ABSTRACT
A scanning mobility particle sizer was used to determine the size, number, and mass concentration of particle emissions from an ethanol-fueled homogeneous charge compression ignition (HCCI) engine. Semi-volatile particle composition was characterized using tandem differential mobility analysis (TDMA). Variable temperature thermal conditioning was used to gain insight into particle volatility and a catalytic stripper was used to determine the solid particle distribution. Four engine conditions were evaluated, including low to moderate range loads and motoring (deceleration, coasting). Results indicated that aerosol from a fully premixed HCCI engine under firing conditions is formed almost entirely via nucleation of semi-volatile material originating from the lubricating oil. TDMA analysis indicated 98% of total particle volume evaporated below 100°C. Results pointed towards homogeneous nucleation of precursors derived from the organic species in the lubricating oil, possibly in combination with a sulfur species. The motoring condition, with no fuel injected, exhibited the highest number and mass concentrations. During motoring, there was poor sealing leading to increased atomization of oil and associated ash emissions. Emissions were lower during firing with better sealing and much less atomization, but evaporation of the most volatile fractions of the lubricating oil still led to significant PM emissions consisting of nearly entirely semi-volatile particles containing very little ash.
© 2017 American Association for Aerosol Research
EDITOR:
1. Introduction
Alternative fuels, in-cylinder combustion strategies, and emission control technology are methods to meet current and future emission regulations. Pre-mixed, low-temperature combustion (LTC) is one broad strategy to reduce particulate matter (PM) and oxides of nitrogen (NOx) emissions of compression ignition (CI) engines (Imtenan et al. Citation2014). CI engines operating in an LTC mode feature the advantages of both diesel and spark ignition (SI) engines. In diesel engines, the ignition event is autoignition following the injection of fuel. In SI engines, the ignition event is the firing of a spark plug. A LTC engine draws in fuel and air, at least some of which is pre-mixed, and compresses the mixture until it autoignites. As such, it differs from both traditional engine cycles because it lacks a common and distinct physical event that controls the start of combustion (SOC). The degree of pre-mixing of the fuel and air varies by LTC concept. In homogeneous charge compression ignition (HCCI), all or nearly all of the fuel and air mixture is pre-mixed. In pre-mixed charge compression ignition (PCCI), only some of the air-fuel mixture is fully pre-mixed. Control of the SOC and rate of combustion are the primary operational challenges with these LTC strategies. A variant of HCCI, reactivity controlled compression ignition (RCCI), addresses SOC control using two fuels (Reitz and Duraisamy Citation2015). The efficacy of all concepts depends on the fuel used.
Ethanol, the most widely used renewable fuel in the U.S., was used as the fuel in this study to examine its characteristics as an HCCI fuel. The work reported here is part of a larger study (Franklin Citation2010) that compared the performance and emissions of ethanol, hydrogen, and ethanol/hydrogen mixtures in HCCI combustion. The combination of ethanol fuel and fully premixed HCCI combustion led to virtually “soot free” combustion, which makes particle formation and growth quite different from conventional diesel and gasoline engines. Some alternative fuels like dimethyl ether (DME), hydrogen (H2), and methane (CH4) may burn essentially “soot-free” even in conventional diesel and spark ignition engines (Arcoumanis et al. Citation2008; Korakianitis et al. Citation2011) and therefore may exhibit some similar emission characteristics.
1.1. HCCI combustion
HCCI was first termed active thermo-atmosphere combustion (ATAC) by Onishi et al. (Citation1979). It was developed to reduce emissions and increase fuel efficiency in 2-stroke SI engines during part throttle operation by exploiting lean burning auto ignition to minimize the cycle-to-cycle variability. HCCI was later adapted to 4-stroke engine applications (Najt and Foster Citation1983). HCCI engines operating un-throttled, with lean burn, and at diesel-like compression ratios have the potential for cycle efficiencies comparable with those of diesel engines. The highly dilute and premixed fuel and air charge leads to very low NOx and PM emissions. Many types of fuels are suitable for HCCI combustion, including (Equation1[1] ) high-octane fuels such as gasoline (Thring Citation1989), natural gas (Yap et al. Citation2004), and hydrogen (Gomes–Antunes Citation2008), (Equation2
[2] ) high cetane fuels such as diesel (Tsolakis and Megaritis Citation2005) and n-heptane (Lü et al. Citation2005), and (3) renewable fuels such as ethanol (Mack et al. Citation2009), DME (Shudo et al. Citation2003), and biodiesel (Tsolakis and Megaritis Citation2005).
The authors are not aware of any pure HCCI engines in current production but engines that use low temperature combustion in part of their operating range, usually at light load, have been introduced by several companies. One example is the Toyota UNIBUS (Hasegawa and Yanagihara Citation2003) and Nissan MK (Ogawa et al. Citation2000; Kawamoto et al. Citation2004). Caterpillar ACERT engines may be adapted to operate in this manner relatively easily (Nevin et al. Citation2007) but it is unclear if this has been done in any of their production engines.
1.2. Semi-volatile particle formation in engines
PM is composed mainly of solid, carbonaceous agglomerates (soot) and semi-volatile material. For conventional combustion engines most of the material found in the nucleation mode is semi-volatile but this comprises little mass. Most of the semi-volatile mass is adsorbed on the carbonaceous agglomerates that mainly comprise the accumulation mode (Kittelson Citation1998). Nucleation mode particles are formed as exhaust dilutes and cools. Nucleation is favored if there is little carbonaceous surface area on which to adsorb. It is a non-linear process so small changes in the ratio of semi-volatile precursors to carbonaceous agglomerates during dilution will influence the concentration of nanoparticles. For example, Lahde et al. (Citation2010) ran a heavy-duty diesel engine over a range of test conditions that gradually changed the amount of material in the accumulation mode while changing other conditions as little as possible. They saw a clear inverse relationship between the size of the nucleation mode and the size of the accumulation mode. Kittelson and Kraft (Citation2014) show size distribution measurements made with a diesel engine running with fuel sulfur concentrations ranging from 1 ppm to 325 ppm. A consistent pattern appeared in which the larger the concentration of soot particles in the accumulation mode, the more sulfur in the fuel was required to produce a semi-volatile nucleation mode. A similar effect was observed with solid nucleation mode particles that appeared only in the two test cases that gave the smallest amount of material in the accumulation mode. Sgro et al. (Citation2012) investigated nucleation in a GDI engine and found the only condition that produced measurable tiny solid particles was at very light load, which produced almost no accumulation mode. They argued that higher load conditions with larger accumulation mode particles led to scavenging the tiny particles before they could leave the engine. Other reports of this tradeoff have been reported (Abdul-Khalek et al. Citation1999; Khalek et al. Citation2000; Kittelson et al. Citation2002).
With soot free engines there is no soot to adsorb semi-volatile material so all of it is found in a nucleation mode—which may grow into the accumulation mode size range. A tiny solid mode related to lubricating oil ash or carbonaceous soot precursors may also be seen, for example with CNG fuel (Jayaratne et al. Citation2012) or hydrogen (Miller et al. Citation2007). Often engines operating in low temperature modes, especially partially premixed modes, still produce soot so that behavior is intermediate between conventional combustion and soot free combustion.
