Abstract
Copper is an inexpensive replacement for silver in electronic applications such as solar cell metallization, electromagnetic interference packaging, and printable electronics. However, copper has a characteristically low reduction potential under ambient conditions, favoring formation of non-conducting copper oxides. Here, a spray pyrolysis method of producing oxidation resistant copper particles with surfaces rich in zinc, without need for post-fabrication modifications is described. The effects of precursor and reactor parameters on the particle surface composition with respect to the bulk composition are explored. At reactor temperature conditions of 1000 °C with a precursor containing 90 at% copper–10 at% zinc, the formation of desired morphologies was achieved, smooth dense particles with surfaces enriched in zinc. Increasing the concentration of zinc in the precursor did not improve enrichment, and instead led to the formation of a zinc diamine chloride [Zn(NH3)2Cl2] byproduct.
© 2018 American Association for Aerosol Research
EDITOR:
Introduction
Silver is widely used as the conductive metal (6.82·107 Ω−1 m−1) in many electronic applications (Speight Citation2004). Copper is a low-cost alternative (6.50E7 Ω−1 m−1) except for its tendency to continuously oxidize and no longer be conductive (Speight Citation2004). A copper that is modified to be oxidation resistant would significantly impact the electronics industry. In the past decade, several methods for establishing oxidation resistance have been achieved, primarily through the application of metallic or organic surface coatings (Pfeffer et al. Citation2001; Papazoglou et al. Citation2010; Kang et al. Citation2012; King, Liang and Weimer Citation2012). Processes for coating the surface of copper include atomic layer deposition, chemical vapor deposition, or electrodeposition (Rickerby and Matthews Citation1991; Jehn and Gissler Citation1992). These processes are time consuming, costly, and hard to control. Herein, we have attempted to tackle the problems of copper oxidation via a single-step, scalable, spray pyrolysis production method. The importance of establishing a method of scalable production for oxidation resistant powders lies in applications such as inexpensive conductive materials for solar cell metallization, electromagnetic interference (EMI) packaging, conductive pastes, and printable electronics as hybrid integrated circuitry (Grouchko et al. Citation2009; Zhong et al. Citation2012). Silver has been used as a coating to protect copper by making silver shell-like coatings on copper particles through the use of a horizontal spray pyrolysis apparatus (Wang et al. Citation2007; Jung et al. Citation2011). Tin has been shown to delay the onset of oxidation (Liang et al. Citation2017a,Citationb). However, the usage of zinc, another less expensive material, in such particulate systems has not yet been explored, though zinc coatings on copper nanowires appear to yield superior conductive behavior (Chen et al. Citation2014).
Spray pyrolysis is a well-established technique for the creation of sub-micron particles with tunable morphologies and chemical characteristics (Okuyama and Lenggoro Citation2003). Spray pyrolysis holds many benefits over other particle processing methods, such as milling, sol-gel, or polyol (Gurav et al. Citation1993; Zhong et al. Citation2013b). The morphology of powders generated using spray pyrolysis can be optimized through adjustments of the precursor solution, furnace temperature, and residence time, among other tunable reactor parameters (Lenggoro et al. Citation2000; Lin and Gentry Citation2003). Spray pyrolysis can utilize inexpensive and relatively safe precursors that allow for continuous production of particles with minimal liquid waste.
In the present study, we fabricated copper particles with zinc-enriched surfaces that expressed resistance to oxidation. Particles were analyzed using scanning electron microscopy (SEM), energy dispersive spectroscopy (EDX), X-ray diffraction (XRD), X-ray photoelectron spectroscopy (XPS), and in situ XRD.
