ABSTRACT
Soot particle removal performance of two types of metallic filter media, sintered metal powder and sintered metal fiber, is experimentally evaluated as potential improvements to conventional ceramic filtration media for gasoline direct injection (GDI) engine PM after-treatment application. Soot collection efficiency and flow resistance of several grades of metallic media are measured at temperatures of 25, 350, and 650°C and a range of representative filtration velocities for sub-micrometer soot particles generated from a propane flame. Theoretical collection efficiency based on single fiber efficiency theory shows good agreement with experimental data for nearly spherical KCl particles at 350°C. Improved collection efficiency is observed for soot particles in the interception-dominated size range above ∼100 nm due to enhanced interception length. Soot collection is slightly enhanced at higher temperature, which is consistent with model predictions. Sintered metal fiber media are found capable of removing ∼75% of soot particles by mass with an incremental flow resistance of less than 1.5 kPa under 10 cm/s and 350°C, which is promising for gasoline particulate filter (GPF) application. The media level figure of merit (FOM) is used to quantify the soot collection efficiency versus flow resistance tradeoff of all media tested. It is found that due to their more open structure (higher porosity) sintered metal fiber media have FOMs nearly one order of magnitude higher than those of sintered metal powder media, and by analogy those of conventional wall flow ceramic media. This suggests that sintered metal fiber media represents an attractive alternative to ceramic media for designing GPFs; however, further research into creating comparable surface area to the honeycomb structures used for wall flow filters is needed to extract the full potential of metal fiber media.
Copyright © 2017 American Association for Aerosol Research
EDITOR:
Introduction
State-of-the-art down-sized gasoline direct injection (GDI) engines with boosting technology have enabled high specific power, low fuel consumption, and rapid catalyst light-off compared with conventional port fuel injection (PFI) engines (Yi et al. Citation2009). However, spraying fuel directly into the engine cylinder makes GDI engines more susceptible to particulate matter (PM) formation than their PFI counterparts due to liquid fuel impingement onto piston and cylinder surfaces and incomplete air fuel mixing, especially during cold-start and at aggressive acceleration points (Chan et al. Citation2013, Citation2012; Fu et al. Citation2014; Sobotowski et al. Citation2015; Zhang and McMahon Citation2012). This PM is primarily soot in the form of ∼100 nm fractal-like aggregates, but includes also ash, metallic abrasion particles, sulfate, semi-volatile hydrocarbons, and silicates.
Light duty vehicle sales in the US are currently about 15 million/year, and more than half of these are expected to use GDI engines by 2020 (U.S. Dept. of Energy Citation2015). The numbers are roughly similar for Europe and Asia. To avoid backsliding in air quality from the anticipated fleet change, in 2012 the California Air Resources Board adopted LEV III amendments to its Low Emissions Vehicle regulations. These call for a phased-in reduction of the PM emissions standard from 10 to 3 mg/mi over the 2017–2021 model years and then to 1 mg/mi between 2025 and 2028. The United States Environmental Protection Agency (EPA) promulgated its Tier III standards, which will lower the light duty vehicle PM standard to 3 mg/mi. In Europe, the particulate number standard for light-duty GDI vehicles in current Euro-6 legislation is 6.0 × 1011 particles/km. Such low emission levels are difficult to achieve without exhaust filtration. Therefore, a cost-effective exhaust gasoline particulate filter (GPF) specific to the needs of GDI vehicles is of high interest to lower PM emissions to the levels required by these recent reductions in particle mass and number emission regulations.
Monolithic ceramic wall flow type filters have been successfully applied for diesel vehicle PM emission after-treatment, known as diesel particulate filters (DPF) (Guan et al. Citation2015). But this filter type may not be optimal for GDI engines, which require less filtration efficiency and are more sensitive to backpressure than diesel engines. DPFs have an initial soot removal efficiency of about 70–90%, which quickly rises to >99% owing to the soot cake that forms on the channel walls. However, the internal pore structures of conventional ceramic wall flow filters and the soot cake introduce a backpressure on the exhaust flow that reduces fuel economy. This penalty is relatively higher for GDI engine as compared to diesel engines. This has led to the development of higher porosity ceramic substrates, but with a risk of lower mechanical and thermal durability.
The present study of alternative exhaust filters is motivated by the current needs for GDI engine PM after treatment, but the metal media examined here have potentially broader application to combustion aerosol filtration. Metallic filtration material has been widely used in various hot gas filtration applications, including catalyst recovery in chemical processes, clean process gases in chemical plants, clean combustion gases and waste incineration, power generation and coal gasification. In addition to typical 316L stainless steel, other alloys are available to meet special requirements, such as high temperature or chemical resistance. Moreover, a more uniform temperature distribution during thermal regeneration of GPFs could be achieved using metallic versus ceramic filter material due to its better thermal conductivity.
