Abstract
In this study, the impaction behavior of titanium dioxide (TiO2) agglomerates is evaluated, and the described method allows for the break-up and bounce of the particles to be monitored simultaneously. The degree of sintering and the primary particle size of the TiO2 agglomerates were varied. The agglomerates were impacted onto the impaction plate of a single-stage micro-orifice uniform impactor, after which the bounced particles were collected in a low-pressure sampling chamber for subsequent analyses. The particle trajectories were simulated to accurately estimate the impaction velocity, which is one of the key parameters in the impaction process. A high degree of sintering significantly reduced the number of broken bonds, whereas reducing the primary particle size caused only minor differences in the number of broken bonds. The particles that bounced but did not break up either had a smaller primary particle size or were sintered. Decreasing the primary particle size also reduced the mass-based fraction of the bouncing particles.
Copyright 2014 American Association for Aerosol Research
1. INTRODUCTION
Titanium dioxide (TiO2) is a well-known and widely used material in aerosol science and industry. This compound has been used in everyday products, such as paints, sunscreens, and toothpaste, as well as in state-of-the-art applications, such as photocatalysis, photovoltaics, electrochromics, and photochromics (Fujishima and Zhang Citation2006; Chen and Mao Citation2007). Although TiO2 has been well characterized, the impaction behavior, the break-up and bounce, of TiO2 agglomerates and their interaction with other materials is not completely understood.
Break-up and bounce behavior due to an impaction remain a problem for researchers modeling a severe nuclear accident, for example, in steam generator tube rupture (SGTR) situations. During SGTR, agglomerates may impact surfaces at near sonic conditions, which may affect the distribution of aerosols and their release into the environment (Guntay et al. Citation2004). Particle impaction is of concern also in gas turbines because of erosion (Khalil and Rosner Citation1996). Impaction is a commonly used measurement technique; thus, considerable research has been carried out to minimize undesirable measurement errors from the bounce process. The bounce process is also exploited in some measurement methods. For example, the particle bounce in an impactor has been practically applied to study the particles’ physical state (Virtanen et al. Citation2010).
Seipenbusch et al. (Citation2002, 2007, 2010) and Froeschke et al. (Citation2003) have studied the break-up of submicron agglomerates by impaction. In these studies, a single-stage low-pressure impactor with a single orifice was used to impact particles with various properties. Froeschke et al. (Citation2003), and Seipenbusch et al. (Citation2002, 2007) studied agglomerates made of different materials and the primary particle size was varied, whereas Seipenbusch et al. (Citation2010) concentrated on the effect of sintering of agglomerates on the break-up process. Transmission electron microscopy (TEM) was used to determine how many interparticle bonds broke up during impaction. The bond strength was also estimated using the impaction energy, which is related to the initial velocity of the particle. The impaction velocity was estimated by evaluating the average gas velocity. Early impactor simulations by Marple (Citation1970) for high Stokes number impaction showed that the impaction velocity was 0.85 times the gas jet velocity. Although this result is frequently used as a general rule to estimate the impaction velocity, Rennecke and Weber (Citation2013a) found that the impaction velocity was overestimated at low jet velocities and underestimated at high speeds. They developed a semi-analytical and impactor geometry independent model to estimate the impaction velocities in a single-stage low-pressure impactor. This method was applied by Rennecke and Weber (Citation2013b) in the determination of the critical velocities for nanoparticle rebound in a low-pressure impactor. In addition to the agglomerate properties, the material of the impaction surface affects the particles’ bounce, especially at low impaction velocities (Wall et al. Citation1990).
Ihalainen et al. (Citation2012) studied the impaction and bounce behavior of TiO2 particles at a single impaction velocity of 98 m/s using a micro-orifice uniform deposit impactor (MOUDI) impactor (Marple et al. Citation1991). A method was developed to monitor particle impaction, de-agglomeration and bounce, and a basic framework and apparatus to measure impaction were introduced. However, more in-depth characterization was required to calculate the energies involved in the impaction processes.
The impaction measurement system developed by Ihalainen et al. (Citation2012) was used in this study to investigate impaction behavior, break up and bounce of TiO2 agglomerates in greater detail. Both the primary particle diameter and the degree of sintering of the TiO2 agglomerates were varied. The experimental measurements were carried out for different agglomerate sizes. Numerical simulations are presented for an important impaction parameter, the impaction velocity, along with experimental results for the deposition, de-agglomeration, and bounce behavior of TiO2 agglomerates over a range of impaction velocities. We also estimate the kinetic energy consumed per broken bond, and we will detail in a subsequent report how this energy can be subdivided between the processes involved in the impaction, such as break-up and bounce. In the near future, the impaction processes will be simulated using a discrete element method in conjunction with the results obtained in this study.
