Abstract
In the present study, we found that pressure-dependent droplet-to-particle formation is important for the control of both droplet and particle characteristics during the production of particles with enhanced properties. Using experimental and simulation approaches, the present study investigated the droplet-to-particle formation of zinc oxide as a model material that was synthesized via low-pressure spray pyrolysis. The size distributions of both the droplets generated under low-pressure and the synthesized particles were measured and compared. The effects of operating conditions, i.e., operating pressure, carrier gas-, and liquid-flow rates, reactor temperature, and precursor concentration, on the characteristics of the generated droplets and synthesized zinc oxide particles were systematically investigated. We found that broad and bimodal droplet size distributions shifted to narrow and monodispersed distributions as chamber pressures were reduced. The low-pressure-synthesized zinc oxide nanoparticles were highly crystallized with unimodal distributions and sizes of approximately 8 nm. Droplet temperature decreased with decreasing chamber pressure, which confirmed both the evaporative cooling of droplets and the formation of smaller droplet sizes. The chamber temperature and droplet size simulation results were in accordance with the experimental results. In conclusion, we found that the chamber pressure is the primary determinant of monodispersity with respect to droplet size distribution and to the size and morphology of the synthesized particles.
NOMENCLATURE
![]() | = |
= flow rate of liquid [kg s−1] |
![]() | = |
= flow rate of air [kg s−1] |
r′ g0 | = |
= Geometric mean radius [μ m] |
C m (r') | = |
= Cunningham's correction factor of radius r' |
K 0 | = |
= Coagulation rate function |
L 1 | = |
= distance between measuring point and detector/lens [mm] |
L 2 | = |
= distance between dip of sprayer and measuring point [mm] |
P ch | = |
= chamber pressure [Pa] |
Q c | = |
= carrier gas flow rate [m3 s−1] |
Q l | = |
= liquid flow rate [m3 s−1] |
d 32 | = |
= Sauter mean diameter [μ m] |
d c | = |
= crystallite size [nm] |
d d | = |
= droplet diameter [m] |
d o | = |
= discharge orifice diameter [m] |
d p | = |
= product particle size (Feret diameter) [μ m] |
d v,50 | = |
= volumetric diameter at 50 vol% [μ m] |
Δ P L | = |
= atomizing pressure differential [Pa] |
Greek Symbols | = | |
ρ A | = |
= air density [kg m−3] |
ρ l | = |
= density of water liquid [kg m− 3] |
ϵ o | = |
= Average energy dissipation rate [m2/sec3] |
γ | = |
= surface tension of precursor [N m−1] |
η | = |
= viscosity of liquid/precursor [N s m−2] |
σ | = |
= Standard deviation |
Subscripts | = | |
a | = |
Air |
l | = |
Liquid |
1. INTRODUCTION
Control of droplet and particle characteristics, including size, morphology, and composition, is essential for the production of fine particles using spray pyrolysis. Many applications necessitate non-agglomerated and spherical particles with a narrow size distribution. One particle-synthesis method—spray pyrolysis (SP)—offers the ability to control the characteristics of the final particles such that they meet specified criteria (CitationLenggoro et al. 2003; CitationKodas 1989; CitationMessing et al. 1993). Generally, SP involves the atomization of a precursor solution into discrete droplets followed by evaporation of the solvent. Many studies have proposed droplet-to-particle formation that is based on the reduction of droplet size due to evaporation of the solvent (CitationXiong and Kodas 1993; CitationLenggoro et al. 2003). However, the formation of large and non-spherical particles that have a broad and bimodal size distribution due to droplet coagulation remains a limitation.
Compared with atmospheric spray pyrolysis, low-pressure spray pyrolysis (LPSP) has a unique capability of producing nanoparticles from micron-sized droplets (CitationFisenko et al. 2006). The evaporation of submicron-sized droplets extends nearly to the free molecular regime and determines the mechanism by which nanoparticles form from micron-sized droplets during LPSP, particularly at low pressures of 1.33 × 103−5.33 × 103 Pa (10−40 Torr) (CitationLefebvre 1989). Evaporation behaviors of smaller droplets differ from those of larger droplets because of a higher evaporation rate, less storage of heat energy, and the Kelvin effect. Evaporation for Knudsen number, Kn > 1 corresponds to the evaporation of small droplets, and the processes associated with the droplets occur in non-continuum regimes (CitationEslamian and Ashgriz 2006, CitationQu and Davis 2001). Therefore, this could be the determinant of the particle formation mechanism in LPSP compared with processes of continuum regimes (Kn ≪ 1). This process enables the reduction of droplet coagulation by reducing the number of droplets as pressure is reduced. Nevertheless, droplet-to-particle formation is very complex because many precursor properties and parameters, e.g., melting point, surface tension, evaporation rate, etc., are pressure-dependent (CitationEslamian and Ashgriz 2006; CitationFisenko and Khodyko 2009). The application of low pressure also reduces droplet size due to evaporation of the solvent, during which both heat and mass transfer of the evaporating aerosol droplets play an important role in the formation of small droplets, thereby affecting the final particles. Therefore, it is important to consider droplet-to-particle formation during low-pressure synthesis. A more thorough understanding of this mechanism would allow for the development of better strategies to design and produce fine particles that would allow enhancement of both the efficiency of the process and the properties of the particles that are produced.
The results of our earlier studies strongly suggested that both the droplet characteristics and the ambient conditions were the primary determinants of the characteristics of the final particles. Furthermore, we also demonstrated a reduction in droplet size due to droplet evaporation—so-called evaporative cooling—via both experimental and simulation data, which was confirmed by a reduction in chamber temperature as chamber pressure decreased (CitationOgi et al. 2009; CitationFisenko et al. 2006; CitationFisenko and Khodyko 2009). However, direct measurement of the characteristics of the sprayed droplets remained infeasible because of the difficulties associated with the low-pressure experimental system. Direct measurement of droplet size distribution provides direct evidence for a reduction in droplet size as pressure is reduced, which is important for clarification of droplet-to-particle formation via LPSP. For this purpose, in the present study we measured the size distributions of both precursor droplets generated using a TFN and the synthesized zinc oxide particles, because their physicochemical aspects are well known. The measurements were conducted under reduced pressures and comparisons were made with the final produced particles. In addition, a simulation-based approach was used to validate the experimental results.