Recent research suggests that HCCI particle emissions from fully pre-mixed combustion consist primarily of semi-volatile material (Bullock and Olfert Citation2014). One tool to investigate properties of such particles is the catalytic stripper (CS; Swanson and Kittelson Citation2010) which is used to remove the semi-volatile component of the aerosol prior to measurement. Another method that provides more detailed information is a tandem differential mobility analyzer (TDMA) consisting of two DMAs in series with a “conditioning” apparatus in-between (Rader and McMurry Citation1986). The conditioning section can humidify, heat, or cool the sample to elucidate further the chemical and physical properties such as droplet evaporation and growth rates and the semi-volatile fraction (Rader and McMurry Citation1986, Orsini et al. Citation1999). Sakurai et al. (Citation2003) used TDMA to study diesel nanoparticle composition. They reported that nucleation mode particles from diesel engines have very high semi-volatile volume fractions with nearly all of the particle volume evaporating below 100°C. Surawski et al. (Citation2010) used a similar TDMA to study composition and volatility of PM emitted from a diesel engine fueled by diesel with supplementary ethanol fumigation. These authors showed increased ethanol energy fractions led to higher semi-volatile volume fractions of particles generated at low to moderate engine loads.
Few studies have thoroughly investigated PM emissions from HCCI engines. Kaiser et al. (Citation2002) determined PM emissions from a gasoline-fueled HCCI engine using an early direct injection (DI) strategy. HCCI combustion was achieved with intake temperatures ranging from 150°C to 200°C at a compression ratio of 15.2:1 and air-fuel equivalence ratios (λ) ranging from 2 to 18. Particle size distributions were measured for three operating conditions (λ = 2.35, 3.25, and 6.77) at 1100 rpm and for the same engine running in a direct injection spark ignition (DISI) (λ = 1) mode and a motored condition. At two of the HCCI conditions, λ = 2.35 and λ = 3.25, accumulation mode number concentrations were higher than those of DISI operation and the diameter of accumulation mode particles was larger. The presence of large accumulation mode particles was explained by the existence of some degree of diffusion burning that was a result of the DI nature of the fuel injection system and the cool operation of lean burning HCCI combustion. This creates the need for longer evaporation and mixing times to fully vaporize and mix the fuel. The λ = 6.77 condition produced fewer accumulation mode particles than either of the above mentioned HCCI conditions or the DISI condition. However, an order of magnitude increase was seen in nucleation mode number concentrations compared with the other conditions. This condition was also associated with the highest hydrocarbon (HC) emissions explained by extremely lean operation. The reduction of accumulation mode particles may have also facilitated nucleation by reducing the amount of adsorption and condensation sites.
Price et al. (Citation2007) reported on PM emissions from a gasoline HCCI engine. A DI-HCCI fueling strategy very similar to the one of Kaiser et al. (Citation2002) was used. A fueling condition of λ = 1 was maintained while valve timings and intake temperature were varied. For all conditions, particle distributions were bimodal, with the nucleation mode concentration significantly higher than the accumulation mode. One HCCI and SI comparison showed a notable increase in accumulation mode particles and decrease in nucleation mode particles for HCCI. These results are consistent with Kaiser et al. (Citation2002) where some degree of diffusion burning was present due to the DI nature of this type of HCCI.
Misztal et al. (Citation2009) used a DI-HCCI fuel system consisting of unleaded gasoline injected directly into the cylinder. PM emissions increased with increasing intake air temperature, which was attributed to enhanced fuel evaporation due to higher in-cylinder temperatures during compression. Trends of NOx and PM emissions decreasing with increasing EGR rate differed from a typical PM—NOx tradeoff curve in which a decrease in NOx leads to an increase in PM. More recently, Bullock and Olfert (Citation2014) showed the natural gas-fueled HCCI emissions were semi-volatile, with less than 5% of particle mass remaining at 100°C. Effective density measurements determined particle density was 850 kg/m3, independent of size, which is consistent with the density of lubricating oil.
Overall, previous results strongly suggest HCCI PM emissions are very closely linked to mixture homogeneity. Except for Bullock and Olfert (Citation2014), all of the aforementioned mentioned PM emission studies conducted with DI fueling systems show strong effects of diffusion burning. The objective of this work is to characterize the particle size and volatility of PM generated during HCCI combustion in which the air and fuel are fully pre-mixed. In order to clearly understand PM formation in HCCI and other low sooting engines, it is critical to understand the most basic cases of premixed compression ignition combustion that employ a fully premixed charge. Although difficult to achieve, this is the purest form of HCCI.
2. Material and methods
2.1. Engine test apparatus
Low temperature combustion research engines are derived from either a diesel or a spark ignition engine. Diesel engines tend to be larger, and are typically designed for very long service life. Consequently, they run at lower speeds and have higher oil consumption. The test engine in this study was based on a medium-duty diesel engine that would be expected to have higher oil consumption and oil related particle emissions than an engine based on a light-duty gasoline engine. The test engine, shown in , is based on a model year 2005, 4-cylinder, 5.2 l, turbo charged, DI diesel engine. It was originally equipped with common rail fuel injection and met on-road emissions standards at the time of production. Modifications were made to convert it to an HCCI engine fueled with non-denatured ethanol. The lubricating oil was Shell Rotella 15W-40, API CJ-4 grade. The common rail fuel injection system, including the injector rail, high pressure pump, and fuel distribution piping, was removed to accommodate a new intake manifold that ensured even air flow and enabled independent control of intake air temperature to each cylinder. For each condition, the intake air temperature was set such that the combustion produced the maximum indicated mean effective pressure. The EGR system was modified to allow independent control for each intake runner. The stock 18.5:1 compression ratio, piston design, and valve timings were maintained and the crankcase was vented to the atmosphere.
The diesel fuel injectors were removed and a port fuel injection system with four independently controlled injectors was installed. The injectors were oriented to focus the spray pattern on the intake port. Injectors were timed to inject in advance of intake valve opening to give adequate time for droplet evaporation. To promote evaporation of fuel droplets, the high pressure injector supply line was heated to very near the 85°C ambient pressure boiling point of ethanol and intake air temperatures were also above the fuel boiling point. Calculation of droplet lifetimes at these conditions indicated enough time for full evaporation of the fuel droplets.
Experiments were conducted at three fired loads and a motored condition, with engine speed held constant at 1500 rpm as shown in . Conditions were selected to include low to moderate engine loads with the highest load condition bounded by the onset of engine knock. Motoring occurs in vehicles during braking and downhill driving when the engine is not fueled. Emissions during motoring have been observed to contribute up to ∼25% of the total number of particles emitted during real-world driving (Rönkko et al. Citation2014; Karjalainen et al. Citation2014). The motoring condition was operated with 120°C intake air, which was in the same range used for the fired tests. This resulted in exhaust and oil temperatures of 80°C and 96°C. All measurements were made at steady state. The sampling time for each condition, after oil temperature stabilization, was in excess of an hour. The engine was not equipped with an exhaust catalyst or filter because the focus was on engine out emissions. In any case, low temperature combustion produces low temperature exhaust that may challenge traditional exhaust catalysts.
