Abstract
An experimental investigation has been conducted to investigate the film cooling performance of the louver scheme over the surface of a gas turbine stator using a transient thermochromic liquid crystal technique. A two-dimensional airfoil cascade has been employed during the study. The exit Reynolds number based on the true chord length is 1.5E5 and the exit Mach number is 0.23. Two rows of an axially oriented louver scheme are distributed on both suction and pressure sides in a staggered arrangement. The effect of hole location on the cooling performance is investigated for each row individually; then row interaction is investigated at four different blowing ratios ranging from 1 to 2 and a 0.9 density ratio. The detailed local performance distribution and the lateral-averaged normalized performance are presented over both sides of the vane in terms of heat transfer coefficient and cooling effectiveness. The louver scheme provides a better cooling performance compared with the similar cylindrical scheme of the same base diameter at the same cooling amount. The blowing ratio does not influence significantly the performance for the louver scheme due to the considerable decrease in the jet momentum that impedes the jet lift-off at exit. The location of the scheme exit has a high impact on the cooling performance as it affects the development of the boundary layer. The double injection on the pressure side provides a superior effectiveness due to the blockage of the mainstream by the coolant injected from the first row. The louver scheme provides higher net heat flux reduction, which suits the cooling capacity needed for the next generation of gas turbines.
ACKNOWLEDGMENT
This research could not be conducted without the support and advice of the cooling research and development department of Pratt and Whitney Canada.
NOMENCLATURE
Br | = | blowing ratio [(ρv)j/(ρv)m] |
Cρ | = | specific heat capacity, J kg−1 K−1 |
Cx | = | axial chord, cm |
d | = | hole diameter, m |
HTC | = | heat transfer coefficient, W m−2 K−1 |
h | = | heat transfer coefficient with film cooling, W m−2 K−1 |
ho | = | heat transfer coefficient without film cooling, W m−2 K−1 |
k | = | thermal conductivity, W m−1 K−1 |
l | = | hole length, m |
L | = | actual chord, cm |
NHFR | = | net heat flux reduction |
P | = | pressure, bar |
p | = | pitch (distance between two holes), m |
PIV | = | particle image velocimetry |
PSP | = | pressure-sensitive paint |
q | = | heat load, W |
qh | = | DC electric power input, W |
Re | = | Reynolds number, ρvL/μ |
RGB | = | red, green, and blue |
ROI | = | region of interest |
SLA | = | stereolithography (technique of building the model vane) |
s | = | surface distance, m |
TLC | = | thermochromic liquid crystal |
TSP | = | temperature-sensitive paint |
T | = | temperature, K |
Ti | = | initial temperature of the surface, K |
t | = | time, s |
v | = | velocity, m s−1 |
x | = | distance downstream the hole exit, m |
Greek Symbols
α | = | thermal diffusivity, m2 s−1 |
ϵ | = | least square error |
φ | = | overall cooling effectiveness |
η | = | film cooling effectiveness |
μ | = | viscosity, Pa-s |
θ | = | inverse of overall cooling effectiveness |
ρ | = | density, kg m−3 |
τ | = | color change time, s |
Subscripts
c | = | coolant |
elec | = | electric |
f | = | film |
j | = | jet |
loss | = | losses |
m | = | main flow |
o | = | total |
p | = | pressure side |
s | = | suction side |
w | = | wall (surface) |
Additional information
Notes on contributors
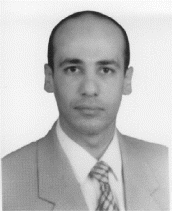
Tarek Elnady
Tarek Elnady received his Ph.D. degree from the Mechanical and Industrial Engineering Department at Concordia University in 2010. Since then he has been a staff in Military Technical College, Cairo, Egypt. He received his master's degree in 2003 and bachelor's degree in 1996 from Military Technical College. His main interests are cooling in gas turbines, and renewable energy resources.
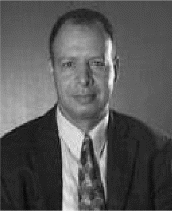
Ibrahim Hassan
Ibrahim Hassan is a professor of mechanical engineering at Texas A&M University at Qatar. His research interests include heat transfer, micro fluids, thermal MEMS, multiphase flow, and CFD applications. The research conducted by him at present includes state-of-the-art solutions to applications found in industries such as aerospace, nuclear power, and solar energy. He has published more than 200 articles in refereed journals, conference proceedings, and book chapters. He recently received the prestigious NSERC (National Science and Research Council of Canada) Discovery Accelerator Supplement (DAS) Award in 2010.
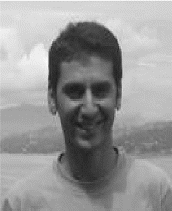
Lyes Kadem
Lyes Kadem is an associate professor in the Department of Mechanical and Industrial Engineering at Concordia University. He received his bachelor's degree in mechanical engineering from USTHB (Algeria) in 1998, his M.Sc. in biomechanics from ESM2 (France) in 2000, and his Ph.D. in biomechanics from ESM2 (France), as well as a Ph.D. in experimental medicine from Laval University, both in 2004. He joined Concordia University in 2006 and received early promotion in 2010. Since his arrival in the department, he has developed a very productive research program (funded by NSERC and FQRNT) in cardiovascular fluid dynamics. His research group is currently working on numerical and experimental investigations of the flow in the cardiovascular system under normal and pathological conditions, and on the development of new noninvasive parameters allowing a more accurate diagnosis of cardiovascular disease. He won the CSME Student Chapter award for excellence in teaching and the CSME I. W. Smith Award for outstanding achievement in creative mechanical engineering within 10 years of graduation.