The objectives of the present study were as follows: to measure the droplet size distributions generated by a two-fluid nozzle using a laser diffraction method; and, to compare the size distributions of LPSP-synthesized zinc oxide particles to systematically investigate the droplet-to-particle formation of zinc oxide under reduced pressures using both experimental and simulation-derived data. Herein, we show that the droplet-to-particle formation of zinc oxide under reduced pressure is consistent with that of zirconia at atmospheric pressure (CitationWang et al. 2008) and provides additional evidence for, and a more in-depth explanation of, the formation of metal oxides in general.
2. EXPERIMENTAL DETAILS
2.1. Droplet Generation and Measurement
The system that was used for generation and measurement of the sprayed droplets is shown in . It was comprised of an atomizer and a droplet-measurement system. The atomizer system consisted of a sprayer, a measurement chamber with an inner diameter of 3.78 × 10−2 m (Figure S1), and a heater. The droplets were generated by a TFN (BIMV-4502 series, Ikeuchi Co. Ltd.), which is an internal-mixing-type of atomizer. The nozzle pattern was a flat-spray-type with a spray angle of 45°. The temperature of the atomizer chamber was maintained at 303 K by means of a controlled heater. A high-pressure air cylinder tank supplied the dry air as the atomizing gas, which was equipped with a pressure regulator (type 650NE, Tanaka Engineering Works, Ltd., Japan). The air flow rate was controlled at a predetermined value using a rotameter (Kofloc), which is a variable-flow meter. In this way, the atomizing-gas pressure and flow rate of atomizing gas could be independently controlled.
FIG. 1 Experimental setup for (a) droplet measurement and (b) particle synthesis under low-pressure conditions.
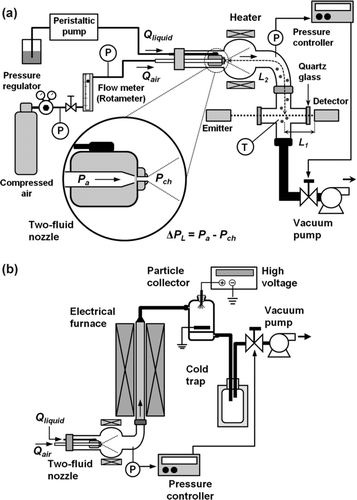
Initially, to the investigate the effect of ambient pressure on droplet size distribution, the differential atomizing pressure Δ P L of the TFN was varied by two methods as follows: (1) varying the air pressure P a and fixing the chamber P ch at atmospheric pressure; and (2) fixing the air pressure P a and varying the chamber pressure P ch . To investigate the factors that affect droplet characteristics, two types of solution were selected as the precursors. First, pure water was chosen to investigate its effect on the spray droplet characteristics. Second, a zinc acetate solution was selected as the precursor for synthesis of zinc oxide particles to investigate droplet-to-particle formation via LPSP.
The droplet measurement system consisted of a laser-diffraction-based spray particle analyzer (Spraytech, Malvern Instruments Ltd., Malvern, U.K.) that used a Ne-laser with a wavelength and a beam diameter of 670 nm and 1.0 × 10−2 m, respectively. The lens, which was 100 mm in size, was able to measure droplets ranging from 0.1 to 230 μ m. The distances between the measured droplets and the laser detector (L1) and the TFN dip and laser beam (L2) were held constant at 7.0 × 10−2 and 3.0 × 10−1 m, respectively. The temperature of the measured-spray was monitored using a thermocouple placed in the measuring chamber about 1.0 × 10−2 m below the laser beam.
The measurements were carried out in a dark room to eliminate electromagnetic noise that might originate from the environment. The pressure controller system, which was comprised of a pressure sensor, an Adaptive Pressure Controller (ACX2200, Nihon Mykrolis, Tokyo) and a vacuum pump, precisely maintained the chamber pressure at a predetermined value. The metal measuring chamber was equipped with quartz glasses that each had a transmittance of 99%. The quartz glasses were attached to the chamber at the entry and exit of the laser measurement path. The flow of the droplets was perpendicular to the laser beam.
2.2. Physicochemical Measurement of Liquid
The physicochemical properties of a liquid determine the characteristics of both the generated droplets and synthesized particles. The viscosity, η, and surface tension, γ, of the liquid precursor were measured by means of a viscometer, a programmable rheometer (DV-III Ultra, Brookfield Engineering Labs, Middleboro, MA), and a surface tensiometer (CBVP-Z, Kyowa Interface Science Co., Ltd., Saitama, Japan), respectively. summarizes the physicochemical properties of the precursor liquid measured at 293 K.
TABLE 1 Physicochemical properties of liquid at 293 K
2.3. Particle Synthesis
shows a schematic diagram of the particle synthesis via LPSP using a vertically positioned electrical furnace 8 × 10−1 m in length and with an inner diameter of 2.5 × 10−2 m. The reactor temperature was varied from 1073–1473 K. The liquid precursor was fed into the atomizer using a peristaltic pump and dry air was used as the atomizing gas. The synthesized particles were collected using an electric precipitator operated at 423 K to prevent condensation of water vapor. A cold trap system condensed the water vapor that was produced during the process. The air pressure was held constant at 2 × 105 Pa, while the chamber pressure was varied: 5.33 × 103, 8.00 × 103, 1.33 × 104, 4.00 × 104, or 9.87 × 104 Pa.
