Abstract
The main objective of this study was to assess the performance of electrochemical regeneration of granular activated carbon via a set of bench‐scale experiments using different operating conditions in the regeneration of several different activated carbons loaded with phenol or natural organic matter. The regeneration efficiency can be increased by increasing the charge applied, whether this was achieved by an increase in current or regeneration time. The degree of phenol‐adsorption saturation did not significantly affect the regeneration efficiencies. The regeneration efficiencies of the various types of phenol‐loaded activated carbon were quite similar despite the differences in their conductivity. The activated carbon exhibiting fully reversible adsorption of phenol had slightly higher regeneration efficiencies than those involving partially irreversible adsorption. Electrochemical regeneration of activated carbon is feasible at a laboratory scale as regeneration efficiencies up to 80% were achieved during electrochemical regeneration of phenol‐loaded or natural organic matter‐loaded activated carbons.
Introduction
In response to more stringent water quality regulations, many treatment systems use granular activated carbon (GAC) column adsorbers to meet the required effluent standards. GAC column adsorbers are being used in upgrading water treatment plants (for taste and odour removal, toxic organics removal and/or disinfection by‐product precursor removal), in groundwater remediation (for toxic organics removal), in upgrading wastewater treatment plants (for toxic organics removal and for polishing to permit reuse) and in home water treatment units. The relatively high cost of GAC and its regeneration are the main disadvantages of GAC adsorbers. The cost can be significantly reduced by reactivating spent GAC rather than replacing it with virgin carbon [Citation1–Citation3]. Although one can economize by purchasing regenerated GAC, owing to safety considerations drinking water applications are only permitted to use virgin GAC or regenerated GAC from the same site.
Although thermal, chemical, biological, and electrochemical methods of regeneration have been researched, in practice, thermal regeneration is used almost exclusively. It involves the gradual heating of the GAC to about 800 °C in furnaces with an oxygen deficient atmosphere. This causes the adsorbed impurities to volatilize and desorb without burning the GAC. The high temperature also results in the oxidation of some of the desorbed contaminants. This process has resulted in regeneration efficiencies greater than 90%. However, the process characteristics include: (1) loss of carbon mass (5–15% during each cycle) due to carbon burn‐off and attrition; (2) transfer of some contaminants to the air; (3) high energy cost of heating the GAC to 800–850°C; (4) changes in pore size distribution; and (5) it is only economically feasible when GAC average usage rate is over 620 kg d−1 [Citation3]. Electrochemical regeneration has been studied as an alternative to thermal regeneration [Citation4–Citation14]. The electrochemical regeneration technique possesses several potential advantages over thermal regeneration. These include possible in situ regeneration, minimal GAC losses, high regeneration efficiencies, destruction of the contaminants desorbed from GAC via oxidation at the anode, and suitability for use in small and medium sized treatment facilities.
As researchers in this area have used different reactor configurations, a different activated carbon for each reactor configuration, different adsorbates, etc. [Citation8–Citation14] for further development of electrochemical GAC regeneration technology there is an obvious need for a systematic evaluation of many design and operational variables of electrochemical GAC regeneration systems. Natural organic matter (NOM), which is present in all natural water sources, is the most prevalent organic chemical group in surface waters entering water treatment plants. The adsorption of NOM tends to reduce the adsorption of target contaminants by up to 70% owing to the strong competitive adsorption interaction [Citation15]. The NOM adsorption often controls the regeneration frequency even though the primary purpose in applying the activated carbon may be to remove trace organic compounds [Citation16]. The electrochemical regeneration of NOM‐loaded GAC has not yet been investigated. Given that water treatment is one of the main applications of activated carbon, this is an area that merits study.
The main objective of this study is to investigate the applicability of electrochemical regeneration of GAC via a set of bench‐scale experiments with an improved reactor to assess the impact of regeneration current, regeneration time, three types of GAC, and two different adsorbates (phenol and NOM).
Experimental materials and methods
The following subsections discuss the materials, equipment, procedures, and analytical methods utilized in this study.
Adsorbates
Phenol and naturally occurring background organic matter were used as adsorbates in this research. Phenol (pKa = 9.99) was chosen as a model organic contaminant as it is a common industrial chemical and thus is found in many industrial effluents. Phenol was also selected because it will permit comparisons with earlier electrochemical regeneration research conducted by the present author and co‐worker [Citation7]. The experiments used ACS grade (>99% purity) phenol (Aldrich Chemical Company, Milwaukee, WI).
