ABSTRACT
A study of evaporative cooling of water was conducted using dual-scale hierarchically porous aluminum coating. The coating was created by brazing aluminum powders to a flat aluminum plate. The effects of particle size and thickness on evaporative heat transfer were investigated using average aluminum particle diameters of 27, 70, and 114 µm and average coating thicknesses of 560, 720, and 1200 µm. Constant ambient temperature of 24°C and relative humidity of 50% were provided throughout the study. Evaporative cooling tests on the coated surfaces were compared to the plain surface. Tested dual-scale porous coatings enhanced evaporative heat transfer significantly, compared to that of the plain surface, due to the effective wicking of water to the entire heated area. With particle size increase, both the wickability and dryout heat flux were significantly increased. The dryout heat flux with the particle size of 114 µm was 3.2 times higher than that with the particle size of 27 µm. At the fixed particle size of 70 µm the dryout heat flux increased as thickness increased, which resulted in the maximum dryout heat flux of 10.6 kW/m2 and the maximum heat transfer coefficient of 251 W/m2K at the coating thickness of 1200 µm.
Acknowledgment
The authors are grateful for the support of their work by Bill & Melinda Gates Foundation through the Grant OPP1069110.
Nomenclature
A | = | area (m2) |
AL-HPC | = | Aluminum Hierarchically Porous Coating |
e | = | Euler number |
g | = | gravitational acceleration (m/s2) |
h | = | heat transfer coefficient (W/m2K) |
H | = | fluid height (m) |
P | = | pressure (Pa) |
Q | = | heat transfer rate (W) |
q” | = | heat flux (W/m2) |
r | = | roughness factor |
R | = | average pore radius (m) |
t | = | time (s) |
T | = | temperature (K) |
W(x) | = | Lambert function |
x | = | arbitrary variable in Lambert function |
Greek symbols | ||
ΔT | = | temperature difference (K) |
θ | = | contact angle of smooth surface (deg) |
θ* | = | contact angle of rough surface (deg) |
θd | = | dynamic contact angle (deg) |
μ | = | dynamic viscosity (N/m2s) |
ρ | = | density (kg/m3) |
σ | = | surface tension (N/m) |
Subscripts | ||
amb | = | ambient air |
avg | = | average |
c | = | capillary |
Additional information
Notes on contributors
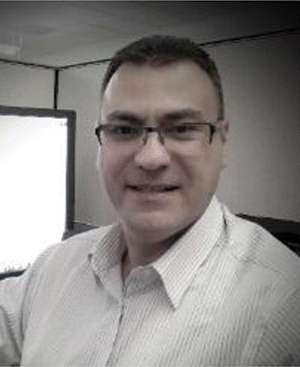
Nabeel Fathi
Nabeel Fathi received his bachelor of science degree in mechanical engineering from the University of Mosul, Iraq in 1993. During the following 10 years he worked as a CAD teacher in different private institutes in Iraq. In 2005 he worked as a site design manager for Huawei Technologies in Iraq and continued to work for the same company after moving to Texas, USA. In 2013 he joined the Master of Science program in the Erik Johnson School of Computer Science and Engineering at the University of Texas at Dallas.
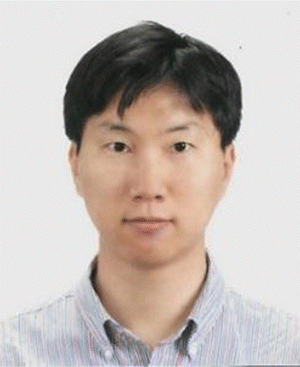
Jinsub Kim
Jinsub Kim received his M.S. (2002) and Ph.D. (2007) degrees from the Seoul National University in South Korea. After graduation, he worked for Samsung Electronics as a senior engineer from 2007 to 2014. Then, he joined Multiscale Heat Transfer lab at the University of Texas at Dallas and worked there from 2014 to 2016. Currently, he is a senior researcher at the Korea Institute of Machinery and Materials. His research interests include the surface topography and wettability effect on the boiling heat transfer, evaporation on the superhydrophilic surface and electronics cooling for high power chips.
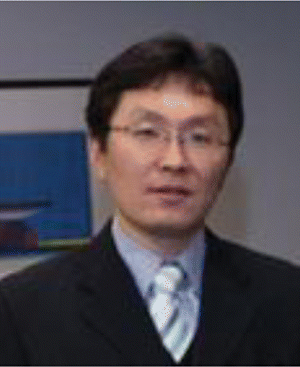
Seongchul Jun
Seongchul Jun is a research associate at the University of Texas at Dallas. He received M.S. degree from the University of California at Irvine and received his Ph.D. from the University of Illinois at Chicago in 2013. His research is mainly in the area of phase change heat transfer, especially, the boiling and evaporative cooling enhancement by using micro and nano scale coatings.
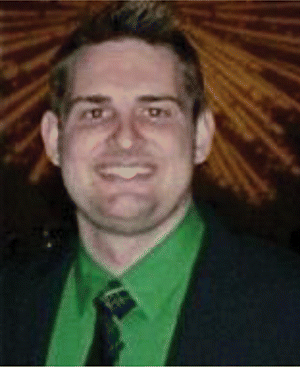
Ryan M. King
Ryan M. King is a Design Engineering Manager at Zodiac Seats US in Gainesville, Texas. He received his Master of Science in Mechanical Engineering in 2011 and performed his research under the supervision of Prof. S. M. You. His research focused on enhancing evaporative heat transfer by creating highly wicking and wetting surfaces.

Miguel Amaya
Miguel Amaya is a Senior Lecturer at the Department of Mechanical and Aerospace Engineering of the University of Texas at Arlington (UTA). He received his Ph.D. from UTA in 1997. After a time in manufacturing, he re-joined UTA in 2008 as a research associate in Prof. S. M. You's Microscale Heat Transfer Laboratory, located at UTA at that time. In that capacity, he participated in various facets of two-phase heat transfer research and particularly in the enhancement of wettability. He currently is an instructor of thermal engineering courses and of other mechanical engineering courses at UTA.
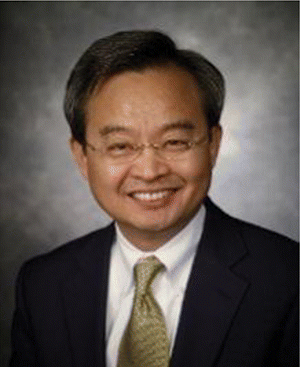
Seung M. You
Seung M. You is currently a Professor at the Mechanical Engineering Department of The University of Texas at Dallas starting from 2013. He received his Ph.D. from the University of Minnesota in 1990 and he was a professor at The University of Texas at Arlington from 1990 to 2012. He has authored and co-authored numerous publications and he is a Fellow of ASME. He has extensive research experience in thermal science focusing on the enhancement of boiling and evaporative heat transfer using microporous and nano-structured surfaces. His research interest also includes 3-D embedded cooling for high-heat-flux microelectronics, thermal ground planes, and heat transfer in thermal energy systems.