Abstract
In order to understand the size distributions of metal nanopowders inside manufacturing equipment operated at elevated pressures, a scanning mobility particle sizer is used to carry out in-situ measurements of metal nanopowders manufactured by the wire electrical explosion process. A pressure reducer and rotating disk diluter are used for conditioning metal nanopowder samples appropriate for real-time aerosol instruments operated at atmospheric pressure. Based on measurement data collected downstream of the evaporation chamber, the production of metal nanopowders shows good stability and uniformity for a total number concentration of approximately 5 × 107 particles/cm3, and a unimodal size distribution with a mean diameter of approximately 170 nm. Using an aerosol electrometer and two sets of electrostatic classifiers, positively charged particles slightly outnumber negatively charged particles. The performance of the rotating disk diluter is confirmed by comparing the size distributions of metal nanopowders diluted with five different dilution factors, ranging from 235 to 2500. SEM and TEM image analysis indicates that most metal nanopowders manufactured by this process consist of aggregated particles, and their size distributions obtained from SEM images are similar to those measured by the SMPS. The changes in particle size distribution at each stage of the manufacturing process, including the evaporation chamber, trap buffer, cyclone, and mesh filter, are also monitored using the above in-situ monitoring system. The resulting in-situ measurement data can be used for design modifications of equipment, as well as for investigating the sources of nanopowder release to the workplace environment.
1. INTRODUCTION
Metallic nanoparticles exhibit unique properties and characteristics when compared to their corresponding bulk materials. These properties and characteristics include a lower melting point, enhanced catalytic activity, and a quantum effect (Granqvist and Buhrman Citation1976; El-Sayed 2001). Since knowledge of the unique properties of nanoparticles has been rapidly increasing, an extensive amount of scientific effort has been devoted to understanding the dependency of these properties on the size, shape, and crystallinity of the particles. In addition, various synthesis methods for nanoparticles, which can be used to control their physical and chemical characteristics, have been investigated.
One of the more commonly studied techniques is gas-phase synthesis based on aerosol technology. During gas-phase synthesis, the particle formation process begins with nucleation and condensation from a supersaturated vapor in a gas phase. The major advantages of gas-phase synthesis are the comparative ease of upsizing the apparatus to produce large amounts of material, as well as the applicability of measurement techniques for online determination of particle size in the manufactured aerosols. A number of gas-phase methods have been employed for nanoparticle synthesis, including laser ablation (Gaertner and Lydtin Citation1994), microwave plasma synthesis (Brenner et al. Citation1997), spray pyrolysis (Okuyama and Lenggoro Citation2003), and condensation using physical evaporative sources (Jung et al. Citation2006, Citation2007, Citation2008) or chemical precursor flame pyrolysis (Zhu and Pratsinis Citation1997).
FIG. 1 Schematic diagram of the equipment used for manufacturing metal nanopowders via the wire electrical explosion process.
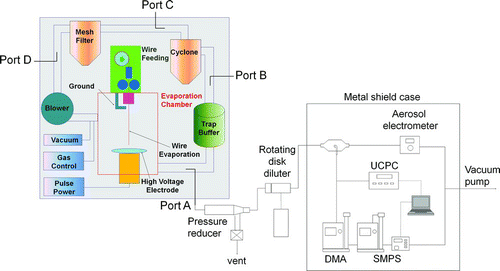
The wire electrical explosion (WEE) method is another gas-phase synthesis method, in which metallic nanoparticles are synthesized by the explosion of a target material wire subjected to a high electric current in an inert atmosphere (Phalen Citation1972). The duration of the WEE process is 1–10 μs at a plasma temperature of ∼104 K (Kwon et al. Citation2004). Most metallic materials including alloys can be reduced to nanoparticles by the WEE method. The size and composition of the nanoparticles can be controlled by the electrical energy entering the wire and the surrounding conditions of pressure and temperature. The WEE method also offers the advantages of high energy efficiency and low production of by-products. The most attractive feature of this technique is its ability to produce a metal nanopowder at a high speed (∼200 g/h per each machine) on an industrial scale (Jiang and Yatsui Citation1998; Ozawa et al. Citation2001). However, nanoparticles created by the WEE method have a broad size distribution, or are agglomerated due to their rapid cooling rate and high evaporation rate. Also, a few microscale particles are occasionally produced, even though most of the particles have sizes <200 nm. These large particles could result from structural or chemical nonhomogeneity in the initial wire material, including drawing defects and uneven composition (Kwon et al. Citation2001).
To monitor particle stability and uniformity, in-situ characterization of nanoparticles produced during a continuous process is considered to be a promising future technique.
In previous research, metallic nanoparticles produced by the WEE process have been characterized by off-line diagnostic analysis of a sample of nanoparticles, using a scanning electron microscope (SEM), a transmission electron microscope (TEM), wide-angle X-ray diffraction (WAXD), normal X-ray diffraction (XRD), or selected-area electron diffraction (SAED) (Wang et al. Citation2001; Kotov Citation2003; Sarathi et al. Citation2007, Citation2009). However, these methods are not applicable for continuous monitoring of nanoparticles during production. In this study, we demonstrate an in-situ characterization method for metal nanopowders manufactured by the WEE process, using a real-time aerosol instrument, namely, a scanning mobility particle sizer (SMPS) with a pressure reducer and a diluter. The relative abundance of positively and negatively charged particles is also investigated, using an aerosol electrometer and two sets of electrostatic classifiers. The results should prove very useful for modifying the components of existing metal nanopowder manufacturing equipment to improve product quality, and also for investigating the possible sources of abnormal nanopowder release to the workplace environment.