The phenol solutions were prepared by adding phenol to ultrapure water in a glass carboy and mixing them overnight to obtain a uniform concentration. Ultrapure water was prepared with a Milli‐Q Water System (Millipore, Bedford, MA) consisting of a mixed bed of ion exchange resins, a synthetic activated carbon, organic scavengers, and membranes. The initial phenol concentrations were set at 300 mg l−1. This concentration was selected for two reasons: first, to enable comparison with the results of Narbaitz and Cen [Citation8]; second, they yielded readily measurable equilibrium concentrations when using 1.2 g of GAC and 500 ml solution. The 1.2 g of GAC was needed to have a full single layer of GAC particles on top of an electrode within the regeneration reactor. The initial pH of the unbuffered solution was 6.5 for phenol. The pH was measured by a digital pH meter (Accumet 910, Fisher Scientific, Fairlawn, NJ). Owing to the mixing in a carboy with a headspace of 5 l for 48 h the phenol solutions were saturated in terms of dissolved oxygen.
Given the characteristics of NOM adsorption (i.e. competition among NOM fractions with different adsorbabilities) loading GAC with NOM using a continuous flow column is more representative of GAC adsorption in full‐scale adsorbers than batch experiments. This study investigated the regeneration of NOM‐loaded GAC using Filtrasorb F300 GAC loaded at the pilot‐scale columns located at the Britannia water treatment plant of the city of Ottawa, Canada. This reduced the number of loading column runs required.
Adsorbents
As the properties of GAC depend on the raw material and the method of activation, this study tested three GACs (Filtrasorb 400, Calgon Corp., Pittsburgh, PA; Westvaco Carbon WV‐B, Westvaco Chemical Division, Covington, WV; and Darco, American Norit Company Inc., Atlanta, GA) that were loaded with phenol. These GACs were sieved to obtain a 12 × 16 mesh size (average diameter of 1.4 mm). The smaller GAC particles were discarded to minimize the GAC mass loss during loading/reloading filtration process. The testing also included one NOM‐loaded adsorbent (Filtrasorb 300 (F300), Calgon Corp., Pittsburgh, PA) whose particle size was 8 × 30 mesh and was not adjusted.
Filtrasorb 400 (F400) and Filtrasorb F300 are manufactured from bituminous coal, Westvaco Carbon (WV‐B) is made from wood and Darco Norit (DA‐N) is a lignite‐based activated carbon. Filtrasorb F300 (Calgon Corp., Pittsburgh, PA), which was used in the NOM‐loaded tests, differs from Filtrasorb F400 primarily in its particle size distribution. Moreover, F400 was studied because its regeneration was previously investigated by the present author and co‐worker [Citation7]. They suspected that the less than perfect regeneration of phenol‐loaded F400 was related to the fact that phenol adsorbs partially irreversibly on this GAC. Thus, it was of interest to study the regeneration of sorbate/sorbent systems involving fully reversible adsorption. The sorbate/sorbent combination of phenol/WV‐B was chosen because Vidic et al. [Citation17] showed that it exhibits fully reversible adsorption. As regeneration is likely to be aided by the conductivity of the GACs, the GACs were selected based on their different conductivities. The electrical resistance in air of 4 cm deep GAC beds of F400, WV‐B, and Darco were 13, 2, and 124 Ω, respectively (i.e. WV‐B has the highest conductivity and Darco has the lowest conductivity). It was expected that higher GAC conductivity would increase the regeneration efficiency.
The activated carbons were prepared by boiling in distilled water for 30 min, cooling and settling, then rinsing three times with distilled water to remove fines and impurities that may have desorbed from the GAC. All GAC samples were then placed in glass drying pans and dried in an oven at 105 °C for 24 h. Finally, the GACs were cooled in desiccators and stored until needed. The activated carbon manufacturers report that the total surface area of F400, WV‐B and DAN are 900–1100, 1400–1600, and 600 m2 g−1, respectively. Their manufacturers give their minimum iodine numbers as 900, 900, and 625 mg g−1, respectively. The pH of zero charge was measured following the approach used by Summers [Citation18], the value generated for F400 was 10.3, for WV‐B was 5.0, and for DAN was 7.0. These values are consistent with those reported by Summers [Citation18].
Electrolyte
The electrolyte, which is necessary for electron transfer, was a 0.1 M NaCl solution (5850 mg l−1). The choice of NaCl arose from the facts that it is an inexpensive salt and it performed better than several other salts [Citation7,Citation11,Citation13,Citation14]. Using NaCl as the electrolyte has a drawback in that the oxidation reactions at the anode lead to the formation of some chlorinated organics which may be toxic and will require more time for the system to destroy. These studies also showed that higher concentrations of NaCl did not improve the regeneration efficiencies.
