Abstract
This study describes developments in large-scale logging technology in Sweden from 1985 to 2010. Data were collected from manufacturers' sales material and from large forest enterprises. On average, forwarders manufactured in 2010 had 27–33% higher boom lifting torque than those manufactured in 1985–1989. The inflation-adjusted prices of medium-sized single-grip harvesters remained the same, but prices of forwarders increased by 30–50% in this period. The mechanical availability of various classes of machinery used increased from 70–80% to 85–88% between 1985 and 2008. The harvesting costs of thinning decreased between 1990 and 1998, while those of final fellings decreased from 1985 to 2006. However, in 2008 costs of both thinning and final felling tended to increase. The productivity of logging by the Swedish forest enterprise SCA increased almost three-fold in the period 1985–2010. However, since 2003 there have been signs of declining productivity. Currently, there is considerable interest in harvesting forest biomass for energy production. The new work tasks involved will affect the configuration of forest machines. A possible trend is that a new generation of forest machines and methods will be developed to facilitate integrated handling of roundwood and forest biomass for energy generation.
Introduction
Fennoscandia is at the forefront of large-scale cut-to-length (CTL) forest operations technology. In 1982, all extraction and most of the harvesting work in Swedish large-scale forestry was mechanized (Sundberg, Citation1990; Andersson, Citation2004). For final fellings, a combination of three machines (feller–buncher, different kinds of processor for delimbing and bucking, and forwarder) were used to harvest 50% of the total volume. Another 20% was harvested with double-grip harvesters (DGHs). However, motor-manual felling and processing was still applied, also accounting for slightly more than 20% of the total volume in this year. For thinning, motor-manual felling and processing was the main approach, handling 68% of the total volume, motor-manual felling and a processor for delimbing and bucking handled 27% of the volume, and single-grip harvesters (SGHs) had only just been introduced in 1982 (Freij & Tosterud, Citation1989).
A forest machine works with either transportation or processing of the trees. The type of power transmission with which the machinery is equipped indicates the utility of the machine for transportation. In general, a hydrostatic–mechanical (HS) power transmission is easier to control (Frumerie, Citation1993) and provides greater power efficiency than a hydrodynamic–mechanical (HD) system. A fully hydrostatic power transmission with wheel motors has many benefits, notably the freedom to mount wheels on independent pendulum arms, and avoidance of the need for many heavy mechanical power transmission components. In addition, the boom lifting torque of a forest machine is a good indicator of its ability to handle heavy loads. However, a forest machine cannot apply more lifting torque on the boom than the machine's stability allows. Hence, for well-designed forest machines the lifting torque and both the mass and design of the machine should be well matched. The maximum pressure in the work hydraulics is also an indirect indicator of the power and speed of the hydraulic components.
The technology for large-scale forest operations has undergone rapid development. This development has mainly been compiled and described only for the period before 1985, or descriptions have been rather elementary (Sundberg, Citation1990; Östberg, Citation1990; Fryk et al., Citation1991; Drushka & Konttinen, Citation1997; Andersson, Citation2004).
The aim of this study was to describe trends in large-scale logging technology in Sweden from 1985 to 2010. The study focuses on issues such as key indicators of technical performance (type of power transmission, hydraulic pressure in work hydraulics and crane lifting torque), machine prices, the mechanical availability (MA) of the machines and the average harvesting costs.
Such data have not been compiled in this form before and could be a basis for theoretical analysis of future harvesting systems and comparisons of new and old systems, as well as being of general interest in the development of off-road vehicle technology.
Materials and methods
Machine data were collated from the manufacturers' sales material collected at machine exhibitions in the years 1985–1989, together with data from Forskningsstiftelsen Skogsarbeten (Citation1988) and Fryk et al. (1991). To enlarge the sample size, data for machines marketed in the years 1985–1989 were pooled. Data on new machinery were collected from the main manufacturers' web pages in March 2010. For new machines, only data on machines supplied by the four most common manufacturers on the Nordic market were used (John Deere, Citation2010; Komatsu, Citation2010; Ponsse, Citation2010; Rottne, Citation2010). For data on boom lifting torque, the strongest boom was chosen if there was more than one option for a specific machine.
