Abstract
Wire matrix inserts are used in different applications of tubular heat exchangers to improve tube side heat transfer. They have also been used to suppress fouling in crude oil refining services. In this paper it is investigated whether the changed hydrodynamic and thermal conditions when applying wire matrix inserts have an impact on crystallization fouling compared to the plain tube. With a turbulent flow, at Reynolds number of 9877 and an inlet temperature of 42°C, fouling tests with an aqueous calcium sulfate solution for two wire matrix inserts with a different packing density were carried out and compared with a plain tube. Integral and local measurements of the fouling were performed. The experiments were realized in a double-pipe heat exchanger with a pipe length of 2000 mm. The integral fouling resistances between the inserts and the plain tube showed no significant difference, whereas major differences of the local fouling resistances were observed. Compared to the plain tube, the inserts showed an increased heat transfer up to a maximum of 35% but also a significantly increased pressure drop. Fouling on the inserts themselves, which was observed optically, is the possible explanation for this behavior.
NOMENCLATURE
A | = | heat transfer area, m2 |
cF | = | bulk phase concentration, mol/L |
cP | = | heat capacity, J/(kg-K) |
d | = | diameter, m |
L | = | length, m |
LMDT | = | logarithmic mean temperature difference, K |
= | mass flow rate, kg/s | |
= | heat flow, W | |
= | heat flow density, W/m2 | |
Pr | = | Prandtl number cpμ/λ, dimensionless |
Re | = | Reynolds number based on the hydraulic diameter udh/μ, dimensionless |
Rf | = | fouling resistance, (m2-K)/W |
Rov | = | overall thermal resistance, (m2-K)/W |
s | = | wall thickness, m |
t | = | time, s |
T | = | temperature, K |
u | = | flow velocity, m/s |
U | = | overall heat transfer coefficient, W/(m2-K) |
x | = | local position, m |
Greek Symbols
α | = | heat transfer coefficient, W/(m2-K) |
λ | = | thermal conductivity of the liquid, W/(m-K) |
λw | = | thermal conductivity of the tube wall, 15 W/(m-K) |
μ | = | dynamic viscosity, Pa-s |
Subscripts
0 | = | without fouling |
f | = | fouling |
h | = | hydraulic |
i | = | inlet |
int | = | integral |
n | = | segment number |
m | = | measurement point |
o | = | outlet |
out | = | outside |
ss | = | shell side |
ts | = | tube side |
w | = | wall |
x | = | axial position |
Additional information
Notes on contributors
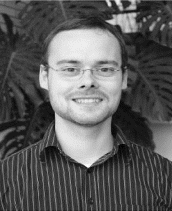
Robert Goedecke
Robert Goedecke is Ph.D. student at the Institute for Chemical and Thermal Process Engineering, Technische Universität Braunschweig, Germany. In 2010 he received his Dipl.-Ing. from Technische Universität Braunschweig. He worked on structural influences of crystallization fouling on heat transfer, and currently he is working on the experimental investigation of heat transfer and fluid dynamics in a pillow plate thermosiphon reboiler.
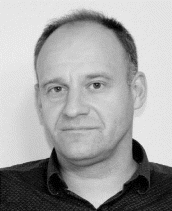
Peter Drögemüller
Peter Drögemüller works as research and development manager for Cal Gavin Ltd in the United Kingdom. His main research area is enhanced heat transfer in single- and two-phase flow applications. This includes research into suppression of fouling using tube-side enhancement technology. He is also responsible for software development, providing engineers with the opportunity to incorporate high-performance tube-side enhancement to the design of various types of tubular heat exchangers.
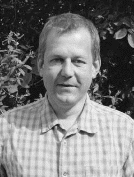
Wolfgang Augustin
Wolfgang Augustin is a senior researcher at the Institute for Chemical and Thermal Process Engineering, Technische Universität Braunschweig, Germany. He received his Dr.-Ing. in 1992 from Technische Universität Braunschweig. His main research interests are heat and mass transfer, fouling, viscous fluid flow, and surface interactions on the microscale level.
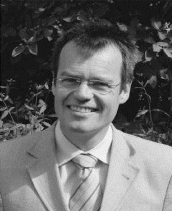
Stephan Scholl
Stephan Scholl is a professor of chemical and thermal process engineering at the Technische Universität Braunschweig, Germany. He received his doctorate degree in 1991 from the Technical University of Munich. After 11 years with BASF AG, Ludwigshafen, Germany, he joined Technische Universität Braunschweig in 2002. His main research areas are heat and mass transfer with an emphasis on fouling and viscous systems, separation processes in biotechnological applications, and process intensification.