Table 1. Engine operating conditions. All conditions were tested at 1500 rpm. Oil temperature was 100°C ± 5°C for all conditions.
2.2. Exhaust dilution
A two-stage dilution system was used to dilute exhaust with temperature controlled ambient air (Abdul-Khalek et al. Citation1999). Dilution air temperature and humidity impact nanoparticle formation and therefore must be carefully controlled (Abdul-Khalek et al. Citation1999, Citation2000; Mathis et al. Citation2004; Rönkkö et al. Citation2006). A CO2 analyzer continuously monitored CO2 during the fired conditions to determine the primary dilution ratio (DR), which was 15:1. The DR during motoring was assumed to be the same.
Secondary dilution was set to 19:1 for a total DR of 285:1. All measurements were corrected for DR. Primary dilution air and the dilution tunnel were maintained at 35°C. The secondary stage dilution air temperature was 25°C. Total particle mass and number were found to be very sensitive to primary dilution conditions. For example, increasing the primary dilution temperature from 25°C to 45°C decreased the number concentration by a factor of three. In related work (Kittelson et al. Citation2011) using the same engine and pure ethanol fuel, raising the primary DR from 6 to 16 decreased the number concentrations by factors of six and nine for two mid load conditions similar to those used here. The dilution conditions selected for this work were intermediate values that gave stable, repeatable measurements. Only the primary stage of dilution was used when collecting TDMA data to increase measurement sensitivity.
2.3. Particle measurements
The exhaust aerosol size distribution was measured with a TSI model 3080 scanning mobility particle sizer (SMPS; Wang and Flagan Citation1990) consisting of a TSI model 3085 nano-differential mobility analyzer (nDMA,) and a TSI model 3025A ultrafine condensation particle counter (CPC). The SMPS was operated over a size range of 3–64 nm. All measurements included a minimum of three SMPS scans and results are shown with error bars representing one standard deviation of the mean. SMPS measurements were made with and without a CS and all CS data shown are corrected for losses using standard methods (Swanson et al. Citation2013).
The TDMA apparatus consists of a thermal conditioning section (Orsini Citation1999; Sakurai et al. Citation2003; Surawski et al. Citation2010), a long column DMA (TSI 3081; TSI Inc., Shoreview, MN, USA) as the fixed voltage DMA to size select particles prior to entry into the thermal conditioning section, and an SMPS with a nano-DMA and TSI 3025A CPC. Small differences in DMA geometry, flow rate, and power supply performance led to small differences (less than ±2 nm) in size measurement and results were corrected for sizing error. For each test condition, engine exhaust was first sampled with the fixed voltage DMA bypassed and the thermal conditioning section at ambient temperature to collect a full particle size distribution. After determining the mode of the size distribution from this measurement, the aerosol was routed through the fixed voltage DMA, with its voltage set to correspond to the mode of the initial size distribution. The temperature of the thermal conditioner was varied over a range and the change in monodisperse particle size due to evaporation was determined by subtracting the mode size determined by the SMPS from the initial mode size.
2.4. Gas measurements
An AVL SESAM FTIR was used to measure gas emissions using reference spectra developed by the manufacturer specifically for ethanol fuel. The spectrometer was operated with a sample flow of 10 L/min pulled through a heated filter and sample line maintained at 185°C. Species measured included water vapor, carbon dioxide, carbon monoxide (CO), nitric oxide (NO), nitrogen dioxide (NO2), nitrous oxide (N2O), ammonia (NH3), formaldehyde (HCHO), methane (CH4), acetylene (C2H2), ethylene (C2H4), propene (C3H6), biethylene (C4H6), acetaldehyde (CH3CHO), acrylaldehyde (C3H4O), ethanol (C2H5OH), methanol (CH3OH), and hydrogen cyanide (HCN).
3. Results and discussion
3.1. Gas measurements
shows gaseous emission measured during HCCI operation. Concentrations of CO and C2H5OH were high, resulting from incomplete combustion. NOx concentrations were extremely low as expected from low temperature combustion. Significant concentrations of formaldehyde and acetaldehyde, ∼40 ppm each, were also measured at each operating condition. Schuetzle et al. (Citation1994) identified methanol and ethanol as primary fuel precursors to formaldehyde and acetaldehyde, respectively. The high concentrations of HCN were unexpected but others have also measured significant levels of HCN in engine exhaust (Karlsson Citation2004).
3.2. Particle size distributions
Engine exhaust particle number size distributions are shown in . The Low Load and Mid Load 1 conditions produced similar total number concentrations of 5.8 × 107 part/cm3, with modes of 24 nm and 35 nm, respectively. The highest average concentration of the fired loads of 1.8 × 108 part/cm3 with a mode near 31 nm occurred at the Mid Load 2 condition. The motored engine test condition produced a total number concentration of 3.7 × 10−8 part/cm3 and a mode of 22 nm. Because no fuel was injected, these particles must consist of atomized oil and/or nucleated oil vaporized and evaporated from the cylinder walls or piston ring pack.
The total PM mass emissions rates for Motoring, Low Load, Mid Load 1 and Mid Load 2 conditions, were 0.69 g/hr, 0.05 g/hr, 0.19 g/hr, and 0.56 g/hr, respectively. Brake specific values are reported in . Note that brake specific emissions cannot be calculated for the motoring case since no power was produced. These calculations assume a density of ∼0.81 kg/m3 based on the assumed bulk constituent C32H66. The highest particle mass emission rate was observed for the motored condition, which partially results from the inability of the piston rings to seat properly during the sharp pressure drop during motored expansion. Overall, these emission levels are much lower than typical oil consumption rates of about 0.1% of fuel flow rate (Givens et al. Citation2003; Yilmaz et al. Citation2004; Apple et al. Citation2009) for a three main reasons. First, crankcase emissions, resulting from substantial blow-by of this high compression engine, account for some oil consumption and these emissions are not reflected in the particle size distributions. Second, particle size and mass distributions were highly sensitive to dilution conditions, with some dilution conditions producing much more mass (Franklin Citation2010) than the conditions reported on here. The relatively high primary dilution ratio used here favored partitioning oil into the vapor phase. Finally, some oxidation of the evaporated light ends of the lubricating oil is expected.
3.3. Volatility analysis
shows the experimental result of TDMA analysis as the change of mode diameter as a function of temperature. In addition, changes in particle diameter for evaporating droplets of pure normal alkanes, including C28H58 through C36H72, were calculated using Equation (Equation1[1] ) where the evaporation rate in the free molecular regime is expressed in terms of molecular weight (MW), a condensation coefficient (αC = 1), vapor pressure of the liquid (pd), density of the liquid (ρp), Avogadro's constant (NA), single molecule mass (m), Boltzmann's constant (k), and temperature (T) (Hinds Citation2000).
[1]
Figure 4. Evaporation profiles of PM at three fired loads and a motored load. Lines drawn to connect experimental points are to aid the eye.