Experimental methods
Spray pyrolysis apparatus
A dual-furnace spray pyrolysis process () was utilized for production of powders. At the first furnace inlet, an ultrasonic generator operating at 1.7 MHz atomizes precursor solution to volume average droplet diameters of 5 ± 2 µm (Zhong et al. Citation2013a). These droplets were carried by nitrogen (N2, Airgas, 99.5%) at a flow rate of 2.5 L/min into the dual furnaces, which were set to either 825 °C or 1000 °C. At this 2.5 L/min flow rate condition, the residence time of the droplets within the furnace was estimated to be 3.9 s at 825 °C, and 2.0 s at 1000 °C, following the procedures presented by Liang et al. (Citation2017a). The furnace outlet contained quench nitrogen gas flowing at 2.5 L/min prior to a polytetrafluoroethylene filter for collection of particles. Gaseous compounds such as water vapor, reacted precursor, or any vaporized metallic material traverse the filter and exit through the reactor exhaust.
Figure 1. Spray pyrolysis schematic depicting (1) carrier gas introduction, (2) atomization of the precursor solution, (3) dual furnaces heating atomized droplets, evaporating droplet solvents and nucleating salts, and the densification of particles, (4) quench gas introduction, and (5) the particle collection filter and vapor byproduct outlet.
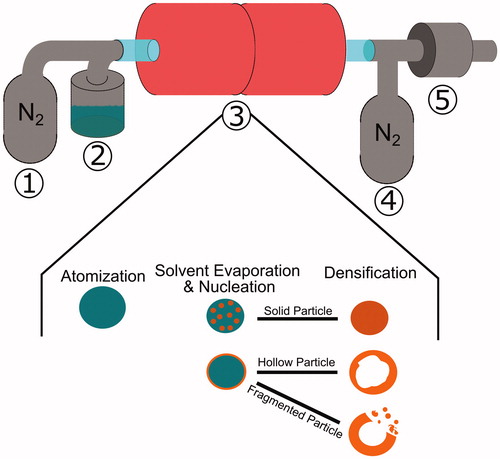
Precursor solution
Precursors of 0.5 M total metal-salt concentration were made using copper nitrate trihydrate (Cu(NO3)2·3H2O, 99.5% purity, Strem Chemicals) and anhydrous zinc chloride (ZnCl2, ≥97% purity, Strem Chemicals). The Cu:Zn ratio of the precursor was varied to yield solutions of 0 atomic % (at%) Zn, 10 at% Zn, and 45 at% Zn. The precursor solvent was 80 volume % (vol%) deionized water, and 20 vol% ethylene glycol as the co-solvent.
Instrumentation
Particle morphologies were analyzed using scanning electron microscopy (SEM, Hitachi SU-70, Schaumburg, IL, USA). The crystalline character of the particles was probed using X-ray powder diffraction (XRD, Bruker D8 Advance, Billerica, MA, USA). Compositions of representative regions in powder SEM were analyzed using energy dispersive spectroscopy (EDX, Bruker XFlash with Silicon Drift Detector). X-ray photoelectron spectroscopy (XPS) was utilized to probe the surface compositions as well as to characterize the nature of metal complexes using high resolution (HR) scanning XPS (Kratos Axis 165, Manchester, UK). In situ XRD was used to characterize the oxidation behavior of the powders by collecting diffraction data while heating the powders. The in situ XRD samples were heated from 100 °C to 600 °C at a ramp rate of 5 °C/min with measurements taken at every 100 °C. Sputtering of powders by argon ions was also performed for 20 min in vacuo allowing XPS analysis of the composition below the particle surfaces. The sputtering gun was set to 4 kV and 5 mA.