Metallic filter media can be categorized into three types: (1) metal powder or metal bead (typically known as sintered metal), (2) metal fiber or metal wire, and (3) metal foam media. Metal powder media is a porous membrane filtration material manufactured by sintering metallic powders having carefully graded nearly spherical shapes into a micro-structure similar to a granular bed. It typically has a high solid volume fraction of 0.35 to 0.65; thus, it is widely used in many high temperature high pressure filtration applications because of its good mechanical strength and where very high filtration efficiency is desired. The granular porous structure of metal powder media is similar to that of a typical ceramic wall flow substrate, so one can expect comparable filtration performance of these two in media level.
Metal fiber media has a non-woven structure made of long metallic fibers with controlled diameters ranging upwards from 1.5 µm. An outstanding characteristic of sintered metal fiber media is their very high porosity. Metal foam is non-fibrous depth filter, whose filter matrix is continuous. It consists of a large number of tightly-packed bubbles, which are made to burst at points of contact to produce a single ramifying and anastomosing space within a matrix formed by the residual metallic material (Brown Citation1993). Metal foam media has cylindrical collectors similar to those of metal fiber media, so its filtration performance can be reasonably estimated according to that of metal fiber media.
While metal filters are widely used in applications, their filtration performance, including collection efficiency and pressure drop, is not often reported, especially for ultrafine particles. Heikkinen and Harley (Citation2000) experimentally determined the fractional efficiency of clean sintered metal powder media with pore size from 100 to 2 μm using monodisperse NaCl and latex particles. Although the filter pressure drop was reported, further discussion about the filter figure of merit and its relationship to the media physical properties was not provided. Damit et al. (Citation2014) evaluated the filtration efficiency and figure of merit of several metal powder media against B. subtilis endospore and MS2 virus aerosols. A physical removal efficiency greater than 99.9% was observed, but with a low figure of merit (0.25–0.75 kPa−1) because of a high pressure drop. Li (Citation1997) evaluated the super-micron size latex bead filtration efficiency of metal fiber media. Lee et al. (Citation2006) investigated the performance of a bed-type metal alloy fiber under periodic regeneration. Park et al. (Citation2015) investigated the fractional efficiency of metal fiber media for capturing radioactive aerosols at HEPA or EPA levels, but the limited data reported for the media pressure drops impedes further discussion on filter figure of merit versus metal fiber media properties. Ghidossi et al. (Citation2009) evaluated metallic foams for separating particles from hot gases. Because of its very open structure and coarse collector size, fractional efficiencies of less than 20% were found for super-micron particles; however, a very low pressure drop (less than 200 Pa) can be achieved even at high filtration velocity (0.5 m/s).
In the present study, we experimentally investigate both the fractional efficiency and pressure drop of two types of metallic filter media, metal powder and metal fiber. This is done for both nearly spherical particles and fractal-like soot particles at elevated temperatures to explore the effects of particle shape and flow temperature. A comparison to model predictions shows good agreement to experimental data for spherical particles. Factors influencing the filter figure of merit are discussed for the various media types and the grades within each filter type, and the suitability for GPF applications is examined.
Experiments and theory
Metallic filter media specifications
Two types of commercially available metallic filter media (from Shengda Filtration Technology Co., Ltd., Xinxiang, Henan, China) are evaluated for their soot particle collection efficiency and flow resistance: sintered metal powder and sintered metal fiber. Both media are sintered from their original loosely packed collectors. shows example scanning electron microscope (JEOL 6500, SEM, Akishima, Tokyo, Japan) images of the microstructures of these two types of media. The detailed specifications of the media are listed in .
Figure 1. SEMs of (a) sintered metal powder (grade 2) and (b) sintered metal fiber filter media (Fecralloy).
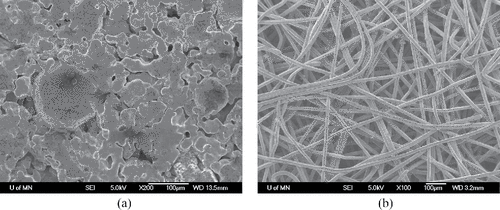
Table 1. Specifications of filter media tested.
Four grades of sintered powder media are evaluated, grades 20, 10, 5, and 2. The number roughly indicates the size of particles in micrometers with 99% collection efficiency in water. With decreasing grade, the collection efficiency increases, while the permeability decreases due to reduced pore size. All four sintered metal powder media are made of stainless steel 316L, with a maximum rated temperature of 400°C for long-term application.