2. EXPERIMENTAL
2.1. Aerosol Generation
The TiO2 agglomerates were generated by chemical vapor synthesis using a slightly modified version of an apparatus developed by Miettinen et al. (Citation2009). shows the apparatus used to generate the agglomerates. The liquid precursor, titanium tetra isopropoxide (C12H28O4Ti), was vaporized at a temperature of 50°C, which was maintained with a heated water bath. The vaporized precursor was carried by nitrogen (at a volumetric flow of 1 Nlpm) to a laminar hot wall reactor (at 500°C or 700°C). The hot wall reactor contained a ceramic tube with a length of 700 mm and a diameter of 25 mm. The feeding line was heated (60°C) and insulated to prevent the precursor material condensing onto the walls of the line. The precursor material thermally decomposed in the reactor, and the primary particles were formed by the nucleation and condensation of the gaseous species. Due to processes of nucleation, condensation, growth, coagulation, and agglomeration, TiO2 agglomerates with the desired properties could be generated. The aerosol generation process was quenched by dilution air, which was supplied through a porous tube diluter (PRD), as described by Lyyränen et al. (Citation2004). The gas temperature and the aerosol concentration decreased simultaneously.
After the TiO2 agglomerates were generated, their sizes were classified by measuring their electrical mobility with a differential mobility analyzer (DMA). The sample flow rate through the DMA was 1 Nlpm. The impactor flow rate was higher than that of the DMA; thus, a PRD and an ejector diluter were used to increase the sample flow rate to the desired flow rate (10–20 Nlpm) before introducing the size-classified agglomerates into the impactor.
An experiment was carried out to investigate the effect of sintering between the primary particles on the impaction behavior. A secondary hot wall reactor (i.e., the sintering reactor shown in ) was added to the aerosol generation line downstream of the DMA. The tube inside the reactor had a length and diameter of 1000 and 25 mm, respectively. The flow rate through the secondary reactor was 1 NLpm, and the temperature was 950°C, corresponding to a residence time of approximately 10 s. After the sintering process, the high-temperature aerosol was cooled to the ambient temperature by the ejector and PRDs.
2.2. Impaction Method
The DMA, the single-stage MOUDI and a sampling chamber were used in combination to investigate the break-up and bounce of the TiO2 agglomerates. Details of the measurement system can be found in Ihalainen et al. (Citation2012).
shows the nomenclature used for the types of particles investigated in this study. We will refer to the different particle types as (a) intact, (b) de-agglomerated and bounced, (c) bounced and unbroken, or (d) deposited particles.
FIG. 2 Schematic of the impaction process. (a) Intact particles; (b) de-agglomerated and bounced particles; (c) bounced and unbroken particles; (d) deposited particles (unbroken or de-agglomerated).
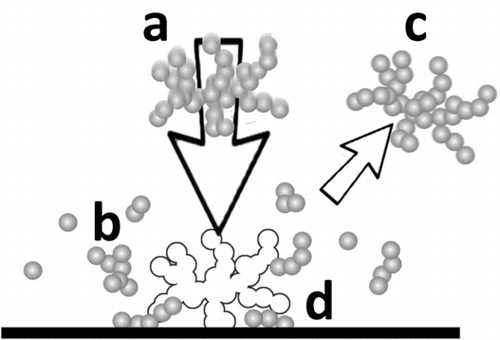
The generated TiO2 agglomerates were first size-classified using the DMA to produce monodisperse particles and then introduced into the MOUDI for impaction onto the impaction plate. A copper grid-supported carbon film (Agar Scientific) was placed on the impaction plate, as described by Ihalainen et al. (Citation2012), and the particles deposited on the grid were analyzed by a TEM (JEOL JEM-2100F FEG/STEM), which was operated at 200 kV. The bounced particles were collected in the sampling chamber, which is designed for low-pressure sampling (Ihalainen et al. Citation2012). The bounced particles were then analyzed on-line by the SMPS. TEM samples were collected using an aspiration sampler (Lyyränen et al. Citation2009) with copper-supported carbon films with holes (Agar Scientific). The intact particles were characterized by carrying out the same analysis and sampling procedure without the impaction plate.
The kinetic impaction energy E imp is proportional to the square of the impaction velocity of the particles v imp:
In this study, the impaction surface consisted of aluminum foil, which was placed on the impaction plate of the MOUDI. The Poisson's ratio, Young's modulus, and Hamaker constant of aluminum are 0.33, 87 GPa, and 15E-20, respectively. The effect of different impaction surface materials will be studied in more detail in a future publication.
2.3. Experimental Conditions
shows how the agglomerate properties were varied during the experiments. The parameters given below were investigated.