Results and Discussion
Precursors of dissolved metal salts of varying compositions (solely copper, 90 at% copper–10 at% zinc, and 55 at% copper–45 at% zinc) were used to fabricate powders at two different temperatures, 825 °C and 1000 °C. Fabrication temperatures were chosen to correspond to the α and β phases in the copper–zinc phase diagram as it was initially believed that the metals may alloy to form these phases (Massalski et al. Citation1986). From the phase diagram, the 825 °C condition at equilibrium would yield the α phase for the entirety of the fabrication process, while the 1000 °C condition may exist above the liquidus at equilibrium and could possibly quench into the β phase. Particles generated from precursors of either copper or 90 at% copper–10 at% zinc were of spherical morphology as determined using SEM (). At the 825 °C fabrication temperature (), particles had volume mean diameters of 0.72 ± 0.20 µm (Figure S2). The SEM images have low contrast, likely a result of unreacted or incompletely reacted ethylene glycol. This is a result consistent with previous work in the analysis of spray processed powders (Majumdar et al., Citation1996; Zhong et al. Citation2012). At the 1000 °C fabrication condition (), particles had volume mean diameters of 0.78 ± 0.2 µm (Figure S2), spherical morphology, and sharper contrast suggesting higher temperatures led to full decomposition of ethylene glycol. This is supported by previous spray pyrolysis studies (Majumdar et al. Citation1996; Zhong et al. Citation2012).
Figure 2. (a and b) SEM of 10 at% zinc particles generated at 825 °C and 1000 °C, respectively. (c and d) SEM of 45 at% zinc particles generated at 825 °C and 1000 °C, respectively. (e) SEM of copper only particles generated at 1000 °C.
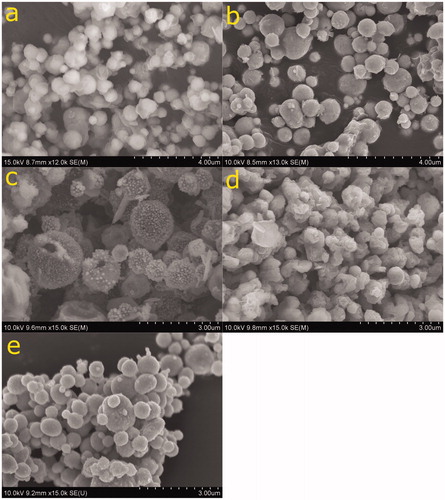
The volume mean particle diameters at each temperature condition are statistically different at the 95% confidence level with the diameter at the lower temperature being smaller than the diameter at the higher temperature. This is a surprising result considering densification typically increases as temperature increases. It may be that the particles become near to fully dense at temperatures as low as 825 °C, with the discrepancy in SEM images solely being due to the differences in decomposition of remnant organics. The theoretical diameter of a fully dense particle is approximately 0.75 ± 0.30 µm using the method of Berglund and Liu detailed in the Supplemental Information (Berglund and Liu Citation1973).
Particles fabricated from precursors of 45 at% zinc had spherical and platelet morphologies (). At the 825 °C furnace temperature (), particles had volume mean diameters of 1.4 ± 0.5 µm and appear to consist of larger particles with many smaller particles (approximately 90 nm in diameter) on the surface. A portion of these large particles had visible holes, suggesting that they were hollow. This is consistent with the volume mean diameter being significantly larger than the theoretical diameter of a fully dense particle (Figure S2). The formation of hollow particles is most commonly due to evaporation and nucleation rates that overcome the salt rate of diffusion within the droplet (Gurav et al. Citation1993). At the 1000 °C fabrication temperature (), particles fabricated from precursors of 45 at% zinc had volume mean diameters of 0.70 ± 0.2 µm and were spherical with rough surfaces. However, there was no presence of smaller particles at the surfaces of the spherical particles, and platelet morphologies were still observed at these conditions. This suggests a unique fabrication route that differs from that of either pure copper or lower zinc content precursors.
X-ray diffraction of the 10 at% zinc powders revealed that under both temperature conditions the primary crystalline phase was copper (PDF #00-004-0836) with no apparent peak shift, which would initially suggest zinc is not incorporated into copper in powders fabricated from 10 at% zinc precursors (). However, alloying of copper and zinc in the α region is unlikely to produce significant XRD peak shift, as intercalated atoms are of roughly the same size. Thus, the absence of a segregated zinc phase and peak shift in the 10 at% zinc powder XRD does not disprove alloying, as zinc may be either amorphous or alloyed with copper. The formation of metallic copper and the absence of crystalline metal oxides is due to the reducing environment provided by the addition of the ethylene glycol co-solvent to the precursor (Kim et al. Citation2002; Speight Citation2004; Zhong et al. Citation2012). While no pure crystalline zinc was observed in the 10 at% zinc powders, a zinc diammine chloride (ZDC) byproduct was found via powder diffraction, the quantity of which increased significantly with increasing precursor zinc concentration ().