Analytical techniques
Phenol concentrations in solution were measured using a high‐pressure liquid chromatograph (HPLC, model 1090, Hewlett Packard, Palo Alto, CA) with an ultraviolet detector operated at 271 nm following the method used by Ning [Citation19]. The HPLC detection limit was 0.1 mg l−1.
Electrochemical regeneration apparatus
The electrochemical regeneration apparatus consisted of a power supply and a regeneration reactor. The regeneration reactor consisted of a 25 cm high, 7.6 cm inner diameter glass column with sealed ends which housed two platinum wire mesh electrodes (Figure ). For ease of cleaning and assembly, the column reactor consisted of three glass parts, which were joined by clamps. This reactor held the preloaded GAC on top of a platinum wire mesh electrode that acted as the cathode. Previous work has shown that cathodic regeneration is more effective than anodic regeneration [Citation7, Citation9]. The mesh electrodes were placed 2 cm apart. This reactor is superior to that used by Narbaitz and Cen [Citation7] in that the wire mesh electrodes facilitate the removal of bubbles (as some bubbles pass through the wire mesh) and facilitate the migration of the desorbed solute towards the oxidizing electrode (i.e. anode). The impact of regeneration reactor design is discussed elsewhere [Citation8,Citation10]. To minimize potential problems with the electrode fouling, after each test the platinum electrodes were soaked in H2SO4 and then rinsed with Milli‐Q water.
The electrical power was supplied by a potentiostatic controller (model 410, Electrosynthesis, Buffalo, NY) and an accessory power supply (model 420A, Electrosynthesis, Buffalo, NY). This unit was used as a transformer‐rectifier to provide constant current.
Granular activated carbon loading procedure
For phenol related experiments, the GAC was batch‐loaded via the bottle‐point method [Citation20]. In the bottle‐point method, an accurately weighed mass of GAC and the solution of known initial phenol concentration were contacted in 500 ml glass bottles with Teflon™ lined caps. About 1 ml of the bottle volume was left unfilled to avoid losing floating GAC and to leave a bubble within the bottle to facilitate mixing. To provide the necessary mixing, the bottles were placed in an end‐over‐end tumbler which rotated the bottles at 10 revolutions/min. A two‐week contact time was utilized, which was significantly longer than required to achieve equilibrium [Citation8]. The tumbler was operated in a constant‐temperature room maintained at 22±1°C. After a two‐week equilibrium period, each batch of GAC particles was separated from solution via vacuum filtration through a pre‐washed 0.45 µm pore size cellulose nitrate membrane filter (Micro Filtration System, Dublin, CA). The filtrate was stored in a refrigerator at 4 °C until analysed.
Natural organic matter‐loaded Filtrasorb F300 GAC from the pilot‐scale continuous flow columns of the Britannia water treatment plant was also used to investigate the regeneration of GAC. This approach avoided many long‐term batch tests that would have been required if the batch loading (used for phenol loading) had been used. The column was fed coagulated, settled, and mixed media filtered water with average pH, alkalinity, and DOC of 6.9, 3 mg l−1 as CaCO3, and 3 mg l−1, respectively. Analysis of the NOM of the coagulated and settled water at this plant has shown that it consists of 25% fulvic acids and 75% humic acids [Citation19]. Molecular size fractionation indicates that the >30 kdaltons, 10–30 kdaltons, 3–10 kdaltons, 1–3 kdaltons, 0.5–1 kdaltons and <0.5 kdaltons fractions make up 8.2, 9.9, 25.5, 25.2, 8.4, and 22.9% of the dissolved organic carbon (DOC), respectively [Citation21]. As reloading the GAC under the same conditions was not possible, the regeneration efficiency was evaluated based on the iodine number. While the iodine number is not truly representative of NOM adsorption it is a standard technique in the water treatment industry to assess regeneration efficiency.