2. EXPERIMENTS
2.1. Manufacturing Process for Metal Nanopowders
shows a schematic diagram of the equipment used for manufacturing metal nanopowders via the electrical explosion process, including in-situ monitoring systems at the four different sampling locations chosen for this study. It consists of an evaporation chamber (where the metal wire is evaporated by an electrical energy pulse), a trap buffer (where large particles are trapped by gravity), a cyclone (where coarse powder is excluded via gravity and centrifugal force), a mesh filter (for collecting the nanopowder products), and a blower (which maintains a flow of inert gas, such as nitrogen, as a carrier).
The operating conditions were as follows. A wire made of Cu and Ni alloy (Cu:Ni = 90:10, Dasan Inc., Korea) was used, with a diameter of 0.4 mm and without any special treatment. The possible Fe content of the wire was 1.0–1.8%, with maximum impurities of 0.05% Pb, 1.0% Zn, 0.05% Sn, and 1.0% Mn. The length of the wire used in each process was 83 mm. The feed rate was once per 8 s. The capacitance of the explosion circuit was 6.0 μF. A high-voltage pulse of approximately 25 kV was applied to the high-voltage electrode every 8 s. It was verified that these operating parameters were maintained within a variation of less than 15% during the entire manufacturing period. The pressure of the inert gas inside the manufacturing equipment was sustained at approximately 1.5 bar (i.e., 0.15 MPa) throughout the manufacturing process to minimize the penetration of oxygen from outside. It has been empirically determined that this is within the range of normal operational pressures for the wire electrical explosion process (Kwon et al. Citation2001; Kotov Citation2003; Sarathi et al. Citation2007).
2.2. In-Situ Measurement of Metal Nanopowders
The in-situ measurement of the size distributions and charge levels of metal nanopowders was carried out during the manufacturing process, using real-time aerosol instruments at the sampling ports, as shown in . The sampling ports A, B, C, and D were placed downstream of the evaporation chamber, the trap buffer, the cyclone, and the mesh filter, respectively. The charge levels of the nanopowders was measured only at port A, or downstream of the evaporation chamber. In order to reduce the carrier gas pressure of approximately 1.5 bar to ambient pressure, a pressure reducer (TSI model 7847) was used. This pressure reducer was originally designed at the University of Minnesota to measure particulate contamination in a high-purity compressed gas system with low particle loss (Lee et al. 1993). In their research, the particle penetration of the pressure reducer was greater than 80% for particles smaller than 2 μm, increased slightly when the system gas pressure decreased from 2 bar to 1 bar, and was relatively unaffected by orifice diameters in the range of 0.51–1.27 mm. In the present study, it can therefore be assumed that the particle penetration of the pressure reducer was greater than 80% for particles smaller than 2 μm, since the gas pressure was sustained at approximately 1.5 bar, and an orifice with a diameter of 1.0 mm was used. In order to maintain the gas pressure inside the manufacturing equipment, nitrogen gas was continually supplied at a flow rate of 12.5 L/min during the in-situ measurement. A pressure gauge with a minimum scale of 10 mbar was unable to detect any pressure at the outlet of the pressure reducer, implying reduction to near ambient pressure.
Highly concentrated particles should be diluted, primarily in order to comply with the maximum detectable concentrations of aerosol instruments, and to prevent coagulation of particles during sampling and measurement. Dilution is also needed for continuous measurement because the cleaning interval of the impaction plate at an SMPS inlet might be shortened to a few minutes for measurement of highly concentrated particles. In this study, a rotating disk diluter (Matter Engineering, MD19-2E) was used for dilution factors greater than 100, offering a continuous range of dilution factors from 15–3000. The dilution performance of the rotating disk diluter was previously reported to be independent of the particle diameter in the SMPS size region of 0.01–0.7 μm (Hueglin et al. 1997).
The total number concentrations of metal nanopowders larger than 3 nm were monitored every second by an ultrafine condensation particle counter (UCPC, TSI model 3025A). The size distributions of the metal nanopowders were investigated using an SMPS (TSI model 3936) for particles ranging from 14–681 nm in electrical mobility diameter. The SMPS was composed of an electrostatic classifier (TSI model 3080L), including a long differential mobility analyzer (long-DMA, TSI model 3081) and a condensation particle counter (CPC, TSI model 3010). The particle sizes were scanned for 180 s (150 s for the up-scan and 30 s for the retrace) every 4 min. The particle concentrations measured using the SMPS were corrected for the effect of multi-charging and diffusion loss by selecting the appropriate software options.
To characterize the charge distribution of a specific particle size, another electrostatic classifier (TSI model 3080L, the same model as that of the SMPS) was inserted in front of the SMPS (). The polarity of the high-voltage power supply installed inside the electrostatic classifier was changed from negative to positive when the measurement target was switched from positively charged to negatively charged particles.