Five grades of sintered metal fiber media are evaluated, including three commercially available stainless steel 316L fiber media (grades 5, 10, and 15), one commercial media made of Fecralloy fibers, and one custom-made stainless steel 316L media (grade 12 µm). All four commercial media have a layered structure, with fiber diameter decreasing with depth, which increases the filter holding capacity. The Fecralloy media consists of iron-chromium-aluminum alloy fibers rated up to 1000°C. It is used in high-temperature applications where high creep and oxidation resistance, surface stability, and mechanical strength are required. The custom filter media is homogeneous, to simplify comparisons between measured and modeled filtration efficiency. It consists of uniform 12 µm fibers, has a porosity of 0.78 (as determined from the ratio of apparent to material density), and a thickness of 1.2 mm.
shows a schematic of the experimental apparatus used for particle generation and filter performance evaluation. A propane diffusion flame burner, based on the one described by Shah and Dobson (Citation2007), is used to generate soot particles with similar morphologies to those in GDI engine exhaust, as illustrated in Figure S2 in the online supplemental information (SI). In the flame burner, propane is brought in through a 13 mm O.D. (11 mm I.D.) stainless steel tube held concentrically inside of a 30 mm O.D. (27 mm I.D.) quartz tube. Filtered dry air is provided through the quartz tube such that the air forms an annulus around the propane flow. The addition of nitrogen at 10 L/min quenches the burning gases and freezes changes in particle size and morphology. The fuel/oxygen ratio and the amount of time between particle generation and quenching controls the degree of agglomeration achieved in the burner. Soot particles are then diluted by a two-stage injection dilutor to further reduce their concentration to the level suitable for aerosol instruments.
A small portion (typically 1.0 liter per minute) of this diluted soot-laden aerosol flow is then introduced into a DMA and only particles with mobility in a narrow range exit. These nearly mono-dispersed soot particles represent the challenge aerosols for the filter media initial collection efficiency measurements. Their concentrations are maintained to be less than 10000 #/cc to avoid any loading effect on the measurements. The flat disk filter media sample with 25 mm diameter is held in a home-made filter holder, which sits in the middle of a tube furnace, the temperature of which can be adjusted from 25°C to 650°C to investigate the effect of temperature on filtration performance. A condensation particle counter (CPC, Model 3775, TSI Inc., Shoreview, MN, USA) is used to measure the soot particle number concentrations both upstream and downstream of the filter sample. The collection efficiency (E) of each particle size is determined by taking the ratio of downstream-to-upstream reading, after correcting for particle loss as measured in a blank test; thus,[1] Here, P denotes the size dependent penetration of soot particles,
and
are the upstream and downstream particle number concentrations, and
and
are the upstream and downstream particle number concentrations for the blank test. The latter is conducted under the same test condition as the efficiency measurement, but with no filter media in the filter holder; its purpose is to account for particle losses in the test system, which mostly comes from diffusion and thermophoresis of soot particles.
The filtration velocity is controlled by a mass flow controller (MKS 1479A, MKS, Andover, MA, USA). A heat exchanger upstream of the MFC reduces the temperature of the flow to near room temperature for filter evaluations at elevated temperatures. The mass flowrate exiting the CPC is monitored by a mass flow meter (TSI 4041). By doing so, the total mass flowrate in the system is kept constant as the furnace temperature is varied. As a result, the volumetric flowrate and the actual filtration velocity increase with the temperature inside filter holder. It is to be noted that the filtration velocities reported in this article are their room temperature equivalents. A correlation between the actual and nominal filtration velocity is tabulated in Table S1 in the SI. For example, a nominal velocity of 10 cm/s equates to 20.9 cm/s at 350°C and 31.0 cm/s at 650°C. The flow resistance of the filter sample is measured by a differential pressure sensor (Model 616, Dwyer Inc., Michigan City, IN, USA).
Single fiber efficiency theory
According to the classic single fiber efficiency theory (Brown Citation1993; Liu and Rubow Citation1990; Stechkina and Fuchs Citation1966), the penetration through a fibrous filter media (Pf) can be calculated as[2] where α, t, and df are the solidity, thickness, and fiber diameter of the filter, respectively. Ef is the single fiber efficiency, which is a summation of the collection by different mechanisms, including diffusion (Ef_D), interception (Ef_R), interception of diffusion particles (Ef_DR), and inertia impaction (Ef_I) and is calculated as:
[3]
A detailed description of the models is provided in the SI.
Besides collection efficiency, another important characteristic of filter media is its resistance to the flow, which is measured by the pressure drop across the media. These two characteristics can be combined to define a filter figure of merit (FOM), also known as quality factor (Q) (Brown Citation1993),[4]
The benefit of using FOM is that it provides a consistent means to compare overall performance across different filter media and operating conditions. is either number or mass weighted average efficiency over the relevant soot size distribution,
[5] where
and
are the desired weighting function for number or mass and soot particle number distribution, respectively. The choice of weighting function and size distribution depends on the intended application. For example, in the case of GDI vehicle exhaust after treatment one can chose a size distribution representative of GDI soot emissions and a weighting function of unity for particle number based emissions standards or particle mass for application to mass based standards.
is the filter media pressure drop. The theoretical flow resistance for fibrous media is determined using Davies' expression for drag (Davies Citation1973),
[6] where
is the filtration velocity,
is the filter packing density,
is the dynamic viscosity of the fluid, th is the filter thickness, and
is fiber diameter of the filter.