Evaluation of regeneration efficiency (RE) for GACs loaded with phenol
The evaluation of regeneration efficiencies for the phenol‐loaded GAC was based on the virgin GAC phenol isotherm plus three sets of sequential experiments. They were: (1) batch loading 1.2 g samples of virgin GAC with phenol using the bottle‐point approach; (2) electrochemical regeneration of the loaded GAC followed by separation of the GAC particles via membrane filtration; and (3) reloading the regenerated GAC by repeating the batch loading step following the electrochemical regeneration. The regenerated GAC particles were then reloaded following the same loading procedure. Knowing the adsorption capacity of GAC in steps (1) and (3), the regeneration efficiencies were calculated by method PR3 or PR2 discussed by Narbaitz and Cen [Citation22]. PR3 method defines the regeneration efficiency as the ratio of the solid phase concentration (q e) of the reloaded GAC to that of the virgin GAC at the liquid phase concentration achieved during the reloading (C e2). This is not the classical definition of regeneration efficiency, however, it does compare the virgin and reactivated loadings on a common basis (i.e. the same liquid phase concentration), it yields similar values to the classical definition [Citation22], and it requires less experimental effort. To use this method, the adsorption isotherm experiment for the virgin GAC must be conducted once and the reloading step only needs to be conducted for a single batch of GAC particles. The regeneration efficiency can be calculated as
where RE3 is the regeneration efficiency calculated via method PR3, q e2 is the adsorption capacity of reactivated carbon (mg adsorbate g−1 GAC), C o2 and C e2 are the initial and the equilibrium liquid phase concentrations within the reloading cycle (mg l−1), q e1 is the adsorption capacity of virgin carbon at C e2 (mg g−1 GAC), M 2 is the mass of GAC used in the reloading cycle (g), V 2 is the volume of adsorbate solution used in the reloading cycle (litres), and k and 1/n are the Freundlich constants for the virgin GAC adsorption isotherm.
The results of a few experiments involving non‐equilibrium conditions were assessed using the PR2 method of calculating the regeneration efficiency as PR3 is not suitable when equilibrium is not reached. For the PR2 method the reloading was conducted using the same procedure as the loading except that the GAC was the same batch of GAC particles (now regenerated), thus the C 02 = C 01 which resulted in C e2 ≠ C e1. In this method regeneration efficiency is calculated as
where RE2 is the regeneration efficiency calculated via method PR2, C 01 and C e1 are the initial and the equilibrium liquid phase concentrations within the loading (mg l−1), M 1 is the mass of GAC used in the loading cycle (g), V 1 is the volume of adsorbate solution used in the loading cycle (litres). This method tends to overestimate the regeneration efficiencies [Citation22].
Evaluation of regeneration efficiency (RE) for GACs loaded with NOM
The regeneration efficiency of the NOM‐loaded GAC was based on the ratio of iodine number [Citation24] of the regenerated GAC to that of the virgin GAC. This avoided NOM reloading in a pilot‐scale column, which would take considerably longer. The iodine number method was not used when assessing GAC loaded with phenol, because in this technique the reactivated GAC must first be dried, which may cause losses of residual phenol due to volatilization, as phenol is semi‐volatile.
Results
In the following subsections the results from isotherm studies, effects of operating conditions (time, electric current, loading, and reloading time) on the regeneration efficiency, and electrochemical process applicability (effect of GAC type and contaminant type) are presented and discussed.
Isotherm studies
The phenol adsorption isotherms were developed to describe the adsorptive properties of virgin F400, WV‐B, and Darco GAC at the pH of the loading experiments (pH 6.5). The results are shown in Figure and the data fit the Freundlich isotherm model: q e = kC e 1/n , where q e is the equilibrium solid phase concentration (mg phenol g−1 GAC), C e is the equilibrium liquid phase concentration (mg l−1), and k and 1/n are the Freundlich model coefficients. The values of the Freundlich coefficients are obtained by linearly regressing the logarithm transformed data. Their simulations of the data are shown in Figure . The correlation coefficients for F400, WV‐B, and Darco isotherms were 0.995, 0.992, and 0.990, respectively. The values of k and 1/n are comparable with those in the literature [Citation7, Citation17]. These isotherms were used for the calculation of the regeneration efficiencies (RE3) in this study.
Effect of current and time on the regeneration efficiency
The regeneration of GACs was carried out at various electric currents, and the corresponding cell potential varied with electric current and time. There was an increase in the cell potential during the first few hours of operation, and it then remained almost constant over long periods of time. Every set of runs was accompanied by at least a replicate for one of the conditions tested, the differences in the RE values were consistently within ± 2%. The concentration of ions derived from the solutes (desorbed organics and NaCl) decreased with the reactions at the electrodes for the first few hours. The decrease in concentration of ions lowered the electrolyte conductivity. Thus, the cell potential increased correspondingly to maintain a constant electric current. However, over an extended period of time, the principal electrode reactions involve water‐generated ions rather than ions derived from the solutes [Citation23] and this kept the potential almost constant. For applied electric currents of 50 and 100 mA, the cell potentials were slightly different and remained almost constant at 3.4 and 3.6 V, respectively.
The regeneration efficiency (RE3) of phenol‐loaded F400 could be increased to about 75% by increasing the electric current and/or time. The effect of electric current was very marked from 10 to 50 mA and more gradual from 50 to 100 mA. Experiments conducted with phenol‐loaded WV‐B yielded similar results [Citation8]. A higher electric current might have accelerated the contaminant desorption owing to rapid pH changes and/or polarization of the GAC surface [Citation9].
