Abstract
Ultrafine carbon, metal, and metal oxide particles were generated with a commercially available spark generator designed for the production of carbon particles. Aerosols with number concentrations up to 107 cm−3 were produced at flow rates up to 150 lpm. Lognormal size distributions with modal diameters in the range of 18–150 nm and geometric standard deviations of about 1.5 were obtained. The chemical composition, size, number concentration, morphology, and surface area of the particles were varied, and the generation of particles with fixed characteristics could be maintained over many hours. The particle characteristics, however, could not be varied independently. For a certain chemical composition only size and number concentration were variable; morphology and surface area were fixed regardless of particle size. The particles grow by coagulation of primary particles formed by nucleation. The coagulated particles can either stick together and maintain their identity or fuse together and lose their identity. Each material used for the generation of ultrafine particles is thus associated with a certain morphology and surface area: silver with a low mass-related BET surface area (20 m2 g−1), metal oxides and iridium with a low-to-intermediate BET surface area (50 m2 g−1 for cadmium oxide, 120 m2 g−1 for iridium, and 300 m2 g− 1 for ferric oxide), and carbon with a large BET surface area (750 m2 g−1). Iridium, on the other hand, has a huge volume-related BET surface area (2800 m2 cm−3). It was not possible to generate ultrafine carbon particles without contaminations with the generator. However, these contaminations could be decreased in this study from 25% to 6% by replacing organic components of the generator by pure inorganic components.
INTRODUCTION
The community of environmental toxicologists and epidemiologists has come to the consensus that the inhalation of fine ambient particles (particles in the geometrical diameter range from 0.1 to 2.0 μ m) is associated with a health risk for susceptible individuals and that the appropriate dose metric for quantifying this risk is the mass of the particles deposited in the respiratory tract of these individuals. No consensus was achieved so far regarding the risk associated with the inhalation of ultrafine particles (particles smaller than 0.1 μ m in diameter) and their appropriate dose metric. Several characteristics of ultrafine particles can explain why these particles may be more potent in inducing adverse health effects than larger particles: their number concentration, surface area, and deposition efficiency in the human respiratory tract are much higher compared to larger particles. They can easily penetrate into the epithelium and thus reach interstitial sites or even the circulatory system, and their large surface area acts as a carrier for toxic gases and chemicals into the lungs. The following hypotheses are currently tested using in vitro and in vivo studies:
-
Deposition of ultrafine particles in the respiratory tract causes adverse reactions in the respiratory and cardiovascular system.
-
Ultrafine particles deposited in the lungs are harmful because of their generic nature as particles. In other words, they carry a “physical toxicity” independent of their chemical composition.
-
The appropriate dose metric for quantifying the risk associated with the deposition of ultrafine particles in the respiratory tract is the number concentration or the surface area of the particles.
To test these hypotheses ultrafine particles simulating the physical properties of ambient particles (size, surface area, number concentration) are required. It was the aim of this study to provide, in the size range of 5 to 100 nm, highly concentrated, quasi-monodisperse aerosols with particles of pure carbon, pure metals, and metal oxides without surface contaminations for toxicological in vivo studies. In addition, it should be possible to vary the morphology of the particles. The priority assignment was to produce all these desired ultrafine particles by the same generator.
Ultrafine particles can be produced in flames (CitationPratsinis and Kodas 1993). However, due to the steep temperature gradient in a flame this process offers poor control over particle size and morphology. Ultrafine aerosol particles can also be generated by dispersion of solutions or suspensions by jet nebulizers or Taylor cones, but the impurities of the dispersed liquid will contaminate the particles. The same argument applies to vaporization of material in tube furnaces and subsequent homogenous nucleation, condensation, and coagulation. Impurities evaporating from crucibles and tube materials are incorporated in the ultrafine particles (CitationRoth et al. 1994).
Spark discharging between two solid electrodes of known chemical composition through an ultrapure noble gas is a suitable production method for ultrafine particles which will meet most of the requirements mentioned above.
Spark discharging has been shown to produce large (> 500 nm) polydisperse cadmium oxide particles (CitationHochrainer and Soderholm 1986), small (< 10 nm) quasi-monodisperse carbon, silver, and gold particles (CitationSchwyn et al. 1988), and polydisperse copper, iron, and zinc particles in the size range 10–1000 nm (CitationWatters et al. 1989). The spark generator developed by CitationHelsper et al. (1993) is now available as a commercial product for producing carbon particles with high mass output (Palas, GFG 1000, Karlsruhe, Germany). This generator has recently been used for the production of radioactive labelled carbon particles. For this purpose CitationBrown et al. (2000) applied carbon electrodes covered with pertechnetate. The generator was also used for the production of 192iridium particles (CitationKreyling et al. 2002).