Data on machine prices and MA were acquired from a number of large, Swedish forest enterprises. In general, the prices paid for forest machines are agreed in negotiations between the manufacturers/dealers and the major buyers, such as forest enterprises. Consequently, prices are usually confidential. Therefore, relative machine prices are presented in this study. To compare the prices over time, all prices were adjusted for inflation (using the Swedish Consumer Price Index (CPI)) to January 2010 prices (Statistics Sweden, Citation2010). Prices were collected for five categories of machines: medium-size forwarders (mid-forwarders), large forwarders (large forwarders), double-grip harvesters (DGHs), medium-sized single-grip harvesters (mid-SGHs) and large single-grip harvesters (large SGHs). The definitions of size categories were the ones used in practice in the specific year, according to the terminology used by the main buyers of machines. These definitions have changed over time for forwarders. A mid-forwarder made before 1995–2000 normally had a load capacity of 11–12 tonnes (t). After this, the load capacity rose to 12–14 t. The definition of a large forwarder changed correspondingly. The corresponding difference between mid-SGHs and large SGHs has been 16 t throughout the whole period from 1985 to 2010, even though a number of very large SGHs (21–24 t) were introduced to the market after 2003. The price of a forest machine can differ substantially depending on its equipment. The prices used in this study relate to machines equipped to the standard for major Swedish forest enterprises, which generally means a high standard level. Prices of forwarders after 1998 refer to machines with eight wheels. Forwarders from 1985 had six wheels, but already by 1987 some prices refer to eight-wheel machines. Prices for all large SGHs, and mid-SGHs after 1998, refer to six-wheel machines. For older mid-SGHs some prices refer to four-wheel machines.
The yearly average costs of large-scale harvesting operations were collected from the Swedish Forest Agency (1990, 1999, 2009) and corrected for inflation by the Swedish CPI, to January 2010 (Statistics Sweden, 2010).
No country-wide data sets covering time series of productivity in logging operations are available. Statistics on harvested volumes and person-days of forest work can be obtained from the official data (Swedish Forest Agency, 2009). However, forest work also covers other elements, e.g. silvicultural operations. There is one unique set of productivity data for logging operations from 1955, originating from the forest enterprise SCA, which has been used in this study. It is assumed that the data in this set, reflecting operations in only part of Swedish forestry, follow general trends in productivity.
Results
In 1985 the three-machine system (feller-buncher, processor and forwarder) had been almost entirely replaced by the two-machine system (harvester and forwarder). The previous processors were presented at exhibitions as late as 1987, but it is unclear whether any of them were sold. Among the machines marketed in 1985, most had HD power transmissions, but a high proportion also had HS power transmissions (). In general, the machines had six wheels, but both four-wheel SGHs, of around 11 t, and eight-wheel 8–9 t forwarders were available. In general, the hydraulic systems of forest machines operated with a maximum pressure of 15–19 MPa for forwarders and 19–24 MPa for harvesters. Some DGHs were equipped with two separate hydraulic systems with different maximum pressures to operate the crane and the processor individually.
Table I. Characteristics of major forest machines in Sweden marketed in the period 1985–1989.
Depending on the working life of machines, changes in the machinery used in practice lagged somewhat behind changes in the machinery available on the market. The proportions of the total volume handled in large-scale final felling in 1987 by DGHs, processors, motor-manual processing and SGHs were 45%, 25%, 16% and 11%, respectively (Freij & Tosterud, Citation1989). The estimates for 1985 indicate that approximately the same proportions of the volume in final fellings (35–37%) were handled by processors and DGHs (Freij & Tosterud, Citation1989). Most of the volume handled using processors was felled with feller-bunchers, but motor-manual felling was also common. Almost 20% was still motor-manually processed, and for perhaps 5% of the volume an SGH was used (Freij & Tosterud, Citation1989). The proportions of the total volume handled in large-scale thinning in 1987 by motor-manual processing, SGHs and processors were 40%, 38% and 13%, respectively. Corresponding estimates for thinning in 1985 were approximately 52%, 22% and 18%, respectively (Freij & Tosterud, Citation1989).