Regeneration time had a similar effect to that of electric current. The RE3% increased rapidly with increasing regeneration time in the first few hours, followed by a more gradual increase for longer times. This pattern is likely to be linked to the mechanisms involved. First, a key step in GAC regeneration is desorption of contaminant from the surface of the GAC [Citation9]. As desorption is a time‐dependent phenomenon, longer regeneration times increased the extent of desorption. Second, with increasing time, more of the desorbed contaminant is oxidized resulting in lower contaminant concentrations in the electrolyte and an increased desorption driving force [Citation8]. This leads to greater desorption and a higher regeneration efficiency. However, the longer regeneration time will also have some disadvantages. It will increase the energy consumption required in GAC electrochemical regeneration. The surface of the GAC may also be altered by exposure to high currents for long periods. Another problem with longer regeneration time is that, as time passes, there will be a depletion of desorbed contaminants and a possible accumulation of reaction products on the platinum electrode surface. This may cause electrode fouling and consequently a decrease in the current efficiency. Therefore, it is important to determine if there is an optimum regeneration time.
The charge applied to the GAC was calculated by multiplying the electric current (A) by time (s). Figure shows that all electric currents produced almost the same RE3 per charge passed. Therefore, the coulombic efficiency for GAC regeneration is independent of the current/time applied. However, a higher electric current can rapidly oxidize the phenol, but it may also alter or deteriorate the adsorption sites. Thus in general, a lower electric current may be more appealing. A similar conclusion was reached by others [Citation6,Citation13].
As high electric current and long regeneration time may contribute to the destruction of all the desorbed contaminant as well as oxidation of by‐products. One could possibly drain electrolyte and treat it in another electrochemical reactor (with possibly different electrodes) for an extended time at a much higher electric current to oxidize more completely the desorbed contaminants in the electrolyte before discharge or reuse.
Effect of loading and reloading time on the regeneration efficiency
Phenol adsorption kinetic studies showed that adsorption on F400 apparently occurs rapidly initially and continues at a decreasing rate [Citation6]. The slower rate adsorption, which has been called a slow adsorption phenomenon, has been hypothesized to be caused by chemisorptions or pore size limitations [Citation25] and by polymerization reactions [Citation17,Citation26]. It has also been hypothesized that these mechanisms are responsible for the portion of the adsorption that is irreversible. As electrochemical regeneration is partly driven by high‐pH‐induced desorption [Citation9], it was hypothesized that if the activated carbon was loaded for a shorter time, it may be more readily reactivated, as it would be less loaded. The shorter time will result in a small fraction of the adsorption taking place in the smaller pores (i.e. less pore size limitations) and there would be less time for phenol polymerization reactions to occur.
A series of experiments investigated the impact of loading time on regeneration efficiency. Figure shows the effect of loading/reloading time on the regeneration efficiency of phenol‐loaded F400 using 50 mA cathodic regeneration for 2.5 h. As a range of values of GAC loading time were used in this set of tests the GAC does not necessarily achieve equilibrium. Accordingly the PR3 method used the virgin isotherm equation (which represents equilibrium conditions) and is not appropriate for the evaluation of regeneration efficiency for this set of experiments [Citation22]. The PR2 method was therefore used to evaluate the regeneration efficiencies, i.e. Equation (Equation3). Figure indicates that there appears to be no significant difference among the various loading/reloading times.
To assess the impact of initial phenol loading on RE2, the above was plotted as GAC regeneration efficiency versus the phenol solid phase concentration (Figure ). The different solid phase concentrations were achieved using the same GAC doses, the same phenol solution (300 mg l−1), and varying the loading time. Figure shows that while the solid phase concentrations of phenol on the GAC ranged between 20 and 120 mg g−1, it had a very slight impact on regeneration efficiencies. Figures and indicate that either irreversible adsorption did not significantly affect the regeneration efficiency or that, given the relatively large GAC dose, there was relatively little slow (irreversible) adsorption. The results illustrated in Figures and show that slow and rapid adsorption kinetic phenomena do not appear to impact the regeneration efficiency.
Evaluation of the impact of GAC types and two different adsorbates
The nature of the adsorbate and the characteristics of the activated carbon determine the adsorption capacity and consequently the ability to reactivate. Thus, the process applicability was investigated by reactivating different types of commercial GACs (F400, WV‐B, Darco) loaded with phenol and F300 loaded with NOM.