Figure 3. (a and b) XRD of particles generated from 10 at% zinc precursors at 825 °C and 1000 °C with (b) providing a better depiction of the low 2θ diffraction. (c and d) XRD of particles generated from 45 at% zinc precursors at 825 °C and 1000 °C with (d) depicting the low 2θ diffraction. Droplines represent reference peaks of copper (PDF #00-004-0836) (squares, ▪), zinc diammine chloride (PDF #00-024-1435) (triangles, Δ), and copper chloride (PDF #00-006-0344) (circles, •).
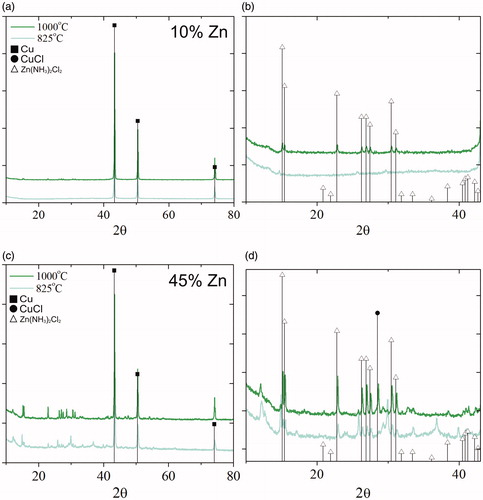
Similar to the results of lower zinc content precursors, X-ray diffraction revealed that 45 at% zinc precursors yielded metallic copper as the primary phase, without evidence of a crystalline zinc or zinc oxide phase (). At this higher zinc content condition, slight peak shift to higher 2θ values was visible in the X-ray diffraction results, which is likely due to minor alloying at this condition (Massalski et al. Citation1986). As with the 10 at% zinc precursors, the diffraction presents positive confirmation of the presence of a crystalline zinc diammine chloride (ZDC) complex, however, at these higher at% zinc conditions the peaks are more easily observed. With the increase of furnace temperature from 825 °C to 1000 °C, the sharpness of ZDC peaks improve, which suggests the crystallites are larger at this condition. The formation of the ZDC complex via the spray route has not been previously reported. The theorized formation mechanism for the complex is discussed in the Supplemental Information.
Energy-dispersive X-ray spectroscopy (EDX) analysis of the powders indicated that for precursors of 10 at% zinc with respect to precursor metal content, the effective bulk metal composition was approximately 10 at% zinc (). EDX of powders fabricated from 45 at% zinc precursors shows that these particles did not have effective-bulk metal compositions of 45 at% zinc (). This result was surprising, but it supports the hypothesis that higher zinc content precursors yield a particle formation route quite different than that of pure copper precursors. It is believed that this formation route involves the volatilization of zinc and is discussed in the Supplemental Information.
Figure 4. EDX of particles fabricated at various concentrations and temperatures. The “Cu Only” condition was fabricated at 1000 °C. “Precursor” denotes the concentration of the precursor solution, and thus an ideal concentration to compare to EDX; it is not an EDX result.