Results and discussions
Experimental soot penetration through metallic media
Soot penetration was evaluated for particle mobility diameters between 35 nm and 400 nm, for different media types and grades, filtration velocities, and operating temperatures, as listed in . and give examples of the measured soot particle penetration through one grade of sintered metal powder and one grade of sintered metal fiber media: shows particle penetration versus particle mobility size for sintered metal powder media grade 5 at 350°C and nominal filtration velocities of 2, 5, and 10 cm/s, respectively. shows the penetration of sintered metal fiber media grade 5 at 350°C and nominal filtration velocities of 5, 10, and 30 cm/s, respectively. The velocities are not the same because we impose a packaging constraint that is required for application to motor vehicles, namely that the metal media (powder and fiber) achieve the same filtration efficiency with the same filter volume as current ceramic wall flow GPFs. We estimate that powder media can be more efficiently packaged than fiber media, and therefore can operate at lower velocity.
Table 2. Summary of pressure drop, efficiency and FOM of cases tested.
Figure 3. Soot particle penetration through (a) sintered powder media grade 5 at 350°C and 2, 5, and 10 cm/s, and (b) sintered fiber media grade 5 at 350°C and 5, 10, and 30 cm/s.
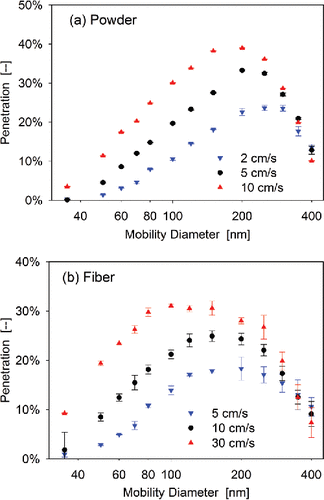
The penetration curves for both media exhibit characteristic inverted-U shapes with maxima that represent the most-penetrating particle size (MPPS), which is the size of particles having the highest penetration at a specified filtration condition. Above the MPPSs, penetration decreases due to enhanced collection by interception; below the MPPSs media penetration decreases because of higher diffusion rates as particles become smaller. Since the smallest particles tested were 35 nm, thermal rebound was not observed even at elevated temperatures (Kim et al. Citation2007; Shin et al. Citation2008; Wang and Kasper Citation1991). Similar penetrations are found for metal powder and metal fiber media in the 300 to 400 nm size range over a variety of filtration velocities, because interception is the dominant collection mechanism, and it is not sensitive to filtration velocity. Below 300 nm, penetration increases with increasing filtration velocity owing to the reduced residence time available for diffusion. This causes the MPPSs to shift towards smaller size with increasing filtration velocity.
In contrast to and , and compare penetration efficiencies at constant velocity as a function of media grade. The nominal velocities are 5 cm/s for sintered metal powder and 10 cm/s for metal fiber, and the temperature is 350°C. The stainless steel fiber grade 15 and Fecralloy media have very low soot removal efficiency; therefore multiple layers are stacked together to achieve measurable changes in penetration (as denoted in ). Although the media are rated by liquid filtration measurement for super-micron particles, the sub-micron soot penetrations follow the same trend with grade. The Fecralloy fiber media has higher penetration than its stainless steel counterparts because of its coarser fiber size. SEM images indicate the Fecralloy media has 35 µm fiber diameter on upstream side and 17 µm on downstream side, while the layered stainless steel media have fiber sizes ranging from 1.5 µm to 8 µm. This also explains why the custom made 12 µm sintered fiber media has higher penetration than its layered stainless steel counterparts even though it is thicker than them. The measured MPPSs decrease slightly (from 250 nm to 200 nm for metal powder and from 200 nm to 150 nm for metal fiber media) with decreasing grade number, consistent with finer collectors (powder or fiber) in media with smaller grade numbers. The MPPSs are found to be less sensitive to media grade than to filtration velocity. Also, penetration through sintered powder media varies less among samples than sintered fiber media, which is attributed to their more densely packed structure helping provide a more uniform media.
Figure 4. Soot particle penetration through different grades of (a) sintered powder media and (b) sintered fiber media, at 350°C and filtration velocity of (a) 5 cm/s and (b) 10 cm/s, respectively.