2.4. Particle Characterization
The size and morphology of the synthesized particles were analyzed using a field emission scanning electron microscope (FE-SEM, S-5000, Hitachi Corp., Tokyo, Japan) operated at 20 kV. The mean and standard deviation of the prepared particle size were expressed as the geometric mean diameter (GMD, d p ) and the geometric standard deviation (GSD, σ p ), respectively, which were calculated using the equations log d p = ∑nlog d/∑ n, and log σ = {∑[n(log d − log d p )2]/∑ n}1/2, respectively, where d was the size of approximately 1000 randomly sampled particles in the corresponding FE-SEM images. The crystallinity of the synthesized particles was analyzed using powder X-ray diffraction (XRD, RINT 2200 V, Rigaku Denki, Tokyo, Japan) with nickel-filtered Cu Kα radiation (wavelength, λ = 1.504 Å), an operating voltage of 40 kV, a scan step of 0.02°, and a scan speed of 6.67 × 10−2 °/s. The Material Analysis Using Diffraction (MAUD) program was used for Rietveld refinement of the XRD patterns for phase identification of the synthesized particles. The crystal structure of the particles was analyzed using a field emission transmission electron microscope (FE-TEM; JEM - 3000F, JEOL, Tokyo, Japan) operated at 300 kV. Furthermore, the crystallinity of the particles was analyzed using selected area electron diffraction (SAED). The chemical composition was determined using scanning transmission electron microscopy (STEM).
3. RESULTS AND DISCUSSION
3.1. Measurement of Droplet Size Distributions
3.1.1. Effect of Atomizing Pressure Differential
Both the air injection pressure and the ambient pressure play an important role in the formation of sprayed droplets. Lefebvre (1989) showed that the effects of the atomizing pressure differential and the liquid flow rate on droplet size can be described by the following equation:
In the present study, to investigate the effect of the chamber pressure on the droplet characteristics, the atomizing pressure differential of the atomizer was increased as follows: 1.01 × 105, 1.60 × 105, 1.87 × 105, 1.92 × 105, and 1.96 × 105 Pa. compares the size distributions of water droplets generated under an atomizing pressure differential that was created by one of two methods: (1) varying the injection air pressure, while holding the chamber pressure constant at 9.87 × 104 Pa; or, (2) fixing the injection air pressure at 2.00 × 105 Pa, while reducing the chamber pressure. At equivalent atomizing pressure differentials, the size distribution of the droplets generated at atmospheric pressure (a fixed chamber pressure of 9.87 × 104 Pa) was bimodal and broad (). As the atomizing pressure differential was increased, the size distribution remained bimodal, but the peak decreased slightly from 6.07 to 5.39 μ m. Moreover, the distributions became narrower, as indicated by the decrease in the span of values from 2.16 to 1.72. By contrast, varying the atomizing pressure differential by decreasing the chamber pressure at a fixed air pressure of 2.00 × 105 Pa resulted in a significant decrease in peak droplet size from 5.94 to 4.47 μ m (). This result is consistent with our previous investigation of the size distribution of ultrasonic-atomized droplets at atmospheric pressure (CitationWang et al. 2008). Herein, we found that a reduction in ambient pressure was associated with a shift from bimodal to monodispersed size distributions. In addition, a decrease in span values from 1.39 to 0.27 indicated the formation of monodispersed distributions. compares the decrease in droplet size, expressed as volumetric diameter, at 50% (d v,50), and verifies the increase in specific surface area (SSA) as the droplet size decreased (inset of ). The notable feature of the results is the significant improvement in the monodispersity of droplet size distributions at low atomization-chamber-pressures compared with the results shown in and . As also noted in Equation (Equation1), droplet sizes decreased with a reduction in chamber pressure.
FIG. 2 Size distributions and chamber temperatures of pure water droplets generated at various atomizing pressure differentials, Δ P L , that equal 1.01 × 105, 1.60 × 105, 1.87 × 105, 1.92 × 105, and 1.96 × 105 Pa. Variation in Δ P L was achieved by (a) varying air pressure, P a , at a fixed-chamber pressure, P ch , of 9.87 × 105 Pa, or (b) by fixing P a at 2.00 × 105 Pa and decreasing P ch .
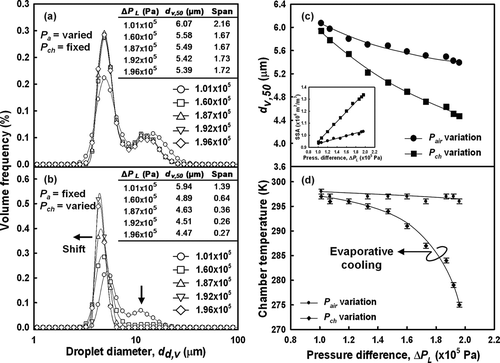
As implicitly noted in Equations (S1)−(S5) in the supplemental information, droplets exhibit greater variation in diameter at lower chamber pressures and show temperature variation during vaporization. The models show that the rate of droplet evaporation is pressure-dependent. The experimental results () indicate that at equivalent atomizing pressure differentials, the droplets generated at low pressure were remarkably smaller than those synthesized at atmospheric pressure. Hence, these results provide evidence that the decrease in droplet size originated from droplet evaporation as pressure was reduced.
In addition to droplet evaporation, droplet loss from impaction in the transport tubing was considered in the reduction of larger droplets. The decrease in chamber pressure, while maintaining the flow rate, increased the velocity of generated droplets, which consequently shortened the residence time, as noted in Equation (S7) (supplemental information). This resulted in increased droplet loss from inertial deposition in the bend, contraction and enlargement of the transport tube as the sprayed droplets flowed through. Figure S1 shows the droplet loss, as calculated using a Particle Loss Calculator, which is a software package developed by von der CitationWeiden et al. (2009), as they flowed through the transport tubing to the measurement area. Droplets with sizes of 8–10 μ m experienced approximately 15% loss at a carrier gas flow rate of 1.67 × 10−4 m3/s.
The reduction in droplet size due to higher droplet evaporation at lower chamber pressures was also confirmed by the evaporative cooling of droplets, as described in the droplet modeling section (see supplemental information). As shown in , the temperature of the spray chamber was relatively constant (298−296 K) while the atomizing pressure differential was increased at atmospheric ambient pressure. By contrast, when the ambient pressure was reduced to 4.00 × 103 Pa from 9.87 × 104 Pa, the ambient temperature declined significantly from 293 to 274 K (with an σ of 0.5, temperature drop ca. 22 K, σ of 0.5 compared with that of atmospheric pressure). The temperature drop that occurred at low pressure provides clear evidence that the generated droplets underwent evaporative cooling. The temperature drop along with the decrease in size distribution provides strong support for the formation of smaller droplets with narrow and monodispersed size distributions due to droplet evaporation.