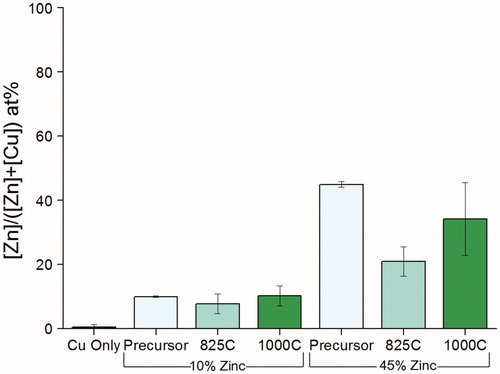
To probe the surface and near-surface composition, XPS and argon sputtering were utilized. Evidence of surface enrichment is defined by XPS zinc atomic percentages significantly greater than the bulk zinc atomic percentage as determined using EDX. XPS of particles generated with 10 at% zinc precursors showed that the particles generated at 825 °C appeared depleted in zinc at the surface (). Sputtering of these 10 at% zinc precursor powders generated at 825 °C showed that deeper layers had higher concentrations of zinc. When the furnace temperature was increased to 1000 °C, XPS analysis suggested that the outer layers of the particle surfaces were enriched in zinc with atomic compositions of roughly 60% (). Subsequent sputtering revealed that the particle subsurface composition contained less zinc (). This information suggests differing furnace temperatures between fabrication conditions may cause the significant differences in morphology depicted in SEM. Thus, the driving force behind the surface enrichment with zinc may be the gradation in heating time and temperature, which possibly acts through the melting of zinc improving mobility within particles and the ability to wet copper surfaces. It is believed that the process is controlled by interfacial tension effects, which would suggest surface enrichment is a thermodynamic process, which is discussed further in the Supplemental Information. X-ray photoelectron spectroscopy of the powders yielded no evidence of surface enrichment in particles fabricated from 45 at% zinc precursors (). This suggests that the fabrication route leading to the zinc ammine chloride byproduct disrupts the surface enrichment process.
Figure 5. XPS of particles generated from (a) 10 at% zinc precursors and (b) 45 at% zinc precursors at various temperatures. The designation of (S) after the fabrication temperature denotes XPS analysis on the same sample after argon sputtering for 20 min.
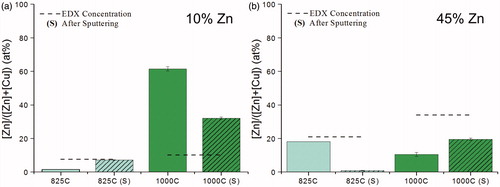
The oxidation behavior of the surface enriched 10 at% zinc particles was obtained using in situ XRD, wherein samples were heated on an XRD stage and diffraction behavior collected at regular temperature intervals. In situ XRD was performed on powders generated from pure copper precursors with a furnace temperature of 1000 °C, and 10 at% zinc precursors under both the 825 °C and the 1000 °C furnace temperature conditions. In all powders () the formation of Cu2O (2θ = 36.5) was visible at 200 °C, however, there is a variance in the sharpness of this peak between all samples. Differences in peak sharpness are a qualitative indication of oxide crystallinity, with sharper peaks being indicative of larger crystallites. The 10 at% zinc precursors fabricated at 825 °C () had the least sharp peaks over all temperature conditions, which would suggest that it is the sample most resistant to oxidation. However, the improved resistance to the formation of crystalline oxides in the 825 °C fabrication condition is most likely due to the higher degree of organic material within the powders fabricated at 825 °C, evidenced using the SEM images () and consistent with the results of previous studies (Wang et al. Citation2007).
Figure 6. In situ XRD of samples generated from (a) copper only precursors at 1000 °C, (b) 10 at% zinc precursors at 825 °C, and (c) 10 at% zinc precursors at 1000 °C. Droplines represent peaks of Cu2O (PDF #00-005-0667) (squares, ▪) and CuO (PDF #00-041-0254) (circles, •). The peaks at 2θ of approximately 43 are copper (PDF #00-004-0836).