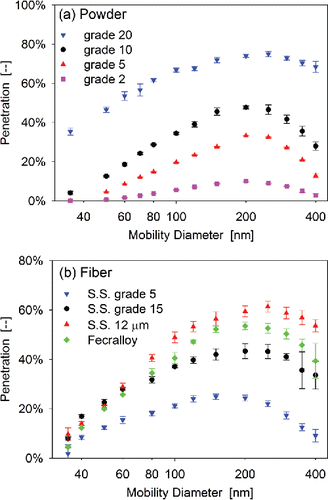
The effect of temperature, at constant mass flow, can be found in , with a more clearly graphical illustration shown in Figure S3 in the SI. Raising temperature influences the collection efficiency in two opposing ways, both related to diffusion. Firstly, the diffusivity of soot particles increases which enhances collection. Secondly, actual filtration velocity increases, reducing residence time in the filter media. As a result there is an observable, but small, increase in collection efficiency with increasing temperature. The maximum mass efficiency increase from 25°C to 650°C found in this study is 13.4% for sintered fiber Fecralloy media at 10 cm/s, while the minimal difference is 8.8% for sintered powder grade 5 at 5 cm/s. This result is consistent with the observation by Shin et al. (Citation2008) for screen mesh penetration of 3 to 20 nm silver particles over the temperature range of 296 to 500 K.
Comparison of particle penetration between measurement and theory
Models will be necessary tools with which to optimize filter design for practical engine exhaust applications. Thus, we take a brief look here at the ability of single fiber efficiency theory to predict metal fiber media filtration. The custom-made 12 µm metal fiber media has several well controlled characteristics, including fiber diameter, porosity, and thickness. For homogeneous media, this is sufficient information to calculate particle penetration from the single fiber efficiency theory described above. compares theoretical predictions to experimental data for both soot and KCl particles at 350°C and 10 cm/s. The penetration of nearly spherical KCl particles is measured using the same apparatus as shown in , except for a home-made Collison-Type atomizer for aerosol generation. The circles and solid line display measurements and the model prediction for KCl particles. The good agreement is attributed to the well-controlled homogeneous structure of the custom-made metal fiber media, which has very uniform fiber diameter () unlike most fibrous media.
Figure 5. Comparison of the penetration of custom-made sintered metal fiber grade 12 µm between experimental measurements and model predictions for both KCl and soot particles.
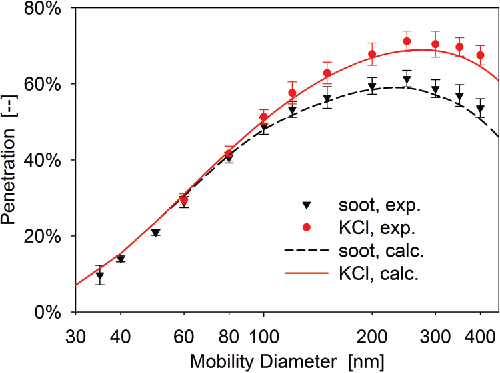
Soot particles have a fractal-like structure that enhances their effective interception length, as reported for other non-spherical particles including nanoparticle agglomerates (Boskovic et al. Citation2009; Kim et al. Citation2009), fibrous aerosols (Asgharian and Cheng Citation2002; Myojo Citation1999), and carbon nanotubes (Wang et al. Citation2011a,Citationb). As can be seen in , soot particles below 80 nm have nearly the same penetration as KCl particles. In this size range soot particles are composed of only a few ∼20 nm primary particles making them relatively compact. With increasing size soot develops the fractal-like structure exhibited in Figure S2, and its penetration falls below that of KCl particles from the resultant enhanced interception. Soot penetration is about 10% lower than that of KCl particles at 200 nm and 15% lower at 400 nm.
We interpret this enhancement using the intuitive idea of interception equivalent diameter (Lange et al. Citation2000). This is the diameter of a spherical particle having an equal collection by interception as the soot particle. It is determined by comparing the measured efficiency difference between soot and KCl particles for sizes above 80 nm and attributing this to the change in interception diameter. For the soot particles studied here, interception diameter increases monotonically with mobility diameter (Figure S4, see the SI), as also reported by Lange et al. (Citation2000) for carbon agglomerates. While this relationship will vary with particle morphology, it should apply generally to soot, which widely exhibits a fractal dimension of 1.7–1.8. We then use this equivalent diameter to calculate the single fiber penetration of soot particles. The resulting predictions, plotted as the dash line in , capture the decrease in soot particle penetration arising from the enhanced interception of soot agglomerates.
Filter figure of merit and its impact factors
Pressure drop, number and mass weighted efficiency, and corresponding FOMs for the metal powder and metal fiber media are listed in . These are measured using the propane flame generated polydisperse soot aerosol, with a ∼80 nm geometric mean diameter that compares well to typical GDI exhaust soot emissions. The geometric standard deviation of 1.65 is significantly lower than the ∼ 2.05 found for GDI vehicles (Harris and Maricq Citation2001), but we do not expect this to have a large impact on the resulting FOMs.
