Abstract
In this study, thermoelectric generator (TEG) adaptation in a condensing combi boiler was investigated. The first part of the study comprises experimental analysis, performance tests of a commercially available TEG, and efficiency tests of a condensing combi boiler without TEG adaptation. In the second part of the study, a numerical analysis was carried out to determine the locations of TEGs inside the heat cell. According to the results of the performance tests, approximately 16 V open circuit voltage was generated under 201°C temperature difference. The electrical efficiency of the tested TEG is calculated to be 4.5%. Natural gas was used as fuel in the efficiency tests of the condensing combi boiler and the thermal efficiency was calculated to be 92.3% for 40–60°C water supply and return temperatures. Numerical study showed that the highest temperature difference could be obtained at the upper side of the heat cell with a value of 270°C. The hot side of the TEG module was heated from the inner surface of the heat cell via conduction through the wall, and the water channel was used as the heat sink. Therefore, TEGs were located inside the water channel of the heat cell, with a modification process on the heat cell itself. The performance tests and numerical results show that it is possible to integrate TEGs into the heat cell and decrease the electricity consumption or use combi boilers without an electricity network connection with a properly designed TEG integrated heat cell.
NOMENCLATURE
cp | = | specific heat, J kg−1 K−1 |
Dh | = | hydraulic diameter, mm |
Gk | = | generation of turbulent kinetic energy |
Gω | = | ω generation |
h | = | local heat transfer coefficient, W m−2 K−1 |
k | = | turbulent kinetic energy |
k | = | heat conduction coefficient, W m−1 K−1 |
Nu | = | Nusselt number, dimensionless |
P | = | pressure, Pa |
Re | = | Reynolds number, dimensionless |
= | turbulent Reynolds number, dimensionless | |
T | = | temperature, °C |
u, v, w | = | velocity components, m s−1 |
= | mean velocity components, m s−1 | |
u′, v′, w′ | = | fluctuation velocity components, m s−1 |
Yk | = | dissipation of k due to turbulence |
Yω | = | dissipation of ω due to turbulence |
Greek Symbols
α* | = | damping function |
μ | = | dynamic viscosity, kg m−1 s−1 |
μt | = | eddy viscosity, dimensionless |
ν | = | kinematic viscosity, m2 s−1 |
ρ | = | density, kg.m−3 |
σk | = | turbulent Prandtl number for k, dimensionless |
σω | = | turbulent Prandtl number for ω, dimensionless |
ω | = | dissipation rate |
Additional information
Notes on contributors
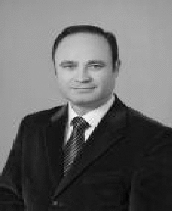
Senol Baskaya
Senol Baskaya obtained his B.Sc. in mechanical engineering from Gazi University, Turkey, in 1988. He became a research assistant in the same department in 1989 and completed his M.Sc. thesis in 1991. He earned his Ph.D. degree in 1996 from the University of Strathclyde, England. He became an assistant professor at Gazi University in 1997 and was appointed as an associate professor in 1999. He became a full professor in 2005. Some of his areas of research interest are electronics cooling, combustion technologies and systems, ventilation by convection, fluid jets, application of numerical methods to energy systems, and heat and mass transfer, as well as problems of fluid mechanics, and similar numerical and experimental research areas.
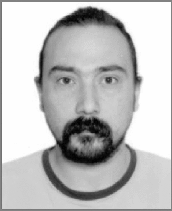
Salih Karaaslan
Salih Karaaslan obtained his B.Sc. in mechanical engineering from Gazi University, Turkey, in 2003. He became a research assistant in the same department in 2004 and completed his M.Sc. thesis in 2008. He is a Ph.D. student at the same department. Some of his areas of research interest are internal combustion engines, fire in tunnels, fire control and ventilation, experimental and numerical fluid dynamics, and conventional energy systems.
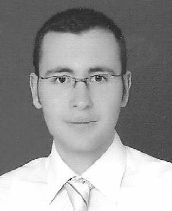
Tamer Calisir
Tamer Calisir obtained his B.Sc. in mechanical engineering from Kirikkale University, Turkey, in 2008. He became a research assistant at Gazi University in 2011 and completed his M.Sc. thesis also in 2011. He is a Ph.D. student at the same department. Some of his areas of research interest are electronics cooling, fluid jets, application of numerical methods to heat and mass transfer, and problems of fluid mechanics, and similar numerical and experimental research areas.
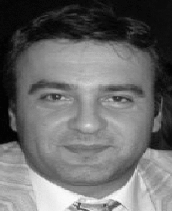
M. Zeki Yilmazoglu
M. Zeki Yilmazoglu obtained his B.Sc. in mechanical engineering from Karadeniz Technical University, Turkey, in 2002. He became a research assistant at Gazi University in 2006 and completed his M.Sc. thesis in 2006. He earned his Ph.D. degree in 2012 from Gazi University, Turkey. Some of his areas of research interest are clean coal technologies, energy efficiency, advanced power plant technologies, and integrated gasification combined cycles (IGCCs).
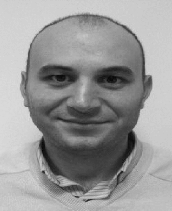
Turgut O. Yilmaz
Turgut O. Yilmaz obtained his B.Sc. in mechanical engineering and physics from Koc University, Turkey, in 2006. He earned his M.Sc. and Ph.D. degrees from Lehigh University, USA, in 2009 and 2011, respectively. He is currently working as a product development engineer at Bosch Thermotechnic R&D in Manisa, Turkey. Some of his areas of research interest are experimental and computational fluid mechanics, aerodynamics, heat transfer, gas dynamics, thermodynamics, and physics.