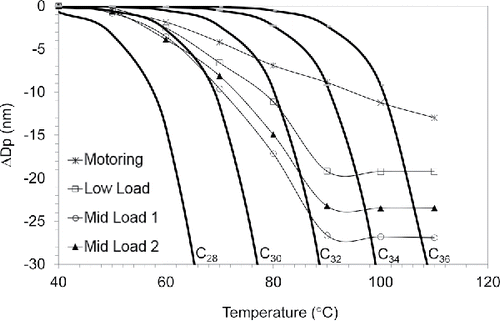
Data from all engine loads exhibit similar evaporative behavior; for each case the primary change in mobility diameter occurs below 90°C. The motored particles are much less volatile. All particles are evidently mixtures, initially losing light ends in the C30H62 range and then shrinking more slowly as less volatile materials evaporate. The calculated evaporation profiles of C30H62 and C34H66 bound the evaporation rates of motored and fired particles. Sakurai et al. (Citation2003) found diesel nanoparticles to be external mixtures of “more volatile particles” that evaporated very much like the particles measured here and “less volatile particles,” evidently coated soot agglomerates that shrank only slightly. There was no evidence of soot-like “less volatile particles” but above 90°C there is little further decrease in diameter. In all cases this corresponds to mode diameters around 5 nm. Sakurai et al. (Citation2003) also observed residue particles and attributed them to either a solid core or pyrolysis. They also tested particles of pure C32H66 and found that they closely followed the C32H66 theoretical evaporation profile but they also left a solid residue, suggesting pyrolysis or an unknown artifact of the method (Ziemann and McMurry Citation2001).
To illustrate further how these profiles affect total volume of PM, shows the remaining particle volume as a fraction of the initial particle volume measured at 40°C. Volume changes due to evaporation were calculated from mode diameter changes assuming spherical droplets. shows more than 98% of particle volume is composed of semi-volatile material at fired engine loads. Comparing the data in with the results shown by Sakurai et al. (Citation2003), very similar behavior is observed. Although a completely different fuel, engine, and combustion mode were used in the Sakurai study, the trends in remaining volume fraction of PM closely agree with those presented here. In both cases, roughly 90% of particle volume is evaporated between 50°C and 100°C. The work of Sakurai et al. (Citation2003) and related work (Tobias et al. Citation2001; Vaaraslahtiet al. 2005) showed that the majority of the mass in these “more volatile,” mainly nucleation mode, particles is derived from the lubricating oil.
There is a much higher fraction of low volatility material during motored operation, suggesting a different formation mechanism. The volume fraction curve for motored operation indicates that nearly 20% of this PM is composed of much less volatile components. The CS was used to further evaluate PM composition. Particle size distributions collected with and without a CS are shown in for the Mid Load 1 and motoring test conditions. Without the CS, the motoring size distribution has a mode of 22 nm with an average total concentration of 3.7 × 108 part/cm3. With the CS, a clear distribution can be observed with a mode near 7 nm and a total concentration of 3 × 107 part/cm3. The total PM mass concentration from motoring operation is 2,900 µg/m3 with a solid fraction measured with the CS of 0.4%. We assumed the solids are lube oil ash, of which a major constituent is calcium sulfate (Sappok et al. Citation2009), and used the density of calcium sulfate of 2.32 kg/m3 for calculations. In this case, the solid ash fraction is consistent with the known trace metal ash content of typical lubricating oils of ∼1% (Apple et al. Citation2009). While we believe the tiny, solid particles are ash, the literature contains alternative explanations. Sgro et al. (Citation2012) argues that tiny nuclei “cores” emitted by engines can be primarily carbonaceous. Other work has observed cores (De Filippo and Maricq Citation2008; Lähde et al. Citation2009) but did not determine core particle composition.
The fired condition (Mid Load 1) size distribution shows that total mass emissions were much lower (220 µg/m3), but more apparent was that measurements with the CS showed nearly zero solid particles. The estimated solid volume fraction is ∼0.02%. Low Load and Mid Load 2 conditions also show near zero solid fractions and results are not shown. These are much lower than ash fractions of typical lubricating oils, suggesting that these particles are not simply atomized oil droplets. Instead, they are likely lighter components of the oil containing less metal that have evaporated in the combustion chamber and undergo gas to particle conversion as the exhaust is cooled and diluted. Differences in motored and fired condition ash fractions point towards differences in the mechanisms of in-cylinder oil transport. The high ash fraction emissions during motoring must result from the transport of bulk oil into the cylinder as atomized droplets. On the other hand, the low ash fractions and more volatile particles emitted during fired operation indicate more emissions due to evaporation of oil films. Metallic additives in general are less volatile than lubrication oil HCs (Nemoto et al. Citation2004; Aravelli and Heibel Citation2007) and Ca and Mg based detergents, major contributors to ash, are not volatile (Watson Citation2010; Givens et al. Citation2003).
3.4. Discussion
The only possible sources of particles in this study are the fuel and the lubricating oil. The fuel was high purity undenatured anhydrous ethanol with principle impurities methanol, <0.1%, and water, 0.2%. The principal partial combustion products of ethanol, acetaldehyde, and formaldehyde (Kohse-Hoeinghaus et al. Citation2010) are much too volatile to play a role here. Furthermore, when fueled with pure hydrogen, this engine produces nearly the exact same size distributions compared to ethanol (Franklin Citation2010). Thus, we conclude the PM generated by ethanol HCCI in this study was composed of components, nearly all semi-volatile, that originated from lubricating oil. In this section, we consider the causes and sources of oil emissions and the nucleation and adsorption processes responsible for formation of particles from lube oil vapor.
3.4.1. Oil emissions
Oil emissions are the difference between oil consumption and oil oxidation that naturally occurs in-cylinder (Tornehed and Olofsson Citation2010). Oil consumption is due to evaporation, blowby, throw-off, and reverse gas flow (Yilmez et al. Citation2004). Yilmez et al. (Citation2004) suggest oil transport via reverse gas flow through the ring pack is high at idle and drops, as load is increased to roughly 50%, where it stabilizes. The increase in reverse gas flow oil transport is attributed to a decrease in blowby as load is decreased which leaves more oil available on piston ring and top land surfaces for transport into the cylinder via reverse gas flow. Piston rings are generally designed to seat best when operating at high engine loads, thus high in-cylinder pressures. At very low loads, such as motoring, ring seating is likely at its worst. Motoring pressures were ∼5 MPa, high enough to provide a significant pressure gradient to drive reverse gas flow processes. Additionally, oil throw off from the top piston ring, a function of inertial effects due to piston motion (Watson Citation2010), contributes to atomization. The engine was motored at 1500 rpm, the same speed as the fired conditions, giving a similar set of driving forces for oil throw off in all tests, but the presence of more oil on the ring would likely lead to more throw off during motoring. Liquid oil consumption is the only means of transport of detergents containing Ca and Mg, primary ash constituents, into the combustion chamber because these additives are not volatile (Watson Citation2010; Givens et al. Citation2003). Thus many factors lead to more liquid oil consumption during motoring than during firing and the introduction of more ash metals into the combustion chamber and ultimately into the exhaust. Under fired conditions, liquid oil consumption is less and higher in-cylinder temperatures promote evaporation.