It is seen in that raising the filtration velocity causes a rapid loss in FOM owing to the simultaneous decrease in filtration efficiency and increase in pressure drop. FOM is sensitive to temperature. Both media exhibit a roughly 5-fold decrease in FOM at 650°C relative to 25°C. Temperature raises collection efficiency by speeding up diffusion, but this is more than offset by the concomitant increases in volumetric flow and viscosity. Since engine exhaust temperature dictates filtration temperature in the application to GDI vehicle exhaust, filtration velocity remains as a primary means to optimize FOM. Pleating is a common solution to pack more media area within limited space, but will introduce extra viscous flow resistance which can be equally important to media flow resistance under some circumstances (Chen et al. Citation1995).
At the same filtration velocity and temperature, metal fiber media offers a substantially higher FOM than metal powder. For example, at nominal 10 cm/s and 350°C, FOMs of metal fiber media ranges from 1.3–3 kPa−1, while those of metal powder are from 0.14–0.22 kPa−1. The likely explanation for the roughly order of magnitude better FOMs of metal fiber compared to metal powder media originates from the latter's higher solid volume fraction/lower porosity. The necessity of sufficient contact points for mechanical strength typically limits metal powder media to a porosity of about 65%, whereas metal fiber media can achieve porosities of 90% or higher. For most filter media, increasing solid fraction has a lower marginal gain on collection efficiency than the additional penalty on flow resistance; the increase in collector surface is more than offset by narrower flow paths that reduce residence time and increase pressure drop.
shows calculated FOMs as a function of filter porosity for both fibrous and powder media at assumed fiber/powder diameters of 4, 12, or 40 µm, at 350°C and 10 cm/s. The collection efficiency is calculated by single fiber/single sphere efficiency theory assuming a GDI soot distribution and using the interception equivalent diameter in Figure S4. A detailed description and equations used for this calculation can be found in the SI. Equation (Equation6[6] ) for fibrous media pressure drop is valid for 0.006 < α < 0.3, but in it is applied for α up to 0.7.
Figure 6. Calculated fibrous media FOM as a function of porosity. (






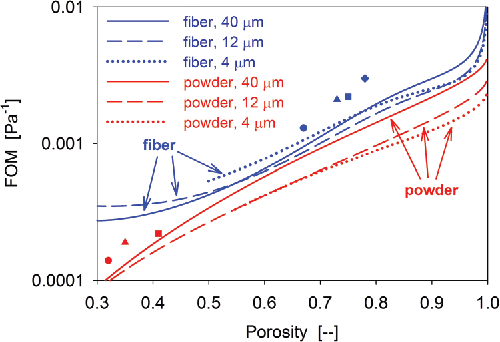
To compare fibrous and powder media we utilize the classical Rudnick-Happel expression for the flow resistance of powder media (Rudnick and First Citation1978),[7] where
is the diameter of the powder in media. This equation was originally proposed for a loosely-packed granular bed and later widely used for filtration cake. Differences between the microstructure of granular beds and metal powder media likely make this expression non-quantitative for the latter; thus, here we employ it for a relative trend in pressure drop with media grade. qualitatively demonstrates a substantial reduction in FOM with decreasing porosity for both media types. As porosity decreases from 75% to 40%, which roughly corresponds to the sintered metal fiber and sintered metal powder media examined in this study, the calculated FOMs decrease by 72% to 89% depending on fiber/powder size, which is consistent with the experimental difference in FOMs. Also illustrated in are the measured FOMs of each media as a function of porosity at 350°C and 10 cm/s. Owing the expressions used to estimate pressure drop, the measured FOMs are slightly higher than the calculated values. Uncertainties in the accuracy of the single sphere efficiency equations could be another source of the discrepancies. Nevertheless, the predicted FOMs qualitatively agree with the experimentally observed increase in FOM with higher porosity regardless the media type.
Conclusion
The present study has investigated the use of metal fiber and metal powder media for GDI exhaust filtration and found the former to be a promising option. Both media were examined as a function of media grade, filtration velocity, and temperature. Both exhibit expected trends. Filtration efficiency increases at lower velocity. Typical GDI soot particles are filtered primarily by diffusion and interception; thus, lower velocity provides a longer residence time in the filter medium. Efficiency increases slightly with temperature; the increase in diffusion rate just overcomes the reduction in residence time. These trends are confirmed by calculations based on single fiber theory. Model predictions are in good agreement with experiment for compact particles (KCl), within experimental uncertainty. Soot filtration is more efficient than that of KCl, owing to enhanced interception due to its fractal-like morphology, with an enhancement of near 0% below 80 nm to about 15% at 400 nm. The similarities in filtration efficiency observed between metal fiber and metal powder media suggest that, analogous to single fiber theory, a model based on an isolated spherical collector could be developed to calculate powder media efficiency.
