Abstract
Human-Robot interaction plays a vital role in the service robotics field, especially to support old age-dependent people for socio-economic reasons. In this paper, an indigenous 3D printed 6 DoF robotic arm is proposed to support specially-abled people in their independent-feeding process. The objective of the present paper is to find the combination of optimal positional controllers such as CPID, FC, FPID and FOPID, which can handle the cubic reference input signal and can produce an output signal with minimal overshoot and lesser positional error. The reduced positional error helps the robotic arm to accurately reach the destination with minimal oscillations. This would reduce the wastage of food in the middle of the trajectory as well as at the destination. The technical challenge of the paper is to synchronize machine vision, robot kinematics and trajectory planning with robot control for multiple intermediate points, subjected to the cubic input signal. The feeding robotic arm is equipped with Intel© visual depth camera, which is in synchronization with the microcontroller, servo controller, and servo actuators. Here, six intermediate points were identified in the C-space using FK, among which, fuzzy controller was selected for the first two IPs, the GA optimized FOPID was selected for IP3 to IP5 and FPID was deployed for the last IP. The GA: FOPID produced a negligible overshoot of 0.67%, whereas FC and FPID produced an overshoot of 1.4% and 0.8% respectively. The positional error gap between GA: FOPID, FC and FPID was 0.9, and 0.6 Deg/sec respectively. The selection of combination of optimal controllers helps the manipulator to successfully deliver the food without wasting it. The repeatability of the feeding process is ensured by successfully conducting user testing on 20 users for 25 cycles.
Disclosure statement
No potential conflict of interest was reported by the author(s).
Additional information
Funding
Notes on contributors

Priyam Parikh
Priyam A Parikh has been working as an assistant professor, Industrial Design Department, Institute of Design, Nirma University. He is pursuing his PhD from Nirma University, Gujarat, India in the area of robotics and human robot interaction. He has published more than 20 research papers in the field of mechatronics, robotics and design. He has been awarded Research Excellence Award by INSC Banglore, India. His Area of interest includes: robotics, mechatronics, HCI design, human robot interaction and open source electronics. Email: [email protected]

Reena Trivedi
Reena Trivedi is working as associate professor in Mechanical Engineering Department, Nirma University. She has experience of more than 23 years in the field of teaching, research and industry. She obtained PhD degree from IIT Bombay in 2016. She has published more than 7 research papers in the areas of MEMS, optimization, FEA, etc. in international referred journals and presented/published over 20 papers in international conferences/proceedings. She is a reviewer of international refereed journals in the fields of design engineering, MEMS, optimization, etc. Her areas of research interest include CAD, CAE, FEA, design and robotics.
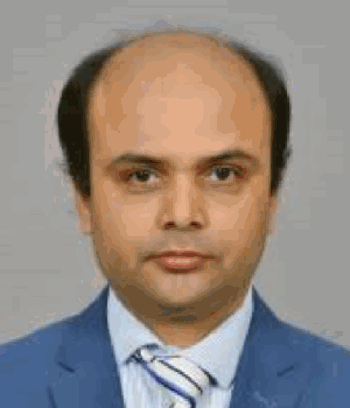
Jatin Dave
Jatinkumar Dave is working as assistant professor in Mechanical Engineering Department, Nirma University since 2005. He has experience of more than 16 years in the field of teaching, research and industry. He obtained BE (mechanical engineering) degree in 1999 and ME (CAD/CAM) degree in 2002 respectively from Gujarat University. He obtained PhD degree from Nirma University in 2016. He has published more than 30 research papers in the area of stress analysis of composite material, finite element analysis, machine design, CAD and robotics. Email: [email protected]
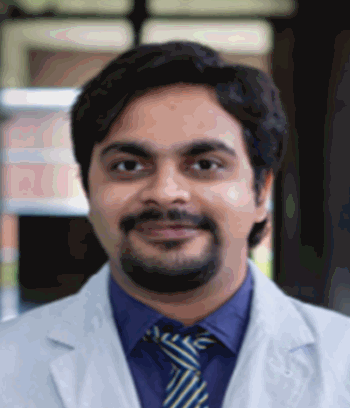
Keyur Joshi
Keyur D Joshi is a researcher, teacher and learner in the fields relating to mechatronics engineering. He completed his PhD in mechanical engineering from Queen's University at Kingston, Canada in 2018 with specializations machine vision. He was a teaching assistant at the university and taught mechatronics, instrumentation and control system related concepts. He has several publications on topics such as mechatronics, machine vision and digital image processing. His current research interests are machine vision, computer vision, fuzzy logic, deep machine learning and artificial intelligence. Email: [email protected]

Dipak Adhyaru
Dipak M Adhyaru received his PhD from the IIT Delhi, India and at present, he is working as a professor of the Electronics and Instrumentation Department, Institute of Technology, Nirma University, Gujarat, India. His research interest includes soft computing applications in control and automation. Email: [email protected]