curve is shown for each sample.
For each material, an onset temperature was defined as the temperature at which 5% of the total mass change of the reaction was observed, while the maximum rate temperature was obtained by analysis of the first derivative of the reaction. This was performed in order to adopt a consistent basis of comparison between each sample, which at times demonstrated widely varying behaviors.
Fragments of the material were also collected for oxygen and nitrogen measurement using a LECO TC436DR, and the powder residues produced during the oxidation reaction were themselves collected and analyzed, such that the oxidation extent could be assessed using both the change in mass as well as direct oxygen measurement. For samples of UN and for the composite, oxygen and carbon was found to be 800 and 500 ppm, respectively, while for U3Si2 and U3Si5, these were determined to be 600 and 500 ppm, respectively. The UO2, provided by Westinghouse, was found to have 11.9% oxygen, consistent with stoichiometric UO2.0.
3. Results and discussion
3.1. Oxidation of ATF candidates and UO2
Initial studies focused on comparing the differences in reaction rate for the various ATF candidates compared to the reference UO2, which can be seen in . At the same time, a quantitative analysis of each oxidation featuring the reaction rate of each oxidation reaction can be seen in . Relevant material properties and indices are presented for each sample in .
In the case of UO2, the onset of reaction occurred at 405 °C (see (A)), while a maximum rate of 10% per minute was observed at 440 °C. The conversion of UO2 to U3O8, as noted by McEachern, nominally causes a 3.95% mass increase and causes the formation of a fine powder residue [Citation22]. In the case of UN of low density and high open porosity, UN:0 (see (B)), the onset of reaction occurred at 320 °C, while the maximum was observed at 360 °C. The reaction itself was extremely rapid, reaching a peak consumption rate of nearly 50% per minute before reaching completion. A slow, steady mass decrease can be observed which has been interpreted as the release of nitrogen from a UNxOy intermediate product, consistent with the observations of Dell [Citation3]. A final mass increase of 11.4% was observed, suggesting the formation of U3O8, confirmed by elemental analysis of the final product which showed 15.1% ± 0.2} oxygen, and consistent with earlier work by Wheeler [Citation23].
In the case of U3Si2 (see (C)), the onset of reaction occurred at 470 °C, while the maximum rate was observed at 478 °C. The reaction was extremely rapid, reaching nearly 80% per minute consumption of the material. Unlike UN, however, the onset of the reaction occurred at very high temperatures, even greater than those required for the oxidation of UO2. For this reaction, a mass increase of 19.9% was observed. For U3Si5 (see (D)), the onset of reaction occurred at a rather low temperature of 325 °C, while the maximum rate was observed rather late in the oxidation at 600 °C. This would seem to suggest a rather different oxidation reaction for this material versus U3Si2. Moreover, the observed increase in mass was 20% and 24% for U3Si2 and U3Si5, respectively, consistent with the reactions proposed in Equations (Equation3(3)
(3) ) and (Equation4
(4)
(4) ), suggesting the formation of U3O8 and SiO [Citation24]. It bears noting that, given similar reactions in steam, this measured mass increase would entail a 6x, 5x, and 1.8x increase in H2 production for U3Si5, U3Si2, and UN, respectively, when compared to UO2, which will have important ramifications for the accident tolerance of these materials.
These results offer a high degree of congruity with similar studies which have been conducted on these fuel candidates [Citation12]. Of the ATF candidates, only U3Si2 appears to offer any improvement in oxidation compared to reference UO2 fuel, while the behaviors of highly porous UN:0 and U3Si5 are considerably worse. Given the ability of previous authors to study the behavior of UN prepared in this condition only, the interest in U3Si2, here assessed to oxidize at significantly higher temperatures than low-density UN samples, becomes clear.
3.2. Microstructure and oxidation of UN
Of high interest in this study, however, is the profound effect of porosity on the oxidation kinetics of UN. While an onset temperature of 320 °C was observed in UN of low density and open porosity (UN:0), identical to the behavior observed by Nelson, it has been shown that by decreasing porosity, in particular by eliminating open porosity within the material, the onset and rate of oxidation for UN can be delayed considerably. Indeed simply by eliminating open porosity from the material, the rate of oxidation can be decreased by an order of magnitude, consistent with oxygen diffusing more rapidly along grain boundaries and vacancies than the bulk [Citation12,Citation25]. (B) shows the effect of pore closure on the oxidation reaction of UN, while a description of the microstructural characteristics of each material can be found in .