TABLE 1 Properties of TiO2 agglomerates for the investigated cases: primary particle diameter (d pp, nm), agglomerate electrical mobility diameter (d agg, nm), and whether the particles were sintered (YES, NO)
1. | The size of the primary particles was adjusted by controlling the temperature of the hot wall reactor without changing the total vapor concentration. | ||||
2. | The size of the agglomerates was varied using size classification by the DMA for nonsintered agglomerates with a primary particle diameter (dpp ) of 27 nm. Agglomerate electrical mobility diameters (dagg ) of 250, 300, and 400 nm were used. | ||||
3. | The sintering between the primary particles of 250 nm agglomerates with an initial dpp of 27 nm was carried out to increase the bond energy between the primary particles. The sintering was induced thermally using the optional reactor at an operating temperature of 950°C. |
The impaction of the agglomerates for the cases shown in was studied at various impaction velocities, which depended on the applied pressure difference across the MOUDI. Pressure differences of 60, 100, 150, and 250 mbar were applied. Cases 4 and 5 were investigated at a single pressure difference of 150 mbar.
TEM was used to calculate the distribution of area equivalent diameters from the agglomerate images for each case. Approximately 100–500 individual agglomerates were analyzed using a process that has been described in detail by Ihalainen et al. (Citation2012). The geometric mean of the distribution of the calculated diameters was used to compare the average size of the deposited particles with the size of the bounced particles. The electrical mobility diameter of the bounced particles was also compared with these values.
2.4. Effective Density
An aerosol particle mass (APM) analyzer and a scanning mobility particle sizer (SMPS) were used to analyze the fractal dimension and the effective density of the intact particles to obtain the parameters required to calculate the mass distributions and average masses of the intact and bounced particles. This method has been used previously; see, for example, Malloy et al. (Citation2009) and Ihalainen et al. (Citation2012). The particle mass m was first determined using APM and then the electrical mobility de was measured by SMPS. These data were then used in the following equation (Park et al. Citation2003):
APM and SMPS can also be used to estimate the effective densities of agglomerates of different sizes. The effective density for a given agglomerate size can be calculated using the following equation:
The fractal dimension in EquationEquation (2) is associated with the power-law relation between the electrical mobility diameter and the agglomerate mass; thus, the effective density in EquationEquation (3) can be rewritten in the following form (Park et al. Citation2003):
2.5. Bounced Particle Mass Concentration
The mass concentration of the bounced particles was calculated using the SMPS data of the bounced particles and the size-dependent effective density from EquationEquation (4). The mass of the spherical particles is proportional to the particle diameter raised to the power three; thus, the noise in the SMPS data of the larger particles would have introduced relatively high uncertainties into the calculated values of the total mass concentration of the bounced particles. To lower the effect of the noise in the data of the larger particles, the number size distribution data of the SMPS was fitted with three-mode lognormal distributions using the least squares method. The first mode described the bounced and de-agglomerated particles, and the other two modes described the singly and doubly charged particles that bounced without de-agglomeration. The mass concentrations of the bounced particles for each mode were then compared to that of an intact particle to determine the bounce fraction of the particles. A two-mode distribution was used to determine the intact particle mass concentration, where the two modes represented the singly and doubly charged particles.
2.6. Degree of Fragmentation
The average number of broken bonds per agglomerate was calculated in the following manner. The geometric mean diameter of the de-agglomerated and intact particles and the size-dependent effective density were used to estimate the average mass of the agglomerates before and after impaction. For simplicity, the agglomerates were assumed to have a branched chain-like structure. The masses of an average agglomerate before (m intact) and after (m bounced) impaction were used to estimate the number of fragments the agglomerate disintegrated into during impaction. The minimum number of broken bonds (N bonds,broken) required for a particle to disintegrate is given by
The primary particle mass mpp can be calculated from the known values of the primary particle size and the bulk density of the material. The number of primary particles per agglomerate can then be estimated. The same simplification of a branched structure can then be used to calculate the number of bonds for an average intact agglomerate:
This relation only holds if there are no looped structures in the agglomerate, i.e., the branch is only connected to the ‘‘main’’ agglomerate at one location.
The degree of fragmentation F, i.e., the ratio of the broken bonds to the intact bonds, can then be written as
The impaction energy per broken bond can be calculated as follows:
3. IMPACTION VELOCITY SIMULATIONS
3.1. Method
Computational fluids dynamics simulations were used in combination with the Lagrangian particle trajectory method to estimate the impaction velocity of the agglomerates. This method was previously used by Arffman et al. (Citation2011) to estimate the D 50 cutoff sizes of an electrical low-pressure impactor. The detailed description of the method can be found in the online supplemental information.
3.2. Velocity Simulation Results
The simulation results for the impaction velocities in the single-stage MOUDI are shown in . The simulations were carried out for the first three cases with pressure differences of 60, 80, 100, 150, 200, and 250 mbar and an absolute pressure above the impaction plate of 500 mbar. In the tests with larger agglomerates, the particle trajectories were simulated for a pressure difference of 150 mbar.