MATERIALS AND METHODS
Spark Generator
In this study, a Palas spark generator (model GFG 1000) has been used. A schematic view of this generator is shown in . The flat ends of the cylindrical carbon electrodes are positioned 2 mm apart in the middle of a polyamide chamber of 19 cm3 volume. During particle production the width of this gap is maintained automatically to keep the breakdown voltage constant. A 20 nF capacitor connected to the electrodes is charged by a high-voltage supply with adjustable output current. When the breakdown voltage of 2 kV is reached it discharges in a spark across the electrode gap, vaporizing material from the receiving electrode and producing primary particles a few nm in diameter by homogeneous nucleation of the vapor. These particles are carried by a flow of pure argon (less than 10− 6 impurities) into the polyamide chamber where they grow in size due to coagulation or coalescence. The aerosol outlet is located about 15 mm downstream from the electrodes. The aerosol leaving the outlet is diluted with pure nitrogen in order to stop coagulation.
The argon flow through the gap between the electrodes must be large enough to remove all primary particles and ions from the gap before the ignition of the next spark to achieve a stable spark frequency. An argon flow of 6 l/min is sufficient to exchange the gas volume in the gap in the time elapsing between ignitions of two sparks at a spark frequency of 300 Hz (CitationHelsper et al. 1993).
The spark frequency can be adjusted by the current charging the capacitor. When the gap between the electrodes is 2 mm wide, increasing the current from 0.13 to 20 mA enhances the spark frequency from 3 to 300 Hz. The frequency can be further enhanced by lowering the gap between the electrodes. At higher frequencies larger particles can be produced.
The following electrodes have been used: carbon (RW0, SGL Carson AG, Bonn, Germany) with less than 2 × 10−7 metal contaminations and diameters of 6 mm; and silver (Degussa, Hanau, Germany), iridium, iron, and cadmium (Alfa, Karlsruhe, Germany) with impurities of less than 10−6 and diameters ranging from 1 to 4 mm. For the production of iron and cadmium oxide particles the argon was mixed with oxygen up to concentrations of 3%.
The aerosols were used to expose animals in a whole body chamber of 330 liter volume and with a uniform horizontal flow (CitationKarg et al. 1998; CitationRoth et al. 1998). Before entering the chamber the aerosols were neutralized with ions generated by a 3 mCi 85Kr source and diluted with pure air to achieve the desired particle number concentration. The dilution device consisted of two concentric tubes. The air entered the inner aerosol-conducting tube through its perforated wall so that homogenous mixing was obtained. Gaseous impurities in the aerosols (nitrogen oxides, ozone, and hydrocarbons) were monitored inside the exposure chamber and the mass concentration of the aerosol leaving the exposure chamber was gravimetrically determined after collecting the particles on a filter. The entire set-up is shown in .
Evaluation of Particle Size and Concentration
Size distribution and number concentration of the generated aerosols were measured with a differential mobility analyzer (EMS 150, Hauke, Gmunden, Austria) and a condensation particle counter (CPC model 3022A, TSI, St. Paul, USA). The EMS data were corrected for losses by diffusion in the sampling line and for the counting efficiency of the CPC as suggested by CitationBartz et al. (1985).
Evaluation of Particle Morphology
The particles generated were collected by diffusional precipitation on grids for electron microscopic examinations of their morphology.
Evaluation of Particle Surface Area
Two metrics carry the name “surface area”: the “Brunauer-Emmett-Teller surface area (BET)” and the “active surface area (ASA).”
The BET surface area was determined by adsorption of nitrogen on particle surfaces at the boiling temperature of liquid nitrogen (77 K). To obtain a clean surface for nitrogen adsorption a particle sample was outgassed at 200°C. From the adsorption curve in a relative pressure range p/p o (p o = saturation pressure of boiling nitrogen) from 0.05 to 0.3 the nitrogen mass necessary to form a monolayer on all particles was calculated according to the BET theory (CitationGregg and Sing 1995), with the assumption that each adsorbed nitrogen molecule occupies an area of 0.162 nm2. Thus the entire geometrical surface area of the particle ensemble was estimated.