Table 2. Oxidation reactions for ATF fuels.
In the case of 0.2%, fully closed porosity (UN:3) the oxidation resistance of the UN has been observed to actually be superior even to UO2 under the test conditions of this study. This is invariably due to the higher porosity in the UO2 pellet, and it is certainly worth noting that it is highly unlikely that UN of this density could be employed in any LWR concept due to the issues of swelling which would emerge during irradiation. Nevertheless, it demonstrates the importance of controlling for microstructural characteristics when performing experiments of this type, and illustrates the remarkable potential for improvement in UN performance obtained by adjusting these characteristics.
Given the very high densities of the arc-melted silicide alloys used in this study, it may be of interest to perform future studies on samples prepared by a powder metallurgical route, rather than in the as-cast condition, such that the microstructure of the material will be characteristic of the material in its intended reactor form.
Here theoretical density has been calculated to include the effect of separate phases of UO2 based upon the concentrations measured by elemental analysis, causing a slight depression from the literature values of UN and U3Si2, and a slight increase for U3Si5.
3.3. Evaluation of the 
composite
The behavior of the UN–U3Si2 composite, shown in , seems to offer some combination of behaviors between UN and U3Si2. The material generally follows the onset of reaction observed for UN:3, the best performing UN candidate, though with a slightly delayed onset of reaction and maximum rate, understandable given their highly similar material characteristics according to and as can be seen from the etched micrographs provided in . Despite this, the reaction itself seems to exhibit some of the rapid kinetics observed with pure U3Si2, as the reaction accelerates and reaches completion at the same point as the generally more poorly performing UN:2. In addition, the overall mass increase was 12.4%, in line with expectations.
4. Conclusions
In assessing the accident tolerance of potential nuclear fuels, there are a number of factors which must be taken into consideration. By increasing the thermal conductivity of the fuel, significant reductions can be made in the centerline fuel temperature and the overall ability of the fuel to withstand severe accident scenarios can be improved. At the same time, any new fuel must demonstrate an ability to avoid severe reactions with the coolant during normal operation and accident conditions.
While the vastly higher thermal conductivities of U3Si2 and U3Si5 offer improved thermomechanical performance compared to the reference UO2, the lower melting temperatures actually result in a nearly identical margin to fuel melt and a potentially greatly increased production of H2, 5x and 6x, respectively, during oxidation, neither of which bode well for the accident tolerance of these materials. UN, on the other hand, boasts a high thermal conductivity while retaining a high melting temperature, resulting in a margin to fuel melt over twice that of UO2. This is offset somewhat by an increased production of H2 gas during oxidation.
In this study, the oxidation behavior of several ATF candidates was investigated and compared to reference oxide fuel. By removing porosity from UN and sintering the material to a density useful for thermal reactor purposes, and by eliminating open porosity from the material, it has been possible to improve its oxidation resistance in air to a level greater than that even for reactor quality UO2 pellets, as evaluated by thermogravimetry. Furthermore, this study has shown that the oxidation resistance of uranium silicide can only offer marginal improvements compared to UN and, due to the very rapid nature of the oxidation, would likely suffer very violent reactions at moderate temperatures. The performance of the UN–U3Si2 composite, while it may offer advantages in improving the sinterability of UN, does not seem to offer significant improvements to this behavior when compared to UN, which casts some doubt on its perceived role in improving fuel performance.
It bears mentioning that these studies, at best, describe only the behavior of these materials as they would exist in beginning of life conditions. The effect of irradiation on these materials would induce deformation and possibly cracking, depending on the material, which would significantly degrade their performance. Moreover, the difference caused by high pressure and steam may not be immediately inferable. Indeed, numerous studies have been performed on the reactions between UO2 and steam which show a strong dependence on environment chemistry and steam concentration, as well as burn-up [Citation26,Citation27]. It is therefore suggested that future studies should focus on the impact of such environmental factors on oxidation. Nevertheless, the results of this study would seem to indicate that improvements in the fabrication process and the optimization of material microstructure in UN fuel can greatly improve its oxidation resistance, and that this resistance, coupled with its high thermal conductivity and high melting point, makes UN a promising accident tolerant fuel candidate.
Acknowledgements
The preceding work has been conducted within the framework of the ASGARD project under the European Atomic Energy Community’s 7th Framework Programme. The authors also wish to acknowledge the cooperation of the Materials and Environmental Chemistry Department at Stockholm University, as well as Westinghouse Electric Corporation for providing reference UO2 materials.