The impaction velocity results are shown in . The impaction velocity increased with the pressure difference () for all of the cases. The impaction velocities of the agglomerates with a primary particle size of 27 nm were close to those of the sintered agglomerates. This result was expected because the particle properties, such as the diameter and the effective density, do not change extensively during the sintering process. However, the effective density decreased for the smaller primary particle size, resulting in lower impaction velocities. This result should not be considered to be general, as shown in the online supplementary information.
shows the relationship between the impaction velocities and the average gas jet velocities. At the highest pressure differences and, thus impaction velocities, the ratio of the impaction velocity to the jet velocity was close to 0.85, as in Marple's (Citation1970) early fluid dynamic simulations for impactions at a high Stokes number. The 0.85 ratio has occasionally been used as a general rule to estimate the impaction velocity. However, this approximation did not hold under the prescribed conditions for the single-stage MOUDI used in this study. The ratio was close to 0.9 at high-pressure differences, but at low-pressure differences, the ratio decreased drastically. Rennecke and Weber (Citation2013a) obtained a similar conclusion by comparing the traditional estimate of the impaction velocity to the results of their semianalytical model, which was based on similarity theory. The authors reported that the impaction velocity was overestimated in the low impact velocity regime and underestimated at high velocities when Marple's method was used to calculate the impaction velocities.
The impaction angles were also observed in the simulations. The angles corresponded quite closely to a perpendicular impaction. More information on the impaction angles and impaction velocity results can be found in the supplemental information.
FIG. 4 TEM micrographs of intact particles: (a) base case with d pp = 27 nm, (b) smaller primary particle size d pp = 16 nm, and (c) sintered particles.
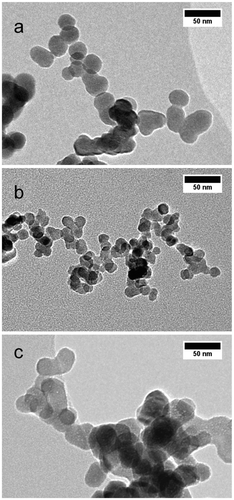
TABLE 2 Geometric mean diameters of the bounced particles measured with SMPS for a 150 mbar pressure difference
4. RESULTS
4.1. TiO2 Agglomerates
shows close-up images of agglomerates with different properties. show agglomerates with average primary particle sizes of 27 and 16 nm. The close-up image in of a sintered agglomerate shows increased necking between the primary particles compared to the non-sintered agglomerate in . shows the measured effective densities of different types of TiO2 agglomerates. The effective densities increased as the agglomerate size decreased because of the fractal nature of the agglomerates. The effective densities of the base and sintered cases were close to each other, with the effective density of the sintered case being slightly larger than that of the base case. This difference can be attributed to the slight decrease in the electrical mobility diameter from the sintering process, whereas the mass of the particles is not expected to change during sintering. Decreasing the size of the primary particles lowered the effective density. This result could be primarily attributed to the scalability of the fractal agglomerate. The fractal dimension can be defined in terms of the radius of gyration of the agglomerate df, gyr as follows (Mandelbrot Citation1983):
The ratio of the new agglomerate mass to the original agglomerate mass for a constant bulk material density is given as follows:
Thus, decreasing the primary particle size decreases the mass of the agglomerate of the same size as long as Df ,gyr is less than 3. Thus, the effective density decreases with the primary particle diameter. However, this result only holds if the parameters of the agglomerate structure remain unchanged.
Miettinen et al. (Citation2009) and Backman et al. (Citation2004) produced TiO2 agglomerates with approximately the same primary particle diameters (13–22 nm) and reactor temperature (500–1100°C). In these studies, the crystal phase was found to be primarily anatase: thus, the crystal phase of the particles in this study is assumed to be anatase.
The generation process of the agglomerates produced fairly polydisperse strengths for the bonds between the primary particles. More heat and time were available to form bonds in the earlier stages in the reactor before quenching by the dilution air; thus, these bonds were stronger than those that formed in the later stages because of the sintering process. Thus, the agglomerates were actually a combination of agglomerates and aggregates of differing bond strengths. Increasing the degree of sintering of the agglomerates strengthened the bonds. The bond strengths the depended on the residence time and the temperature of the sintering process, as well as the characteristics of the agglomerates, such as the existence of necking between the primary particles and the primary particle diameters. The strengths of the bonds formed after the sintering process were also assumed to be polydisperse.
4.2. Effect of Agglomerate Characteristics on Break-Up
The breakup and bounce of the TiO2 agglomerates were studied using a single-stage MOUDI and a sampling chamber. The size distributions of the bounced particles were measured using an SMPS, and the projection characteristics were analyzed using TEM. The deposited particles were examined using TEM.