Impact of the GAC type
The phenol loading procedure for three different GACs was the same but differences in the GAC characteristics resulted in equilibrium solid phase concentrations (i.e. the loading before regeneration) of 108, 84, and 96 mg phenol/g GAC for F400, WV‐B and, Darco, respectively. The differences in the loadings can be attributed to the differences in the GAC micropore surface area and surface functional groups among these GACs [Citation27]. The regeneration efficiency for different regeneration periods at a constant current of 50 mA for three types of GAC loaded with phenol is shown in Figure . Considering the experimental error, F400 and WV‐B performed essentially the same. Phenol‐loaded Darco showed almost the same performance at lower regeneration times but lower performance at higher regeneration times. Accordingly total surface area is not a good indicator of regeneration efficiency.
Phenol adsorption is partially irreversible on F400 and fully reversible on WV‐B, therefore, higher regeneration efficiencies were expected for WV‐B. The regeneration efficiencies for all the conditions in Figure , however, were essentially the same for both F400 and WV‐B. This may be an indication that electrochemical regeneration could remove both reversibly and irreversibly adsorbed species. Alternatively, the electrochemical regeneration may not have been sufficiently intense to show a difference between reversibly and partially irreversibly adsorbed solute. Karimi‐Jashni and Narbaitz [Citation9] have shown that pH‐induced desorption is one of the main mechanisms in electrochemical regeneration, the adsorption reversibility must still have an impact on electrochemical regeneration efficiency.
The GAC’s performance was also compared after 5 h of regeneration by applying different currents (Figure ). The regeneration efficiency of Darco reaches a maximum and then decreases for higher currents, which may be caused by an alteration of Darco’s surface owing to its lower conductivity. Figure shows that at higher currents, the F400 had slightly lower regeneration efficiencies than WV‐B. This is consistent with partial reversibility of phenol sorbed on F400 and full reversibility of phenol sorbed on WV‐B, but the differences in RE3 are less than expected based on desorption behaviour measured by Karimi‐Jashni [Citation28]. Owing to the similarity of the RE3 values for F400 and VW‐B, it is not readily evident that that there are links between the differences in the RE3 and the differences in the GAC’s physical and chemical surface characteristics reported in the literature for these GACs [Citation27].
Regeneration of GAC loaded with natural organic matter (NOM)
Figure shows the impact of regeneration time (at 50 mA) for F300 loaded with NOM on the regeneration efficiency based on the ratio of the iodine number of the regenerated GAC to that of the virgin GAC. It shows there was a linear relation (null hypothesis probability <0.015) between the iodine‐number‐based regeneration efficiency and regeneration time; the regeneration efficiency increased to 80% as the regeneration time increased to 25 h. The much lower impact of regeneration time on the regeneration of NOM‐loaded GAC as opposed to phenol‐loaded GAC is likely to be due to the greater degree of irreversibility of NOM adsorption [Citation20, Citation21]. Figure also shows that the capacity of virgin F300 subjected to 50 mA current for 25 h was reduced by 2%. This decrease in performance is likely to have been caused by changes in GAC surface chemistry [Citation14,Citation29], but may have been simply experimental error.
Figure 8 Iodine number based regeneration efficiency of NOM‐loaded F300 versus time (current = 50 mA, GAC = 5 g)
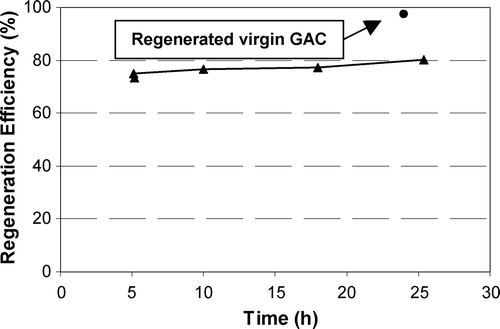
Figure also shows the impact of current on the regeneration of F300 loaded with NOM after 5 h of regeneration. Figure shows that the regeneration efficiency increases slightly with increasing current. Both Figures and show that the F300 loaded with NOM followed similar patterns to the other GACs loaded with phenol. A direct comparison between the regeneration efficiencies of phenol‐loaded GACs and NOM‐loaded GAC is not possible, as two different methods for the calculation of regeneration efficiencies were employed, but an indirect comparison is possible. The regeneration of phenol‐loaded F400 was 59% after 5 h regeneration at 50 mA (Figure ), whereas NOM‐loaded F300 showed 75% regeneration for the same conditions (Figure ). The higher regeneration of NOM‐loaded GAC over phenol‐loaded GAC is surprising because NOM adsorption is expected to be less reversible than phenol adsorption [Citation21,Citation22] and lower regeneration efficiencies for NOM‐loaded GAC are expected. The higher efficiency of NOM‐loaded GAC regeneration may be a matter of the different way of measuring the regeneration efficiency (i.e. using the iodine number).