The charge level of the metal nanopowders was measured with an aerosol electrometer (TSI model 3068). The sampling flow rate of the aerosol electrometer was set at 1.2 L/min. The dilution factor was set at 25 in order to increase the signal.
2.3. Aerosol Sampling for TEM and SEM Image Analysis
Metal nanopowders manufactured by the wire electrical explosion process were collected for TEM image analysis on a copper TEM grid (Carbon grid type-A, Ted Pella Inc.) coated with a carbon film, using an electrostatic precipitator or a nanometer aerosol sampler (TSI model 3089). In this study, a high voltage of 8–9 kV was applied for approximately 5 min at a sampling flow rate of 1 L/min to collect the metal nanopowders. An analytical transmission electron microscope (Philips model CM30) with an accelerating voltage of 200–300 keV was used for the TEM image analysis.
For the SEM image analysis, the metal nanopowders were also collected on a polycarbonate membrane filter (Whatmann 111103) with a pore diameter of 0.05 μm for 5 min at a sampling flow rate of 1.2 L/min, using a filter holder. The polycarbonate membrane filter sample, which was coated with Pt–Pd using an ion sputtering coater (Eiko model IB-3), was analyzed in a high vacuum mode (10−5 mbar) with a scanning electron microscope (Philips Electrons Optics model XL30 ESEM-FEG).
3. RESULTS
3.1. In-Situ Monitoring Downstream of the Evaporation Chamber
shows the concentration changes of metal nanopowders measured by UCPC and SMPS during the wire electrical explosion process, and corrected with a dilution factor of 2500. The dilution factor was fixed at 2500, except in the measurements taken with the aerosol electrometer, and in the performance tests of the rotating disk diluter. In , the solid and open triangles denote production (i.e., explosion) start and stop times, respectively. As measured by the UCPC and corrected with a dilution factor of 2500, the concentration of metal nanopowders larger than 3 nm increased from 3 × 103 particles/cm3 to approximately 5 × 107 particles/cm3 within 30 s after the start of each explosion, and returned to the base level within 5 min after the explosion stopped. As measured by the SMPS, the concentration of metal nanopowders ranging from 14 nm to 681 nm was approximately 4 × 107 particles/cm3 as a steady-state level over the production period (), which is about 80% of the UCPC measurement. From these stable nanopowder concentrations, it can be inferred that newly generated particles are relatively unaffected by particles that penetrate the mesh filter and return to the evaporation chamber. The standard variations in the concentration over the long production period denoted by period A were 4% for metal nanopowders larger than 3 nm, and 2% for metal nanopowders ranging from 14 nm to 681 nm, implying that the wire electrical explosion process has good production stability in terms of concentration.
FIG. 2 Concentration changes of metal nanopowders larger than 3 nm (UCPC) and ranging from 14–681 nm (SMPS), measured downstream of the evaporation chamber during the wire electrical explosion process, and corrected with a dilution factor of 2500. Solid and open triangles denote production start and stop times, respectively.
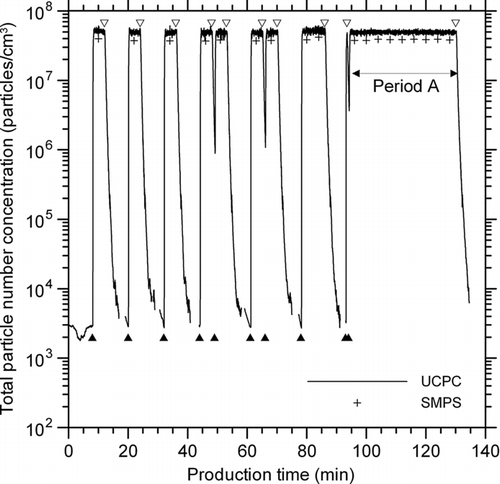
FIG. 3 Average size distributions of metal nanopowders manufactured by the wire electrical explosion process over a period of approximately 36 min, measured nine times by the SMPS downstream of the evaporation chamber.
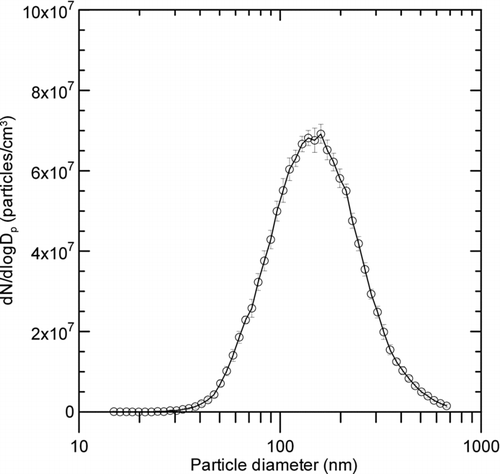
shows the average size distributions of metal nanopowders manufactured during period A in . Nine SMPS measurements of the particle size distribution were taken during that period. The average mean diameter and geometric standard deviation for the metal nanopowders measured by the SMPS were 169 ± 2 nm and 1.67 ± 0.003, respectively. Thus the wire electrical explosion process also shows good production stability in terms of particle size distribution.