Studies of the role of evaporation in engine oil consumption showed that it could account for up to 35% and 17% of oil consumption, respectively, in a spark ignition engine (Yilmaz et al. Citation2002) and a diesel engine (Audette and Wong Citation1999). Both studies showed a very strong dependence of the evaporation rate on liner temperature and consequently coolant temperature. The liner temperature also increased with gas temperatures but was much more closely linked to coolant temperature. Oil films were found to be very thin, 1 mm to 10 mm, so that the film temperature was very close to the wall temperature. Yilmaz et al. (Citation2002) found that at moderate load conditions the evaporation rate of a standard 10W-30 mineral oil increased sevenfold as the liner temperature increased from 80 to 110°C. The rate of evaporation was also found to depend strongly on oil volatility, especially front end volatility. Yilmaz et al. (Citation2002) showed that at light ends, the first 6% evaporated in a distillation curve accounted for 80% of the evaporative loss. Coolant and wall temperatures were not measured in our work but intake air temperature was used to control combustion and oil temperature was maintained at 100°C ± 5°C. Other prevailing conditions (intake air, exhaust temperature, etc.) are shown in .
Bullock and Olfert (Citation2014) measured oil particle emissions from monograde oil (SAE 30) during motoring. Number emissions were similar to those observed here but the particles were larger, 65 nm versus 22 nm, so mass emissions were much higher. Furthermore, the particles were much more volatile than those observed here. Several factors may explain these differences. In this work, intake air was preheated to 120°C, while they used unheated air. Preheating the air raises the temperatures throughout the cycle and would lead to more evaporation of light ends so that liquid oil leaving the cylinder would be less volatile. They also used a lower primary dilution ratio, 10 versus 15. This would lead to less evaporation during sampling, again favoring the survival of more volatile particles. There may also be differences in the volatility of the oil itself and other differences in in-cylinder thermal processing.
3.4.2. Nucleation processes
As discussed earlier, oil consumption during motoring is mainly due to throw off or atomization of liquid oil that has reached the top ring. These liquid oil droplets partially evaporate and oxidize on exposure to in-cylinder gases that can reach temperatures approaching 800°C even during motoring. Their measured ash mass fraction of 0.4% is low compared to the expected ash fraction of this oil type of about 1%. This is partially explained by the fact that the only ash constituents that will survive the CS are calcium (Ca) and magnesium (Mg). Zinc (Zn) additives are volatile, and Zn may be as much as 1/3 of the metal in the oil. Furthermore, the number concentration of solid particles in the motoring test, (shown in ) is only about 1/10 of the total particle number concentration. These concentrations should be equal if we are measuring a solid ash core of atomized particles. Part of the discrepancy may be due to particles below measurement range of the instrument (3 nm) and part may be due to under correction of losses in the CS, although these corrections may account for factors of 2 or 3, not 10. Thus it appears that even in the motoring case some nucleation is occurring.
On the other hand, during firing, evaporation of more volatile oil components and subsequent nucleation are the likely mechanisms but details of the nucleation process are not clear. Experiments and modeling have shown that species that play a predominant role in nucleation and growth in diesel exhaust are sulfuric acid and low-volatility hydrocarbons (Mirabel and Katz Citation1974; Khalek et al. Citation2000; Lemmetty et al. Citation2006; Du and Yu Citation2008; Arnold et al. Citation2012; Rönkkö et al. Citation2013). Sulfur in fuel and lube oil is converted into SO2 during the combustion process. Subsequent heteromolecular sulfuric acid-water nucleation leads to the formation of nucleation mode particles about 1 nm in diameter (Mirabel and Katz Citation1974; Khalek et al. Citation2000). Growth occurs via condensation of sulfuric acid and hydrocarbon vapors. The growth rate depends on the types and concentrations of growth species, the concentration of carbonaceous aggregates and details of the exhaust/dilution process (Khalek et al. Citation2000).
The propensity for sulfuric acid particles to form via homogeneous nucleation is described by Equation (Equation2[2] ), which is the ratio of the actual concentration of sulfuric acid to the concentration of acid required to produce a nucleation rate of 1 particle/cm3/s (Seinfeld and Pandis Citation1998) or C/C*. Sulfuric acid nuclei are expected to form when C/C* > 1. A model using the sulfur concentrations, temperatures, and dilution ratios as inputs was used to evaluate the likelihood of sulfuric acid nucleation for the Low Load condition. Some values were estimated based on likely high and low values. The lube oil sulfur was not measured but the regulated limit for CJ4 oil is 4,000 ppm. In this case there is essentially no sulfur in the fuel; the only source is the lubricating oil. The efficiency of converting lube sulfur to SO3 was estimated to be 2% or 6%. The low estimate is a typical conversion efficiency in raw exhaust (Cooper and Roth Citation1991) and the high estimate is based on Kittelson et al. (Citation2008) findings that lube oil sulfur forms more sulfate than fuel derived sulfur by a factor of about three in an oxidation catalyst. It is not clear if this finding extends to the formation potential in raw exhaust but it is a reasonable upper bound. Other values including dilution air temperature and RH were set to match experimental conditions.
[2]
Results from this calculation for the Mid Load 1 fired condition shows that a peak C/C* ratio of about was 0.5 was reached when all of the very high upper-bound estimates were used. This suggests that it is unlikely for sulfuric acid nuclei to form based on homogeneous nucleation alone. There are other possible explanations for nucleation in this system. Modeling results show the presence of ammonia increases nucleation rates in sulfuric acid/water systems (Lemmetty et al. Citation2007). However, concentrations of ammonia in exhaust gas were very low—0.2 ppm for the motored case but lower than the detection limit (∼0.1 ppm) for the fired cases. These measurements are consistent with Bielaczyc et al. (Citation2012), who reported measurements of ammonia in the 0.1 to 1 ppm range and Keenan and Thomson (Citation2004) reported ammonia was “not observed,” i.e., below detection limit of a few ppm. Heterogeneous nucleation of lube-oil vapor with existing solid particles (De Filippo and Maricq Citation2008) is also not a sufficient explanation in all cases because the concentration of solid particles was ∼10% of the total concentration during motoring and only ∼0.02% while firing. Furthermore, the strong dependence of total number on dilution conditions is inconsistent with heterogeneous nucleation on a fixed concentration of solid particles.
Homogeneous nucleation of hydrocarbons occurs at much higher concentrations than required for sulfuric acid. Similar work in a low temperature combustion system concluded hydrocarbon concentrations were too low for homogeneous nucleation and suggested that unknown, very low volatility species are responsibility for nucleation (Lucachick et al. Citation2016). This is consistent with other findings that other low volatility hydrocarbons, not found in lubricating oil but potentially formed when subjected to high temperature cylinder conditions, such as organic acids, impact nucleation (Arnold et al. Citation2012). Furthermore, very low volatility oxygenated hydrocarbons have been measured in diesel nucleation mode particles (Inoue et al. Citation2006). Other work points towards simultaneous nucleation of sulfuric and organic vapors as the explanation that best fits experimental data (Pirjola et al. Citation2015). A better understanding of nucleation in exhaust in the presence of very low sulfuric acid concentrations is needed.