In the years 1985–86 forest enterprises owned 35% of the total number of forest machines in Sweden, less than in 1980. Contractors were the main owners (Sundberg, Citation1990). In 1987 almost 3500 forest machines were used in large-scale forest operations in Sweden, of which 61% were forwarders, 13% DGHs, 12% processors and 11% SGHs (Freij & Tosterud, Citation1989). It should be noted that a small number of machines in use, less than 0.5% of the total, were intended for combined roundwood and bioenergy procurement (Freij & Tosterud, Citation1989).
A change in the market from 1985 to 1989 was that several forest machine manufacturers merged (Östberg, Citation1990; Drushka & Konttinen, Citation1997; Andersson, Citation2004). At the end of this period eight-wheel forwarders were more common than in 1985. The maximum load capacity of forwarders found on the market in 1989 was 18 t, compared with 15 t in 1985. The majority of DGHs had HS power transmissions in 1989. The largest DGH in 1989 was 21 t, compared with 18.5 t in 1985, and an important development during the period from 1985 to 1989 was the introduction of computer-aided measuring and bucking tools (Fryk et al., 1991). However, the greatest change in this period was in SGHs. The number of brands and models was 2.5 times higher in 1989 than in 1985. In 1985 the size of SGHs was in the range 11–14 t, but by 1989 this range had expanded to 5–17 t, since SGHs were produced for a wider range of tasks, including some final felling. Some SGHs still had basically the same chassis as forwarders in 1989, but the majority by then had purpose-built chassis.
In 1993 more SGHs than DGHs were used in Swedish forestry (Nordlund, Citation1996), but after that very few new DGHs were sold and they ceased to be marketed in 1995. Another development was that in 1993 the first computer-controlled HS power transmissions appeared (Drushka & Konttinen, Citation1997).
Many developments of technological interest were presented during the period from 1985 to 2000, without representing any major breakthroughs. For instance, the front chassis of the Ponsse S15 forwarder was made of aluminium to save mass in 1985; fully hydrostatic power transmissions were installed in forwarders by NorCar in 1987, and subsequently in other brands; the MINI 678 forwarder introduced in 1987 could be changed to a harvester with an SP 21 single-grip harvesting head in just 2 h; a combined machine for harvesting and forwarding tree-parts built on a Valmet 838 forwarder chassis appeared in 1989; and the Ford New Holland Bruun, a forwarder with a dirigible rear wheel in the bogie to reduce the turning radius and ground damage, was introduced in 1990, and Rottne presented a dirigible bogie for the same reason a few years later. The most recent examples are perhaps the combined harvesters and forwarders (harwarders) that were marketed most intensively from 1998 to 2005 (Talbot et al., Citation2003; Bergkvist, Citation2010). Some of those models are still on the market, but they are not sold in large numbers.
Nearly all machines marketed in March 2010 had HS power transmissions, but there was also a number of small brands of SGHs, or small models of other types of machine, that had an FHS power transmission. Most forwarders had eight wheels, but many of them could also be purchased with six wheels as a less expensive option. Most SGHs had six wheels, but some models were also offered with four or eight wheels. In general, the hydraulic system of forest machines had a maximum working pressure of 22–24 (26) MPa for forwarders and 24–28 MPa for SGHs. Between 1985 and 2010 there have been increases in the pressure of the work hydraulics of forwarders and SGHs of 15–60% and up to 47%, respectively. Synthetic esthers have replaced mineral hydraulic oils in the hydraulic systems, and engine emissions have been reduced according to international regulations. The use of high-tensile steel materials in components such as harvester heads, grapples and chassis was common in machines available in early 2010, and the cabins of most large SGHs can be levelled when operating on slopes, and in many cases the cabin can be rotated. Many forwarders also had these features. Options for many current large forwarders are a load-scaling system and an enlargeable load space. Many current machines are also equipped with Global Positioning System (GPS) and Geographical Information System (GIS).