Equation (S5) was derived from the energy balance as latent heat was required for evaporation and was applied so that the temperature change could be calculated. The simulation results shown in , applying Equation (S5), shows that temperature declined as pressure was reduced. Previous results showed that droplets instantaneously evaporated at a distance of about 3.0 × 103 times the droplet radius (CitationFisenko et al. 2006). For a droplet size of 10 μ m, evaporation occurs at a distance of 15 × 10−3 m from the atomizer. Particularly in the LPSP reactor, droplets evaporated at a distance of 1.6 × 10−2− 2.8 × 10−2 m from the TFN tip, as reported in our previous work (CitationWidiyastuti et al. 2010). The temperature drop indicated higher droplet evaporation. These results demonstrate that ambient pressure controlled droplet evaporation and determined the characteristics of the generated droplets. When droplets evaporate, they experience heat loss due to the latent heat required for evaporation. As a result, their temperature is decreased and droplet cooling due to evaporation takes place. In general, the results shown in illustrate how the chamber pressure controls the monodispersity of droplet size distributions. These results are supported by the theoretical approach shown in , which compares the experimental and simulation-based results regarding the pressure-dependence of chamber temperature and droplet size. The results of the simulation show that the chamber temperature decreased as the pressure was reduced. At low chamber pressures, the simulation results showed a decrease in temperature, which was consistent with the experimental results. These results confirm that the decrease in both temperature and droplet size are due to evaporative cooling of the evaporated droplets.
FIG. 3 Comparison of experimental and simulation-based results for chamber temperature and droplet size at reduced pressures.
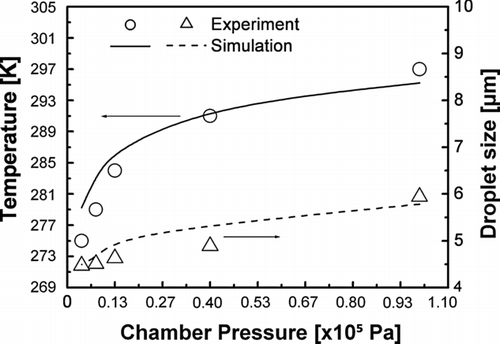
The driving force for evaporation is the difference in concentration of the droplet vapor between the droplet surface and the free stream (water vapor in the surrounding gas). Water vapor concentration is determined by the partial pressure of the vapor. As the pressure chamber is reduced from atmospheric to low pressure, the concentration of water vapor in free stream is decreased (CitationFisenko and Khodyko 2009; CitationFisenko et al. 2006). This increases the evaporation rate of droplets and results in the formation of smaller droplets and a reduction in droplet temperature, as noted in Equations (S1)–(S5). Thus, droplets experience a smaller evaporation rate at atmospheric pressure than that at reduced pressure.
3.1.2. Effect of Carrier Gas Flow Rate
CitationSakai et al. (1978) investigated the effects of the carrier gas- and liquid-flow rates on the atomization of water using air as the atomizing gas and derived the Sauter Mean Diameter (SMD), d 32, of sprayed droplet as follows:
shows the droplet size distributions with increasing carrier gas flow rates of 1.33 × 10−4, 1.50 × 10−4 and 1.67 × 10−4 m3/s. As the carrier gas flow rate was increased, the distribution peak shifted from 6.74 μ m (σ of 0.04) to 5.94 (σ of 0.03) μ m, indicating a decrease in droplet size (). It is important to note that at equivalent chamber pressures, an increase in the air flow rate resulted in smaller droplets with more uniform size distributions (indicated by the decrease in span values of 1.44−1.39). In comparison, at a low pressure of 5.33 × 103 Pa, an increase in the carrier gas flow rate decreased droplet size (from 4.77 to 4.50 μ m) and increased the uniformity of the size distributions with span values of 0.42−0.26 (). Similar results were found at all reduced chamber pressures, as shown in . Thus, these results show that droplet size decreased at higher carrier gas flow rates. The formation of smaller droplets at higher air flow rates was confirmed by the SSA data. The results of show that the SSA of the droplets increased with the carrier gas flow rate, which confirms the formation of smaller droplets. As described by Equation (Equation2), mean droplet size is inversely proportional to the carrier gas flow rate. Thus, these results demonstrate that the carrier gas flow rate influenced the size of the generated droplets.
FIG. 4 Droplet size distribution of water at various carrier gas flow rates at (a) atmospheric pressure or (b) low pressure, and comparison of (c) volumetric mean diameter and (d) specific surface area of generated droplets.
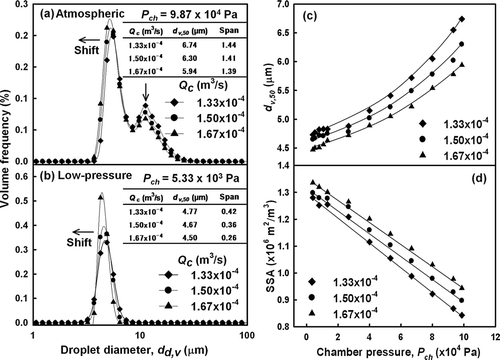
The kinetic energy of the atomizing air and the energy difference between the inlet air and the emerging spray are the primary determinants of mean droplet size (CitationLefebvre 1989). Accordingly, use of higher gas flow rates increases both the kinetic energy of atomization and the energy difference of atomization. In addition, increasing the carrier gas flow rate while maintaining a constant liquid flow rate results in a greater liquid-air ratio, which improves atomization quality (CitationLiu 2000). Thus, in the present study, the kinetic energy of atomization was increased at higher carrier gas flow rates. As a result, smaller droplets with enhanced monodispersity were obtained.
