ABSTRACT
Performance analysis and optimization of a circular pin-fin with inside gaps in a rectangular cooling channel were performed at Reynolds number, 10,000, using three-dimensional Reynolds-averaged Navier–Stokes equations and a multi-objective genetic algorithm. The low-Reynolds-number version of the shear stress transport model was used as turbulence closure. A parametric study was also performed to identify the geometrical effects of the pin-fin on heat transfer and pressure drop. The straight and reference gapped pin-fins yielded better performances than those of the circular pin-fin without the gap in terms of both heat transfer and pressure drop. The objective of the optimization was to maximize the heat transfer and minimize the pressure loss, simultaneously. The area-averaged Nusselt number and pressure loss coefficient were considered as objective functions, and three design variables related to the geometry of the gapped pin-fin were chosen for the optimization. Twenty-seven design points were generated using Latin hypercube sampling in the design space, and response surface approximation models were constructed for the objective functions. The optimization results were analyzed using five representative solutions on the Pareto-optimal front. The objective functions were found to be significantly affected by variation in the design variables, especially, the width of front gap and the rear gap angle.
Nomenclature
Ap | = | pin surface area (m2) |
Ac | = | channel surface area (m2) |
CFD | = | computational fluid dynamics |
D | = | diameter of circular pin-fin (m) |
Dc | = | hydraulic diameter of the channel (m) |
Dh | = | hydraulic diameter (m) |
Dp | = | hydraulic diameter of the pin-fin (m) |
FNu | = | objective function related to the heat transfer |
G1 | = | width of front part of gapped pin-fin (m) |
G2 | = | width of rear part of gapped pin-fin (m) |
H | = | height of channel (m) |
K | = | pressure loss coefficient of the channel |
kf | = | fluid thermal conductivity (W/mK) |
L | = | streamwise length of the channel (m) |
Lp | = | streamwise distance from the inlet to the center of the pin-fin (m) |
LHS | = | Latin hypercube sampling |
MOGA | = | multi-objective generic algorithm |
Nu | = | Nusselt number |
Nuc | = | channel Nusselt number |
Nup | = | pin Nusselt number |
= | area-averaged Nusselt number | |
NSGA | = | non-dominated sorting genetic algorithm |
POD | = | Pareto-optimal design |
Pr | = | Prandtl number |
△p | = | pressure drop (Pa) |
q0 | = | wall heat flux (W/m2) |
R | = | real numbers |
R2 | = | coefficient of determination |
RANS | = | Reynolds-averaged Navier–Stokes |
Re | = | Reynolds number |
R2adj | = | adjusted R square |
RMSE | = | root-mean-square error |
RSA | = | response surface approximation |
SST | = | shear stress transport |
Tb | = | bulk temperature (K) |
Tw | = | wall temperature (K) |
Tw, c | = | wall temperature of channel (K) |
Tw, p | = | wall temperature of pin-fin (K) |
Uin | = | average velocity at the inlet (m/s) |
W | = | width of channel (m) |
X | = | design matrix of the system |
x, y, z | = | orthogonal coordinate system |
y+ | = | dimensionless wall distance |
Greek symbols
α | = | surface angle (°) |
β | = | coefficient of regression analysis |
ϵ | = | random error |
θ | = | rear gap angle (°) |
ρ | = | fluid density (kg/m3) |
Additional information
Notes on contributors
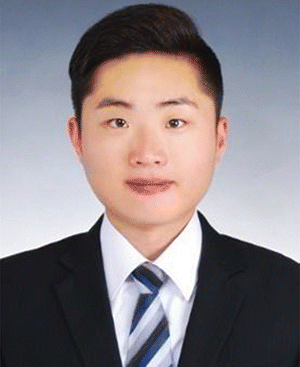
Kwang-Jin Sa
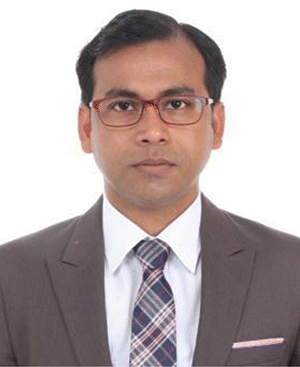
Arshad Afzal
Arshad Afzal received his Ph.D. degree (Thermal and Fluids Engineering) from Inha University, Korea in 2015. He received his M. Tech (Thermal Engineering) and B. Tech (Mechanical Engineering) degrees from Aligarh Muslim University in 2009 and 2006, respectively. Presently, he is working as INSPIRE Faculty in the Department of Mechanical Engineering at Indian Institute of Technology Kanpur, India. His research interests are microfluidics, gas turbine cooling, thermal-fluid design optimization and surrogate modeling.
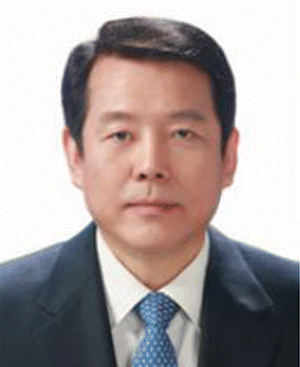
Kwang-Yong Kim
Kwang-Yong Kim received his B.S. degree from Seoul National University in 1978, and his M.S. and Ph.D. degrees from the Korea Advanced Institute of Science and Technology (KAIST), Korea, in 1981 and 1987, respectively. He is currently a professor in the department of mechanical engineering and dean of college of engineering in Inha University, Incheon, Korea. He is also the current co-editor-in-chief of the International Journal of Fluid Machinery and Systems (IJFMS), and associate editor of ASME Journal of Fluids Engineering. He is current chairman of Asian Fluid Machinery Committee (AFMC). He is also a fellow of Korean Academy of Science and Technology, a fellow of the American Society of Mechanical Engineers (ASME) and an associate fellow of the American Institute of Aeronautics and Astronautics (AIAA).