Aerosol particles dispersed by nebulization, combustion, or powder dispersion are usually electrostatically charged. The charge level of the particles is an important parameter in designing a control device for particle size, which could be useful for improving nanopowder quality. Hence, the SMPS has a Kr-85 neutralizer (TSI model 3077) ahead of the DMA, to create a Boltzmann charge distribution on the surfaces of the sampled particles. Highly charged particles might not become neutralized relative to a Boltzmann charge distribution after passing through the neutralizer, so that the measured particle size distribution could be distorted (Ji et al. Citation2004). These authors reported that when highly positively charged particles are not sufficiently neutralized by the Kr-85 neutralizer of the SMPS, the peak concentrations become higher, and the mode diameters of the particle size distributions become slightly smaller than the actual results. Therefore, whether or not nanopowders manufactured by the wire electrical explosion process are highly charged is not only of general interest to manufacturers, but also necessary information for this in-situ measurement research. Because the dilution factor was set at 25 for the measurement of the charge level, the number concentration of metal nanopowders larger than 3 nm was estimated to be 2 × 106 particles/cm3 when the metal nanopowder current measured with the aerosol electrometer was 0.08 pA. The average number of positive ion charges per metal nanopowder particle was estimated to be 0.013 ion/particle, implying that the positively charged particles slightly outnumbered the negatively charged particles. This charge level is not high, considering the artifact in SMPS measurements. The number of charges per particle with a diameter of approximately 160 nm was more than three after passing a corona discharger, where a high voltage of 4 kV was applied (Ji et al. Citation2004). When the neutralizer removed from the SMPS was installed ahead of the aerosol electrometer, the current became negative (–0.05 pA), since the equilibrium charge distribution created by a bipolar charger such as the Kr-85 neutralizer has a slightly negative bias in the submicron particle size range (Wiedensohler Citation1988). Accordingly, there is thought to be no distortion in the particle size distributions measured by the SMPS, such as might be caused by failure in the neutralization of the highly charged particles passing through the neutralizer.
FIG. 4 Particle size distributions of metal nanopowders measured downstream of the evaporation chamber, according to the use of a neutralizer and DMA polarities.
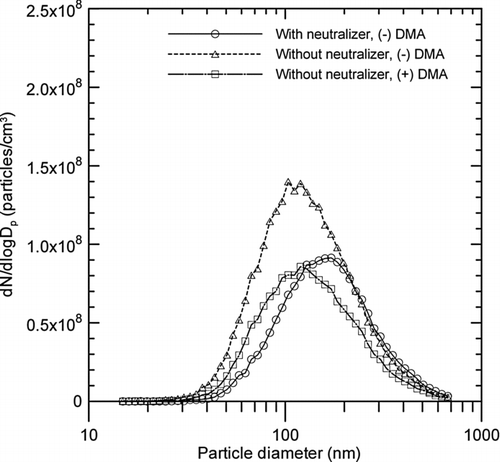
shows the differences in the size distributions of metal nanopowders according to the use of a neutralizer and DMA polarities. The peak concentration of particles classified by negative DMA after bypassing the neutralizer (positively charged particles) was higher than the peak concentration of particles classified by positive DMA after bypassing the neutralizer (negatively charged particles), as well as the peak concentration of particles classified by negative DMA after passing through the neutralizer (all particles). This is consistent with the implications of the above aerosol electrometer measurements, that the positively charged particles slightly outnumbered the negatively charged particles during the wire electrical explosion process. It follows that the fraction of uncharged (neutral) metal nanoparticles was small, which has also been observed for soot particles measured at a specific height in a premixed ethylene flame (Maricq Citation2005). The size distributions of the positively and negatively charged particles were shifted by approximately 50 nm toward the lower diameters for singly charged particles. This shift could have resulted from the effect of multi-charged particles that were classified at diameters smaller than their actual size due to their excess charges, as has also occurred in the measurement of diesel exhaust particles (Maricq 2006).
FIG. 5 Particle size distributions of metal nanopowders classified at 156 nm of electrical mobility diameter by using the first electrostatic classifier without a neutralizer, and scanned with the second electrostatic classifier.
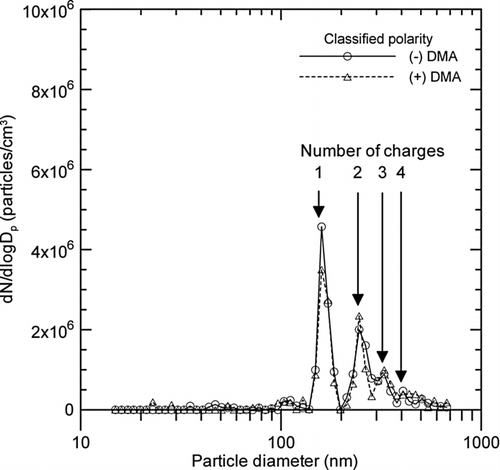
shows the size distributions of metal nanopowders classified at 156 nm of electrical mobility diameter by using the first electrostatic classifier without a neutralizer, and scanned with the second electrostatic classifier (which was the same as the first). This classified particle size corresponds to an electrical mobility of 1.3 × 10−4 cm2/V·s. Peaks for multi-charged particles can be observed for both positively and negatively charged particles, as shown in . This size distribution is similar to what is typical for monodisperse particles classified by an electrostatic classifier (Maricq Citation2005), and this is why the multi-charged correction option should be selected in the instrument software. However, the fraction of multi-charged particles differed slightly from that of the Boltzmann charge distribution, because the first electrostatic classifier was used without a neutralizer. Compared to the peak concentration of singly charged particles, the peak concentration of doubly charged particles was 45% for positive particles and 58% for negative particles, which is approximately 1.7 times higher than the peak concentration for an equilibrium bipolar charge distribution.
