ABSTRACT
Understanding shear stress at the heat transfer surface is important because sufficient shear stress (velocity) is known to mitigate heat transfer fouling. This comprehensive paper references much literature and complements it by deriving, generally starting from force balances, the equations for calculating isothermal shear stress at the wall for single-phase flow in all of the common heat exchanger geometries: tubular, annular, parallel plate (with and without corrugations), shell-side longitudinal/window, and shell-side cross. The method for shell-side flow crossing a bundle was based upon computational fluid dynamics simulations that computed the skin friction drag on the heat transfer surface as a fraction of the total pressure drop in a cross-pass.
Funding
The authors gratefully acknowledge Chevron and HTRI for permission to publish this work. The critical reviews performed by Les Jackowski of Chevron and Kevin Farrell of HTRI are highly appreciated.
Nomenclature
A1 | = | Equation (Equation13 |
A2 | = | Equation (Equation14 |
Aw | = | wetted area, m2 |
Ax | = | cross-sectional area, m2 |
Ax,fa | = | finned annulus cross-sectional area, m2 |
a | = | Equation (Equation65 |
BC | = | baffle cut, percent of shell ID |
b | = | Equation (Equation66 |
bp | = | plate spacing, m |
c | = | Equation (Equation67 |
D | = | diameter, m |
D* | = | Equation (Equation27 |
De | = | equivalent diameter, m |
Dh,a | = | annular hydraulic diameter, m |
Dh,fa | = | finned annulus hydraulic diameter, m |
Dh,ub | = | unbaffled shell-and-tube hydraulic diameter, m |
Dh,w | = | window hydraulic diameter, m |
Di | = | inside diameter, m |
Dmax | = | diameter of maximum velocity in the annular velocity profile, m |
Do | = | outside diameter, m |
Dotl | = | outer tube limit diameter, m |
Ds | = | shell inside diameter, m |
F1 | = | pressure force acting on upstream face of flowing finite-volume element, N |
F2 | = | pressure force acting on downstream face of flowing finite-volume element, N |
F3 | = | skin friction force acting at interface of flowing finite-volume element and wall, N |
F4 | = | skin friction force acting at interface of flowing finite-volume element and wall, N |
FDP | = | form drag percentage, percent |
fa | = | annular Blasius/Darcy/Moody friction factor, dimensionless |
ffa | = | finned annulus Blasius/Darcy/Moody friction factor, dimensionless |
flam,fa | = | laminar finned annulus Blasius/Darcy/Moody friction factor, dimensionless |
fp | = | plate Blasius/Darcy/Moody friction factor, dimensionless |
ft | = | tube-side Blasius/Darcy/Moody friction factor, dimensionless |
ftur,fa | = | turbulent finned annulus Blasius/Darcy/Moody friction factor, dimensionless |
fw | = | shell-side window Blasius/Darcy/Moody friction factor, dimensionless |
fx | = | shell-side cross-flow Blasius/Darcy/Moody friction factor, dimensionless |
fx,l | = | laminar component of the shell-side cross-flow Blasius/Darcy/Moody friction factor, dimensionless |
fx,l,1 | = | Equation (Equation70 |
fx,t | = | turbulent component of the shell-side cross-flow Blasius/Darcy/Moody friction factor, dimensionless |
fx,t,1 | = | Equation (Equation72 |
f0 | = | Equation (Equation47 |
f1 | = | Equation (Equation48 |
Gc | = | mass flux, kg/s m2 |
L | = | length, m |
Lb | = | central baffle spacing, m |
Lfh | = | fin height, m |
Lft | = | fin thickness, m |
Ltp | = | tube pitch correction factor, m |
Lw | = | plate width, m |
m | = | multiplication factor for computing the skin friction drag as a function of the total pressure loss incurred in shell-side cross-flow, dimensionless |
Ncp | = | number of channels per pass, dimensionless |
Nf | = | number of fins, dimensionless |
NT | = | number of tubes, dimensionless |
NTW | = | number of tubes in window, dimensionless |
P | = | pressure, Pa |
P1 | = | pressure acting on upstream face of flowing finite-volume element, Pa |
P2 | = | pressure acting on downstream face of flowing finite-volume element, Pa |
Pf | = | fin perimeter, m |
Pl | = | longitudinal tube pitch, m |
Pp | = | corrugated plate depth, m |
Pr | = | root perimeter, m |
Pt | = | transverse tube pitch, m |
Pw | = | wetted perimeter, m |
Pw,fa | = | finned annulus wetted perimeter, m |
Re | = | Reynolds number, dimensionless |
Refa | = | Reynolds number for a finned annulus, dimensionless |
Rex | = | Reynolds number for cross-flow, dimensionless |
r | = | cylindrical coordinate, m |
Sm | = | shell-side cross-flow area, m2 |
T | = | plate gap, m |
tp | = | plate wall thickness, m |
TP | = | tube pitch, m |
V | = | average velocity, m/s |
V(D) | = | velocity profile, m/s |
VB | = | B-stream velocity, m/s |
Vfa | = | velocity in a finned annulus, m/s |
Vr | = | radial velocity, m/s |
Vw | = | window velocity, m/s |
Vy | = | velocity in y-direction |
Vz | = | axial velocity, m/s |
Vθ | = | circumferential velocity, m/s |
W | = | plate width, m |
Wm | = | mass flow rate, kg/s |
y | = | Cartesian coordinate, m |