To determine the active surface area ASA of the particles their mobility diameter d was evaluated with a differential mobility analyzer. ASA is the surface area of a sphere with diameter d and density ρ having the same mobility or diffusivity as the particle (CitationRogak et al. 1991). Thus, the mass/volume-related surface areas for a particle size distribution with surface median diameter d SMD and mass median diameter d MMD are given by
RESULTS AND DISCUSSION
Oscilloscopic measurements have shown that each discharge consists of up to 10 single oscillating sparks of 4 μ s duration and different polarity caused by the inductive and capacitive properties of the high voltage circuit. The sparks with different polarity explain the flat shape of the electrode ends, since a direct current spark would produce a concave anode and a convex cathode surface (CitationWeizel and Rompe 1949; CitationGerthsen et al. 1982). A second consequence is that the gap between the electrodes remains at the same position with respect to the argon inlet in the spark chamber, with the result that the generator operates in a rather stable manner during continuous operation. Therefore, the particle number concentration varied only by 10% during a 10 day exposure experiment generating aerosols for 6 h a day. In four animal exposure experiments with 30 nm carbon particles over a period of one year the reproducibilty of the modal diameter for fixed operation conditions of the generator (spark frequency and flow rates) was 10%. The operation stability proved spark discharging to be superior over most of the particle generation techniques.
Carbon particles produced with the generator were contaminated by up to 25% volatile material by weight. This fraction was measured by heating samples at 320°C for half an hour. For this purpose a high temperature furnace equipped with a quartz glass tube, an argon atmosphere, and a differential flame ionisation detector (Model 108A, JUM, Karlsfeld, Germany) was used.
These contaminations were due to organics evaporating from the walls of the polyamide chamber of the generator. To reduce the organic contaminations on the particles this chamber was replaced by a ceramic chamber. In addition, all plastic tubing in the generator was replaced by stainless steel tubing with polished inner surfaces, and purified gases (model PS4-MT3, Saes Pure Gas Inc., San Luis Obispo, CA, USA) were used for production. These modifications allowed producing carbon particles with less than 6 ± 1% of organic volatile material by weight.
Particle Size Distributions
Both particle size and concentration depend on the particle material, the discharge frequency, and the flow rates of argon, nitrogen, and air. With an increase of the discharge frequency the modal diameter of the size distribution increased (). Typical characteristics of ultrafine aerosols generated for a number of operation parameters of the generator and measured at the inlet of the exposure chamber are listed in . Some of the corresponding size distributions are shown in .
FIG. 3 Dependence of the modal diameters of ultrafine aerosols on the discharge frequency for operation parameters shown in .
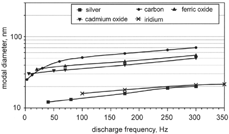
TABLE 1 Characteristics of ultrafine aerosols generated for various operation parameters of the generator
Increasing the discharge frequency of the generator had the effect of increasing the number concentration of the generated particles and thus their coagulation rate. As a consequence, carbon particles increased in median diameter from 25 to 70 nm when the frequency was raised from 3 to 300 Hz (, ). To demonstrate the influence of coagulation the particle size distribution of carbon aerosols was determined at the inlet and outlet of the exposure chamber (). The mean residence time of the aerosol in the chamber was about 150 s. In this time the particle number concentration decreased from 107 to 3 × 106 cm−3 and the modal diameter increased from 32 to 50 nm. The particle size can further be raised to 150 nm by coagulation when the aerosol is not diluted with nitrogen (). It can therefore be concluded that the increase in the modal diameter of ultrafine carbon aerosols with increasing discharge frequency is due to coagulation. Isotropic conditions for the number concentration in the exposure chamber can therefore only be obtained for number concentrations smaller than 107 cm−3.
FIG. 5 Size distribution of a carbon aerosol of 107 cm− 3 number concentration at the inlet and outlet of the exposure chamber.
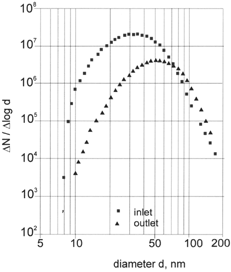
Sampling of 25 nm carbon aerosol with about 106 cm−3 particle number concentration at six locations inside the exposure chamber in a plane perpendicular to the aerosol flow revealed that the flow pattern in the chamber could be characterized by a low turbulent displacement flow. The aerosol concentration was 1.4 × 106 cm−3 with a standard deviation of only 4%.
Particle Morphology
Transmission electron microscopy revealed that particles composed of different material have different shapes (). It seems that the particle material solely determines particle morphology. This can be due to either the thermodynamics in the chamber or to material characteristics such as the surface tension.