Whereas metal fiber and metal powder media exhibit similar filtration efficiencies and trends, they have quite different figures of merit. FOM combines soot removal efficiency with pressure drop. For grades giving comparable filtration efficiency, the metal fiber media reveal FOMs roughly an order of magnitude higher than powder media. Model calculations corroborate this; both media reveal steep declines in FOM with decreasing porosity, about an 80% decrease if porosity is reduced from 0.75 to 0.4. Even if the media FOM is high, application to engine exhaust requires high filter surface area to reduce filtration velocity to a level that meets desired efficiency and backpressure targets. Metal fiber media offers the advantage of being amenable to pleating, whereas some version of wall flow design would be required for powder media. Full vehicle life application over 150 K miles requires the exhaust filter to tolerate ash accumulation, for which the open structure of metal fiber media may be advantageous. These questions of packaging and ash tolerance require further research and development.
Acknowledgments
Parts of this work were carried out in the Characterization Facility, University of Minnesota, a member of the NSF-funded Materials Research Facilities Network (www.mrfn.org) via the MRSEC program.
UAST_1349871_Supplementary_File.zip
Download Zip (860.9 KB)Funding
The authors thank the support of members of the Center for Filtration Research: 3 M Company, A. O. Smith Corporation, Applied Materials, Inc., BASF Corporation, Boeing Company, Corning Inc., Cummins Filtration Inc., Donaldson Company, Inc., Entegris, Inc., Guangxi WatYuan Filtration System Co., Ltd., MSP Corporation, Samsung Electronics Co., Ltd., Shigematsu Works Co., Ltd., TSI Inc., W. L. Gore & Associates, Inc., Xinxiang Shengda Filtration Technique Co., Ltd., Yancheng Environmental Protection Science and Technology City, and the affiliate member National Institute for Occupational Safety and Health (NIOSH). The authors acknowledge funding by Ford Motor Company through its University Research Program.
References
- Asgharian, B., and Cheng, Y. S. (2002). The Filtration of Fibrous Aerosols. Aerosol Sci. Technol., 36:10–17.
- Boskovic, L., Altman, I. S., Braddock, R. D., and Agranovski, I. E. (2009). Removal of Elongated Particle Aggregates on Fibrous Filters. CLEAN – Soil, Air, Water 37:843–849.
- Brown, R. C. (1993). Air Filtration: An Integrated Approach to the Theory and Applications of Fibrous Filters. Pergamon Press, New York.
- Chan, T. W., Meloche, E., Kubsh, J., Brezny, R., Rosenblatt, D., and Rideout, G. (2013). Impact of Ambient Temperature on Gaseous and Particle Emissions from a Direct Injection Gasoline Vehicle and its Implications on Particle Filtration. SAE Int. J. Fuels Lubr., 6:350–371.
- Chan, T. W., Meloche, E., Kubsh, J., Rosenblatt, D., Brezny, R., and Rideout, G. (2012). Evaluation of a Gasoline Particulate Filter to Reduce Particle Emissions from a Gasoline Direct Injection Vehicle. SAE Int. J. Fuels Lubr., 5:1277–1290.
- Chen, D.-R., Pui, D. Y. H., and Liu, B. Y. H. (1995). Optimization of Pleated Filter Designs Using a Finite-Element Numerical Model. Aerosol Sci. Technol., 23:579–590.
- Damit, B., Bischoff, B. L., Phelps, T. J., Wu, C.-Y., and Cheng, M.-D. (2014). Filtration of Bioaerosols Using a Granular Metallic Filter with Micrometer-Sized Collectors. J. Environ. Eng., 140:06014007.
- Davies, C. N. (1973). Air Filtration. Academic Press, London.
- Fu, H., Wang, Y., Li, X., and Shuai, S.-J. (2014). Impacts of Cold-Start and Gasoline RON on Particulate Emission from Vehicles Powered by GDI and PFI Engines. SAE International. doi: 10.4271/2014-01-2836
- Ghidossi, R., Bonnet, J. P., Rebollar-Perez, G., Carretier, E., Ferrasse, J. H., Vicente, J., Topin, F., and Moulin, P. (2009). Separation of Particles from Hot Gases Using Metallic Foams. J. Mater. Process. Technol., 209:3859–3868.
- Guan, B., Zhan, R., Lin, H., and Huang, Z. (2015). Review of the State-of-the-Art of Exhaust Particulate Filter Technology in Internal Combustion Engines. J. Environ. Manage., 154:225–258.