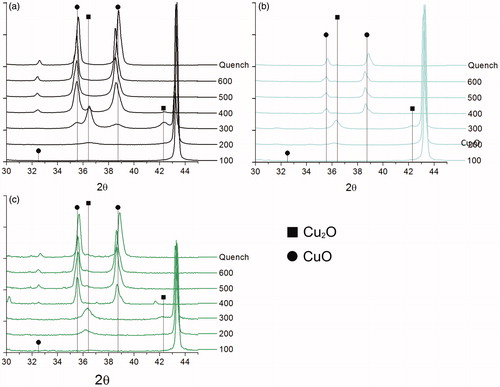
At the 200 °C temperature condition, the 10 at% zinc–1000 °C sample appears to have less Cu2O peak sharpness than the copper only–1000 °C sample (). Furthermore, at the 300 °C temperature, there is no evidence for the formation of CuO in the surface-enriched 10 at% zinc–1000 °C sample, while CuO has already begun to form in the copper only powders. The results suggest that the zinc surface enrichment in the 10 at% zinc precursors at 1000 °C delays the onset of oxidation of copper within the particles, evidenced by the decreased formation of crystalline oxides. These results are consistent with results for previously fabricated copper–tin particles that displayed oxidation resistance as determined using in situ XRD (Liang et al. Citation2017b). In related work, silver–copper core-shell particles were shown to be oxidation resistant (Jung et al. Citation2011), but the oxidation studies were conducted under ambient conditions, and so the results are not directly comparable to this study.
Conclusions
Smooth and fully dense copper particles with surfaces enriched in zinc were fabricated from a single-step ultrasonic spray pyrolysis route. Such particles were generated from salt precursors with low zinc concentrations (10 at% Zn and high reactor temperatures of 1000 °C). These particles hold potential for application as a replacement for silver in electronic applications because initial investigations suggest that surface zinc delays the onset of copper oxidation, defined by a reduction in the amount of crystalline oxides formed. The process is especially useful as it eliminates the need for post-fabrication modifications typically utilized in generation of oxidation resistant coatings. Precursors of higher zinc concentration (45 at%) did not improve surface enrichment and instead yielded copper particles in addition to a zinc diammine chloride complex. Formation of this metal ammine complex using the spray pyrolysis route has not previously been reported.
Supplemental Material
Download Zip (4.4 MB)Acknowledgments
The authors would like to acknowledge Dr. Peter Zavalij and Daniel Taylor for aid with XRD (Department of Chemistry and Biochemistry, University of Maryland), Dr. Karen Gaskell and Ifetkhar Jaim for aid with XPS (Department of Chemistry and Biochemistry, University of Maryland). We acknowledge the support of the Maryland NanoCenter and its AIMLab.
Additional information
Funding
References
- Berglund, R. N., and B. Y. Liu. 1973. Generation of Monodisperse Aerosol Standards. Environ. Sci. Technol. 7:147–53.
- Chen, Z., S. Ye, I. E. Stewart, and B. J. Wiley. 2014. Copper Nanowire Networks with Transparent Oxide Shells That Prevent Oxidation Without Reducing Transmittance. ACS Nano 8:9673–79.
- Grouchko, M., A. Kamyshny, and S. Magdassi. 2009. Formation of Air-Stable Copper–Silver Core–Shell Nanoparticles for Inkjet Printing. J. Mater. Chem. 19:3057–62.
- Gurav, A., T. Kodas, T. Pluym, and Y. Xiong 1993. Aerosol Processing of Materials. Aerosol Sci. Technol. 19:411–52.
- Jehn, H., and W. Gissler. 1992. Advanced Techniques for Surface Engineering. Kluwer, Brussels.
- Jung, D., H. Lee, Y. Kang, and S. Park. 2011. Air-Stable Silver-Coated Copper Particles of Sub-micrometer Size. J. Colloid Interface Sci. 364:574–81.
- Kang, D., J. Y. Kwon, H. Cho, J.-H. Sim, H. S. Hwang, C. S. Kim, Y. J. Kim, R. S. Ruoff, and H. S. Shin. 2012. Oxidation Resistance of Iron and Copper Foils Coated with Reduced Graphene Oxide Multilayers. ACS Nano 6:7763–69.
