Abstract
For the designer, the production of innovative seacraft involves the use of atypical materials at the shipyard. This article presents a comparison between traditional (SMAW) and innovative [LBW, electron beam welding (EBW)] welding technologies to illustrate the feasibility and suitability – also in economic terms – of the penetration of new welding technologies in the shipbuilding sector. In particular, the material considered for the production of submerged bearing components in an innovative submerged-wing hydrofoil is X4CrNiMo13-4, a martensitic stainless steel presenting improved resilience chosen by the shipbuilding company (Rodriquez Cantieri Navali), above all, on account of its high mechanical strength. In order to avoid costly PWHT, which, given the large size of the components, has a heavy influence on production costs, welding procedure specifications were developed using an austenitic filler material that, while inducing a limited reduction in performance in the melt zone, allows for conspicuous economic advantages. Research has shown how EBW technology undoubtedly allows for better results, while – although it would be more suitable for large-size components – LBW technology requires a more critical optimization of parameters.
Notes
Paper presented at the National Welding Days 6 Workshop: ‘Fabrication of welded structures and components’, Genoa, 26–27 May 2011.
a. CALEF. Consortium for the Development of Industrial Applications of Laser and Electron Beam and of Process engineering. Materials, Methods and Production Technology.
b. CETMA. Planning, Design and Materials Technology Centre.
Additional information
Notes on contributors
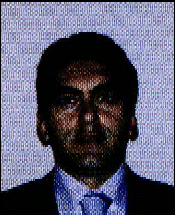
G. Barbieri
Giuseppe Barbieri graduated with honours in Mechanical Engineering at the University of Calabria in 1997. In 2002, he was awarded a research Doctorate qualification in Machine Engineering at the Bari Polytechnic. From 1999, he has been a researcher at the ENEA Technical Unit for Materials Technology. In 2005, he was awarded the EWE diploma. He is also an expert in high energy density and hybrid welding (laser-arc) processes. He has been a member of the RINA Certification Committee since 2009. He is currently a welding task leader for ENEA in the European Project MATTER.

F. Cognini
Francesco Cognini, a graduate in Mechanical Engineering, works at the ENEA Technical Unit for Materials Technology and is involved in work related to the application of laser and electron beam technologies in mechanical engineering and processing. He has taken part in various national research programmes in the field of transportation and energy production.

M. Moncada
Massimo Moncada graduated in Mechanical Engineering at the ‘Roma Tre’ University. Since June 2000, he has been working at CR ENEA at Casaccia in the Technical Unit for Materials Technology. He is involved in feasibility studies, the development and validation of joining methods based on the use of high-energy density sources, such as electron beam and laser. He has taken part in various research activities in projects funded by the MIUR, with a particular bias on the application of HDE technologies in the transport sector. He is enrolled in a course of Doctoral-level studies in Mechanical and Industrial Engineering at the Roma Tre University.
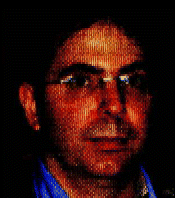
G. Morabito
Giovanni Morabito graduated in Materials Engineering in 1995 at the University of Messina. In 1997, he gained further qualification in Structural Mechanics at the Department of Mechanical Engineering of the University of Catania. Since 2000, he has been working at the Rodriquez Shipyard in Messina as a researcher and designer.