- Harris, S. J., and Maricq, M. M. (2001). Signature Size Distributions for Diesel and Gasoline Engine Exhaust Particulate Matter. J. Aerosol Sci., 32:749–764.
- Heikkinen, M. S. A., and Harley, N. H. (2000). Experimental Investigation of Sintered Porous Metal Filters. J. Aerosol Sci., 31:721–738.
- Kim, S. C., Harrington, M. S., and Pui, D. Y. H. (2007). Experimental Study of Nanoparticles Penetration Through Commercial Filter Media, in Nanotechnology and Occupational Health, A. D. Maynard, and D. Y. H. Pui, eds., Springer Netherlands, Dordrecht, pp. 117–125.
- Kim, S. C., Wang, J., Emery, M. S., Shin, W. G., Mulholland, G. W., and Pui, D. Y. H. (2009). Structural property effect of nanoparticle agglomerates on particle penetration through fibrous filter. Aerosol Sci. Technol., 43:344–355.
- Lange, R., Fissan, H., and Schmidt-Ott, A. (2000). A new method for the determination of the interception equivalent diameter. J. Aerosol Sci., 31:221–231.
- Lee, K. M., Lee, Y. S., and Jo, Y. M. (2006). Fine dust filtration using a metal fiber bed. J. Air Waste Manag. Assoc., 56:1139–1145.
- Li, T. (1997). Dependence of filtration properties on stainless steel medium structure. Filtr. Sep., 34:265–273.
- Liu, B. Y. H., and Rubow, K. L. (1990). Efficiency, Pressure Drop and Figure of Merit of High Efficiency Fibous and Membrance Filter Media. in 5th World Filtration Congress, Nice, France.
- Myojo, T. (1999). A simple Method to Determine the Length Distribution of Fibrous Aerosols. Aerosol Sci. Technol., 30:30–39.
- Park, M., Lee, S., Kim, J., Lee, B., Lee, J., and Ahn, Y. (2015). Optimal Design and Performance Evaluation of a Metal Fiber Filter for Capturing Radioactive Aerosols. Part. Sci. Technol. 34:359–365.
- Rudnick, S. N., and First, M. W. (1978). Specific Resistance of Filter Dust Cakes: Comparison of Theory and Experiments. Third Symposium on Fabric Filteers fbr Particulate Collection. Research Triangle Park, NC. pp. 251–288.
- Shah, S. D., and Dobson, D. A. (2007). A Soot Generator for DPF Qualification Studies. SAE Technical Paper. doi:10.4271/2007-01-0322.
- Shin, W. G., Mulholland, G. W., Kim, S. C., and Pui, D. Y. H. (2008). Experimental Study of Filtration Efficiency of Nanoparticles Below 20 nm at Elevated Temperatures. J. Aerosol Sci., 39:488–499.
- Sobotowski, R. A., Butler, A. D., and Guerra, Z. (2015). A Pilot Study of Fuel Impacts on PM Emissions from Light-Duty Gasoline Vehicles. SAE Int. J. Fuels Lubr., 8:214–233.
- Stechkina, I. B., and Fuchs, N. A. (1966). Studies on Fibrous Aerosol Filters–I. Calculation of Diffusional Deposition of Aerosols in Fibrous Filters. Annals Occup. Hyg., 9:59–64.
- U.S. Department of Energy. (2015). April 20, 2015 Gasoline Direct Injection Captures 38% Market Share In Just Seven Years From First Significant Use. https://energy.gov/eere/vehicles/fact-869-april-20-2015-gasoline-direct-injection-captures-38-market-share-just-seven
- Wang, H.-C., and Kasper, G. (1991). Filtration Efficiency of Nanometer-Size Aerosol Particles. J. Aerosol Sci., 22:31–41.
- Wang, J., Kim, S., and Pui, D. (2011a). Measurement of Multi-Wall Carbon Nanotube Penetration Through a Screen Filter and Single-Fiber Analysis. J. Nanopart. Res., 13:4565–4573.
- Wang, J., Kim, S. C., and Pui, D. Y. H. (2011b). Carbon Nanotube Penetration Through a Screen Filter: Numerical Modeling and Comparison with Experiments. Aerosol Sci. Technol., 45:443–452.
- Yi, J., Wooldridge, S., Coulson, G., Hilditch, J., Iyer, C. O., Moilanen, P., Papaioannou, G., Reiche, D., Shelby, M., VanDerWege, B., Weaver, C., Xu, Z., Davis, G., Hinds, B., and Schamel, A. (2009). Development and Optimization of the Ford 3.5L V6 EcoBoost Combustion System. SAE Int. J. Engines, 2:1388–1407.
- Zhang, S., and McMahon, W. (2012). Particulate Emissions for LEV II Light-Duty Gasoline Direct Injection Vehicles. SAE Int. J. Fuels Lubr., 5:637–646.