There were correlations between the lifting torque of forwarder booms and the mass of forwarders available in both 1985–1989 and March 2010. Heavier forwarders also had higher lifting boom torque (). In general, forwarders available in 2010 have higher lifting boom torque than those manufactured in 1985–1989 (by on average 30% for a 12 t forwarder) ().
Figure 1. Boom lifting torque (kNm) as a function of machine mass (kerb weight) of forwarders (tonnes) manufactured in 1985–1989 and 2010.
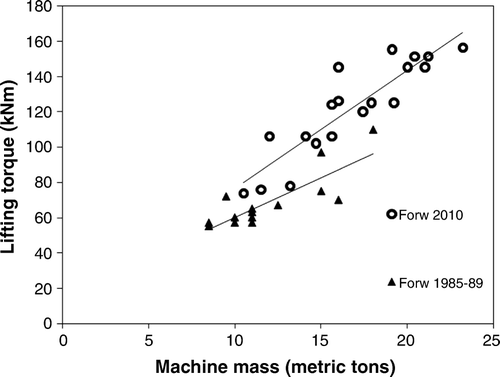
In the years 1985–1989 there was hardly any correlation between the mass of harvesters and the lifting torques of their booms; almost all harvesters manufactured in 1985–1989 had a lifting torque of 100–160 kNm, regardless of the mass of the machine itself (). Among machines available in March 2010 the correlation between mass and lifting torque was strong (R 2=0.95) and heavier machines were also equipped with stronger booms (). In general, the boom lifting torques of 12 t harvesters available in March 2010 and 1985–1989 were very similar (), and in both cases booms of 15 t harvesters had 37–39% higher lifting torque than those of 15 t forwarders.
Figure 2. Boom lifting torque (kNm) as a function of the machine mass (kerb weight) of harvesters (tonnes) manufactured in 1985–1989 and 2010.
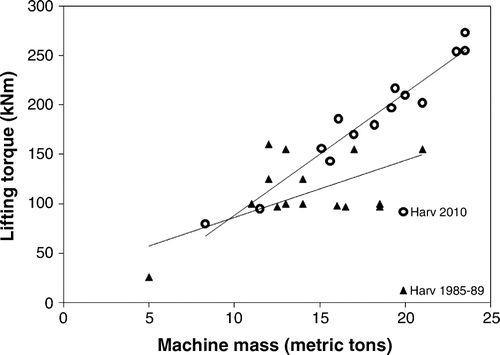
Depending on differences between brands and equipment, there were variations in the prices, as shown in Figure 3, of ± 8–9% (on average for a single year), for all machines except for DGHs and large forwarders, for which the variation was only ± 3–4%.
The price of mid-SGHs was approximately the same in 2009 as in 1985 (). However, there have been variations over time, as can be seen for all machine categories (). The prices of forwarders have increased substantially; for large forwarders by 30% and for medium-sized forwarders by 50%, from 1985 to 2009. However, it is important to remember that load capacities (especially those of medium-sized forwarders) increased during that period owing to a shift in definition. In addition, large SGHs have increased in price, but the large rise in prices in 2004 reflects more the introduction of a number of very large SGHs (21–24 t) to the market than price rises for already existing types of large SGHs. The price of the very large SGHs in 2009 was on a par with those of DGHs when they disappeared from the market in 1993–1995, but still 15–20% below those of DGHs in around 1990 (). The price gap between medium-sized SGHs and forwarders decreased substantially from 1985 to 2009. In 1985 a medium-sized harvester was 75% more expensive than a medium-sized forwarder. By 2009 this difference had decreased to 21% ().
Figure 3. Relative prices of new forest machines, as a function of manufacturing year, adjusted by the Swedish consumer price index (CPI) to January 2010 level. DGH = double-grip harvester; SGH = single-grip harvester; Forw = forwarder.
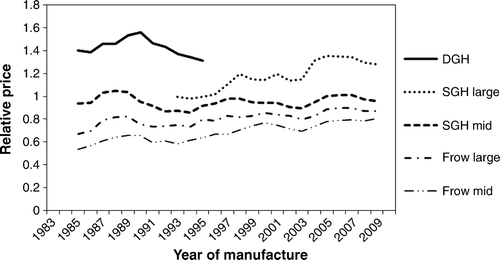
The MA increased in the period from 1985 to 2008, from 80% to 88% for forwarders and from 70% to 85% for SGHs (). The relative difference in MA between new forwarders and SGHs was larger in 1985 than in 2008 (). The MA of DGHs increased from approximately 75% in 1985 to approximately 78% in 1990 (data not shown).