The effect of the impaction velocity on the bounced particles is shown in and and . Increasing the impaction velocity decreased the size of the bounced particles. The impaction velocity also affected the number concentration of the bounced particles. The highest concentration was observed at high impaction velocities and the concentration declined significantly as the impaction velocity approached 50 m/s.
TABLE 3 Kinetic energy per broken bond for different particle sizes for a 150 mbar pressure difference across the impactor
FIG. 6 SMPS size distributions of intact and bounced particles at different impaction velocities for (a) a primary particle size of 27 nm, (b) a primary particle size of 16 nm, and (c) sintered particles. (d) Geometric mean diameter of bounced and de-agglomerated particles measured with SMPS. (Color figure available online.)
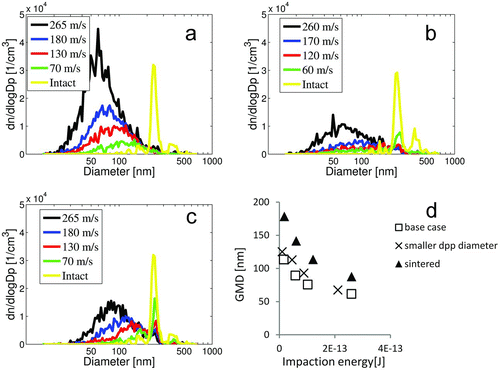
shows the SMPS size distributions of the bounced particles. Similar results were obtained for the three different agglomerate types. Increasing the impaction velocity decreased the average size of the bounced particles and increased the number concentration. Three distinct features were observed in the results. First, the geometric mean diameter (GMD) () of the bounced particles depended on the particle type and the impaction energy. Second, the change in the bounced particle size decreased as the impaction energy increased. Third, all of the agglomerates did not break up for the smaller primary particle size and a high degree of sintering ().
shows the degree of fragmentation F, i.e., the fraction of the broken intact bonds, of the bounced TiO2 particles. A degree of fragmentation of 0.5 corresponds to half of the bonds being broken by impaction. In an ideal case, this degree of fragmentation would result in fragments of duplets of primary particles, on average. The particles with the smaller primary particle diameters resulted in the lowest degree of fragmentation. This result was obtained not because there was less disintegration during impaction, but because there were more bonds before impaction. shows that the estimated number of broken bonds for the base case was quite close to that for the smaller primary particle case. For the sintered particles, both the degree of fragmentation and the number of broken bonds was lower than for the base case. Froeschke et al. (Citation2003) conducted an impaction fracture study using TiO2 agglomerates and found complete fragmentation at an impaction velocity of 71 m/s. In this study, the maximum velocity was over 250 m/s, but most of the bonds were left intact. However, there was a major difference between the two studies. The primary particle size was 93 nm in Froechke et al.'s study compared to primary particle sizes of 27 and 16 nm in the present study. The larger primary particle size resulted in a higher kinetic energy per primary particle for the same impaction velocity. If the 27 nm primary particles had the same kinetic energy as the 93 nm particles, with the same density and a velocity of 71 m/s, a quick calculation results in an impaction velocity of approximately 450 m/s. Other properties, such as the adhesive force, also depend on the primary particle diameter. In an earlier study by Ihalainen et al. (Citation2012), the degree of fragmentation was higher; however, this value was estimated using a mass-based degree of fragmentation described by Froeschke et al. (Citation2003) and was not based on the number of bonds.
FIG. 7 Number of broken bonds per agglomerate and degree of fragmentation of bounced TiO2 particles.
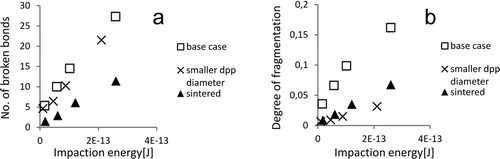
FIG. 8 Area equivalent geometric mean diameters of deposited and bounced de-agglomerated particles measured from TEM micrographs for agglomerates with primary particle sizes of (a) 27 nm and (b) 16 nm, and (c) for agglomerates with a high degree of sintering.