Conclusions
-
The electrochemical regeneration of GAC in these bench‐scale tests reached regeneration efficiencies up to 80% for both phenol‐loaded and NOM‐loaded GACs.
-
The regeneration efficiency could be increased to a maximum by increasing the regeneration current and/or regeneration time. The regeneration efficiency increases rapidly with increasing regeneration time in the first few hours, followed by a more gradual increase for longer times. Also the effect of current was very marked from 10 to 50 mA and more gradual from 50 to 100 mA. However, the coulombic efficiency for the GAC regeneration was independent of the current/time applied.
-
Loading and reloading time did not significantly affect the regeneration efficiencies of phenol‐loaded F400.
-
The percent regeneration of the various phenol‐loaded GACs was fairly similar for most operating conditions. WV‐B showed slightly better performance than phenol‐loaded F400 at higher currents. The observed results were consistent with degree of phenol adsorption reversibility from these GACs. Darco GAC showed slightly better performance than the other GACs at lower regeneration times and/or higher currents and somewhat lower performance at higher regeneration times and/or currents. It is possible that the surface chemistry of Darco GAC changed over the longer regeneration times and/or higher currents owing to its lower conductivity.
-
Regeneration of GAC loaded with NOM showed that there was a linear relation between the regeneration efficiency and regeneration time; regeneration increases to 80% as the regeneration time increases to 25 h. These higher regeneration efficiencies for NOM‐loaded GAC were unexpected and may result from the characteristics of the iodine number technique used to quantify the regeneration efficiency. It is recommended that future studies on NOM regeneration be based on DOC loadings instead of the iodine number.
Notation
C e1 | = |
equilibrium liquid phase concentrations within the loading (mgl−1) |
C e2 | = |
equilibrium liquid phase concentrations within the reloading (mgl−1) |
C o1 | = |
initial liquid phase concentrations within the loading (mgl−1) |
C o2 | = |
initial liquid phase concentrations within the reloading (mgl−1) |
k | = |
Freundlich constant for the virgin GAC isotherm (mg·g−1 GAC/(l·mg−1)1/n) |
1/n | = |
Freundlich model exponent for the virgin GAC isotherm |
M 1 | = |
mass of GAC used in the loading cycle (g) |
M 2 | = |
mass of GAC used in the reloading cycle (g) |
q e1 | = |
adsorption capacity of virgin carbon at C e2 (mg·g−1 GAC) |
q e2 | = |
adsorption capacity of the reactivated carbon (mg·g−1 GAC) |
RE2 | = |
regeneration efficiency calculated via method PR2 (%) |
RE3 | = |
regeneration efficiency calculated via method PR3 (%) |
V 1 | = |
volume of adsorbate solution used in the loading cycle (l) |
V 2 | = |
volume of adsorbate solution used in the loading cycle (l) |
Acknowledgements
The authors gratefully acknowledge the Natural Sciences and Engineering Research Council of Canada (NSERC) for its financial support of this work.
References
- Adams , J.Q. and Clark , R.M. 1989 . Cost estimates for GAC treatment systems . J. Am. Wat. Works Assoc. , 81 ( 1 ) : 35 – 42 . (1989)
- Adams , J.Q. , Clark , R.M. , Lykins , B.W. , DeMarco , J. and Kittredge , D. 1988 . GAC treatment cost experience at two drinking water utilities . J. Environ. Engng , 114 : 944 – 961 .
- Clark , R.M. and Lykins , B.W. Jr. 1989 . “ Cost Analysis for GAC, in Granular Activated Carbon; Design, Operation and Cost ” . Boca Raton, FL : Lewis Publisher .
- Sveshnikova , D.A. , Ramazanov , A.K. , Aliev , Z.M. , Shakhnazarov , T.A. , Kamalutdinova , I.A. and Babaev , M.‐S. 1987 . Electrochemical regeneration of activated carbon . Khimiya i Tekhnologiya Vody , 9 : 466 – 467 .
- Lazareva , L.P. , Lisitskaya , I.G. , Gorchakova , N.K. and Khabalov , V.V. 1991 . Investigation of patterns of electrochemical regeneration of carbon sorbents after adsorption of dyes . Khimiya i Tekhnologiya Vody , 13 : 980 – 983 .
- Cen , J. 1994 . “ Electrochemical regeneration of granular activated carbon ” . Ottawa, ON, , Canada : Department of Civil Engineering, University of Ottawa . M.A.Sc. thesis
- Narbaitz , R.M. and Cen , J‐Q. 1994 . Electrochemical regeneration of activated carbon . Wat. Res. , 28 : 1771 – 1778 .