The energy, E, requirement for atomizing unit liquid mass, m l , is given by (CitationLiu 2000)
Moreover, droplet size increased with the air-to-liquid ratio (CitationHede et al. 2008; CitationLefebvre 1989). Thus, an increase in carrier gas flow rate while maintaining the liquid flow rate increased the air-to-liquid ratio and atomization kinetic energy consequently increased the air velocity. Measurement results in show that increasing the carrier gas flow rate resulted in a smaller droplet size. Equation (Equation3) indicates that with higher atomization energy, more liquid mass can be atomized resulting in a higher concentration of droplets. As shown in , at both atmospheric and low pressures, the concentration numbers of droplets increased with an increase in carrier gas flow rate.
TABLE 2 Comparison of number concentration of water droplet generated at various operating parameters
Figure S2 shows the transmission efficiency at various carrier gas flow rates. The sampled efficiency decreased with carrier gas flow rates. Larger droplets exhibited a smaller sampling efficiency compared with smaller droplets indicating that impaction loss of larger droplets was higher as carrier gas flow rate increased. This result verified the shift of size distribution and large droplet reduction, as shown in .
3.1.3. Effect of Liquid Flow Rate
A high particle-production rate is required for industrial application of a process. For that reason, higher liquid-precursor flow rates are preferable. Hence, the effects of higher liquid flow rates on the generated droplets were investigated. As described in both Equations (Equation1) and (2), the liquid flow rate has a direct effect on droplet size. That is, an increase in the liquid flow rate corresponds to an increase in the mean droplet size. Other studies have reported that mean droplet size increases at higher liquid flow rates (CitationWang et al. 2008). shows the effect of the liquid flow rate on the droplet size distribution, while maintaining a constant low ambient pressure, and shows that droplet size increased with liquid flow rate. At higher ambient pressures, particularly at atmospheric chamber pressure (9.87 × 104 Pa), larger droplets (5.39−5.88 μ m) were obtained as the liquid flow rate was increased (). A bimodal droplet size distribution was observed with an increase in span values (1.64−1.91), despite the increased liquid flow rate. By comparison, at a lower chamber pressure of 8.00 × 103 Pa, the formation of a monodispersed distribution with span values of 0.57−0.67 was observed, as shown in . The variation in the liquid flow rate had a negligible effect on droplet size (4.72−4.77 μ m). shows the correlations between droplet size and liquid flow rate at various chamber pressures. These results demonstrate that at lower ambient pressures and a constant carrier gas flow rate, the liquid flow rate has a smaller effect on droplet size. Thus, these results suggest that the application of low pressure is beneficial because it allows the use of higher flow rates, which are required to enhance productivity, with no significant alteration in the droplet characteristics. As noted in Equation (Equation2), use of higher liquid flow rates decreases the air-liquid ratio, which results in the generation of larger droplets. Higher liquid flow rates require more kinetic energy for atomization and, thus, larger droplets are generated due to inadequate kinetic energy of the atomizing air.
3.1.4. Effect of Solution Concentration
Many studies have reported that the concentration of the precursor solution determines the characteristics of the resultant fine particles. CitationCho et al. (2009) demonstrated that solution concentration determined the average size of the particles. Furthermore, the use of high-concentration precursor solution is preferable as it enhances particle production such that it is industrially applicable. To investigate the effects of concentration on the characteristics of the generated droplets, zinc acetate solutions at various concentrations were used as the precursors. Instead of pure water, zinc acetate solutions were used to generate droplets and to synthesize solid particles under reduced pressure conditions. shows the size distributions of zinc acetate droplets generated from solutions of various concentrations. As shown in , the size distributions of the zinc acetate droplets generated at atmospheric pressure tended to decrease (5.58−5.01 μ m) when higher concentrations were applied. It is interesting to note that at higher precursor concentrations the monodispersity of the distributions decreased, as evidenced by the higher span values (1.73−1.96). To explain this result, a subsequent investigation was carried out at reduced pressure. shows that a similar result was obtained when a reduced chamber pressure of 5.33 × 103 Pa was applied. Likewise, the droplet size decreased from 4.36−4.15 μ m and broader size distributions were found (0.32−0.34) when higher concentrations were used. In addition, when the chamber pressure was reduced from atmospheric pressure to a lower pressure, the size distribution shifted from a bimodal to a monodispersed distribution. In summary, the effects of concentration were similar at pressures equal to or less than atmospheric pressure (). The volumetric mean droplet diameter decreased at higher concentrations. Thus, the use of more highly concentrated solutions resulted in smaller droplets with a reduction in the monodispersity of the droplet size distributions.
FIG. 6 Size distribution of droplets generated from various concentrations of zinc acetate solution at (a) atmospheric pressures or (b) low pressure, and (c) volumetric mean diameter as a function of pressure at various precursor concentrations.
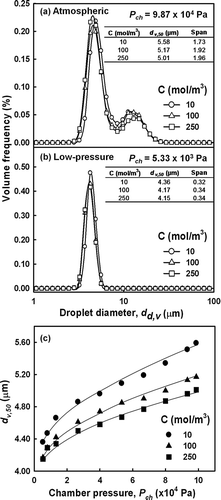
The effect of the precursor solution concentration on droplet size can be explained by considering the physicochemical properties of the liquid precursors. The important liquid properties that affect atomization via a two-fluid nozzle are viscosity, density and surface tension (CitationLiu 2000; CitationHede et al. 2008). An increase in surface tension typically increases the mean droplet size, ∝ γ a , where a may have values of 0.19 and 0.25. Similarly, mean droplet size increases with surface tension in relation to mean droplet size, ∝ μ b , where b values may vary 0.16, 0.20, 0.118, 0.16, 0.06, and 0.215 (CitationLefebvre 1989). As reported in our previous study of atmospheric ultrasonic atomization, higher viscosity results in coarser atomization, but has a negligible effect on droplet size (CitationWang et al. 2008). As summarized in , the more concentrated solutions had greater viscosities, which was associated with a decrease in droplet size (). In addition, a decrease in surface tension was correlated with a decrease in droplet size. Therefore, surface tension was considered the primary determinant of droplet size that is responsible for droplet break-up. At higher concentrations, the surface tension was reduced, which resulted in the formation of smaller droplets. The role of surface tension in the break-up of droplets during atomization of a liquid is described in Equation (Equation4) (CitationLefebvre 1989):
To confirm the formation of smaller droplets at higher concentrations, the number concentration of the generated droplets was calculated, and the derived results are summarized in . Parameters that represent the monodispersity of the distribution (d v,50 and span) are summarized in as well. At both atmospheric and reduced pressure, droplets with a higher number concentration formed as the solution concentration increased. These results indicate the formation of smaller droplets that occurs with increased solution concentration is due to a lower surface tension.