Figure 4. Mechanical availability (%) of forwarders (Forw) and single-grip harvesters (SGH) as a function of year. The definition of mechanical availability used here is productive work time including delays with duration shorter than 15 min (E15 time) divided by direct work time according to Björheden (Citation1991) (i.e. excluding time for preparations, maintenance and relocation).
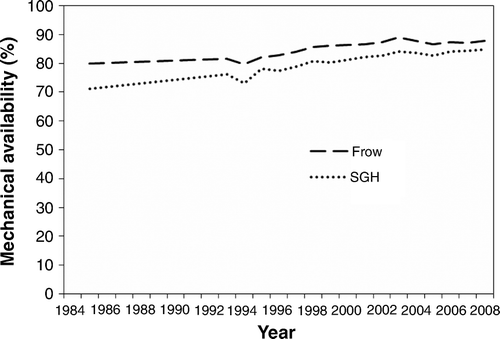
The harvesting cost of thinnings decreased in the period from 1990 to 1998, and then remained quite constant until 2007 (). The harvesting costs of final fellings decreased in the period 1985–2006. The peak that can be seen in in 2005 was due to unusual circumstances, i.e. the harvesting of forests felled by the storm Gudrun in southern Sweden (). In 2008, costs of both thinning and final felling tended to increase ().
Figure 5. Costs of large-scale harvesting operations in Sweden (SEK m−3 gross volume) as a function of the year adjusted by the Swedish consumer price index (CPI) to January 2010 level. 1 m3 gross volume = 0.82 m3 solid volume under bark. The data for the period before 1989 were not divided according to type of harvesting operation. The curve for Total includes proportions for thinning of 13–17% of the total volume for the years 1985–1987, and 21–28% for the years 2006–2008.
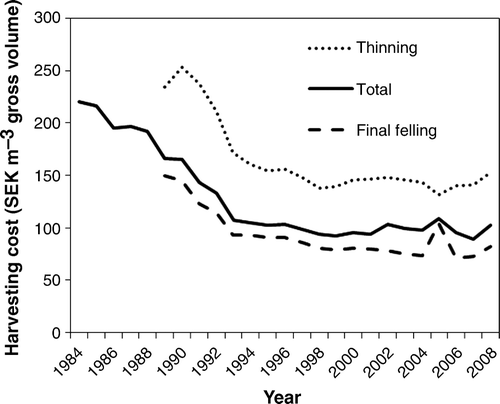
The major factors influencing productivity in logging at the stand level are average stem volume and extraction distance. There were no obvious trends in these factors, based on several surveys from the period 1987–2008. Overall, the average stem volume seems to have increased slightly in final felling (from 0.26 to 0.31 m3 sub), whereas in thinning the volume has been quite stable (0.10–0.11 m3 sub). Extraction distances have also remained fairly similar, at around 380 m in thinning and 410 m in final felling, according to data presented by Freij and Tosterud (Citation1989), Nordlund (Citation1996), Johansson (Citation1997, Citation2001) and Brunberg (Citation2005, Citation2009).
The productivity of logging by the Swedish forest enterprise SCA increased almost three-fold in the period from 1985 to 2010 (). As a consequence of maturing machine technology and the lack of major changes in technology and practices, the forestry sector in Sweden further increased the outsourcing of logging operations in the 1990s (e.g. Lidén, Citation1995). Thus, the productivity increase also has an organizational component. However, since 2003 there have been signs of declining productivity ().
Figure 6. Trends in productivity for Swedish forestry in general (solid line, including logging and silviculture; Swedish Forest Agency, Citation1990, Citation1999, Citation2009) and for the SCA forest enterprise (dotted line, logging only) 1985–2008. 1 m3 gross volume = 0.82 m3 solid volume under bark.