4. Conclusions
Particle emissions from an ethanol HCCI engine were characterized using a SMPS and particle volatility was analyzed using TDMA and CS techniques. Particles were nearly entirely semi-volatile and in the nucleation mode size range. Number and mass were related to engine load for fired operating conditions. TDMA analysis indicated that HCCI combustion generated PM was almost entirely semi-volatile. Ninety-eight percent of total particle volume evaporated below 100°C. The volatility of these particles was found to be in the range of C30 to C34 normal alkanes. Typical partial combustion products of ethanol, e.g., acetaldehyde and formaldehyde, are much more volatile than this and very unlikely to be the source. Thus, these particles must be formed from the lubricating oil. Additional analysis was done using the CS. During fired operation, the solid (ash) content of these particles was very low. It was much lower than the ash content of the lubricating oil. Thus, the particles likely are formed by evaporation of oil from cylinder surfaces and subsequent nucleation and growth. During fired operation, oil consumption was mainly due to evaporation rather than atomization of oil. On the other hand, during motoring, CS measurements showed ash content similar to the lube oil itself, suggesting that the particles were formed from liquid oil reaching the top piston ring and subsequently atomized.
These results suggest that for low temperature combustion modes that produce very little soot, particle emissions are composed almost entirely of semi-volatile components formed from evaporation and subsequent nucleation of the lubricating oil components. Evaluation of the possible routes of nucleation strongly suggests that low volatility materials formed from lube-oil hydrocarbons, perhaps organic acids or partially oxygenated hydrocarbons rather than or in combination with sulfuric acid are responsible for particle formation and growth. This differs from the typical route of particle formation in diesel engines with emission control devices. Differences in oil composition and the sensitivity of evaporation to temperature may lead to oil particles from different engines that have rather different physical and thermal properties, which in turn may further impact particle formation and growth.
References
- Arcoumanis, C., Bae, C., Crookes, R., and Kinoshita, E. (2008). The Potential of Di-methyl Ether (DME) as an Alternative Fuel for Compression-ignition Engines: A review. Fuel, 87(7):1014–1030.
- Abdul-Khalek, I., Kittelson, D., and Brear, F. (2000). Nanoparticle Growth During Dilution and Cooling of Diesel Exhaust: Experimental Investigation and Theoretical Assessment. SAE Technical Paper Series, 2000-01-0515.
- Abdul-Khalek, I., Kittelson, D. B., and Brear, F. (1999). The Influence of Dilution Conditions on Diesel Exhaust Particle Size Distribution Measurement. SAE Technical Paper Series, 1999-01-1142.
- Apple, J., Gladis, D., Watts, W., and Kittelson, D. (2009). Measuring Diesel Ash Emissions and Estimating Lube Oil Consumption Using a High Temperature Oxidation Method. SAE Int. J. Fuels Lubr., 2(1):850–859.
- Aravelli, K., and Heibel, A. (2007). Improved Lifetime Pressure Drop Management for Robust Cordierite (RC) Filters with Asymmetric Cell Technology (ACT). SAE Technical Paper Series Series, 2007-01-0920.
- Arnold, F., Pirjola, L., Rönkkö, T., Reichl, U., Schlager, H., Lähde, T., Heikkilä, J., and Keskinen, J. (2012). First Online Measurements of Sulfuric Acid Gas in Modern Heavy-Duty Diesel Engine Exhaust: Implications for Nanoparticle Formation. Environ.Sci. Technol., 46(20):11227–11234.
- Audette, W. E., and Wong, V. W. (1999). A Model for Estimating Oil Vaporization from the Cylinder Liner as a Contributing Mechanism to Engine Oil Consumption. SAE Technical Paper Series, 1999-01-1520.
- Bielaczyc, P., Szczotka, A., Swiatek, A., and Woodburn, J. (2012). Investigations of Ammonia Emissions from Euro 5 Passenger Cars over a Legislative Driving Cycle. Proceedings of the FISITA 2012 World Automotive Congress; Springer-Verlag, Berlin, 189:671–685.
- Bullock, D. S., and Olfert, J. S. (2014). Size, Volatility, and Effective Density of Particulate Emissions from a Homogeneous Charge Compression Ignition Engine Using Compressed Natural Gas. J. Aerosol. Sci., 75:1–8.
- Cooper, B.J., and Roth, S.A. (1991). Flow-through Catalysts for Diesel Engine Emissions Control. Platinum Met. Rev., 35:178–187.
- De Filippo, A., and Maricq, M.M. (2008). Diesel Nucleation Mode Particles: Semivolatile or Solid? Environ. Sci. Technol., 42(21):7957–7962.
- Du, H., and Yu, F. (2008). Nanoparticle Formation in the Exhaust of Vehicles Running on Ultra-low Sulfur Fuel. Atmos. Chem. Phys., 8:4729–4739.
- Franklin, L. (2010). Effects of Homogeneous Charge Compression Ignition (HCCI) Control Strategies on Particulate Emissions of Ethanol Fuel. Ph.D. thesis, University of Minnesota.
- Givens, W., Buck, W., Jackson, A., Kaldor, A. et al. (2003). Lube Formulation Effects on Transfer of Elements to Exhaust After-Treatment System Components. SAE Technical Paper Series, 2003-01-3109.
- Givens, W.A., Buck, W.H., JacksonA., Kaldor, A., Hertzberg, A., Moehrmann, W., Mueller-Lunz, S., PelzN., and Wenninger, G. (2003). Lubricant Formulation Effects on Transfer of Elements to Exhaust After-treatment System Components. SAE Technical Paper Series, 2003-01-3109.
- Gomes Antunes, J. M., Mikalsen, R., and Roskilly, A. P. (2008). An Investigation of Hydrogen-fueled HCCI Engine Performance and Operation. Int. J. Hydrogen Energy, 33(20):5823–5828.
- Hasegawa, R., and Yanagihara, H. (2003). HCCI Combustion in DI Diesel Engine. SAE Technical Paper Series, 2003-01-0745.
- Hinds, W.C. (2000). Aerosol Technology: Properties, Behavior, and Measurement of Airborne Particles 2nd Ed. John Wiley & Sons, Hoboken, NJ.
- Imtenan, S., Varman, M., Masjuki, H.H., Kalam, M.A., Sajjad, H., Arbab, M.I., and Fattah, I.M. (2014). Impact of Low Temperature Combustion Attaining Strategies on Diesel Engine Emissions for Diesel and Biodiesels: A review. Energy Convers. Manage., 80:329–356.
- Inoue, M., Murase, A., Yamamoto, M., and Kubo, S. (2006). Analysis of Volatile Nanoparticles Emitted from Diesel Engine using TOF-SIMS and Metal-assisted SIMS (MetA-SIMS). Appl. Surface Sci., 252(19):7014–7017.
- Jayaratne, E., Meyer, N., Ristovski, Z., and Morawska, L. (2012). Volatile Properties of Particles Emitted by Compressed Natural Gas and Diesel Buses During Steady-state and Transient Driving Modes. Environ. Sci. Technol., 46:196–203.
- Karjalainen, P., Pirjola, L., Heikkilä, J., Lähde, T., Tzamkiozis, T., Ntziachristos, L., Keskinen, J., and Rönkkö, T. (2014). Exhaust Particles of Modern Gasoline Vehicles: Laboratory and On-Road Study. Atmos. Environ., 97:262–270.
- Karlsson, H. L. (2004). Ammonia, Nitrous Oxide and Hydrogen Cyanide Emissions from Five Passenger Vehicles. Sci. Total Environ., 334–335:125–132.