Disclosure statement
No potential conflict of interest was reported by the authors.
Additional information
Funding
References
- Johnson KD, Raftery A, Lopes D. Fabrication and microstructural analysis of UN-U3Si2 Composites for accident tolerant fuel applications. J Nucl Mater. 2016;477:18–23
- Streit M, Ingold F. Nitrides as a nuclear fuel option. J Eur Ceramic Soc. 2005;25(12):2687–2692.
- Dell RM, Wheeler VJ, McIver EJ. Oxidation of uranium mononitride and uranium monocarbide. Trans Faraday Soc. 1966;62:3591–3606.
- Metroka RR. Fabrication of uranium mononitride compacts. Washington (DC): NASA; July 1970. (NASA Technical Note TN-5876).
- Arai Y, Fukushima S, Shiozawa K, et al. Fabrication of (U,Pu)N fuel pellets. J Nucl Mater. 1989;168:280–289.
- Matthews RB, Chidester KM, Hoth CW, et al. Fabrication and testing of uranium nitride fuel for space power reactors. J Nucl Mater. 1988;151:334–344
- German RM. Sintering: from empirical observations to scientific principles. Oxford: Butterworth-Heinemann, 2014. Print.
- Lessing P. Oxidation protection of uranium nitride fuel using liquid phase sintering. Idaho Falls, ID: Idaho National Laboratory; March 2012. (INL/EXT-12-24974).
- Ortega LH, Blamer BJ, Evans JA, et al. Development of an accident-tolerant fuel composite from uranium mononitride (UN) and uranium sesquisilicide (U3Si2) with increased uranium loading. J Nucl Mater. 2016;471:116–121.
- Muta H, Kurosaki K, Uno M. Thermal and mechanical properties of uranium nitride prepared by SPS technique. J Mater Sci. 2008;43(19):6429–6434.
- Johnson KD, Wallenius J, Jolkkonen M, et al. Spark plasma sintering and porosity studies of uranium nitride. J Nucl Mater. 2016;473:13–17.
- Nelson AT, White JT, Byler DD, et al. Overview of properties and performance of uranium-silicide compounts for light water applications. Trans Amer Nucl Soc. 2014;110:987–989.
- Malkki P. The manufacturing of uranium nitride for possible use in light water reactors [Licentiate Thesis]. Stockholm: Department of Reactor Physics, KTH; 2014.
- Duderstadt JJ, Hamilton LJ. Nuclear reactor analysis. John Wiley and Sons; 1976.
- Schneider CA, Rasband WS, Eliceiri KW. NIH image to ImageJ: 25 years of image analysis. Nat Methods. 2012;9(7):671–675.
- Wallenius P. Transmutation of nuclear waste. Stockholm, Sweden: LeadCold Reactors, 2011. Print.
- White JT, Nelson AT, Byler DD, et al. Thermophysical properties of U3Si2 to 1773 K. J Nucl Mater. 2015;464:275–280.
- White JT, Nelson AT, Byler DD, et al. Thermophysical properties of U3Si5 to 1773 K. J Nucl Mater. 2015;456:442–448.
- Yemel’yanov VS, Yevstyukhin AI, Dunworth JV. The metallurgy of nuclear fuel. Oxford: Pergamon Press; 1969. Print.
- Carvajal Nunez U, Prieur D, et al. Melting point determination of uranium nitride and uranium plutonium nitride: a laser heating study. J Nucl Mater. 2014;449:1–8.
- ASTM E112-96. Standard test methods for determining average grain size. West Conshohocken, PA: ASM International; 2004.
- McEachern RJ, Taylor P. A review of the oxidation of uranium dioxide at temperatures below 400 °C. J Nucl Mater. 1998;254:87–121.
- Wheeler VJ, Dell RM, Wait E. Uranium trioxide and the UO3 hydrates. J Inorganic Nucl Chem. 1964;26:1829–1845.
- Solomon AA, Revankar S, McCoy JK. Enhanced thermal conductivity oxide fuels, D.o.E. Technical Report: DOE/SF/22613, TRN: US0702439, Jan 2006.
- Smallman RE, Ngan AHW. Modern physical metallurgy. Kent: Elsevier Science; 2013.
- Abrefah J, de Aguiar Braid A, Wang W, et al. High temperature oxidation of UO2 in steam-hydrogen mixtures. J Nucl Mater. 1994;208:98–110.
- Imamura M, Une K. High temperature steam oxidation of UO2 fuel pellets. J Nucl Mater. 1997;247:131–137.