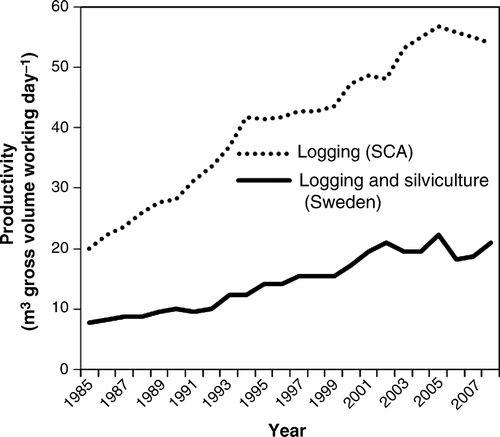
Discussion
The changes in prices of forest machines over time () are highly correlated with changes in the market for forestry products, i.e. Swedish market prices for roundwood (Swedish Forest Agency, 2009).
Compared with other off-road vehicles, few forest machines are manufactured (Drushka & Konttinen, Citation1997). Consequently, for developments in general vehicle technology the forest machine manufacturers depend on progress in other vehicle industries, even though the forest environment requires specialized solutions. One example is electro-hybrid transmissions. This is an area that is developing rapidly, and there is an innovative example of a forwarder on the market with such a system (Löfroth, Citation2007). Whether this becomes a common feature of forestry machines will depend, to a great extent, on how common it becomes in other vehicles.
Other examples are damping and other ground-contact systems to reduce soil damage and vibrations in the machine, e.g. active systems to damp shock in the front parts of a forwarder (Ponsse, Citation2010) and hydraulic damping for the cabin (Rottne, Citation2010) or intelligent bogie systems that can adjust the footprint to the ground conditions. A further example is the emergence of autonomous vehicles, for which there are rapid developments in the agricultural sector and research on forest machines is also ongoing (Hellström et al., Citation2009).
Forest machines, especially Scandinavian machines, rely heavily on boom handling for the main work (Björheden, Citation1997). Hence, development of systems that make operation of the boom faster, less stressful and/or partially automatic will continue (Löfgren, Citation2009). Another way to decrease the time constraints of boom operation is to eliminate crane cycles, e.g. through direct loading of the transport unit by the processing unit (Bergkvist, Citation2008, and the discussion of harwarders, below). Even though new technology often also equals more complex technology, there are examples of the opposite. For example, a new boom with a pivot in the middle has proven to be more productive in thinning, because it can more easily reach trees behind other trees (Lindroos et al., Citation2008).
Another development that can save time, and energy, is direct loading on harwarders rather than using the conventional two-machine system (Talbot et al., Citation2003; Bergkvist, Citation2010). The harwarder has been operating in practical forestry on a trial scale with promising results, delivering potential cost and fuel savings of 10–15% and 20–40%, respectively (Bergkvist, Citation2010). It will probably be most competitive in final-felling in situations where there are moderate stem volumes and transport distances (Bergkvist, Citation2010), as well as in small stands requiring many machine relocations (Talbot et al., Citation2003). Hence, this system is most likely to be further developed and applied.
At present, harvesting forest biomass for energy is receiving considerable attention in Swedish forestry. The annual harvest for this purpose has increased by 1–1.5 million m3 year–1, corresponding to 3 TWh year–1, and the increase in demand is projected to continue for some years. The new work task, to produce wood for the traditional forest industry and biomass for energy and material conversion, will undoubtedly affect the configuration of forest machines. Currently, roundwood and biomass are harvested with different machines, e.g. one system for roundwood, another for logging residues and, sometimes, a third system for stump recovery. A possible trend is that a new generation of forest machines and methods may be developed to facilitate integrated handling of roundwood and forest biomass for energy generation. This would reduce the number of machine relocations required and the number of crossings on site. Similar trends were apparent in the early 1980s when, triggered by the oil crisis of 1972–1973, several prototypes for combined roundwood and bioenergy procurement were tested (Jonsson, Citation1985; Freij & Tosterud, Citation1989; Östberg, Citation1990; Drushka & Konttinen, Citation1997). Now, the international interest in renewable energy sources, such as forest bioenergy, seems even stronger (IPCC, Citation1996, Citation2007; United Nations, Citation1997; Allison et al., Citation2009). This may, with time, reduce the almost complete dominance of the cut-to-length system in the Nordic countries. Clearly, it does not make sense to divide trees into roundwood, treetops and branches on site if the whole tree, including the stump, will be eventually recovered. Alternative ways of harvesting forests will be analysed in coming years, including both new concepts for full-tree harvesting and ideas that have already been proposed and tested in the early stages of development.