As discussed above, monodispersed or nearly monodispersed sprays are desirable for the production of fine particles. However, collision between droplets within the spray can cause droplet coagulation and reduces the monodispersity of the generated droplets. The probability of uniform droplets coagulating to create doublets or triplets is greater in a dense or turbulent spray. This problem may be avoided by use of the appropriate dispersion air around the spray (CitationLiu 2000). Droplet size, relative velocity, and collision angle determine if collisions between droplets will lead to droplet coagulation. CitationMessing et al. (1993) reported that droplet coagulation is insensitive to temperature, but is strongly dependent on the initial number concentration of the droplets, such that higher initial droplet concentrations accelerate droplet coagulation. Thus, the initial number concentration of the droplets is the primary determinant of droplet coagulation. Hence, coagulation is most likely to occur in high-concentration sprays (CitationLefebvre 1989; CitationLiu 2000; CitationLee et al. 1979; CitationKim 2003). The change in monodispersity of droplet size distributions due to variation in droplet concentration can be used as an indicator of droplet coagulation. The present study investigated the effect of chamber pressure on droplet coagulation.
The concentration numbers of droplets experiencing Brownian and turbulent coagulation can be expressed as follows (CitationOkuyama et al. 1978):
The first term on the right-hand side is the turbulent coagulation rate as a function of the power of three for droplet size. Thus, turbulent coagulation was considered to be dominant compared with Brownian coagulation for large droplet sizes of ca. 4−10 μ m (CitationOkuyama et al. 1978). Due to the complexity of flow and measurement in a vacuum system, droplet coagulation under reduced pressure will be left for future work. The above equations state that the period of time and the initial concentration determines the final concentration due to coagulation. As a result of a longer coagulation time, a longer residence time equates to a smaller concentration number of droplets. This affects the size distributions of measured aerosol. As noted in Equation (S7), the residence time is shorter due to higher velocity as chamber pressure is reduced.
As summarized in , the concentration numbers of droplets generated at atmospheric pressure was approximately one order of magnitude greater than that of droplets generated at low pressure (1012 compared with 1011 droplets/m3). In addition, the volumetric mean droplet diameter (d v,50) and span values of the size distributions were markedly reduced at lower pressures. Consequently, droplet coagulation due to collision was more likely to occur at atmospheric pressure, thereby creating larger droplets. Thus, the lower chamber pressure generated droplets with a lower number concentration and reduced droplet coagulation. As a result, monodispersed distributions formed at low chamber pressures.
3.2. Particle Synthesis
3.2.1. Effect of Ambient Pressure
During our investigation of the droplet-to-particle formation of zinc oxide, the corresponding zinc acetate precursors were synthesized via LPSP, and the size and morphology of resulting particles were then measured and calculated. Measurement conditions were similar to those used for droplet measurement. shows the size and morphology of particles synthesized by LPSP at pressures of 5.33 × 103 – 9.87 × 104 Pa and at a constant operating temperature (1073 K) and liquid concentration (250 mol/m3). At 9.87 × 104 Pa, large crinkled particles formed, while at 4.00 × 104 Pa, smaller particles, some of which were crinkled, formed to create a bimodal size distribution (). At the ambient pressure of 1.33 × 104 Pa, 8-nm nanoparticles formed, as shown in . The particles had a uniform size distribution with a geometric standard deviation, δ, of 1.32. At a lower ambient pressure of 5.33 × 103 Pa, the size of synthesized particles remained unchanged at 8 nm with a uniform size distribution, δ, of 1.28 (). The evolution of droplet and particle size as a function of chamber pressure is shown in Table S1 (in supplemental information). These results demonstrate that use of reduced pressures results in smaller particles with narrow distributions and in the formation of fewer large particles. This result is similar to that obtained for the measurement of droplet size distributions. Thus, a reduction in ambient pressure results in the synthesis of smaller particles and in the formation of monodispersed size distributions.
FIG. 7 Size and morphology of particles synthesized at (a) 9.87 × 104, (b) 4.00 × 104, (c) 1.33 × 104, or (d) 5.33 × 103 Pa at a constant temperature (1073 K) and concentration (250 mol/m3).
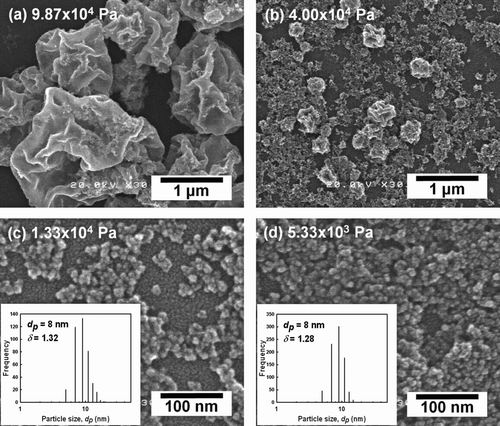
In the production of fine particles, particle crystallinity is an important determinant of the properties of the produced particles. In addition to a fine size and morphology, full single crystalline nanoparticles are desirable. shows XRD patterns of the synthesized ZnO particles. The synthesized particles follow JCPDS 79-0207, which indicates the formation of ZnO with a wurtzite crystal structure. As the ambient pressure was reduced to 9.87 × 104, 4.00 × 104, 1.33 × 104, and 5.33 × 103 Pa, the crystallite size decreased to 16, 6, 6, and 5 nm, as indicated by a broadening of the measured XRD peaks, corresponding to the droplet sizes of 5.01, 4.58, 4.34, and 4.15 μ m, respectively. Particularly at pressures of 1.33 × 104 and 5.33 × 103 Pa, synthesized particle sizes were 8 nm (), indicating an evolution from micron-sized droplets to single crystalline nanoparticles (crystallite sizes 6 and 5 nm), which originated from the higher droplet evaporation rate.