- Karimi‐Jashni , A. 2001 . “ Electrochemical reactivation of granular activated carbon ” . Ottawa, ON, , Canada : Department of Civil Engineering, University of Ottawa . Ph.D. thesis
- Karimi‐Jashni , A. and Narbaitz , R.M. 2005 . Electrochemical reactivation of granular activated carbon: pH dependence . J. Environ. Engng Sci. , 4 : 187 – 194 .
- Karimi‐Jashni , A. and Narbaitz , R.M. 2007 . “ Electrochemical regeneration of granular activated carbon: Impact of reactor design ” . in preparation
- Zhang , H. , Ye , L. and Zhong , H. 2002 . Regeneration of phenol‐saturated activated carbon in an electrochemical reactor . J. Chem. Technol. Biotechnol. , 77 : 1246 – 1250 .
- Taiwo , E.A. and Adesina , A. 2005 . Electrochemical regeneration of a native activated carbon . Chem. Biochem Engng Q. , 19 : 269 – 273 .
- Zhou , M.H. and Lei , L.C. 2006 . Electrochemical regeneration of activated carbon loaded with p‐nitrophenol in a fluidized electrochemical reactor . Electrochem. Acta , 51 : 4489 – 4496 .
- García‐Otón , M. , Montilla , F. , Lillo‐Ródenas , M.A. , Morallón , E. and Vazquez , J.L. 2005 . Electrochemical regeneration of activated carbon saturated with toluene . J. Applic. Electrochem. , 35 : 319 – 325 .
- Narbaitz , R.M. and Benedek , A. 1994 . Adsorption of 1,1,2‐trichloroethane from river water . J. Environ. Engng. , 120 : 1400 – 1415 .
- Snoeyink , V.L. 1990 . “ Adsorption of organic compounds ” . In AWWA Water Quality and Treatment , 781 – 875 . New York, NY : McGraw‐Hill . Ch. 13
- Vidic , R.D. , Suidan , M.T. , Sorial , G.A. and Brenner , R.C. 1993 . Molecular oxygen and the adsorption of phenols‐effect of functional groups . Wat. Environ. Res. , 65 : 156 – 161 .
- Summers , R.S. 1986 . “ Activated carbon adsorption of humic substances: Effect of molecular size and heterodispersity ” . Stanford, CA : Department of Civil Engineering, Stanford University . Ph.D. thesis
- Ning , Z. 1997 . “ Modelling of simultaneous removal of easily degradable substrates and chlorinated phenols in UASB reactors ” . Ottawa, ON, , Canada : Department of Civil Engineering, University of Ottawa . Ph.D. thesis
- Narbaitz , R.M. 1996 . “ Modelling the competitive of 1,1,2‐trichloroethane with naturally occurring background organics onto activated carbon ” . Hamilton, ON, , Canada : Department of Chemical Engineering, McMaster University . Ph.D. thesis
- Storrar , M.D. 2006 . “ Adsorption and desorption characteristics of natural organic matter in natural waters on granular activated carbon ” . Ottawa, ON, , Canada : Department of Civil Engineering, University of Ottawa . M.A.Sc thesis
- Narbaitz , R.M. and Cen , J‐Q. 1997 . Alternative methods for determining the percent regeneration of activated carbon . Wat. Res. , 31 : 2532 – 2542 .
- Mortimer , C.E. 1979 . Chemistry a Conceptual Approach. , 4th ed. , New York, NY : Van Nostrand .
- 1995 . “ ASTM D4607‐94: Standard test method for determination of iodine number of activated carbon ” . In Annual Book of ASTM Standards , Gaithersburg, MD : National Institute of Standards and Technology, US Department of Commerce .
- Peel , R.G. and Benedek , A. 1980 . Dual rate kinetic model of fixed bed adsorber . J. Environ. Engng Div., ASCE , 106 : 797 – 813 .
- Karanfil , T. and Kilduff , J.E. 1999 . Role of granular activated carbon surface chemistry on the adsorption of organic compounds. 1. Priority pollutants . Environ. Sci. Technol. , 33 : 3217 – 3224 .
- Leng , C.‐C. and Pinto , N.G. 1997 . Effects of surface properties of activated carbons on adsorption behaviour of selected aromatics . Carbon , 35 : 1375 – 1385 .
- Karimi‐Jashni , A. 1994 . “ Effect of pH on adsorption and desorption equilibria and kinetics of 2‐nitrophenol and phenol onto two activated carbon ” . Ottawa, ON, , Canada : Department of Civil Engineering, University of Ottawa . M.A.Sc. thesis
- Mehta , P.M. and Flora , J.R.V. 1997 . Effect of electrochemical treatment of granular activated carbon on surface acid groups and the adsorptive capacity for phenol . Wat. Res. , 31 : 2171 – 2176 .