z | = | Cartesian or cylindrical coordinate, m |
Greek symbols
βp | = | chevron angle measured from the vertical, degrees |
ΔP | = | pressure drop, Pa |
ΔPf,cf | = | frictional pressure drop for shell-side cross-flow, Pa |
ΔPf,w | = | frictional pressure drop for shell-side window flow, Pa |
ΔPt | = | total pressure drop, Pa |
θ | = | cylindrical coordinate, radians |
µ | = | viscosity, kg/m s |
ρ | = | density, kg/m3 |
σ | = | normal stress, Pa |
σrr | = | cylindrical coordinate normal stress acting on radial surface in radial direction, Pa |
σzz | = | cylindrical coordinate normal stress acting on axial surface in axial direction, Pa |
σθθ | = | cylindrical coordinate normal stress acting on circumferential surface in circumferential direction, Pa |
τ | = | shear stress, Pa |
= | total stress tensor, Pa | |
τfa,ave | = | estimate of the average shear stress in a finned annulus, Pa |
τfric | = | estimate of the frictional shear stress in a plate heat exchanger that excludes the form drag component caused by the corrugations, Pa |
τi | = | shear stress acting on inner annular surface, Pa |
τij | = | shear stress acting on i-surface in j-direction, Pa |
τji | = | shear stress acting on j-surface in i-direction, Pa |
τmax | = | shear stress acting at diameter of maximum velocity in the annular velocity profile, Pa |
τo | = | shear stress acting on outer annular surface, Pa |
τp | = | shear stress acting on the plate walls, Pa |
τrz | = | cylindrical coordinate shear stress acting on radial surface in axial direction, Pa |
τrθ | = | cylindrical coordinate shear stress acting on radial surface in circumferential direction, Pa |
τt | = | shear stress acting on the tube walls, Pa |
τw | = | estimate of shell-side longitudinal/window flow shear stress, Pa |
τx | = | estimate of shell-side cross-flow shear stress, Pa |
τyz | = | Cartesian coordinate shear stress acting on y-direction surface in z-direction, Pa |
τzr | = | cylindrical coordinate shear stress acting on axial surface in radial direction, Pa |
τzθ | = | cylindrical coordinate shear stress acting on axial surface in circumferential direction, Pa |
τθr | = | cylindrical coordinate shear stress acting on circumferential surface in radial direction, Pa |
τθz | = | cylindrical coordinate shear stress acting on circumferential surface in axial direction, Pa |
ϕa | = | area enlargement factor, dimensionless |
Notes
1 The trigonometric functions in this equation are in radians.
Additional information
Notes on contributors
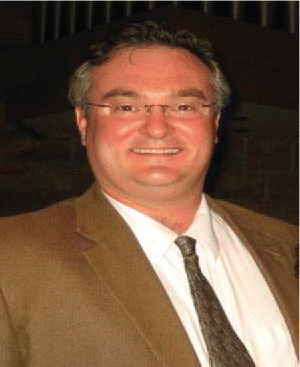
Christopher A. Bennett
Christopher A. Bennett earned a B.S. in chemical engineering with a minor in chemistry, specializing in physical chemistry, from the University of Toledo, Toledo, OH, and then an M.S. and a Ph.D. in chemical engineering from the University of Michigan, Ann Arbor, MI. His research in graduate school focused on the synthesis, characterization, and catalytic evaluation of mono- and bimetallic early transition metal nitrides, from which he concluded that the catalytic sites for n-butane dehydrogenation over vanadium nitride were nonmetal vacancy defects. He then entered industry as a researcher working for Heat Transfer Research, Inc. (HTRI), where he applied his knowledge of characterization, heat transfer, and fluid dynamics to fouling, specializing in crude oil fouling. He was consequently the first to report the manifestation of the isokinetic/compensation effect in high-temperature crude oil fouling, and because the laboratory observations parallel industrial experiences observed in multiple crude oil preheat trains, he can assure you that at least this manifestation of the isokinetic/compensation effect is not the result of experimental errors. During his tenure at HTRI he also chaired the Crude Oil Fouling Task Force (COFTF) and co-chaired the Exchanger Design Margin Task Force (EDMTF). He is currently a heat exchanger specialist at Chevron Energy Technology Company, where he continues his study of fouling.
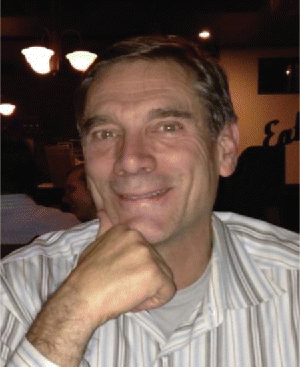
Robert P. Hohmann
Robert P. Hohmann is a heat exchanger specialist with more than 35 years of experience with Chevron Corporation. He provides design, troubleshooting, technical development, training, and consulting services to refining, chemical processing, and wellstream producing operations worldwide. He began working for Chevron Research during summers as a process engineer in 1977, and continues as a senior advisor (process engineering) after joining Chevron full time in 1979. He chaired the HTRI (Heat Transfer Research, Inc.) Computer Programs Subcommittee from 1991 to 1998 and has been a member of the HTRI Technical Committee from 1998 to 2000 and 2003 to the present. He is a degreed chemical engineer—M.Ch.E., Massachusetts Institute of Technology, and B.S.Ch.E. (Highest Honors), University of California at Berkeley. He is a member of Phi Beta Kappa, an Eagle Scout, and an avid backpacker.