FIG. 6 Changes in SMPS measurements of metal nanopowders downstream of the evaporation chamber with respect to dilution factor; (a) Particle size distribution; (b) Particle concentration, geometric mean and mode diameters, and geometric standard deviation.
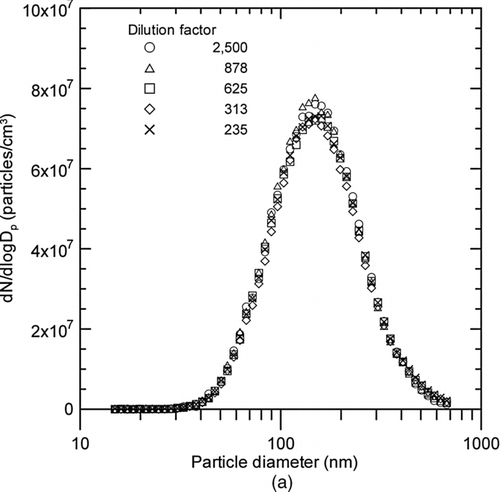
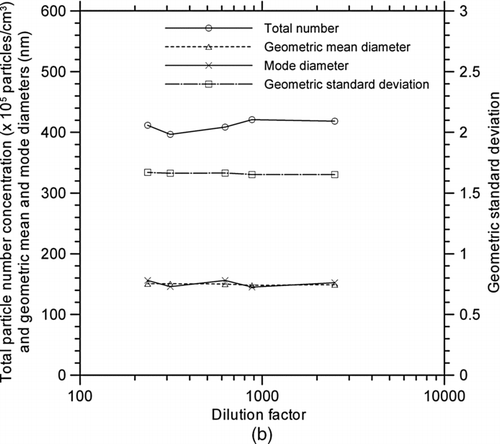
The advantage of the rotating disk diluter is the broad range of adjustable dilution factors that can easily be set by changing the rotational speed of the disk. In this study, the dilution factor was changed from 2500 to 235 using an eight-cavity disk, in order to determine the appropriate use for in-situ measurement during the wire electrical explosion process. shows that the particle size distributions measured by the SMPS, and corrected with dilution factors of 2500, 878, 625, 313, and 235, were all virtually identical. Their average concentrations, geometric mean diameters, mode diameters, and geometric standard deviations were 4 ± 0.1 × 107 particles/cm3, 150 ± 1 nm, 151 ± 5 nm, and 1.66 ± 0.01, respectively. All of the standard deviations were less than 3%, indicating that these quantities are independent of the dilution factor under the given measurement conditions.
3.2. Comparison of In-Situ Measurements and Image Analysis
The morphology of the metal nanopowders was examined by traditional methods, such as SEM and TEM image analysis, as shown in . Most of the particles appear to be aggregated, with primary particle diameters of 10–100 nm, which is typical of metal nanopowders manufactured by the wire electrical explosion process (Phalen Citation1972; Wang et al. Citation2001; Kotov Citation2003; Kim et al. 2007; Sarathi et al. Citation2007, Citation2009). Some of the primary particles collided with others to form aggregates, but each surface can be clearly distinguished. Nevertheless, coalescent particles are found in both the SEM and TEM images (). This coalescence may have occurred among the aggregated particles in the evaporation chamber as a result of surface melting caused by the high energy. In light of the collision and aggregation processes occurring under highly concentrated conditions, the number of individual particles smaller than 14 nm (which could not be detected with the SMPS used in this research) seems insignificant, since particles of that size were not observed independently in the TEM images, as shown in . The total number concentration of particles measured by the SMPS could also account for 80–90% of the concentration measured by the UCPC.
FIG. 8 Comparison of particle size distributions obtained from the in-situ measurement data (SMPS) and the SEM analysis results (n = 226).
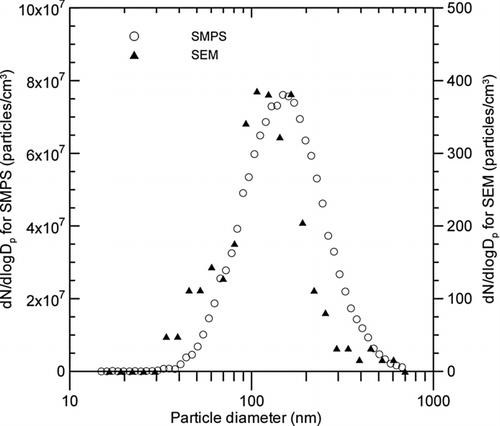
shows the size distribution of the nanopowders derived from SEM image analysis of non-primary but separate particles, including single and aggregated particles, compared with the size distribution obtained from the SMPS measurements. The total number of particles analyzed with the SEM was 226. The particle diameters are assumed to be those of spheres with the same projected areas, since the projected equivalent diameter is the most commonly used, and has a good correlation with the mobility equivalent diameter of the SMPS (Hinds 1999; Kim and Zachariah Citation2005). The particle size distribution obtained from the SEM appears to be similar to that obtained from the SMPS, even though the contribution from small particles (ranging from 30 nm to 60 nm) is relatively larger, and the contribution from large particles (ranging from 200 nm to 400 nm) is relatively smaller. The reason for this difference is not known, but some breakdown of large particles might occur during filter sampling. Despite the small discrepancy, the particle size distribution obtained from the in-situ measurements using the SMPS seems to effectively represent the real-time data inside the manufacturing equipment.