FIG. 8 XRD patterns of zinc oxide particles synthesized at (a) 9.87 × 104, (b) 4.00 × 104, (c) 1.33 × 104, or (d) 5.33 × 103 Pa at a constant temperature (1073 K) and concentration (250 mol/m3).
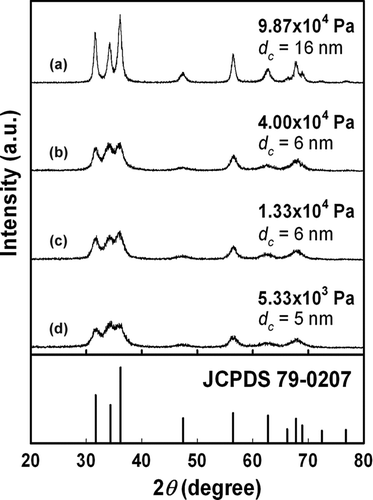
These results verified the formation of smaller particles, as illustrated by the SEM images in . Thus, the crystallite sizes closely corresponded to the particle size, which indicates the formation of single crystalline ZnO. As demonstrated in our previous reports, droplet evaporation is considered as the key factor in the formation of nanoparticles by LPSP based on the assumption that the rate of solvent evaporation in the droplet is much higher than the solute precipitation rate (CitationLenggoro et al. 2003). At constant temperature and carrier gas flow rates, low pressure results in greater rates of evaporation than high pressure, which allows the solute crystal to grow more rapidly. Thus, in the present study, low-pressure droplet evaporation resulted in smaller nanoparticles with smaller crystallite sizes (). The size evolution from micron-sized droplets to nanoparticles, as shown in droplet size distribution (), SEM images (), and crystallite size of synthesized particles (), indicated the ability of LPSP to produce nanoparticles from micron-sized droplets via droplet evaporation.
To more thoroughly investigate the effects of pressure on the crystallinity of the synthesized particles, the particle interior was also analyzed. The apparent crystallinity of the synthesized particles at various pressures was evaluated by the TEM, HR-TEM and SAED images shown in . The formation of smaller and more uniform particle size distributions was evident as the pressure was reduced from 9.87 × 104 – 5.33 × 103 Pa (, , and ). The surface of a particle produced at 9.87 × 104 Pa showed a larger crystallite size () and lattice fringes of (100) were detected. Along with the XRD patterns, this result confirmed the formation of large particles when atmospheric pressure was applied. Smaller crystallite sizes were evident at lower operating pressures of 1.33 × 104 and 5.33 × 103 Pa, which provided strong evidence for the formation of smaller particles ( and ) with predominant lattice fringes of (100). These HR-TEM images suggest the formation of single crystalline particles at reduced pressures of 1.33 × 104 and 5.33 × 103 Pa, as indicated by the SEM and XRD measurements. The SAED patterns showed many diffraction rings, which indicated that the synthesized particles were comprised of crystals with various lattice orientations (insets of ).
3.2.2. Effect of Operating Temperature
We previously reported that the operating temperature determines the characteristics of particles produced by LPSP. Control of both particle size and crystallinity was possible by manipulation of the operating temperature. Compared with the result shown in , synthesis at 4.00 × 104 Pa and 1073 K resulted in the formation of large particles with a bimodal size distribution. CitationWidiyastuti et al. (2009) demonstrated the formation of bimodal to unimodal size distributions of silica due to solid particle evaporation at high reactor temperatures. To investigate the effect of temperature on the synthesized particles, reactor temperatures as high as 1273 and 1473 K were applied (). At 1273 K, nearly spherical nanoparticles with a uniform distribution formed (). Compared with particles synthesized at 1073 K, the particles were larger and more uniform in size (d p of 17 nm, δ of 1.12), as shown by the size distributions in . When the temperature was increased to 1473 K, the synthesized-particle size increased slightly (d p = 23 nm, δ = 1.19) with formation of uniform distributions and no change in morphology ().
FIG. 10 SEM images and size distributions of zinc oxide particles synthesized at (a) and (c) 1273 K, (b) and (d) 1473 K at a constant pressure (4.00 × 104 Pa) and concentration (250 mol/m3). XRD patterns (e).
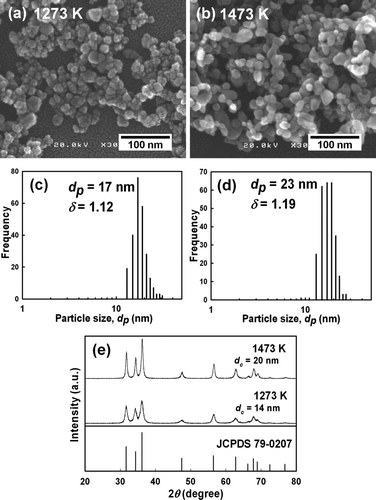
The shift in peak distributions shown in confirmed the formation of slightly larger particles. The XRD patterns also confirmed the formation of larger crystallite sizes as the reactor temperature was increased. The crystallite sizes were 14 and 20 nm at operating temperatures of 1273 and 1473 K, respectively (). These results strongly suggest that the shift from a bimodal to unimodal distribution occurred due to evaporation of the synthesized particles at higher reactor temperatures. As summarized in Table S3, the initial droplets (4.89 μ m) evolved into nanoparticles that were 17 or 23 nm in diameter as the operating temperature was increased (at pressure of 4.00 × 104 Pa).