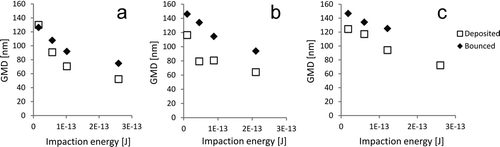
Teleki et al. (Citation2008) broke up TiO2 agglomerates using high-pressure dispersion and found that the particles disintegrated into primary particles and larger aggregates, which could not be de-agglomerated into smaller pieces even at higher pressures. The authors also showed that increasing the sintering increased the de-agglomerated fragment size. Also, Seipenbusch et al. (Citation2010) found that the degree of fragmentation of SiO2 agglomerates and aggregates reached a plateau as the impaction energy increased and that the value of the plateau decreased as the bonds between the primary particles were strengthened by a high degree of sintering. In the present study, the high degree of sintering lowered the degree of fragmentation, but the degree of fragmentation did not plateau.
presents results for the agglomerates of different types and sizes. The measurements were made for the same pressure difference, thus the impaction velocity for each case was slightly different due to the different agglomerate properties. Note that the geometric mean diameter of the bounced particles remained approximately the same even for different sizes of intact. Larger bounced agglomerates were observed for the smaller primary particle size, and the largest agglomerates were observed for the sintered particles.
shows the energies per broken bond for the different types of agglomerates. The energies for the different-sized agglomerates were quite close to each other. Even though the larger intact agglomerates required that more bonds be broken to obtain bounced particles of the same size, more kinetic energy was available because of the higher particle mass. The available kinetic energy is directly proportional to the mass of the agglomerate and also the number of bonds in an agglomerate can be estimated as being directly proportional to the mass of the agglomerate. Thus, in simplified terms, the size of the bounced particles should not be sensitive to the size of the intact particles. The calculated energy per bond of the agglomerates with a smaller primary particle size was slightly higher than that of the base case. This result was reported in de-agglomeration studies by Seipenbusch et al. (Citation2007). However, sintering increased the energy by three-fold compared to the base case, because the sintering process increased the necking between the primary particles. Note that kinetic energy was consumed not only by the break-up process but also by other processes such as the elastic and plastic deformation of the surface and the agglomerates, and more importantly, by the bounce of the particles.
FIG. 9 Mass-based fraction of the bounced unbroken and de-agglomerated particles: (a) base case, (b) case with high degree of sintering, and (c) case with a smaller primary particle size.
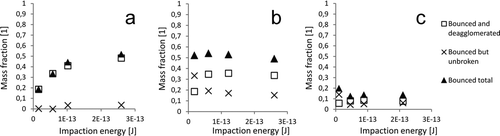
The results of the TEM analysis are shown in . Particles with an area equivalent to diameter of 235 nm and smaller were analyzed, i.e., only de-agglomerated particles were used. The deposited particles were found to be smaller than the bounced particles in almost every case. This could be explained in terms of the energy consumption between the de-agglomeration and bounce processes during impaction. If less energy is consumed on break-up, i.e., there is a larger average fragment size, more energy is available for the bounce. Larger bounced particles may have been observed for this reason. Ihalainen et al. (Citation2012) found that the surface area equivalent diameter of the deposited particles was very close to that of the bounced particles; however, only one data point was presented in their study. In the present study, the overall trend observed was that the bounced particles were larger than the deposited particles, and there was only one datum for which the bounced and deposited particles had similar sizes.
After the break-up of the agglomerate, the fragments may form new physical bonds as they collide to each other which would affect the fragment size. The significance of this process is not clear yet. However, as the kinetic energies involved were quite high, this probably does not have a significant effect on the results. Furthermore, after the bounce, the fragments will soon be diluted in the sample flow reducing the probability of re-agglomeration.
4.3. Mass Fraction of Bounced Particles
The mass concentrations of the bounced particles were calculated from lognormal fits to the SMPS size distributions, where the size-dependent effective density was used to determine the mass-based bounce fraction. In the fitting process, the geometric mean diameter and the standard deviation of the second and third modes (i.e., the singly and doubly charged intact particles) of the bounced particles were restricted to the values found for the intact particles. The geometric mean diameter of the second mode was restricted to vary between 235 and 255 nm, and the geometric standard deviation was restricted to vary between 1.05 and 1.08. The third mode of the geometric mean diameter was restricted to vary from 350 to 390 nm, and the geometric standard deviation was restricted to vary between 1.05 and 1.09. The results are shown in .
For base case (), i.e., a primary particle diameter of 27 nm, the bounce fraction increased linearly to 50%. In this case, the agglomerates broke up even at the lowest velocities investigated.
For the sintered particles (), the de-agglomerated particle bounce mass fraction increased until it saturated at 35%. Approximately 30% of the mass bounced unbroken at the lowest velocity, and this fraction decreased as the impaction velocity increased. Thus, the total bounced fraction was approximately 50% for all of the investigated velocities. The main difference between the sintered and base cases was the presence of the unbroken bounced particles. These unbroken particles resulted in a fairly high total bounce fraction of the sintered particles at the lowest velocities, even though the impaction energy was not significantly higher than in the base case. This behavior can be attributed to the energy consumption. The particles that did not break up corresponded to no or little energy being consumed in the break-up process, leaving more energy for the bounce. Seipenbusch et al. (Citation2010) also found that the degree of fragmentation decreased to zero for aggregates with complete sintering.