3.3. Changes in Particle Size Distribution at Each Stage of the WEE Process
In-situ monitoring can be used to study particle formation and growth inside a metal nanopowder production system, and to evaluate the performance of size control devices such as the cyclone, as well as the collection efficiency of collecting devices such as the mesh filter over a short period of time.
FIG. 9 Changes in the particle size distribution at each stage of the wire electrical explosion process.
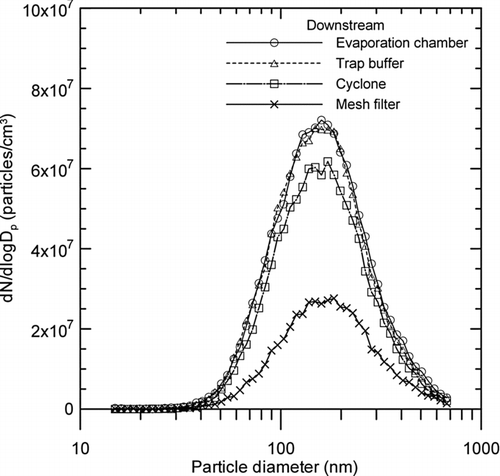
shows the changes in the particle size distribution of the metal nanopowders measured at four different locations at each stage of the wire electrical explosion process. As the figure indicates, the distribution retained its unimodal shape throughout the manufacturing process. The mean diameters and geometric standard deviations measured by the SMPS were in the very narrow ranges of 179–196 nm and 1.68–1.71, respectively, during the entire process. It stands to reason that there is virtually no difference between the particle size distributions measured downstream of the evaporation chamber (upstream of the trap buffer) and downstream of the trap buffer. It is also useful to know that the fraction of particles ranging from 60–400 nm is approximately 43% downstream of the mesh filter, unlike the other locations (where the fraction is greater than 90%), as will be discussed later.
FIG. 10 Changes in the size-resolved particle concentration normalized with respect to the concentration downstream of the evaporation chamber (dN E ) at each stage of the wire electrical explosion process.
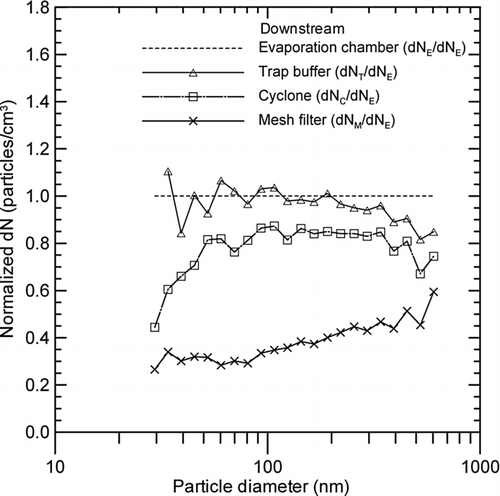
The size-resolved penetration characteristics of the trap buffer, the cyclone, and the mesh filter are plotted as concentrations normalized with respect to the concentration downstream of the evaporation chamber, as shown in . As mentioned above, it makes sense that more than 80% of the particles pass the trap buffer, especially small particles. The difference between the normalized curves for the trap and the cyclone indicates the relative contribution of the cyclone to the change from the initial concentration downstream of the evaporation chamber. The cyclone removes less than 30% of the evaporation chamber concentration of particles larger than 40 nm. For particles smaller than 40 nm, diffusion loss at the cyclone wall is what seems to impel the concentration change. The ultimate particle penetration of the entire WEE process shows an increasing trend with respect to particle size. It is interesting that the collection efficiency of the mesh filter is lower for larger particles (>400 nm) than for relatively smaller particles (∼100 nm). As measured by the UCPC, the number concentration of particles larger than 3 nm decreased from 15,800 particles/cm3 downstream of the cyclone to 7,800 particles/cm3 downstream of the mesh filter, due to particle collection by the mesh filter. Therefore, the overall collection efficiency of the mesh filter is estimated to be 51%. Since particles penetrating the mesh filter are carried into the evaporation chamber, they can act as seeds for particle formation and growth, which might be one reason for broadening the size distribution of metal nanopowders manufactured by the wire electrical explosion process. However, under the experimental conditions of this study, the seed effect appears to be insignificant over the SMPS size range, in view of the stability observed in both the concentration and size distribution of the nanopowder products (Figures and ).