4. CONCLUSIONS
The effects of operating parameters, i.e., atomizing pressure differential, carrier gas- and liquid- flow rates, liquid concentration, and chamber pressure, on the droplet size distributions were investigated via experimental and simulation-based data. Low-pressure synthesis of zinc oxide nanoparticles via LPSP at various temperatures was demonstrated. The shift in droplet sizes from a bimodal to a monodispersed distribution was determined to be an effect of an increase in the droplet evaporation rate due to a reduction in operating pressure. An increase in the pyrolysis temperature resulted in larger particles. The formation of single crystalline zinc oxide nanoparticles was attributed to the formation of smaller droplets that resulted from enhanced droplet evaporation at lower pressures. We concluded that pressure is the primary determinant of both droplet and particle size during LPSP.
Supplemental File.zip
Download Zip (197.1 KB)Acknowledgments
We thank Dr. Eishi Tanabe (Hiroshima Prefectural Institute of Industrial Science and Technology) for his assistance with the TEM and Dr. Wei-Ning Wang (Washington University, St. Louis, Missouri, USA) for assistance with the measurement equipment. We also acknowledge the Ministry of Education, Culture, Sports, Science and Technology of Japan for providing a doctoral scholarship (D.H).
[Supplementary materials are available for this article. Go to the publisher's online edition of Aerosol Science and Technology to view the free supplementary files.]
REFERENCES
- Cho , K. , Chang , H. , Kil , D. S. , Park , J. , Jang , H. D. and Sohn , H. Y. 2009 . Mechanisms of the Formation of Silica Particles from Precursors with Different Volatilities by Flame Spray Pyrolysis . Aerosol Sci. Technol. , 43 : 911 – 920 .
- Eslamian , M. and Ashgriz , N. 2006 . Effect of Precursor, Ambient Pressure, and Temperature on the Morphology, Crystallinity, and Decomposition of Powders Prepared by Spray Pyrolysis and Drying . Powder Technol. , 167 : 149 – 159 .
- Fisenko , S. P. and Khodyko , J. A. 2009 . Low Pressure Evaporative Cooling of Micron-Sized Droplets of Solutions and its Novel Applications . Int. J. Heat Mass Transfer , 52 : 3842 – 3849 .
- Fisenko , S. P. , Wang , W. N. , Lenggoro , I. W. and Okuyama , K. 2006 . Evaporative Cooling of Micron-Sized Droplets in a Low-Pressure Aerosol Reactor . Chem. Eng. Sci. , 61 : 6029 – 6034 .
- Hede , P. T. , Bach , P. and Jensen , A. D. 2008 . Two-fluid Spray Atomization and Pneumatic Nozzles for Fluid Bed Coating/Agglomeration Purposes: A Review . Chem. Eng. Sci. , 63 : 3821 – 3842 .
- Kim , H. and Sung , N. 2003 . The Effect of Ambient Pressure on the Evaporation of a Single Droplet and a Spray . Combust. Flame , 135 : 261 – 270 .
- Kodas , T. T. 1989 . Generation of Complex Metal Oxides by Aerosol Processes: Superconducting Ceramic Particles and Films . Adv. Mat. , 6 : 180 – 192 .
- Lee , K. W. , Putnam , A. A. , Gieseke , J. A. , Golovin , M. N. and Hale , J. A. 1979 . Spray Nozzle Designs for Agricultural Aviation Applications NASA-CR-159702
- Lefebvre , A. H. 1989 . Atomization and Sprays , Hemisphere publishing corporation .
- Lenggoro , I. W. , Itoh , Y. , Iida , N. and Okuyama , K. 2003 . Control of Size and Morphology in NiO Particles Prepared by a Low-Pressure Spray Pyrolysis . Mater. Res. Bull. , 38 : 1819 – 1827 .
- Liu , H. 2000 . Science and Engineering of Droplets , New York : William Andrew Publishing .
- Messing , G. L. , Zhang , S. C. and Jayanthi , G. V. 1993 . Ceramic Powder Synthesis by Spray Pyrolysis . J. Am. Ceram. Soc. , 76 : 2707 – 2726 .
- Ogi , T. , Hidayat , D. , Iskandar , F. , Purwanto , A. and Okuyama , K. 2009 . Direct Synthesis of Highly Crystalline Transparent Conducting Oxide Nanoparticles by Low Pressure Spray Pyrolysis . Adv. Powder Technol. , 20 : 203 – 209 .
- Okuyama , K. , Kousaka , Y. and Yoshida , T. 1978 . Turbulent Coagulation of Aerosol in a Pipe Flow . J. Aerosol Sci. , 9 : 399 – 410 .
- Qu , X. and Davis , E. J. 2001 . Droplet evaporation and condensation in the near-continuum regime . J. Aerosol Sci. , 32 : 861 – 875 .
- Sakai , T. , Kito , M. , Saito , M. and Kanbe , T. Characteristics of Internal Mixing Twin-Fluid Atomizer . Proceedings of the 1st International Conference on Liquid Atomization and Sprays . Tokyo . pp. 235 – 241 .
- Wang , W. N. , Purwanto , A. , Lenggoro , I. W. , Okuyama , K. , Chang , H. and Jang , H. D. 2008 . Investigation on the Correlations between Droplet and Particle Size Distribution in Ultrasonic Spray Pyrolysis . Ind. Eng. Chem. Res. , 47 : 1650 – 1659 .
- Weiden , S.-L. , Drewnick , F. and Borrman , S. 2009 . Particle Loss Calculator – A New Software Tool for the Assessment of the Performance of Aerosol Inlet Systems . Atmos. Meas. Tech. , 2 : 479 – 494 .
- Widiyastuti , W. , Balgis , R. , Iskandar , F. and Okuyama , K. 2010 . Nanoparticle Formation in Spray Pyrolysis under Low Pressure Condition . Chem. Eng. Sci. , 65 : 1846 – 1854 .
- Widiyastuti , W. , Purwanto , A. , Wang , W.-N. , Iskandar , F. , Setyawan , H. and Okuyama , K. 2009 . Nanoparticle Formation through Solid-Fed Flame Synthesis: Experiment and Modeling . AIChE J. , 55 : 885 – 895 .
- Xiong , Y. and Kodas , T. T. 1993 . Droplet Evaporation and Solute Precipitation during Spray Pyrolysis . J. Aerosol Sci. , 24 ( 7 ) : 893