The bounce fractions of the de-agglomerated particles with the smaller primary particle size () exhibited a slightly increasing trend as the impaction velocity was increased. The fraction of unbroken particles was dominant at the lowest velocity and contributed a significant fraction to the total bounced particles at higher velocities. In this case, the bounce fraction of de-agglomerated particles was quite low over this velocity range compared to the other two cases. This may be attributed to smaller primary particle size, but the exact process is still unknown. The ability to store elastic energy by an agglomerate with a smaller primary particle size compared to an agglomerate with larger primary particle size may be one potential reason.
5. CONCLUSIONS
A single-stage micro-orifice impactor and a low-pressure sampling chamber were used to study the break-up and bounce of TiO2 agglomerates by impaction. The properties of the TiO2agglomerates were varied by changing the primary particle diameter, the degree of sintering, and the agglomerate size.
Simulations were performed to estimate the particle trajectories to obtain a good estimate of the impaction velocity, which is one of the key parameters in the impaction process. The ratio between the impaction velocity to the jet velocity did not remain constant over the velocity range for the impactor used in this study, but varied from 0.3 to 0.9.
The experimental results showed that the primary particle diameter and the degree of sintering affected the break-up and the bounce. Decreasing the primary particle diameter and increasing the degree of sintering both decreased the degree of fragmentation. However, the number of broken bonds decreased only slightly when the primary particle diameter decreased from 27 nm to 16 nm. A considerably lower number of broken bonds was observed for the sintered particles. The calculated energy per bond exhibited the same trend: decreasing the primary particle diameter decreased the value slightly. However, sintering the particles increased the energy by threefold.
The mass fractions of the bounced particles were affected by the properties of the TiO2 agglomerates. The change was most obvious at low impaction velocities where approximately 15%–35% of the particles bounced intact for smaller primary particles and agglomerates with a high degree of sintering. This behavior was not observed for the base case. Image analysis of the deposited particles showed that the fragment sizes of the bounced particles were larger than those of the deposited particles.
Experiments were also carried out on agglomerates of different sizes. The size of the bounced particles was not sensitive to the intact agglomerate size, because the sizes of the bounced and de-agglomerated particles were very close to each other for an intact agglomerate size of 250–400 nm.
In the near future, simulations of the agglomerate impaction will be carried to clarify how energy is consumed in the impaction processes for break up and bounce. The discrete element method LAMMPS (Lechman, Citation2010) will be used to simulate the break up and bounce of the agglomerates.
Inhalainen_et_al_supplemental_information.zip
Download Zip (435.1 KB)Acknowledgments
[Supplementary materials are available for this article. Go to the publisher's online edition of Aerosol Science and Technology to view the free supplementary files.]
This work was carried out in support of the international ARTIST II program. The authors express their gratitude to those members of the Laboratory for Thermal-Hydraulics at Paul Scherrer Institut (PSI) and members of the Fine Particle and Aerosol Technology Laboratory at the University of Eastern Finland who participated in the experimental work and construction of the facility.
REFERENCES
- Arffman , A. , Marjamaki , M. and Keskinen , J. 2011 . Simulation of Low Pressure Impactor Collection Efficiency Curves . J. Aerosol Sci , 42 ( 5) : 329 – 340 .
- Backman , U. , Tapper , U. and Jokiniemi , J. K. 2004 . An Aerosol Method to Synthesize Supported Metal Catalyst Nanoparticles . Synth. Met , 142 ( 1–3 ) : 169 – 176 .
- Chen , X. and Mao , S. S. 2007 . Titanium Dioxide Nanomaterials: Synthesis, Properties, Modifications, and Applications . Chem. Rev , 107 ( 7 ) : 2891 – 2959 .
- Froeschke , S. , Kohler , S. , Weber , A. P. and Kasper , G. 2003 . Impact Fragmentation of Nanoparticle Agglomerates . J. Aerosol Sci , 34 ( 3 ) : 275 – 287 .
- Fujishima , A. and Zhang , X. 2006 . Titanium Dioxide Photocatalysis: Present Situation and Future Approaches . Comptes. Rendus Chimie. , 9 ( 5–6 ) : 750 – 760 .
- Guntay , S. , Suckow , D. , Dehbi , A. and Kapulla , R. 2004 . ARTIST: Introduction and First Results . Nucl. Eng. Des. , 231 ( 1 ) : 109 – 120 .
- Ihalainen , M. , Lind , T. , Torvela , T. , Lehtinen , K. E. J. and Jokiniemi , J. 2012 . A Method to Study Agglomerate Breakup and Bounce During Impaction . Aerosol Sci. Technol , 46 ( 9 ) : 990 – 1001 .