- Kim, J. H., T. A. Germer, G. W. Mulholland, and S. H. Ehrman. 2002. Size-monodisperse Metal Nanoparticles Via Hydrogen-Free Spray Pyrolysis. Adv. Mater. 14:518.
- King, D. M., X. Liang, and A. W. Weimer. 2012. Functionalization Of Fine Particles Using Atomic and Molecular Layer Deposition. Powder Technol. 221:13–25.
- Lenggoro, I. W., T. Hata, F. Iskandar, M. M. Lunden, and K. Okuyama. 2000. An Experimental and Modeling Investigation of Particle Production by Spray Pyrolysis Using a Laminar Flow Aerosol Reactor. J. Mater. Res. 15:733–43.
- Liang, Y., R. Felix, H. Glicksman, and S. Ehrman. 2017a. Cu-Sn Binary Metal Particle Generation by Spray Pyrolysis. Aerosol Sci. Technol. 51:430–42.
- Liang, Y., S. C. Oh, X. Wang, H. Glicksman, D. Liu, and S. Ehrman. 2017b. Oxidation-Resistant Micron-Sized Cu–Sn Solid Particles Fabricated by a One-step and Scalable Method. RSC Adv. 7:23468–477.
- Lin, J.-C., and J. W. Gentry. 2003. Spray Drying Drop Morphology: Experimental Study. Aerosol Sci. Technol. 37:15–32.
- Majumdar, D., T. T. Kodas, and H. D. Glicksman. 1996. Gold Particle Generation by Spray Pyrolysis. Adv. Mater. 8:1020–22.
- Massalski, T. B., H. Okamoto, P. Subramanian, L. Kacprzak, and W. W. Scott. 1986. Binary Alloy Phase Diagrams. Metals Park, OH: American Society for Metals.
- Okuyama, K., and I. W. Lenggoro. 2003. Preparation of Nanoparticles Via Spray Route. Chem. Eng. Sci. 58:537–47.
- Papazoglou, M., D. Chaliampalias, G. Vourlias, E. Pavlidou, G. Stergioudis, and S. Skolianos. 2010. Examination of the Oxidation Protection of Zinc Coatings Formed on Copper Alloys and Steel Substrates. In 7th International Conference of the Balkan Physical Union, 801–806. Melville, NY: AIP Publishing.
- Pfeffer, R., R. N. Dave, D. Wei, and M. Ramlakhan. 2001. Synthesis of Engineered Particulates with Tailored Properties Using Dry Particle Coating. Powder Technol. 117:40–67.
- Rickerby, D. S., and A. Matthews. 1991. Advanced Surface Coatings: A Handbook of Surface Engineering. Chapman and Hall, Blackie.
- Speight, J. 2004. Lange’s Chemistry Handbook. New York, NY: McGraw-Hill Professional.
- Wang, J. N., L. Zhang, F. Yu, and Z. M. Sheng. 2007. Synthesis of Carbon Encapsulated Magnetic Nanoparticles with Giant Coercivity by a Spray Pyrolysis Approach. J. Phys. Chem. B 111:2119–24.
- Zhong, K., G. Peabody, E. Blankenhorn, H. Glicksman, and S. Ehrman. 2013a. A Spray Pyrolysis Approach for the Generation of Patchy Particles. Aerosol Sci. Technol. 47:i–v.
- Zhong, K., G. Peabody, E. Blankenhorn, H. Glicksman, and S. Ehrman. 2013b. Spray Pyrolysis of Phase Pure AgCu Particles Using Organic Cosolvents. J. Mater. Res. 28:2753–61.
- Zhong, K., G. Peabody, H. Glicksman, and S. Ehrman. 2012. Particle Generation by Cosolvent Spray Pyrolysis: Effects of Ethanol and Ethylene Glycol. J. Mater. Res. 27:2540–50.