ABSTRACT
Carbon nanotube(CNT)-based materials is a promising thermally conductive filler for phase change materials(PCM), while its widely applications are greatly hampered by the hydrophobicity of CNTs. In this work, a novel composite PCM based on hydrophilic modified porous copper network(PCN)-CNT filler and erythritol(Ery) was explored. The hydrophilic modified PCN-CNT filler can be obtained upon heat treatment. During the heat treatment process, defects and oxygen-containing functional groups formed on the surface of CNTs, thus improving the hydrophilicity of CNTs. The optimum heat treatment temperature is determined to be 500°C, at which the adsorptive capacity of the modified filler reaches 88.2% for Ery, larger than 28.2% of the unmodified one. The as-prepared PCN-CNT/Ery composite PCM maintains a similar melting point to that of pure Ery, and its latent heat is as high as 213.2 J g−1. The thermal conductivity of PCN-CNT/Ery composite PCMs increases by 892% and 51% compared with pure Ery and PCN/Ery composite PCM, respectively. Moreover, the PCN-CNT filler could help improve the supercooling of Ery significantly. Besides, the enthalpy loss of the composite PCM was negligible after 20 cycles.
Graphical Abstract
Defects and functional groups are introduced on the surface of CNTs by heat treatment. Therefore, the heat-treated CNTs showed a transition from hydrophobic to hydrophilic, thus improving the interface compatibility of PCN-CNT and Ery phases in composites. Highly conductive PCN-CNT filler modified under the optimal heat treatment temperature compound with pure Ery by vacuum impregnation, significantly improving the thermal transfer properties of Ery.
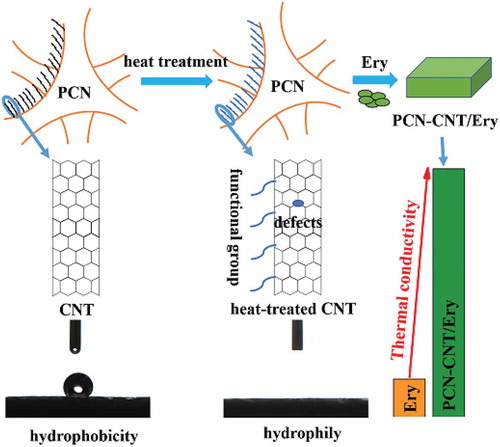
Acknowledgments
We gratefully acknowledge the National Key Research and Development Program of China (No. 2016YFB0301400), the National Natural Science Foundation of China (No. 51601226, No. 51874370), the Natural Science Foundation of Hunan Province (No.2019JJ40375, No. 2019JJ50793) and the State Key Laboratory of Powder Metallurgy for financial support. The authors also wish to thank the reviewers and editor for kindly giving revising suggestions.
Disclosure Statement
No potential conflict of interest was reported by the authors.
Supplementary material
Supplemental data for this article can be accessed here.