4. DISCUSSION
The quality of a nanopowder is mainly dependent on its purity and size uniformity. As mentioned earlier, the WEE method offers the advantage of high purity through production under pure inert gas conditions. However, the size uniformity of nanopowders produced by the WEE process should be improved by installing a control device. There are a number of devices available for controlling particle size, including impactors that use inertia, diffusion batteries that use Brownian motion, differential mobility analyzers that use electrostatic force, and cyclones of the type employed in this research, which use centrifugal force (Hinds 1999). When these particle devices are applied to a WEE system, in-situ measurement is both necessary and useful. For example, in the present study it was determined that the size distribution of nanopowders produced by the WEE process is unimodal with a mode diameter of approximately 150 nm, and that the fraction of particles ranging from 60–400 nm is greater than 90%. Accordingly, it would be better to narrow the particle size distribution by removing smaller particles (<60 nm) with an electrical trap using an applied electrical field, and by collecting larger particles (>400 nm) with a sharp-cutoff impactor. As regards the electrical trap, it should be kept in mind that there are both positively and negatively charged particles, as shown in Figures and . Hence it might be better to install a unipolar charger ahead of the electrical trap in order to collect all smaller particles inside the trap.
Some of the operating parameters of the WEE system are pulse high voltage, flow rate and pressure of the carrier gas, and choice of carrier gas. Sarathi et al. (Citation2009) reported that the size of the nucleus is relatively smaller in a helium ambience (due to the high cooling rate), so that the final mean size of the particles is also relatively smaller in comparison to those of argon and nitrogen ambiences. In any case, when the above operating parameters are set to obtain high uniformity of particle sizes, in-situ measurement using an SMPS equipped with a pressure reducer and a rotating disk diluter is an excellent strategy for determining the optimum conditions in a short time.
The in-situ measurement data on particle size distribution at each stage of the WEE process are also very useful for finding the process stage at which nanopowder release to the workplace environment becomes a severe exposure emergency. For example, if the fraction of particles ranging from 60–400 nm is found to be less than 50% of the workplace exposure, the problem is surely due to a leak downstream of the mesh filter. These fingerprints of metal nanopowders can help distinguish them from other nanomaterials, such as carbon nanotubes, whose size response peaks at 200–400 nm (Lee et al. Citation2010). This is important because nanopowders are widely used as catalysts for producing carbon nanotubes.
5. CONCLUSIONS
In-situ measurement of metal nanopowders manufactured by the wire electrical explosion process was carried out using a real-time aerosol instrument (a scanning mobility particle sizer equipped with a pressure reducer and a rotating disk diluter), in order to characterize metal nanopowder production and verify the usefulness of the in-situ measurement system through this characterization. The pressure reducer was used to reduce the high pressure of the nitrogen gas (1.5 bar) inside the manufacturing equipment to near ambient pressure. By applying the rotating disk diluter, a wide range of dilution factors was obtained (235–2500).
The total number concentrations of metal nanopowders obtained with the UCPC (>3 nm) and the SMPS (14–681 nm) were approximately 5 × 107 and 4 × 107 particles/cm3, respectively, measured downstream of the evaporation chamber during the WEE process. Good production stability was observed, in terms of both concentration and the unimodal size distribution of nanopowders with a mean diameter of approximately 170 nm.
Using data from the aerosol electrometer, the average number of positive ion charges per metal nanopowder particle was estimated as low as 0.013 ion/particle, since the concentration peak for positively charged particles was slightly higher than the concentration peak for negatively charged particles. However, this charge level is not high in view of the artifact in SMPS measurements.
The average concentrations, geometric mean diameters, mode diameters, and geometric standard deviations for five different dilution factors ranging from 235–2500 were 4 ± 0.1 × 107 particles/cm3, 150 ± 1 nm, 151 ± 5 nm, and 1.66 ± 0.01, respectively, indicating their independence of the dilution factor, as well as proper use of this type of measurement system.
Because of the close similarity of its results to the size distribution of nanopowders obtained from SEM image analysis, the in-situ measurement system used in this study appears to effectively measure the real-time data inside the manufacturing equipment for the WEE process.
These in-situ measurement data could be useful in designing a control device for particle size to improve the product quality, and for identifying a specific process stage that is responsible for nanopowder exposure in the workplace environment.
This research was supported by the Small and Medium Business Administration, Korea (grant number S0807222-L0616100-10100001).
REFERENCES
- Brenner , J. R. , Harkness , J. B. L. , Knickelbein , M. B. , Krumdick , G. K. and Marshall , C. L. 1997 . Microwave Plasma Synthesis of Carbon-Supported Ultrafine Metal Particles . Nanostruct. Mater. , 8 : 1 – 17 .
- El-sayed , M. A. 2001 . Some Interesting Properties of Metals Confined in Time and Nanometer Space of Different Shapes . Acc. Chem. Res. , 34 : 257 – 264 .
- Gaertner , G. F. and Lydtin , H. 1994 . Review of Ultrafine Particle Generation by Laser Ablation from Solid Targets in Gas Flows . Nanostruct. Mater. , 4 : 559 – 568 .
- Granqvist , C. and Buhrman , R. 1976 . Ultrafine Metal Particles . J. Appl. Phys. , 47 : 2200 – 2219 .
- Hind , W. C. 1999 . Aerosol Technology: Properties, Behavior, and Measurement of Airborne Particles. , 253 403 New York : Wiley .
- Hueglin , C. , Scherrer , L. and Burtscher , H. 1997 . An Accurate, Continuously Adjustable Dilution System (1: 10 to 1: 104) for Submicron Aerosols . J. Aerosol Sci. , 28 ( 6 ) : 1049 – 1055 .