Acknowledgements
Data have been kindly provided by Jan Åhlund (head of forest technology at Holmen Skog forest enterprise), Hans Eliasson (Chairman Cranab AB), Magnus Bergman (head of technique and business development at SCA forest enterprise), Bo Morenius (former head of forest technology at Stora Enso Skog forest enterprise) and Per Lindén (former head of forest technology at SCA forest enterprise). This study has been funded by the Department of Forest Resource Management, at SLU.
References
- Allison , I. , Bindoff , N. L. , Bindschadler , R. A. , Cox , P. M. , de Noblet , N. , England , M. H. , et al. . 2009 . The Copenhagen diagnosis, 2009: Updating the world on the latest climate science . Sydney : Climate Change Research Centre (CCRC), University of New South Wales.
- Andersson , S. 2004 . Skogsteknik förr och nu [Forest technology, past and present] 102 116 . Skogshistoriska sällskapets årskrift [Swedish Society of Forest History]. (In Swedish.)
- Bergkvist , I. 2008 . Direct-loading upstarts can break dominance of harvester–forwarder system Resultat nr 9 . pp. 1 4 . Uppsala : Skogforsk . (In Swedish with English summary.)
- Bergkvist , I. 2010 . The harwarder in Swedish forestry: Experiences and potential for further development Redogörelse nr 1 , pp. 1 28 . Uppsala : Skogforsk . (In Swedish with English summary.)
- Björheden , R . 1991 . Basic time concepts for international comparisons of time study reports . Journal of Forest Engineering” , 2 ( 2 ) : 33 – 39 .
- Björheden , R. 1997 . Studies of large scale forest fuel supply systems . Doctoral thesis . Acta Universitatis Agriculturae Sueciae, Silvestria , 31 .
- Brunberg , T. 2005 . Forestry costs rise in 2004 Resultat nr 13 , pp. 1 4 . Uppsala : Skogforsk . (In Swedish with English summary.)
- Brunberg , T. 2009 . Forestry balance sheet 2008: Rising costs and timber prices Resultat nr 7 , pp. 1 4 . Uppsala : Skogforsk . (In Swedish with English summary.)
- Drushka , K and Konttinen , H . 1997 . Tracks in the forest , 1 – 254 . Helsinki : Timberjack Group .
- Forskningsstiftelsen Skogsarbeten 1988 . 50 Years of forest technology R&D in Sweden Redogörelse nr 6 , pp. 1 45 . Kista : Forskningsstiftelsen Skogsarbeten . (In Swedish with English summary.)
- Freij , J. & Tosterud , A. 1989 . Systems and methods used in large scale forestry—Logging, silviculture and roads 1987–1992 (Redogörelse nr 6 , pp. 1 66 . Kista : Forskningsstiftelsen Skogsarbeten . (In Swedish with English summary.)
- Frumerie , G. 1993 . Terrängmaskinen Del 1 The off-road vehicle 1 1 476 . Stockholm : Skogforsk . (In Swedish.)
- Fryk , J , Larsson , M , Myhrman , D and Nordansjö , I . 1991 . Forest operations in Sweden , 1 – 59 . Kista : Forskningsstiftelsen Skogsarbeten .
- Hellström , T , Lärkeryd , P , Nordfjell , T and Ringdahl , O . 2009 . Autonomous forest vehicles—Historic, envisioned and state-of-the-art . International Journal of Forest Engineering” , 20 ( 1 ) : 31 – 38 .
- IPCC (Intergovernmental Panel on Climate Change) 1996 . Climate change 1995. Impacts, adaptation and mitigation of climate change: Scientific–technical analysis . IPCC WG II Report . Cambridge : Cambridge University Press .