-
Silver particles: These particles were found to be compact, spherical particles with smooth surfaces.
-
Cadmium oxide particles: These particles were less spherical than silver particles but they were compact particles with rough surfaces.
-
Iron oxide particles: These particles were agglomerates of closely packed primary particles.
-
Carbon and iridium particles: These particles were chain agglomerates and, independent of their size, composed of spherical primary particles with a uniform size of a few nanometers.
FIG. 6 Micrographs of ultrafine particles: (a) silver particles, (b) cadmium oxide particles, (c) iron oxide particles, (d) iridium particles, and (e) carbon particles. (Continued)
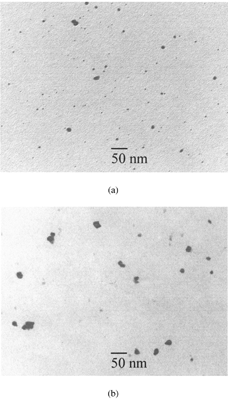
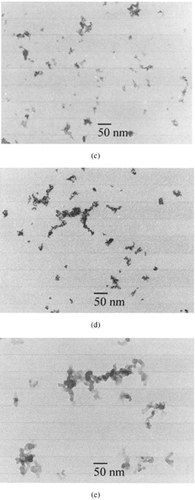
The differences in particle morphology were the result of different competitive processes. The primary particles formed by nucleation grew further either by collision with product molecules (condensation) or particles (coagulation). The colliding particles maintain their identity or fuse together into a single particle. This fusion can be complete or incomplete. In the case of silver, complete fusion (full coalescence) occurred. These particles were therefore compact particles of nearly spherical shape. In the case of metal oxide particles, incomplete fusion (partial sintering) occurred, and thus iron oxide particles were compact nonspherical particles, whereas cadmium oxide particles were compact particles of nearly spherical shape. In the case of carbon and iridium particles, coagulation of the primary particles was the dominant process, with the result of the formation of chain agglomerates.
Particle Surface Area
In BET and ASA are given as mass-related surface area: BETm varied between 20 m2 g−1 for ultrafine silver particles and 750 m2 g−1 for ultrafine carbon particles. As anticipated, the variation in ASAm was much smaller, since ASAm is determined by the size rather than the morphology of the particles.
When particles were formed by complete fusion of primary particles it was anticipated that their BETm and ASAm were similar. This was really observed for silver particles. Since metal oxide particles were formed by incomplete fusion, their BETm should be larger than their ASAm. This was also observed. However, this difference was found to be larger for iron than for cadmium oxide particles. Therefore, fusion occurred closer to completion when iron oxide particles collided. When particles are formed by collision of primary particles without any fusion their BETm should be much larger than their ASAm. That was observed for carbon and iridium particles. The observed differences in BETm and ASAm thus confirmed that the particles were produced by processes as suggested by their appearance in electron microscopy.
Since the size of ultrafine particles can only be increased by increasing the number of primary particles and thus enhancing their coagulation rate, the surface areas of all particles produced from the same material will be the same regardless of the size of the particles. That is the case, as can be seen from , for carbon particles of two different sizes.
The appearance of carbon and iridium particles in electron microscopy was rather similar. It was therefore anticipated that their BETm and ASAm were also similar. That this was not the case might have been due to the normalization of BET and ASA to the total mass of the considered particle sample since the density of iridium is much larger than that of carbon. This discrepancy is therefore no longer observed when the surface areas are normalized to the volume of the particle sample ().
From the toxicological point of view it is more likely that BETv and not BETm is the appropriate dose metric. Neither ASAv nor ASAm are, however, of toxicological relevance.
CONCLUSIONS
Spark discharging is a simple and reliable technique for the generation of ultrafine aerosol particles. Aerosols with number concentrations up to 107 cm−3 can be produced at flow rates up to 150 lpm. The chemical composition, size, number concentration, morphology, and surface area of the particles can be varied, and particles with fixed characteristics can be produced over many hours. It is, however, not possible to vary all these characteristics independently. For a certain chemical composition only size and number concentration can be varied; morphology, and thus surface area, will be fixed regardless of size. Each material used for the generation of ultrafine particles is thus associated with a certain morphology and surface area: silver with a low mass-related BET surface area (20 m2 g−1), metal oxides and iridium with a low-to-intermediate BET surface area (50 m2 g−1 for cadmium oxide, 120 m2 g−1 for iridium and 300 m2 g−1 for ferric oxide), and carbon with a large BET surface area (750 m2 g−1). Iridium, on the other hand, has a huge volume-related BET surface area of 2800 m2 g− 1. With this generator it was not possible to generate ultrafine carbon particles without contaminations. However, these contaminations could be decreased in this study from 25% to 6% by replacing organic components of the generator with pure inorganic components.