- Kaiser, E. W., Yang, J., Culp, T., and Maricq, M. M. (2002). Homogeneous Charge Compression Ignition Engine-Out Emissions—Does Flame Propagation Occur in Homogeneous Charge Compression Ignition? Int. J. Engine Res., 3(4):185–195.
- Kawamoto, K., Araki, T., Shinzawa, M., Kimura, S. et al. (2004). Combination of Combustion Concept and Fuel Property for Ultra-Clean DI Diesel. SAE Technical Paper Series, 2004-01-1868.
- Keenan, M., and Thomson, J. (2004). The Challenges of Meeting Future Emissions Legislation with a Novel Low Precious Metal TWC. SAE Technical Paper Series, 2004-01-2984.
- Korakianitis, T., Namasivayam, A.M., and Crookes, R.J. (2011). Natural-gas Fueled Spark-ignition (SI) and Compression-ignition (CI) Engine Performance and Emissions. Prog.Energy Combust. Sci., 37(1):89–112.
- Kittelson, D., Watts, W., and Johnson, J. (2002). Diesel Aerosol Sampling Methodology, CRC E-43, final report No.E-43. Available at: http://www.me.umn.edu/centers/mel/reports/crce43ts.pdf
- Kittelson, D. B. (1998). Engines and Nanoparticles: A Review. J. Aerosol Sci., 29(5–6):575–588.
- Kittelson, D., and Kraft, M. (2014). Particle Formation and Models. Encyclopedia of Automotive Engineering. John Wiley & Sons Ltd, Chichester, pp. 107–130.
- Kittleson, D., Bika, A., Fang, W., Franklin, L., and Huang, B. (2011). Particles from Soot Free Engines. 15th ETH-Conference on Combustion Generated Nanoparticles, Zurich, Switzerland.
- Kittelson, D. B., Watts, W.F., Johnson, J.P., Thorne, C., McCann, C., Payne, M., Goodier, S., Warrens, C., Preston, H., Zink, U., Pickles, D., Goersmann, C., Twigg, M.V., Walker, A.P., and Boddy, R. (2008). Effect of Fuel and Lube Oil Sulfur on the Performance of a Diesel Exhaust Gas Continuously Regenerating Trap. Environ. Sci. Technol., 42(24):9276–9282.
- Kohse-Hoinghaus, K., Osswald, P., Cool, T. A., Kasper, T., Hansen, N., Qi, F., Westbrook, C. K., and Westmoreland, P. R. (2010). Biofuel Combustion Chemistry: From Ethanol to Biodiesel. Angew. Chem., Int. Ed., 49:3572–3597.
- Lähde, T., Rönkkö, T., Virtanen, A., Solla, A., Kytö, M., Söderström, C., and Keskinen, J. (2010). Dependence between Nonvolatile Nucleation Mode Particle and Soot Number Concentrations in an EGR Equipped Heavy-Duty Diesel Engine Exhaust. Environ. Sci. Technol., 44(8):3175–3180.
- Lähde, T., Rönkkö, T., Virtanen, A., Schuck, T.J., Pirjola, L., Hämeri, K., Kulmala, M., Arnold, F., Rothe, D., and Keskinen, J. (2009). Heavy-duty Diesel Engine Exhaust Aerosol Particle and Ion Measurements. Environ. Sci. Technol., 43(1):163–168.
- Lemmetty, M., Pirjola, L., Makela, J. M., Ronkko, T., and KeskinenJ. (2006). Computation of Maximum Rate of Water-sulphuric Acid Nucleation in Diesel Exhaust. J. Aerosol Sci., 37:1596–1604.
- Lemmetty, M., Vehkamäki, H., Virtanen, A., Kulmala, M., and Keskinen, J. (2007). Homogeneous Ternary H2SO4–NH3–H2O Nucleation and Diesel Exhaust: a Classical Approach. Aerosol Air Qual. Res., 7:489–499.
- Lucachick, G., Curran, S., Storey, J., PrikhodkoV., and Northrop, W. F. (2016). Volatility Characterization of Nanoparticles from Single and Dual-Fuel Low Temperature Combustion in Compression Ignition Engines. Aerosol Sci. Technol., 50(5):436–447.
- Lü, X., Chen, W., and Huang, Z. (2005). A Fundamental Study on the Control of the HCCI Combustion and Emissions by Fuel Design Concept Combined with Controllable EGR. Part 1.The Basic Characteristics of HCCI Combustion. Fuel, 84(9):1074–1083.
- Mack, J. H., Aceves, S. M., and Dibble, R. W. (2009). Demonstrating Direct Use of Wet Ethanol in a Homogeneous Charge Compression Ignition (HCCI) Engine. Energy, 34(6):782–787.
- Mathis, U., Ristimäki, J., Mohr, M., Keskinen, J., Ntziachristos, L., Samaras, Z., et al. (2004). Sampling Conditions for the Measurement of Nucleation Mode Particles in the Exhaust of a Diesel Vehicle. Aerosol Sci. Technol., 38(12):1149–1160.
- Miller, A. L., Stipe, C. B., Habjan, M. C., and Ahlstrand, G. G. (2007). Role of Lubrication Oil in Particulate Emissions from a Hydrogen-Powered Internal Combustion Engine. Environ. Sci. Technol., 41(19):6828–6835.
- Misztal, J., Xu, H., Tsolakis, A., Wyszynski, M. L., Constandinides, G., Price, P., et al. (2009). Influence of Inlet Air Temperature on Gasoline HCCI Particulate Emissions. Combustion Sci. Technol., 181(5):695–709.
- Mirabel, P., and Katz, J. L. (1974). Binary Homogeneous Nucleation as a Mechanism for the Formation of Aerosols. J. Chem. Phys., 60:1138–1144.
- Najt, P. M., and Foster, D. E. (1983). Compression-ignited Homogeneous Charge Combustion. SAE Technical Paper Series, 830264.
- Nemoto, S., Kishi, Y., Matsuura, K., Miura, M., et al. (2004). Impact of Oil-derived Ash on Continuous Regeneration-type Diesel Particulate Filter - JCAPII Oil WG Report. SAE Technical Paper Series, 2004-01-1887.
- Nevin, R., Sun, Y., Gonzalez, D. M., and Reitz, R. (2007). PCCI Investigation Using Variable Intake Valve Closing in a Heavy Duty Diesel Engine. SAE Technical Paper Series, 2007-01-0903. doi:10.4271/2007-01-0903.
- Ogawa, H., Kimura, S., Koike, M., and Enomoto, Y. (2000). A Study of Heat Rejection and Combustion Characteristics of a Low-temperature and Pre-mixed Combustion Concept Based on Measurement of Instantaneous Heat Flux in a Direct-Injection Diesel Engine. SAE Technical Paper Series, 2000-01-2792.
- Onishi, S., Han Jo, S., Shoda, K., Do Jo, P., and Kato, S. (1979). Active Thermoatmosphere Combustion (ATAC): A New Combustion Process for Internal Combustion Engines. SAE Technical Paper Series, 790501.