- IPCC (Intergovernmental Panel on Climate Change) 2007 . Summary for policymakers . In S. Solomon et al. Climate change 2007: The physical science basis . Contribution of Working Group I to the Fourth Assessment Report of the IPCC, AR4 . Cambridge : Cambridge University Press .
- Johansson , A. 1997 . Costs and revenue in Swedish forestry 1995–1996 Resultat nr 25 , pp. 1 4 . Uppsala : Skogforsk . (In Swedish with English summary.)
- Johansson , A. 2001 . Forestry costs and revenue 2000: A year of storms and floods Resultat nr 7 , pp. 1 4 . Uppsala : Skogforsk . (In Swedish with English summary.)
- John Deere 2010 . Homepage for John Deere forest machines . Accessed March 1, 2010 http://www.deere.com/
- Jonsson , Y. 1985 . Stumpwood utilization techniques Redogörelse nr 3 , pp. 1 35 . Stockholm : Forskningsstiftelsen Skogsarbeten . (In Swedish with English summary.)
- Komatsu 2010 . Homepage for Komatsu forest machines . Accessed March 1, 2010 http://www.komatsuforest.se/
- Lidén , E. 1995 . Forest machine contractors in Swedish industrial forestry Report no 195 , pp. 1 43 . Garpenberg : Department of Operational Efficiency, Swedish University of Agricultural Sciences.
- Lindroos , O , Bergström , D , Johansson , P and Nordfjell , T . 2008 . Cutting corners with a new crane concept . International Journal of Forest Engineering” , 19 ( 2 ) : 21 – 27 .
- Löfgren , B. 2009 . Kinematic control of redundant knuckle booms with automatic path-following functions TRITA-MMK 2009 24 , pp. 1 158 . Doctoral thesis, Department of Machine Design, KTH School of Engineering Sciences, Stockholm .
- Löfroth , C. 2007 . Hybrid forwarder achieves reduction in fuel consumption Resultat nr 10 , pp. 1 4 . Uppsala : Skogforsk. . (In Swedish with English summary.)
- Nordlund , S. 1996 . Logging technology and methods: Trends in large-scale forestry Resultat nr 4 , pp. 1 4 . Uppsala : Skogforsk . (In Swedish with English summary.)
- Östberg , M. 1990 . En smedjas förvandling—ÖSAs historia [The transformation of a blacksmith's workshop—The history of ÖSA] 1 175 . Bollnäs, , Sweden : Nyströms tryckeri AB . (In Swedish.)
- Ponsse 2010 . Homepage for Ponsse forest machines . Accessed March 1, 2010: http://www.ponsse.com/
- Rottne 2010 . Homepage for Rottne forest machines . Accessed March 1, 2010: http://www.rottne.com/ [accessed 1 April 2010] .
- Statistics Sweden 2010 . Consumer Price Index for January 2010 . Statistiska meddelanden PR 14 SM 1002 [Table: Consumer Price Index (CPI) 1980 = 100, fixed index numbers] Retrieved from http://www.scb.se/Pages/TableAndChart_272151.aspx (In Swedish.)
- Sundberg , U. 1990 . Bruket av skogen [The use of forest] In Skogen, Sveriges nationalatlas [The Forest, The Swedish National Atlas] 104 117 Stockholm : Sveriges nationalatlas . (In Swedish.)
- Swedish Forest Agency 1990 . Swedish Statistics Yearbook of Forestry . Official Statistics of Sweden .
- Swedish Forest Agency 1999 . Swedish Statistics Yearbook of Forestry . Official Statistics of Sweden .
- Swedish Forest Agency 2009 . Swedish Statistics Yearbook of Forestry . Official Statistics of Sweden .
- Talbot , B , Nordfjell , T and Suadicani , K . 2003 . Assessing the utility of two integrated harvester-forwarder machine concepts through stand level simulation . International Journal of Forest Engineering” , 14 ( 2 ) : 31 – 43 .
- United Nations 1997 . The Kyoto Protocol to the Convention on Climate Change . Bonn : Climate Change Secretariat .