Acknowledgments
We thank Dr. X. Hecht, Institute for Technical Chemistry II, TU Munich, for the BET analysis and Drs. W. Kreyling and J. Gentry for valuable discussions.
REFERENCES
- Bartz , H. , Fissan , H. , Helsper , C. , Kousaka , C. , Okuyama , K. , Fukushima , N. , Keady , P. B. , Kerrigan , S. , Fruin , S. A. , McMurry , P. H. , Pui , D. Y. H. and Stolzenburg , M. H. 1985 . Response Characteristics for Four Different Condensation Nucleus Counters to Particles in the 3–50 nm Diameter Range . J. Aerosol Sci. , 5 : 443 – 456 .
- Brown , J. S. , Kim , C. S. , Reist , P. C. , Zeman , K. L. and Bennett , W. D. 2000 . Generation of Radiolabelled “Soot-Like” Ultrafine Aerosols Suitable for Use in Human Inhalation Studies . Aerosol Sci. Technol. , 32 : 325 – 337 .
- Gerthsen , C. , Kneser , H. O. and Vogel , H. 1982 . Physik , p. 328 Berlin : Springer Verlag .
- Gregg , S. J. and Sing , K. S. W. 1995 . Adsorption, Surface Area and Porosity , London : Academic Press .
- Helsper , C. , Mölter , W. , Löffler , F. , Wadenpohl , C. , Kaufmann , S. and Wenninger , G. 1993 . Investigations of a New Aerosol Generator for the Production of Carbon Aggregate Particles . Atmospheric Environment , 27A : 1271 – 1275 .
- Hochrainer , D. and Soderholm , S. 1986 . “ A Generator for Cadmium Oxide Fume Aerosols ” . In Aerosols, Formation and Reactivity , pp. 1053 – 1056 . New York : Pergamon Press .
- Karg , E. , Roth , C. and Heyder , J. 1998 . Do Inhaled Ultrafine Particles Cause Acute Health Effects in Rats? II: Exposure System . J. Aerosol Sci. , 29 : S315 – S316 .
- Kreyling , W. G. , Semmler , M. , Erbe , F. , Mayer , P. , Takenaka , S. , Schulz , H. , Oberdörster , G. and Ziesenis , A. 2002 . Translocation of Ultrafine Insoluble Iridium Particles from Lung Epithelium to Extrapulmonary Organs Is Size Dependent but Very Low . J. Tox. Environ. Health , A65 : 1513 – 1529 .
- Pratsinis , S. E. and Kodas , T. T. 1993 . “ Manufacturing of Materials by Aerosol Processes ” . In Aerosol Measurements, Principles, Techniques and Applications , Edited by: Willeke , K. and Baron , P. A. pp. 721 – 746 . New York : Van Nostrand Reinhold .
- Reist , P. C. 1984 . Introduction to Aerosol Science , pp. 23 – 25 . New York : Maximilian Publishing .
- Rogak , S. N. , Baltensperger , U. and Flagan , R. C. 1991 . Measurement of the Mass Transfer to Agglomerate Aerosols . Aerosol Sci. Technol. , 14 : 447 – 458 .
- Roth , C. , Karg , E. and Heyder , J. 1998 . Do Inhaled Ultrafine Particles Cause Acute Health Effects in Rats? I. Particle Production . J. Aerosol Sci. , 29 : S679 – S680 .
- Roth , C. , Scheuch , G. and Stahlhofen , W. 1994 . Clearance Measurements with Radioactively Labelled Ultrafine Praticles . Ann. Occup. Hyg. , 38 ( Suppl. 1 ) : 101 – 106 .
- Schwyn , S. , Garwin , E. and Schmidt-Ott , A. 1988 . Aerosol Generation by Spark Discharge . J. Aerosol Sci. , 19 : 639 – 642 .
- Watters , R. L. Jr. , deVoe , J. R. , Shen , F. H. , Small , J. A. and Marinenko , R. B. 1989 . Characteristics of Aerosol Produced by Spark Discharge . Analyt. Chem. , 61 : 1826 – 1833 .
- Weizel , W. and Rompe , R. 1949 . Theorie elektrischer Lichtbögen und Funken , Leipzig : Johann Ambrosius Barth Verlag .