- Ji , J. H. , Bae , G. N. and Hwang , J. 2004 . Characteristics of Aerosol Charge Neutralizers for Highly Charged Particles . J. Aerosol Sci. , 35 : 1347 – 1358 .
- Jiang , W. and Yatsui , K. 1998 . Pulsed Wire Discharge for Nanosized Powder Synthesis . IEEE Trans. Plasma Sci. , 26 : 1498 – 1501 .
- Jung , J. H. , Kim , S. B. and Kim , S. S. 2008 . Nanoparticle Generation using Corona Discharge Ions from a Supersonic Flow in Low Pressure . Powder Technol. , 185 : 58 – 66 .
- Jung , J. H. , Oh , H. C. , Noh , H. S. , Ji , J. H. and Kim , S. S. 2006 . Metal Nanoparticle Generation Using a Small Ceramic Heater with a Local Heating Area . J. Aerosol Sci. , 37 : 1662 – 1670 .
- Jung , J. H. , Park , H. H. and Kim , S. S. 2007 . Effects of Corona Discharge Ions on the Synthesis of Silver Nanoparticles by a Supersonic Nozzle Expansion Method . J. Vac. Sci. Technol. , B25 : 169 – 174 .
- Kim , S. H. and Zachariah , M. R. 2005 . In-Flight Size Classification of Carbon Nanotubes by Gas Phase Electrophoresis . Nanotechnol. , 16 : 2149 – 2152 .
- Kim , W. B. , Park , J. S. , Suh , C. Y. , Lee , J. C. , Kim , J. H. and Oh , Y. J. 2007 . Cu-Ni-P Alloy Nano Powders Prepared by Electrical Wire Explosion . J. Korean Powder Metallurgy Inst. , 14 ( 2 ) : 108 – 115 .
- Kotov , Y. A. 2003 . Electrical Explosion of Wires as a Method for Preparation of Nanopowders . J. Nanopart. Res. , 5 : 539 – 550 .
- Kwon , Y. S. , Gromov , A. A. , Ilyin , A. P. , Ditts , A. A. , Kim , J. S. , Park , S. H. and Hong , M. H. 2004 . Features of Passivation, Oxidation and Combustion of Tungsten Nanopowders by Air . Int. J. Refract. Met. Hard Mater. , 22 : 235 – 241 .
- Kwon , Y. S. , Jung , Y. H. , Yavorovsky , N. A. , Illyn , A. P. and Kim , J. S. 2001 . Ultra-Fine Powder by Wire Explosion Method . Scripta Mater. , 44 : 2247 – 2251 .
- Lee , J. K. , Rubow , K. L. , Pui , D. Y. H. and Liu , B. Y. H. 1993 . Design and Performance Evaluation of a Pressure-Reducing Device for Aerosol Sampling from High-Purity Gases . Aerosol Sci. Technol. , 19 ( 3 ) : 215 – 226 .
- Lee , S. B. , Lee , J. H. and Bae , G. N. 2010 . Size Response of an SMPS–APS System to Commercial Multi-Walled Carbon Nanotubes . J. Nanopart. Res. , 12 : 501 – 512 .
- Maricq , M. M. 2005 . The Dynamics of Electrically Charged Soot Particles in a Premixed Ethylene Flame . Combust. Flame , 141 : 406 – 416 .
- Maricq , M. M. 2006 . On the Electrical Charge of Motor Vehicle Exhaust Particles. . J. Aerosol Sci. , 37 ( 7 ) : 858 – 874 .
- Okuyama , K. and Lenggoro , I. W. 2003 . Preparation of Nanoparticles via Spray Route . Chem. Eng. Sci. , 58 : 537 – 547 .
- Ozawa , E. , Kawakami , Y. and Seto , T. 2001 . Formation and Size Control of Tungsten Nano Particles Produced by Nd:YAG Laser Irradiation . Scripta Mater. , 44 : 2279 – 2283 .
- Phalen , R. F. 1972 . Evaluation of an Exploded-Wire Aerosol Generator for use in Inhalation Studies . J. Aerosol Sci. , 3 : 395 – 406 .
- Sarathi , R. , Sindhu , T. K. and Chakravarthy , S. R. 2007 . Generation of Nano Aluminum Powder Through Wire Explosion Process and its Characterization . Mater. Charact. , 58 : 148 – 155 .
- Sarathi , R. , Sindhu , T. K. , Chakravarthy , S. R. , Sharma , A. and Nagesh , K. V. 2009 . Generation and Characterization of Nano-Tungsten Particles Formed by Wire Explosion Process . J. Alloys Compd. , 475 : 658 – 663 .
- Wang , Q. , Yang , H. , Shi , J. and Zou , G. 2001 . Preparation and Characterization of Nanocrystalline Powders of Cu-Zn Alloy by Wire Electrical Explosion Method . Mater. Sci. Eng. , A307 : 190 – 194 .
- Wiedensohler , A. 1988 . An Approximation of the Bipolar Charge Distribution for Particles in the Submicron Size Range . J. Aerosol. Sci. , 19 : 387 – 389 .
- Zhu , W. and Pratsinis , S. E. 1997 . Synthesis of SiO2 and SnO2 Particles in Diffusion Flame Reactors . AIChE J. , 43 : 2657 – 2664 .