- Khalil , Y. F. and Rosner , D. E. 1996 . Erosion Rate Prediction and Correlation Technique for Ceramic Surfaces Exposed to High Speed Flows of Abrasive Suspensions . Wear. , 201 ( 1–2 ) : 64 – 79 .
- Lechman , J . 2010 . Aerosol Cluster Impact and Break-up: I. Model and Implementation , Sandia National Laboratories . SAND2010-7105. Albuquerque, NM:
- Lyyränen , J. , Backman , U. , Tapper , U. , Auvinen , A. and Jokiniemi , J. 2009 . A Size Selective Nanopartile Collection Device Based on Diffusion and Thermophoresis . J. Phys.: Conf. Ser , 170 : 012011
- Lyyränen , J. , Jokiniemi , J. , Kauppinen , E. I. , Backman , U. and Vesala , H. 2004 . Comparison of Different Dilution Methods for Measuring Diesel Particle Emissions . Aerosol Sci. Technol , 38 ( 1 ) : 12 – 23 .
- Malloy , Q. G. J. , Nakao , S. , Qi , L. , Austin , R. , Stothers , C. Hagino , H. 2009 . Real-Time Aerosol Density Determination Utilizing a Modified Scanning Mobility Particle SizerAerosol Particle Mass Analyzer System RID F-4442-2010 . Aerosol Sci. Technol. , 43 ( 7 ) : 673 – 678 .
- Mandelbrot , B. 1983 . The Fractal Geometry of Nature . Earth Surf. Process. Landforms. , 8 ( 4 ) : 406 – 406 .
- Marple , V. A. 1970 . Fundamental Study of Inertial Impactors , Minneapolis, MN: Particle Technology Lab, Minnesota University . Ph.D. diss.
- Marple , V. , Rubow , K. and Behm , S. 1991 . A Microorifice Uniform Deposit Impactor (Moudi) - Description, Calibration, and use . Aerosol Sci.Technol , 14 ( 4 ) : 434 – 446 .
- Miettinen , M. , Riikonen , J. , Tapper , U. , Backman , U. , Joutsensaari , J. and Auvinen , A. 2009 . Development of a Highly Controlled Gas-Phase Nanoparticle Generator for Inhalation Exposure Studies . Hum. Exp. Toxicol. , 28 ( 6–7 ) : 413 – 419 .
- Park , K. , Cao , F. , Kittelson , D. and McMurry , P. 2003 . Relationship Between Particle Mass and Mobility for Diesel Exhaust Particles . Environ. Sci. Technol. , 37 ( 3 ) : 577 – 583 .
- Rennecke , S. and Weber , A. P. 2013a . A Novel Model for the Determination of Nanoparticle Impact Velocity in Low Pressure Impactors . J. Aerosol Sci. , 55 : 89 – 103 .
- Rennecke , S. and Weber , A. P. 2013b . The Critical Velocity for Nanoparticle Rebound Measured in a Low Pressure Impactor . J. Aerosol Sci , 58 : 135 – 147 .
- Seipenbusch , M. , Froeschke , S. , Weber , A. P. and Kasper , G. 2002 . Investigations on the Fracturing of Nanoparticle Agglomerates: First Results . Proc. Inst. Mech. Eng. E: J. Process Mech. Eng , 216 ( E4 ) : 219 – 225 .
- Seipenbusch , M. , Rothenbacher , S. , Kirchhoff , M. , Schmid , H. , Kasper , G. and Weber , A. P. 2010 . Interparticle Forces in Silica Nanoparticle Agglomerates . J. Nanopart. Res. , 12 ( 6 ) : 2037 – 2044 .
- Seipenbusch , M. , Toneva , P. , Peukert , W. and Weber , A. P. 2007 . Impact Fragmentation of Metal Nanoparticle Agglomerates . Part. Part. Syst. Char , 24 ( 3 ) : 193 – 200 .
- Teleki , A. , Wengeler , R. , Wengeler , L. , Nirschl , H. and Pratsinis , S. E. 2008 . Distinguishing Between Aggregates and Agglomerates of Flame-Made TiO2 by High-Pressure Dispersion . Powder Technol. , 181 ( 3 ) : 292 – 300 .
- Virtanen , A. , Joutsensaari , J. , Koop , T. , Kannosto , J. , Yli-Pirila , P. and Leskinen , J. 2010 . An Amorphous Solid State of Biogenic Secondary Organic Aerosol Particles . Nature. , 467 ( 7317 ) : 824 – 827 .
- Wall , S. , John , W. , Wang , H. and Goren , S. L. 1990 . Measurements of Kinetic Energy Loss for Particles Impacting Surfaces . Aerosol Sci. Technol , 12 ( 4 ) : 926 – 946 .
- Wang , H. and John , W. 1987 . Comparative Bounce Properties of Particle Materials . Aerosol. Sci. Technol. , 7 ( 3 ) : 285 – 299 .