- Orsini, D. A., Wiedensohler, A., Stratmann, F., and Covert, D. S. (1999). A New Volatility Tandem Differential Mobility Analyzer to Measure the Volatile Sulfuric Acid Aerosol Fraction. J. Atmos.Ocean. Technol., 16(6):760–772.
- Pirjola, L., Karl, M., Rönkkö, T., and Arnold, F. (2015). Model Studies of Volatile Diesel Exhaust Particle Formation: Organic Vapours Involved in Nucleation and Growth? Atmos. Chem. Phys. Discuss., 15:4219–4263.
- Price, P., Stone, R., Misztal, J., Xu, H., Wyszynski, M., Wilson, T., et al. (2007). Particulate Emissions From a Gasoline Homogeneous Charge Compression Ignition Engine. SAE Technical Paper Series, 2007-01-0209.
- Rader, D. J., and McMurry, P. H. (1986). Application of the Tandem Differential Mobility Analyzer to Studies of Droplet Growth or Evaporation. J Aerosol Sci., 17(5):771–787.
- Reitz, R.D., and Duraisamy, G. (2015). Review of High Efficiency and Clean Reactivity Controlled Compression Ignition (RCCI) Combustion in Internal Combustion Engines. Prog. Energy Combust. Sci., 46:12–71.
- Rönkkö, T., Lähde, T., Heikkilä, J., Pirjola, L., Bauschke, U., Arnold, F., Schlager, H., Rothe, D., Yli-Ojanperä, J., and Keskinen, J. (2013). Effects of Gaseous Sulphuric Acid on Diesel Exhaust Nanoparticle Formation and Characteristics. Environ. Sci. Technol., 47(20):11882–11889.
- Rönkkö, T., Virtanen, A., Vaaraslahti, K., Keskinen, J., Pirjola, L., and Lappi, M. (2006). Effect of Dilution Conditions and Driving Parameters on Nucleation Mode Particles in Diesel Exhaust: Laboratory and On-road Study. Atmos. Environ., 40:2893–2901.
- Ronkko, T., Pirjola, L., Ntziachristos, L., Heikkila, J., Karjalainen, P., Hillamo, R., and Keskinen, J. (2014). Vehicle engines produce nanoparticles even when not fuelled. Environ. Sci. Technol., 48:2043–2050.
- Sakurai, H., Tobias, H. J., Park, K., Zarling, D., Docherty, K. S., Kittelson, D. B., et al. (2003). On-line Measurements of Diesel Nanoparticle Composition and Volatility. Atmos. Environ., 37(9–10):1199–1210.
- Sappok, A., Santiago, M., Vianna, T., and Wong, V. (2009). Characteristics and Effects of Ash Accumulation on Diesel Particulate Filter Performance: Rapidly Aged and Field Aged Results. SAE Technical Paper Series, 2009-01-1086.
- Schuetzle, D., Siegl, W. O., Jensen, T. E., Dearth, M. A., Kaiser, E. W., Gorse, R., Kreucher, W., and Kulik, E. (1994). The Relationship Between Gasoline Composition and Vehicle Hydrocarbon Emissions: A Review of Current Studies and Future Research Needs. Environ. Health Perspect., 102(Suppl. 4):3–12.
- Seinfeld, J. H., and Pandis, S. N. (1998). Atmospheric Chemistry and Physics: from Air Pollution to Climate Change. John Wiley & Sons, Hoboken, NJ.
- Sgro, L. A., Sementa, P., Vaglieco, B. M., Rusciano, G., D'anna, A., and Minutolo, P. (2012). Investigating the Origin of Nuclei Particles in GDI Engine Exhaust. Combust. Flame, 159(4):1687–1692.
- Surawski, N. C., Miljevic, B., Roberts, B. A., Modini, R. L., Situ, R., Brown, R. J., et al. (2010). Particle Emissions, Volatility, and Toxicity from an Ethanol Fumigated Compression Ignition Engine. Environ. Sci. Technol., 44(1):229–235.
- Shudo, T., Ono, Y., and Takahashi, T. (2003). Ignition Control by DME-reformed Gas in HCCI Combustion of DME. SAE Technical Paper Series, 2003-01-1824.
- Swanson, J., and Kittelson, D. (2010). Evaluation of Thermal Denuder and Catalytic Stripper Methods for Solid Particle Measurements. J. Aerosol Sci., 41(12):1113–1122.
- Swanson, J., Kittelson, D., Bergmann, A., Giechaskiel, B., and Twigg, M. (2013). A Miniature Catalytic Stripper for use in a Solid Particle Counting System for Particles <23 Nanometers. SAE Int. J. Fuels Lubr., 6(2), doi:10.4271/2013-01-1570.
- Thring, R. H. (1989). Homogeneous Charge Compression Ignition (HCCI) Engines. SAE Tech. Paper Ser., 892068.
- Tobias, H. J., Beving, D. E., Ziemann, P. J., Sakurai, H., Zuk, M., McMurry, P. H., et al. (2001). Chemical Analysis of Diesel Engine Nanoparticles using a Nano-DMA/Thermal Desorption Particle Beam Mass Spectrometer. Environ. Sci. Technol., 35(11):2233–2243.
- Tornehed, P. and Olofsson, U. (2010). Towards a Model for Engine Oil Hydrocarbon Particulate Matter. SAE Int. J. Fuels Lubr., 3(2):543–548.
- Tsolakis, A., and Megaritis, A. (2005). Partially Premixed Charge Compression Ignition Engine with On-Board H2 Production by Exhaust Gas Fuel Reforming of Diesel and Biodiesel. Int. J. Hydrogen Energy, 30(7):731–745.
- Vaaraslahti, K., Keskinen, J., Giechaskiel, B., Solla, A., Murtonen, T., and Vesala, H. (2005). Effect of Lubricant on the Formation of Heavy-Duty Diesel Exhaust Nanoparticles. Environ. Sci. Technol., 39:8497–8504.
- Watson, S.A.G. (2010). Lubricant-Derived Ash—In-Engine Sources and Opportunities for Reduction. Ph.D. thesis, Massachusetts Institute of Technology.
- Wang, S. C., and Flagan, R. C. (1990). Scanning Electrical Mobility Spectrometer. Aerosol Sci. Technol., 13(2):230–240.
- Yilmaz, E., Tian, T., Wong, V. W., and Heywood, J. B. (2002). An Experimental and Theoretical Study of the Contribution of Oil Evaporation to Oil Consumption. SAE Tech. Paper Ser., 2002-01-2684.
- Yilmaz, E., Tian, T., Wong, V. W., and Heywood, J. B. (2004). The Contribution of Different Oil Consumption Sources to Total Oil Consumption in a Spark Ignition Engine. SAE Tech. Paper Ser., 2004-01-2909.
- Yap, D., Megaritis, A., Peucheret, S., and Wyszynski, M. L. (2004). Effect of Hydrogen Addition on Natural Gas HCCI Combustion. SAE Tech. Paper Ser., 2004-01-1972.
- Ziemann, P., and McMurry, P. (2001). Chemical Analysis of Diesel Nanoparticles Using a Nano-DMA/Thermal Desorption Particle Beam Mass Spectrometer. Final Report for Phase 2, Coordinating Research Council Contract No. E-43-4.